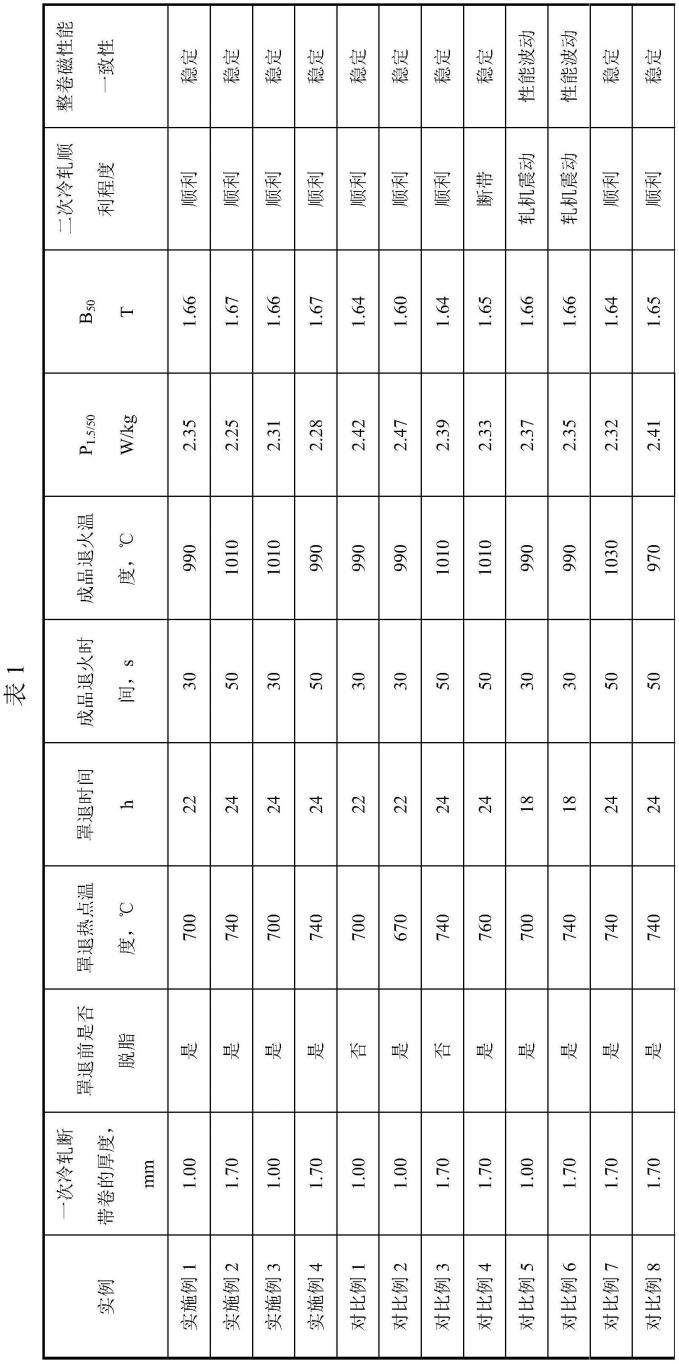
1.本发明属于无取向硅钢制备技术领域,具体涉及一种高牌号无取向硅钢一次冷轧断带后的生产方法。
背景技术:2.随着国家电机能效标准的升级,对于高牌号无取向硅钢的需求量逐渐增加,原本不生产硅钢的钢企也纷纷新建产线投入到无取向硅钢的生产队伍中。受技术水平的限制和冷轧设备能力影响,部分企业特别是民营企业在生产高牌号无取向硅钢的过程中不可避免地出现冷轧断带的现象,据报道统计部分企业在生产高牌号无取向硅钢(si含量≥3.0%)的过程中存在1%左右比例的冷轧断带问题无法命中目标成品厚度。
3.断带出现后由于加工硬化和高si含量硅钢自身的脆性导致无法继续生产只能报废处理,或者经过中间退火后能够再次冷轧至目标厚度但成品磁性能不满足国标要求只能报废处理,损失较大。
4.中国专利cn102634729a-《一种低铁损高磁感高牌号无取向硅钢的制备方法》公开了一种3.0~3.4%si含量且加sn的成分,一次冷轧至0.8mm厚度后进行840~900℃保温1~4min连续中间退火的工艺,制备了0.35mm厚度的目标成品。
5.中国专利cn111235461a-《一种含稀土高碳新能源驱动电机用高强度无取向电工钢及其制造方法》公开了一种2.0~3.0%si/1.0~2.0%als且添加稀土元素ce和微合金元素nb、ti的成分,一次冷轧至0.70~0.75mm厚度后进行720~760℃保温20~40min连续中间退火的工艺,制备了0.35mm厚度的目标成品。
6.贾成义等在期刊《电工材料》2010年第4期中发表的《常化温度对二次冷轧无取向硅钢组织和磁性能的影响》一文中采用二次冷轧法研究了3.10%si、0.54als为主要成分的高牌号无取向硅钢的性能情况,其中一次冷轧至0.78mm厚度后在连续退火炉中进行850℃保温160s的中间退火,最终制备了0.35mm厚度的目标成品。
7.现有技术中通常采用二次冷轧法工艺生产高牌号无取向硅钢,即先一次冷轧至某一特定的中间厚度然后再二次冷轧至成品厚度,然而目前部分企业冷轧断带是随机出现的,也就是说中间厚度不是特定的,因此无现有技术可供借鉴参考。根据材料学原理可知不同中间厚度和中间退火工艺对硅钢组织和织构的影响较大,进而直接影响最终的成品磁性能,但是现有技术中并没有针对如何对冷轧断带后的问题报废卷进行挽救再生产的方法。
技术实现要素:8.为解决上述技术问题,本发明提供了一种高牌号无取向硅钢一次冷轧断带后的生产方法,该方法既能保证厚度为1.00~1.70mm一次冷轧断带卷二次冷轧的顺利、又能保持磁性能维持在正常水平,挽救高牌号无取向硅钢冷轧断带后的直接报废,减少损失。
9.为实现上述目的,本发明采取的技术方案如下:
10.一种高牌号无取向硅钢一次冷轧断带后的生产方法,所述生产方法包括以下步
骤:一次冷轧断带卷
→
中间退火
→
二次冷轧
→
成品退火
