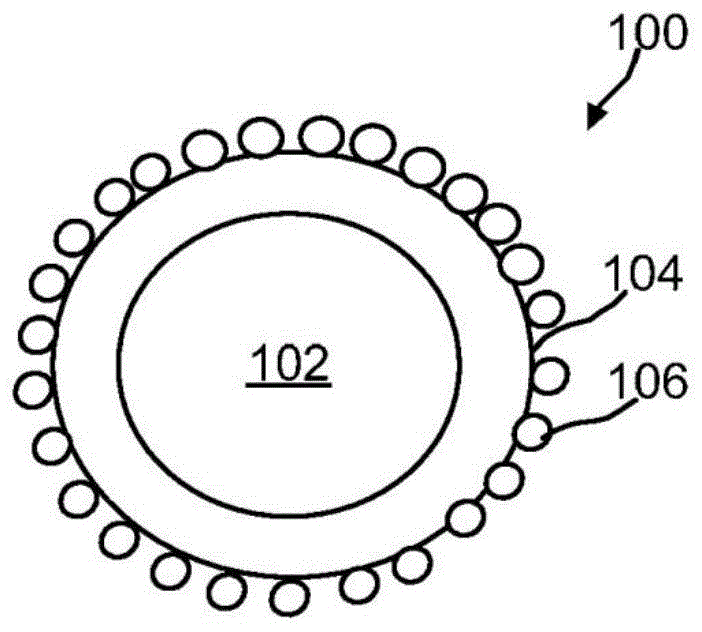
相关申请的交叉引用本申请要求2018年9月12日提交的美国临时专利申请第62/730294号的优先权权益,其全部内容通过引用整体并入本文。
背景技术:
:a.
技术领域:
本发明一般涉及使用催化剂的烃类(如甲烷)双重整,所述催化剂具有核-壳结构,其中活性金属沉积在壳的表面上。壳具有包含金属掺杂剂的氧化还原-金属氧化物相。b.
背景技术:
钢铁工业使用合成气(“syngas”)将铁矿石还原为铁金属,合成气中氢气与一氧化碳的比(h2/co)为1.6至2.0,或者为1.85。h2/co的比可以影响与还原铁矿石运输或进一步处理相关的性能(例如流动性能、物理性能和形态性能)。美国technologies和hyltechnologies(墨西哥)是该工艺的两家主要技术供应商。的重整器使用将甲烷干重整和甲烷蒸汽重整相结合的甲烷双重整来生产具有所需h2/co比的产品原料。甲烷双重整如反应式(1)所示。δh298k=220千焦/摩尔;δh298k=151千焦/摩尔(1)。双重整的原料流可以包含受控量的h2、co2和h2o,以产生所需的h2/co比。举例来说,原料流可以由14体积%至16体积%的co、12体积%至14体积%的co2、32体积%至36体积%的h2、16.5体积%至19.5体积%的h2o、14体积%至18体积%的ch4和3.5体积%至4.5体积%的n2组成。在850℃至900℃在0.1mpa的催化剂作用下,加工上述组合物可以制备产物流,所述产物流由30体积%至32体积%的co、2体积%至3体积%的co2、55体积%至57体积%的h2、7体积%至8体积%的h2o、0.3体积%至0.1体积%的ch4和2.2体积%至3.2体积%的n2组成。由于各种不可控的事件和使用中催化剂的自然状态,碳总是在催化剂上沉积,逐渐导致重整器中的压降增加。由于工艺气流受限,生产率降低。此外,在低流速下,重整器可能发生损坏(如机械完整性和热完整性)。尽管许多催化剂适用于使用co2和/或co2和氧气(o2)的甲烷干重整(氧-co2重整)(参见例如d’souza等人的wo2017001987),但将这些催化剂直接应用于甲烷的双重整是不可预测的。正如kumar等人在甲烷双重整的概述(currentopinioninchemicalengineering,2015,9:8-15)中所讨论的,与干重整或者氧-co2重整相比,双重整过程是更富氧的系统。因此,催化剂更容易氧化。由于失去活性位点,催化剂的氧化可导致催化剂随着时间推移而失活。因此,原料配比和催化剂选择可以成为双重整反应获得更高的h2/co比的限制条件。尽管已知催化剂可用于甲烷双重整反应,但由于焦化和/或氧化,这些催化剂会失活。因此,需要可以承受促进氧化和/或碳沉积的条件的催化剂。技术实现要素:已经发现了与双重整反应过程中催化剂的成本、失活和/或降解有关的至少一些问题的解决方案。出人意料地发现,具有特定的核-壳结构的催化剂在甲烷双重整反应中具有高催化活性和对氧化、焦化和烧结良好的抗性。核-壳结构可以包括被壳包围的化学惰性的核,其中活性/催化金属在壳的表面上沉积。壳可以具有包含金属掺杂剂(例如nb、in、ga和/或la)的氧化还原-金属氧化物相(例如二氧化铈(ceo2)相)。可以将掺杂剂掺入氧化还原-金属氧化物相的晶格框架中。不希望受理论约束,认为这种结构设置在甲烷的双重整反应中提供了许多优点。例如,核-壳结构可以提供增加的机械强度、热完整性,和降低的催化剂生产成本。而且,认为壳中氧化还原-金属氧化物相的掺杂可以在其晶格结构内制造相对高浓度的缺陷,从而提高了氧迁移率并增加了晶格结构中的氧空位。这继而提高了相的还原性,并有利于从其活性位点持续清除碳沉积。此外,可以通过改变壳层的厚度调节氧迁移率特性(例如,壳层的厚度可以调节为1个原子层至100个原子层)。还认为碱土金属铝酸盐(如mgal2o4)的核对co2具有高亲和力,其可以吸收更多的co2,并有助于氧化催化剂上形成的碳,如以下方程式所示:c+co2→2co。这些特征的组合导致了甲烷催化剂的双重整,其(1)生产在经济上可行,(2)具备足够的机械强度,(3)高活性,和/或(4)耐氧化、耐焦化和耐烧结(热完整性)。在一些方面,描述了用于由甲烷制备合成气的方法。方法可以包括在足以制备气体产物流的条件下将包含氢气(h2)、一氧化碳(co)、二氧化碳(co2)、甲烷(ch4)和水(h2o)的反应物气体流与本发明的催化剂材料接触,所述气体产物流包含h2和co,h2/co摩尔比为1.4至2.0,优选为1.6至2.0,更优选为约1.85。反应物流可以包含25体积%至40体积%的h2、5体积%至30体积%的co、5体积%至20体积%的co2、10体积%至30体积%的ch4和10体积%至30体积%的h2o,优选30体积%至35体积%的h2、10体积%至20体积%的co、10体积%至15体积%的co2、15体积%至20体积%的ch4和15体积%至20体积%的h2o。反应条件可以包括700℃至1000℃的温度、约0.1mpa至2mpa的压力、500h-1至100000h-1的气时空速,或其任意组合。反应条件可以包括在催化剂与气体反应物流接触之前,在至少550℃的温度下将催化剂与含有至少50体积%的co2的co2流接触至少6小时。co2流中的一部分co2可以用ch4、h2o、co和h2代替,以生成气体反应物流。co2的代替可以包括(a)将ch4引入co2流,并在至少600℃的温度下使加热的催化剂与co2/ch4流接触至少1个小时,(b)随时间增加co2/ch4流中ch4相对于co2的量的浓度,以产生含有约等量的co2和ch4的co2/ch4流,(c)在至少700℃的温度下将h2o引入co2/ch4流中以形成co2/ch4/h2o流,和(d)在至少700℃的温度下将co和h2引入co2/ch4/h2o流中,形成包含h2、co、co2、ch4和h2o的气体反应物流。步骤(b)可以包括以约5℃每小时至10℃每小时的速率将温度从600℃增加至至少700℃。特别是,在合成气制备过程中,可以基本上或完全抑制催化剂上焦炭的形成。在合成气制备过程中,压力可以保持恒定至少600小时或至少1200小时。产物流可以提供给直接还原铁单元,并用于将氧化铁还原为铁。催化剂材料可以包括化学惰性的金属氧化物核、沉积在金属氧化物核表面上的包含掺杂剂的氧化还原金属氧化物层和沉积在氧化还原金属氧化物层表面上的催化活性的金属。金属氧化物层和碱土金属铝酸盐核可以是核/壳结构,其中氧化还原-金属氧化物层包围氧化铝或碱土金属铝酸盐核。