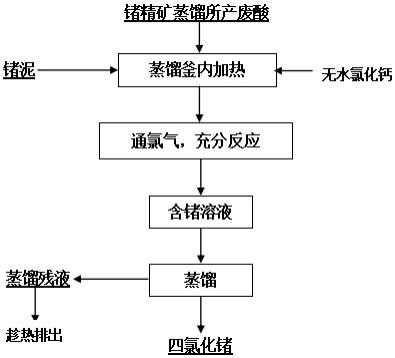
1.本发明申请型涉及工业固废处理技术领域,具体涉及一种利用锗精矿蒸馏废盐酸从锗泥中回收锗的方法。
背景技术:2.锗在半导体、航空航天测控、核物理探测、光纤通讯、红外光学、太阳能电池、化学催化剂、生物医学等领域都有广泛而重要的应用,对国防军工及国民经济意义重大,是一种重要的战略资源。其中,锗在红外光学领域的年需求量占锗消费量的20-30%左右,占据锗消费第一的位置。锗作为红外光学材料,具有红外折射率高,红外透过波段范围宽,吸收系数小、色散率低、易加工、闪光及腐蚀等优点,特别适用于军工及重大民用中的热成像仪与红外雷达及其他红外光学装置的窗口、透镜、棱镜与滤光片的材料。因此,锗常被用来制作红外成像镜头。在进行红外光学镜头加工时会产生一些锗泥,其主要成分为含锗金属颗粒和加工过程中所使用的辅料的混合物。锗是一种不可再生、非常稀缺的分散元素,经济价值较高,锗的回收尤其重要。但锗泥的粒度非常细,对其进行物理分离十分困难。所以需要对锗泥进行处理,回收其中的锗金属。
3.此外,锗精矿蒸馏时产生的废酸中含有盐酸(270-280(g/l))、氯化铁(18-22(g/l))等酸性氯化物混合溶液;若把废酸直接当作废料进行处理,不仅要花费处理成本,还浪费了废酸中的有价物质。
4.现有技术中有利用锗精矿蒸馏时产生的废酸从红外光学镜头加工产生的锗泥中回收锗的技术,但其存在以下技术缺陷:(1)蒸馏残液冷却后,有大量氯化亚铁晶体析出堵塞管道,可能造成生产不能正常进行。(2)四氯化锗为无色油状液体,遇水会立即发生分解,而废酸中成分复杂蒸馏时难免有水蒸汽混进四氯化锗的收集瓶内,造成四氯化锗产率不高。
技术实现要素:5.为解决或部分解决相关技术中存在的问题,本发明申请提供一种利用锗精矿蒸馏废盐酸从锗泥中回收锗的方法,针对当前废酸资源的浪费和锗泥中锗的回收利用等问题。利用本发明能充分利用废酸中的有价物质,降低生产成本,实现锗的有效回收。
6.本发明申请提供了利用锗精矿蒸馏废盐酸从锗泥中回收锗的方法,包括以下步骤a, 把锗泥和锗精矿蒸馏废盐酸按固液比1:10-15的比例混合加入蒸馏釜中,再加入适量无水氯化钙并加热蒸馏釜,控制反应温度为70-80℃,使锗泥中的锗与蒸馏废盐酸反应10-30min,转化为四氯化锗;b, a步骤完成后,通入气固比为3-5l/kg的氯气,充分搅拌混合,控制反应温度为85-90℃,将氯化亚铁再次氧化为氯化铁,在三价铁的催化作用下,进一步将锗泥中的锗氯化生成四氯化锗,反应时间10-20min;c, 最后将四氯化锗从溶液中蒸馏出来,并使用收集瓶收集蒸馏出四氯化锗气体。
7.进一步的,步骤a所述锗泥和锗精矿蒸馏废盐酸的固液比1:10或1:15。
8.进一步的,步骤a所述反应温度为80℃。
9.进一步的,步骤a所述蒸馏废盐酸反应的时间为30min。
10.进一步的,步骤b所述反应温度为90℃。
11.进一步的,步骤b所述反应时间为20min。
12.进一步的,所述无水氯化钙的质量为锗泥的10%。
13.进一步的,蒸馏工作完毕后保持釜内温度,并排出剩余物料即可。
14.应当理解的是,以上的一般描述和后文的细节描述仅是示例性和解释性的,并不能限制本发明申请。
15.本发明的有益技术效果:(1)本发明中整个工艺过程所消耗的原料主要为工业废料,实现了锗精矿蒸馏废酸的循环再利用,极大降低了生产成本,避免了资源浪费和环境污染;并且实现了稀散金属锗的回收,有良好的经济效益。
16.(2)在反应体系加入了无水氯化钙,既可以作为氯化反应的催化剂,使得锗尽可能多的氯化为四氯化锗,也可以作为吸水剂,去除反应体系中的水,避免四氯化锗遇水分解。
17.(3)在反应结束后,保持釜内温度,趁热排出废液,避免了废液降温后,大量氯化亚铁结晶析出堵塞管道。
附图说明
18.图1为本发明申请中利用锗精矿蒸馏废盐酸从锗泥中回收锗的方法的一个实施流程示意图。
具体实施方式
