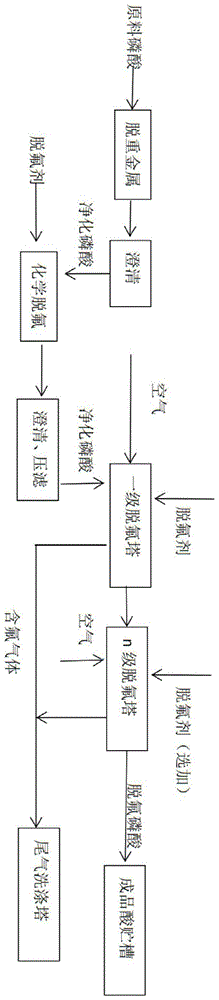
本发明涉及湿法磷酸脱氟工艺领域,具体涉及一种沉淀预脱氟与汽提脱氟耦合的湿法磷酸脱氟方法。
背景技术:
:20世纪50年代以来,世界各国大量使用以湿法磷酸为原料生产磷酸钙盐作为饲料添加剂,其中又以磷酸氢钙为主。采用湿法磷酸生产饲料磷酸盐的关键技术是湿法磷酸的净化,即将湿法磷酸中的氟含量及其它杂质的含量通过净化达到生产饲料级磷酸盐的要求。而脱氟技术的优劣直接影响到最终产品的产量和质量。湿法磷酸脱氟的技术主要有两种:化学沉淀法和汽提脱氟法。化学沉淀法的原理是加入钠盐或钾盐,将磷酸中的氟硅酸转化为氟硅酸钠或氟硅酸钾沉淀,从而达到脱氟的目的。但是脱氟效率不高,需要加入石灰乳进行二次沉淀脱氟,过程操作较为复杂,且磷损失较大。汽提脱氟法的原理是向磷酸中加入活性sio2,磷酸通过热介质加热后,酸中的hf和h2sif6与sio2反应转化为sif4逸出,从而达到脱氟的目的。根据磷酸加热方式的不同,汽提脱氟法又分为槽式脱氟工艺和塔式脱氟工艺两种。槽式脱氟工艺的原理是向浓磷酸中添加活性sio2,向装有浓磷酸的贮槽中鼓入热空气,酸中的hf和h2sif6于约80℃下呈sif4随鼓入空气自酸中逸出。该方法磷酸是连续相,空气是分散相,磷酸与空气接触不充分,脱氟效果不佳。而且存在设备投资高、能耗大的缺点,目前工业上采用的较少。塔式脱氟工艺的原理是浓磷酸与活性sio2按比例混合后,通过酸加热器循环加热后喷淋至空塔中,空塔底部通入常温空气,使浓酸液滴与常温空气逆流接触将酸中hf、h2sif6以sif4的形态逸出。塔式脱氟工艺的特点是连续相为空气,分散相为磷酸,磷酸能与空气充分接触。因此脱氟效果优于槽式脱氟,在工业生产上使用也较多。中国专利cn104176719a公开了一种塔式空气气提磷酸脱氟方法:将原料磷酸与脱氟剂混合,加热至90~105℃引入脱氟塔中;自脱氟塔的下部通入空气,使磷酸与空气充分接触完成脱氟;此方法可以实现连续化生产,使磷酸中的磷氟比(p2o5/f)提高至260。但是,此方法直接用未经净化的浓磷酸进行脱氟,生产出的脱氟磷酸杂质较多,达不到生产饲料级磷酸钙盐的原料要求,需要进一步澄清、过滤才能使用。汽提脱氟对于浓磷酸的杂质含量要求比较高,特别是其中金属阳离子的含量严重影响脱氟的效率。在实际生产中,预期30万吨/年产能的汽提脱氟设备,受磷酸品质影响通常只能做到15万吨/年的产量。技术实现要素:本发明的目的在于提供一种沉淀预脱氟与汽提脱氟耦合的湿法磷酸脱氟方法,解决现有技术中脱氟磷酸杂质多、磷损失大、产能受限的问题。