化学惰性的金属氧化物核可以是氧化铝或铝酸镁,氧化还原-金属氧化物层可以是二氧化铈(ceo2),金属掺杂剂可以是铌(nb)、铟(in)或镧(la)或其任意组合,以及活性金属可以是镍。碱土金属铝酸盐核可以是铝酸镁、铝酸钙、铝酸锶、铝酸钡或其任意组合。碱土金属铝酸盐核可以是铝酸镁,氧化还原-金属氧化物层可以是二氧化铈层,金属掺杂剂可以是铌(nb)、铟(in)镧(la)或镓(ga)或其任意组合,以及活性金属可以是镍(ni)。在一些实施方案中,催化剂可以包含65重量%至85重量%的氧化铝或铝酸镁、10重量%至20重量%的二氧化铈和5重量%至10重量%的镍。在某些情况下,可以将0.5重量%至2重量%的铌或铟引入二氧化铈层的晶格框架中。本发明的用于通过甲烷双重整制备合成气的催化剂的氧化还原-金属氧化物层的厚度可以是1纳米(nm)至500nm,优选为1nm至100nm,或更优选为1nm至10nm。在一些实施方案中,描述了用于直接还原铁矿石的系统。系统可以包括能够由包含h2、co、二氧化碳(co2)、甲烷(ch4)和水(h2o)的气体反应物流制备合成气的重整装置,所述合成气包含h2/co摩尔比为1.6至2.0的氢气(h2)和一氧化碳(co)。重整装置可以包括含有气体反应物原料和催化剂材料的反应区。催化剂材料可以包含化学惰性的金属氧化物核、沉积在金属氧化物核表面上的包含掺杂剂的氧化还原金属氧化物层和沉积在氧化还原金属氧化物层表面上的催化活性的金属,以及与重整器流体连通的熔炉,熔炉能够使用从重整器接收到的合成气还原铁矿石。以下包括本说明书全文使用的各种术语和短语的定义。术语“氧迁移率”指氧离子(o-)从金属氧化物中除去的难易程度,并且与金属氧化物晶格中的晶体缺陷有关。在ceo2-x的情况下,x代表了可用于氧化还原反应的可除去的氧或可移动的氧。术语“催化剂”指改变化学反应速率的物质。“催化”指具有催化剂的性质。术语“掺杂物”或“掺杂剂”指添加或引入到催化剂中以优化催化性能的杂质(例如提高或降低催化活性)。与未掺杂的催化剂相比,掺杂的催化剂可以提高或降低由催化剂催化的反应的选择性、转化率和/或产率。掺杂和促进在本公开全文中可互换使用。术语“约”或“大约”被定义为如本领域普通技术人员所理解的接近于。在一个非限制性的实施方案中,该术语被定义为10%以内,优选地5%以内,更优选地1%以内,并且最优选地0.5%以内。术语“基本上”及其变体被定义为10%以内、5%以内、1%以内或0.5%以内。术语“抑制”或“减少”或“防止”或“避免”或这些词语的任何变体当在权利要求和/或说明书中使用时,包括任何达到预期结果的可测量的减少或完全抑制。术语“有效地”当在权利要求和/或说明书中使用时,指足以达到希望的、期望的或预期的结果。与权利要求或说明书中的任意术语“包含”、“包括”、“含有”或“具有”结合使用时,在要素前不使用数字可以表示“一个”,但是它也与“一个或多个”、“至少一个”和“一个或多于一个”的含义一致。词语“包含”、“具有”、“包括”或“含有”是包括性的或开放式的,并且不排除其他另外的、未列举的要素或方法步骤。本发明的催化剂、方法和系统可以“包含”说明书全文所公开的特定成分、组分、组合物等,或“基本上由”或“由”说明书全文所公开的特定成分、组分、组合物等组成。在一个非限制性方面,关于过渡短语“基本上由……组成”,本发明的催化剂、方法和系统的基本和新颖的特征是它们双重整甲烷以制备h2/co比为1.4至2.0、优选约1.85的合成气的能力,这种合成气适用于直接还原铁。在本发明的上下文中,描述了至少20个实施方案。实施方案1是由甲烷制备合成气的方法。方法包括在足以制备包含h2和co的气体产物流的条件下,将包含氢气(h2)、一氧化碳(co)、二氧化碳(co2)、甲烷(ch4)和水(h2o)的反应物气体流与催化剂材料接触的步骤,其中h2/co的摩尔比为1.4至2.0。催化剂材料含有化学惰性的金属氧化物核;沉积在金属氧化物核表面上的包含掺杂剂的氧化还原金属氧化物层;和沉积在氧化还原金属氧化物层表面上的催化活性的金属。实施方案2是实施方案1的方法,其中反应条件包括700℃至1000℃的温度、约0.1mpa至2mpa的压力和500h-1至100000h-1的气时空速。实施方案3是实施方案1至2中任一项的方法,其中反应物流含有25体积%至40体积%的h2、5体积%至30体积%的co、5体积%至20体积%的co2、10体积%至30体积%的ch4和10体积%至30体积%的h2o。实施方案4是实施例3的方法,其中反应物流含有30体积%至35体积%的h2、10体积%至20体积%的co、10体积%至15体积%的co2、15体积%至20体积%的ch4和15体积%至20体积%的h2o。实施方案5是实施方案1至4中任一项的方法,其中h2/co的摩尔比为1.6至2.0,优选为1.85。实施方案6是实施方案1至5中任一项的方法,其中条件包括在催化剂与气体反应物流接触之前,在至少550℃的温度下使催化剂与含有至少50体积%的co2的co2流接触至少6小时。实施方案7是实施方案6的方法,其还包括用ch4、h2o、co和h2代替co2流中的一部分co2以产生气体反应物流的步骤。实施方案8是实施方案7的方法,其中代替co2流中的一部分co2包括将ch4引入co2流,并在至少600℃的温度下使加热的催化剂与co2/ch4流接触至少1小时;随时间增加co2/ch4流中ch4相对于co2的量的浓度,以产生含有约等量co2和ch4的co2/ch4流;在至少700℃的温度下将h2o引入co2/ch4流中以形成co2/ch4/h2o流;在至少700℃的温度下将co和h2引入co2/ch4/h2o流,形成含有h2、co、co2、ch4和h2o的气体反应物流。实施方案9是实施方案8的方法,其中步骤(b)还包括以约5℃每小时至10℃每小时的速率将温度从600℃增加至至少700℃。实施方案10是实施方案1至9中任一项的方法,其中催化剂上焦炭的形成被基本抑制或完全抑制。实施方案11是实施方案1至10中任一项的方法,其中压力保持恒定至少600小时或至少1200小时。实施方案12是实施方案1至11中任一项的方法,其还包括向直接还原铁装置提供产物流并将氧化铁还原为铁的步骤。实施方案13是实施方案1至12中任一项的方法,其中催化剂具有核/壳结构,其中氧化还原-金属氧化物层包围核,优选地核为氧化铝或碱土金属铝酸盐核。实施方案14是实施方案13的方法,其中碱土金属铝酸盐核是铝酸镁、铝酸钙、铝酸锶、铝酸钡或其任意组合。