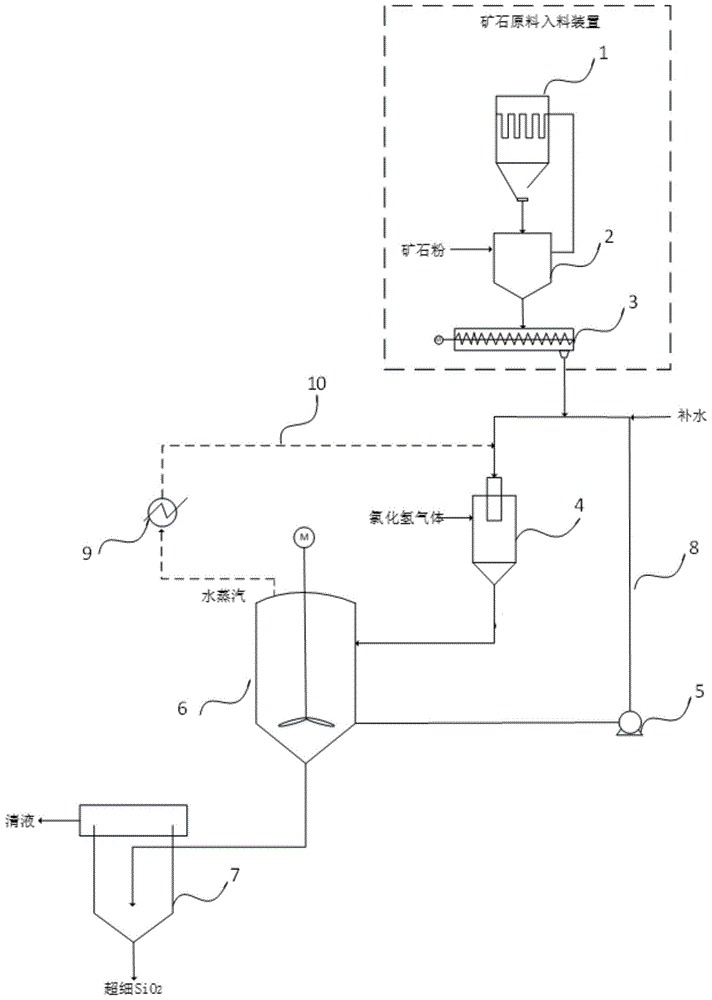
本实用新型涉及一种利用氯化氢气体浸取硅酸盐矿制备超细二氧化硅的系统。
背景技术:
:超细sio2具有比表面积大、多孔、耐高温、电绝缘性强、良好的补强作用以及不燃烧等特性,其在涂料、塑料、医学、生物、造纸、橡胶、农业、化工、国防及机械等领域有广泛应用。超细sio2生产工艺较多,从基本原理上划分只有气相法和沉淀法。沉淀法由于工艺简单,生产条件稳定,成本较低,产量大,是目前工业生产中普遍采用的方法,目前沉淀法又分为传统沉淀法和新型沉淀法,新型沉淀法又称离解法,与传统沉淀方法相比,离解法主要是在硅源方面不再采用传统的水玻璃,而是以非金属矿及其延伸物或其他物质为硅源,其技术关键是将结晶的二氧化硅和硅酸盐转变成非晶态的二氧化硅。根据使用的原料不同可以分为非金属矿物法、禾本科植物法、副产品回收法等。以非金属矿为原料的离解法大致分为两种,一种是以氢氧化钠溶液浸取原料,得到硅酸钠溶液后再用盐酸酸化得到超细sio2,一种是采用盐酸溶液或混合酸溶液直接浸取原料得到超细sio2。但目前,大部分的研究都停留在实验研究阶段,且硅酸盐矿石与酸的浸取反应慢,需要高温和强酸环境,高温下高浓度盐酸挥发。技术实现要素:本实用新型的目的是提供一种利用氯化氢气体浸取硅酸盐矿制备超细二氧化硅的系统,本实用新型采用hcl气体直接溶解的方式,酸浓度高、活性强,溶解热可以为浸取过程供热。本实用新型所涉及的超细二氧化硅指的是粒径为10~15μm的二氧化硅。本实用新型提供的利用氯化氢气体浸取硅酸盐矿制备超细二氧化硅的系统,包括矿石原料入料装置、射流器、搅拌釜和液固分离装置;所述射流器上设有液体入口、液体出口和气体入口;所述搅拌釜的循环物料出口通过循环管路与所述射流器的液体入口相连通;所述射流器的液体出口与所述搅拌釜的循环物料入口相连通;所述矿石原料入料装置的物料出口与所述循环管路相连通;所述循环管路上设有循环泵;所述搅拌釜的循环物料出口与所述液固分离装置相连通。所述的系统中,所述矿石原料入料装置的物料出口与所述循环管路的连接处靠近所述射流器一端。所述的系统中,所述搅拌釜包括至少一个所述循环物料入口、至少一个所述循环物料出口和至少一个所述排料口。所述的系统中,所述矿石原料入料装置包括粉体定量输送装置;所述粉体定量输送装置通过一入料管与所述循环管路相连通;所述粉体定量输送装置将硅酸盐矿石的原料粉通过所述入料管加入至所述循环管路中,并与所述循环管路中的物料混合。所述的系统中,所述矿石原料入料装置还包括一与所述粉体定量输送装置相连通的预混罐;所述预混罐的浆料出口和浆料入口分别与所述射流器和所述循环管路相连通;所述循环管路中的部分物料通过所述循环泵引入至所述预混罐中使其与加入的硅酸盐矿石粉体预混;预混后的浆料通过所述浆料出口输入至所述射流器中。所述的系统中,所述搅拌釜上设有一蒸汽出口,用以排出汽化的水蒸汽及少量未反应的氯化氢气体;优选地,所述蒸汽出口通过一冷却水管路与所述循环管路相连通,所述冷却水管路上设有换热器,用于将水蒸汽及少量未反应的氯化氢气体冷凝后重新返回所述射流器中,同时可移去部分反应热量,保持反应温度稳定。所述的系统中,所述液固分离装置可为沉降分离器、旋液分离器、离心机或过滤分离器。