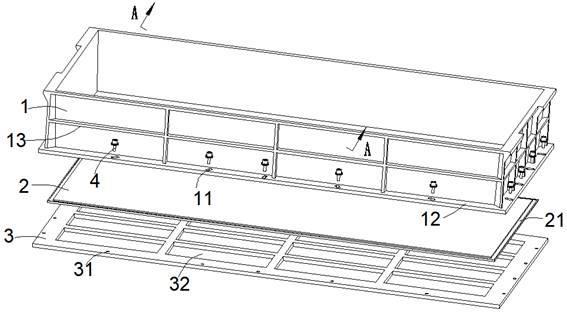
1.本发明涉及泡沫铝模具,尤其是一种减少模具塑性变形量的方法及泡沫铝成型模具。
背景技术:2.泡沫铝具有轻量化、吸音降噪、吸能缓冲、阻热隔热、防弹防爆和电磁屏蔽等性能,具有广阔的应用环境,泡沫铝模具(下文简称模具)是用来生产泡沫铝铝锭的容器。模具工作温度区间大,模具初始加热温度达到700℃以上,随后在使用过程中温度逐渐降低;当模具降到500℃左右时,泡沫铝模具急速冷却,使泡沫铝铝锭成形。在泡沫铝成型的过程中,模具受力复杂,包括加热时加热不均匀会受到热应力作用,包括模具工作过程中受到铝液重力、工装的静压力作用以及模具冷却过程中会受到强烈热应力作用。由于模具在实际生产应用中会受到各种力的综合作用,其每次使用后都会产生一定塑性变形,当使用次数达到一定数值,变形累积到一定程度时,模具无法满足泡沫铝产品质量和工艺要求而报废。通过对模具使用过程进行分析,发现泡沫铝模具变形主要产生在冷却阶段,即泡沫铝生产过程中铝液发泡完成后成熔融状态,此时需要通过对模具底部进行高速喷水,使泡沫铝铝锭及模具快速冷却至室温,从而使泡沫铝铝锭合格。
3.泡沫铝铝锭朝着大规格方向发展,目前可生产的泡沫铝尺寸最大可达到2700mm*1100mm*600mm。大尺寸泡沫铝铝锭生产存在以下问题:1、由于模具尺寸增大,模具和泡沫铝铝锭所含热量更多,为了满足泡沫铝铝锭冷却速度要求,需要对模具进行更为快速的冷却;2由于模具尺寸增大,模具各部分冷却速度差异增大、温度分布更加不均匀,导致泡沫铝模具变形大、寿命低。
4.现有泡沫铝模具主要整体式模具,这类模具结构笨重,使用过程中能源消耗大,此外这类模具在使用过程中变形大,变形后难以恢复,模具寿命普遍较低,并且没有解决模具变形的实际问题。
技术实现要素:5.本发明的目的在于:针对上述存在的问题,提供一种减少模具塑性变形量的方法及泡沫铝成型模具,采用弹性性能不同的材料和具有约束特定方向位移的连接方式,使得部件之间存在让位空间,既保证了泡沫铝模具的密封性,又减少了泡沫铝模具在使用过程中的塑性变形量,大幅提高了模具寿命。
6.本发明采用的技术方案如下:一种减少模具塑性变形量的方法,包括以下步骤:s1:分体式设置模具,使模具有若干种部件组成;s2:组成模具的部件之间能够相对滑动,使得部之间存在让位空间;s3:通过部件之间的让位来消除材料的热胀冷缩应力,达到降低塑性变形量的目的。
7.一种泡沫铝成型模具,应用所述的方法,包括主体、底座和夹持在主体与底座之间
的底板;所述底板与主体、底板与底座之间均滑动连接以使得所述底板与主体之间、底板与底座之间存在相对滑动,所述主体与底座之间可拆卸的活动连接以使得所述主体与底座之间存在同一方向上的相对滑动。
8.进一步地,所述底板的四周边缘处均开设有滑槽,所述主体的底部置于该滑槽内以使得所述主体与底板之间存在相对滑动。
9.进一步地,所述主体的内壁与滑槽的内壁之间填充有耐高温密封材料。
10.进一步地,所述主体的外壁上设置有连接板,所述连接板上开设有若干个腰孔,所述底板上设置有螺纹孔,该螺纹孔的位置和分布与所述腰孔相匹配,所述主体和底座通过螺杆穿过腰孔与螺纹孔连接实现所述主体与底座可拆卸的活动连接。
11.进一步地,所述螺杆的螺帽与连接板之间设置有弹性垫圈。
12.进一步地,所述若干个腰孔沿着所述主体四周均匀分布,并且若干个所述腰孔的中心线均与所述主体的同一中心轴相交。
13.进一步地,所述底板由弹簧钢板制成。
14.进一步地,所述底座由模具钢板制成。
15.进一步地,所述底座上开设有若干个冷却孔。
16.进一步地,所述主体的外侧面焊接有加强筋。
