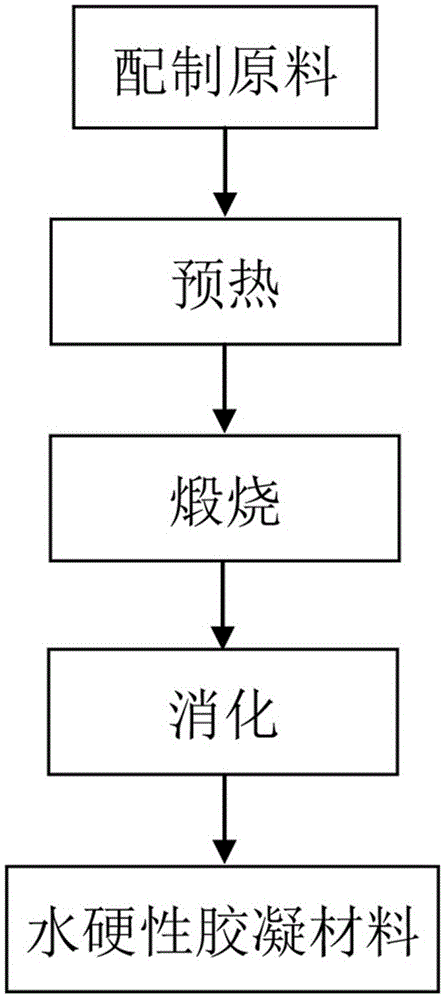
本发明属于建筑材料
技术领域:
,更具体地讲,涉及一种水硬性胶凝材料及其制备方法。
背景技术:
:水硬性胶凝材料可以作为建筑材料,其主要特征不同于石灰和水泥。与石灰相比,水硬性胶凝材料具有凝结速度快,粘度好,附着力强,具有高耐水性,高机械强度;与水泥相比,可使墙壁透气,保持呼吸,有利于水蒸气的交换,并具有很好的抗冻性和耐碱性,柔韧性好,可加工性好,自修复能力强等特点。由于水硬性胶凝材料的硬化速率较慢,水化放热量较低,从而避免了快速固化引起的内应力,使其具有良好的韧性。在国外,水硬性胶凝材料可以用于替代水泥制备装饰砂浆,清水混凝土,并大量用于文物保护与古建筑修复上。国内引进水硬性胶凝材料主要应用于历史建筑的修缮加固等方面,可以消除硫酸盐对历史建筑的侵蚀。目前国内对以石灰石尾矿来生产水硬性胶凝材料的研究属于空白。技术实现要素:针对现有技术中存在的不足,本发明的目的之一在于解决上述现有技术中存在的一个或多个问题。例如,本发明的目的之一在于提供一种合理利用资源的水硬性胶凝材料及其制备方法。为了实现上述目的,本发明的一方面提供了一种水硬性胶凝材料制备方法,所述制备方法可以包括以下步骤:配制原料;将配制后的原料粉磨、预热,在950℃~1200℃温度条件下煅烧,冷却,消化,干燥后得到水硬性凝胶材料,其中,所述配制原料包括将品位相同或者品位不同的石灰石尾矿破碎后混合,控制混合石灰石尾矿的氧化钙与氧化硅质量比为0.85~6.90,所述品位相同或者品位不同的石灰石尾矿的化学成分包括,按质量百分比计,31.8%~49%的氧化钙、7.1%~37.6%的氧化硅以及不超过4.5%的氧化铝。在本发明的水硬性胶凝材料制备方法的一个示例性实施例中,所述品位相同或者品位不同的石灰石尾矿在950℃加热0.5小时情况下的烧失量为25%~39%。在本发明的水硬性胶凝材料制备方法的一个示例性实施例中,所述煅烧的温度为950℃~1200℃,煅烧的升温速度可以为5℃/min~50℃/min,煅烧时间可以不超过1小时。在本发明的水硬性胶凝材料制备方法的一个示例性实施例中,所述消化可以包括测定煅烧冷却后产物中的游离氧化钙含量,在湿度为50%~90%的环境中循环消化,记录消化前后产物重量变化,当产物中的游离氧化钙消化率达到98%时,消化结束。在本发明的水硬性胶凝材料制备方法的一个示例性实施例中,所述预热温度可以为750℃~950℃,预热时间可以为0.5小时~1小时。在本发明的水硬性胶凝材料制备方法的一个示例性实施例中,所述水硬性胶凝材料在0.2mm筛余量可以不超过2%,0.09mm筛余量可以不超过15%。在本发明的水硬性胶凝材料制备方法的一个示例性实施例中,按质量百分比计,所述水硬性胶凝材料中的氢氧化钙含量为15%~78%,三氧化硫含量不超过2.0%。在本发明的水硬性胶凝材料制备方法的一个示例性实施例中,所述方法还包括控制所述混合石灰石尾矿的氧化钙与氧化硅质量比以制备抗压强度不同的水硬性胶凝材料,其中,控制氧化钙与氧化硅的质量比为0.85~1.04,制备得到的水硬性胶凝材料养护28天的抗压强度范围为5mpa~15mpa,水硬性胶凝材料中的氢氧化钙含量不低于15%;控制氧化钙与氧化硅的质量比大于1.04并小于1.27,制备得到的水硬性胶凝材料养护28天的抗压强度范围为3.5mpa~10mpa,水硬性胶凝材料中的氢氧化钙含量不低于25%;控制氧化钙与氧化硅的质量比为1.27~6.90,制备得到的水硬性胶凝材料养护28天的抗压强度范围为2.0mpa~7.0mpa,水硬性胶凝材料中的氢氧化钙含量不低于35%。