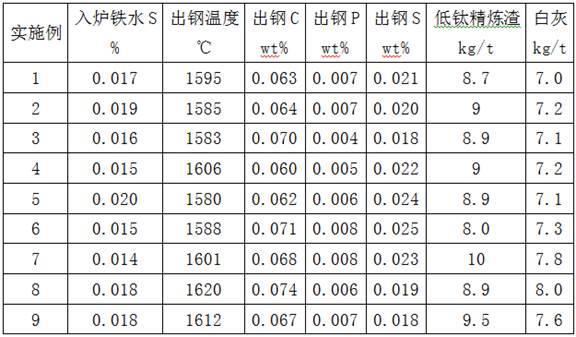
1.本发明涉及一种冶炼方法,尤其是一种超低硫抗硫管线钢的生产方法。
背景技术:2.随着经济和社会的发现,对石油、天然气输送管线钢的质量要求逐步提高,应有于复杂环境、潮湿、酸性环境中的抗氢致裂纹(hic)管线钢的需求日益增大。要获得良好的抗hic和抗硫应力致裂纹(ssc)钢要求具有良好的韧性、抗疲劳性、抗断裂性能,要求钢水中硫含量≤0.001%;因此需要生产过程中稳定、有效地脱硫。
技术实现要素:3.本发明要解决的技术问题是提供一种能有效地降低成品硫含量的超低硫抗硫管线钢的生产方法。
4.为解决上述技术问题,本发明所采取的技术方案是:其包括转炉冶炼、lf精炼、vd真空处理和连铸工序;所述转炉冶炼工序:入炉铁水s≤0.020wt%;转炉出钢温度为1580~1620℃,出钢碳≥0.06wt%、出钢磷≤0.008wt%、出钢硫≤0.025wt%,出钢过程中加入低钛精炼渣8~10kg/t、白灰加入量7~8kg/t;所述lf精炼工序:精炼到位加入白灰10~13kg/吨钢、低钛精炼渣14~23kg/吨钢、铝粒0.4~0.5kg/吨钢;精炼到位给电10~15分钟后,按0.06~0.07kg/t钢喂入纯钙线;所述连铸工序:连铸中包使用高碱度吸渣剂替代普通无碳覆盖剂。
5.进一步的,所述转炉冶炼工序,白灰中s≤0.030wt%,低钛精炼渣中s≤0.035wt%。
6.进一步的,所述lf精炼工序,入vd前倒渣量≥3吨。
7.进一步的,所述vd真空处理:vd真空时间≥23min、vd保持时间≥12min;首炉vd破空后钙线加入量为0.13~0.17kg/吨钢、连浇炉钙线加入量为0.04~0.08kg/t,喂入钙线后按0.4~0.7kg/吨钢加入高碱度吸渣剂,再补加钢包覆盖剂。
8.进一步的,所述连铸工序,高碱度吸渣剂中s≤0.064wt%。
9.进一步的,所述连铸工序,采用重钙塞棒。
10.采用上述技术方案所产生的有益效果在于:通过降低冶炼前期铁水硫含量,冶炼时选用涉钢原辅料进行优化,通过对铁水硫含量的要求以及出钢白灰和精炼渣加入量的调整,到精炼位钢水第二个样硫含量控制在0.003%以下,为后面lf精炼炉的深脱硫打下了良好的基础;所述lf精炼前期强化脱氧,温度升高后通过高碱度大渣量的强力搅拌双重冶炼模式进行深脱硫工艺;连铸使用高碱度覆盖剂防止回硫,使用重钙塞棒,生产出符合要求的成品s:0.0008~0.001%超低硫管线钢。
具体实施方式
11.下面结合具体实施方式对本发明作进一步详细的说明。
12.实施例1-9:本超低硫抗硫管线钢的生产方法依次采用原料准备、转炉冶炼、lf精炼、vd真空处理和连铸工序;各工序工艺如下所述:(1)原料准备工序:禁止装入高s铁块等钢铁料。钢包采用双透气砖。钢包要求烘烤良好、无残钢、残渣,且钢包包沿残渣必须彻底清理。
13.(2)转炉冶炼工序:入炉铁水s≤0.020wt%;转炉出钢温度为1580~1620℃,出钢碳≥0.06wt%、出钢磷≤0.008wt%、出钢硫≤0.025wt%;转炉出钢过程中,先加入钼铁、低钛精炼渣,然后加入白灰,低钛精炼渣加入量为8~10kg/t、白灰加入量7~8kg/t,白灰中s≤0.030wt%、低钛精炼渣中s≤0.035wt%;所述低钛精炼渣的主要成分要求为(wt):cao 48%~55%、sio2≤6.0%、al2o
3 34%~42%、tio2≤0.03%、b≤0.05%、caf2≤5.0%、mgo 3.0%~8.0%、p≤0.3%、s≤0.3%。各实施例转炉冶炼工艺参数见表1;低钛精炼渣的主要成分见下述表3。
14.表1:转炉冶炼工艺参数(3)lf精炼工序:钢水到精炼位后再加入白灰10~13kg/吨钢、低钛精炼渣14~23kg/吨钢、铝粒0.4~0.5kg/吨钢,白灰中s≤0.030wt%、低钛精炼渣中s≤0.035wt%;精炼到位给电10~15分钟后,按0.06~0.07kg/t钢喂入纯钙线;精炼前期强化脱氧,温度升高后通过高碱度大渣量的强力搅拌双重冶炼模式进行深脱硫工艺;入vd前倒渣量≥3吨。所述低钛精炼渣的主要成分要求为(wt):cao 48%~55%、sio2≤6.0%、al2o
