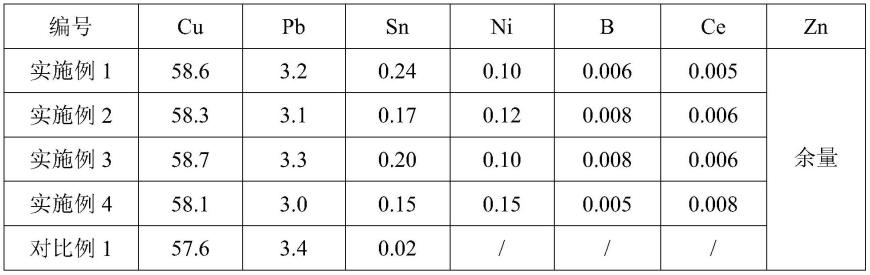
1.本发明属于铜合金技术领域,具体涉及一种黄铜合金及其制备方法。
背景技术:2.铅黄铜因含有一定量的铅,游离态的铅质点分布于基体中,有较强的润滑和减磨作用,使合金具备极高的可切削性能,机械加工时切屑易碎,制成的工件表面光洁。因此铅黄铜以其良好的易切削和易加工成型特性,广泛用于加工制备成各种高精密零件。其中在车载镜筒领域,对材料的综合性能提出了更高的要求。因镜筒生产加工对于表面精度要求极高,且后续加工需进行发黑染色处理,同时在使用过程中需具备一定抗腐蚀性能,因此所使用的铅黄铜原材料需具备优异的切削性能、发黑染色性能和耐腐蚀性能。
3.其中,耐腐蚀性能包含耐盐雾腐蚀性能和耐应力腐蚀性能。一般合格的车载镜筒产品经发黑处理后需进行中性盐雾测试,连续腐蚀时间超过96h后表面不出现腐蚀斑点为合格。发黑工艺是一种化学表面处理手段,使金属表面产生一层氧化膜,以达到隔绝空气和防腐防锈的目的。发黑工艺主要与铜合金成分添加元素、发黑面表面粗糙度、组织特征等因素有关,因此车载镜筒类产品的耐盐雾腐蚀性能一方面与原材料的耐腐蚀性能相关联,另一方面材料表层发黑效果好坏也是重要因素。
4.目前,车载镜筒产品一般选用c3604系列铅黄铜为原材料,c3604系列其铜含量低,铅含量高,虽切削性能优异,成本低廉,但耐腐蚀性能较差,经过发黑染色处理后无法稳定达到盐雾96h不出现腐蚀斑点的要求。同时由于材料zn含量高,组织结构中β相比例值高,材料耐应力腐蚀性能一般。若通过常规热处理工艺降低和消除应力腐蚀,高温软化退火后β相等易腐蚀相数量大幅度减小会降低发黑染色效果,同时材料切削性能降低,降低材料车削后表面粗糙度,表面粗糙度低会影响发黑膜的附着效果。
5.因此针对上述问题,需提供一种综合性能优异的材料,以满足车载镜筒加工使用要求。
技术实现要素:6.本发明所要解决的第一个技术问题是提供一种易切削、具有优异耐腐蚀性能的同时利于后续发黑染色的黄铜合金。
7.本发明所要解决的第二个技术问题是提供一种黄铜合金的制备方法。
8.本发明解决第一个技术问题所采用的技术方案为:一种黄铜合金,其特征在于:该黄铜合金的质量百分比组成为,cu:58.0~59.0wt%;pb:3.0~3.6wt%;sn:0.1~0.3wt%;ni:0.05~0.2wt%;b:0.001~0.01wt%,ce:0.001~0.01wt%,余量为zn。
9.cu的含量为基体相的最主要决定因素,影响材料最终的切削性能、耐腐蚀性以及后续的发黑染色性能。若cu含量低于下限58%,易造成β相比例偏高,虽然利于后续发黑染色,但不利于提高材料耐应力腐蚀和耐盐雾腐蚀性能。若cu含量高于上限59%,则造成α相比例偏高,利于提高材料耐应力腐蚀和耐盐雾腐蚀性能,但不利于提高材料的切削性能。
10.控制pb含量在3.0~3.6%范围,目的为提高材料切削性能,满足转速4000r/min以上的高速车床加工使用要求。加工后零件表面粗糙度低,光滑度高,在一定程度上也有利于改善材料发黑染色效果。同时pb以软质点的形式分布于晶界中,有利于阻断应力通道形成,提高材料耐应力腐蚀性能。若pb含量过高,则易恶化材料冷热加工性能。
11.加入一定量ni元素目的为改善材料耐盐雾腐蚀及耐应力腐蚀性能。
12.加入一定量sn元素,一方面有利于提高材料强度和改善切削性能,另一方面,促进γ相形成,一定程度上阻断腐蚀通道的形成,提高材料的耐盐雾腐蚀性能。
13.加入一定量b元素,目的为起到细化晶粒的作用,从而提高晶粒分布均匀性。一方面能够提高pb颗粒分布数量,改善切削性能。另一方面通过变形加工后能够使α相之间的结合力提高,改善材料的耐盐雾腐蚀和耐应力腐蚀性能。b含量过高,会降低材料加工塑性,b含量过低,晶粒细化效果不明显,难以达到上述改善效果。