为解决上述的技术问题,本发明采用以下技术方案:一种沉淀预脱氟与汽提脱氟耦合的湿法磷酸脱氟方法,其特征在于包括如下步骤:1)脱除重金属处理:将原料磷酸进行脱除砷铅重金属处理,然后澄清脱出磷酸中的固体杂质,得到质量浓度为42~48%p2o5、含固量为0.8~2.0%、f含量为0.5~0.9%的澄清浓磷酸a;2)沉淀法预脱氟:将步骤1)的澄清浓磷酸a采用沉淀法脱氟,经过澄清、压滤脱出磷酸中的固体杂质,得到质量浓度为41~47%p2o5、含固量为0.4~1.0%、f含量为0.3~0.4%的澄清浓磷酸b;3)多级汽提脱氟:将步骤2)中得到的澄清浓磷酸b与脱氟剂在一级脱氟塔连通槽中混合,然后经酸加热器加热后送入一级脱氟塔,与来自脱氟塔的下部的空气逆流接触进行脱氟;脱氟到一定程度的磷酸一部分与新加入的原料磷酸、脱氟剂混合继续脱氟,另一部分导出脱氟塔进入下一级脱氟塔继续加热脱氟;经过多级脱氟后氟含量达标的磷酸导出脱氟塔进入成品酸槽,含氟气体送入尾气洗涤塔中净化处理。更进一步的技术方案是所述步骤1)中脱除重金属处理的具体步骤为:原料磷酸进入到混合反应槽与一定量的硫化钠溶液进行搅拌,混合反应20~25min后,输送至预处理澄清槽中并加入絮凝剂进行澄清,得到澄清浓磷酸a;混合反应槽及预处理澄清槽中产生的硫化氢气体由洗涤塔用氢氧化钠溶液循环洗涤吸收;其中硫化钠用量为理论量的2~7倍,理论用量根据化学反应方程式计算而来。主要化学反应方程式如下:2as3++3s2-→as2s3↓pb2++s2-→pbs↓2na++sif62-→na2sif6↓h2s+2naoh→na2s+2h2o更进一步的技术方案是所述步骤2)沉淀法预脱氟的具体步骤为向浓磷酸a中加入理论用量1.1~2.0倍的脱氟剂,搅拌反应20~30分钟后,将其打入养晶槽澄清,养晶6~8小时后上部澄清酸经压滤后打入清酸收集槽,得到澄清浓磷酸b。主要化学反应方程式如下:2na++sif62-→na2sif6↓2k++sif62-→k2sif6↓所述预脱氟使用的脱氟剂为物质a与物质b的混合物,物质a为白炭黑、活性sio2、硅藻土、微硅粉中的至少一种,物质b为硫酸钠、硫酸钾、氢氧化钠、氢氧化钾中的至少一种。更进一步的技术方案是所述多级汽提脱氟具体步骤为:s1:向浓磷酸b中加入理论用量1.0~2.0倍的脱氟剂在脱氟塔连通槽中混合反应得到混合酸c,混合酸c通过循环泵输送至酸加热器中加热至90~110℃,送入一级脱氟塔;s2:送入一级脱氟塔的混合酸c通过塔内上部多层喷头喷洒于塔中,与自脱氟塔下部通入的温度为20~30℃的自然空气充分接触脱氟,得到混合酸d,产生的含氟废弃送至尾气洗涤塔;s3:脱氟程度达到本级工艺要求的混合酸d中的一部分与塔底部分混合酸c混合进行循环脱氟,循环的混合酸d的质量为混合酸c加入量的40~80倍,剩余的混合酸d导出本级脱氟塔后进入下一级脱氟塔继续加热脱氟,以此类推,经过多级脱氟后的磷酸导出脱氟塔进入成品酸槽得到脱氟成品磷酸。更进一步的技术方案是所述脱氟塔内的压力为-0.1~-1.0kpa,温度为85~100℃,液气比0.01~0.05m3/m3,混合酸进出酸加热器的温度差小于10℃。