3 34%~42%、tio2≤0.03%、b≤0.05%、caf2≤5.0%、mgo 3.0%~8.0%、p≤0.3%、s≤0.3%。各实施例lf精炼工艺参数见表2,各实施例所述低钛精炼渣的主要成分见表3。
15.表2:lf精炼工艺参数
表2中,所述给电时间是指精炼过程取样间隔时的给电时间。
16.表3:低钛精炼渣的主要成分(wt%)(4)vd真空处理:vd真空时间≥23min、vd保持时间≥12min;首炉vd破空后钙线加入量为0.13~0.17kg/吨钢、连浇炉钙线加入量为0.04~0.08kg/吨钢,喂入钙线后按0.4~0.7kg/吨钢加入高碱度吸渣剂,再按1.2~1.5kg/吨钢加入预熔的钢包覆盖剂。各实施例vd真空处理工艺参数见表4。
17.表4:vd真空处理工艺参数
0.002%~0.0035%,余量为fe和不可避免的杂质;各实施例所得抗硫管线钢化学成分见表5;表5:抗硫管线钢化学成分(wt%)(7)所述抗硫管线钢,lf冶炼20~30分钟后停电,氩气搅拌3分钟后取样1;再次送电冶炼10~12分钟后停电取样2,使用碳硫仪分析s含量;再次送电冶炼9~10分钟后停电取样3,使用碳硫仪分析s含量;vd破空后取破空样使用碳硫仪分析s含量。各实施例过程硫和成品硫检验结果见表6。
19.表6:过程硫和成品硫检验结果(wt%)备注:上表6中,样1的s含量为光谱仪分析结果,样2、样3、破空、成品的s含量为碳硫仪(cs)分析结果。
技术特征:1.一种超低硫抗硫管线钢的生产方法,其特征在于:其包括转炉冶炼、lf精炼、vd真空处理和连铸工序;所述转炉冶炼工序:入炉铁水s≤0.020wt%;转炉出钢温度为1580~1620℃,出钢碳≥0.06wt%、出钢磷≤0.008wt%、出钢硫≤0.025wt%,出钢过程中加入低钛精炼渣8~10kg/t、白灰加入量7~8kg/t;所述lf精炼工序:精炼到位加入白灰10~13kg/吨钢、低钛精炼渣14~23kg/吨钢、铝粒0.4~0.5kg/吨钢;精炼到位给电10~15分钟后,按0.06~0.07kg/t钢喂入纯钙线;所述连铸工序:连铸中包使用高碱度吸渣剂替代普通无碳覆盖剂。2.根据权利要求1所述的一种超低硫抗硫管线钢的生产方法,其特征在于:所述转炉冶炼工序,白灰中s≤0.030wt%,低钛精炼渣中s≤0.035wt%。3.根据权利要求1所述的一种超低硫抗硫管线钢的生产方法,其特征在于:所述lf精炼工序,入vd前倒渣量≥3吨。4.根据权利要求1所述的一种超低硫抗硫管线钢的生产方法,其特征在于:所述vd真空处理:vd真空时间≥23min、vd保持时间≥12min;首炉vd破空后钙线加入量为0.13~0.17kg/吨钢、连浇炉钙线加入量为0.04~0.08kg/t,喂入钙线后按0.4~0.7kg/吨钢加入高碱度吸渣剂,再补加钢包覆盖剂。5.根据权利要求1所述的一种超低硫抗硫管线钢的生产方法,其特征在于:所述连铸工序,高碱度吸渣剂中s≤0.064wt%。6.根据权利要求1-5任意一项所述的一种超低硫抗硫管线钢的生产方法,其特征在于:所述连铸工序,采用重钙塞棒。
技术总结本发明公开了一种超低硫抗硫管线钢的生产方法,其包括转炉冶炼、LF精炼、VD真空处理和连铸工序;所述转炉冶炼工序:入炉铁水S≤0.020wt%;转炉出钢温度为1580~1620℃,出钢碳≥0.06wt%、出钢磷≤0.008wt%、出钢硫≤0.025wt%,出钢过程中加入低钛精炼渣8~10kg/t、白灰加入量7~8kg/t;所述LF精炼工序:精炼到位加入白灰10~13kg/吨钢、低钛精炼渣14~23kg/吨钢、铝粒0.4~0.5kg/吨钢;精炼到位给电10~15分钟后,按0.06~0.07kg/t钢喂入纯钙线;所述连铸工序:连铸中包使用高碱度吸渣剂替代普通无碳覆盖剂。本方法通过降低冶炼前期铁水硫含量,冶炼时选用涉钢原辅料进行优化,通过对铁水硫含量的要求以及出钢白灰和精炼渣加入量的调整,到精炼位钢水第二个样硫含量控制在0.003%以下。控制在0.003%以下。
技术研发人员:刘中凯 安建平 刘奇 常尧 杜卓
受保护的技术使用者:石钢京诚装备技术有限公司
技术研发日:2022.10.20
技术公布日:2023/2/3