14.加入一定量ce元素,一方面能够起到除杂、净化作用,减少夹杂弱化晶界的可能。另一方面ce能够改善黄铜发黑染色效果,增加发黑膜与黄铜基体之间的粘合附着力,有效避免发黑膜与黄铜基体之间发生脱落的风险。同时有利于增加发黑膜层结构致密性。实现良好的发黑染色效果能够对车削后的零件表面形成良好保护,是实现良好耐盐雾腐蚀性能的重要因素之一。ce元素添加过高,改善效果无法进一步提升,同时降低材料塑性。ce元素添加过低,则上述改善效果不明显。
15.作为优选,该黄铜合金的微观组织包括基体相以及分散在基体相中的γ相以及pb颗粒,其中,所述基体相占总相组成面积含量的95%以上,所述基体相由α相和β相组成,所述β相占总相面积含量的5~15%,所述γ相占总相面积含量的0.5~2%。
16.基体相由α相和β相组成,α相的具有良好耐腐蚀性能,β相作为易腐蚀相能够促进与发黑剂发生化学反应形成致密的氧化发黑膜,为实现耐腐与发黑效果相平衡,所述基体相占总相组成面积含量的95%以上,所述β相占总相面积含量的5~15%。
17.γ相与β相作为易腐蚀相能够促进与发黑剂发生化学反应形成致密的氧化发黑膜。当材料同时存在β相与γ相时,发黑效果更佳优异。在γ相比例达到0.5%以上,且β相比例达到5%以上时,能够达到良好的发黑染色效果。若γ与β相比例过高,则不利于改善材料耐腐蚀性能和加工塑性提升。因此优选控制γ相比例在0.5~2%范围,β相比例在5~15%范围。因此达到上述组织特征能够促进与发黑剂发生化学反应形成致密的氧化发黑膜。
18.作为优选,所述α相晶粒的平均尺寸为5~12μm,γ相晶粒的平均尺寸为0.1~1μm,1mm2单位面积pb颗粒数20000~28000个。使得合金同时具备良好切削性能,同时有利于提升发黑染色效果。
19.本发明解决第二个技术问题所采用的技术方案为:一种黄铜合金的制备方法,其特征在于:包括以下制备步骤:
20.1)熔炼:按所需成分进行配比,熔炼温度控制在1000~1100℃;
21.2)铸造:采用水平连铸方式拉铸铸锭,其中,牵引速率50~100mm/min,牵引节距2~10mm,反推长度:0.5~2.0mm,反推时间:0.1~0.5s,冷却水压力:1.0~2.0mpa,冷却水进水温度:10~30℃,出水温度:20~40℃,铸造温度控制在950~1050℃;
22.3)挤压:挤压前对铸锭进行加热,将铸锭分段加热,铸锭自头部到尾部的分段加热温度逐渐增高,相邻段的温度差值控制在5~15℃,铸锭加热温度控制在620~700℃,升温
时间60~120min,到达加热温度后保温30~60min,挤压速度10~25mm/s,挤压比50~280,得到挤压坯;
23.4)退火:退火分三阶段进行,第一阶段退火温度为320~400℃,保温30~60min;第二阶段退火温度450~500℃,保温50~120min;第三阶段对挤压坯进行冷却处理,控制冷却速度在60~100℃/min;
24.5)酸洗;将退火后的坯料置于酸洗池进行酸洗处理;
25.6)联合拉拔:拉拔加工率控制在10~15%,拉拔速率控制在40~80m/min,得到棒材;
26.7)去应力退火:将棒材置于气氛保护箱式炉中进行去应力退火,退火温度200~280℃,保温时间2~6h;
27.8)矫直。
28.上述步骤1)熔炼工序中,控制熔炼温度在1000~1100℃范围,在保证理想熔炼效率前提下避免zn元素过度挥发,实现zn元素损耗量控制在0.01%/min以下。
