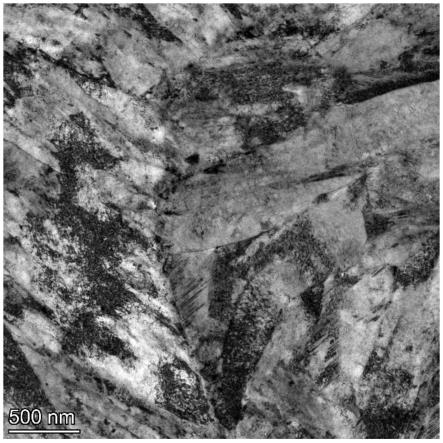
1.本发明属于钢板热处理工艺技术领域,特别涉及一种超薄规格高性能钢板淬火控制工艺。
背景技术:2.随着现有用户对装备轻量化、大型化的需求,尤其是热处理后钢板的性能、质量一致性、表面质量、平整度等要求越来越严苛。目前,高硬度钢板淬火主要使用压力淬火和辊式连续淬火两种方式。压力式淬火是同时实现压力的拘束和近似于水浸式淬火冷却方式,但存在钢板表面冷却不均、表面压痕、板形平直度较差等问题,导致超薄规格高硬度钢板质量一致性较差,钢板性能及平直度无法保证。辊压式淬火方式是连续性淬火,钢板出炉后连续通过多组上下水冷设施组成的辊式淬火设备进行冷却。辊式淬火设备通常通过调节水冷系统的水量及设备辊速等参数,实现钢板淬火均匀性、冷速控制以及板形的控制。辊式连续淬火由于钢板上下表面均可以见水冷却,无淬火软点,其冷却均匀性、冷速控制等问题可以得到极大改善,较压力式淬火更有利于实现钢板的板形控制。
3.然而,随着钢板厚度减至8mm以下,其淬火的冷却均匀度和板形平直度的控制成为超薄规格高硬度钢板淬火工艺的关键。辊式连续淬火方式中,常用的技术包括缝隙式喷嘴冷却、双联或三联水箱式喷嘴冷却、传统层流冷却、水管冷却等;缝隙式喷嘴宽度一定,可调范围较小,导致缝隙式喷嘴瞬时冷速过大且调节难度极大,对于设备制造及安装精度要求过高,超薄规格钢板在极短时间内即冷却至室温,淬火过程中板形极难控制。
技术实现要素:4.本发明的目的在于提供一种超薄规格高硬度钢板分段淬火控制工艺,超薄规格高硬度钢板由于其厚度超薄,对冷却速度的变化更为敏感,基于现有热处理设备及淬火工艺,超薄规格高硬度钢板在淬火过程中极易出现冷却不均、板形平直度较差,淬火后难矫直等问题,本发明提供了一种经济性高、工业稳定性好,可实现超薄规格高硬度钢板淬火冷却的工艺控制方法。不仅实现超薄规格高硬度钢板高效淬火冷却,而且有效解决钢板在降温过程中板形的变化及淬火后板形控制等问题,可得到不同组织的超薄规格高硬度钢板,无传统压力淬火中淬火软点等问题,与现有辊式淬火工艺相比,具备可实现分段式冷却、淬火时板形可控且淬火后板形平直、批次质量稳定性强及受设备精度制约较小等优势。
5.本发明的核心在于区分出高温段和低温段两个区间进行单独控制冷却,也可进行高低温段不同冷速与压力控制的组合实现。高温段旨在控制与冷却相关的基本参数,实现钢板在冷速可控的条件下达到设定的目标值。低温段(相变应力区)的控制主要是由拘束应力设计(主要依靠辊径、辊间距和压应力的有机组合)和水冷却系统控制(冷速、冷却方式、间断冷却和水嘴间距)。
6.超薄规格高硬度钢板具有高硬度、高强度、厚度小等特征,在淬火过程中,组织可调控及板形控制成为超薄规格高硬度钢板淬火工艺的关键。组织可调控需要钢板在淬火过
程中实现冷速可控,与此同时,淬火全程钢板需保证板型平直。采用分段冷却控制旨在:在分段点以上根据钢板的规格和化学成分可调整冷速,避免形成铁素体、贝氏体等其他组织;在分段点以下,钢板需实现冷速大范围调控,以得到不同以马氏体为主体的组织形态。
7.本发明基于辊式连续淬火方式,针对超薄规格高硬度钢板淬火工艺提出:
8.1、基于钢材的淬火变形特征,即在相变内应力远远大于热应力,两者的分段点在于ms点温度;
9.2、基于在热应力控制时(高温段),根据钢板的规格和化学成分可调整冷速,实现钢板不产生变形而降温到设定目标值;
10.3、基于相变应力控制时(低温段),通过具有过冷奥氏体组织钢板的温度控制来提高热状态时钢板的强度,同时可以更为有效的提高约束能力将有效保证钢板的平直度;
