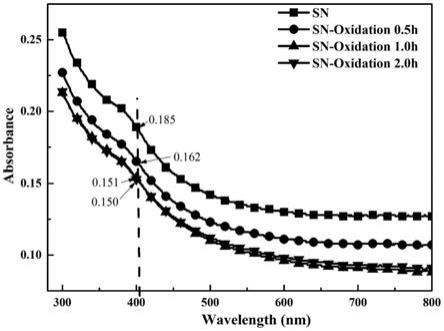
1.本发明涉及氮化硅陶瓷技术领域,尤其涉及一种基于粉体改性的氮化硅陶瓷浆料、氮化硅陶瓷及制备方法。
背景技术:2.氮化硅(si3n4)陶瓷是综合性能最好的结构陶瓷之一,因其优异的硬度、高抗弯强度、良好的化学稳定性和优越的耐高温性能而被广泛应用于军事、航空航天和民用工程等耐高温领域。传统制造方法常用注浆成型或干压成型等方法制备个性化的复杂形状si3n4部件。随着si3n4部件应用领域的不断增加,对高精度复杂形状产品的需求越来越大,如高温换热器、喷嘴等。由于si3n4陶瓷具有高硬度和脆性的特点,传统的制造工艺难以制备出具有复杂结构且精度高的si3n4部件。因此,有必要探索制造复杂形状陶瓷产品的新技术。
3.近十年来,增材制造(am)技术因其无模成形的特点,引起了研究者和工业界的极大关注和兴趣。因此,am技术也被认为是制造复杂形状零件的理想方法。随着am技术的快速发展,涌现出越来越多的制备方法,如:选择性激光烧结(sls)、选择性激光熔化(slm)、三维打印(3dp)、直写自由成型(diw)、数字光处理(dlp)、立体光固化成型(sla)等。slm和sls常用于制备金属材料部件。由于陶瓷的熔点很高,以及基于激光的am技术固有的高热梯度和残余热应力,slm和sls不适用于制备陶瓷材料。3dp和diw是应用最广泛的am技术,可用于所有材料系统,包括金属、陶瓷和聚合物。然而,3dp和diw成型精度太低,限制了它们的应用前景。sla用的是紫外线激光光源进行光固化成型,通过使用激光束在液态树脂表面勾画出物体,由点到线,再由线到面形成实体模型,因些工作效率要远低于dlp。此外,sla可达到的最小光斑尺寸为
±
100微米。由于sla激光器功率高从而容易导致成型光斑误差大,另外微米级精度对于sla的主要部件激光器以及振镜的要求很高,一般国内振晶很难达到要求,要达到微米级成本就会大幅度增加。
4.dlp是一种基于光聚合效应成型的3d打印方法。利用光器件将2d图案投射到浆料池中,然后在几秒钟内固化光敏树脂,完成层层打印和堆积,其特点是片成型,打印速度快。随后,坯体经过脱脂和烧结工艺,得到成型精度好和表面光洁度极高的部件。目前,由于dlp高精度和高表面光滑度的特点,已广泛应用于陶瓷增材制造领域。
5.基于dlp的光聚合固化成型原理,具有低光吸收和低折射率的白色或浅色陶瓷粉末表现出良好的光固化能力。因此,dlp已成功地制备了多种白色或浅色陶瓷材料,例如:氧化锆、氧化铝、氮化铝等。然而,灰色si3n4陶瓷具有高吸光率和高折射率的特点,很难直接利用dlp制备氮化硅陶瓷。
6.目前已有对氮化硅进行改性以降低si3n4粉末的光吸收和折射率的技术。例如表面氧化技术。表面氧化技术可有效实现si3n4表面改性,与其他改性技术相比,表面氧化粉体制备工艺相对简单,仅需要控制氧化的温度和时间,就能完成改性的目的;同时,氧化粉体的效果较为稳定,粉体处理的效果可重复性较高。经过氧化后的si3n4陶瓷颗粒表面能够形成
厚度较为均一的氧化膜(非晶态的二氧化硅)。经过粉体氧化后,si3n4陶瓷的在紫外光区的吸光度和折射率理论上都会有很大程度的降低,能够满足si3n4陶瓷浆料高固化深度的要求。然而利用氧化改性si3n4同时也存在一定的问题,如氧化后粉体容易团聚,需要后续球磨工艺细化陶瓷粉体颗粒;另一方面,氧化后的陶瓷粉体,由于sio2的存在,对某些具有特殊要求的si3n4陶瓷会产生不利影响,如si3n4高温力学性能、热学性能等。