利用本实用新型所述系统制备所述超细二氧化硅时,可包括如下步骤:所述硅酸盐矿石的粉末经所述矿石原料入料装置与所述循环管路输送的循环液混合后高速泵入至所述射流器中;所述氯化氢气体通过所述射流器上的所述气体入口吸入至所述射流器中并溶解于所述循环液中,经盐酸与所述硅酸盐矿石的反应即得到二氧化硅;所述反应依次于所述射流器、所述循环管路和所述搅拌釜中进行(在所述射流器中进行初步接触反应,之后反应液进入所述循环管路和所述搅拌釜中进一步反应);所述循环液为所述硅酸盐矿石与水形成的浆液(反应起初)或所述盐酸与所述硅酸盐矿石反应后的反应液。上述方法利用部分物料循环的目的如下:第一,用部分循环物料流过所述射流器,在所述射流器中形成负压,将氯化氢气体吸入,从而可以不使用压缩机对氯化氢气体加压;第二,循化的物料中未反应的硅酸钙在所述射流器及其后的管线与氯化氢快速反应,此时氯化氢的浓度高,管线中混合快,反应速率高。本实用新型利用文丘里效应,在所述射流器中形成负压,从而将氯化氢气体吸入至所述射流器中进而与硅酸盐矿石进行反应,浸取二氧化硅。上述的制备方法中,所述硅酸盐矿石可为长石(正长石、斜长石、副长石)、云母、橄榄石、石榴子石、红柱石、绿帘石、辉石、角闪石、硅灰石、滑石、高岭石、绿泥石和蛇纹石至少一种;所述硅酸盐矿石的粉末的粒径不小于50目,基于泰勒标准筛制;所述硅酸盐矿石中sio2的质量含量不低于40%;所述射流器气体入口处氯化氢气体的压强与所述搅拌釜中的压强之差不大于所述射流器所能达到的最大真空度,如3.3kpa;所述搅拌釜中的所述反应的温度可为70~120℃;所述射流器中所述循环液与所述氯化氢气体的体积流量之比可为2~3.5:1。上述的制备方法中,将所述硅酸盐矿石的粉末连续加入至所述射流器中即能实现所述超细二氧化硅的连续制备;具体操作是:氯化氢气体通过所述射流器上的所述气体入口吸入所述射流器并溶解于所述循环液中,并与所述循环液中的硅酸盐矿石粉末初步反应,随后反应液进入所述搅拌釜进一步反应;所述搅拌釜内的浆液一部分排入所述液固分离装置进行固液分离操作得到超细二氧化硅,一部分通过所述循环泵进入所述循环管道中进行循环;所述氯化氢气体与所述硅酸盐矿石的摩尔比可为2~3:1,其中所述硅酸盐矿石的量以sio2计。上述的制备方法中,将所述硅酸盐矿石的粉末直接加入至所述搅拌釜中与水形成浆液;所述浆液经所述循环管路输入至所述射流器中;吸入至所述射流器中的所述氯化氢气体溶解于所述浆液中,经盐酸与所述硅酸盐矿石的反应即得到二氧化硅,进而实现所述超细二氧化硅的批式制备;所述氯化氢气体与所述硅酸盐矿石的摩尔比为2~2.5:1,其中所述硅酸盐矿石的量以sio2计。本实用新型的原理是在盐酸存在下对硅酸盐矿石进行浸取,使得浸取液中形成可溶性氯化物盐。矿物浸出的反应机理是在固相和液相的两相界面上发生的多相反应,浸出过程分为两个阶段:第一阶段是矿物表面的浸出;第二阶段是毛细孔扩散浸出。前者浸出反应速度快,时间短;后者反应速度慢,时间长。本实用新型利用氯化氢气体浸取硅酸盐矿制备超细二氧化硅的系统,提供了连续化浸取硅酸盐矿石制备二氧化硅的工业化可行方案,而且通过选用射流器,采用氯化氢气体直接溶解在硅酸盐循环浆料中的方式,氯化氢气体和循环浆液接触后短时形成接近饱和的盐酸溶液,使浸取反应更容易进行,同时溶解热可以为浸取过程供热的优点,而且由于射流器中浆液的高浓度、高分散性和高浓度的盐酸溶液初步接触,大大提高了矿石的溶解效率和盐酸的利用率。附图说明图1为本实用新型实施例1利用氯化氢气体浸取硅酸盐矿制备超细二氧化硅的系统的示意图。