本发明的另一方面提供了一种水硬性胶凝材料,所述水硬性胶凝材料由所述的水硬性胶凝材料制备方法所制备得到,所述水硬性胶凝材料可以包括,按质量百分比计,15%~78%的氢氧化钙以及不超过2.0%的三氧化硫,所述水硬性胶凝材料标准养护7天的抗压强度为0.9mpa~4.0mpa,标准养护28天的抗压强度为2.0mpa~15mpa。在本发明的水硬性胶凝材料的一个示例性实施例中,所述水硬性胶凝材料的0.2mm筛余量可以不超过2%,0.09mm筛余量可以不超过15%。与现有技术相比,本发明的水硬性胶凝材料制备方法能够合理利用石灰石尾矿,能够实现资源的最大化利用,工艺操作简单,适用于工业大规模生产;水硬性胶凝材料可以大量应用在文物保护,古建筑修复,历史建筑的修缮加固等方面,具有柔性和施工性好,粘性好并对墙体有很强的附着力,能使墙体透气保持呼吸有利于水蒸气的交换,具有较高的防水性,有很好的自我修复性,有很好的抗冻性,有很好的抗盐性,价格便宜,经济型好等优点。附图说明通过下面结合附图进行的描述,本发明的上述和其他目的和特点将会变得更加清楚,其中:图1示出了本发明一个示例性实施例的水硬性胶凝材料制备方法的部分工序流程示意图。具体实施方式在下文中,将结合附图和示例性实施例详细地描述根据本发明的一种水硬性胶凝材料及其制备方法。具体来讲,本发明的方法通过把同一矿区不同位置的石灰石尾矿或者不同矿区的石灰石尾矿进行混合配比,由于同一矿区不同位置的石灰石尾矿或者不同矿区的石灰石尾矿之间的成分含量存在一定差异,按照氧化钙和氧化硅规定的配比范围,将成分含量不同或者达到氧化钙和氧化硅规定配比的相同的石灰石尾矿进行混料,将混合后的石灰石尾矿作为原料,通过干燥,破碎,煅烧,消化等工艺步骤来制备胶凝材料,能够将石灰石尾矿进行合理利用,确保资源合理利用最大化。图1示出了一个示例性实施例的水硬性胶凝材料制备方法的部分工序流程示意图。本发明的一方面提供了一种水硬性胶凝材料制备方法,在本发明的水硬性胶凝材料制备方法的一个示例性实施例中,如图1所示,所述制备方法可以包括:步骤s01,配制原料。在本实施例中,以石灰石尾矿作为主要原料制备水硬性胶凝材料。同一矿山不同位置的石灰石尾矿或者不同矿山的石灰石尾矿可能存在品位上的差距,由于本发明的原料需要保证氧化钙和氧化硅的比值含量以及氧化铝含量满足一定的要求,对于某一些氧化钙和氧化硅比值含量达不到配比要求或者氧化铝含量达不到要求的石灰石尾矿,利用不同位置的石灰石尾矿的品位含量之间的差异,通过将不同品位的石灰石尾矿进行配料以满足氧化钙与氧化硅的比值范围以及氧化铝含量要求。对于化学成分含量原本就满足要求的石灰石尾矿,可以作为原料直接使用,并不需要进行配料。所述石灰石尾矿可以包括石灰石和硅质黏土。以上,氧化钙与氧化硅的质量比可以为0.85~6.90。对于不同的氧化钙与氧化硅的比值可以生产出抗压强度不同的水硬性胶凝材料。例如,对于控制氧化钙与氧化硅的比值大约在0.85~1.04时,可以制备得到的水硬性胶凝材料养护28天的抗压强度范围为(5mpa,15mpa)。对于控制氧化钙与氧化硅的比值大约在大于1.04并小于1.27时,可以制备得到的水硬性胶凝材料养护28天的抗压强度范围为(3.5mpa,10mpa)。对于控制氧化钙与氧化硅的比值大约在1.27~6.90时,可以制备得到的水硬性胶凝材料养护28天的抗压强度范围为(2.0mpa,7.0mpa)。并且,不同的氧化钙与氧化硅含量比值得到的水硬性胶凝材料中的氢氧化钙含量对同。例如,对于氧化钙与氧化硅的比值大约在0.85~1.04时,氢氧化钙的含量不低于15%;比值为大于1.04并小于1.27时,氢氧化钙含量不低于25%;比值为1.27~6.90时,氢氧化钙含量不低于35%。