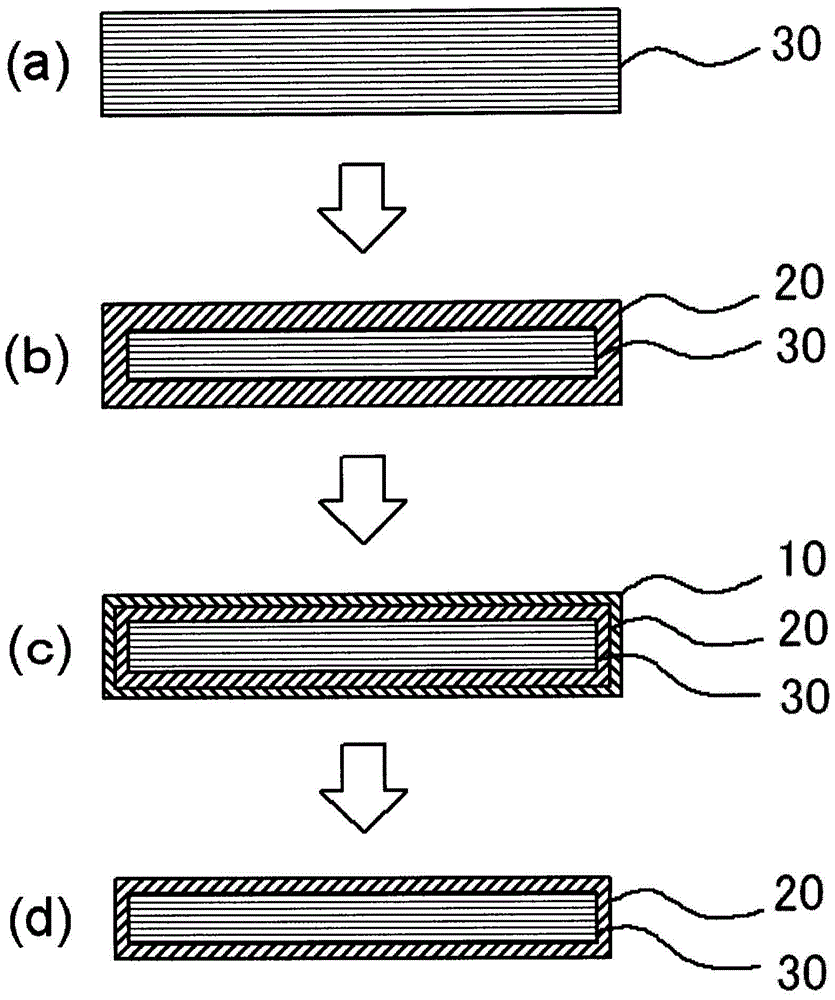
本发明涉及化学强化玻璃。
背景技术:数码相机、手机或便携式信息终端PDA(PersonalDigitalAssistants)等平板显示装置中,为了保护显示器和提高美观,以区域比图像显示部分更广的方式将薄的板状保护玻璃配置于显示器的正面。虽然玻璃的理论强度高,但是由于带有损伤而强度大幅降低,因此使用通过离子交换等在玻璃表面形成了压应力层的化学强化玻璃作为要求强度的玻璃。伴随着对平板显示装置的轻量化和薄型化的要求,要求保护玻璃本身也变薄。因此,为了满足该目的,对保护玻璃要求在表面和端面都具有更高的强度。为了提高化学强化玻璃的强度,以往已知的方法是,在化学强化处理后实施表面蚀刻处理(专利文献1)。在此,关于玻璃的强度,已知由于玻璃中氢(水分)的存在而玻璃的强度降低(非专利文献1、2)。现有技术文献专利文献专利文献1:日本特表2013-516387号公报非专利文献非专利文献1:S.ITO等人,“CrackBluntingofHigh-SilicaGlass”,JournaloftheAmericanCeramicSociety,第65卷,第8期,(1982),368-371非专利文献2:Won-TaekHan等人,“Effectofresidualwaterinsilicaglassonstaticfatigue”,JournalofNon-CrystallineSolids,127,(1991)97-104
技术实现要素:发明所要解决的问题本发明人等发现,有时化学强化后玻璃的强度降低,其主要原因是由于环境中的水分侵入到玻璃表层中而导致产生化学缺陷。另外还发现,该现象并不限于化学强化,在玻璃的制造工序中由于经历升温工序也会发生。作为除去玻璃表层的水分的方法,也考虑了通过研磨化学强化后的玻璃表面、或者浸渍于氢氟酸等而进行蚀刻处理等方法,削去含有水分的层。但是,由于研磨而导致玻璃表面带有损伤,强度反而有可能降低。另外,在玻璃表面具有潜在损伤的情况下,如果使用氢氟酸等进行蚀刻处理,则潜在损伤会扩大,有可能产生由凹坑导致的外观不良。另外,氢氟酸从安全方面考虑需要注意操作。本发明的目的在于提供一种即使进行化学强化也有效地抑制玻璃强度降低的化学强化玻璃。用于解决问题的手段本发明人等发现,通过使化学强化玻璃的表层中的氢浓度分布为特定的范围并且表面粗糙度(Ra)为特定值以上,即使不研磨化学强化后的玻璃表面或不进行使用氢氟酸的蚀刻处理,玻璃的面强度也会显著提高,并且面强度的可靠性提高,从而完成了本发明。即,本发明如下所示。<1>一种化学强化玻璃,其在表层具有通过离子交换法形成的压应力层,其中,表面粗糙度(Ra)为0.20nm以上,从玻璃的最外表面起的深度X的区域中的氢浓度Y在X=0.1~0.4(μm)的情况下满足下述关系式(I),通过环上球试验在下述条件下测定的面强度F(N)对于玻璃板的板厚t(mm)为F≥1500×t2,并且在表面上没有磨痕,Y=aX+b(I)式(I)中的各符号的含义如下所示:Y:氢浓度(按H2O换算,mol/L),X:从玻璃最外表面起的深度(μm),a:-0.270~-0.005,b:0.020~0.220,环上球试验条件:将板厚t(mm)的玻璃板配置在直径30mm、接触部具有曲率半径2.5mm的圆度的不锈钢环上,在使直径10mm的钢球体与该玻璃板接触的状态下,将该球体在静荷载条件下荷载于该环的中心,将玻璃被破坏时的破坏荷载(单位N)作为BOR强度,将该BOR强度的20次的测定平均值作为面强度F。其中,将玻璃的破坏起点距离该球体的荷载点2mm以上的情况从用于计算平均值的数据中除去。<2>上述<1>所述的化学强化玻璃,其中,所述玻璃为铝硅酸盐玻璃、铝硼硅酸盐玻璃或钠钙玻璃。发明效果根据本发明的化学强化玻璃,通过使玻璃表层中的氢浓度分布为特定的范围并且表面粗糙度(Ra)为特定值以上,即使不研磨化学强化后的玻璃表面,也可以大幅提高玻璃的面强度并且提高面强度的可靠性。附图说明图1为用于说明环上球试验的方法的示意图。图2为表示本发明的化学强化玻璃的制造工序的示意图。图3为将实施例1、实施例2中得到的各化学强化玻璃的表层的氢浓度分布作图而得到的图。图4为将实施例3、实施例4中得到的各化学强化玻璃的表层的氢浓度分布作图而得到的图。图5为将比较例1、比较例2、比较例3中得到的各化学强化玻璃的表层的氢浓度分布作图而得到的图。图6为用于从将实施例1中得到的化学强化玻璃的表层的氢浓度分布作图而得到的图导出关系式(I)的说明图。图7为用于从将比较例1中得到的化学强化玻璃的表层的氢浓度分布作图而得到的图导出关系式(I)的说明图。图8为实施例1和比较例1中得到的各化学强化玻璃的BOR强度评价的威布尔图。图9为参考例1的化学强化玻璃表面的AFM图像。