更进一步的技术方案是所述一级脱氟塔内的压力为-0.8~-1.0kpa,温度为88~95℃,液气比0.04~0.05m3/m3;二级脱氟塔内的压力为-0.5~-0.8kpa,温度为93~99℃,液气比0.03~0.04m3/m3;三级脱氟塔内的压力为-0.3~-0.5kpa,温度为95~101℃,液气比0.02~0.03m3/m3;四级脱氟塔内的压力为-0.1~-0.3kpa,温度为99~105℃,液气比0.01~0.02m3/m3。一二级脱氟塔内液气比高,可达到提高混合酸温度的目的,便于后续脱氟;三四级液气比低,通气量大,大大提高了脱氟速率,提高了生产效率。更进一步的技术方案是所述汽提脱氟脱氟剂为白炭黑、活性sio2、硅藻土、微硅粉中的一种或几种。更进一步的技术方案是所述脱氟剂需要预先调浆,其质量浓度为5%~20%。更进一步的技术方案是所述成品磷酸中p2o5含量为50~53%、磷氟比为(p2o5/f)≥315、含固量≤1.6%、f含量≤0.18%。工作机理:4hf+sio2=sif4↑+2h2o。与现有技术相比,本发明的有益效果是:提供一种沉淀预脱氟与汽提脱氟耦合的湿法磷酸脱氟方法,先对原料磷酸进行脱砷铅重金属净化工序,得到澄清、杂质含量低的净化磷酸后再进入预脱氟工序;预脱氟工序采用化学沉淀法,将含氟化合物变成沉淀后经过澄清、压滤,得到氟含量降低了的预脱氟澄清酸;脱氟工序采用多级汽提脱氟工艺,采取间接或直接蒸汽加热方式,级数可以根据实际情况选择一级到四级;生产的脱氟磷酸品质较好,杂质含量低,其磷氟比(p2o5/f)可达305以上,能直接用于生产饲料级磷酸钙盐,年产量可达到25-30万吨。附图说明图1为本发明的工艺流程图。具体实施方式为了使本发明的目的、技术方案及优点更加清楚明白,以下结合附图及实施例,对发明进行进一步详细说明。应当理解,此处所描述的具体实施例仅仅用以解释本发明,并不用于限定本发明。实施例1某磷酸厂25万吨/年饲料级磷酸装置,采用化学沉淀法预脱氟与塔式空气吹净深度脱氟耦合工艺净化磷酸。首先将原料磷酸进行脱砷铅重金属处理,原料磷酸在混合反应槽与2倍理论用量的硫化钠溶液进行搅拌,混合反应20min后,输送至预处理澄清槽中并加入絮凝剂进行澄清,得到澄清浓磷酸a,浓磷酸a中p2o5含量为47.28%,f含量为0.82%,含固量1.71%。混合反应槽及预处理澄清槽中产生的硫化氢气体由洗涤塔用氢氧化钠溶液循环洗涤吸收。理论用量通由化学反应方程式计算得出。沉淀法预脱氟:按理论用量的1.1倍向浓磷酸a中加入脱氟剂,经20分钟反应时间后,将浓磷酸a打入养晶槽澄清,养晶8小时后上部澄清酸经压滤后打入清酸收集槽,得到浓磷酸b。浓磷酸b中p2o5含量为46.45%,f含量为0.32%,含固量0.62%。脱氟剂为质量浓度为12%的白炭黑和硫酸钠。多级汽提脱氟:向脱氟塔连通槽内加入来自清酸收集槽的净化浓磷酸b80m3,脱氟剂1.6m3,脱氟剂的质量浓度为11%,脱氟剂为白炭黑、活性sio2、硅藻土、微硅粉中的一种。浓磷酸b与脱氟剂在脱氟塔连通槽中混合反应后得到混合酸c。混合酸c加热至95℃后送至脱氟塔内喷淋,与自脱氟塔下部通入的温度为20℃的自然空气充分接触脱氟。