实施方案15是实施方案14的方法,其中碱土金属铝酸盐核是铝酸镁,氧化还原-金属氧化物层是二氧化铈层,金属掺杂剂是铌(nb)、铟(in)、镧(la)、镓(ga)或其任意组合,以及活性金属是镍(ni)。实施方案16是实施方案1至15中任一项的方法,其中化学惰性的金属氧化物核是氧化铝或铝酸镁;氧化还原-金属氧化物层是二氧化铈(ceo2),并且金属掺杂剂是铌(nb)、铟(in)、镧(la)、镓(ga)或其合金或其任意组合;以及活性金属是镍。实施方案17是实施方案16的方法,其中化学惰性的金属氧化物核含有65重量%至85重量%的氧化铝或铝酸镁;氧化还原-金属氧化物层含有10重量%至20重量%的二氧化铈;以及镍的量为5重量%至10重量%。实施方案18是实施方案17的方法,其中0.5重量%至2重量%的铌或铟被引入到二氧化铈层的晶格框架中。实施方案19是实施方案1至18中任一项的方法,其中氧化还原-金属氧化物层的厚度为1纳米(nm)至500nm,优选为1nm至100nm,更优选为1nm至10nm。实施方案20是一种用于直接还原铁矿石的系统,其中系统包括能够由气体反应物流制备合成气的重整装置,合成气包含h2/co摩尔比为1.6至2.0的氢气(h2)和一氧化碳(co),反应物气体流包含h2、co、二氧化碳(co2)、甲烷(ch4)和水(h2o)。在某些方面,重整装置包括(i)含有气体反应物原料和催化剂材料的反应区,催化剂材料含有化学惰性的金属氧化物核;沉积在金属氧化物核表面上的含有掺杂剂的氧化还原金属氧化物层;和沉积在氧化还原金属氧化物层表面上的催化活性的金属;以及(ii)与重整器流体连通的炉,所述炉能够使用从重整器接收到的合成气还原铁矿石。由以下的附图、详细描述和实施例,本发明的其他目的、特征和优点将变得明显。然而应当理解,附图、详细描述和实施例虽然说明了本发明的具体实施方案,但是仅以说明的方式给出,并不意味着限制。另外可以预期,通过这些详细描述,本领域技术人员在本发明的精神和范围内做出的改变和修改是明显的。附图说明受益于以下详细描述并参考所附的附图,本发明的优点对本领域技术人员而言是明显的。图1描述了催化剂核-壳结构的示意图。图2a至图2c描述了通过本发明的催化剂氧化残留碳的反应示意图。图3是包含本发明的催化剂的直接还原铁系统的示意图。图4a和图4b显示了(图4a)γ-al2o3的扫描透射电子显微镜(stem)图像和(图4b)γ-al2o3的能量色散x射线衍射光谱edx光谱,其中电子束瞄准图4a中为“束”的点。图5a和图5b显示了(图5a)1重量%in+25重量%ceo2/γ-al2o3的stem图像和(图5b)样品的edx光谱,其中电子束瞄准图5a中为“束”的点。图6a和图6b显示了(图6a)8重量%ni/1重量%ino2+25重量%ceo2/γ-al2o3的stem图像和(图6b)样品的edx光谱,其中电子束瞄准图6a中为“束”的点。图7显示了表2中列出的不同原料、步骤编号和原料组成中转化的co2%。图8显示了表2中列出的不同原料、步骤编号和原料组成中转化的ch4%。图9显示了用表2中列出的不同原料、步骤编号和原料组成获得的h2/co比。图10显示了废催化剂的x射线衍射(xrd)图谱,(a)商用催化剂,(b)ni/in-ceo2-mgal,(c)ni/nb-ceo2-mgal和(d)ni/la-ceo2-mgal核-壳催化剂。图11显示了废催化剂的程序升温氧化曲线。图12显示了针对商用催化剂、ni/in-ceo2-mgal和ni/la-ceo2-mgal核-壳催化剂进行的加速焦化研究。尽管本发明容易获得各种修改和替换形式,但其具体实施方案通过附图以举例说明的方式示出。附图可能未按比例绘制。具体实施方式目前可获得的用于烃类双重整制备合成气的催化剂具有生成碳残留物(例如焦炭和碳晶须)和烧结的倾向,这会导致催化剂性能低下,并在使用相对较短的时间后导致催化剂最终失效。这会导致合成气生产效率低下,以及与生产和最终其用于将铁矿石还原为铁的用途有关的成本增加。已经发现了避免与双重整催化剂的失活和机械降解有关的问题的解决方案。该发现基于使用具有特定核-壳结构的催化剂。核包含化学惰性或基本上惰性的材料(比如:金属氧化物核、黏土核或沸石核,或其任意组合)。壳包围核并具有氧化还原-金属氧化物相,其包含引入氧化还原-金属氧化物相的晶格框架中的金属掺杂剂。活性/催化金属沉积在壳的表面上。不希望受理论约束,认为在说明书全文中所描述的具有这种核-壳结构的催化剂可以氧化由于甲烷分解和一氧化碳歧化而在其表面上形成的碳。这种催化剂在超过300小时的使用中催化活性损失最小。此外,当与目前可获得的基于甲烷双重整的催化剂相比时,本发明的催化剂具有增加的机械强度和在制备过程中降低的成本。更进一步,在核材料为碱土金属铝酸盐(如铝酸镁mgal2o4)核的一些特定情况下,认为这种核对co2有高亲和力,从而吸收更多的二氧化碳,并有助于氧化催化剂上形成的碳,以进一步减少焦化和烧结的发生率。该催化剂可用于甲烷双重整反应以制备h2/co的摩尔比为1.4:1至2.0:1,优选约1.85:1的产物流。产物流可以用于直接还原铁而不需要进一步纯化。本发明的这些和其他非限制性方面将在以下章节中更详细地讨论。a.催化剂和催化剂结构催化剂材料可以包含化学惰性的金属氧化物核(例如al2o3、碱土金属铝酸盐、sio2、tio2、沸石、无定形硅铝、黏土、橄榄石砂、尖晶石、钙钛矿、mgo或zro2,优选al2o3或γ-al2o3或碱土金属铝酸盐(如铝酸镁、铝酸钙、铝酸锶、铝酸钡));沉积在金属氧化物核的表面上的氧化还原金属氧化物(例如二氧化铈(ceo2))层,氧化还原金属氧化物层包含掺杂剂(铌(nb)、铟(in)、或镧(la)、镓(ga)或其任意组合);以及沉积在氧化还原金属氧化物层的表面上的催化活性的金属(如镍、铑、钌、铂或其任意组合)。在一些实施方案中,催化剂可以包含氧化铝或铝酸镁核,具有nb、in和/或la作为金属掺杂剂的ceo2氧化还原-金属氧化物层和活性金属ni。在一些实施方案中,催化剂包含65重量%至85重量%的氧化铝或铝酸镁、10重量%至20重量%的二氧化铈;和5重量%至10重量%的镍。在某些情况下,可以将0.5重量%至2重量%的铌或铟引入二氧化铈层的晶格框架中。氧化还原-金属氧化物层的厚度可以为1纳米(nm)至500nm,优选1nm至100nm,或更优选1nm至10nm。在一些方面,催化剂可以具有核/壳结构,其中氧化还原-金属氧化物层包围氧化铝或碱土金属铝酸盐核。在优选的实施方案中,催化剂包含铝酸镁核,二氧化铈层,nb、in、la、ga或其任意组合的掺杂剂和活性金属ni。