扫描区域为5×5μm2。图10为实施例1的化学强化玻璃表面的AFM图像。扫描区域为5×5μm2。图11为实施例3和参考例2中得到的各化学强化玻璃的BOR强度评价的威布尔图。图12为将实施例3和参考例2中得到的各化学强化玻璃的表层的氢浓度分布作图而得到的图。图13为具有表面磨痕的玻璃表面的AFM图像。图14为不具有表面磨痕的玻璃表面的AFM图像。具体实施方式以下,详细说明本发明,但是本发明并不限定于以下的实施方式,在不脱离本发明的主旨的范围内,可以任意变形后实施。在此,在本说明书中,“质量%”与“重量%”、“质量ppm”与“重量ppm”分别为同义。另外,在仅记载为“ppm”的情况下,表示“重量ppm”。<化学强化玻璃>本发明的化学强化玻璃为在表层具有通过离子交换法形成的压应力层的化学强化玻璃,其特征在于,从玻璃的最外表面起的一定深度区域中,氢浓度满足后述的关系式(I),且在玻璃表面上没有磨痕。压应力层是指通过使作为原料的玻璃与硝酸钾等无机盐接触,从而通过玻璃表面的Na离子与熔盐中的K离子发生离子交换而形成的高密度层。对于本发明的化学强化玻璃而言,玻璃表层中的氢浓度分布在特定的范围内。具体而言,从玻璃的最外表面起的深度X的区域中的氢浓度Y在X=0.1~0.4(μm)的情况下满足下述关系式(I),Y=aX+b(I)式(I)中的各符号的含义如下所示:Y:氢浓度(按H2O换算,mol/L),X:从玻璃最外表面起的深度(μm),a:-0.270~-0.005,b:0.020~0.220,关于玻璃的强度,虽然已知由于玻璃中氢(水分)的存在而玻璃的强度降低,但是本发明人等发现,有时在化学强化处理后玻璃的强度会降低,其主要原因是由于环境中的水分侵入到玻璃表层中而导致产生化学缺陷。另外还发现,该现象并不限于化学强化,在玻璃的制造工序中由于经历升温工序也会发生。当玻璃中的氢浓度高时,氢以Si-OH的形式进入玻璃的Si-O-Si键网络中,从而Si-O-Si键被切断。认为玻璃中的氢浓度高时,Si-O-Si键被切断的部分变多,容易生成化学缺陷,强度降低。上述的关系式(I)在从最外表面起的深度X=0.1~0.4μm的区域内成立。通过离子交换而形成的压应力层的厚度取决于化学强化的程度,可以在5~50μm的范围内形成。而且,氢侵入到玻璃中的深度取决于扩散系数、温度和时间,除了这些以外,环境中的水分量也会影响氢的侵入量。对于化学强化后的氢浓度而言,最外表面最高,到未形成压应力层的深部(主体)逐渐降低。上述关系式(I)为规定了其降低状况的关系式,在最外表面(X=0μm)处,由于经时劣化而水分浓度有可能变化,因此,在认为没有该影响的近表面(X=0.1~0.4μm)的区域内成立。式(I)中,a为规定该氢浓度的降低状况的斜率。a的范围为-0.270~-0.005,优选为-0.240~-0.030,更优选为-0.210~-0.050。式(I)中,b相当于最外表面(X=0μm)处的氢浓度。b的范围为0.020~0.220,优选为0.020~0.215,更优选为0.030~0.210,进一步优选为0.040~0.200。一般认为,玻璃的强度降低的原因在于,由于来自于外部的机械压力而使存在于玻璃表面的微小裂纹扩展。根据非专利文献2,考察了裂纹的前端的玻璃结构越是富Si-OH的状态,则裂纹越容易扩展。据推测,假定裂纹的前端暴露在环境中,则裂纹的前端的Si-OH量表现出与玻璃最外表面的氢浓度正相关。因此,相当于最外表面的氢浓度的b优选为上述所示程度的低范围。如图3~5所示,对于经过化学强化工序的玻璃,没有确认到氢的侵入深度显著不同。氢的侵入深度取决于化学强化工序条件,变化的可能性高,但是如果没有变化,则相当于最外表面的氢浓度的b表现出与相当于规定氢浓度的降低状况的斜率的a负相关。因此,a优选为上述所示程度的高范围。可见,在本发明中并不是仅规定表层的氢浓度本身,而是着眼于氢浓度分布,发现通过将表层氢浓度与其降低状况规定在特定的范围内,能够大幅提高化学强化玻璃的强度。[氢浓度分布测定方法]在此,玻璃的氢浓度分布(H2O浓度、mol/L)为在以下的分析条件下测定的分布。在玻璃基板的氢浓度分布的测定中,使用二次离子质谱分析法(SecondaryIonMassSpectrometory:SIMS)。在使用SIMS得到定量的氢浓度分布的情况下,需要氢浓度已知的标准试样。标准试样的制作方法和氢浓度定量方法如下所示。1)将测定对象的玻璃基板的一部分切下。2)将从切下的玻璃基板的表面起的50μm以上的区域,通过研磨或化学蚀刻除去。除去处理在两面都进行。即,两面上的除去厚度为100μm以上。将该除去处理后的玻璃基板作为标准试样。3)对标准试样实施红外光谱法(Infraredspectroscopy:IR),求出IR谱图的3550cm-1附近的峰顶的吸光度高度A3550和4000cm-1的吸光度高度A4000(基线)。