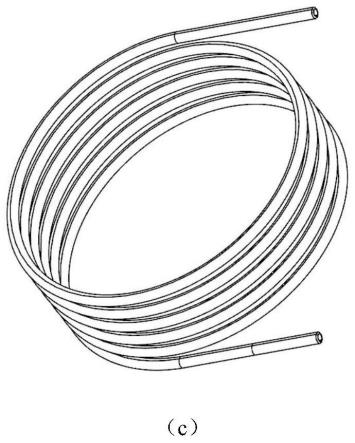
1.本发明属于铝合金加工技术领域,具体涉及一种随形冷却内流道铝合金零件复合制造方法。
背景技术:2.承载高温工况的模具或零件,内流道均匀冷却效果直接决定其使用寿命。传统冷却采用简单直线钻孔流道,无法均匀布管,难以满足复杂曲面型腔均匀冷却;镶拼结构配合精度难以控制,且在高温高压作用下易产生形变泄露。采用基于离散-堆积原理的增材制造技术,可实现零件内部冷却流道的随形柔性设计,其制造方式主要包括以下三种:
3.(1)基材加工冷却流道槽,槽底铺设支撑管材,装夹焊接固定后,增材堆焊填充剩余空间,但高热输入条件下仍易发生管材变形翘曲甚至焊缝开裂。
4.(2)拆分内流道为上下两部分,无悬臂下半部分成形完毕后机加,悬臂上半部分采用随形盖板拼接封口(但盖板拼接过程中易发生变形),或焊枪实时变换姿态无支撑直接成形上半部分(但对于复杂结构存在焊枪干涉问题),或调整内流道上半部分截面形状为水滴形、三角形等,避免较大悬空面(但内流道上表面为粗糙面)。
5.(3)采用增材制造砂型内芯后浇注,但易出现气孔、裂纹等缺陷。
技术实现要素:6.针对现有技术的不足或改进需求,本发明提出了一种随形冷却内流道铝合金零件复合制造方法,包括以下步骤:
7.步骤s1:依据零件结构特征进行砂型模具设计;
8.步骤s2:随形冷却内流道加工;
9.步骤s3:砂型模具增材制造;
10.步骤s4:随形冷却内流道与砂型模具装配预热;
11.步骤s5:铝合金零件浇注与整体热处理。
12.优选地,步骤s1中,所述砂型模具根据零件结构特征及原材料铸造性能进行设计。
13.优选地,步骤s2中,所述随形冷却内流道依据零件结构特征采用弯管成形、挤压成形或机加拼接进行制造,材质为不锈钢或铜合金,制造完毕后表面进行薄层喷砂糙化处理,增加浇注润湿性。
14.优选地,步骤s3中,所述砂型模具采用3d喷墨增材制造,使用原料包括硅砂、酚醛树脂粘结剂与锆英粉耐火涂料,制造完毕后在150℃~200℃干燥箱中进行固化。
15.优选地,步骤s4中,所述随形冷却内流道与砂型模具依据零件几何特征进行定位装配,随后整体放入热处理炉预热至300℃~400℃。
16.优选地,步骤s5中,所述铝合金金属液在电炉中熔炼至700℃~750℃进行浇注,零件完全冷却后开模清理表面,最后依据室温与高温强塑性使用要求进行相应热处理。
17.优选地,随形冷却内流道加工完毕后,依据gb50242及使用要求进行无泄漏打压测
试。
18.优选地,耐火涂料刷涂厚度为1mm~2mm。
19.优选地,一种随形冷却内流道铝合金零件,包括外部半封盖zl101a壳体与内嵌随形布置316l不锈钢螺旋流道;
20.zl101a壳体内壁为光滑圆筒状电机装配面,zl101a壳体的外壁开口端设置法兰,zl101a壳体的外壁封盖端与内壁间存在一处矩形通风口;
21.316l不锈钢螺旋流道包括6圈等间距等直径连续管道,管道壁厚为1.2mm,所述管道外径为8mm,管道间的中心距为218mm,316l不锈钢螺旋流道管道进出口通过定位凸台从最大圆切线处平直伸出30mm用于外部通水装配。
22.与现有技术相比,本发明的有益效果如下:
23.(1)本发明内流道采用弯管成形、挤压成形或机加拼接进行直接制造,内壁光滑,可实现内流道随形柔性设计,提高均匀冷却效果。
24.(2)本发明基于传统制造与增材制造的结合,发挥多种组合加工技术复合制造的优势,解决了直接浇注内流道存在气孔、裂纹等缺陷,及直接增材制造存在变形、未熔合等缺陷的问题,具有成本低、效率高、方便实现的特点。
