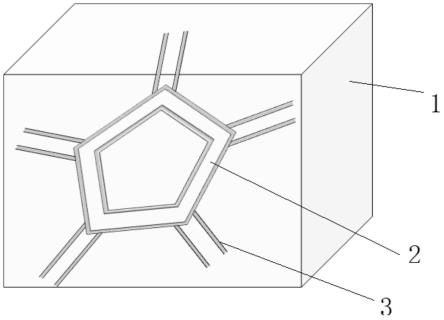
1.本发明涉及金属复合材料技术领域,特别是指一种金刚石中空管道泡沫增强骨架铝基复合材料及其制备方法。
背景技术:2.随着科学技术的发展,金刚石应用于航空航天、军事、工业、国民生产等诸多领域,高功率、高集成度、轻量化电子设备已经成为研发的方向,同时伴随着散热问题却成为制约这些行业发展的重要因素。在集成化微小电子器件材料和半导体芯片之间的热膨胀系数不匹配,电子器件在工作时产生大量的热造成器件之间的应力问题,极其影响大功率通信及导航卫星、定向高能武器以及宽禁带半导体雷达等高功率等先进设备的工作稳定性和使用寿命。因此,高热导率、低膨胀系数和轻量化是选择材料的必要条件。
3.金刚石拥有优异的热导率(2200w/mk)和极低的膨胀系数;多壁碳纳米管具有很高的热导率(3000w/mk)和力学强度还有超高表体比;在常见的金属中,铝有较高的热导率(237w/mk),低密度,耐腐蚀,易加工等优点;金刚石与碳纳米管的单一相或混合相作为增强相与金属复合相,可获得更为优异的导热、导电和力学性能,满足不同领域对导热、导电和力学性能的需求。
4.目前,us6815052b2是将金刚石薄膜沉积到sic泡沫上;cn 105779804 a是将金刚石沉积到铜泡沫上,形成三维立体结构,在此基础上生长碳材料(碳纳米管、石墨烯等)再与金属(铝、铜、银、镁、钛等)结合,均取得一定效果,但是以上均未去除泡沫衬底并且每层物质之间存在缓冲层这样会增加界面热阻,对热传导和热散失的效果大打折扣。
技术实现要素:5.本发明要解决的技术问题是提供一种金刚石中空管道泡沫增强骨架铝基复合材料及其制备方法。其中包括金刚石中空管道泡沫骨架、碳纳米管生长在中空金刚石管道内部、中空金刚石管道外部、中空金刚石管道内外部,这种复合结构的中空金刚石管道网状薄膜犹如人体血管一样遍布复合体,碳纳米管(热导率,3000-3500w/mk)宛如人体神经纤维一样伸入每一处基体中,大大增加接触热源面积,提高导热性能。
6.本发明的金刚石-碳纳米管骨架再与铝基相结合时不需要使用过渡层,这是由于使用sps设备具有高温高压技术功能,在高温高压条件下diamond-cnts与金属铝之间的空隙降低以及结合效果提高,并且高温条件下,金刚石和cnts会与金属铝产生al4c3化合物,即金刚石与cnts之间为化学结合,降低了界面热阻;而传统结构中通常使用过渡层,目的就是为了金刚石和cnts与金属铝之间的结合性能要好,减弱物理结合,增强化学结合,降低界面热阻,但是使用过渡层定会引入新的金属原子,改变晶格参数,影响晶格振动,造成声子传输受阻,但反而增加了界面热阻。本发明制成优异的热管理材料作为热冗余或散热器件,可以协调逐渐增大的功率密度与周围环境的温差,实现高效散热并降低与芯片材料热膨胀系
数不匹配的目的,提高系统的稳定性和可靠性,增加器件的使用寿命。
7.为解决上述技术问题,本发明提供如下技术方案:
8.第一方面提供一种金刚石中空管道泡沫增强骨架铝基复合材料的制备方法,其特征在于,包括以下步骤:
9.s1、将铜泡沫骨架衬底经超声清洗、烘干后,进行沉积金属过渡层;
10.s2、将s1所得的具有金属过渡层的铜泡沫骨架放在金刚石粉胶体中超声、浸泡、冲洗、烘干,得到镶嵌金刚石颗粒的泡沫骨架;
11.s3、在s2所得的镶嵌金刚石颗粒的泡沫骨架上,采用mpcvd进行金刚石薄膜骨架生长;