7.然而,目前尚未有兼具高固化能力、高固相含量和低粘度的si3n4陶瓷浆料以便于利用dlp技术获得高质量的氮化硅陶瓷。
技术实现要素:8.本发明所要解决的技术问题是提供一种兼具高固化能力、高固相含量和低粘度的si3n4陶瓷浆料以可以利用dlp技术获得高质量的氮化硅陶瓷。
9.为了解决上述问题,本发明提出以下技术方案:
10.第一方面,本发明提供一种基于粉体改性的氮化硅陶瓷浆料的制备方法,包括以下步骤:
11.s1、将氮化硅粉体于空气氛围中加热,加热温度为500~1500℃,得到氧化的氮化硅粉体;
12.s2、将烧结助剂、树脂、分散剂、光引发剂、硅烷偶联剂以及s1得到的氮化硅粉体混合,得到氮化硅陶瓷浆料。
13.进一步的,所述氮化硅陶瓷浆料的固含量为30
‑
50vol.%。
14.进一步的,步骤s1中,对氮化硅粉体加热后进行保温,保温时间为0.5~2h。
15.进一步的,所述硅烷偶联剂选自kh560、kh540、kh792中的至少一种。
16.进一步的,所述硅烷偶联剂的用量为总粉体的0.5~3wt%。
17.进一步的,所述烧结助剂的用量为总粉体的6~12wt%。
18.进一步的,所述烧结助剂选自氧化铝、氧化钇。
19.进一步的,所述树脂选自bpa10eodma,hdda,pptta,正辛醇中的至少一种。
20.第二方面,本发明提供一种基于粉体改性的氮化硅陶瓷的制备方法,以所述的基于粉体改性的氮化硅陶瓷浆料为原料,采用dlp成型方式打印出坯体;对坯体进行脱脂、烧结,得到氮化硅陶瓷。
21.进一步的,烧结温度为1800
‑
1850℃。
22.第三方面,本发明提供一种基于粉体改性的氮化硅陶瓷,由所述的基于粉体改性的氮化硅陶瓷的制备方法得到。
23.第四方面,本发明提供一种基于粉体改性的氮化硅陶瓷,包括以下原料:氧化的氮化硅粉体、烧结助剂、硅烷偶联剂;
24.其中,所述硅烷偶联剂的用量为氧化的氮化硅粉体与烧结助剂质量总和的0.5~3wt%;
25.所述烧结助剂的用量为氧化的氮化硅粉体与烧结助剂质量总和的6~12wt%。
26.进一步的,所述的基于粉体改性的氮化硅陶瓷的原料中,还包括用树脂、分散剂、光引发剂制备氮化硅陶瓷浆料;再经制坯、脱脂、烧结得到氮化硅陶瓷;
27.所述氮化硅陶瓷浆料的固含量为30
‑
50vol.%;
28.所述分散剂的用量为氧化的氮化硅粉体质量的1~5wt%;
29.所述光引发剂的用量为树脂质量的1~3wt%。
30.虽然氮化硅粉体经过氧化后,si3n4陶瓷在紫外光区的吸光度和折射率理论上都会有很大程度的降低,能够满足si3n4陶瓷浆料高固化深度的要求。然而氧化后粉体容易团聚,粉体与树脂的相容性较差,难以获得高固相含量和低粘度等高质量的si3n4陶瓷浆料。
31.对此,本发明通过向浆料中增加硅烷偶联剂以提高氧化后的氮化硅粉体与树脂的相容性,减少陶瓷浆料的粘度,增加陶瓷浆料的固相含量。
32.与现有技术相比,本发明所能达到的技术效果包括:
33.本发明采用氧化工艺可以有效提高si3n4陶瓷浆料的固化深度和稳定性。此外,硅烷偶联剂的加入能够改善si3n4陶瓷浆料的流变性能和润湿性。
34.本发明的si3n4陶瓷浆料具有光固化能力强、固含量高、粘度低、稳定性可靠的特点,适用于通过dlp打印制备出致密的si3n4陶瓷零件。实验证明,该si3n4陶瓷零件的抗弯强度、硬度、断裂韧性和导热率分别为:577.06