设置上述氧化钙与氧化硅质量配比为0.85~6.90的好处在于,如果低于上述设置的下限或者超过设置的上限,均会使生产制备的胶凝材料中的氢氧化钙含量达不到要求,影响产品性能。对于品位相同或者品位不同的石灰石尾矿的化学成分含量可以包括,按质量百分比计,31.8%~49%的氧化钙、7.1%~37.6%的氧化硅以及不超过4.5%的氧化铝。优选的,按质量百分比计,石灰石尾矿可以包括32%~47.5%的氧化钙、8.3%~36.8%的氧化硅以及不超过4.0%的氧化铝,更优选的,按质量百分比计,石灰石尾矿可以包括35%~45%的氧化钙、8.6%~35%的氧化硅以及不超过3.2%的氧化铝。对于石灰石尾矿中所包含的其他成分为一些不可避免的元素,例如,可以包括三氧化二铁、三氧化硫、氧化钾、氧化镁以及二氧化钛等。设置上述石灰石尾矿成分的好处在于能够满足水硬性胶凝材料的生产需要,能够通过调节上述设置范围内石灰石尾矿的化学成分,可以控制胶凝材料中成分含量,可以生产不同强度的水硬性胶凝材料。如果低于上述设置的下限或者超过设置的上限,均会使生产制备的胶凝材料中的氢氧化钙含量达不到要求,影响产品性能。在本实施例中,所述品位相同或者品位不同的石灰石尾矿在950℃加热0.5小时情况下的烧失量为25%~39%。以上,根据生产的需要,可以对石灰石尾矿进行破碎处理。破碎的粒径可以根据经验值或者现场进行确定。破碎完毕后,可以运送至不同的堆场进行预均化,然后根据确定的氧化钙和氧化硅的配值以及规定的氧化铝含量进行配料。步骤s02,将配制后的原料粉磨、预热,在950℃~1200℃温度条件下煅烧,冷却,消化,干燥后得到水硬性凝胶材料。在本实施例中,可以对配制完成后的原料进行粉磨。例如,可以利用球磨机进行球磨1~3小时,并可以对球磨后的原料进行筛分,例如,可以过160~190目筛。当然,对于本发明的粉磨以及筛分不限于此。在本实施例中,原料的预热温度可以为750℃~950℃,优选的,预热温度可以为800℃~900℃,例如,可以为850℃。预热时间可以根据现场原料的量进行确定,例如,为了节约能耗的同时达到较好的预热效果,预热的时间可以为0.5小时~1小时。以上,将配制后的原料粉磨是为了让石灰石尾矿间能够更好反应。预热是为了分解石灰石尾矿中的碳酸钙。在本实施例中,优选的,煅烧温度可以为950℃~1200℃,例如,煅烧温度可以为1040℃。煅烧的升温速度可以为5℃/min~50℃/min,煅烧时间不超过1小时。优选的,煅烧升温速度可以为10℃/min~40℃/min。煅烧可以使用立窑或者隧道窑进行煅烧。煅烧的好处在于,能够确保氧化钙和二氧化硅之间能够反应,升温速度越快反应完全的煅烧保温时间会越长,升温速度越慢所需保温时间越短。在本实施例中,冷却可以在空气中进行自然冷却至室温。在本实施例中,冷却完成后需要对产物进行消化。所述消化可以包括产物冷却完毕后测定冷却后产物中的游离氧化钙含量,在湿度为50%~90%的环境中循环消化,记录消化前后产物重量变化,当产物中的游离氧化钙消化率达到98%时,消化结束。在本实施例中,产物消化完成后,可以对消化后的产物进行干燥,粉磨以使产品达到需要的粒度。干燥的温度和时间、粉磨的方式和时间均可以是经验值或者根据现场进行确定。例如,粉磨可以是球磨机进行粉磨,粉磨的时间可以为1小时~3小时。当然,本发明的粉磨不限于此。粉磨完成后,产品水硬性胶凝材料的粒度满足0.2mm筛余量不超过2%,0.09mm筛余量为不超过15%。例如,0.09mm筛余量可以为5%~15%。水硬性胶凝材料的堆积密度可以为453kg/m3-595kg/m3。