在一些情况下,催化剂不包含金属掺杂剂,但包含沉积在氧化还原-金属氧化物壳的表面上的两种或多于两种金属。在甲烷双重整反应中,核可以是化学惰性的,并且还可以为催化剂的反应性壳提供足够的机械支撑。壳可以具有包含金属掺杂剂(如铟、铌或两者)的氧化还原-金属氧化物相,所述金属掺杂剂掺入氧化还原-金属氧化物相的晶格框架中。与核相比,壳的氧迁移率更高。在一个特定方面,核为al2o3,氧化还原-金属氧化物相是二氧化铈,金属掺杂剂是铟、铌或两者,并且沉积在壳表面上的金属是镍、铑、钌、铂或其任意组合(例如镍、镍和铂或镍和铑)。壳的厚度可以为1个原子单层至100个原子多层(如1个原子厚、10个原子厚、20个原子厚、30个原子厚、40个原子厚、50个原子厚、60个原子厚、70个原子厚、80个原子厚、90个原子厚或100个原子厚)。在一些方面,催化剂包含5重量%至50重量%、优选7重量%至20重量%、并且更优选9重量%至15重量%的氧化还原金属氧化物相,0.1重量%至5重量%、优选0.75重量%至4重量%、或更优选1重量%至3重量%的金属掺杂剂,沉积在壳表面上的1重量%至40重量%、优选2重量%至15重量%、或更优选5重量%至12重量%的金属,或其任意组合。催化剂可以是颗粒形式的。在一些情况下,催化剂的平均粒径为100μm至1000μm,优选200μm至800μm,或更优选250μm至550μm。在本发明的某些方面,催化剂是自负载的,然而,催化剂可以负载在基材(例如玻璃、聚合物珠或金属氧化物)上。图1为本发明的催化剂的核-壳结构的示意图。催化剂100包含核102、壳104和活性金属106。核102可以是整个说明书中描述的基本上化学惰性的材料。核102可以为壳104提供机械强度。壳104可以是能够发生电子态(例如还原态和氧化态(氧化还原))转变的材料(例如金属氧化物)。这样的材料在整个说明书中进行描述。壳104可以在核上形成。在优选的实施方案中,壳104基本上包围核或完全包围核。在一些方面,壳104可以附着在核102的外表面。壳104的晶格中可以包含整个发明书中描述的一种或多于一种掺杂剂(未示出)。整个发明书中描述的活性金属106可以沉积在壳104层的顶部。活性金属106在甲烷干重整反应过程中具有催化活性。催化剂100的核-壳结构可以提供用于甲烷干重整反应的经济、机械强度高和高效的催化剂。催化剂100可以为任何形式或形状。在优选的实施方案中,催化剂是颗粒形式。颗粒的平均粒径可以为100μm至1000μm,优选地,200μm至800μm,或更优选地250μm至550μm,或者为100μm、110μm、120μm、130μm、140μm、150μm、160μm、170μm、180μm、190μm、200μm、210μm、220μm、230μm、240μm、250μm、260μm、270μm、280μm、290μm、300μm、310μm、320μm、330μm、340μm、350μm、360μm、370μm、380μm、390μm、400μm、410μm、420μm、430μm、440μm、450μm、460μm、470μm、480μm、490μm、500μm、510μm、520μm、530μm、540μm、550μm、560μm、570μm、580μm、590μm、600μm、610μm、620μm、630μm、640μm、650μm、660μm、670μm、680μm、690μm、700μm、710μm、720μm、730μm、740μm、750μm、760μm、770μm、780μm、790μm、800μm、810μm、820μm、830μm、840μm、850μm、860μm、870μm、880μm、890μm、900μm、910μm、920μm、930μm、940μm、950μm、960μm、970μm或1000μm或者其中的任何值或范围。可以使用brunauer、emmett和teller(bet)方法测量表面积。在一些实施方案中,催化剂负载在基材上。基材的非限制性实例包括玻璃、聚合物珠或金属氧化物。金属氧化物可以与核材料或壳材料的金属氧化物相同或者不同。1.核核102可以是金属氧化物、黏土、沸石或其任意组合。核102可以是多孔材料、化学惰性的材料或二者。金属氧化物的非限制性实例包括耐高温的氧化物、α氧化铝(al2o3)、β氧化铝或θ氧化铝、活性al2o3、碱土金属铝酸盐、二氧化硅(sio2)、二氧化钛(tio2)、氧化镁(mgo)、氧化钙(cao)、氧化锶(sro)、氧化锆(zro2)、氧化锌(zno)、氧化铝锂(lialo2)、氧化铝镁(mgalo4)、锰的氧化物(mno、mno2、mn2o4)、氧化镧(la2o3)、硅胶、铝硅酸盐、无定形硅铝、镁砂、尖晶石,钙钛矿或其任意组合。碱土金属铝酸盐的非限制性实例包括铝酸镁、铝酸钙、铝酸锶、铝酸钡或其任意组合,其中特别优选铝酸镁。黏土的非限制性实例包括高岭土、硅藻土、活性白土、蒙脱石、坡缕石、海泡石、酸改性的黏土、热改性的黏土、化学处理的黏土(例如离子交换的黏土)或其任意组合。沸石的实例包括y-沸石、β沸石、丝光沸石、zsm-5沸石和镁碱沸石。所有用于制造本发明的负载型催化剂的材料都可以购买或通过本领域普通技术人员已知的方法制造(例如:沉淀/共沉淀、溶胶凝胶法、模板/表面衍生金属氧化物合成、固相合成、混合金属氧化物、微乳液技术、溶剂热、声化学、燃烧合成等)。核材料的商业制造商的非限制性实例包括zeolyst(美国)、alfa(美国)cri/标准催化剂和技术公司(美国)和(美国)、basf(德国)以及(美国)。核材料可以是任何形状或形式。形状或形式的非限制性实例包括球形、圆柱形(例如挤出物、粒料)、中空圆柱形、圆球状或成型为具有2瓣、3瓣或4瓣,或为块体。核材料可以是直径为约0.10厘米(cm)至0.5cm、0.15cm至0.40cm或0.2cm至0.3cm的圆柱状颗粒。核材料的表面积可以为5m2/g至300m2/g、10m2/g至280m2/g、20m2/g至270m2/g、30m2/g至250m2/g、40m2/g至240m2/g、50m2/g至230m2/g、60m2/g至220m2/g、70m2/g至210m2/g、80m2/g至200m2/g、100m2/g至150m2/g或其中的任何值或范围。在优选的实施方案中,载体材料是直径约0.32cm(1/8英寸)、bet表面积约230m2/g的γ-氧化铝挤出物。载体材料的barrett-joyner-halenda(bjh)吸附累积孔体积可以是0.557cm3/g的1.7000nm至300.0000nm,bjh吸附平均孔径(4v/a)为6.78nm。