19.下面将参照附图更详细地描述本发明申请的可选实施方式。虽然附图中显示了本发明申请的可选实施方式,然而应该理解,可以以各种形式实现本发明申请而不应被这里阐述的实施方式所限制。相反,提供这些实施方式是为了使本发明申请更加透彻和完整,并且能够将本发明申请的范围完整地传达给本领域的技术人员。
20.在本发明申请使用的术语是仅仅出于描述特定实施例的目的,而非旨在限制本发明申请。在本发明申请和所附权利要求书中所使用的单数形式的“一种”、“所述”和“该”也旨在包括多数形式,除非上下文清楚地表示其他含义。还应当理解,本文中使用的术语“和/或”是指并包含一个或多个相关联的列出项目的任何或所有可能组合。
21.如图1,本发明申请提供了利用锗精矿蒸馏废盐酸从锗泥中回收锗的方法,包括以下步骤a, 把锗泥和锗精矿蒸馏废盐酸按固液比1:10-15的比例混合加入蒸馏釜中,再加入适量无水氯化钙并加热蒸馏釜,控制反应温度为70-80℃,使锗泥中的锗与蒸馏废盐酸反应10-30min,转化为四氯化锗;在反应体系加入了无水氯化钙,既可以作为氯化反应的催化剂,使得锗尽可能多的氯化为四氯化锗,也可以作为吸水剂,去除反应体系中的水,避免四氯化锗遇水分解。
22.b, a步骤完成后,通入气固比为3-5l/kg的氯气,充分搅拌混合,控制反应温度为
85-90℃,将氯化亚铁再次氧化为氯化铁,在三价铁的催化作用下,进一步将锗泥中的锗氯化生成四氯化锗,反应时间10-20min;c, 最后将四氯化锗从溶液中蒸馏出来,并使用收集瓶收集蒸馏出四氯化锗气体。
23.本发明回收锗资源的原理如下:(1)锗与三价铁在盐酸环境下加热发生化学反应产生四氯化锗,该过程所涉及的主要化学反应如下:(2)通过第一步反应后,废酸中的三价铁(fe
3+
)会转变为二价铁(fe
2+
),氯化铁生成氯化亚铁,锗生成四氯化锗;此时加入氯气(cl2)作为氧化剂把氯化亚铁再次氧化成为氯化铁,边通氯气边搅拌,控制反应温度85-90℃,一方面促进循环生成三价铁与锗反应,另一方面使锗泥中的锗尽可能的完全反应生成四氯化锗,并使四氯化锗(沸点:82-84℃)快速从溶液中蒸馏出来;该过程涉及的主要化学反应如下:在本发明申请的一种实施方式中,步骤a所述锗泥和锗精矿蒸馏废盐酸的固液比1:10或1:15。
24.在本发明申请的一种实施方式中,步骤a所述反应温度为80℃。
25.在本发明申请的一种实施方式中,步骤a所述蒸馏废盐酸反应的时间为30min。
26.在本发明申请的一种实施方式中,步骤b所述反应温度为90℃。
27.在本发明申请的一种实施方式中,步骤b所述反应时间为20min。
28.进一步的,所述无水氯化钙的质量为锗泥的10%。
29.进一步的,蒸馏工作完毕后保持釜内温度,并排出剩余物料即可。
30.为更清楚起见,下面通过以下实施例进行详细说明。
31.实施例1分别取锗精矿通过蒸馏后产生的废酸50l,锗泥5kg,进行3次试验。
32.实验一:取品位为85.22%的锗泥5kg,废酸50l,在蒸馏釜内进行加热,控制温度为70℃,反应10min,通氯气后控制温度为87℃,反应15min,最后蒸馏5h, 从溶液中蒸馏出四氯化锗(gecl4)并用收集瓶进行收集。
33.实验二:取品位为85.22%的锗泥5kg,废酸50l,在蒸馏釜内进行加热,控制温度为75℃,反应20min,通氯气后控制温度为87℃,反应15min,最后蒸馏5h, 从溶液中蒸馏出四氯化锗(gecl4)并用收集瓶进行收集。
34.实验三:取品位为85.22%的锗泥5kg,废酸50l,在蒸馏釜内进行加热,控制温度为80℃,反应30min,通氯气后控制温度为87℃,反应15min,最后蒸馏5h, 从溶液中蒸馏出四氯化锗(gecl4)并用收集瓶进行收集。
35.按上述工艺所得锗回收率如表1所示:表1实验结果
由实验结果可以看出,蒸馏釜内温度越高,反应时间越长,锗的回收率越大且大于91%。
36.实施例2分别取锗精矿通过蒸馏后产生的废酸50l,锗泥5kg,进行3次试验。
37.实验一:取品位为85.22%的锗泥5kg,废酸50l,在蒸馏釜内进行加热,控制温度为80℃,反应30min,通氯气后控制温度为85℃,反应10min,最后蒸馏5h, 从溶液中蒸馏出四氯化锗(gecl4)并用收集瓶进行收集。