11.4、基于材料冷却相变特征,若将钢板快速冷却到ms点-30到+50℃的区域内,钢板将只能发生下贝氏体转变或马氏体转变及两者的复合组织,在此基础上即可通过控制低温区冷却获得马贝复合组织、超快冷马氏体组织、自回火马氏体组织、碳配分的马氏体基钢板等组织,实现钢板的性能优化。
12.本发明针对2~15mm厚度钢板,基于辊道式连续淬火系统,钢板行进速度范围为200mm/s~1500mm/s,采用分段式控冷技术,即以ms点-50到+150℃为分段点,将钢板分为高温段与低温段。具体工艺步骤及控制的技术参数如下:
13.(1)钢板加热及出炉:钢板经加热炉获得830~1050℃的温度和保持设定的时间,随后钢板以200~1500mm/s的速度出炉,保持均速前进,进入淬火设备冷却区域;
14.(2)高温段冷却:通1~12组辊道,每道次实现降温值为20~600℃/道,在1~20s内钢板总计降温350~800℃,实现钢板降温至设定值,即至ms点以上-50到+150℃之间;
15.(3)低温段冷却:当钢板降温设定为ms点以上-50到+150℃,通3~10组辊道进行冷却,每道次实现对钢板的降温值为0~500℃/道;同时保证2~10组辊子产生拘束应力,以保证钢板相变段板形平直。
16.通过喷嘴形式的有效结合可实现钢板温度均匀且不产生变形的条件下降温到设定目标值:高温段采用分级控制降温方式,根据钢板的规格和化学成分可调整冷速,用单组或多组形式的水嘴组合进行冷却,高速射流冷却方式的单喷嘴为冷却区基本组合单元,单喷嘴在滞流区的冷却速度控制在10
3-5
℃/s,从而实现钢板冷却降温值为20~600℃/道。低温段可以采用缝隙式连续水刀方式或速射流水嘴的结构组合,水刀在滞流区冷却速度控制在10
4-5
℃/s,水嘴组合结构中的单喷嘴在滞流区的冷速为10
2-5
℃/s,实现从而实现钢板冷却降温值为20~600℃/道,并可实现冷却速度定量化控制。
17.经过高温段的冷却控制后,此时在低温段区域的钢板可获得温度范围为330-460℃的过冷态奥氏体为主组织,这是实现组织性能的控制必要保障,具体工艺如下
18.1)采用超快冷单喷嘴在滞流区冷却效能达到10
4-5
℃/s的组合或水刀实现强冷却控制,实现钢板整板在ms到mf点之间的冷却效能达到10
3-4
℃/s,获得高位错密度马氏体,实现钢板的高强度化;
19.2)采用超快冷单喷嘴在滞流区冷却效能达到10
2-4
℃/s的组合冷却控制,通过组合实现冷却钢板在ms点温度和mf点之间的温度有效分级控制,控制温度达到10
1-2
℃/s,获得少内应力的马氏体组织,以保证材料的强韧性最优匹配;
20.3)实现定制化的冷却速度控制,通过组合实现冷却钢板的温度有效分级控制,实现钢板整板冷却效能定制化控制,实现整体的控制温度达到10
1-3
℃/s之间,单位控制时间步长为0.03-2秒,实现钢获得马贝复合组织、自回火马氏体、碳元素的配分的复相组织,以获得更优异的材料性能。
21.因此,针对超薄规格高硬度钢板的淬火控制工艺,实现钢板温度和冷速可调、淬火时有拘束应力防止钢板变形成为关键。以ms点为终冷温度控制关键点,钢板淬火全程可分为两段式调控,每段冷速均可调节:钢板出炉后,采用单组或多组降温组合控制方式,均匀降至ms点以上-50℃~+150℃温度区间内;之后钢板进入低温段,采用拘束应力控制工艺,可保证板形平直,同时与多种冷却工艺组合调控,以期实现不同组织性能。
附图说明
22.图1为传统工艺处理得到的马氏体组织图。
23.图2为发明实施例9的典自回火高位错密度马氏体图。
24.图3为实施例3获得高位错密度马氏体和少量亚稳奥氏体图。(马氏体板条和板条间亚稳奥氏体).