4)用千分尺等板厚测定器测定标准试样的板厚d(cm)。5)以文献A作为参考,设定玻璃的H2O的红外实际吸光系数εpract(L/(mol·cm))为75,使用式II求出标准试样的氢浓度(按H2O换算、mol/L)。标准试样的氢浓度=(A3550-A4000)/(εpract·d)式II文献A)S.Ilievski等人,Glastech.Ber.GlassSci.Technol.,73(2000)39.将作为测定对象的玻璃基板与通过上述方法得到的氢浓度已知的标准试样同时传送到SIMS装置内,依次进行测定,获得1H-和30Si-的强度的深度方向分布。之后,从1H-分布除以30Si-分布,得到1H-/30Si-强度比的深度方向分布。由标准试样的1H-/30Si-强度比的深度方向分布计算深度1μm~2μm的区域中的平均1H-/30Si-强度比,并以通过原点的方式制作该值与氢浓度的校准线(一级的标准试样的校准线)。使用该校准线,将作为测定对象的玻璃基板的分布的纵轴的1H-/30Si-强度比变换成氢浓度。由此,得到作为测定对象的玻璃基板的氢浓度分布。需要说明的是,SIMS和IR的测定条件如下所示。[SIMS的测定条件]装置:アルバック·ファイ公司制ADEPT1010一次离子种:Cs+一次离子加速电压:5kV一次离子电流值:500nA一次离子入射角:相对于试样面的法线为60°一次离子栅网尺寸:300×300μm2二次离子的极性:负二次离子的检测区域:60×60μm2(一次离子栅网尺寸的4%)ESAInputLens:0中和枪的使用:有将横轴从溅射时间变换为深度的方法:通过触针式表面形状测定器(例如,Veeco公司制的Dektak150)测定分析弧坑的深度,求出一次离子的溅射速率。使用该溅射速率,将横轴从溅射时间变换为深度。1H-检测时的场轴电压(FieldAxisPotential):对于每个装置最佳值有可能变化。测定者要注意将背景充分去掉,同时对值进行设定。[IR的测定条件]装置:ThermoFisherScientific公司制Nic-plan/Nicolet6700分辨率:4cm-1累计:16检测器:TGS检测器为了从通过上述分析条件测定的玻璃的氢浓度分布(H2O浓度、mol/L)导出关系式[I],使用以下的步骤。如图6和图7所示,对于0.1~0.4μm的深度区域的氢浓度分布进行线性近似。将所得到的近似直线的式子作为关系式[I]。另外,作为控制a和b的手段,可以列举例如:改变化学强化工序中的熔剂浓度、钠浓度、温度、时间等。另外,本发明的化学强化玻璃在近表面(从最外表面起的深度X=0.1~0.4μm)区域中的平均氢浓度c优选为0.070~0.150mol/L。认为通过平均氢浓度为该范围,除了具有高的面强度以外,面强度的可靠性也提高。需要说明的是,平均氢浓度c可以从上述氢浓度分布得到。(表面磨痕)本发明的化学强化玻璃在表面上不具有磨痕。在此,本发明中的研磨是指通过使用磨粒磨削玻璃表面而使其平滑化。另外,磨痕的有无可以通过利用AFM(AtomicForceMicroscope;原子力显微镜)的表面观察来判别,在10μm×5μm的区域内如果不存在两根以上的长度5μm以上且宽度0.1μm以上的划痕,则可以说是在表面上没有磨痕的状态。图13和图14中分别表示具有表面磨痕的状态和没有表面磨痕的状态。(玻璃强度)本发明的化学强化玻璃的强度可以通过环上球试验进行评价。(环上球试验)对于本发明的化学强化玻璃而言,在将玻璃板配置在直径30mm、接触部具有曲率半径2.5mm的圆度的不锈钢制成的环上,并且使直径10mm的钢制成的球体与该玻璃板接触的状态下,通过将该球体在静荷载条件下荷载于该环的中心,进行环上球试验(BallonRing;BOR),用测定的BOR强度F(N)来评价。本发明的化学强化玻璃为F≥1500×t2,更优选为F≥1800×t2[式中,F为通过环上球试验测定的BOR强度(N),t为玻璃基板的板厚(mm)]。通过BOR强度F(N)在该范围内,即使在薄板化的情况下也表现出优良的强度。图1中表示用于说明本发明中使用的环上球试验的示意图。环上球(BallonRing;BOR)试验中,在将玻璃板1水平载置的状态下,使用SUS304制的加压夹具(淬火钢、直径10mm、镜面精加工)对玻璃板1加压,并测定玻璃板1的强度。在图1中,将作为试样的玻璃板1水平设置在SUS304制的支撑夹具3(直径30mm、接触部的曲率R2.5mm、接触部为淬火钢、镜面精加工)上。在玻璃板1的上方,设置用于加压玻璃板1的加压夹具2。在本实施方式中,从实施例和比较例后得到的玻璃板1的上方,对玻璃板1的中央区域加压。需要说明的是,试验条件如下所示。加压夹具2的下降速度:1.0(mm/分钟)此时,将玻璃被破坏时的破坏荷载(单位N)作为BOR强度,将20次的测定的平均值作为BOR平均强度。