38.实验二:取品位为85.22%的锗泥5kg,废酸50l,在蒸馏釜内进行加热,控制温度为80℃,反应30min,通氯气后控制温度为87℃,反应15min,最后蒸馏5h, 从溶液中蒸馏出四氯化锗(gecl4)并用收集瓶进行收集。
39.实验三:取品位为85.22%的锗泥5kg,废酸50l,在蒸馏釜内进行加热,控制温度为80℃,反应30min,通氯气后控制温度为90℃,反应20min,最后蒸馏5h, 从溶液中蒸馏出四氯化锗(gecl4)并用收集瓶进行收集。
40.按上述工艺所得锗回收率如表2所示:表2实验结果
由实验结果可以看出,通氯气后温度越高,反应时间越长,锗的回收率越大且大于91%。
41.实施例3分别取锗精矿通过蒸馏后产生的废酸150l,锗泥10kg,进行3次试验。
42.实验一:取品位为85.22%的锗泥10kg,废酸150l,在蒸馏釜内进行加热,控制温度为80℃,反应30min,通氯气后控制温度为85℃,反应10min,最后蒸馏5h, 从溶液中蒸馏出四氯化锗(gecl4)并用收集瓶进行收集。
43.实验二:取品位为85.22%的锗泥10kg,废酸150l,在蒸馏釜内进行加热,控制温度为80℃,反应30min,通氯气后控制温度为87℃,反应15min,最后蒸馏5h, 从溶液中蒸馏出四氯化锗(gecl4)并用收集瓶进行收集。
44.实验三:取品位为85.22%的锗泥10kg,废酸150l,在蒸馏釜内进行加热,控制温度为80℃,反应30min,通氯气后控制温度为90℃,反应20min,最后蒸馏5h, 从溶液中蒸馏出四氯化锗(gecl4)并用收集瓶进行收集。
45.按上述工艺所得锗回收率如表3所示:表3实验结果
由实验结果可以看出,增加废酸用量时,锗的回收率增加且大于92%。
46.实施例4分别取锗精矿通过蒸馏后产生的废酸150l,锗泥10kg,进行3次试验。
47.实验一:取品位为85.22%的锗泥10kg,废酸150l,在蒸馏釜内进行加热,控制温度为80℃,反应30min,通氯气后控制温度为85℃,反应10min,最后蒸馏5h, 从溶液中蒸馏出四氯化锗(gecl4)并用收集瓶进行收集。
48.实验二:取品位为85.22%的锗泥10kg,废酸150l,在蒸馏釜内进行加热,控制温度为80℃,反应30min,通氯气后控制温度为87℃,反应15min,最后蒸馏5h, 从溶液中蒸馏出四氯化锗(gecl4)并用收集瓶进行收集。
49.实验三:取品位为85.22%的锗泥10kg,废酸150l,在蒸馏釜内进行加热,控制温度为80℃,反应30min,通氯气后控制温度为90℃,反应20min,最后蒸馏5h, 从溶液中蒸馏出四氯化锗(gecl4)并用收集瓶进行收集。
50.按上述工艺所得锗回收率如表4所示:表4实验结果
由实验结果可以看出,增加废酸用量时,锗的回收率增加且大于92%。
51.实施例5分别取锗精矿通过蒸馏后产生的废酸50l,锗泥5kg,进行2次试验。
52.实验一:取品位为85.22%的锗泥5kg,废酸50l,在蒸馏釜内进行加热,控制温度为80℃,反应30min,通氯气后控制温度为90℃,反应20min,最后蒸馏5h, 从溶液中蒸馏出四氯化锗(gecl4)并用收集瓶进行收集。
53.实验二:取品位为85.22%的锗泥5kg,废酸50l,无水氯化钙0.5kg在蒸馏釜内进行加热,控制温度为80℃,反应30min,通氯气后控制温度为90℃,反应20min,最后蒸馏5h, 从溶液中蒸馏出四氯化锗(gecl4)并用收集瓶进行收集。
54.按上述工艺所得锗回收率如表5所示:表5实验结果由实验结果可以看出,在反应体系中加入无水氯化钙,锗的回收率增加且大于96%。
55.以上已经描述了本发明申请的各实施例,上述说明是示例性的,并非穷尽性的,并且也不限于所披露的各实施例。在不偏离所说明的各实施例的范围和精神的情况下,对于
本技术领域的普通技术人员来说许多修改和变更都是显而易见的。本文中所用术语的选择,旨在最好地解释各实施例的原理、实际应用或对市场中的技术的改进,或者使本技术领域的其它普通技术人员能理解本文披露的各实施例。