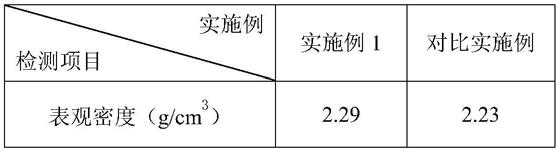
1.本发明涉及陶瓷基复合材料制备领域,特别涉及一种缝合复合材料的制备方法及缝合复合材料。
背景技术:2.陶瓷基复合材料在航空航天及核裂变、核聚变领域具有广泛的应用潜力,连续纤维增韧的陶瓷基复合材料是目前的研究热点,其制备方法主要有:聚合物浸渍裂解工艺(polymer infiltration and pyrolysis,pip)、化学气相渗透工艺(chemical vapor infiltration,cvi)、纳米浸渍与瞬时共晶相工艺(nan o-infiltrated and transient eutectoid,nite)和反应浸渗工艺(reaction i nfiltration,ri)等。
3.pip工艺是用液态陶瓷前驱体浸渍纤维预制件(浸渍),液态陶瓷前驱体交联固化(固化),再经高温裂解(裂解),转化为陶瓷基体,随后重复浸渍-固化-裂解过程而最终制得陶瓷基复合材料。
4.现有的陶瓷基复合材料层间性能较差,层间剪切强度较低。
技术实现要素:5.基于上述问题,本发明提供一种缝合复合材料的制备方法,该方法制备的缝合复合材料的层间剪切强度提高了60%。
6.一种缝合复合材料的制备方法,包括以下步骤:
7.1)缝合预制体:
8.①
将二维平纹碳化硅纤维布裁剪为方形;
9.②
将裁剪好的碳化硅纤维布表面喷涂一层不干胶,叠层平铺成铺层;
10.③
将铺层夹持,以缝合密度:针距
×
行距=5mm
×
4mm缝合,缝合线为碳化硅纤维缝合线,相邻两行的针头与针尾之间的连线与水平方向的缝合线之间形成的角度基本为直角;
11.④
采用模具进行定型得到碳化硅纤维缝合预制体;
12.2)将1)制成的预制体进行化学气相沉积制备热解碳界面层;
13.3)将2)制成的预制体进行化学气相沉积制备碳化硅界面层;
14.4)将3)制成的预制件浸渍;
15.5)将4)浸渍后的预制件沥干进行高压固化;
16.6)将5)固化后的预制件高温裂解;
17.7)反复进行4)~6)步,直至预制体的重量变化小于设定值或目标值,完成复合材料的制备。
18.在本技术的一个或多个具体地实施方式中,所述2)中,沉积温度:700~1100℃,保温时间:3~6h,炉内压力:0.8~2kpa,先驱体为:丙烷,界面厚度为:60~800nm。
19.在本技术的一个或多个具体地实施方式中,所述3)中,沉积温度900~1200℃,保
温时间10~20h,压力1~2kpa,先驱体为:甲基三氯硅烷,厚度为60~800nm。
20.在本技术的一个或多个具体地实施方式中,所述4)中,浸渍的浸渍液为聚碳硅烷先驱体溶液。
21.在本技术的一个或多个具体地实施方式中,所述4)中,真空度-0.07mpa,时间2~4h,压力2~6mpa,时间2~4h。
22.在本技术的一个或多个具体地实施方式中,所述5)中,固化温度200~400℃,固化压力3~5mpa,固化时间2~8h。
23.在本技术的一个或多个具体地实施方式中,所述6)中,高温裂解为在氮气气氛中以5~10℃/min的升温速率升至1000~1200℃,保温60~120min,自然降温至室温。
24.在本技术的一个或多个具体地实施方式中,所述设定值或目标值为1%。
25.本发明还提供一种缝合复合材料。
26.一种缝合复合材料,该缝合复合材料由上述的缝合复合材料的制备方法制备而成。
27.本发明还提供一种航空材料。
28.一种航空材料,其特征在于,该航空材料含有上述的缝合复合材料。
29.本发明的原理及有益效果在于:
30.本技术采用缝合线使多层二维织物结合成准三维立体织物或使分离的数片织物连接成整体结构形成缝合预制体。与预制体相比,缝合预制体主要具备以下特点:
①
可设计性强,缝合预制体的铺层方向,铺层距离和纤维结构等均可以进行优化组合,同时缝合方式和缝合区域也可以按需调整;
②
缝合对原纤维分布影响较小,而且通过缝合参数的合理设定可以获得一定程度的整体结构,并达到合理的均匀应力状态;
③
缝线可以承受大部分载荷,而且减少了周围树脂的应力集中,可以显著提高复合材料层间性能;
④
可高度自动化,目前已开发出用于提高缝合一致性和缝合效率的高度自动化缝合设备;
⑤
装配工艺优异,缝合作为一种连接技术,与复合材料其他连接技术(粘接、铆接等)相比,缝合复合材料整体性强,不易产生局部应力集中。
31.本技术制成的缝合复合材料,有效改善复合材料层间性能,缝合复合材料层间剪切强度最高可提高61.31%。缝线厚度方向的增强作用降低了缝合复合材料在剪切载荷下层间滑移,使复合材料具有更高的整体性。与只铺层不缝合预制体比较缝合预制体纤维体积含量高,大大的降低了复合材料的孔隙率。
附图说明
32.图1为本技术碳化硅纤维缝合预制体主视图。
33.图2为本技术碳化硅纤维缝合预制体俯视图;
具体实施方式
34.下面将结合附图对本发明作进一步说明。
35.一种缝合复合材料的制备方法,包括以下步骤:
36.1)缝合预制体:
37.①
将二维平纹碳化硅纤维布裁剪为200mm*150mm的长方形;
38.②
将裁剪好的碳化硅纤维布表面喷涂一层不干胶,叠层平铺成铺层,平铺厚度为3mm;
39.③
将铺层平纹布使用缝合工装夹具夹持后,缝合密度:针距
×
行距=5mm
×
4mm,将锥管刺入布内,并使用缝针将碳化硅纤维缝合线带入锥管,在缝针插入锥管的同时将锥管推出,缝合后得到缝合预制体;相邻两行的针头与针尾之间的连线与水平方向的缝合线之间形成的角度基本为直角。
40.④
采用石墨模具进行定型得到碳化硅纤维缝合预制体。
41.现有技术中,纤维成预制体主要是靠编织技术,编织技术由于专业性较强,且复杂构件成型技术难度大,效率低下,不适合工业化生产复合材料。本技术
③
的该种缝合技术可以后期开发缝纫机实现批产,
③
的缝合技术不像线的缝合,拉不断。而且,因为纤维是很脆的,没有想象的那么容易进行缝合,而本技术通过将锥管刺入布内,并使用缝针将碳化硅纤维缝合线带入锥管,在缝针插入锥管的同时将锥管推出。
42.2)将1)制成的预制体放入化学气相沉积炉中制备热解碳界面层,沉积温度:700~1100℃,保温时间:3~6h,炉内压力:0.8~2kpa,先驱体为:丙烷,界面厚度为:60~800nm;
43.3)将2)制成的预制体放入化学气相沉积炉中制备碳化硅界面层,沉积温度:900~1200℃,保温时间:10~20h,炉内压力:1~2kpa,先驱体为:甲基三氯硅烷,厚度为:60~800nm;
44.4)将3)制成的预制件放入真空高压浸渍罐中,注入聚碳硅烷先驱体溶液液淹没预制件,抽真空-0.07mpa,保真空2~4h,加压至2~6mpa,保压2~4h;
45.5)将4)浸渍后的预制件取出沥干模具表面浸渍液,装入高压固化炉进行固化,固化温度:200~400℃,固化压力:3~5mpa,固化时间:2~8h;
46.6)将5)固化后的预制件装入高温裂解炉裂解中裂解,在氮气气氛中以5~10℃/min的升温速率升至1000~1200℃,保温60~120min,自然降温至室温;
47.7)反复进行4)~6)步,直至预制体的重量变化小于1%,完成复合材料的制备。
48.实施例1:
49.1)缝合预制体:
50.①
将二维平纹碳化硅纤维布裁剪为200mm*150mm的长方形;
51.②