图2为本实用新型实施例2利用氯化氢气体浸取硅酸盐矿制备超细二氧化硅的系统的示意图之二。图中各标记如下:1除尘器、2储料罐、3粉体定量输送装置、4射流器、5循环泵、5’浆料泵、6搅拌釜、7液固分离装置、8循环管路、9换热器、10冷却水管线。具体实施方式下面结合附图对本实用新型做进一步说明,但本实用新型并不局限于下述实施例。实施例1、图1为本实用新型第一实施例的制备系统的示意图,该系统包括矿石原料入料装置、射流器4、搅拌釜6和液固分离装置7。其中,矿石原料入料装置包括依次连接的除尘器1、储料罐2和粉体定量输送装置3;射流器4上设有液体入口(图中未标)、液体出口(图中未标)和气体入口(图中未标);射流器4的液体入口与搅拌釜6的排料口间连通一循环管路8,射流器4的液体出口与搅拌釜6的循环物料入口相连通;粉体定量输送装置3通过一入料管将硅酸盐矿石的原料粉加入至循环管路8中,并与循环管路8中的物料混合。搅拌釜6的排料口与液固分离装置7相连通;循环管路8上设有循环泵5,用于泵送循环液。本实用新型制备系统中,搅拌釜6上设有一蒸汽出口(图中未标),用以排出汽化的水蒸汽及少量未反应的氯化氢气体。该蒸汽出口通过一冷却水管路10与循环管路8相连通,冷却水管路10上设有换热器9,用于将水蒸汽及少量未反应的氯化氢气体冷凝后重新返回射流器4中,同时可移去部分反应热量,保持反应温度稳定。本实用新型制备系统中,液固分离装置7可为沉降分离器、旋液分离器、离心机或过滤分离器。本实用新型第一实施例的制备系统的工作过程为:采用连续操作,输送到储料罐2的矿石原料粉通过粉体定量输送装置3连续加入到循环管路8中并与循环液混合形成浆液,高速打入到射流器4中,利用文丘里效应,在射流器中形成负压,将氯化氢气体吸入并进行初步接触反应,随后反应液进入搅拌釜6进一步反应,搅拌釜反应后的浆液一部分排入固液分离装置7进行固液分离操作,一部分作为循环液由循环泵5泵入循环管路8。作为一种具体的实施例,选择矿石原料粉的有效成分为casio3,搅拌釜的反应温度为120℃,氯化氢气体的温度为250℃,氯化氢气体的摩尔流量与casio3的摩尔流量之比为2:1的工艺条件,采用aspen模拟得到的物料平衡和热量平衡数据见表1。表1物料平衡及热量平衡数据作为一种具体的实施例,本例硅酸盐矿以硅灰石为例,硅灰石来源于江西上高,粒度200目(基于泰勒标准筛制),平均矿物组成如表2所示:表2硅灰石的平均矿物组成(%)作为一种具体的实施例,储料罐体积为4m3,粉体定量输送装置选用螺旋给料机,搅拌釜体积为4m3,转速为30rpm,硅灰石粉的加入量为110kg/h,水的加入量为880kg/h,控制氯化氢的流量为45m3/h(氯化氢气体与硅灰石粉的摩尔比为2:1,其中硅灰石粉的量以sio2计),设置搅拌釜的温度为80℃,停留时间为2h,循环流量为100kg/h,沉降后固渣经进一步洗涤过滤干燥得到超细sio2,技术指标如表3所示。表3利用硅灰石矿粉制备的超细sio2技术指标二氧化硅%95加热减量%5.8灼烧减量%5.1dbp吸收值/ml/g2.98bet比表面积/m2/g198ph6.4平均粒径/um10.5铁/ppm180作为一种具体的实施例,本例硅酸盐矿以蛇纹石为例,蛇纹石来源于河南信阳,粒度200目(基于泰勒标准筛制),平均矿物组成如表4所示:表4蛇纹石的平均矿物组成(%)作为一种具体的实施例,储料罐体积为4m3,粉体定量输送装置选用螺旋给料机,搅拌釜体积为4m3,转速为30rpm,蛇纹石粉的加入量为91kg/h,水的加入量为880kg/h,控制氯化氢的流量为45m3/h(氯化氢气体与蛇纹石粉的摩尔比为2:1,其中蛇纹石粉的量以sio2计),设置搅拌釜的温度为120℃,停留时间为2h,循环流量为100kg/h,沉降后固渣经进一步洗涤过滤干燥粉碎得到超细sio2,技术指标如表5所示。