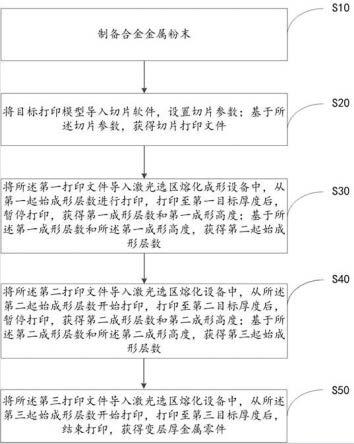
1.本技术涉及金属粉末制造领域,尤其涉及一种变层厚金属零件激光选区熔化成形方法。
背景技术:2.激光选区熔化技术是通过专用软件对零件三维数模进行切片分层,获得各截面的轮廓数据后,利用高能量激光束根据轮廓数据逐层选择性地熔化金属粉末,通过逐层铺粉,逐层熔化凝固堆积的方式进行零件制造的一种技术。
3.目前的激光选区熔化技术主要针对同一零件的同层厚进行打印,无法针对变层厚金属零件进行打印。
技术实现要素:4.本技术的主要目的是提供一种变层厚金属零件激光选区熔化成形方法,旨在解决现有激光选区熔化技术无法针对变层厚金属零件进行打印的技术问题。
5.为解决上述技术问题,本技术提出了:一种变层厚金属零件激光选区熔化成形方法,包括以下步骤:制备合金金属粉末;其中,所述合金金属粉末作为打印粉料;将目标打印模型导入切片软件,设置切片参数;基于所述切片参数,获得切片打印文件;其中,所述切片参数包括切片层厚和打印参数;所述切片层厚包括第一切片层厚、第二切片层厚和第三切片层厚,所述打印参数包括第一打印参数、第二打印参数和第三打印参数,所述切片打印文件包括第一打印文件、第二打印文件和第三打印文件;将所述第一打印文件导入激光选区熔化成形设备中,从第一起始成形层数进行打印,打印至第一目标厚度后,暂停打印,获得第一成形层数和第一成形高度;基于所述第一成形层数和所述第一成形高度,获得第二起始成形层数;其中,所述第一起始成形层数为1层;将所述第二打印文件导入激光选区熔化设备中,从所述第二起始成形层数开始打印,打印至第二目标厚度后,暂停打印,获得第二成形层数和第二成形高度;基于所述第二成形层数和所述第二成形高度,获得第三起始成形层数;将所述第三打印文件导入激光选区熔化设备中,从所述第三起始成形层数开始打印,打印至第三目标厚度后,结束打印,获得变层厚金属零件。
6.作为本技术一些可选实施方式,所述制备合金金属粉末,包括:通过真空气雾化法制备第一合金金属粉末;其中,所述第一合金金属粉末包括:20wt%~24wt%铬、8wt%~9wt%钼、3.5wt%~4.5wt%铌、5wt%~6wt%铁、0.2wt%~0.3wt%铝、0.4wt%~0.5wt%钛,余量为镍;将所述第一合金金属粉末进行真空干燥处理,获得第二合金金属粉末。
7.作为本技术一些可选实施方式,所述合金金属粉末为规则球形或近似球形,其粒
径为10μm~53μm,氧含量<300ppm。
8.作为本技术一些可选实施方式,所述真空干燥处理参数包括:干燥温度为100℃,干燥时间为4h~6h,真空压力为-6.0mpa。
9.作为本技术一些可选实施方式,所述切片层厚为20μm~60μm;所述打印参数包括逐层扫描偏转增量为60
°
~66
°
,光斑直径为60μm~100μm,扫描实体激光功率为150w~380w,扫描速度为800mm/s~1000mm/s,扫描间距为0.08mm~0.12mm。
10.作为本技术一些可选实施方式,在所述打印时,基板加热温度为100℃,保护气体氩气纯度为99.999%,腔室内氧含量低于400ppm,腔室内压力为0mbar~25mbar。
11.作为本技术一些可选实施方式,所述第二起始成形层数通过如下关系式获得:q2=1+(n1*δ1)/δ2其中,q2为第二起始成形层数,n1为第一打印层数,δ1为第一切片层厚,δ2为第二切片层厚。
12.作为本技术一些可选实施方式,所述第三起始成形层数通过如下关系式获得:q3=1+(n2*δ2)/δ3其中,q3为第三起始成形层数,n2为第二打印层数,δ2为第二切片层厚,δ3为第三切片层厚。