脱氟后得到混合酸d,达到工艺要求的成品磷酸一部分进入成品酸槽,一部分与塔底部分混合酸c,将混合酸d再次送入脱氟塔内喷淋,不断循环,循环酸总量为1210m3/h,其混合酸d质量为混合酸c加入的40倍。脱氟塔压力保持-0.4kpa,温度96℃。2h后测定磷酸中的f含量为0.17%。将脱氟合格的磷酸经脱氟磷酸出酸泵输送至成品酸贮槽,出酸量为24m3/h,装置切换至连续生产模式,原料磷酸加入量为31m3/h,脱氟剂加入量为1.8m3/h。经测定,该套装置生产的脱氟磷酸的磷氟比(p2o5/f)可以达到310,含固量为1.59%,符合生产饲料级磷酸氢钙的原料要求。本实施例中各阶段磷酸有关组分含量如表1:表1实例1中各阶段磷酸组分含量实施例2某磷酸厂26万吨/年饲料级磷酸装置,采用化学沉淀法预脱氟与塔式空气吹净深度脱氟耦合工艺净化磷酸。首先将原料磷酸进行脱砷铅重金属处理,原料磷酸在混合反应槽与3倍理论用量的硫化钠溶液进行搅拌,混合反应21min后,输送至预处理澄清槽中并加入絮凝剂进行澄清,得到澄清浓磷酸a,浓磷酸a中p2o5含量为47.45%,f含量为0.77%,含固量1.62%。混合反应槽及预处理澄清槽中产生的硫化氢气体由洗涤塔用氢氧化钠溶液循环洗涤吸收。理论用量通由化学反应方程式计算得出。沉淀法预脱氟:按理论用量的1.5倍向浓磷酸a中加入脱氟剂,经25分钟反应时间后,将浓磷酸a打入养晶槽澄清,养晶6小时后上部澄清酸经压滤后打入清酸收集槽,得到浓磷酸b。浓磷酸b中p2o5含量为46.43%,f含量为0.29%,含固量0.78%。脱氟剂为质量浓度为10%的硅藻土和硫酸钾。多级汽提脱氟:向脱氟塔连通槽内加入来自清酸收集槽的净化浓磷酸b80m3,脱氟剂2.4m3,脱氟剂的质量浓度为5%,脱氟剂为白炭黑和活性sio2的混合物。浓磷酸b与脱氟剂在脱氟塔连通槽中混合反应后得到混合酸c。混合酸c加热至90℃后送至一级脱氟塔内喷淋,与自脱氟塔下部通入的温度为25℃的自然空气充分接触脱氟。脱氟后得到混合酸d,一部分混合酸d与塔底部分混合酸c循环脱氟,循环酸总量为1480m3/h,其混合酸d质量为混合酸c加入的60倍。脱氟塔压力保持-0.8kpa,温度93℃,液气比0.05m3/m3。另一部混合酸d经脱氟磷酸出酸泵转入进入二级脱氟塔,塔内循环喷淋。脱氟塔压力保持-0.5kpa,温度98℃,液气比0.03m3/m3。经过两级脱氟后氟含量达标的磷酸导出脱氟塔进入成品酸槽。1.8h后测定磷酸中的f含量为0.17%。将脱氟合格的磷酸经脱氟磷酸出酸泵输送至成品酸贮槽,出酸量为24m3/h,装置切换至连续生产模式,原料磷酸加入量为33m3/h,脱氟剂加入量为1.6m3/h。经测定,该套装置生产的脱氟磷酸的磷氟比(p2o5/f)为305,含固量为1.46%,符合生产饲料级磷酸氢钙的原料要求。