在一些特别优选的情况下,即核包含铝酸镁时,核可以包含5重量%至60重量%的mgo,或10重量%、15重量%、20重量%、25重量%、30重量%、35重量%、40重量%、45重量%、50重量%、55重量%、60重量%或其中任何范围或值的mgo。2.壳壳104可以是包含金属氧化物的层,金属氧化物可以根据化学条件或其氧化还原能力呈现多种氧化态。还原剂和氧化剂可以是氧化还原对(例如m+/m2+)。壳104的厚度可以为1个原子单层至100个原子多层,或5个原子多层至80个原子多层、10个原子多层至60个原子多层或20个原子多层至5个原子多层,或1个原子单层、5个原子多层、10个原子多层、15个原子多层、20个原子多层、25个原子多层、30个原子多层、35个原子多层、40个原子多层、45个原子多层、50个原子多层、55个原子多层、60个原子多层、65个原子多层、70个原子多层、75个原子多层、80个原子多层、85个原子多层、90个原子多层或100个原子多层或者其中的任何范围或值。可以具有氧化还原-金属氧化物相(例如氧化还原对)的金属氧化物的非限制性实例包括铈(ce)氧化物、铁(fe)氧化物、钛(ti)二氧化物、锰(mn)氧化物、铌(nb)氧化物、钨(w)氧化物或锆(zr)氧化物,优选铈氧化物。这些金属氧化物可以在特定的化学条件(例如加热)下形成氧化铈相、氧化铁相、氧化钛相、氧化锰相、氧化铌相、氧化钨相或氧化锆相。氧化还原-金属氧化物的量可以为基于催化剂总重量的5重量%至50重量%、7重量%至20重量%、9重量%至15重量%,或1重量%、2重量%、3重量%、4重量%、5重量%、6重量%、7重量%、8重量%、9重量%、10重量%、11重量%、12重量%、13重量%、14重量%、15重量%、16重量%、17重量%、18重量%、19重量%、20重量%、21重量%、22重量%、23重量%、24重量%、25重量%、26重量%、27重量%、28重量%、29重量%、30重量%、31重量%、32重量%、33重量%、34重量%、35重量%、36重量%、37重量%、38重量%、39重量%、40重量%、41重量%、42重量%、43重量%、44重量%、45重量%、46重量%、47重量%、48重量%、49重量%或50重量%。金属氧化物相(或金属氧化物层)可以包含一种或多于一种金属掺杂剂。可以将金属掺杂剂掺入金属氧化物的晶格中。掺杂剂可以为金属氧化物晶格提供机械强度、减少从金属氧化物晶格中除去氧阴离子所需的能量,或两者。金属掺杂剂的非限制性实例包括铟(in)、镓(ga)、铌(nb)、镧(la)、锗(ge)、砷(as)、硒(se)、锡(sn)、锑(sb)、碲(te)、铊(tl)或铅(pb)或其任意组合,优选铟。氧化还原-金属氧化物的量可以为基于催化剂总重量的0.1重量%至5重量%、0.75重量%至4重量%、1重量%至3重量%或0.1重量%、0.2重量%、0.3重量%、0.4重量%、0.5重量%、0.6重量%、0.7重量%、0.8重量%、0.9重量%、1.0重量%、1.1重量%、1.2重量%、1.3重量%、1.4重量%、1.5重量%、1.6重量%、1.7重量%、1.8重量%、1.9重量%、2.0重量%、2.1重量%、2.2重量%、2.3重量%、2.4重量%、2.5重量%、2.6重量%、2.7重量%、2.8重量%、2.9重量%、3.0重量%、3.1重量%、3.2重量%、3.3重量%、3.4重量%、3.5重量%、3.6重量%、3.7重量%、3.8重量%、3.9重量%、4.0重量%、4.1重量%、4.2重量%、4.3重量%、4.4重量%、4.5重量%、4.6重量%、4.7重量%、4.8重量%、4.9重量%或5.0重量%。金属氧化物和金属掺杂剂都可以从商业制造商如购买。氧化还原-金属氧化物相可以改变氧化态。因此,可以释放与晶格键合的氧阴离子,并吸收其他含氧化合物(例如分子氧、超氧化物和臭氧),由此壳104中的氧具有迁移性。由于金属氧化物的氧化还原能力,壳104的氧迁移率比核102更高。由于金属氧化还原相的结构,可以在不打乱或破坏金属氧化物晶格的情况下除去氧阴离子。随着更多的氧原子被提取出来,空位的浓度会增加,从而留下由金属原子共享的两个电子。氧原子可以从金属氧化物的任何表面或表面下提取。以类似的方式,金属可以吸收分子氧(o2)进入空位,其由于可用电子的增加而氧化一部分金属。不期望受理论约束,认为壳通过这种氧化还原过程来储存和释放氧阴离子的能力有助于将沉积在催化剂表面上的碳氧化为一氧化碳。例如,如图2所示,碳原子可以沉积在金属氧化物表面吸附的氧上,并作为一氧化碳释放。图2是碳通过与催化剂100的氧化还原-金属氧化物相接触而氧化的示意图。在图2中,为简便起见,没有绘出活性金属106和核102。参照图2a,碳原子202被氧原子204吸引,氧原子204与壳104的金属-氧化还原相的金属原子206键合。如图2b所示,碳原子202和氧原子204键合以形成一氧化碳208。在图2c中,一氧化碳208可以从壳104中扩散出来,氧分子210可以被吸收到空位212中以继续残留碳的氧化过程。3.活性金属催化剂100可以包含一种或多于一种活性(催化)金属以促进将甲烷重整为二氧化碳。活性金属106可以附着在壳104的表面(见图1)。活性金属106可以包括一种或多于一种元素周期表中第7列至11列(viib族、viii族和ib族)的金属。活性金属的非限制性实例包括镍(ni)、铑(rh)、钌(re)、铱(ir)、铂(pt)、钯(pd)、金(au)、银(ag)、钴(co))、锰(mn)、铜(cu)或其任意组合或合金,优选镍、铑、钌或铂,或其任意组合或合金。壳104上的活性金属的量特别取决于催化剂的催化(金属)活性。在一些实施方案中,壳上催化剂的量可以是基于催化剂总重量的1重量%至40重量%、2重量%至15重量%、5重量%至12重量%,或1重量%、2重量%、3重量%、4重量%、5重量%、6重量%、7重量%、8重量%、9重量%、10重量%、11重量%、12重量%、13重量%、14重量%、15重量%、16重量%、17重量%、18重量%、19重量%、20重量%、21重量%、22重量%、23重量%、24重量%、25重量%、26重量%、27重量%、28重量%、29重量%、30重量%、31重量%、32重量%、33重量%、34重量%、35重量%、36重量%、37重量%、38重量%、39重量%、40重量%。