附图说明
25.图1是本发明的随形冷却内流道铝合金零件结构示意图:(a)整体三维外轮廓;(b)带随形内流道的局部装配图;(c)随形内流道管道示意图。
26.图2是本发明的随形冷却内流道铝合金零件实物图。
27.图中:1-外部半封盖zl101a壳体;2-内嵌随形布置316l不锈钢螺旋流道。
具体实施方式
28.下面结合附图与实施例对本发明的实施方式作进一步详细描述。以下实施例的详细描述和附图用于示例性地说明本发明的原理,但不能用来限制本发明的范围,本领域技术人员无需创造性劳动即可将实施例中的技术特征组合形成新的实施例,且这些新的实施例同样涵盖在本发明的保护范围之内。
29.如图1所示,以某电机壳体为例,该随形冷却内流道铝合金零件,包括外部半封盖zl101a壳体1与内嵌随形布置316l不锈钢螺旋流道2,整体外轮廓尺寸为254.5mm
×
243mm
×
229mm,重量约16.6kg。该zl101a壳体1内壁为光滑圆筒状电机装配面,外壁开口端设置法兰,外壁封盖端与内壁间存在一处矩形通风口。该316l不锈钢螺旋流道2由6圈等间距等直径连续管道构成,管道壁厚1.2mm,外径8mm,中心距218mm,整体随形内嵌在zl101a壳体1中间均匀34mm壁厚处,管道进出口通过定位凸台从最大圆切线处平直伸出30mm用于外部通水装配。该薄壁长中心距且需精确定位的随形管道特征,通过砂芯浇注与直接增材堆焊均易发生变形。
30.本实施方案具体包括以下步骤:
31.步骤s1:依据零件结构特征进行砂型模具设计;
32.步骤s2:随形冷却内流道加工;
33.步骤s3:砂型模具增材制造;
34.步骤s4:随形冷却内流道与砂型模具装配预热;
35.步骤s5:铝合金零件浇注与整体热处理。
36.本实施方案的砂型模具根据零件结构特征及原材料铸造性能进行设计。
37.本实施方案的随形冷却内流道依据零件结构特征采用弯管成形进行制造,材质为316l不锈钢,壁厚1.2mm,制造完毕后表面进行薄层喷砂糙化处理,外表面粗糙度达到ra12.5,增加浇注润湿性。
38.本实施方案的砂型模具采用3d喷墨增材制造,使用原料包括硅砂、酚醛树脂粘结剂与锆英粉耐火涂料,制造完毕后在200℃干燥箱中进行固化。
39.本实施方案的随形冷却内流道与砂型模具依据零件几何特征进行定位装配,随后整体放入热处理炉预热至350℃。
40.本实施方案的zl101a铝合金金属液在电炉中熔炼至725℃进行浇注,零件完全冷却后开模清理表面,最后进行整体t6热处理(固溶:随炉升温至535℃,保温9h,60℃水冷;时效:随炉升温至180℃,保温5h,空冷。)。
41.本实施方案的随形冷却内流道加工完毕后采用3mm厚316l薄板点焊固定位置,并进行10kg水压保持20min无泄漏打压测试。
42.本实施方案的耐火涂料刷涂厚度为2mm。
43.图2是本发明经复合制造的随形冷却内流道zl101a铝合金机壳零件实物照片,打压无泄漏,表面无气孔等缺陷,x射线结果表明零件质量符合gb/t9438-2013ⅱ类铸件要求,尺寸公差符合gb/t 6414-2017ct9级,表面粗糙度为ra 12.5,成品率100%。
44.本领域的技术人员容易理解,未作详细描述的内容属于本领域技术人员的公知技术,且以上所述仅为本发明的较佳实例而已,并不用于限制本发明,凡在本发明的精神和原则之内所作的任何修改、等同替换和改进等,均应包含在本发明的保护范围之内。