本实施例中各阶段磷酸有关组分含量如表2:表2实例2中各阶段磷酸组分含量p2o5含固量f含量p2o5/f原料磷酸48.492.30.9153浓磷酸a47.451.620.7762浓磷酸b46.430.780.29160一级脱氟混合酸50.32--0.22229二级脱氟混合酸51.27--0.20256成品磷酸51.891.460.17305实施例3某磷酸厂27万吨/年饲料级磷酸装置,采用化学沉淀法预脱氟与塔式空气吹净深度脱氟耦合工艺净化磷酸。首先将原料磷酸进行脱砷铅重金属处理,原料磷酸在混合反应槽与4倍理论用量的硫化钠溶液进行搅拌,混合反应22min后,输送至预处理澄清槽中并加入絮凝剂进行澄清,得到澄清浓磷酸a,浓磷酸a中p2o5含量为47.28%,f含量为0.72%,含固量1.66%。混合反应槽及预处理澄清槽中产生的硫化氢气体由洗涤塔用氢氧化钠溶液循环洗涤吸收。理论用量通由化学反应方程式计算得出。沉淀法预脱氟:按理论用量的1.8倍向浓磷酸a中加入脱氟剂,经30分钟反应时间后,将浓磷酸a打入养晶槽澄清,养晶7小时后上部澄清酸经压滤后打入清酸收集槽,得到浓磷酸b。浓磷酸b中p2o5含量为46.42%,f含量为0.34%,含固量0.67%。脱氟剂为质量浓度为5%的白炭黑和硫酸钠的混合物。多级汽提脱氟:向脱氟塔连通槽内加入来自清酸收集槽的净化浓磷酸b80m3,脱氟剂2.1m3,脱氟剂的质量浓度为9%,脱氟剂为硅藻土和微硅粉的混合物。浓磷酸b与脱氟剂在脱氟塔连通槽中混合反应后得到混合酸c。混合酸c加热至90℃后送至一级脱氟塔内喷淋,与自脱氟塔下部通入的温度为30℃的自然空气充分接触脱氟。脱氟后得到混合酸d,一部分混合酸d与塔底部分混合酸c进行循环脱氟,循环酸总量为1580m3/h,其混合酸d质量为混合酸c加入的80倍。脱氟塔压力保持-1.0kpa,温度92℃,液气比0.04m3/m3。另一部混合酸d经脱氟磷酸出酸泵转入进入二级脱氟塔,与自脱氟塔下部通入的温度为20℃的自然空气充分接触脱氟。脱氟后得到混合酸e,一部分混合酸e与塔底部分混合酸d进行循环脱氟,循环酸总量为1470m3/h,其混合酸e质量为混合酸d加入的70倍。脱氟塔压力保持-0.5kpa,温度97℃,液气比0.03m3/m3。另一部分混合酸e经脱氟磷酸出酸泵转入进入三级脱氟塔,塔内循环喷淋。脱氟塔压力保持-0.3kpa,温度99℃,液气比0.02m3/m3。经过三级脱氟后氟含量达标的磷酸导出脱氟塔进入成品酸槽。1.6h后测定磷酸中的f含量为0.17%。将脱氟合格的磷酸经脱氟磷酸出酸泵输送至成品酸贮槽,出酸量为24m3/h,装置切换至连续生产模式,原料磷酸加入量为42m3/h,脱氟剂加入量为1.0m3/h。经测定,该套装置生产的脱氟磷酸的磷氟比(p2o5/f)为308,含固量为1.53%,符合生产饲料级磷酸氢钙的原料要求。本实施例中各阶段磷酸有关组分含量如表3:表3实例3中各阶段磷酸组分含量实施例4某磷酸厂28万吨/年饲料级磷酸装置,采用化学沉淀法预脱氟与塔式空气吹净深度脱氟耦合工艺净化磷酸。