→
涂覆涂层
→
精整包装;
11.所述一次冷轧断带卷的厚度为1.00~1.70mm;
12.所述中间退火的温度为700~740℃,由于织构具有较强的遗传性,中间退火的作用是既要保证钢带的晶粒大小合适以保证二次冷轧的顺利完成、又要保证具有良好的织构组分以满足最终成品的磁性能需要,当罩退的温度过低时{100}和{110}织构的组分较少而{111}织构组分多,对磁性能不利;当罩退温度过高时晶粒尺寸较大不利于二次冷轧顺利。
13.所述高牌号无取向硅钢中的si、mn、als的重量百分比为:3.0%≤si≤3.2%、0.1%≤mn≤0.5%、0.4%≤als≤1.0%。
14.所述一次冷轧断带卷经炼钢
→
连铸
→
铸坯加热
→
热轧
→
常化酸洗
→
一次冷轧得到,且一次冷轧过程中发生了断带。
15.在进行一次冷轧之前,酸洗后的热轧钢带的厚度为2.20mm,其晶粒为均匀的再结晶铁素体组织,平均晶粒尺寸为90~100μm,具有较强的goss({110}《001》)织构、{112}《110》织构和γ织构。
16.所述中间退火采用罩式炉退火,罩式炉内全氢气氛保护;一次冷轧断带卷进罩式炉之前进行脱脂处理。脱脂处理的目的一方面是为了保持罩式炉内的还原性气氛避免硅钢被氧化,另一方面硅钢表面的油脂在罩式炉退火期间发生化学反应导致硅钢表层增碳增氮会恶化成品磁性能,所以需要进行脱脂处理。
17.所述中间退火的保温时间为22~24h,这样的保温时间内可保证整个钢卷的组织均匀使得最终成品的性能一致性提升,如果保温时间过短会导致钢卷均匀性差、而保温时间过长会导致成本增加。
18.二次冷轧至成品厚度0.35mm。
19.所述成品退火步骤中,退火温度为990~1010℃、保温时间为30~50s,退火过程中采用h2体积百分比为10~15%的n2和h2的混合气体保护。退火温度过低时,成品晶粒尺寸较小不利于铁损;退火温度过高时,可能会过烧导致混晶,既增加能耗又恶化铁损和磁感。退火保温时间过短,成品晶粒不均匀不利于铁损;退火保温时间过长,生产效率低下增加成本。氢气百分比过低,退火炉内还原性气氛不足,会使硅钢表面发生弱氧化恶化成品铁损,氢气百分比过高增加生产成本。
20.本发明还提供了一种高牌号无取向硅钢,所述高牌号无取向硅钢经本发明所述的生产方法生产得到,此方法可以在较低的生产成本下挽救高牌号无取向硅钢冷轧断带后的问题报废卷,降低直接报废的损失,且使得其成品磁性能满足p
1.5/50
=2.25~2.35w/kg、b
50
=1.66~1.67t,远超国标要求。
21.与现有技术相比,本发明的提供的一种高牌号无取向硅钢一次冷轧断带后的生产方法具有以下优点:
22.(1)本发明可以在较低的生产成本下挽救高牌号无取向硅钢冷轧断带后的问题报废卷,降低直接报废的损失;
23.(2)本发明生产的高牌号无取向硅钢成品磁性能p
1.5/50
=2.25~2.35w/kg、b
50