12.s4、在s3所得金刚石泡沫骨架上进行激光打孔,开孔密度为5-15个/mm2,得到具有通孔的金刚石泡沫骨架;
13.s5、将s4所得金刚石泡沫骨架浸入酸溶液中进行酸溶,以去除铜泡沫基;然后冲洗去除酸;得到金刚石中空管道泡沫;
14.s6、在含铁催化剂存在下,采用mpcvd,在s5所得金刚石中空管道泡沫上生长碳纳米管,形成碳纳米管包覆金刚石中空管道骨架的混合强化层;
15.s7、利用管式炉将金属铝填充在s6所得的中间产物中进行初步成型处理,以将铝融入泡沫中;
16.s8、利用sps烧结炉,将s7所得中间产物进行高温高压处理,减小金属铝之间的空隙和金属铝与金刚石-cnts泡沫之间的空隙;然后任选的进行抛光和打磨,形成高密集度的铝基复合材料;其中,所述高温高压处理中高温为450-550℃、优选500-550℃,高压为15-20mpa。
17.其中优选地,s1中,所述金属过渡层包括镍、钨、钼、钛、银、铬中的一种或多种复合金属层。
18.本领域技术人员可以选择s1镀金属过渡层的过程和工艺参数。在一些优选实施方式中,所述沉积金属过渡层的工艺条件包括:基底温度为室温,射频功率为180-220w,腔压为0.5-1kpa,ar流量为60-80sccm,靶间距为7-10cm,转速为5-10rpm。
19.优选地,s1所述超声的过程包括:将铜泡沫骨架衬底放入分别放入丙酮、乙醇、去离子水中进行超声震荡清洗5min,取出烘干待用。
20.优选地,s1所述沉积的方式包括电镀、化学镀、蒸镀、磁控溅射、化学气相沉积、物理气相沉积中的任一种。
21.其中优选地,s2中,金刚石粉胶体通过下述方法制得:将质量比为1:1.5-3的w10金刚石粉与w5金刚石粉,以及去离子水调浆后,煮沸3-8min。
22.其中优选地,s2中,所述超声的时间为8-12min,所述浸泡的时间为15-25min。
23.s2所述冲洗和烘干的过程包括:捞出铜泡沫,再用乙醇冲洗干净,放进烘干箱烘干,得到网孔中间镶嵌大量纳米晶和微米晶金刚石颗粒的泡沫骨架衬底。
24.其中优选地,s3中,所述金刚石薄膜骨架生长的过程包括:通入氢气250-350sccm,腔压为6-7kpa,在温度750-800℃条件下进行5-15min退火处理;然后维持温度,通入10-20sccm甲烷,生长70-90h;接下来进行反面生长,通入氢气250-350sccm,腔压为6-7kpa,在温度750-800℃条件下保温3-8min,再通入10-20sccm甲烷,生长70-90h。
25.其中优选地,s4中,所述激光打孔的过程包括:在金刚石泡沫骨架的下表面辐射激光束,将激光功率开到25-35%;同时使用乙醇与去离子水质量比为0.8-1.2:1的混合溶液没过金刚石泡沫骨架上表面30-50μm,混合溶液的液体流速为90-110ml/s。
26.s5中酸溶的酸溶液可为稀盐酸,稀硫酸,稀硝酸,稀硝酸和稀硫酸的混合物,稀盐酸和浓硫酸的混合物,稀盐酸和稀硝酸的混合物,稀盐酸、稀硫酸和稀硝酸的混合物的任一种。
27.本发明中,通过控制含铁催化剂的引入方式和位置以及在mpcvd设备中的覆盖方式来控制生长碳纳米管的位置。其中优选地,s6中具体包括:先将s5所得金刚石中空管道泡沫在含铁催化剂中进行蘸取或者进行超声和浸泡,以及烘干后,再采用mpcvd生长碳纳米管。其中,所述蘸取能在金刚石中空管道外表面生长cnts,所述超声和浸泡能在金刚石中空管道内表面和外表面生长cnts。