首先将原料磷酸进行脱砷铅重金属处理,原料磷酸在混合反应槽与5倍理论用量的硫化钠溶液进行搅拌,混合反应23min后,输送至预处理澄清槽中并加入絮凝剂进行澄清,得到澄清浓磷酸a,浓磷酸a中p2o5含量为41.26%,f含量为0.73%,含固量1.42%。混合反应槽及预处理澄清槽中产生的硫化氢气体由洗涤塔用氢氧化钠溶液循环洗涤吸收。理论用量通由化学反应方程式计算得出。沉淀法预脱氟:按理论用量的1.9倍向浓磷酸a中加入脱氟剂,经25分钟反应时间后,将浓磷酸a打入养晶槽澄清,养晶8小时后上部澄清酸经压滤后打入清酸收集槽,得到浓磷酸b。浓磷酸b中p2o5含量为40.64%,f含量为0.28%,含固量0.43%。脱氟剂为质量浓度为18%的硅藻土、硫酸钾和氢氧化钠的混合物。多级汽提脱氟:向脱氟塔连通槽内加入来自清酸收集槽的净化浓磷酸b80m3,脱氟剂1.7m3,脱氟剂的质量浓度为8%,脱氟剂为硅藻土和微硅粉的混合物。浓磷酸b与脱氟剂在脱氟塔连通槽中混合反应后得到混合酸c。混合酸c加热至93℃后送至一级脱氟塔内喷淋,与自脱氟塔下部通入的温度为22℃的自然空气充分接触脱氟。脱氟后得到混合酸d,一部分混合酸d与塔底部分混合酸c进行循环脱氟,循环酸总量为1360m3/h,其混合酸d质量为混合酸c加入的65倍。脱氟塔压力保持-0.8kpa,温度92℃,液气比0.05m3/m3。另一部混合酸d经脱氟磷酸出酸泵转入进入二级脱氟塔,与自脱氟塔下部通入的温度为26℃的自然空气充分接触脱氟。脱氟后得到混合酸e,一部分混合酸e与塔底部分混合酸d进行循环脱氟,循环酸总量为1450m3/h,其混合酸e质量为混合酸d加入的75倍。脱氟塔压力保持-0.6kpa,温度97℃,液气比0.04m3/m3。另一部分混合酸e经脱氟磷酸出酸泵转入进入三级脱氟塔,与自脱氟塔下部通入的温度为28℃的自然空气充分接触脱氟。脱氟后得到混合酸f,一部分混合酸f与塔底部分混合酸e进行循环脱氟,循环酸总量为1550m3/h,其混合酸f质量为混合酸e加入的80倍。脱氟塔压力保持-0.3kpa,温度99℃,液气比0.02m3/m3。另一部分混合酸f经脱氟磷酸出酸泵转入进入四级脱氟塔,塔内循环喷淋。脱氟塔压力保持-0.1kpa,温度103℃,液气比0.01m3/m3。经过四级脱氟后氟含量达标的磷酸导出脱氟塔进入成品酸槽。1.5h后测定磷酸中的f含量为0.18%。将脱氟合格的磷酸经脱氟磷酸出酸泵输送至成品酸贮槽,出酸量为24m3/h,装置切换至连续生产模式,原料磷酸加入量为49m3/h,脱氟剂加入量为1.1m3/h。经测定,该套装置生产的脱氟磷酸的磷氟比(p2o5/f)为307,含固量为1.48%,符合生产饲料级磷酸氢钙的原料要求。本实施例中各阶段磷酸有关组分含量如表4:表4实例4中各阶段磷酸组分含量实施例5某磷酸厂30万吨/年饲料级磷酸装置,采用化学沉淀法预脱氟与塔式空气吹净深度脱氟耦合工艺净化磷酸。首先将原料磷酸进行脱砷铅重金属处理,原料磷酸在混合反应槽与6倍理论用量的硫化钠溶液进行搅拌,混合反应25min后,输送至预处理澄清槽中并加入絮凝剂进行澄清,得到澄清浓磷酸a,浓磷酸a中p2o5含量为41.42%,f含量为0.77%,含固量1.63%。