但是,将玻璃板的破坏起点距球按压位置2mm以上的情况从用于计算平均值的数据中除去。本发明的化学强化玻璃如上所示除了具有高的面强度以外,面强度的可靠性也高。如后述的实施例中各化学强化玻璃的BOR强度评价的威布尔图所示,可知本发明的化学强化玻璃的面强度的变动小。其理由尚不明确,推测是由于玻璃表层附近的氢(水分)浓度稍高。(表面粗糙度)对于本发明的化学强化玻璃而言,进一步地,表面粗糙度(Ra)为0.20nm以上。通过表面粗糙度为上述数值以上,可以得到面强度高的化学强化玻璃。据推测,通过玻璃表面具有一定程度的表面粗糙度,可以抑制应力集中,使强度上升。表面粗糙度例如可以通过AFM表面观察并设定测定范围为1μm×1μm进行测定。需要说明的是,以往的未研磨的化学强化玻璃板的表面粗糙度小于0.20nm。[AFM的测定条件]装置:Bruker公司制NanoscopeV+MultiMode8或DimensionICON模式:ScanAsyst模式探针:RTESPA(弹簧常数:40N/m)试样/线(Samples/Line):256线(Lines):256扫描速率:1Hz测定视野:1×1μm2(对准无污染区域)<化学强化玻璃的制造方法>以下说明制造本发明的化学强化玻璃的方法的一个方式,但是本发明并不限定于此。(玻璃组成)本发明中使用的玻璃中含有钠即可,只要是具有能够成形、通过化学强化处理进行强化的组成的玻璃,就可以使用各种组成的玻璃。具体而言,可以列举例如:铝硅酸盐玻璃、钠钙玻璃、硼硅酸盐玻璃、铅玻璃、碱钡玻璃、铝硼硅酸盐玻璃等。玻璃的制造方法没有特别限定,可以将所需的玻璃原料投入到连续熔融炉中,将玻璃原料优选在1500~1600℃下加热熔融、澄清后,供给到成形装置,将熔融玻璃成形为板状,并缓慢冷却而制造。需要说明的是,玻璃的成形可以采用各种方法。例如可以采用:下拉法(例如溢流下拉法、流孔下引(SlotDown)法和重新引下(redraw)法等)、浮法、轧制成形法和压制法等各种成形方法。玻璃的厚度没有特别限制,但是为了有效地进行化学强化处理,通常优选为5mm以下,更优选为3mm以下。另外,本发明中使用的玻璃的形状没有特别限定。例如可以采用:具有均匀的板厚的平板形状、在表面和背面中的至少一者上具有曲面的形状以及具有弯曲部等的立体形状等各种形状的玻璃。作为本发明的化学强化玻璃的组成没有特别限定,例如可以列举以下的玻璃的组成。(i)以由摩尔%表示的组成计,含有SiO250~80%、Al2O32~25%、Li2O0~10%、Na2O0~18%、K2O0~10%、MgO0~15%、CaO0~5%和ZrO20~5%的玻璃。(ii)以由摩尔%表示的组成计,含有SiO250~74%、Al2O31~10%、Na2O6~14%、K2O3~11%、MgO2~15%、CaO0~6%和ZrO20~5%,SiO2和Al2O3的含量的合计为75%以下,Na2O和K2O的含量的合计为12~25%,MgO和CaO的含量的合计为7~15%的玻璃。(iii)以由摩尔%表示的组成计,含有SiO268~80%、Al2O34~10%、Na2O5~15%、K2O0~1%、MgO4~15%和ZrO20~1%的玻璃。(iv)以由摩尔%表示的组成计,含有SiO267~75%、Al2O30~4%、Na2O7~15%、K2O1~9%、MgO6~14%和ZrO20~1.5%,SiO2和Al2O3的含量的合计为71~75%,Na2O和K2O的含量的合计为12~20%,在含有CaO的情况下其含量小于1%的玻璃。本发明的化学强化玻璃在玻璃表面具有通过离子交换而得到的压应力层。离子交换法中,对玻璃的表面进行离子交换,形成残留压应力的表面层。具体而言,在玻璃化转变点以下的温度下,通过离子交换而将玻璃板表面的离子半径小的碱金属离子(典型的是Li离子、Na离子)置换成离子半径较大的碱金属离子(典型的是,对于Li离子而言为Na离子或K离子,对于Na离子而言为K离子)。由此,在玻璃的表面残留有压应力,玻璃的强度提高。在本发明的制造方法中,通过使玻璃与含有硝酸钾(KNO3)的无机盐接触而进行化学强化。由此,通过使玻璃中的Na离子与无机盐中的K离子进行离子交换,形成高密度的压应力层。作为使玻璃与无机盐接触的方法可以为:涂布糊状的盐的方法、向玻璃喷射无机盐的水溶液的方法、将玻璃浸渍于已加热到熔点以上的熔盐的盐浴的方法等。在这些之中,优选浸渍于熔盐的方法。作为无机盐,优选具有进行化学强化的玻璃的应变点(通常500~600℃)以下的熔点,本发明中优选含有硝酸钾(熔点300℃)的盐。通过含有硝酸钾而在玻璃的应变点以下为熔融状态,且在使用温度范围内操作容易,因此优选。无机盐中的硝酸钾的含量优选为50质量%以上。