13.作为本技术一些可选实施方式,所述将所述第三打印文件导入激光选区熔化设备中,从所述第三起始成形层数开始打印,打印至第三目标厚度后,结束打印,获得变层厚金属零件,包括:将所述第三打印文件导入激光选区熔化设备中,从所述第三起始成形层数开始打印,打印至第三目标厚度后,结束打印,获得第一打印件;将所述第一打印件取出依次进行清粉处理、固溶处理和机械加工处理,获得变层厚金属零件。
14.作为本技术一些可选实施方式,所述固溶处理包括:将清粉处理后的打印件置于真空度为1
×
10-3 pa~1
×
10-4 pa的真空炉中,升温至1100
±
10℃进行保温1h~2h;保温结束后进行气淬,待温度降至300℃后取出。
15.与现有技术相比,通过本技术所述方法能实现变层厚金属零件的激光熔化打印,使得所获得的金属零件表面晶粒度等级可达8级,表面粗糙度值可达ra3.2μm,室温抗拉强度不低于860mpa,屈服强度不低于351mpa,延伸率不低于42%;由此可见,通过本技术所述方法获得的变层厚金属零件的强度和质量均可达到应用需求。目前的现有激光选区熔化成形技术主要是先将零件进行等层厚切片,即零件切片后使用一个层厚进行打印;对于一些成形截面较大的复杂零件,为了顾及一些精细结构处的表面质量,在等层厚切片的前提下,只能采用小层厚进行打印,从而造成了实际零件打印的耗时过长,效率较低,进而增加零件的打印成本和打印周期;而通过本技术所述方法可以对变层厚的零件进行打印,从而提高了零件的成形效率。
附图说明
16.图1是本技术实施例所述方法的流程示意图。
具体实施方式
17.应当理解,此处所描述的具体实施例仅仅用以解释本技术,并不用于限定本技术。
18.激光选区熔化成形技术(selective laser melting,以下简称slm)采用高能量密度激光器作为热源,通过逐层铺粉,逐层激光加热熔化而实现增材制造零件的一种技术。它集计算机辅助设计、激光选区熔覆、快速成型于一体,在无需任何硬质工模具或模型的情况下,能快速制备出不同材料的复杂形状、多品种、小批量的零件,所成型零件致密度高,具有快速凝固组织特征,能满足直接使用要求,在航天器件、飞机发动机零件及武器零件的制备上具有广阔的应用前景。还可通过改变成型材料,得到不同部位由不同材料组成的零件,与计算机相结合,发展材料的智能制备系统。探索直接制备满足工程使用条件的金属零件快速成型技术,将有助于快速成型技术向快速制造技术的转变,能极大地拓展其应用领域。此外,利用逐层制造的优点,探索制造具有功能梯度、综合性能优良、特殊复杂结构的零件也是一个新的发展方向。而快速成型技术与传统制造技术相结合,形成产品快速开发—制造系统也是一个重要趋势。
19.但目前的激光选区熔化技术主要针对同一零件的同层厚进行打印,无法针对变层厚金属零件进行打印。即随着slm成形技术的不断发展,对于使用该工艺进行大型复杂结构零件的成形技术以及成形效率的需求越来越迫切,现有的slm工艺主要是将零件进行等层厚剖分,即零件剖分后使用一个层厚进行打印;对于一些成形截面较大的复杂零件,为了顾及一些精细结构处的表面质量,在等层厚剖分的前提下,只能采用小层厚进行打印,造成实际零件打印的耗时过长,效率较低,进而增加零件的打印成本和打印周期,不利于提高slm技术打印零件的竞争力。因此,对于大型复杂结构零件而言,开发出一种可实现变层厚零件的成形方法尤为重要。
20.基于上述技术问题,如图1所示,本技术实施例提供了一种变层厚金属零件激光选区熔化成形方法,包括以下步骤:步骤s10、制备合金金属粉末;其中,所述合金金属粉末作为打印粉料。