混合反应槽及预处理澄清槽中产生的硫化氢气体由洗涤塔用氢氧化钠溶液循环洗涤吸收。理论用量通由化学反应方程式计算得出。沉淀法预脱氟:按理论用量的2.0倍向浓磷酸a中加入脱氟剂,经24分钟反应时间后,将浓磷酸a打入养晶槽澄清,养晶7.5小时后上部澄清酸经压滤后打入清酸收集槽,得到浓磷酸b。浓磷酸b中p2o5含量为40.85%,f含量为0.36%,含固量0.48%。脱氟剂为质量浓度为16%的微硅粉、硫酸钾和氢氧化钠的混合物。多级汽提脱氟:向脱氟塔连通槽内加入来自清酸收集槽的净化浓磷酸b80m3,脱氟剂2.1m3,脱氟剂的质量浓度为11%,脱氟剂为活性sio2、硅藻土和微硅粉的混合物。浓磷酸b与脱氟剂在脱氟塔连通槽中混合反应后得到混合酸c。混合酸c加热至95℃后送至一级脱氟塔内喷淋,与自脱氟塔下部通入的温度为30℃的自然空气充分接触脱氟。脱氟后得到混合酸d,一部分混合酸d与塔底部分混合酸c进行循环脱氟,循环酸总量为1420m3/h,其混合酸d质量为混合酸c加入的60倍。脱氟塔压力保持-0.9kpa,温度95℃,液气比0.045m3/m3。另一部混合酸d经脱氟磷酸出酸泵转入进入二级脱氟塔,与自脱氟塔下部通入的温度为27℃的自然空气充分接触脱氟。脱氟后得到混合酸e,一部分混合酸e与塔底部分混合酸d进行循环脱氟,循环酸总量为1470m3/h,其混合酸e质量为混合酸d加入的65倍。脱氟塔压力保持-0.7kpa,温度99℃,液气比0.035m3/m3。另一部分混合酸e经脱氟磷酸出酸泵转入进入三级脱氟塔,与自脱氟塔下部通入的温度为25℃的自然空气充分接触脱氟。脱氟后得到混合酸f,一部分混合酸f与塔底部分混合酸e进行循环脱氟,循环酸总量为1550m3/h,其混合酸f质量为混合酸e加入的70倍。脱氟塔压力保持-0.4kpa,温度102℃,液气比0.025m3/m3。另一部分混合酸f经脱氟磷酸出酸泵转入进入四级脱氟塔,塔内循环喷淋。脱氟塔压力保持-0.2kpa,温度104℃,液气比0.015m3/m3。经过四级脱氟后氟含量达标的磷酸导出脱氟塔进入成品酸槽。1.5h后测定磷酸中的f含量为0.18%。将脱氟合格的磷酸经脱氟磷酸出酸泵输送至成品酸贮槽,出酸量为25m3/h,装置切换至连续生产模式,原料磷酸加入量为54m3/h,脱氟剂加入量为1.8m3/h。经测定,该套装置生产的脱氟磷酸的磷氟比(p2o5/f)为308,含固量为1.44%,符合生产饲料级磷酸氢钙的原料要求。本实施例中各阶段磷酸有关组分含量如表5:表5实例5中各阶段磷酸组分含量实施例6某磷酸厂30万吨/年饲料级磷酸装置,采用化学沉淀法预脱氟与塔式空气吹净深度脱氟耦合工艺净化磷酸。首先将原料磷酸进行脱砷铅重金属处理,原料磷酸在混合反应槽与7倍理论用量的硫化钠溶液进行搅拌,混合反应20min后,输送至预处理澄清槽中并加入絮凝剂进行澄清,得到澄清浓磷酸a,浓磷酸a中p2o5含量为45.36%,f含量为0.74%,含固量1.38%。