29.上述步骤3)挤压工序中,将铸锭分段加热,铸锭自头部到尾部的分段加热温度逐渐增高,由于挤压过程伴随铸锭温度降低,且挤压时间越长,铸锭温度下降越多,一根均匀受热的铸锭一般头部的实际挤压温度高于尾部,因此,保持铸锭自头部到尾部的分段加热温度逐渐增高,利于提高挤压坯料的性能均匀性,相邻段的温度差值控制在5~15℃,结合挤压速度控制在10~25mm/s,实现了挤压后各段挤压坯料性能均匀性良好,挤压坯硬度hv差值控制在10hv以内,晶粒度差值控制在5μm以内,β相比例差值在5%以内,利于提高材料组织性能均匀性,控制铸锭升温时间60~120min范围,有利于使铸锭均匀受热升温,避免出现里外受热不均的现象。
30.上述步骤4)退火工序中第一阶段退火为预升温阶段,一方面使挤压坯均匀受热,另一方面降低晶粒长大的趋势,保持良好的组织均匀性。第二阶段退火控制温度在450~500℃有利于γ相充分析出。若温度提高,pb粒子易发生聚集,影响材料切削性能,同时促进β相转变为α相。第三阶段为冷却过程,快速冷却目的为达到预期的组织特征。若采用自然冷却或慢速冷却,易导致圈线坯料内外冷却不均匀。若冷却过快,则会形成残余应力,降低坯料的加工塑性。
31.上述步骤7)去应力退火工序目的为消除棒材拉拔后产生的残余应力,从而有效改善材料耐应力腐蚀性能。进行去应力退火后,棒材轴向和周向残余应力值有效控制在60mpa以内。残余应力的降低有利于后续矫直工序的进行,提高矫直效率和质量。
32.作为优选,所述步骤2)中,铸锭中尺寸>100μm的α相晶粒占总α相面积含量的20%以下,尺寸<25μm的α相晶粒占总α相面积含量的50~80%,β相占总相面积含量的10~30%。
33.作为优选,所述步骤3)中,将铸锭自头部到尾部平分成头部、中部以及尾部三段,头部与中部的温度差值控制在5~15℃,中部与尾部的温度差值控制在5~15℃。
34.作为优选,所述步骤6)中,拉拔模具参数为:进口弧度15~20
°
,出口弧度20~45
°
,定径带长度5~8mm。同时设定合适的拉拔加工率和拉拔速度,保证成品棒材各部位应力分布均匀且直线度良好。合理的拉拔参数有利于达到理想的产品拉拔后直度,拉拔后直线度良好有利于后续矫直工序进行。最终成品的直线度良好是获得良好切削效果的关键因素,
经切削加工后表面粗糙度低且更光滑平整,有利于提升后续发黑处理效果,在此条件下形成的氧化发黑膜能够更好地平整附着在铜材基体表面。直线度有效控制在1mm/m以内,达到后续矫直工序的加工要求。若直度不佳,去应力退火后进行矫直时,棒材易发生甩动,存在严重安全影响,同时会降低成品棒材的表面品质。拉拔后α相晶粒尺寸降低,分布于晶界pb粒子数提升。
35.与现有技术相比,本发明的优点在于:通过控制黄铜合金中添加元素以及含量,使材料兼具良好切削性能,发黑染色性能,耐盐雾、应力腐蚀性能,实现满足车载镜筒的加工使用要求,该黄铜合金的切削性能优异,材料经过发黑处理后,满足中性盐雾96h不出现腐蚀斑点和28%氨水氨熏72h不出现应力裂纹。
附图说明
36.图1为本发明实施例1的金相组织照片。
37.图2为本发明对比例的金相组织照片。
具体实施方式
38.以下结合附图实施例对本发明作进一步详细描述。
39.本发明提供4个实施例和1个对比例,具体成分见表1。
40.实施例1
41.1)熔炼:按所需成分进行配比,熔炼温度控制在1030℃。
42.2)铸造:采用水平连铸方式拉铸毛坯,其中牵引速率为60mm/min,牵引节距为7mm,反推长度:1.0mm,反推时间:0.5s,冷却水压力:2.0mpa,冷却水进水温度:20~30℃,出水温度:30~40℃,铸造温度:1000℃;得到铸锭规格为φ250mm,长度1000mm。
