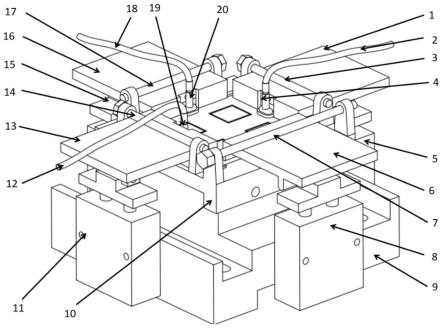
1.本发明涉及玻璃连接工艺,具体而言,涉及一种基于玻璃料的玻璃连接方法及装置。
背景技术:2.玻璃连接工艺广泛应用于光电器件封装、真空玻璃连接等方面。玻璃料通常是由玻璃粉、溶剂、粘接剂、填料构成。
3.在玻璃与玻璃这类透明材料焊接上的应用主要有两个方向:一个是使用超短脉冲激光对两块玻璃直接焊接;另外一个研究方向是在下玻璃板上镀上一层对激光波长不透明的材料,或在中间添加一层对激光波长不透明的玻璃料,以此来增加两块玻璃在界面的对激光能量的吸收,然后通过热传导的方式将吸收的能量传递到上、下两层玻璃,从而实现玻璃与玻璃的焊接。目前对于采用具有低软化温度的玻璃料作为中间层的玻璃与玻璃激光焊接方面的研究还较少,基于玻璃料的玻璃连接过程通常分为以下几步,(a)玻璃料在基板上涂敷(通常采用丝印方式)获得玻璃料涂层,(b)热处理(烧结)涂覆玻璃料的基板,需在加热炉中加热升温至少依次经过以下三个加热温度阶段:去除玻璃料涂层中有机溶剂、去除粘接剂、预烧结得到烧结层,(c)盖上盖板,连接基板和盖板。当夹层中的涂层被加热到连接温度后,实现连接过程。
4.基于玻璃料的玻璃连接技术通常是通过激光辐射使玻璃基板和玻璃盖板间的玻璃料进行局部熔化,以实现连接过程。在使用玻璃料为中间层的激光连接过程前,不可避免的要进行烧结。烧结最常使用的方法为将涂敷涂层的玻璃基板整体放入加热炉中,按与玻璃料所对应的加热曲线进行加热。rui et al.[1](rui t,et al.the effect of glass frit paste levelling property on encapsulation.international conference on electronic packaging technol 2018.)研究了加热第三阶段不同温度对烧结后涂层表面形貌的影响,表面越平整,连接效果越好。liu et al.[2](liu y,et al.glass frit bonding with controlled width and height using a two-step wet silicon etching procedure.j.micromech.microeng.2016;26:035018)严格控制加热温度曲线将气孔控制在最小,改进烧结工艺,将原来的60min的空气中450℃保温改为先在空气中保温30min,后在同温度的真空条件下保温30min,最后升温至500℃保温60min,以降低玻璃涂层中裂纹的生成。在烧结后,采用激光连接法连接玻璃基板和盖板。但是这些都需要采用加热炉对玻璃基板及涂层进行加热至完成预烧结,且加热时长普遍在2h以上。要降低连接过程中的气孔及裂纹则需要更复杂的加热方式,消耗更长的时间。而且,在玻璃料中或多或少的存在大颗粒玻璃料、杂质及残留气体等,无法在传统烧结方式中得到充分去除,如图16(a)所示,将诱发少量杂质型气孔。同时传统烧结方式得到的玻璃料涂层,在焊接过程中需要严格控制激光能量的输入,否则极易出现如图16(b)所示的密集型气孔,导致了焊接窗口狭窄。在焊接过程前,玻璃料涂层可能存在被污染的情况,焊后将出现如图16(c)所示,大量气孔出现,甚至能贯穿整个焊缝,严重影响焊接质量;其中,图16(a)玻璃料中存在少量杂质诱发气孔,图
16(b)激光能量输入过大诱发密集型气孔,图16(c)玻璃料被污染诱发大量气孔。
技术实现要素:[0005]
本文提出一种基于玻璃料的玻璃连接方法及装置,利用激光对丝印的玻璃料涂层进行烧结,能够有效降低制备工艺时间,且制得玻璃涂层连接效果更好,同样能够实现有效减少气孔、提高焊接工艺窗口进而焊接质量的效果。在此基础上使用装置,同一工位上完成激光烧结及激光连接的两个步骤,进一步的提高了生产效率。
[0006]