混合反应槽及预处理澄清槽中产生的硫化氢气体由洗涤塔用氢氧化钠溶液循环洗涤吸收。理论用量通由化学反应方程式计算得出。沉淀法预脱氟:按理论用量的2.0倍向浓磷酸a中加入脱氟剂,经25分钟反应时间后,将浓磷酸a打入养晶槽澄清,养晶8小时后上部澄清酸经压滤后打入清酸收集槽,得到浓磷酸b。浓磷酸b中p2o5含量为44.63%,f含量为0.29%,含固量0.57%。脱氟剂为质量浓度为16%的微硅粉、硫酸钾和氢氧化钠的混合物。多级汽提脱氟:向脱氟塔连通槽内加入来自清酸收集槽的净化浓磷酸b80m3,脱氟剂2.3m3,脱氟剂的质量浓度为15%,脱氟剂为活性sio2、硅藻土和微硅粉的混合物。浓磷酸b与脱氟剂在脱氟塔连通槽中混合反应后得到混合酸c。混合酸c加热至94℃后送至一级脱氟塔内喷淋,与自脱氟塔下部通入的温度为26℃的自然空气充分接触脱氟。脱氟后得到混合酸d,一部分混合酸d与塔底部分混合酸c进行循环脱氟,循环酸总量为1330m3/h,其混合酸d质量为混合酸c加入的65倍。脱氟塔压力保持-1.0kpa,温度96℃,液气比0.05m3/m3。另一部混合酸d经脱氟磷酸出酸泵转入进入二级脱氟塔,与自脱氟塔下部通入的温度为24℃的自然空气充分接触脱氟。脱氟后得到混合酸e,一部分混合酸e与塔底部分混合酸d进行循环脱氟,循环酸总量为1380m3/h,其混合酸e质量为混合酸d加入的70倍。脱氟塔压力保持-0.8kpa,温度99℃,液气比0.04m3/m3。另一部分混合酸e经脱氟磷酸出酸泵转入进入三级脱氟塔,与自脱氟塔下部通入的温度为22℃的自然空气充分接触脱氟。脱氟后得到混合酸f,一部分混合酸f与塔底部分混合酸e进行循环脱氟,循环酸总量为1430m3/h,其混合酸f质量为混合酸e加入的75倍。脱氟塔压力保持-0.5kpa,温度100℃,液气比0.03m3/m3。另一部分混合酸f经脱氟磷酸出酸泵转入进入四级脱氟塔,塔内循环喷淋。脱氟塔压力保持-0.3kpa,温度102℃,液气比0.02m3/m3。经过四级脱氟后氟含量达标的磷酸导出脱氟塔进入成品酸槽。1.45h后测定磷酸中的f含量为0.18%。将脱氟合格的磷酸经脱氟磷酸出酸泵输送至成品酸贮槽,出酸量为26m3/h,装置切换至连续生产模式,原料磷酸加入量为45m3/h,脱氟剂加入量为1.8m3/h。经测定,该套装置生产的脱氟磷酸的磷氟比(p2o5/f)为316,含固量为1.86%,符合生产饲料级磷酸氢钙的原料要求。本实施例中各阶段磷酸有关组分含量如表6:表6实例6中各阶段磷酸组分含量尽管这里参照本发明的多个解释性实施例对本发明进行了描述,但是,应该理解,本领域技术人员可以设计出很多其他的修改和实施方式,这些修改和实施方式将落在本申请公开的原则范围和精神之内。更具体地说,在本申请公开、附图和权利要求的范围内,可以对的组成部件或布局进行多种变形和改进。除了对组成部件或布局进行的变形和改进外,对于本领域技术人员来说,其他的用途也将是明显的。当前第1页12