28.所述蘸取的过程优选包括:蘸取2次以上并每次在含铁催化剂中持续1-3s。
29.优选地,s6中mpcvd的放料过程包括:将带有fecl2的泡沫放在带有凹槽的钼托上,上表面放一块金刚石自支撑膜盖在凹槽上表面,以在金刚石中空管道外表面或者内外表面生长cnts;或者将带有fecl2的泡沫放在平面的钼托上,以在金刚石中空管道内表面生长cnts。
30.其中优选地,s6中,所述含铁催化剂为氯化亚铁的胶体或乙醇溶液,其中亚铁离子的浓度为0.8-1.2mol/l。
31.更优选地,s6中还包括在进行所述mpcvd之前的还原过程:先通入150-250sccm的h2,温度升到600-750℃,还原25-35min,进行退火5-15min。
32.在一种具体实施方式中,所述含铁催化剂的配置过程具体可以包括:使用液枪取不同的体积商业滴露免洗手液(65%乙醇)凝胶或无水乙醇(ar,99.7%)的一种溶剂,稀释同等体积的fecl2溶液催化剂,并使用磁力搅拌器搅拌20min,可配置不同含铁离子量的凝胶或溶液。
33.其中优选地,s6中,所述mpcvd的过程包括:将带有铁催化剂的泡沫放在带有凹槽的钼托上,上表面放一块金刚石自支撑膜盖在凹槽上表面;将温度升到650-720℃,通入15-25sccm ch4、150-200sccm h2和0.2-1.0vol%o2的混合气,持续10-30min,cnts的长度在10-80μm。
34.s6中,所述碳纳米管包覆金刚石中空管道骨架的混合强化层为选自碳纳米管包覆中空金刚石管道骨架外表面、碳纳米管包覆中空金刚石管道骨架内表面、碳纳米管包覆中空金刚石管道骨架内外表面中的任一种。
35.其中优选地,s7中,所述初步成型处理的过程包括:先通入80-120sccm氩气,持续30-60min,将多余的空气排尽,以3-8℃/min加热至高于金属铝熔点的温度700-800℃持续保温1-1.5h,再以3-8℃/min降到室温下,将多余的铝金属进行打磨平整。
36.其中优选地,s8中,所述高温高压处理的过程包括:先将真空抽到3-5pa,然后以电流20-50a/min的升温速率,将温度升至150-250℃,压力由1-5mpa升至9-13mpa,保温3-8min;继续升温至450-550℃,压力加到15-20mpa,保温3-8min,然后以20-50a/min进行降温直至室温。
37.在本发明的一些具体实施方式中,所述制备方法包括如下步骤:
38.第一步:过渡层的制备
39.将铜泡沫切成2mm厚的长方体(10
×5×
2mm),将其放入丙酮、乙醇、去离子水中分别超声清洗10min,放入烘干箱烘干。将铜泡沫放进射频磁控溅射设备中,先进行镀钛0.5h,再进行反面镀钛0.5h,最终在铜泡沫上得到~1μm的ti过渡层。
40.第二步:播种
41.w10与w5金刚石粉以1:2的比例加去离子水调成浆溶液,煮沸5min,形成胶体。将镀完钛的铜泡沫放进该胶体中超声10min,再浸泡20min,捞出铜泡沫,再用乙醇冲洗干净,放进烘干箱烘干。
42.第三步:制备铜泡沫增强骨架
43.将播完种的铜泡沫,放进微波等离子体化学气相沉积(mpcvd)设备中,进行金刚石薄膜骨架生长,在温度760
±
10℃进行10min退火处理,然后,将温度维持在在760
±
10℃,通入甲烷,生长80h;接下来进行反面生长,温度760
±