±
78.81mpa,12.65
±
0.71gpa,6.17
±
0.39mpa
·
m1/2和41.38w/(m
·
k)。可见,本发明采用dlp打印样品在性能上接近于冷等静压制作的样品。
附图说明
35.图1为实施案例1中不同氧化时间si3n4陶瓷粉体的吸光度;
36.图2为实施案例2中不同氧化时间的si3n4陶瓷浆料的粘度;
37.图3为实施案例3中不同氧化时间的si3n4陶瓷浆料的单层固化深度和过曝宽度;
38.图4为实施案例4中加入硅烷偶联剂后si3n4陶瓷浆料的粘度;
39.图5为实施案例5中各si3n4陶瓷浆料的单层固化深度和过曝宽度;
40.图6为实施案例6中各si3n4陶瓷浆料的稳定性;
41.图7为实施案例7中采用dlp打印烧结后的样品图;
42.图8为实施案例7中烧结后si3n4陶瓷样品的力学性能;
43.图9为实施案例7中烧结后si3n4陶瓷样品的热导率和热扩散系数;
44.图10为实施案例7中烧结后的si3n4陶瓷样品的sem图;
45.图11为实施案例8中各si3n4陶瓷粉体的sem图。
具体实施方式
46.下面将结合本发明实施例中的附图,对实施例中的技术方案进行清楚、完整地描述。显然,以下将描述的实施例仅仅是本发明一部分实施例,而不是全部的实施例。基于本发明中的实施例,本领域普通技术人员在没有作出创造性劳动前提下所获得的所有其他实施例,都属于本发明保护的范围。
47.本发明实施例提供一种基于粉体改性的氮化硅陶瓷浆料的制备方法,包括以下步骤:
48.s1、将氮化硅粉体于空气氛围中加热,加热温度为500~1500℃,保温时间为0.5~2h,得到氧化的氮化硅粉体;
49.s2、将烧结助剂、树脂、分散剂、光引发剂、硅烷偶联剂以及s1得到的氮化硅粉体混
合,得到氮化硅陶瓷浆料。
50.具体实施中,所述氮化硅陶瓷浆料的固含量为30
‑
50vol.%。
51.具体实施中,在混合时,先使用行星式球磨机以350r/min对氮化硅粉体、烧结助剂进行球磨6h。
52.具体实施例中,步骤s1中,对氮化硅粉体加热后进行保温,加热温度为1200℃保温时间为2h。
53.具体实施例中,所述硅烷偶联剂选自kh560。
54.具体实施例中,所述硅烷偶联剂的用量为总粉体(氮化硅粉体与烧结助剂)的0.5~3wt%。
55.具体实施例中,所述烧结助剂的用量为总粉体(氮化硅粉体与烧结助剂)的6~12wt%。
56.具体实施例中,所述烧结助剂选自氧化铝、氧化钇。
57.具体实施例中,所述树脂选自bpa10eodma,hdda,pptta,正辛醇中的至少一种。
58.具体实施例中,所述分散剂的用量为氧化的氮化硅粉体质量的1~5wt%。
59.具体实施例中,所述光引发剂的用量为树脂质量的1~3wt%。
60.以下具体说明不同工艺参数、原料对氮化硅陶瓷浆料的影响:
61.实施案例1:
62.利用紫外可见近红外分光光度计测试不同氧化时间的si3n4陶瓷粉体的吸光度并与未氧化的si3n4粉体进行比较,其中氧化温度为1200℃,保温时间分别为0.5h、1h、2h。结果见附图1所示:
63.图1结果可知,随着氧化时间的增加,在300
‑