优选地,无机盐还含有选自由K2CO3、Na2CO3、KHCO3、NaHCO3、K3PO4、Na3PO4、K2SO4、Na2SO4、KOH和NaOH组成的组中的至少一种盐,其中,更优选含有选自由K2CO3、Na2CO3、KHCO3和NaHCO3组成的组中的至少一种盐。上述盐(以下有时也称为“熔剂”)具有切断以Si-O-Si键为代表的玻璃的网络的性质。由于进行化学强化处理的温度高达数百℃,因而在该温度下玻璃的Si-O间的共价键被适当切断,容易进行后述的低密度化处理。需要说明的是,切断共价键的程度根据玻璃组成、使用的盐(熔剂)的种类、进行化学强化处理的温度、时间等化学强化处理条件而不同,认为优选选择从Si伸出的4个共价键中切断1~2个键的程度的条件。例如在使用K2CO3作为熔剂的情况下,无机盐中的熔剂的含量为0.1摩尔%以上,化学强化处理温度为350~500℃时,则化学强化处理时间优选为1分钟~10小时,更优选为5分钟~8小时,进一步优选为10分钟~4小时。熔剂的添加量从控制表面氢浓度的方面出发优选0.1摩尔%以上,更优选1摩尔%以上,特别优选2摩尔%以上。另外,从生产率的观点出发优选为各盐的饱和溶解度以下。过量添加时,有可能造成玻璃的腐蚀。例如,在使用K2CO3作为熔剂的情况下,优选为24摩尔%以下,更优选为12摩尔%以下,特别优选为8摩尔%以下。无机盐除了硝酸钾和熔剂以外还可以在不损害本发明效果的范围内含有其它化学种类,例如,氯化钠、氯化钾、硼酸钠、硼酸钾等碱金属盐酸盐、硼酸盐等。这些可以单独添加,也可以组合添加多种。以下,以通过将玻璃浸渍于熔盐进行化学强化的方式为例,说明本发明的制造方法。(熔盐的制造1)熔盐可以通过下述所示的工序进行制造。工序1a:硝酸钾熔盐的制备工序2a:向硝酸钾熔盐添加熔剂(工序1a-硝酸钾熔盐的制备-)在工序1a中,将硝酸钾投入到容器中,并通过加热至熔点以上的温度使其熔融,由此制备熔盐。熔融在硝酸钾的熔点(330℃)与沸点(500℃)的范围内的温度下进行。特别是,设定熔融温度为350~470℃,从能够赋予玻璃的表面压应力(CS)与压应力层深度(DOL)的平衡和强化时间的观点出发是优选的。熔融硝酸钾的容器可以使用金属、石英、陶瓷等。其中,从耐久性的观点出发,金属材质是优选的,从耐腐蚀性的观点出发,不锈钢(SUS)材质是优选的。(工序2a-向硝酸钾熔盐中添加熔剂-)在工序2a中,在工序1a中制备的硝酸钾熔盐中添加上述的熔剂,将温度保持在恒定范围,同时通过搅拌叶片等进行混合使得整体成为均匀状态。在并用多种熔剂的情况下,添加顺序并不限定,可以同时添加。温度优选为硝酸钾的熔点以上,即330℃以上,更优选为350~500℃。另外,搅拌时间优选1分钟~10小时,更优选10分钟~2小时。(熔盐的制造2)在上述熔盐的制造1中,例示了在硝酸钾的熔盐的制备之后添加熔剂的方法,但是熔盐还可通过下述所述的工序制造。工序1b:硝酸钾与熔剂的混合工序2b:硝酸钾与熔剂的混合盐的熔融(1b-硝酸钾与熔剂的混合-)在工序1b中,将硝酸钾与熔剂投入到容器中,并通过搅拌叶片等进行混合。在并用多种熔剂的情况下,添加顺序并不限定,可以同时添加。容器可以使用与上述工序1a中使用的容器同样的容器。(工序2b-硝酸钾与熔剂的混合盐的熔融-)在工序2b中通过加热由工序1b得到的混合盐而使其熔融。熔融在硝酸钾的熔点(330℃)与沸点(500℃)的范围内的温度下进行。特别是,设定熔融温度为350~470℃,从能够赋予玻璃的表面压应力(CS)和压应力层深度(DOL)的平衡和强化时间的观点出发是更优选的。搅拌时间优选为1分钟~10小时,更优选为10分钟~2小时。在经由上述工序1a和工序2a或工序1b和工序2b而得到的熔盐中,在由于添加熔剂而产生析出物产生的情况下,在进行玻璃的化学处理前,进行静置直到该析出物沉淀到容器的底部。该析出物中含有:超出饱和溶解度部分的熔剂、熔剂的阳离子在熔盐中交换而得到的盐。对于在本申请发明的制造方法中使用的熔盐而言,Na浓度优选为500重量ppm以上,更优选为1000重量ppm以上。通过熔盐中的Na浓度为500重量ppm以上,通过后述的酸处理工序,容易深化低密度层,因此优选。作为Na浓度的上限没有特别限制,可以容许直至得到所期望的表面压应力(CS)。需要说明的是,在进行了一次以上的化学强化处理的熔盐中含有从玻璃溶出的钠。因此,只要Na浓度已在上述范围内,则可以将来源于玻璃的钠直接作为Na源使用,在Na浓度不足的情况下或者在使用化学强化未使用的熔盐的情况下,可以通过添加硝酸钠等无机钠盐而进行调节。以上,通过上述工序1a和工序2a或工序1b和工序2b,可以制备熔盐。(化学强化)接下来,使用制备的熔盐进行化学强化处理。化学强化处理通过将玻璃浸渍于熔盐中,将玻璃中的金属离子(Na离子)置换成熔盐中的离子半径大的金属离子(K离子)而进行。