10℃,保温5min保证铜泡沫温度均匀性,在通入甲烷,生长80h。得到金刚石薄膜厚度~100μm。
44.第四步:激光穿孔金刚石骨架
45.为了使液膜能够比较好的承载飞溅物,使用乙醇与去离子水1:1混合溶液淹没过金刚石泡沫上表面~50μm,在所述金刚石泡沫的远离所述加工台的表面,持续100ml/s的液体流速淹没金刚石上表面体,以形成流动的液膜,带走激光在金刚石表面产生的烧灼物;将激光器功率调到30%,在所述液膜的远离所述金刚石膜的表面,辐射激光束,得到具有通孔的金刚石泡沫骨架,开孔密度为10个/mm2。
46.去除金属铜泡沫基
47.将打孔完成的金刚石泡沫,放进充足的酸溶液中去除铜泡沫基,酸溶液可为稀盐酸,稀硫酸,稀硝酸,稀硝酸和稀硫酸的混合物,稀盐酸和浓硫酸的混合物,稀盐酸和稀硝酸的混合物,稀盐酸、稀硫酸和稀硝酸的混合物。本案例使用的稀盐酸,将打孔的金刚石泡沫长时间浸泡充足的稀盐酸中,直至铜泡沫基完全被酸消耗殆尽。
48.预处理空中管金刚石泡沫
49.使用流动的去离子水冲洗清洗中空管泡沫,冲洗带多余的稀盐酸溶液。再使用乙醇浸泡中空管金刚石泡沫,然后放进流动气体的烘干箱中,加热150℃,持续半小时,充分去除多余的氯化氢。
50.第五步:配制不同浓度的fecl2溶液催化剂
51.将fe片使用30ml的hcl溶液(ar,36.0-38.0%)去除铁丝表面杂质,静置反应5min,将铁丝放入去离子水、乙醇中分别超声清洗10min,放入烘干箱烘干。将处理好的fe片使用天平称量质量m1,放进10ml的hcl溶液(36.0-38.0%)中,待hcl溶液不在产生气泡,溶液颜色由无色变成黄色最后再变成浅绿色可判断反应完全(fe3+
→
fe2+)。再用乙醇将fe片在烧杯中冲洗干净,称量fe的质量为m2,将冲洗液也倒烧杯中加热50℃去除多余的乙醇和hcl,混合搅拌至均匀,使用ph试纸测量fecl2溶液为酸性,可防止溶液发生氧化和水解反应。使用量筒量取所得溶液体积v,计算,最终得到1.2mol/l的fe离子溶液。
52.在一种可能的实施方式中,使用液枪取商业滴露免洗手液(65%乙醇),取不同的体积v1、v2、v3稀释fe离子溶液,再取1.2mol/l的fe离子溶液体积v放进玻璃样品瓶中,使用磁力搅拌器搅拌20min,可配置不同含铁离子凝胶。在另一种可能的实施方式中,使用液枪
取无水乙醇(ar,99.7%),取不同的体积v4、v5、v6稀释fe离子溶液,再取1.2mol/l的fe离子溶液体积v放进玻璃样品瓶中,使用磁力搅拌器搅拌20min,可配置不同含铁离子的乙醇溶液。
53.第六步:中空金刚石管道骨架上生长cnts
54.此次生长cnts的催化剂使用不同的含铁离子浓度的乙醇溶液,均匀涂覆或蘸取在金刚石中空管道泡沫衬底上,放入烘箱中,90℃烘干30min将乙醇蒸发。将衬底放进mpcvd,生长cnts。
55.另一种可实施方式中,把金刚石中空管道泡沫超声5min,再放入烘箱中,90℃烘干30min将乙醇蒸发。将衬底放进mpcvd或管式炉中,生长cnts。具体参数:
56.先通入200sccm的h2,温度升到~750℃,还原30min,进行退火10min,制得铁催化剂。为了生长cnts,将温度升到~720℃将20sccm ch4、180sccm h2和0.2-1.0vol%o2(优选0.80%o2,o2的作用是去除在化学汽相淀积中覆盖在活性金属催化剂上的无定形碳),持续10-30min,cnts的长度在10-80μm。形成金刚石-碳纳米管泡沫(diamond-cnts foam)复合材料。
