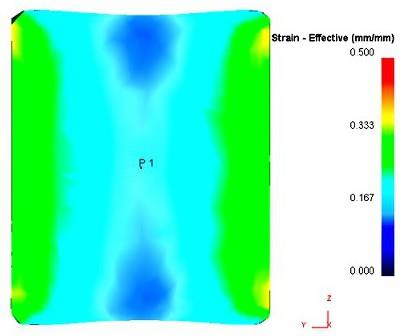
一种20mncr5齿轮钢及其轧制方法
1.技术领域
2.本发明涉及一种20mncr5齿轮钢及其轧制方法,属于冶金行业轧钢技术领域。
背景技术:3.20mncr5 钢在齿轮钢中属德标系列较高端的钢种,φ600mm连铸坯生产的φ200mm~ φ300mm的20mncr5齿轮钢棒材超声探伤合格率91.2%,通过探伤、解剖分析发现95%以上的超声探伤不合缺陷处无氧化、无脱碳层、存在自由表面特征,随着轧材规格减小,缺陷当量也随之减小,说明探伤不合是由于连铸坯中的缩孔在轧制过程中未焊合造成的。
4.目前,连铸坯为堆冷工艺,在步进梁式加热炉中加热时间短,加热速度快,开坯机轧制工艺中最大单道次压下量为90mm,最大压下率18%,并且轧制速度高,变形不能很好的渗透到芯部,芯部应变小,未把连铸坯中的残余缩孔缺陷有效焊合。
技术实现要素:5.本发明的目的是提供一种20mncr5齿轮钢及其轧制方法,能够改善轧材的低倍组织,使组织更加致密,提高超声探伤合格率,解决背景技术中存在的问题。
6.本发明的技术方案是:一种20mncr5齿轮钢,化学成分质量百分比为:c:0.17~0.22、si:0.20~0.40、mn:1.10~1.40、cr:1.00~1.30、p:≤0.025、s:≤0.035、cu:0.01~0.04、ni:0.01~0.10、mo:0.01~0.05,其余为fe和其它不可避免的杂质。
7.一种20mncr5齿轮钢轧制方法,包含连铸、加热、轧制、冷却,化学成分质量百分比为:c:0.17~0.22、si:0.20~0.40、mn:1.10~1.40、cr:1.00~1.30、p:≤0.025、s:≤0.035、cu:0.01~0.04、ni:0.01~0.10、mo:0.01~0.05,其余为fe和其它不可避免的杂质;连铸:连铸坯采用热装或缓冷工艺,采用热装时热装温度≥650℃,采用缓冷工艺时入缓冷坑温度≥650℃,出坑温度<200℃;加热:均热段温度1150~1260℃,出炉温度1240~1260℃;轧制:开坯机轧制温度1080~1180℃,连轧开轧温度980℃~1020℃,终轧温度>950℃;冷却:轧材入缓冷坑温度500~600℃,缓冷时间55h~72h。
8.所述加热:连铸坯热装时:热装温度≥650℃,预热区温度≤850℃,加热时间>9h;连铸坯冷装时:预热区温度≤700℃,加热时间>13h。
9.所述轧制:开坯机轧制9~11道次,第1~4道次压下率≥12%,第5~8道次平均压下率≥18%,并且两个单道次压下量不低于110mm;连轧轧制道次4~6道次,平均延伸系数大于1.13。
10.所述开坯机轧制的速度为1.0~1.5m/s。
11.所述连铸坯规格为φ600mm,成品规格为φ200mm~ φ300mm。
12.本发明的有益效果是:(1)优化了连铸坯缓冷和加热工序,降低了热应力和组织转变应力的叠加;(2)提高了最大单道次的压下量,降低了轧制速度,增加了芯部的变形渗透;(3)有效提高了大规格20mncr5齿轮钢超声探伤合格率,满足gb/t4162 b级的探伤合格率由原来的91.2%提高到99.1%,并且还可以改善轧材的低倍组织,使组织更加致密。
附图说明
13.图1为不同压下量时芯部的等效应变;图2为不同轧制速度时芯部的等效应变;图3为轧制速度为1.0m/s时等效应变云图;图4为轧制速度为3.0m/s时的等效应变云图。
具体实施方式
14.以下结合附图,通过实例对本发明作进一步说明。
15.参照附图1-4,一种20mncr5齿轮钢,化学成分质量百分比为:c:0.17~0.22、si:0.20~0.40、mn:1.10~1.40、cr:1.00~1.30、p:≤0.025、s:≤0.035、cu:0.01~0.04、ni:0.01~0.10、mo:0.01~0.05,其余为fe和其它不可避免的杂质。