在本实施例中,按质量百分比计,所述胶凝材料中的氢氧化钙含量可以为15%~78%,三氧化硫含量可以不超过2%,所述水硬性胶凝材料标准养护7天的抗压强度为0.9mpa~4.0mpa,标准养护28天的抗压强度为2mpa~15mpa。在本实施例中,干燥后可以对水硬性凝胶材料进行粉磨以得到不同粒径的水硬性凝胶材料。本发明的另一方面提供了一种水硬性胶凝材料,在本发明的水硬性胶凝材料的一个示例性实施例中,所述水硬性胶凝材料可以由以上所述的水硬性胶凝材料制备方法所制备得到,所述水硬性胶凝材料可以包括,按质量百分比计,15%~78%的氢氧化钙以及不超过2%的三氧化硫,所述水硬性胶凝材料标准养护7天的抗压强度为0.9mpa~4.0mpa,标准养护28天的抗压强度为2.0mpa~15mpa。在本实施例中,所述胶凝材料0.2mm筛余量可以不超过2%,0.09mm筛余量可以不超过15%。例如,0.09mm筛余量可以为5%~15%。以上,在本发明的水硬性胶凝材料中含有硅酸二钙和氢氧化钙,硅酸二钙(c2s)是主要的水化反应相,它是由石灰石尾矿中可溶性二氧化硅与碳酸钙脱碳后的氧化钙在一定温度下的结合生成的。c2s含量越高其水硬程度也就越高,c2s含量越低其水硬程度也就越低。水硬性胶凝材料在空气中硬化的主要相是ca(oh)2相,其硬化机理类似于气硬性石灰,ca(oh)2是在消化过程中原料煅烧后产生的氧化钙与空气中的水结合而生成的,其含量越高最终水硬性胶凝材料的水硬程度也就越低,其含量低最终水硬性胶凝材料的水硬程度也就越高。水硬性胶凝材料可以通过上述水硬性胶凝材料制备方法所制备得到。为了更好地理解本发明的上述示例性实施例,下面结合具体示例对其进行进一步说明。示例1按氧化钙和氧化硅的质量比0.85进行石灰石尾矿配料,其制备方法包括:1)将同一矿区不同位置的石灰石尾矿破碎后进行预均化;2)按照所需氧化钙和氧化硅的质量比0.85,进行配料;3)原料经经粉磨1.5小时,至180目筛余量为2%;4)将生料于高温炉中在950℃下预热分解0.5小时;5)预热分解后置于高温炉中在1050℃温度下煅烧0.5小时;煅烧完成后自然冷却至室温后测定其游离氧化钙含量;6)在湿度为65%的环境中消化,记录消化前后产物重量变化,当产物中的游离氧化钙消化率达到98%时,消化结束;7)消化完成并烘干后,粉磨2.3小时,当0.2mm筛余量不超过2%,0.09mm筛余量不超过15%时,即制得水硬性胶凝材料。示例2按氧化钙和氧化硅的质量比0.95进行石灰石尾矿配料,其制备方法包括:1)将同一矿区不同位置的石灰石尾矿破碎后进行预均化;2)按照所需氧化钙和氧化硅的质量比0.95,进行配料;3)原料经经粉磨1.8小时,至180目筛余量为2%;4)将生料于高温炉中在950℃下预热分解0.5小时;5)预热分解后置于高温炉中在1050℃温度下煅烧0.5小时;煅烧完成后自然冷却至室温后测定其游离氧化钙含量;6)在湿度为65%的环境中消化,记录消化前后产物重量变化,当产物中的游离氧化钙消化率达到98%时,消化结束;7)消化完成后并烘干后,粉磨2.4小时,当0.2mm筛余量不超过2%,0.09mm筛余量不超过15%时,即制得水硬性胶凝材料。示例3按氧化钙和氧化硅的质量比1.05进行石灰石尾矿配料,其制备方法包括:1)将同一矿区不同位置的石灰石尾矿破碎后进行预均化;2)按照所需氧化钙和氧化硅的质量比1.05,进行配料;3)原料经经粉磨2小时,至180目筛余量为2%;4)将生料于高温炉中在950℃下预热分解0.5小时;5)预热分解后置于高温炉中在1200℃温度下煅烧0.5小时;煅烧完成后自然冷却至室温后测定其游离氧化钙含量;6)在湿度为65%的环境中消化,记录消化前后产物重量变化,当产物中的游离氧化钙消化率达到98%时,消化结束;7)消化完成后并烘干后,粉磨2.4小时,当0.2mm筛余量不超过2%,0.09mm筛余量不超过15%时,即制得水硬性胶凝材料。