600nm波长区间,si3n4粉体的吸收光谱总体下移,吸光度逐渐降低。在405nm波长,si3n4的吸光度从未氧化的0.185逐渐降低。当氧化时间为1h时,si3n4粉体的吸光度降至最低0.15;继续延长氧化时间,si3n4的吸光度不再减少。因此,经过1200℃,1h的加热氧化处理,si3n4的氧化程度达到最佳值。
64.实施案例2:
65.用未氧化si3n4粉体和氧化的si3n4粉体分别制备固相含量为30vol%的si3n4陶瓷浆料(硅烷偶联剂为kh560、烧结助剂为氧化铝和氧化钇),并测试其粘度。其中氧化温度为1200℃,保温时间分别为0.5h,1h和2h。所制浆料的粘度结果如附图2所示:
66.从图中我们可以发现不同氧化时间的si3n4陶瓷浆料的粘度均呈剪切变稀的现象。在同一剪切速率条件下,且随着si3n4氧化程度的增加,si3n4浆料的粘度先减少后增加,当氧化时间为1h时si3n4浆料的粘度达到最小值。继续增加氧化时间,其陶瓷浆料的粘度增加。
67.实施案例3:
68.分别将氧化0h,0.5h,1h和2h的4种氮化硅粉体制备固含量为15vol%的陶瓷浆料(硅烷偶联剂为kh560、烧结助剂为氧化铝和氧化钇),加入1.5wt%的irgacure tpo,采用的光敏树脂为bpa10eodma。测试四种陶瓷浆料的单层固化深度和过曝宽度。实验结果见附图3所示:
69.图3中,(a)为不同氧化时间的si3n4陶瓷浆料的固化深度;(b)为不同氧化时间的si3n4陶瓷浆料的过曝宽度。由图可得,随着氧化时间的增加,15vol%ssi3n4陶瓷浆料的固化深度逐渐增加,在280mj/cm2的曝光能量下,si3n4陶瓷浆料的固化深度分别为65μm、77μm、
84μm和89μm。随着氧化时间的增加,同等曝光能量下,si3n4陶瓷浆料的额外固化宽度逐渐增加。
70.由表1拟合的光固化参数可知,当si3n4粉体氧化后,si3n4陶瓷浆料的深度敏感系数从10μm左右增加到20μm左右后保持稳定,这可能是由于氧化后的粉体表面包覆一层低折射率层物质,粉体和树脂间的折射率差减小,紫外光的前向散射增加,当氧化层的厚度增加到一定值后,折射率差稳定在一定范围内,折射率差不再对si3n4陶瓷浆料的固化深度产生显著影响,使得深度敏感系数保持稳定。随着氧化时间的增加,si3n4陶瓷浆料的宽度临界曝光量减少,浆料在更低的紫外曝光条件下即可引发过曝现象。然而,si3n4陶瓷浆料的扩展深度随着氧化时间的增加而逐渐增大,由60.72μm增大到73.60μm(增长率最高21.2%)。表明氧化后si3n4陶瓷浆料在发生过曝前具有更高的固化深度,说明氧化处理对增加si3n4陶瓷浆料的固化深度,同时增加固化精度的效果是显著的。
71.表1不同氧化时间si3n4浆料光固化参数
[0072][0073]
实施案例4:
[0074]
本发明加入硅烷偶联剂的主要目的主要是减少si3n4陶瓷颗粒与树脂的相容性,降低si3n4浆料的粘度。以下为验证实验:
[0075]
实验条件:将sn、snkm1、oxsn、oxsn
‑
km1粉体分别和光敏树脂bpa10eodma混合(其中sn代表未氧化的氮化硅粉体、snkm1代表未氧化的氮化硅粉体并加入1wt.%kh560、oxsn代表氧化的氮化硅粉体、oxsn
‑
km1代表氧化的氮化硅粉体并加入1wt.%kh560,氧化粉体的氧化处理是在1200℃下保温1h),制备30vol%的si3n4陶瓷浆料,浆料中所用烧结助剂为氧化铝和氧化钇,浆料中不再添加其他分散剂。实验结果见附图4所示。