在一些情况下,活性金属可以是二元合金(m1m2)或三元合金(m1m2m3),其中m1是镍,m2和m3各自为铑(rh)、钌(ru)、铱(ir)、铂(pt)、钯(pd)、金(au)、银(ag)、钴(co)、锰(mn)、铜(cu)、锌(zn)、铁(fe)、钼(mo)或锆(zr)。在特定的情况下,活性金属可以是二元合金(m1m2),其中m1是镍,m2是铑(rh)或铂(pt)(例如:nirh或nipt)。b.核-壳催化剂的制备本发明的催化剂可以通过提供核-壳结构的方法制备。如在实施例中进一步说明的,催化剂可以使用已知的催化剂制备方法(如干浸渍法或湿浸渍法、喷涂法、均匀沉积沉淀法、原子层沉积技术、浸涂法等)制备。在非限制性实例中,将第一金属盐(例如氧化还原-金属盐)和第二金属盐(例如金属掺杂剂的盐)溶解在溶液(例如水)中。第一金属盐的实例包括ce、fe、ti、mn、nb、w或zr的硝酸盐、硝酸铵、碳酸盐、氧化物、氢氧化物、卤化物。第二金属盐的实例包括元素周期表第7列至12列金属的硝酸盐、硝酸铵、碳酸盐、氧化物、氢氧化物、卤化物。在特定的实施方案中,将nbcl5或incl3·4h2o和(nh4)2ce(no3)6溶解在去离子水中。溶液中存在的第一金属盐和第二金属盐的重量比可以为至少5:1、5:1至30:1、7:1至20:1、10:1至15:1,或5:1、6:1、7:1、8:1、9:1、10:1、11:1、12:1、13:1、14:1、15:1、16:1、17:1、18:1、19:1、20:1、21:1、22:1、23:1、24:1、25:1、26:1、27:1、28:1、29:1、30:1,或其中的任何范围或值。在一些实施方案中,没有使用第二金属盐(金属掺杂剂)。可以用溶液浸渍核材料(如金属氧化物核)的孔体积。在特定的实施方案中,用溶液浸渍铝酸镁挤出物的孔体积。浸渍的材料可以在50℃至150℃、75℃至100℃、80℃至90℃,或50℃、55℃、60℃、65℃、70℃、75℃、80℃、85℃、90℃、95℃、100℃、105℃、110℃、115℃、120℃、125℃、130℃、135℃、140℃、145℃或150℃的平均温度下干燥2小时、3小时、4小时、5小时、6小时、7小时、8小时、9小时、10小时或直至认为浸渍的材料是干燥的。干燥的浸渍材料可以在500℃至800℃、600℃至700℃或500℃、525℃、550℃、575℃、600℃、625℃、650℃、675℃、700℃、725℃、750℃、775℃或800℃的平均温度下煅烧(转化为金属氧化物)2小时、3小时、4小时或直至认为浸渍材料已充分地煅烧以获得核-壳的结构,其中壳包围核,并且壳具有由第一金属盐形成的氧化还原-金属氧化物相和由第二金属盐形成的金属掺杂剂,所述金属掺杂剂掺入氧化还原-金属氧化物相的晶格框架中。可以重复该过程以获得含有所需量的掺杂剂的壳,以调节催化材料的氧迁移率。在一些实施方案中,溶液可以逐步地浸渍核材料。例如,氧化还原-金属盐可以浸渍核材料的孔体积,干燥并煅烧,然后可以用掺杂金属浸渍核材料的孔体积,干燥并煅烧,以形成核-壳材料。可以重复该过程以获得含有所需量的掺杂剂的壳,以调节催化材料的氧迁移率。可以通过重复氧化还原金属-盐浸渍的步骤来增加氧化还原金属氧化物层的厚度。可以用x射线衍射方法测定掺杂剂在氧化还原金属氧化物(例如ceo2)相中的引入。例如,由于掺杂剂的引入,含有ceo2和掺杂剂的催化剂在与ceo2相关的衍射图中显示出轻微的偏移。可以将一些掺杂剂分散在核中,然而大部分的掺杂剂保留在壳中,并在煅烧过程中均匀地分散在壳中。可以使用已知的金属沉积法(例如浸渍、喷涂、化学气相沉积等)将一种或多于一种的活性金属沉积在壳的表面。在非限制的实例中,核-壳结构可以用活性金属的水溶液缓慢浸渍。例如,可以在持续的机械搅拌下,将活性金属溶液滴加到金属氧化物挤出物中。浸渍的材料可以在50℃至120℃、75℃至110℃、80℃至90℃,或是50℃、55℃、60℃、65℃、70℃、75℃、80℃、85℃、90℃、95℃、100℃、105℃、110℃、115℃或120℃的平均温度下干燥0.5小时、1小时或2小时或直至认为浸渍的材料是干燥的。干燥浸渍的核-壳材料可以在500℃至850℃、600℃至800℃或500℃、525℃、550℃、575℃、600℃、625℃、650℃、675℃、700℃、725℃、750℃、775℃、800℃、825℃或850℃的平均温度下煅烧(转化为金属氧化物)0.5小时、1小时、2小时或直至认为浸渍的材料已充分地煅烧以获得具有核-壳结构的催化剂(例如,图1中的催化剂100),其中活性金属沉积在壳的表面上。可以将得到的核-壳催化剂粉碎并筛至所需的尺寸,例如300μm至500μm。氧化还原氧化物前体和活性金属前体的浸渍可在粉末或预成形结构例如圆柱中空盘、圆柱盘、球形、4孔至10孔圆柱盘状结构或0.4mm至4mm的挤出物上进行。如果对粉末进行浸渍,则可以使用造粒工具将最终催化剂压制成不同的形式。如实施例章节中描述的,本发明制备的核-壳催化剂是在高温下抗烧结和耐焦的材料,例如通常用于合成气制备或甲烷干重整反应(例如700℃至950℃或725℃至950℃、750℃至950℃、775℃至950℃、800℃至950℃、900℃至950℃)的材料。进一步地,在700℃至950℃或800℃至900℃的温度,0.1mpa的压力和/或500h-1至10000h-1的气时空速(ghsv)下,优选800℃的温度,0.1mpa的压力和75000h-1的ghsv下制备的催化剂可以有效地用于甲烷的二氧化碳重整反应。c.甲烷的双重整还公开了由甲烷的双重整反应制备氢气和一氧化碳(合成气)的方法。在特定的情况下,可以由含有甲烷、水、一氧化碳、氢气、氮气和二氧化碳的反应物气体混合物原料来制备合成气。方法可以包括在足以制备氢气和一氧化碳的条件下使反应物气体混合物与本发明的任意一种催化剂接触,其中甲烷的转化率为至少50%、60%、70%、80%或者大于80%。这种足以制备气体混合物的条件可以包括700℃至1000℃、750℃至950℃或725℃至1000℃、750℃至1000℃、775℃至1000℃、800℃至1000℃、900℃至1000℃的温度,0.1mpa至2.0mpa的压力,和/或500h-1至100000h-1或500h-1至100000h-1、1000h-1至100000h-1、5000h-1至100000h-1、10000h-1至100000h-1、20000h-1至100000h-1、30000h-1至100000h-1、40000h-1至100000h-1、50000h-1至100000h-1、60000h-1至100000h-1、70000h-1至100000h-1、80000h-1至100000h-1、90000h-1至100000h-1的气时空速(ghsv)。