通过该离子交换改变玻璃表面的组成,从而可以形成玻璃表面高密度化的压应力层20[图2(a)~(b)]。通过该玻璃表面的高密度化而产生压应力,因此,可以将玻璃强化。需要说明的是,实际上对于化学强化玻璃的密度而言,从存在于玻璃中心的中间层30(主体)的外缘开始向压应力层表面密度逐渐增大,因此在中间层和压应力层之间没有密度急剧变化的明确的边界。在此,中间层是指在玻璃中心部存在的被压应力层夹持的层。该中间层与压应力层不同,为未进行离子交换的层。本发明中的化学强化处理具体而言可以根据下述工序3进行。工序3:玻璃的化学强化处理(工序3-玻璃的化学强化处理-)在工序3中,将玻璃预热,并将上述工序1a和工序2a或工序1b和工序2b中制备的熔盐调节至进行化学强化的温度。接着,将预热的玻璃浸渍于熔盐中规定时间,然后将玻璃从熔盐中拉起,并自然冷却。需要说明的是,对于玻璃,在化学强化处理前,优选进行根据用途的形状加工例如切断、端面加工和开孔加工等机械加工。玻璃的预热温度取决于浸渍于熔盐的温度,但是一般优选为100℃以上。化学强化温度优选为被强化玻璃的应变点(通常500~600℃)以下,为了得到更高的压应力层深度,特别优选为350℃以上。玻璃在熔盐中的浸渍时间优选为1分钟~10小时,更优选为5分钟~8小时,进一步优选为10分钟~4小时。只要在该范围内,就能够得到强度与压应力层深度的平衡优良的化学强化玻璃。在本发明的制造方法中接着在化学强化处理后进行下述工序。工序4:玻璃的清洗工序5:经过工序4后的玻璃的酸处理在经过上述工序5的时刻,在玻璃表面上,压应力层20的表层进一步具有劣化的、具体而言低密度化的低密度层10[图2(b)~(c)]。低密度层通过从压应力层的最外表面中除去(浸出)Na、K,取而代之渗入(置换)H而形成。以下,对于工序4和工序5进行详述。(工序4-玻璃的清洗-)在工序4中,使用工艺用水、离子交换水等进行玻璃的清洗。其中,优选离子交换水。清洗的条件根据使用的清洗液而不同,在使用离子交换水的情况下,从完全除去附着的盐的观点出发,优选在0~100℃下进行清洗。(工序5-酸处理-)在工序5中,对于工序4中洗净后的玻璃,进一步进行酸处理。玻璃的酸处理通过将化学强化玻璃浸渍于酸性的溶液中而进行,由此可以将化学强化玻璃表面的Na和/或K置换成H。只要溶液为酸性就没有特别限制,pH小于7即可,使用的酸可以为弱酸也可以为强酸。具体而言,优选盐酸、硝酸、硫酸、磷酸、乙酸、草酸、碳酸和柠檬酸等酸。这些酸可以单独使用,也可以组合使用多种。进行酸处理的温度根据使用的酸的种类、浓度、时间而不同,优选在100℃以下进行。进行酸处理的时间根据使用的酸的种类、浓度、温度而不同,从生产率的观点出发,优选10秒~5小时,更优选1分钟~2小时。进行酸处理的溶液的浓度根据使用的酸的种类、时间、温度而不同,但是优选腐蚀容器的可能性小的浓度,具体而言,优选0.1重量%~20重量%。对于低密度层而言,为了通过后述的碱处理而除去,低密度层越厚,玻璃表面越容易被除去。因此,低密度层的厚度从玻璃表面除去量的观点出发,优选为5nm以上,更优选为20nm以上。低密度层的厚度可以通过化学强化工序中的熔剂浓度、钠浓度、温度、时间等进行控制。低密度层的密度从玻璃表面除去性的观点出发,优选与比通过离子交换而得到的压应力层深的区域(主体)的密度相比较低。低密度层的厚度可以从通过X射线反射率法(X-ray-Reflectometry:XRR)测定的周期(Δθ)而求出。低密度层的密度可以通过由XRR测定的临界角(θc)而求出。需要说明的是,简易地通过用扫描型电子显微镜(SEM)观察玻璃的截面,也能够确认低密度层的形成和层的厚度。在本发明的制造方法中,接着在酸处理后进行下述工序。工序6:碱处理通过上述工序6,可以将在工序5之前形成的低密度层10的一部分或全部除去[图2(c)~(d)]。以下,对工序6进行详细说明。(工序6-碱处理-)在工序6中,对于工序5中酸处理后的玻璃,进一步进行碱处理。碱处理通过将化学强化玻璃浸渍于碱性的溶液中而进行,由此可以将低密度层的一部分或全部除去。只要溶液为碱性就没有特别限制,pH大于7即可,可以使用弱碱也可以使用强碱。具体而言,优选氢氧化钠、氢氧化钾、碳酸钾、碳酸钠等碱。这些碱可以单独使用,也可以组合使用多种。进行碱处理的温度根据使用的碱的种类、浓度、时间而不同,优选0~100℃,更优选10~80℃,特别优选20~60℃。只要为该温度范围,则玻璃不可能发生腐蚀,因此优选。进行碱处理的时间根据使用的碱的种类、浓度、温度而不同,从生产率的观点出发优选10秒~5小时,更优选1分钟~2小时。进行碱处理的溶液的浓度根据使用的碱的种类、时间、温度而不同,但是从玻璃表面除去性的观点出发,优选0.1重量%~20重量%。通过上述碱处理,侵入有H的低密度层的一部分或全部被除去,氢浓度分布满足前述特定的关系式(I)的表层露出。