[0076]
根据图4结果可知,硅烷偶联剂改性后的si3n4陶瓷浆料的粘度均有较为明显的降低:剪切速率为0.25s
‑1时,未氧化的si3n4陶瓷浆料粘度从2390pa
·
s降低至650pa
·
s,粘度降低了72.8%;而经过氧化后的si3n4陶瓷浆料在改性前后分别为2710pa
·
s和98pa
·
s,粘度降低了96.4%。因此,经过氧化后的si3n4陶瓷浆料与硅烷偶联剂的结合效果更佳,能够制备更低粘度的si3n4陶瓷浆料。这可能是由于氧化后si3n4表面生成的氧化层更容易和硅烷偶联剂中的
‑
x基团脱水缩合,形成si
‑
o
‑
si键,因此更多的si3n4颗粒能够均匀分散于光敏树脂中,降低了si3n4陶瓷浆料的粘度。
[0077]
实施案例5:
[0078]
探究粉体的表面特性对陶瓷浆料的光固化特性影响。
[0079]
实验条件:将sn、snkm1、oxsn、oxsn
‑
km1粉体分别和光敏树脂bpa10eodma均匀混合,制备固相含量为15vol%si3n4陶瓷浆料,其中光引发剂的含量占光敏树脂1.5wt%的
ingrcure tpo,浆料中所用烧结助剂为氧化铝和氧化钇,浆料中不再添加其他分散剂。光固化单层固化深度和过曝宽度实验结果见附图5所示:
[0080]
图5中,(a)为硅烷偶联改性剂对si3n4陶瓷浆料的固化深度的影响,(b)为硅烷偶联改性剂对si3n4陶瓷浆料的过曝宽度的影响。硅烷偶联改性后,sn和oxsn的单层固化深度均略有所下降。在曝光能量为240mw/cm2时,sn和snkm1浆料的单层固化深度分别为54μm和52μm,差别不是十分明显,同时浆料的过曝宽度的差别也很小,该结果和图1中紫外吸收光谱的结果较为符合,说明硅烷偶联改性对原始的si3n4陶瓷浆料的光固化特性影响较小。oxsn和oxsn
‑
km1浆料的固化深度为80μm和73μm,后者较前者的固化深度下降了约8.8%。在过曝宽度上,随着曝光能量的增加,oxsn
‑
km1的过曝宽度维持在100μm左右,而oxsn的过曝宽度迅速增加,远远超过oxsn
‑
km1浆料,这可能是由于氧化后的si3n4改性效果较好,偶联剂中不饱和c=c双键对紫外光具有一定的吸光度,导致浆料的固化深度和过曝宽度一定程度上下降。
[0081]
实施案例6:
[0082]
由于si3n4陶瓷浆料在树脂中的沉降中无法观察到明显的固
‑
液分界面,因此不能利用测量沉降高度来计算陶瓷浆料的沉降率,仅能通过肉眼观察,定性判断陶瓷浆料的沉降情况。为了更快速清晰地展示硅烷偶联改性前后si3n4陶瓷浆料的沉降现象,所采用的的树脂为低粘度hdda作为光敏树脂原料,分别将sn、snkm1、oxsn、oxsn
‑
km1粉体分别和光敏树脂hdda混合,制备30vol%的si3n4陶瓷浆料,浆料中所用烧结助剂为氧化铝和氧化钇,浆料中不再添加其他分散剂。浆料的沉降照片如附图6所示。
[0083]
其中,图(a)为浆料沉降1h后,图(b)为浆料沉降1天后,图(c)为浆料沉降3天后,图(d)为浆料沉降7天后。
[0084]
由图可知,sn和snkm1在1h后即发生沉降现象,1天后发生明显的沉降,在7天后基本完全沉降。而oxsn和oxsn
‑
km1浆料仅在3天后开始发生沉降,而在7天后浆料依然保持较高的稳定性,沉降率仅为sn1陶瓷浆料的1/5。且oxsn和oxsn
‑