21.在具体应用中,步骤s10所述制备合金金属粉末,包括:步骤s11、通过真空气雾化法制备第一合金金属粉末;其中,所述第一合金金属粉末包括:20wt%~24wt%铬、8wt%~9wt%钼、3.5wt%~4.5wt%铌、5wt%~6wt%铁、0.2wt%~0.3wt%铝、0.4wt%~0.5wt%钛,余量为镍;步骤s12、将所述第一合金金属粉末进行真空干燥处理,获得第二合金金属粉末。
22.在具体应用中,所述真空气雾化法是指利用高速气流作用于熔融液流,使气体动能转化为熔体表面能,进而形成细小的液滴并凝固成粉末颗粒。在具体应用中,所述合金金属粉末为规则球形或近似球形,其粒径为10μm~53μm,氧含量<300ppm。在具体应用中,所述真空干燥处理参数包括:干燥温度为100℃,干燥时间为4h~6h,真空压力为-6.0mpa。将通过上述方法获得的合金金属粉末作为打印粉料进行后续步骤操作。
23.步骤s20、将目标打印模型导入切片软件,设置切片参数;基于所述切片参数,获得切片打印文件;其中,所述切片参数包括切片层厚和打印参数;所述切片层厚包括第一切片层厚、第二切片层厚和第三切片层厚,所述打印参数包括第一打印参数、第二打印参数和第三打印参数,所述切片打印文件包括第一打印文件、第二打印文件和第三打印文件。
24.在具体应用中,所述slm技术先在计算机上设计出零件的三维实体模型,然后通过
专用软件对该三维模型进行切片分层,得到各截面的轮廓数据,将这些数据导入快速成形设备,设备将按照这些轮廓数据,控制激光束选择性地熔化各层的金属粉末材料,逐步堆叠成三维金属零件。因此,在本技术实施例中,由于目标金属零件为变层厚的零件,因此步骤s20中所述的第一切片层厚和所述第二切片层厚的层厚值不同,对应的所述第一打印参数和所述第二打印参数也不同,对应的所述第一打印文件、第二打印文件和第三打印文件也不同;并且,所述第一切片层厚对应第一打印参数和第一打印文件,第二切片层厚对应第二打印参数和第二打印文件,第三切片层厚对应第三打印参数和第三打印文件。需要说明的是,本技术实施例所述方法并不仅仅限于两种层厚的金属零件,上述的“第一”、“第二”和“第三”只是为了举例说明,并不对层厚种类进行任何限定。在具体应用中,所述切片层厚为20μm~60μm;所述打印参数包括逐层扫描偏转增量为60
°
~66
°
,光斑直径为60μm~100μm,扫描实体激光功率为150w~380w,扫描速度为800mm/s~1000mm/s,扫描间距为0.08mm~0.12mm。
25.步骤s30、将所述第一打印文件导入激光选区熔化成形设备中,从第一起始成形层数进行打印,打印至第一目标厚度后,暂停打印,获得第一成形层数和第一成形高度;基于所述第一成形层数和所述第一成形高度,获得第二起始成形层数;其中,所述第一起始成形层数为1层。
26.在具体应用中,在步骤s30和步骤s40所述的打印时,基板加热温度为100℃,保护气体氩气纯度为99.999%,腔室内氧含量低于400ppm,腔室内压力为0mbar~25mbar。
27.在具体应用中,所述第二起始成形层数通过如下关系式获得:q2=1+(n1*δ1)/δ2其中,q2为第二起始成形层数,n1为第一打印层数,δ1为第一切片层厚,δ2为第二切片层厚。
28.步骤s40、将所述第二打印文件导入激光选区熔化设备中,从所述第二起始成形层数开始打印,打印至第二目标厚度后,暂停打印,获得第二成形层数和第二成形高度;基于所述第二成形层数和所述第二成形高度,获得第三起始成形层数。
29.在具体应用中,所述第三起始成形层数通过如下关系式获得:q3=1+(n2*δ2)/δ3其中,q3为第三起始成形层数,n2为第二打印层数,δ2为第二切片层厚,δ3为第三切片层厚。