在特定的情况下,使用750℃至800℃的平均温度、0.1mpa的压力和70000h-1至75000h-1的ghsv。在这种条件下,甲烷的转化率为60%至98%,优选为80%至95%。h2/co比可以为至少1.4:1至2.0:1,或1.5:1至1.95:1、1.7:1至1.90:1,或者至少等于或在1.4:1、1.45:1、1.5:1、1.55:1、1.6:1、1.65:1、1.7:1、1.75:1、1.8:1、1.85:1、1.9:1、1.95:1和2的任意两者之间,或约1.85:1。在特定的情况下,烃包括甲烷,氧化剂是水和二氧化碳。在特定的方面,在核-壳结构催化剂上残留碳的形成或焦化会减少或不发生,和/或在核-壳结构催化剂上烧结减少或不发生。在特定的情况下,当将核-壳结构催化剂置于超过700℃或800℃的温度或725℃至950℃、750℃至950℃、775℃至950℃、800℃至950℃、900℃至950℃的范围时,碳残留形成或焦化和/或烧结会减少或不发生。在特定的情况下,在0.1mpa至0.2mpa的压力下,所述范围可以为700℃至950℃或750℃至1000℃。不期望受到理论约束,认为没有或基本上没有发生烧结,由于在催化剂的晶格中提高了氧迁移率,因此氧化了烃分解产生的焦炭,从而使活性位点在更长的时间内可用。当制备的催化材料用于甲烷双重整反应时,气体原料混合物中的水和二氧化碳可以从各种来源获得。在直接还原铁的系统中,二氧化碳和水可以在竖炉中铁矿石的还原过程中产生。在还原过程中,一氧化碳转化为二氧化碳,氢气转化为水蒸气。反应物气体混合物可以包含天然气或甲烷、包含c2至c5烃、c6+重烃(例如:c6至c24烃如柴油、喷气燃料、汽油、焦油、煤油等)的液化石油气、含氧烃和/或生物柴油、醇类或二甲醚。在特定的情况下,反应物气体混合物的总氧与碳原子之比等于或大于0.9。方法还可以包括分离和/或储存产生的气体混合物。方法还可以包括从制备的气体混合物中分离氢气(例如使制备的气体混合物通过氢气选择性膜以产生氢气渗透物)。方法可以包括从制备的气体混合物中分离一氧化碳(例如使制备的气体混合物通过一氧化碳选择性膜以产生一氧化碳渗透物)。d.直接还原铁系统在一些实施方案中,用于甲烷双重整的双重整装置可以用于直接还原铁(dri)系统。参照图3,描述了dri系统。dri系统可以包括双重整装置302、竖炉304、热回收系统306、洗涤器308和冷却装置310。还需要其他加热和/或冷却装置(例如隔热、电加热器、夹套墙内热交换器)或控制器(例如计算机、流量阀、机械阀等)以控制反应混合物的反应温度和压力。虽然只显示了一个装置,但应该理解一个装置可以容纳多个装置。在系统300中,反应物气体原料流312可以进入双重整装置302。反应物气体原料流312可以包含烃类(例如甲烷、乙烷、丙烷等,优选天然气)、水、一氧化碳、氢气、二氧化碳和任选的惰性气体。在一个优选的方面,原料流可以由14体积%至16体积%的co、12体积%至14体积%的co2、32体积%至36体积%的h2、16.5体积%至19.5体积%的h2o、14体积%至18体积%的ch4和3.5体积%至4.5体积%的n2组成。双重整装置302可以包括反应区314,反应区314包括本发明的催化剂316。在反应区314中,反应物原料312可以与催化剂316接触并生成产物流318。产物流318的h2/co摩尔比可以为1.4:1至2.0:1,或约1.85:1。产物流318可以从双重整装置302中流出并进入竖炉304。氧化铁流320可以进入竖炉304并与产物流318接触。氧化铁流320与产物流318接触可产生直接还原铁流322和循环流324。竖炉304中的接触温度可以是还原氧化铁所需的温度。循环流324可以从竖炉304中流出,通过洗涤器308以除去铁还原过程中的颗粒和/或副产物,然后通过冷却装置310(例如压缩机或一系列压缩机),并与反应物原料流312组合。可以基于控制h2/co摩尔比调节烃、co2、co和氢气的量。组合流可以通过热回收系统306,然后进入双重整装置302继续循环。如图3中所示,燃料价值耗尽的气体(循环流324)与另外的天然气一起循环到重整器中。沿该路径,耗尽气体中的多余水分被除去,以获得原料所需组成,其为14体积%至16体积%的co、12体积%至14体积%的co2、32体积%至36体积%的h2、16.5体积%至19.5体积%的h2o、14体积%至18体积%的ch4和3.5体积%至4.5体积%的n2。实施例本发明将通过具体实施例的方式进行更详细的描述。提供以下实施例仅作说明之用,而不旨在以任何方式来限制本发明。本领域技术人员将容易地识别可以进行改变或调整以产生基本上相同结果的各种非关键参数。实施例1(催化剂的合成)用于本发明的催化剂的金属前体盐包括rhcl3、h2ptcl6、nicl3·6h2o、la(no3)3·6h2o、nbcl3、incl3·4h2o、(nh4)2ce(no3)6。所有化学品均购自sigmamillipore(美国),并按原样使用。直径2mm、长5mm并含有不同量的mgo的mgal2o4挤出物由pacificindustrialdevelopmentcompany(pidc)(德国)提供。所使用的所有气体纯度为99.999体积%。步骤1:将硝酸铈铵(2.38g)和氯化铌(0.0872g)溶解在去离子水(2.83ml)中。用得到的溶液浸渍mgal2o4挤出物(5.0g)。浸渍之后,将浸渍材料在80℃的烘箱中在气流下干燥。在120℃下继续干燥2小时,然后在550℃下煅烧3小时。得到的材料是淡黄色的。步骤2:称量六水合氯化镍(0.911g)并在去离子水(1.63ml)中溶解。用得到的溶液缓慢浸渍步骤1中获得的材料(3g)。将材料在120℃下干燥2小时,并在850℃下煅烧4小时。通过如上所述类似的以下方案,制备含有1重量%in、1重量%ga和1重量%la掺杂剂的催化剂,其中掺杂剂金属盐在步骤1中加入。通过用氯铂酸代替氯化铑来制备具有活性金属pt或rh的催化剂。表1是制备及测试的催化剂的列表,其中mgal代表mgal2o4。表1实施例2(催化剂的表征)图4a和4b显示了在850℃下煅烧4小时的γ-al2o3的扫描透射电子显微照片(stem)和能量色散x射线衍射光谱(edx)。分析表明,样品中只包含“al”和“o”元素。分析拓展到含有1重量%in/25重量%ceo2/γ-al2o3的样品,并发现多层ceo2已经覆盖了al2o3(图5a和5b)。