km1浆料的沉降速度几乎一致。虽然两者浆料的粘度相差较大,但后者依然保持较高的稳定性,原因在于硅烷偶联改性剂更多的和氧化粉体表面的基团发生反应,增加了氧化si3n4粉体颗粒与树脂间的空间位阻作用,因此,即便粘度大大降低,但是陶瓷颗粒和树脂之间的相容性大大增加。
[0085]
实施案例7:
[0086]
采用上述方法制备固相含量为40vol%的si3n4陶瓷浆料:原料包括氧化的si3n4粉末或者未经氧化的si3n4粉末、烧结助剂氧化铝和氧化钇、硅烷偶联剂kh560。
[0087]
氧化温度为1200℃,氧化时间为1h。
[0088]
原料用的si3n4粉末为α相、纯度大于99.8、中位粒径为0.7μm。
[0089]
所述硅烷偶联剂占总粉体(si3n4粉末和烧结助剂总和)的1wt%。
[0090]
将制得的si3n4陶瓷浆料用dlp光固化成型得到坯体,再对坯体进行脱脂、烧结成瓷。
[0091]
作为对比的例子,用相同陶瓷粉原料采用干压
‑
冷等静压成型(dp
‑
cip)制备坯体。具体地,首先将混合好的一定量的陶瓷粉导入钢膜中,并在液压机上对磨具正反面分别加载6mpa的机械轴向压力,各保压10s。经过干压后的陶瓷坯体再使用冷等静压设备,在200mpa的各向同性压力下保压300s。
[0092]
各陶瓷粉体由不同成型方式制备的坯体编号如表2所示:
[0093]
表2成型坯体
[0094][0095]
对坯体烧结成瓷后测试其性能,结果见附图7,8,9和10所示:
[0096]
图7为光固化成型方式烧结后的实物图。
[0097]
图8为光固化和常规干压
‑
冷等静压成型后si3n4样品在1825℃无压烧结后的力学性能。图中(a)为烧结后样品的维氏硬度,(b)为烧结后样品的断裂韧性,(c)烧结后样品的为抗弯强度。结果表明,在含有未氧化的si3n4粉体的陶瓷样品中,1
‑
1#和1
‑
2#在硬度、断裂韧性和抗弯强度上没有明显的差别,分别为13.81
±
0.37gpa和13.55
±
0.35gpa、5.34
±
0.21mpa
·
m
1/2
和5.41
±
0.19mpa
·
m
1/2
、701.66
±
37.38mpa和716.53
±
71.57mpa。力学性能的结果与致密度的结果符合地很好。说明利用光固化的成型方式能够制备出常规干压
‑
冷等成型方式相当的力学性能的si3n4陶瓷。在含有氧化si3n4粉体的陶瓷样品中,2
‑
1#和2
‑
2#样品在硬度和抗弯强度上要低于未氧化的si3n4粉体的陶瓷样品,分别为12.65
±
0.71gpa和10.91
±
1.86gpa;577.06
±
78.81mpa和624.89
±
49.64mpa。而在断裂韧性上要高于未氧化si3n4粉体的陶瓷样品,分别为6.17
±
0.39mpa
·
m
1/2
和6.36
±
0.36mpa
·
m
1/2
。
[0098]
附图10中,(a)为陶瓷样品1
‑
1#的sem图,(b)为陶瓷样品1
‑
2#的sem图,(c)陶瓷样品为2
‑
1#的sem图,(d)为陶瓷样品2
‑
2#的sem图,(e)为陶瓷样品1
‑
1#的断面图,(f)为陶瓷样品2
‑
1#的断面图。从图中si3n4陶瓷样品的显微结构分析可知,氧化后的si3n4陶瓷样品平均晶粒尺寸和长径比较未氧化的si3n4陶瓷样品的更大,烧结后生成更多的长柱状β
‑