43.3)挤压:挤压前对铸锭进行加热,将铸锭自头部到尾部平分成头部、中部以及尾部三段,头部加热温度640℃,中部加热温度650℃,尾部加热温度660℃。铸锭升温时间80min,保温时间60min。铸锭完成加热后进行挤压,挤压速度22mm/s,挤压规格φ16mm,采用双孔挤压方式盘圆收线,挤压比244。
44.4)退火:将挤压坯置于连续在线退火炉中进行退火处理,退火分三阶段进行,第一阶段退火温度为350℃,保温40min,第二阶段退火温度480℃,保温90min,第三阶段对坯料进行冷却处理,控制冷却速度80℃/min。
45.5)酸洗:将退火后的坯料置于酸洗池进行酸洗处理。
46.6)联合拉拔:将酸洗后的坯料置于联合拉拔设备进行拉拔加工,拉拔模具参数为:进口弧度18
°
,出口弧度40
°
,定径带长度6mm,拉拔加工率12%,拉拔速率50m/min,得到φ15mm棒材,棒材定尺长度2.5m。
47.7)去应力退火:将拉拔后的棒材置于气氛保护箱式炉中进行去应力退火,退火温度250℃,保温时间4h。
48.8)矫直:使用辊矫直设备对棒材进行矫直处理。
49.实施例2
50.1)熔炼:按所需成分进行配比,熔炼温度控制在1050℃。
51.2)铸造:采用水平连铸方式拉铸毛坯,其中牵引速率为60mm/min,牵引节距为7mm,
反推长度:1.0mm,反推时间:0.5s,冷却水压力:2.0mpa,冷却水进水温度:20~30℃,出水温度:30~40℃,铸造温度:1000℃;得到铸锭规格为φ250mm,长度1000mm。
52.3)挤压:挤压前对铸锭进行加热,将铸锭自头部到尾部平分成头部、中部以及尾部三段,头部加热温度640℃,中部加热温度655℃,尾部加热温度670℃。铸锭升温时间80min,保温时间60min。铸锭完成加热后进行挤压,挤压速度20mm/s,挤压规格φ16mm,采用双孔挤压方式盘圆收线,挤压比244。
53.4)退火:将挤压坯置于连续在线退火炉中进行退火处理,退火分三阶段进行,第一阶段退火温度为370℃,保温30min,第二阶段退火温度480℃,保温90min,第三阶段对坯料进行冷却处理,控制冷却速度80℃/min。
54.5)酸洗:将退火后的坯料置于酸洗池进行酸洗处理。
55.6)联合拉拔:将酸洗后的坯料置于联合拉拔设备进行拉拔加工,拉拔模具参数为:进口弧度18
°
,出口弧度40
°
,定径带长度6mm,拉拔加工率12%,拉拔速率50m/min,得到φ15mm棒材,棒材定尺长度2.5m。
56.7)去应力退火:将拉拔后的棒材置于气氛保护箱式炉中进行去应力退火,退火温度270℃,保温时间3h。
57.8)矫直:使用辊矫直设备对棒材进行矫直处理。
58.实施例3
59.1)熔炼:按所需成分进行配比,熔炼温度控制在1050℃。
60.2)铸造:采用水平连铸方式拉铸毛坯,其中牵引速率为80mm/min,牵引节距为8mm,反推长度:1.0mm,反推时间:0.5s,冷却水压力:2.0mpa,冷却水进水温度:20~30℃,出水温度:30~40℃,铸造温度:1000℃;得到铸锭规格为φ250mm,长度1000mm。
61.3)挤压:挤压前对铸锭进行加热,将铸锭自头部到尾部平分成头部、中部以及尾部三段,头部加热温度650℃,中部加热温度660℃,尾部加热温度670℃。铸锭升温时间90min,保温时间60min。铸锭完成加热后进行挤压,挤压速度15mm/s,挤压规格φ20mm,采用双孔挤压方式盘圆收线,挤压比156。
62.4)退火:将挤压坯置于连续在线退火炉中进行退火处理,退火分三阶段进行,第一阶段退火温度为330℃,保温60min,第二阶段退火温度490℃,保温90min,第三阶段对坯料进行冷却处理,控制冷却速度70℃/min。
63.5)酸洗:将退火后的坯料置于酸洗池进行酸洗处理。
64.6)联合拉拔:将酸洗后的坯料置于联合拉拔设备进行拉拔加工,拉拔模具参数为:进口弧度18