=1.66~1.67t,远超国标gb/t 2521.1-2016全工艺冷轧电工钢第1部分:晶粒无取向钢带(片))中的性能要求。
附图说明
24.图1为实施例1中生产得到的无取向硅钢的组织图;
25.图2为实施例1中生产得到的无取向硅钢的织构图;
26.图3为对比例2中生产得到的无取向硅钢的组织图;
27.图4为对比例2中生产得到的无取向硅钢的织构图。
具体实施方式
28.一种高牌号无取向硅钢一次冷轧断带后的生产方法,所述生产方法包括以下步骤:一次冷轧断带卷
→
中间退火
→
二次冷轧
→
成品退火
→
涂覆涂层
→
精整包装;
29.所述高牌号无取向硅钢中的si、mn、als的重量百分比为:3.0%≤si≤3.2%、0.1%≤mn≤0.5%、0.4%≤als≤1.0%;
30.所述一次冷轧断带卷经炼钢
→
连铸
→
铸坯加热
→
热轧
→
常化酸洗
→
一次冷轧得到,且一次冷轧过程中发生了断带;一次冷轧断带卷的厚度为1.00~1.70mm;
31.在进行一次冷轧之前,酸洗后的热轧钢带的厚度为2.20mm,其晶粒为均匀的再结晶铁素体组织,平均晶粒尺寸为90~100μm,具有较强的goss({110}《001》)织构、{112}《110》织构和γ织构。
32.所述中间退火采用罩式炉退火,罩式炉内全氢气氛保护,中间退火的温度为700~740℃,保温时间为22~24h;一次冷轧断带卷进罩式炉之前进行脱脂处理;
33.二次冷轧至成品厚度0.35mm;
34.所述成品退火步骤中,退火温度为990~1010℃、保温时间为30~50s,退火过程中采用h2体积百分比为10~15%的n2和h2的混合气体保护。
35.下面结合实施例对本发明进行详细说明。
36.实施例1
37.一种高牌号无取向硅钢一次冷轧断带后的生产方法,包括以下步骤:一次冷轧断带卷
→
中间退火
→
二次冷轧
→
成品退火
→
涂覆涂层
→
精整包装,具体为:采用常规流程(炼钢
→
连铸
→
铸坯加热
→
热轧
→
常化酸洗)获得的厚度为2.20mm的原料,其主合金成分重量百分比为3.0%si、0.5%mn、1.0%als。冷轧过程中出现断带导致无法继续生产,断带卷的厚度为1.00mm,将冷轧断带卷进行脱脂处理后采用罩式炉进行退火,罩退的热点温度为700℃,保温22h,罩式炉内全氢气氛保护;将完成罩退的钢卷再次冷轧至0.35mm的成品厚度,然后进行成品退火涂层,在成品退火工序中,退火温度为990℃、保温时间为30s,退火过程中采用h2体积百分比10%的n2和h2的混合气体保护。
38.采用上述生产方法,可以挽救高牌号无取向硅钢冷轧断带后的问题报废卷,降低直接报废的损失,且使得其成品磁性能p
1.5/50
=2.35w/kg、b
50
=1.66t,远超国标要求。
39.实施例2
40.一种高牌号无取向硅钢一次冷轧断带后的生产方法,包括以下步骤:一次冷轧断带卷
→
中间退火
→
二次冷轧
→