示例4:按氧化钙和氧化硅的质量比1.10进行石灰石尾矿配料,其制备方法包括:1)将同一矿区不同位置的石灰石尾矿破碎后进行预均化;2)按照所需氧化钙和氧化硅的质量比1.10,进行配料;3)原料经经粉磨2小时,至180目筛余量为2%;4)将生料于高温炉中在950℃下预热分解0.5小时;5)预热分解后置于高温炉中在1200℃温度下煅烧0.5小时;煅烧完成后自然冷却至室温后测定其游离氧化钙含量;6)在湿度为65%的环境中消化,记录消化前后产物重量变化,当产物中的游离氧化钙消化率达到98%时,消化结束;7)消化完成后并烘干后,粉磨2.4小时,当0.2mm筛余量不超过2%,0.09mm筛余量不超过15%时,即制得水硬性胶凝材料。示例5按氧化钙和氧化硅的质量比1.15进行石灰石尾矿配料,其制备方法包括:1)将同一矿区不同位置的石灰石尾矿破碎后进行预均化;2)按照所需氧化钙和氧化硅的质量比1.15,进行配料;3)原料经经粉磨2小时,至180目筛余量为2%;4)将生料于高温炉中在950℃下预热分解0.5小时;5)预热分解后置于高温炉中在1200℃温度下煅烧0.5小时;煅烧完成后自然冷却至室温后测定其游离氧化钙含量;6)在湿度为65%的环境中消化,记录消化前后产物重量变化,当产物中的游离氧化钙消化率达到98%时,消化结束;7)消化完成后并烘干后,粉磨2.4小时,当0.2mm筛余量不超过2%,0.09mm筛余量不超过15%时,即制得水硬性胶凝材料。示例6按氧化钙和氧化硅的质量比1.25进行石灰石尾矿配料,其制备方法包括:1)将同一矿区不同位置的石灰石尾矿破碎后进行预均化;2)按照所需氧化钙和氧化硅的质量比1.25,进行配料;3)原料经经粉磨2小时,至180目筛余量为2%;4)将生料于高温炉中在950℃下预热分解0.5小时;5)预热分解后置于高温炉中在1150℃温度下煅烧0.5小时;煅烧完成后自然冷却至室温后测定其游离氧化钙含量;6)在湿度为65%的环境中消化,记录消化前后产物重量变化,当产物中的游离氧化钙消化率达到98%时,消化结束;7)消化完成后并烘干后,粉磨2.4小时,当0.2mm筛余量不超过2%,0.09mm筛余量不超过15%时,即制得水硬性胶凝材料。示例7按氧化钙和氧化硅的质量比1.55进行石灰石尾矿配料,其制备方法包括:1)将同一矿区不同位置的石灰石尾矿破碎后进行预均化;2)按照所需氧化钙和氧化硅的质量比1.55,进行配料;3)原料经经粉磨2小时,至180目筛余量为2%;4)将生料于高温炉中在950℃下预热分解0.5小时;5)预热分解后置于高温炉中在1150℃温度下煅烧0.5小时;煅烧完成后自然冷却至室温后测定其游离氧化钙含量;6)在湿度为65%的环境中消化,记录消化前后产物重量变化,当产物中的游离氧化钙消化率达到98%时,消化结束;7)消化完成后并烘干后,粉磨2.4小时,当0.2mm筛余量不超过2%,0.09mm筛余量不超过15%时,即制得水硬性胶凝材料。示例8按氧化钙和氧化硅的质量比3.0进行石灰石尾矿配料,其制备方法包括:1)将同一矿区不同位置的石灰石尾矿破碎后进行预均化;2)按照所需氧化钙和氧化硅的质量比3.0,进行配料;3)原料经经粉磨2小时,至180目筛余量为2%;4)将生料于高温炉中在950℃下预热分解0.5小时;5)预热分解后置于高温炉中在1150℃温度下煅烧0.5小时;煅烧完成后自然冷却至室温后测定其游离氧化钙含量;6)在湿度为65%的环境中消化,记录消化前后产物重量变化,当产物中的游离氧化钙消化率达到98%时,消化结束;7)消化完成后并烘干后,粉磨2.4小时,当0.2mm筛余量不超过2%,0.09mm筛余量不超过15%时,即制得水硬性胶凝材料。