°
,出口弧度40
°
,定径带长度6mm,拉拔加工率14%,拉拔速率40m/min,得到φ18.5mm棒材,棒材定尺长度2.5m。
65.7)去应力退火:将拉拔后的棒材置于气氛保护箱式炉中进行去应力退火,退火温度260℃,保温时间4h。
66.8)矫直:使用辊矫直设备对棒材进行矫直处理。
67.实施例4
68.1)熔炼:按所需成分进行配比,熔炼温度控制在1050℃。
69.2)铸造:采用水平连铸方式拉铸毛坯,其中牵引速率为70mm/min,牵引节距为7mm,反推长度:1.0mm,反推时间:0.5s,冷却水压力:2.0mpa,冷却水进水温度:20~30℃,出水温
度:30~40℃,铸造温度:1000℃;得到铸锭规格为φ250mm,长度1000mm。
70.3)挤压:挤压前对铸锭进行加热,将铸锭自头部到尾部平分成头部、中部以及尾部三段,头部加热温度635℃,中部加热温度650℃,尾部加热温度665℃。铸锭升温时间70min,保温时间60min。铸锭完成加热后进行挤压,挤压速度18mm/s,挤压规格φ20mm,采用双孔挤压方式盘圆收线,挤压比156。
71.4)退火:将挤压坯置于连续在线退火炉中进行退火处理,退火分三阶段进行,第一阶段退火温度为350℃,保温45min,第二阶段退火温度480℃,保温90min,第三阶段对坯料进行冷却处理,控制冷却速度70℃/min。
72.5)酸洗:将退火后的坯料置于酸洗池进行酸洗处理。
73.6)联合拉拔:将酸洗后的坯料置于联合拉拔设备进行拉拔加工,拉拔模具参数为:进口弧度18
°
,出口弧度40
°
,定径带长度6mm,拉拔加工率14%,拉拔速率40m/min,得到φ18.5mm棒材,棒材定尺长度2.5m。
74.7)去应力退火:将拉拔后的棒材置于气氛保护箱式炉中进行去应力退火,退火温度260℃,保温时间4h。
75.8)矫直:使用辊矫直设备对棒材进行矫直处理。
76.对比例1为普通c3604合金。
77.对得到的实施例和对比例进行力学性能和/或微观组织检测,具体检测指标和检测标准如下:
78.1)硬度hv5:gb/t 4340.1-2009金属材料维氏硬度试验第1部分:试验方法。
79.2)金相显微测试:ys/t 449-2002铜及铜合金铸造和加工制品显微组织检验方法。
80.3)切削指数:根据ys-t 647-2007《铜锌铋碲合金棒》附录b中切削性能检测方法进行评定,设c36000(hpb63-3)的切削指数为100%。
81.4)耐盐雾腐蚀性能:gb/t 10125-2021人造气氛腐蚀试验盐雾试验
82.5)耐应力腐蚀性能:jis h 3250:2015铜及铜合金棒和条残余应力氨熏试验法
83.6)发黑处理方式:使用h2so4+seo2发黑剂对铜棒表面进行发黑处理,发黑处理3min后用清水冲洗,快速干燥后用机油进行封闭处理。发黑膜越致密,说明发黑膜与铜基体之间的结合力越牢固,发黑效果更佳。发黑效果越好在一定程度上能够提高产品的耐盐雾腐蚀性能。
84.7)发黑膜层致密性评判:采用50g砝码包覆砂纸,然后对表面发黑后的黄铜样品来回摩擦,根据露出黄铜基体时所经过的摩擦次数说明膜层的耐磨性及与基体结合情况。
85.表1实施例和对比例成分/wt%
86.87.表2实施例中间阶段性能以及显微组织
[0088][0089]
表3实施例与对比例成品棒材显微组织性能
[0090][0091]
表4实施例与对比例成品棒材力学和耐腐蚀性能
[0092][0093]
表5实施例与对比例成品棒材发黑处理后发黑膜层致密性
[0094]
编号露出黄铜基体时所经过的摩擦次数发黑膜层致密性实施例1239好实施例2245好实施例3237好实施例4266好对比例198一般