成品退火
→
涂覆涂层
→
精整包装,具体为:
41.采用常规流程(炼钢
→
连铸
→
铸坯加热
→
热轧
→
常化酸洗)获得的厚度为2.20mm的原料,其主合金成分重量百分比为3.0%si、0.5%mn、1.0%als。冷轧过程中出现断带导致无法继续生产,断带卷的厚度为1.70mm,将冷轧断带卷进行脱脂处理后采用罩式炉进行
退火,罩退的热点温度为740℃,保温24h,罩式炉内全氢气氛保护;将完成罩退的钢卷再次冷轧至0.35mm的成品厚度,然后进行成品退火涂层,在成品退火工序中,退火温度为1010℃、保温时间为50s,退火过程中采用h2体积百分比15%的n2和h2的混合气体保护。
42.采用上述生产方法,可以挽救高牌号无取向硅钢冷轧断带后的问题报废卷,降低直接报废的损失,且使得其成品磁性能p
1.5/50
=2.25w/kg、b
50
=1.67t,远超国标要求。
43.实施例3
44.一种高牌号无取向硅钢一次冷轧断带后的生产方法,包括以下步骤:一次冷轧断带卷
→
中间退火
→
二次冷轧
→
成品退火
→
涂覆涂层
→
精整包装,具体为:
45.采用常规流程(炼钢
→
连铸
→
铸坯加热
→
热轧
→
常化酸洗)获得的厚度为2.20mm的原料,其主合金成分重量百分比为3.2%si、0.1%mn、0.4%als。冷轧过程中出现断带导致无法继续生产,断带卷的厚度为1.00mm,将冷轧断带卷进行脱脂处理后采用罩式炉进行退火,罩退的热点温度为700℃,保温24h,罩式炉内全氢气氛保护;将完成罩退的钢卷再次冷轧至0.35mm的成品厚度,然后进行成品退火涂层,在成品退火工序中,退火温度为1010℃、保温时间为30s,退火过程中采用h2体积百分比15%的n2和h2的混合气体保护。
46.采用上述生产方法,可以挽救高牌号无取向硅钢冷轧断带后的问题报废卷,降低直接报废的损失,且使得其成品磁性能p
1.5/50
=2.31w/kg、b
50
=1.66t,远超国标要求。
47.实施例4
48.一种高牌号无取向硅钢一次冷轧断带后的生产方法,包括以下步骤:一次冷轧断带卷
→
中间退火
→
二次冷轧
→
成品退火
→
涂覆涂层
→
精整包装,具体为:
49.采用常规流程(炼钢
→
连铸
→
铸坯加热
→
热轧
→
常化酸洗)获得的厚度为2.20mm的原料,其主合金成分重量百分比为3.2%si、0.1%mn、0.4%als。冷轧过程中出现断带导致无法继续生产,断带卷的厚度为1.70mm,将冷轧断带卷进行脱脂处理后采用罩式炉进行退火,罩退的热点温度为740℃,保温24h,罩式炉内全氢气氛保护;将完成罩退的钢卷再次冷轧至0.35mm的成品厚度,然后进行成品退火涂层,在成品退火工序中,退火温度为990℃、保温时间为50s,退火过程中采用h2体积百分比15%的n2和h2的混合气体保护。
50.采用上述生产方法,可以挽救高牌号无取向硅钢冷轧断带后的问题报废卷,降低直接报废的损失,且使得其成品磁性能p