16.一种20mncr5齿轮钢轧制方法,包含连铸、加热、轧制、冷却,化学成分质量百分比为:c:0.17~0.22、si:0.20~0.40、mn:1.10~1.40、cr:1.00~1.30、p:≤0.025、s:≤0.035、cu:0.01~0.04、ni:0.01~0.10、mo:0.01~0.05,其余为fe和其它不可避免的杂质;连铸:连铸坯采用热装或缓冷工艺,采用热装时热装温度≥650℃,采用缓冷工艺时入缓冷坑温度≥650℃,出坑温度<200℃;加热:均热段温度1150~1260℃,出炉温度1240~1260℃;轧制:开坯机轧制温度1080~1180℃,连轧开轧温度980℃~1020℃,终轧温度>950℃;冷却:轧材入缓冷坑温度500~600℃,缓冷时间55h~72h。
17.所述加热:连铸坯热装时:热装温度≥650℃,预热区温度≤850℃,加热时间>9h;连铸坯冷装时:预热区温度≤700℃,加热时间>13h。
18.所述轧制:开坯机轧制9~11道次,第1~4道次压下率≥12%,第5~8道次平均压下率≥18%,并且两个单道次压下量不低于110mm;连轧轧制道次4~6道次,平均延伸系数大于1.13。
19.所述开坯机轧制的速度为1.0~1.5m/s。
20.所述连铸坯规格为φ600mm,成品规格为φ200mm~ φ300mm。
21.实施例1:φ600mm连铸坯轧制φ300mm,按照以下步骤进行:第一步:连铸坯采用热送或者缓冷工艺,冶炼成分如下:单位,wt%,c:0.17~0.22、si:0.20~0.40、mn:1.10~1.40、cr:1.00~1.30、p:≤0.025、s:≤0.035、cu:0.01~0.04、ni:0.01~0.10、mo:0.01~0.05。
22.连铸坯入缓冷坑温度≥650℃,出坑温度<200℃,降低冷却速度,减小连铸坯芯部
的拉应力,cu、ni、mo成分按照下线控制。
23.第二步:φ600mm连铸坯热装或者冷装的连铸坯送入步进式加热炉加热,加热工艺如下:第三步:经过高压水除鳞机除掉连铸坯表面的氧化铁皮,除鳞压力250bar~280bar。
24.第四步:开坯机开轧温度1150℃~1180℃。开坯机轧制工艺如下:轧制速度在1.0~1.5m/s之间,5~8道次压下率不小于10%,并且最少有2道次的单道次大压下量不小于110mm,当最大压下时轧制速度为1.0m/s。
25.第五步:开坯后的中间坯,在液压剪切头后输送至连轧机组,轧制4道次,连轧开轧温度980℃~1020℃,轧制工艺规程如下:第六步:金属锯锯切后经过步进式冷床冷却,缓冷入坑温度500℃~550℃,缓冷时间72h,出坑温度<200℃。
26.第七步:出坑后人工摊检,并进行超声波探伤。满足gb/t4162 b级的探伤合格率为96.1%。
27.实施例2:φ600mm连铸坯轧制φ200mm,按照以下步骤进行:第一步:连铸坯热送或者缓冷工艺,冶炼成分如下:单位,wt%,c:0.17~0.22、si:0.20~0.40、mn:1.10~1.40、cr:1.00~1.30、p:≤0.025、s:≤0.035、cu:0.01~0.04、ni:
0.01~0.10、mo:0.01~0.05。
28.连铸坯入缓冷坑温度≥650℃,出坑温度<200℃,降低冷却速度,减小连铸坯芯部的拉应力。cu、ni、mo成分按照下线控制。
29.第二步:600圆连铸坯热装或者冷装的连铸坯送入步进式加热炉加热,加热工艺如下:第三步:经过高压水除鳞机除掉连铸坯表面的氧化铁皮,除鳞压力250bar~280bar。
30.第四步:开坯机开轧温度1150℃~1180℃。开坯机轧制工艺如下:轧制速度在1.0~1.5m/s之间,5~8道次压下率不小于10%,并且最少有2道次的单道次大压下量不小于110mm,当最大压下时轧制速度为1.0m/s。
31.第六步:开坯后的中间坯,在液压剪切头后输送至连轧机组,轧制6道次,连轧开轧温度980℃~1020℃,终轧温度>950℃,轧制工艺规程如下:第七步:金属锯锯切后经过步进式冷床冷却,缓冷入坑温度500℃~550℃,缓冷时
间72h,出坑温度<200℃。
32.第八步:出坑后人工摊检,并进行超声波探伤。满足gb/t4162 b级的探伤合格率为99.8%。
33.参照附图1-4,选用六面体单元进行变形体的离散,分别对比了压下量和轧制速度对轧材芯部应变的影响。由图1可见,相同条件下,当压下量为120mm和60mm时,芯部的等效应变分别为0.314、0.144。由图2 可见,相同条件下,当轧制速度分别为1.0m/s和3.5m/s时芯部应变分别为0.071、0.103。结果表明,提高单道次压下量和降低轧制速度可以增加芯部的等效应变,对芯部缺陷的焊合是非常有利的。