表5利用蛇纹石矿粉制备的超细sio2技术指标实施例2、图2为本实用新型第二实施例的制备系统示意图,其结构与图1所示系统基本相同,不同之处在于:矿石原料入料装置还包括一与粉体定量输送装置3相连通的预混罐11,预混罐11的浆料出口和浆料入口分别与射流器4和循环管路8相连通,循环管路8中的部分物料通过循环泵5引入至预混罐11中使其与加入的硅酸盐矿石粉体预混;预混后的浆料通过浆料出口输入至射流器4中。在预混罐11与射流器4相连通的管线上设有浆料泵5’。本实用新型第二实施例的制备系统的工作过程为:采用连续操作,输送到储料罐2的矿石原料粉通过粉体定量输送装置3连续加入到预混罐11中,在预混罐11中与一定量的水搅拌混合均匀形成浆液,浆液经浆料泵5’高速打入到射流器4中,利用文丘里效应,在射流器中形成负压,将氯化氢气体吸入并进行初步接触反应,随后反应液进入搅拌釜6进一步反应,搅拌釜反应后的浆液一部分排入液固分离装置7进行固液分离操作,一部分作为循环液由循环泵5经循环管路8泵入预混罐11。作为一种具体的实施例,本例硅酸盐矿以硅灰石为例,硅灰石来源于江西上高,粒度200目(基于泰勒标准筛制),平均矿物组成同表2,作为一种具体的实施例,储料罐体积为4m3,粉体定量输送装置选用螺旋给料机,预混罐体积为3m3,搅拌釜体积为4m3,转速为30rpm,硅灰石粉的加入量为110kg/h,水的加入量为880kg/h,控制氯化氢的流量为45m3/h(氯化氢气体与硅灰石粉的摩尔比为2:1,其中硅灰石粉的量以sio2计),设置搅拌釜的温度为80℃,停留时间为2h,循环流量为100kg/h,沉降后固渣经进一步洗涤过滤干燥得到超细sio2,技术指标如表6所示。表6利用硅灰石矿粉制备的超细sio2技术指标作为一种具体的实施例,本例硅酸盐矿仍以硅灰石为例,硅灰石来源于江西上高,粒度200目(基于泰勒标准筛制),平均矿物组成同表2,作为一种具体的实施例,采用间歇操作,将110kg硅灰石粉加入到搅拌釜中,加入880kg水,控制氯化氢的流量为45m3/h(氯化氢气体与硅灰石粉的摩尔比为2:1,其中硅灰石粉的量以sio2计),设置搅拌釜的温度为80℃,反应时间为1h,循环流量为100kg/h,沉降后固渣经进一步洗涤过滤干燥得到超细sio2,技术指标如表7所示。表7利用间歇操作制备的超细sio2技术指标二氧化硅%95.5加热减量%5.72灼烧减量%5.19dbp吸收值/ml/g2.95bet比表面积/m2/g189ph6.4平均粒径/um14.1铁/ppm180需要说明的是,根据本领域一般技术人员的常识,分解反应器和再生反应器上还会设置相应的温度、液位等测量,控制系统以及相应的阀门,附图中并没有一一表明,这并不表明本实用新型工艺中不包含这些常规的设计。根据转化率以及物料衡算调整本实用新型中原料的进料速率,也是本领域一般技术人员的常识的常规设计,在本实用新型中也没有一一说明,这也并不表明本实用新型工艺中不包含这种常规的设计。当前第1页1 2 3