30.步骤s50、将所述第三打印文件导入激光选区熔化设备中,从所述第三起始成形层数开始打印,打印至第三目标厚度后,结束打印,获得变层厚金属零件。
31.在具体应用中,步骤s50所述将所述第三打印文件导入激光选区熔化设备中,从所述第三起始成形层数开始打印,打印至第三目标厚度后,结束打印,获得变层厚金属零件,包括:步骤s51、所述第三打印文件导入激光选区熔化设备中,从所述第三起始成形层数开始打印,打印至第三目标厚度后,结束打印,获得第一打印件;步骤s52、将所述第一打印件取出依次进行清粉处理、固溶处理和机械加工处理,获得变层厚金属零件。
32.在具体应用中,所述清粉处理是指:待腔室内温度降到室温时开启腔门,取出后清
粉先振动清粉,再吹气清粉。所述固溶处理是指:将清粉处理后的打印件置于真空度为1
×
10-3 pa~1
×
10-4 pa的真空炉中,升温至1100
±
10℃进行保温1h~2h;保温结束后进行气淬,待温度降至300℃后取出。所述机械加工处理是指:采用线切割等机械加工方法去除基板,去除支撑。
33.与现有技术相比,通过本技术所述方法能实现变层厚金属零件的激光熔化打印,使得所获得的金属零件表面晶粒度等级可达8级,表面粗糙度值可达ra3.2μm,室温抗拉强度不低于860mpa,屈服强度不低于351mpa,延伸率不低于42%;由此可见,通过本技术所述方法获得的变层厚金属零件的强度和质量均可达到应用需求。目前的现有激光选区熔化成形技术主要是先将零件进行等层厚切片,即零件切片后使用一个层厚进行打印;对于一些成形截面较大的复杂零件,为了顾及一些精细结构处的表面质量,在等层厚切片的前提下,只能采用小层厚进行打印,从而造成了实际零件打印的耗时过长,效率较低,进而增加零件的打印成本和打印周期;而通过本技术所述方法可以对变层厚的零件进行打印,从而提高了零件的成形效率。
34.下面,结合具体实施例对本技术所述变层厚金属零件的激光选区熔化成形方法进行详细说明:下述实施例1-实施例3中所述第一目标厚度为0.9mm,第二目标厚度为8.1mm,第三目标厚度为1mm。
35.实施例1(1)采用真空气雾化法制备获得规则球形或近似球形的金属粉末,所述金属粉末的粒度均匀一致,无杂物和结块,粉末粒径10~53μm,氧含量小于300ppm;金属粉末由以下成分组成:cr 20~21%、钼8%、铌3.5%、铁5%、铝0.3%、钛0.4%,余量为镍,总质量百分比为100%;激光选区熔化成形前进行粉末真空干燥,干燥温度100℃,时间4h,真空压力-6.0mpa。
36.(2)10mmx10mmx10mm试块模型导入magics软件中,摆放好位置,将第一切片层厚和第三切片层厚均设定为层厚0.02mm,其对应的第一打印参数和第三打印参数均为:扫描偏转增量60
°
,激光功率150w,扫描速度800mm/s,扫描间距0.08mm,进行切片,形成0.02mm层厚的第一打印文件和第三打印文件;将第二切片层厚设定为层厚0.06mm,其对应的第二打印参数为:扫描偏转增量63
°
,激光功率380w,扫描速度1000mm/s,扫描间距0.12mm,进行切片,形成0.06mm层厚的第二打印文件;(3)将第一打印文件导入激光选区熔化成形设备中,安装基板,刮刀,铺粉,设置基板加热温度100℃,待腔室内氧含量低于400ppm,腔室内压力为0~25mbar,开始打印,打印到高度为0.9mm时,也即n1=0.9/δ1=45层时,点击暂停打印,并记录当前成形层数45与成形高度;(4)导入第二打印文件,设置从q2=1+(δ1*n1)/δ2=1+0.02*45/0.06=16层开始打印,打印到高度为0.9+8.1=9mm高度时,也即n2=9/δ2=150时,点击暂停打印,导入第三打印文件,设置从q3=1+(δ2*n2)/δ3=1+0.06*150/0.02=451层开始打印,直至打印结束,这样底部获得0.9mm ,上部获得1mm的小层厚,中间为8.1mm的大层厚,实现变层厚打印,兼顾了打印效率与打印质量的统一。