将裁剪好的碳化硅纤维布表面喷涂一层不干胶,叠层平铺成铺层,平铺厚度为3mm;
52.③
将铺层平纹布使用缝合工装夹具夹持后,缝合密度:针距
×
行距=5mm
×
4mm,将锥管刺入布内,并使用缝针将碳化硅纤维缝合线带入锥管,在缝针插入锥管的同时将锥管推出,缝合后得到缝合预制体;
53.④
采用石墨模具进行定型得到碳化硅纤维缝合预制体。
54.碳化硅纤维缝合预制体主视图如图1,俯视图如图2,其中,1为预制体,2为缝合线,图1和2中,相邻两行的针头与针尾之间的连线与水平方向的缝合线之间形成的角度基本为直角。
55.2)将1)制成的预制体放入化学气相沉积炉中制备热解碳界面层,先驱体为:丙烷,沉积温度:1000℃,保温时间:6h,炉内压力:1kpa,界面厚度为:200nm;
56.3)将2)制成的预制体放入化学气相沉积炉中制备碳化硅界面层,先驱体为:甲基
三氯硅烷,沉积温度:1100℃,保温时间:10h,炉内压力:1kpa,厚度为:200nm;
57.4)将3)制成的预制件放入真空高压浸渍罐中,注入聚碳硅烷先驱体溶液液淹没预制件,抽真空-0.07mpa,保真空4h,加压至3mpa,保压2h;
58.5)将4)浸渍后的预制件取出沥干模具表面浸渍液,装入高压固化炉进行固化,固化温度:200℃,固化压力:5mpa,固化时间:3h;
59.6)将5)固化后的预制件装入高温裂解炉裂解中裂解,在氮气气氛中以5℃/min的升温速率升至1200℃,保温120min,自然降温至室温;
60.7)反复进行4)~6)步,直至预制体的重量变化小于1%,完成复合材料的制备。
61.对比实施例:
62.1)预制体:
63.①
将二维平纹碳化硅纤维布裁剪为200mm*150mm的长方形;
64.②
将裁剪好的碳化硅纤维布表面喷涂一层不干胶,叠层平铺成铺层,平铺厚度为3mm;
65.③
采用石墨模具进行定型得到碳化硅纤维布铺层预制体。
66.2)将1)制成的预制体放入化学气相沉积炉中制备热解碳界面层,先驱体为:丙烷,沉积温度:1000℃,保温时间:6h,炉内压力:1kpa,界面厚度为:200nm;
67.3)将2)制成的预制体放入化学气相沉积炉中制备碳化硅界面层,先驱体为:甲基三氯硅烷,沉积温度:1100℃,保温时间:10h,炉内压力:1kpa,厚度为:200nm;
68.4)将3)制成的预制件放入真空高压浸渍罐中,注入聚碳硅烷先驱体溶液液淹没预制件,抽真空-0.07mpa,保真空4h,加压至3mpa,保压2h;
69.5)将4)浸渍后的预制件取出沥干模具表面浸渍液,装入高压固化炉进行固化,固化温度:200℃,固化压力:5mpa,固化时间:3h;
70.6)将5)固化后的预制件装入高温裂解炉裂解中裂解,在氮气气氛中以5℃/min的升温速率升至1200℃,保温120min,自然降温至室温;
71.7)反复进行4)~6)步,直至预制体的重量变化小于1%,完成复合材料的制备。
72.检测实施例:
73.分别取实施例1-3、对比实施例制成的复合材料进行对比检测,结果见下表1。
74.表1
75.[0076][0077]
从表1得知,本技术通过
③
的缝合技术技术,制备成复合材料的性能达到:表观密度2.29g/cm3、体积密度2.25g/cm3、显气孔率2.07%、rt拉伸强度193.23mpa、rt面内剪切强度89.49mpa、rt层间剪切强度29.55mpa、rt弯曲强度366.10mpa。
[0078]
以上所述仅为本发明的优选实施例而已,并不用于限制本发明,对于本领域的技术人员来说,本发明可以有各种更改和变化。凡在本发明的精神和原则之内,所作的任何修改、等同替换、改进等,均应包含在本发明的保护范围之内。