57.第七步:金属铝填充diamond-cnts foam进行预成型
58.将第六步的产物放入氧化铝磁舟(15mm
×
15mm
×
10mm)或者石墨(φ=24mm)模具中,把金属铝放在diamond-cnts foam周围,将模具放进管式炉中,将铝融入泡沫中,进行初步成型处理,先通入100sccm氩气,持续15min,将多余的空气排尽,以5℃/min加热至700℃(金属铝的熔点在~660℃)持续保温1h,熔融的铝溶液在真空高温下渗进diamond-cnts foam的空隙中。再以5℃/min降到室温下,将多余的铝金属使用800—2500目砂纸打磨平整至光亮,将其尺寸修整为10mm
×
10mm
×
5mm复合材料。
59.第八步:高温高压减少diamond-cnts foam与铝金属之间的空隙
60.将复合材料放入定制的石墨模具中,其石墨内槽尺寸为φ=24mm,在内槽四周使用石墨纸包覆,避免污染石墨模具,然后将复合材料放入定制的石墨模具,上表面使用石墨压头进行压盖,将其模具放入放电等离子体(sps)腔体中,先使用0.3mpa将模具固定,将热电偶丝插入石墨测温口,在高温高压条件下,减少diamond-cnts foam与铝金属之间的空隙,从而降低界面热阻和阻抗。先将真空抽到4pa,然后以电流20a/min的升温速率,将温度升至200℃,压力由0.3mpa升至10mpa,保温5min;继续升温至500℃,压力加到15mpa,保温5min,然后以20a/min进行降温直至室温,最后泄压取出模具。打磨diamond-cnts-al复合材料:分别使用600,1000,1500,2000,3000砂纸将复合材料打磨至表面光亮。
61.第二方面提供一种金刚石中空管道泡沫增强骨架铝基复合材料,其特征在于,其通过第一方面所述的制备方法制得。
62.其中优选地,其包括金刚石中空管道骨架,在所述金刚石中空管道骨架的内表面和/或外表面生长的碳纳米管,以及填充的金属铝。如图1、图2、图3所示,分别为在金刚石中空管道2的内外表面、外表面、内表面生长碳纳米管3的填充铝1的结构图。图4为金刚石中空管道2骨架的未生长碳纳米管3的铝基复合材料。
63.本发明的上述技术方案的有益效果如下:
64.上述方案中,本发明金刚石中空管道泡沫骨架增强铝基复合材料,热导率获得新高,可到达~1200w/(m
·
k)。本发明制得的复合材料完整地复制了泡沫骨架的结构,高导热
材料以无缝连接的方式构成一个全连通的整体,增强体相与基体相在三维空间内保持连续分布,“犹如血管和神经纤维缠绕组成的增强体相与肉体组成的基体相”,形成网络互穿结构,可有效弱化复合界面对材料热学性能的影响,既不降低金属基体良好塑韧性,又能使增强相成为一个整体,最大限度发挥增强体的导热效率,使复合材料具有优异的连续导热能力、电荷传导能力和极低密度,综合性能明显优于传统的金属基复合材料,是一种很有潜力的多功能复合材料,对大功率通信及导航卫星、定向高能武器以及宽禁带半导体雷达等高功率等先进设备的应用性能可以大幅度改善。而且,本发明使用sps设备对骨架与铝基复合时高温高压,骨架与铝基无缓冲层,能够减小界面热阻。
附图说明
65.图1为金刚石中空管道内外生长碳纳米管泡沫骨架铝基复合材料的结构示意图;
66.图2为金刚石中空管道外生长碳纳米管泡沫骨架铝基复合材料的结构示意图;