37.(5)打印完成后,关闭打印设备,待腔室内温度降到室温时开启腔门,取出后清粉
先振动清粉,再吹气清粉。
38.(6)将清粉后的成形件整体置于真空炉中,抽真空,升温到1090℃,真空度为1
×
10-3
~1
×
10-4 pa,保温1h,保温结束后进行气淬,温度降到300℃以下取出;固溶处理后用线切割等机械加工方法去除基板,去除支撑,获得金属打印件1。
39.得到的成形件采用同批试样进行力学性能测试,测试方法为gb/t228.1-2010,测试结果见表1。
40.实施例2(1)采用真空气雾化法制备获得规则球形或近似球形的金属粉末,所述金属粉末的粒度均匀一致,无杂物和结块,粉末粒径10~53μm,氧含量小于300ppm,金属粉末由以下成分组成:cr 22~23%、钼9%、铌4%、铁6%、铝0.2%、钛0.5%,余量为镍,总质量百分比为100%;激光选区熔化成形前进行粉末真空干燥,干燥温度100℃,时间5h,真空压力-6.0mpa。
41.(2)10mmx10mmx10mm试块模型导入magics软件中,摆放好位置,将第一切片层厚设定为层厚0.03mm,其对应的第一打印参数为:扫描偏转增量65
°
,激光功率220w,扫描速度900mm/s,扫描间距0.10mm,进行切片,形成0.03mm层厚的切片文件;将第二切片层厚设定为层厚0.06mm,其对应的第二打印参数为:扫描偏转增量63
°
,激光功率380w,扫描速度1000mm/s,扫描间距0.12mm,进行切片,形成0.06mm层厚的第二打印文件;将第三切片层厚设定为层厚0.02mm,其对应的第三打印参数为:扫描偏转增量60
°
,激光功率150w,扫描速度800mm/s,扫描间距0.08mm,进行切片,形成0.03mm层厚的第三打印文件;(3)将第一打印文件导入激光选区熔化成形设备中,安装基板,刮刀,铺粉,设置基板加热温度100℃,待腔室内氧含量低于400ppm,腔室内压力为0~25mbar,开始打印,打印到高度为0.9mm时,也即n1=0.9/δ1=30层时,点击暂停打印,并记录当前成形层数30与成形高度;(4)导入第二打印文件,设置从q2=1+(δ1*n1)/δ2=1+0.03*30/0.06=16层开始打印,打印到高度为0.9+8.1=9mm高度时,也即n2=9/δ2=150时,点击暂停打印,导入第三打印文件,设置从q3=1+(δ2*n2)/δ3=1+0.06*150/0.02=451层开始打印,直至打印结束,这样底部获得0.9mm ,上部获得1mm的小层厚,中间为8.1mm的大层厚,实现变层厚打印,兼顾了打印效率与打印质量的统一。
42.(5)打印完成后,关闭打印设备,待腔室内温度降到室温时开启腔门,取出后清粉先振动清粉,再吹气清粉。
43.(6)将清粉后的成形件整体置于真空炉中,抽真空,升温到1000℃,真空度为1
×
10-3
~1
×
10-4 pa,保温1.5h,保温结束后进行气淬,温度降到300℃以下取出;固溶处理后用线切割等机械加工方法去除基板,去除支撑,获得金属打印件2。
44.得到的成形件采用同批试样进行力学性能测试,测试方法为gb/t228.1-2010,测试结果见表1。