由于ce的分子量大于al,因此通过亮度的增加表明了ceo2层存在。另外,通过edx分析确认了ceo2层存在。10重量%至15重量%的ceo2负载不足以通过亮度来区分ceo2和al2o3,但是约25重量%的ceo2足以形成多层的ceo2,这能够区分两个不同的氧化物层,即ceo2和al2o3。此外,由于ceo2中“in”的负载较低,所以在斑点edx分析中无法识别该相。图6a和6b显示了8重量%ni/25重量%ceo2/γ-al2o3催化剂样品的stem和edx。图像显示,ni颗粒位于ceo2层上,仅通过比较亮度难以识别。然而,对球形颗粒的edx分析证实,这些颗粒确实是金属“ni”,并且特定地位于ceo2层上。实施例3(甲烷的双重整)在由avantiumbv(荷兰)提供的高通量反应器系统中进行催化剂测试。反应器是塞式流型的,并且由钢制成,内部为石英衬里。石英衬里的内径为4mm、长度为60cm,其用于防止由于钢表面甲烷裂解引起的焦化。将催化剂颗粒粉碎并筛分至300μm至500μm。催化剂筛部分放置在石英衬里的惰性材料顶部。通过混合纯气体并蒸发水来制备13%co2+16%ch4+34%h2+18%h2o+15%co+4%ar的原料气体混合物。用氩气作为质谱分析的内标物。在100%ar的存在下,将氧化态的催化剂加热至800℃,并使它们的实际气体混合物原料通过催化剂床。使用来自thermoscientificmodelthermobt的质谱仪进行气体分析。甲烷转化率按以下方式计算。氢气与一氧化碳的比按以下方式计算,在装置启动期间,通常使n2和co2的混合物流经催化剂床,同时催化剂床中的温度倾斜升温。新鲜催化剂通常处于氧化态,其在重整初期当ch4气体代替部分co2和n2时还原为金属态。至关重要的是,催化剂应能承受高浓度的co2并在启动阶段适应变化的氧化还原气体气氛。表2给出了在温度升高的不同阶段原料组成的变化。选择三种催化剂用于研究并置于相同的原料和反应条件下。实验在550℃下开始,其中原料中含有60%的co2。逐渐地,温度升高至600℃、650℃、700℃、750℃和800℃,逐步在原料中增加ch4同时代替co2。另外,在800℃下,作为最终检查,给实际重整器进料并监测催化剂性能。如预期的,所有三种催化剂都经历了原位还原和活化。ni/in-ce/al2o3在所有条件下都显示出比商用催化剂更好的性能(图7和图8),前者的h2/co比也优于后者(图9)。因为催化剂活化仅在780℃左右发生,ni/in-ce/mgal2o4表现出迟缓的性能,而商用催化剂和(ni/in-ce/al2o3)均在400℃左右活化。在>850℃的更高温度下,由于(ni/in-ce/al2o3)和(ni/in-ce/mgal2o4)均在800℃以下活化,预期两种催化剂的性能相同。表2表3给出了利用不同催化剂在600小时的反应时间(tos)后获得的ch4转化率%和h2/co比。商用催化剂和核-壳催化剂具有几乎相同的转化率。产物气体中h2/co比在可接受范围内,并可通过调节反应参数来改变。基于ni/in-ceo2-mgal和ni/nb-ceo2-mgal的催化剂在1200小时的反应时间内没有显示出碳。在类似条件下,基于ni/la-ceo2-mgal的催化剂和商用催化剂均显示存在焦炭。表3催化剂ghsv,h-1h2/coch4转化率%商用催化剂560001.8694ni-nbceo2-mgal560001.9396ni-laceo2-mgal560001.7886ni-inceo2-mgal291461.7085进一步测试了使用商用催化剂和ni-inceo2-al催化剂在800℃和70000h-1的空速下的合成气质量,结果在表4中给出。发现核-壳催化剂情况下合成气的性能和质量优于商用催化剂情况下合成气的性能和质量,这可能是因为金属的分散性更好,以及由于强金属-载体相互作用效应,ni与ceo2的相互作用所致。表4实施例4(废催化剂的表征和焦炭评估)废催化剂通过粉末x射线衍射表征。图10显示了双重整反应的废催化剂的x-射线衍射图。虚线给出了催化剂中的碳/焦炭的峰。从衍射图中可以明显地看出商用催化剂和ni/la-ceo2-mgal催化剂含有碳,但是ni/in-ceo2-mgal催化剂不含任何碳。这也得到了前面部分提到的tpo研究的支持。为了确认焦炭的形成,使用程序升温氧化过程对双重整反应的废催化剂进行了研究。使用由micromertics提供的tpdautochemii2920设备对样品进行分析。在20%o2+80%n2气体气氛下,将样品以10℃/分钟倾斜升温。导热系数分析仪分析了差异导热系数,在当前情况下,差异导热系数与由于催化剂上焦炭的氧化而形成的co2+co量成正比。如图10所示,商用废催化剂在600℃左右显示出峰,而有在inceo2壳上沉积ni、mgal2o4核的催化剂没有显示出任何峰,这证明了后者不含任何焦炭,表明ceo2壳上沉积ni-mgal2o4核更优越。这是因为mgal2o4被ceo2完全包围,并且ni只沉积在ceo2层上。进行了加速的焦化研究,以确定核-壳催化剂和商用催化剂的脱焦能力。考虑了两种核-壳天然催化剂和一种商用催化剂并将其置于重整反应条件下。原料组成为h2=34%、co=15%、co2=13%、ar=4%、ch4=16%、h2o=18%。首先,在800℃和1巴(0.1mpa)的压力下将催化剂暴露于重整器进料条件下300小时,然后将温度降至700℃,反应继续。在大约470小时,将温度进一步降至600℃并监测反应器压力。如图12所示,在约510小时后反应器内部的压力开始增大。压降直接与形成的焦炭量和焦炭对气流的限制成正比。从图中的图表可以清楚地看出,商用催化剂的焦化比核-壳催化剂更快。而且,ni/in-ceo2-mgal催化剂压降的量几乎可以忽略不计,虽然ni/la-ceo2-mgal确实显示出压降,但是比商用催化剂少得多。总之,本发明的基于核-壳结构的催化剂(例如ni/inceo2/al)在所有条件下均优于商用催化剂,前者的h2/co比也优于后者。负载在mgal2o4上的催化剂(例如:ni/ince/mgal2o4)的活化温度(即约780℃)高于负载在al2o3上的催化剂(例如:ni/inceo2/al2o3)(约400℃)。在更高的温度(>850℃)下,由于两种催化剂均在800℃以下活化,预期(ni/inceo2/al)和(ni/inceo2/mgal2o4)的性能相同。在实际的双重整条件下,超过1200℃时,在商用催化剂的目测和tpo研究均中均观察到焦化。在本发明的催化剂中没有观察到焦化。当前第1页12