67.图3为金刚石中空管道内生长碳纳米管泡沫骨架铝基复合材料的结构示意图;
68.图4为金刚石中空管道泡沫骨架铝基复合材料的结构示意图;
69.图5为本发明实施例1的各阶段产品的实例图像;其中,(a)铝基复合材料数码图像,(b)铝基复合材料截面数码图像(插图为光镜图像),(c)、(d)、(e)均为金刚石中空管道泡沫光镜图像,(f)金刚石中空管道泡沫生长cnts的光镜图像,(g)金刚石中空管道泡沫上的cnts的sem图像。
70.[附图标记]
[0071]
1、铝,2、金刚石中空管道,3、碳纳米管。
具体实施方式
[0072]
为使本发明要解决的技术问题、技术方案和优点更加清楚,下面将结合附图及具体实施例进行详细描述。
[0073]
实施例1
[0074]
金刚石中空管道泡沫骨架增强铝基复合材料,本例中使用孔径为0.2mm-0.6mm泡沫铜作为预支撑衬底,金刚石中空管道泡沫骨架占复合材料体积分数60%,步骤(1)对铜泡沫进行清洗;再按步骤(2)将铜泡沫放进射频直流磁控溅射设备中,先进行镀钛0.5h,再进行反面镀钛0.5h,最终在铜泡沫上得到~1μm的ti过渡层,具体镀ti工艺参数:基底温度为室温,射频功率为200w,腔压为0.7kpa,ar流量为70sccm,靶间距为9cm,转速为8rpm;步骤(3)将过渡层的铜泡沫放进该胶体中超声10min,再浸泡20min,捞出铜泡沫,再用乙醇冲洗干净,放进烘干箱烘干,得到网孔中间镶嵌大量纳米晶和微米晶金刚石颗粒的泡沫骨架衬底。步骤(4)将播完种的铜泡沫,放进mpcvd中,进行金刚石薄膜骨架生长,生长金刚石薄膜厚度~120μm;工艺参数为:氢气300sccm,腔压6.3
±
0.2kpa,温度760
±
10℃进行10min退火处理,然后,将温度维持在在760
±
10℃,通入15sccm甲烷,生长80h;接下来进行反面生长,氢气300sccm,腔压6.3
±
0.2kpa,温度760
±
10℃,保温5min保证铜泡沫温度均匀性,在通入15sccm甲烷,生长80h;步骤(5)将激光功率开到30%,同时使用乙醇与去离子水1:1混合溶液没过金刚石泡沫上表面~50μm,液体流速100ml/s以形成流动的液膜,带走激光在金刚石表面产生的烧灼物;步骤(6)使用的稀盐酸,将打孔的金刚石泡沫长时间浸泡充足的稀盐酸
中,直至铜泡沫基完全被酸消耗殆尽。使用流动的去离子水冲洗清洗中空管泡沫,冲洗带多余的稀盐酸溶液。再使用乙醇浸泡中空管金刚石泡沫,然后放进流动气体的烘干箱中,加热150℃,持续半小时,充分去除多余的氯化氢;步骤(7)使用液枪分别取1.2mol/l的fecl2和无水乙醇(ar,99.7%)30ml,放进玻璃样品瓶中,使用磁力搅拌器搅拌20min,得到催化剂溶液。把金刚石中空管道泡沫放入配制好的催化剂溶液中超声5min,并浸泡10h后再放入烘箱中,90℃烘干30min将乙醇蒸发;步骤(8)使用mpcvd在金刚石中空管道泡沫上生长碳纳米管,形成碳纳米管包覆中空金刚石管道骨架混合强化层;将带有fecl2的泡沫放在带有凹槽的钼托上,上表面放一块金刚石自支撑膜盖在凹槽上表面;先通入200sccm的h2,温度升到~750℃,还原30min,进行退火10min,制得铁催化剂。为了生长cnts,将温度升到~720℃将20sccm ch4、180sccm h2和0.8vol.