si3n4晶粒。可见,氧化后的si3n4陶瓷样品断裂韧性高于未氧化的si3n4陶瓷样品的主要原因是由于si3n4晶粒的粗化,更多的长柱状晶β相si3n4抑制了裂纹的扩展,起到了自增韧的效果,而相反地,晶粒细化的显微结构则有利于提高抗弯强度。
[0099]
图9是光固化和干压
‑
冷等静压成型后的si3n4陶瓷样品在1825℃的热导率和热扩散系数。结果表明,从成型方式看,光固化成型方式制备的si3n4陶瓷样品,其热导率和热扩散系数基本与常规冷等静压相同,均在50w/(m
·
k)以上。说明利用光固化的成型方式可以制备出高导热的si3n4陶瓷。从粉体材料上看,si3n4粉体氧化后,其热导率从55.91w/(m
·
k)降低至38.33w/(m
·
k),降幅达到31.4%。这主要是由于si3n4粉体的氧化引入了过多的氧导致的。
[0100]
实施案例8:
[0101]
探究硅烷偶联剂对氧化或未氧化的si3n4粉体在微观表面的影响,硅烷偶联剂加入量为1wt.%。
[0102]
如图11所示,其中,(a)为未氧化的si3n4粉体(sn)的sem图,si3n4纯度较高,粉体表层包裹一层非晶态的氧化层,但是厚度并不是十分均匀,厚度仅有5nm左右。(c)为氧化的si3n4粉体(oxsn)的sem图,图中氧化后si3n4粉体的表层和芯部在tem照片中界面较为明显,
且表层氧化层厚度较为均匀,测量得到的氧化层的厚度约为25nm左右,si3n4粉体表面包裹的是非晶态的二氧化硅,其发生氧化的反应方程式见下式(1)。(b)图为未氧化的si3n4粉体加入硅烷偶联剂改性后得到的sem图(snkm1);(d)图为氧化后的si3n4粉体加入硅烷偶联剂改性后得到的sem图(oxsn
‑
km1)。图(b)(d)的表层均有两层薄膜,靠近芯部为氧化层,最外层为硅烷偶联剂的改性层。由图可知,氧化过的si3n4粉体的改性层厚度较未氧化的si3n4的改性层厚约2nm左右。这是由于氧化过的si3n4粉体表面提供了更多的基团,更容易和硅烷偶联剂中的
‑
x基团脱水缩合,为硅烷偶联剂的附着提供更多的条件所导致的。
[0103]
si3n4(s)+o2(g)
→
sio2(s)+n2(g)
ꢀꢀꢀ
(1)
[0104]
综上,用氧化过的si3n4粉体制备得到的si3n4陶瓷浆料,一方面降低了陶瓷浆料的粘度,另一方面大大增加了si3n4陶瓷浆料的固化深度和固化精度,加快了si3n4光固化的成型效率,最佳氧化工艺是在1200℃下氧化1h。
[0105]
加入硅烷偶联对si3n4粉体进行改性,其对氧化过的si3n4粉体的改性效果较未氧化过的si3n4粉体更加明显。具体表现在,硅烷偶联剂的改性更能大幅度降低氧化si3n4陶瓷浆料的粘度,增加了si3n4陶瓷与光敏树脂的相容性;另一方面,硅烷偶联剂的加入对氧化过的si3n4陶瓷浆料的光固化特性的影响较未氧化过的si3n4陶瓷浆料更加明显,因此对光固化深度的抑制效果较未氧化过的si3n4陶瓷浆料更强。
[0106]
在上述实施例中,对各个实施例的描述都各有侧重,某个实施例中没有详细描述的部分,可以参见其他实施例的相关描述。
[0107]
以上所述,为本发明的具体实施方式,但本发明的保护范围并不局限于此,任何熟悉本技术领域的技术人员在本发明揭露的技术范围内,可轻易想到各种等效的修改或替换,这些修改或替换都应涵盖在本发明的保护范围之内。因此,本发明的保护范围应以权利要求的保护范围为准。