45.实施例3(1)采用真空气雾化法制备获得规则球形或近似球形的金属粉末,其粒度均匀一致,无杂物和结块,粉末粒径10~53μm,氧含量小于300ppm,金属粉末由以下成分组成:cr 24%、钼8%、铌4.5%、铁6%、铝0.3%、钛0.5%,余量为镍,总质量百分比为100%;激光选区熔
化成形前进行粉末真空干燥,干燥温度100℃,时间6h,真空压力-6.0mpa。
46.(2)10mmx10mmx10mm试块模型导入magics软件中,摆放好位置,将第一切片层厚设定为层厚0.02mm,其对应的第一打印参数为:扫描偏转增量60
°
,激光功率150w,扫描速度800mm/s,扫描间距0.08mm,进行切片,形成0.02mm层厚的第一打印文件;将第二切片层厚设定为层厚0.06mm,其对应的第二打印参数为:扫描偏转增量63
°
,激光功率380w,扫描速度1000mm/s,扫描间距0.12mm,进行切片,形成0.06mm层厚的第二打印文件;将第三切片层厚设定为层厚0.03mm,其对应的第三打印参数为:扫描偏转增量65
°
,激光功率220w,扫描速度900mm/s,扫描间距0.10mm,进行切片,形成0.03mm层厚的第三打印文件;;(3)将第一打印文件导入激光选区熔化成形设备中,安装基板,刮刀,铺粉,设置基板加热温度100℃,待腔室内氧含量低于400ppm,腔室内压力为0~25mbar,开始打印,打印到高度为0.9mm时,也即n1=0.9/δ1=45层时,点击暂停打印,并记录当前成形层数45与成形高度;(4)导入第二打印文件,设置从q2=1+(δ1*n1)/δ2=1+0.02*45/0.06=16层开始打印,打印到高度为0.9+8.1=9mm高度时,也即n2=9/δ2=150时,点击暂停打印,导入第三打印文件,设置从q3=1+(δ2*n2)/δ3=1+0.06*150/0.03=301层开始打印,直至打印结束,这样底部获得0.9mm ,上部获得1mm的小层厚,中间为8.1mm的大层厚,实现变层厚打印,兼顾了打印效率与打印质量的统一。
47.(5)打印完成后,关闭打印设备,待腔室内温度降到室温时开启腔门,取出后清粉先振动清粉,再吹气清粉。
48.(6)将清粉后的成形件整体置于真空炉中,抽真空,升温到1010℃,真空度为1
×
10-3
~1
×
10-4 pa,保温2h,保温结束后进行气淬,温度降到300℃以下取出;固溶处理后用线切割等机械加工方法去除基板,去除支撑,获得金属打印件3。
49.得到的成形件采用同批试样进行力学性能测试,测试方法为gb/t228.1-2010,测试结果见表1。
50.同时,为将本技术所述方法与不变层厚的零件打印时间进行对比,本技术采用打印试棒对层厚分别为0.02mm、0.03mm和0.06mm进行了打印测试,并同样进行力学性能测试,测试方法为gb/t228.1-2010,测试结果见表1:表1:
可以看出,与现有技术相比,通过本技术所述方法能实现变层厚金属零件的激光熔化打印,使得所获得的金属零件表面晶粒度等级可达8级,表面粗糙度值可达ra3.2μm,室温抗拉强度不低于860mpa,屈服强度不低于351mpa,延伸率不低于42%;由此可见,通过本技术所述方法获得的变层厚金属零件的强度和质量均可达到应用需求。并且本技术所述方法相较于现有只打印同一层厚的打印时间大幅缩短,从而提高了打印效率。
51.以上仅为本技术的优选实施例,并非因此限制本技术的专利范围,凡是利用本技术说明书及附图内容所作的等效结构或等效流程变换,或直接或间接运用在其他相关的技术领域,均同理包括在本技术的专利保护范围内。