由此,可以得到面强度提高的化学强化玻璃。此外认为,通过除去低密度层,同时也除去了在玻璃表面上存在的损伤,因此这方面也有助于提高强度。在上述酸处理工序5和碱处理工序6之间、碱处理工序6结束后,优选具有与工序4同样的清洗工序。根据本发明的制造方法,由于操作的试剂液的安全性高,因此不需要特别的设备。因此,可以安全且有效地得到面强度显著提高的化学强化玻璃。需要说明的是,除去的低密度层的量取决于碱处理的条件。图2(d)中,表示低密度层10全部被除去后的形态,也可以除去低密度层10的一部分且残留一部分。从提高强度的观点出发,即使没有去除全部低密度层,也能够得到效果,但是从稳定地确保玻璃的透过率的观点出发,优选移除全部低密度层。实施例以下列举实施例对本发明进行具体说明,但是本发明并不限定于此。<评价方法>本实施例中的各种评价通过以下所示的分析方法进行。(玻璃的评价:表面应力)本发明的化学强化玻璃的压应力层的压应力值和压应力层的深度可以使用EPMA(electronprobemicroanalyzer)或表面应力计(例如折原制作所制、FSM-6000)等来测定。在实施例中,表面压应力值(CS、单位是MPa)和压应力层的深度(DOL、单位是μm)使用折原制作所公司制的表面应力计(FSM-6000)来测定。(玻璃的评价:除去量)玻璃的除去量厚度通过利用分析用电子天平(HR-202i;AND制)测定试剂液处理前后的重量,并使用下式进行厚度换算,从而求出。(每个单面的除去量厚度)=((处理前重量)-(处理后重量))/(玻璃比重)/处理面积/2此时,以玻璃比重为2.48(g/cm3)进行计算。(玻璃的评价:面强度)玻璃面强度通过环上球(BallonRing;BOR)试验来测定。图1中,表示用于说明本发明中使用的环上球试验的示意图。在将玻璃板1水平载置的状态下,使用SUS304制的加压夹具2(淬火钢、直径10mm、镜面精加工)对玻璃板1加压,并测定玻璃板1的强度。在图1中,将作为试样的玻璃板1水平地设置在SUS304制的支撑夹具3(直径30mm、接触部的曲率R2.5mm、接触部为淬火钢、镜面精加工)上。在玻璃板1的上方,设置用于加压玻璃板1的加压夹具2。在本实施方式中,从实施例和比较例后得到的玻璃板1的上方,对玻璃板1的中央区域加压。需要说明的是,实验条件如下所示。加压夹具2的下降速度:1.0(mm/分钟)此时,将玻璃被破坏时的破坏荷载(单位N)作为BOR强度,将20次的测定的平均值作为BOR平均强度。但是,将玻璃板的破坏起点距球按压位置2mm以上的情况从用于计算平均值的数据中除去。(玻璃的评价:表面粗糙度)通过使用AFM的下述条件,测定玻璃的表面粗糙度。[AFM的测定条件]装置:Bruker公司制NanoscopeV+MultiMode8或DimensionICON模式:ScanAsyst模式探针:RTESPA(弹簧常数:40N/m)试样/线(Samples/Line):256线(Lines):256扫描速率:1Hz测定视野:1×1μm2(对准无污染区域)(玻璃的评价:氢浓度)根据在上述的[氢浓度分布测定方法]中记载的方法,测定氢浓度分布,并导出关系式[I]和平均氢浓度(c值)。<实施例1>(化学强化工序)在SUS制的杯子中加入硝酸钾9700g、碳酸钾890g、硝酸钠400g,用覆套式加热器加热至450℃,从而制备碳酸钾6摩尔%、钠10000重量ppm的熔盐。准备50mm×50mm×0.56mm的铝硅酸盐玻璃A(比重为2.48),预热至200~400℃,然后浸渍于450℃的熔盐2小时,进行离子交换处理后,冷却至室温附近,由此进行化学强化处理。将得到的化学强化玻璃进行水洗,供给至后续的工序。铝硅酸盐玻璃A组成(以摩尔%计):SiO264.4%、Al2O38.0%、Na2O12.5%、K2O4.0%、MgO10.5%、CaO0.1%、SrO0.1%、BaO0.1%、ZrO20.5%(酸处理工序)在烧杯中准备13.4重量%的盐酸(HCl:关东化学公司制),使用水浴进行温度调节至41℃。将所述化学强化工序中得到的玻璃浸渍于调节后的盐酸中180秒,进行酸处理,之后用纯水清洗多次,然后用气流进行干燥。将由此而得到的玻璃供给至后续的工序。(碱处理工序)在烧杯中准备4.0重量%的氢氧化钠水溶液,使用水浴进行温度调节至40℃。将酸处理工序中得到的玻璃浸渍于调节后的氢氧化钠水溶液中120秒,进行碱处理,之后用纯水清洗多次,然后用气流进行干燥。通过上述方法,得到实施例1的化学强化玻璃。<实施例2>使用表1所示的板厚的铝硅酸盐玻璃A;将熔盐温度和离子交换处理时间分别设定为430℃、40分钟,使用玻璃平流式清洗机喷淋调节后的盐酸水溶液和氢氧化钠水溶液各自277秒,由此进行酸处理、碱处理。除此以外,与实施例1同样地制造了化学强化玻璃。