1.5/50
=2.28w/kg、b
50
=1.67t,远超国标要求。
51.对比例1
52.与实施例1的不同之处在于罩退前不脱脂,其成品磁性能p
1.5/50
=2.42w/kg、b
50
=1.64t,铁损和磁感均较差。
53.对比例2
54.与实施例1的不同之处在于罩退温度为670℃,其成品磁性能p
1.5/50
=2.47w/kg、b
50
=1.60t,铁损和磁感均较差(特别是磁感),不满足国标要求的b
50
≥1.62t。
55.对比例3
56.与实施例2的不同之处在于罩退前不脱脂,其成品磁性能p
1.5/50
=2.39w/kg、b
50
=1.64t,铁损和磁感均变差。
57.对比例4
58.与实施例2的不同之处在于罩退温度为760℃,其成品磁性能p
1.5/50
=2.33w/kg、b
50
=1.65t,由于罩退温度过高使得二次冷轧前的晶粒较粗大,不利于二次冷轧的顺利进行,
本对比例在二次冷轧的过程中发生了断带。
59.对比例5
60.与实施例1的不同之处在于罩退时的保温时间为18h,其成品磁性能最佳值为p
1.5/50
=2.37w/kg、b
50
=1.66t,但由于罩退保温时间较短导致二次冷轧前的组织均匀性较差,二次冷轧时出现轧机震动且成品磁性能整卷波动大。
61.对比例6
62.与实施例4的不同之处在于罩退时的保温时间为18h,成品退火保温时间为30s,其成品磁性能最佳值为p
1.5/50
=2.35w/kg、b
50
=1.66t,但由于罩退保温时间较短导致二次冷轧前的组织均匀性较差,二次冷轧时出现轧机震动,同时成品退火保温时间也较短,最终成品磁性能整卷波动大。
63.对比例7
64.与实施例4的不同之处在于成品退火的温度为1030℃,其成品磁性能p
1.5/50
=2.32w/kg、b
50
=1.64t,铁损和磁感均变差。
65.对比例8
66.与实施例4的不同之处在于成品退火的温度为970℃,其成品磁性能p
1.5/50
=2.41w/kg、b
50
=1.65t,铁损和磁感均变差。
67.上述各实施例及对比例的主要生产工艺参数及成品高牌号无取向硅钢的性能如表1所示。
[0068][0069]
实施例1、对比例2生产得到的无取向硅钢的组织图、织构图如图1-4所示;从图1-2中可以看出,实施例1生产得到的无取向硅钢成品的成品的晶粒均匀,平均晶粒尺寸达到
108μm,出现了一定强度的对磁性能有利的goss织构;从图3-4中可以看出,对比例2生产得到的无取向硅钢成品的晶粒尺寸均匀性较差,平均晶粒尺寸为96μm,对磁性能不利的γ织构通道尚未完全消失。
[0070]
上述参照实施例对一种高牌号无取向硅钢一次冷轧断带后的生产方法进行的详细描述,是说明性的而不是限定性的,可按照所限定范围列举出若干个实施例,因此在不脱离本发明总体构思下的变化和修改,应属本发明的保护范围之内。