17.综上所述,由于采用了上述技术方案,本发明的有益效果是:1、本发明提出将模具由若干种部件组成,相较于整体式的模具来说,分体式设置模具方便更换变形大的部件,减少模具材料的消耗;2、本发明提出分体式设置模具,并且模具部件之间存在相对滑动,使得模具各个部件在受到温度差异大、热胀冷缩不一致时候存在让位空间,消除热胀冷缩时候因约束的存在产生的应力,从而达到降低塑性变形目的;3、本发明的模具由主体、底座和底板三部分分体式组成,将具有不同冷却速度的部位单独出来,使得各部件之间的热胀冷缩形变相互独立,尽可能的降低温度差异大、热胀冷缩不一致等因素对模具带来的塑性变形;4、本发明将底板与底座之间、底板与主体之间、主体与底座之间均设置为能够相对滑动的连接,使得各部件之间存在自由运动,达到允许各部件具有热胀冷缩的变形让位空间地目的,进一步消除热胀冷缩时候因约束的存在产生的应力,从而达到降低塑性变形目的。
附图说明
18.本发明将通过例子并参照附图的方式说明,其中:图1为本发明实施例1提出的方法的步骤流程图;图2为发明实施例2提出的模具的三维爆炸结构示意图;图3为图2中a-a方向的剖视结构示意图;图4为图3中b处的放大示意图;图中标记:1-主体;11-腰孔;12-连接板;13-加强筋;2-底板;21-滑槽;3-底座;31-螺纹孔;32-冷却孔;4-螺杆;41-弹性垫圈;5-耐高温密封材料。
具体实施方式
19.本说明书中公开的所有特征,或公开的所有方法或过程中的步骤,除了互相排斥的特征和/或步骤以外,均可以以任何方式组合。
20.本说明书中公开的任一特征,除非特别叙述,均可被其他等效或具有类似目的的替代特征加以替换。即,除非特别叙述,每个特征只是一系列等效或类似特征中的一个例子而已。
21.实施例1如图1,一种减少模具塑性变形量的方法,包括以下步骤:s1:分体式设置模具,使模具有若干种部件组成;s2:组成模具的部件之间能够相对滑动,使得部件之间存在让位空间;s3:通过部件之间的让位来消除材料的热胀冷缩应力,达到降低塑性变形量的目的。
22.具体的,在步骤s1中,在对模具进行分体式设计形成各个部件时候,需要根据模具各个位置或部件的冷却速度和热胀冷缩的变形率来进行综合考虑;具体的,冷却速度不同和热胀冷缩的变形率不同的部件作为单独的部件;将模具由若干种部件组成,相较于整体式的模具来说,分体式设置模具方便更换变形大的部件,减少模具材料的消耗。
23.在步骤s2中,组成模具的部件之间能够相对滑动,即部件在发生热胀冷缩时候自由的根据形变产生位移,使得模具各个部件在受到温度差异大、热胀冷缩不一致时候进行让位,消除热胀冷缩时候因约束的存在产生的应力,从而达到降低塑性变形目的。
24.实施例2如图2-图4所示,一种泡沫铝成型模具,应用实施例1所述的方法,包括主体1、底座3和夹持在主体1与底座3之间的底板2,底座3主要起支撑和约束作用,其变形率相对于主体1、底板2最小,将具有不同冷却速度的部位单独出来,使得主体1、底座3和底板2之间的热胀冷缩形变相互独立,尽可能的降低温度差异大、热胀冷缩不一致等因素对模具带来的塑性变形;所述底板2与主体1、底板2与底座3之间均在水平方向上滑动连接以使得所述底板2与主体1之间、底板2与底座3之间存在水平方向上的相对滑动,满足底板2沿着四周膨胀或收缩的需要,所述主体1与底座3之间可拆卸的活动连接以使得所述主体1与底座3之间存在同一方向上的相对滑动,即主体1与底座3之间也能在水平方向上进行相对滑动,满足主体1沿着四周膨胀和收缩的需要。
25.另一方面,主体1与底座3通过可拆卸连接夹持底板2,该连接约束主体1与底板2在竖直方向上的膨胀与收缩,使得主体1与底板2之间乃能保持相应的密封性能,并且主体1与底板2在竖直方向上的形变量较小,几乎对模具的形状不产生影响,所以,将底板2与底座3、底板2与主体1之间限制在水平方向上相对滑动,以及主体1与底座3之间的水平方向的滑动能够满足降低各部件塑性变形的设计目的,具体的,各部件之间存在水平方向上的自由滑动,达到允许各部件具有热胀冷缩的变形让位空间地目的,进一步消除热胀冷缩时候因约束的存在产生的应力,从而达到降低塑性变形目的。
26.在本实施例中,所述底板2的四周边缘处均开设有滑槽21,所述主体1的底部置于该滑槽21内以使得所述主体1与底板2之间存在相对滑动,具体的,滑槽21的宽度大于主体1上置于滑槽21内部分的宽度,使得主体1的内壁与滑槽21的内壁、主体1的外壁与滑槽21的