<实施例3>使用50mm×50mm×0.72mm且下述组成的铝硅酸盐玻璃B(比重:2.41)代替铝硅酸盐玻璃A;在酸处理工序中,在树脂制的槽中准备6.0重量%的硝酸(HNO3;关东化学社制),使用含氟树脂被覆的加热器(KKS14A;八光电机制)进行温度调节至41℃;在调节后的硝酸中浸渍120秒而进行酸处理;除此以外,与实施例1同样地制造了化学强化玻璃。铝硅酸盐玻璃B组成(以摩尔%计):SiO268%、Al2O310%、Na2O14%、MgO8%<实施例4>使用50mm×50mm×0.70mm且下述组成的铝硼硅酸盐玻璃(比重:2.38)代替铝硅酸盐玻璃A;除此以外,与实施例3同样地制造了化学强化玻璃。铝硼硅酸盐玻璃组成(以摩尔%计):SiO267%、B2O34%、Al2O313%、Na2O14%、K2O<1%、MgO2%、CaO<1%<比较例1>在化学强化工序中熔盐中的钠量为表1中所示的值,碳酸钾添加量为0g,不实施酸处理工序、碱处理工序;除此以外,与实施例1同样地制造了化学强化玻璃。<比较例2>在化学强化工序中熔盐中的钠量为表1中所示的值,碳酸钾添加量为0g,不实施酸处理工序、碱处理工序;除此以外,与实施例2同样地制造了化学强化玻璃。<比较例3>在化学强化工序中熔盐中的钠量为表1中所示的值,碳酸钾添加量为0g,不实施酸处理工序、碱处理工序,除此以外,与实施例3同样地制造了化学强化玻璃。对于由此得到的化学强化玻璃进行各种评价。将结果示于表1。另外,在图3~5中,表示将实施例1~4和比较例1~3中得到的各化学强化玻璃的表层的氢浓度分布作图而得到的图。另外,图8表示实施例1和比较例1中得到的各化学强化玻璃的BOR强度评价的威布尔图。图8表示板厚为0.56mm的铝硅酸盐玻璃板样品的BOR强度评价结果的威布尔图。图的横轴表示破坏荷载σ(N)的对数ln(σ),与此相对,纵轴表示关于两组中的各组的样品的累计破坏概率百分数P(%)。表1根据表1的结果,表面粗糙度(Ra)为0.20nm以上且满足关系式(I)的实施例1~4,与比较例1~3相比,面强度大幅提高。另外,根据图8的结果,平均破坏荷载在实施例1中为827N,在比较例1中为455N。10%破坏荷载(B10)在实施例1中为793N,与此相对,在比较例1中为318N,1%破坏荷载(B1)在实施例1中为750N,与此相对,在比较例1中为200N。从该结果可知,实施例1是在不产生低强度制品的情况下对面强度的可靠性大幅提高的制品。(参考例1)将平均粒径1.2μm的氧化铈分散至水中而制作比重0.9的浆料,将与实施例3同样的铝硅酸盐玻璃B在研磨压力10kPa、研磨衬垫(无纺布型)的条件下单面研磨0.6μm。对由研磨工序得到的玻璃,使用与比较例3同样的熔盐,在化学强化处理温度450度,化学强化处理时间2小时的条件下进行化学强化。将进行各种评价的结果示于表1。将用AFM观察该玻璃表面所得到的图像示于图9。需要说明的是,通过AFM测定而测定的表面粗糙度(Ra)为0.40nm。另外,将实施例1中制造的化学强化玻璃的表面观察图像示于图10。需要说明的是,通过AFM测定而测定的表面粗糙度(Ra)为0.33nm。(参考例2)将与实施例3同样的铝硅酸盐玻璃B,使用与比较例3同样的熔盐,在化学强化处理温度450℃,化学强化处理时间2小时的条件下进行化学强化。将化学强化后的玻璃浸渍于包含浓度1.0重量%的氢氟酸和18.5重量%的盐酸的25℃的溶液中60秒,从而单面蚀刻1.06μm。然后,将参考例2和实施例3中得到的各化学强化玻璃的BOR强度评价的威布尔图示于图11。平均破坏荷载在实施例3中为1362N,在参考例2中为1266N。10%破坏荷载(B10)在实施例3中为1339N,与此相对,在参考例2中为1098N,1%破坏荷载(B1)在实施例3中为1307N,与此相对,在参考例2中为904N。从该结果可知,实施例3是在不产生低强度制品的情况下对面强度的可靠性大幅提高的制品。另外,将参考例2和实施例3中得到的各化学强化玻璃的表面的氢浓度分布示于图12。实施例3的表面氢浓度高于参考例2的表面氢浓度。参考例2中近表面(从最外表面起的深度X=0.1~0.4μm)的区域的平均氢浓度c低于实施例1~4的平均氢浓度c。由此推测,理由尚不明确,但是面强度的可靠性的提高是由于玻璃表层附近的氢(水分)浓度稍高。详细且参照特定的实施方式说明了本发明,但是在不脱离本发明的精神和范围的前提下可以施加各种变更、修正,这对于本领域技术人员而言是显而易见的。本申请基于2013年7月19日申请的日本专利申请(日本特愿2013-151116),其内容作为参照并入本文。产业实用性根据本发明,能够安全且低成本地得到面强度大幅提高的化学强化玻璃。本发明的化学强化玻璃可以用于手机、数码相机或触控面板显示器等显示器用保护玻璃。附图标记10低密度层20压应力层30中间层