%o2,持续30min,中空金刚石管道外表面cnts的长度在~50μm,中空金刚石管道内表面cnts的长度在~10μm,形成中空金刚石管道内&外表面都长上cnts,得到all-diamond-cnts foam复合材料;步骤(9)预成型,利用管式炉将金属铝填充all-diamond-cnts foam复合材料,先通入100sccm氩气,持续30min,将多余的空气排尽,以5℃/min加热至700℃(金属铝的熔点在~660℃)持续保温1h,熔融的铝溶液在真空高温下渗进all-diamond-cnts foam的空隙中。再以5℃/min降到室温下,将多余的铝金属使用800—2500目砂纸打磨平整至光亮,将其尺寸修整为10mm
×
10mm
×
5mm复合材料;步骤(10)定型复合材料,利用sps烧结炉,高温高压条件下,减小金属铝之间的空隙和金属铝与diamond-cnts foam之间的空隙,形成高密集度的铝基复合材料(其整体和截面的数码图像分别如图5中(a)、(b)所示);先将真空抽到4pa,然后以电流20a/min的升温速率,将温度升至200℃,压力由0.3mpa升至10mpa,保温5min;继续升温至500℃,压力加到15mpa,保温5min,然后以20a/min进行降温直至室温,最后泄压取出模具;步骤(11)打磨抛光金刚石中空管道内外生长碳纳米管骨架铝基复合材料(all-diamond-cnts-al,如图1所示,如图5中(f)所示)。其中,所得的金刚石中空管道泡沫光镜图像如图5中(c)、(d)、(e)所示,金刚石中空管道泡沫上的cnts的sem图像如图5中(g)所示。
[0075]
性能测试结果:复合材料all-diamond-cnts-al整体热导率~1200w/(m
·
k)。
[0076]
实施例2
[0077]
参照实施例1进行,不同的是,对步骤(7)改变,具体的改变如下:
[0078]
步骤(7)把金刚石中空管道泡沫放入配制好的催化剂溶液中蘸取2次并每次在溶液中持续2s,完成溶液蘸取后再放入烘箱中,90℃烘干30min将乙醇蒸发,以使得后续步骤(8)在金刚石中空管道外表面生长cnts。。
[0079]
性能测试结果:复合材料exterior-diamond-cnts-al(如图2所示)整体热导率~1050w/(m
·
k)。
[0080]
实施例3
[0081]
参照实施例1进行,不同的是,对步骤(8)更改,具体的改变如下:
[0082]
步骤(8)将带有fecl2的泡沫放在平面的钼托上;中空金刚石管道内表面cnts的长度在~10μm,形成中空金刚石管道内表面长cnts,得到inner-diamond-cnts foam复合材料。
[0083]
性能测试结果:复合材料inner-diamond-cnts-al(如图3所示)整体热导率~900w/(m
·
k)。
[0084]
对比例1
[0085]
参照实施例1进行,不同的是,步骤(7-8)去除,其余步骤不变,得到金刚石中空管道泡沫即diamond foam。性能测试结果:复合材料diamond-al(如图4所示)整体热导率~700w/(m
·
k)。
[0086]
通过上述实施例和对比例可以看出,本发明的方案能够获得热导率更高的复合材料。
[0087]
以上所述是本发明的优选实施方式,应当指出,对于本技术领域的普通技术人员来说,在不脱离本发明所述原理的前提下,还可以做出若干改进和润饰,这些改进和润饰也应视为本发明的保护范围。