25.图4为实施例3获得高位错密度马氏体和少量亚稳奥氏体图(亚稳奥氏体衍射斑点)。
26.图5为热处理后钢板平直度图。
27.图6为钢板获得均匀一致的冷却温度图。
28.图7为钢板冷却曲线控制示意图。
具体实施方式
29.本发明适用于由5~20组上下支撑辊道组成连续辊道式的淬火设备,可实现钢板出炉后以一定速度进入并通过淬火冷却区,在辊道之间内设计喷水冷却装置,可实现淬火工艺的分段控制。具体工艺如下:
30.1、钢板加热及出炉:钢板经加热炉获得830~1050℃的温度和保持设定的时间,随后钢板以200~1500mm/s的速度出炉,保持均速前进,进入淬火设备冷却区域。
31.2、高温段冷却:可以通1~12组辊道,每道次实现降温值为20~600℃/道,在1~20s内钢板总计降温350~800℃,实现钢板降温至设定值(即至ms点以上-50到+150℃之间)。
32.3、低温段冷却:当钢板降温设定的点时(ms点以上-50到+150℃),可以通3~10组辊道进行冷却,每道次实现对钢板的降温值为20~500℃/道。同时保证2~10组辊子产生拘束应力,以保证钢板相变段板形平直。
33.4、低温段组织调控:低温段的冷却可以实现三个范围:主要基于辊道间喷水冷却系统的冷却能力控制,采用超快冷单喷嘴在滞流区冷却效能达到10
4-5
℃/s的组合或水刀实现强冷却控制,实现钢板整板在ms到mf点之间的冷却效能达到10
3-4
℃/s,获得高位错密度马氏体,实现钢板的高强度化;2)采用超快冷单喷嘴在滞流区冷却效能达到10
2-4
℃/s的组合冷却控制,通过组合实现冷却钢板在ms点温度和mf点之间的温度有效分级控制,控制温度达到10
1-2
℃/s,获得少内应力的马氏体组织,以保证材料的强韧性最优匹配;3)实现定制
化的冷却速度控制,通过组合实现冷却钢板的温度有效分级控制,实现钢板整板冷却效能定制化控制,实现整体的控制温度达到10
1-3
℃/s之间,单位控制时间步长为0.03-2秒,实现钢获得马贝复合组织、自回火马氏体、碳元素的配分的复相组织,以获得更优异的材料性能。
34.实施例
35.下面结合具体实施实例说明,但本发明不限于以下具体实施实例。本实例基于辊式连续淬火系统,说明了一种超薄规格高硬度钢板淬火控制工艺的实施过程。
36.针对于2~15mm厚度规格钢板,进行冷却工艺匹配,分别针对于高温段和低温段进行工艺设计和实施,实现工艺结合具体实施例如表1~2所示:
37.表1高温段的冷却工艺
[0038][0039]
低温段实施例如表2所示。
[0040]
表2低温段冷却工艺
[0041][0042]
根据上述工艺方案的结合,对长高为500~8000mm,宽度200~2000mm,厚度规格为2~15mm的多种成分系钢板试制,为了便于清晰表述结果,在该项目中仅选用厚度规格为4mm,传统工艺强度级别为1600mpa级的a钢进行对比分析,所有试验钢的力学性能均为进行了165~210℃低温回火处理后的数据,结果见表3。由些可见,本发明专利在大幅度提升钢板平直度的前提下,通过工艺控制获得高位错密度马氏体、下贝氏体和亚稳奥体,实现钢板的强度、塑性和韧性的提升。
[0043]
表3不同冷却工艺钢板力学性能
[0044]