示例9按氧化钙和氧化硅的质量比5.0进行石灰石尾矿配料,其制备方法包括:1)将同一矿区不同位置的石灰石尾矿破碎后进行预均化;2)按照所需氧化钙和氧化硅的质量比5.0,进行配料;3)原料经经粉磨2小时,至180目筛余量为2%;4)将生料于高温炉中在950℃下预热分解0.5小时;5)预热分解后置于高温炉中在1150℃温度下煅烧0.5小时;煅烧完成后自然冷却至室温后测定其游离氧化钙含量;6)在湿度为65%的环境中消化,记录消化前后产物重量变化,当产物中的游离氧化钙消化率达到98%时,消化结束;7)消化完成后并烘干后,粉磨2.4小时,当0.2mm筛余量不超过2%,0.09mm筛余量不超过15%时,即制得水硬性胶凝材料。示例10按氧化钙和氧化硅的质量比6.9进行石灰石尾矿配料,其制备方法包括:1)将同一矿区不同位置的石灰石尾矿破碎后进行预均化;2)按照所需氧化钙和氧化硅的质量比6.9,进行配料;3)原料经经粉磨2小时,至180目筛余量为2%;4)将生料于高温炉中在950℃下预热分解0.5小时;5)预热分解后置于高温炉中在1150℃温度下煅烧0.5小时;煅烧完成后自然冷却至室温后测定其游离氧化钙含量;6)在湿度为65%的环境中消化,记录消化前后产物重量变化,当产物中的游离氧化钙消化率达到98%时,消化结束;7)消化完成后并烘干后,粉磨2.4小时,当0.2mm筛余量不超过2%,0.09mm筛余量不超过15%时,即制得水硬性胶凝材料。对水硬性胶凝材料的抗压强度进行测试。称取水硬性胶凝材料450±2g,标准砂1350±5g,水270±1g,水灰比根据其松散堆积密度确定,制成40mm×40mm×160mm标准试样,将制备好的试块在恒温恒湿标准养护箱中养护。分别测定水硬性胶凝材料的各项指标。示例1~10的水硬性胶凝材料的性能如表1所示:表1示例堆积密度(kg/m3)7d/mpa28d/mpaca(oh)2(wt%)15683.615.015.125483.211.520.235232.56.925.144961.95.828.155321.64.730.465861.23.934.075341.13.642.885870.92.561.595960.72.370.3105190.32.177.5示例1~10的原料化学成分如表2所示:表2从以上数据可以看出,本发明的示例1-3制得水硬性胶凝材料的强度7d/mpa>2mpa,5mpa<28d/mpa<15mpa,水硬性胶凝材料强度较高;示例4-6制得水硬性胶凝材料的强度3.5mpa≤28d/mpa<10mpa,水硬性胶凝材料强度其次;示例7-10制得水硬性胶凝材料的强度2.0mpa<28d/mpa<7mpa,水硬性胶凝材料强度较小。综上所述,本发明的水硬性胶凝材料的制备方法能够合理利用石灰石尾矿,能够实现资源的最大化利用,工艺操作简单,适用于大规模生产;水硬性胶凝材料大量应用在文物保护及古建筑修复方面,历史建筑的修缮加固等方面,具有柔性和施工性好,粘性好并对墙体有很强的附着力,能使墙体透气保持呼吸有利于水蒸气的交换,具有较高的防水性,有很好的自我修复性,有很好的抗冻性,有很好的抗盐性,价格便宜,经济型好等优点。尽管上面已经通过结合示例性实施例描述了本发明,但是本领域技术人员应该清楚,在不脱离权利要求所限定的精神和范围的情况下,可对本发明的示例性实施例进行各种修改和改变。当前第1页12