内壁之间均存在间隙,在底板2出现热胀冷缩形变时候,底板2沿着水平面相对于主体1滑动,滑槽21内壁与主体1内壁、外壁之间的间隙即为底板2可以滑动的行程,即底板2的相对滑动的让位空间,该空间允许底板2让位,达到消除因约束底板2变形形成的热胀冷缩应力的目的,进一步地降低底板2发生塑性变形的可能。
27.在本实施例中,进一步地,所述主体1的内壁与滑槽21的内壁之间填充有耐高温密封材料5,耐高温材料优选耐火棉,一方面能够密封主体1的内壁与滑槽21的内壁之间之间的间隙,降低泡沫铝液体泄露;另一方面耐火棉不会因为泡沫铝的高温而损坏,保证主体1的内壁与滑槽21的内壁之间之间的间隙被密封。
28.在本实施例中,所述主体1的外壁上设置有连接板12,连接板12向主体1的外侧延伸,连接板12的下端面能够与底座3接触,所述连接板12上开设有若干个腰孔11,所述底板2上设置有螺纹孔31,该螺纹孔31的位置和分布与所述腰孔11相匹配,所述主体1和底座3通过螺杆4穿过腰孔11与螺纹孔31连接实现所述主体1与底座3可拆卸的活动连接。
29.具体的,主体1与底座3之间能够在水平方向的相对滑动得益于腰孔11的设计,腰孔11的长度为主体1可以发生形变产生相对滑动的行程,该相对滑动的行程为主体1针对热胀冷缩时候发生形变的让位空间,消除主体1因约束产生的应力,从而降低主体1的塑性变形,螺杆4穿过腰孔11与螺纹孔31连接,螺杆4在竖直方向约束主体1,使得主体1在竖直方向几乎不发生位移,保证主体1被约束使得主体1与底板2之间的密封性能稳定。
30.进一步地,在本实施例中,螺杆4通常具有螺帽,螺帽与连接板12之间依次设置弹性垫圈41和垫片,垫片位于弹性垫圈41与连接板12之间,弹性垫圈41和垫片均套设在螺杆4上,在安装主体1与底座3后,弹性垫圈41存在弹性势能,该弹性势能一方面能够能够降低螺杆4松动的可能,另一方面能够维持主体1(连接板12)与底座3之间、主体1与底板2之间的紧贴,保证密封;具体的,当主体1或/和底板2在竖直方向产生微弱的热胀冷缩形变时候,在主体1)或/和底板2发生竖直方向上的膨胀时候,弹性垫圈41能够储存形变产生的应力,即弹性垫圈41的能够发生形变允许主体1和底板2产生微弱形变,弹性垫圈41的形变为主体1和底板2产生微弱形变提供让位,降低竖直方向上塑性变形;在主体1或/和底板2发生竖直方向上的收缩时候,弹性垫圈41能够恢复形变释放弹性势能使得主体1与底板2之间、主体1与底座3之间乃是紧贴状态,保证密封。
31.在本实施例中,主体1与底板2之间的紧贴受力、主体1与底座3之间的约束受力均匀分布,该效果得益于所述若干个腰孔11沿着所述主体1四周均匀分布。
32.在本实施例中,若干个所述腰孔11的中心线均与所述主体1的同一中心轴相交;在通常情况下,主体1、底板2的热胀冷缩是从中心处向四周均匀的发生形变,限制腰孔11的中心线与主体1的中心轴线之间的关系,能够有效避免腰孔11对主体1的形变产生空间位置干扰。
33.在本实施例中,所述底板2由弹簧钢板制成,弹簧钢板的材质优选65mn、55si2mn中的任意一种,其具有良好的弹性,即其具有较优的形变恢复能够,能够实现在底板2发生形变后,底板2能够自行恢复形变,进一步地降低底板2发生塑性变形可能,保证模具的长期使用。
34.在本实施例中,所述底座3由模具钢板制成,模具钢板的材料优选42crmov、5crnimo中的任意一种。
35.在本实施例中,所述底座3上开设有若干个冷却孔32,底座3优选整块材料切割而成,降低焊接或其他连接防止在高温条件出现的应力集中;冷却孔32均匀分布,通过冷却孔32可以达到直接冷却底板2目的。
36.在本实施例中,所述主体1的外侧面焊接有加强筋13,加强筋13加强主体1的强度,提高主体1抵抗变形的能力,在本实施例中,主体1采用的材料优选q235、q345中的任意一种。
37.本发明并不局限于前述的具体实施方式。本发明扩展到任何在本说明书中披露的新特征或任何新的组合,以及披露的任一新的方法或过程的步骤或任何新的组合。