本发明的目的通过下述技术方案实现一种基于玻璃料的玻璃连接方法,利用玻璃料连接玻璃基板和盖板,其特征在于,按照以下步骤制备:
[0007]
步骤1、在玻璃基板上涂敷玻璃料,获得玻璃料涂层;
[0008]
步骤2、在加热炉中加热所述涂覆玻璃料涂层的玻璃基板,去除玻璃料涂层中有机杂质,获得加热后的玻璃基板试件;步骤3、将步骤2中所述试件覆盖玻璃盖板后,安装于工作台上放置的专用装置中,抬起玻璃盖板,激光烧结所述步骤2中所述玻璃料涂层;步骤4、下压玻璃盖板在所述步骤3中激光烧结的具有玻璃料涂层的玻璃基板试件上,连接玻璃基板和玻璃盖板。
[0009]
进一步地,所述玻璃料涂层的厚度小于5μm,则所述步骤2中,加热炉加热依次包括去除玻璃料涂层中有机溶剂、去除玻璃料中粘结剂两个保温阶段。
[0010]
进一步地,所述玻璃料涂层的厚度大于等于5μm,则所述步骤2,加热炉加热依次包括去除玻璃料涂层中有机溶剂、去除玻璃料中粘结剂、预烧结获得烧结层三个保温阶段。
[0011]
进一步地,所述去除玻璃料中有机溶剂保温阶段工艺参数为:在空气中将涂敷玻璃料涂层的玻璃基板加热至150℃,保温30min,温度上升速度为5℃/min。
[0012]
进一步地,述去除玻璃料中粘结剂阶段工艺参数为:在去除玻璃料中有机溶剂保温阶段后,继续加热涂敷玻璃料涂层的玻璃基板至300℃,保温30min,温度上升速度为5℃/min。
[0013]
进一步地,所述预烧结获得烧结层阶段工艺参数为:在去除玻璃料中粘结剂阶段后,继续加热至480℃保温30min。
[0014]
进一步地,所述步骤4中,采用焊接的方式连接玻璃基板和玻璃盖板或采用热压法连接玻璃基板和玻璃盖板。
[0015]
本发明还提供了一种基于玻璃料的玻璃连接方法的在同一工位上进行激光烧结及激光焊接的装置,包括底座、支撑块及固定在底座四面的四套气压控制组件;使用螺钉连接的方式将支撑块固定在底座顶部;第一气缸、第二气缸、第三气缸、第四气缸通过螺纹连接分别固定在底座的四面;第一销、第二销、第三销、第四销分别通过支撑块预留的孔洞,固定在支撑块顶部的四面。
[0016]
进一步地,第一压板穿过第一销与支撑块间的间隙,第一压板前端与玻璃盖板线接触,第一气缸的顶部与第一压板的后端凸出部线接触;第一气缸升长时,前端通过线接触挤压第一压板,第一压板顶在第一销上,实现第一压板前端对玻璃盖板的压力施加;第一气缸收缩时,第一压板卸力,第一压板可抽离装置,抽离后,可在此位置进行上下料操作;第一气缸、第一压板、第一销构成第一套气压控制组件。
[0017]
进一步地,第三压板放置在第三销与支撑块之间,前端与玻璃盖板线接触,通过销
与第三气缸铰链连接,第三压板绕销转动;第三气缸上升,第三压板前端与玻璃盖板线接;第三气缸伸长时,通过销,使第三压板后部抬升,第三压板顶住第三销,第三压板完成对玻璃盖板的压力施加;第三气缸收缩时,通过销,使第三压板后部降低,第三压板顶住支撑块的凸出部位,实现第三压板前端的抬升;第三压板对玻璃盖板的压力施加时,第三吸盘通过吸气,可完成对玻璃盖板的吸附,吸附后的玻璃盖板可随第三压板端同时上升、下降;第三气缸、第三压板、第三气管、第三吸盘、第三销构成第三套气压控制组件;另有第二套、第四套气压控制组件作用与第三套气压控制组件作用相同。
[0018]
本发明的有益效果是:
[0019]
第一、本发明利用激光对丝印的玻璃料涂层进行烧结,并且通过对不同厚度的玻璃料涂层的玻璃连接质量的深入研究,针对不同厚度的玻璃涂层,制定不同的加工工艺,实现使用激光对玻璃料涂层进行充分的烧结处理,进一步去除其中含有的大颗粒玻璃料、杂质及残留气体等。可有效降低后续的激光焊接工艺中气孔的形成,同时使激光焊接工艺获得更大的工艺窗口,可容许其中存在较大玻璃料颗粒、杂质等,降低了对玻璃料涂层的质量要求;而且使用激光烧结处理后的玻璃料涂层能将其中隐藏的缺陷完全暴露出来,避免激光焊接过程中导致的整个器件的报废。
[0020]
第二、本发明可以替代低厚度的玻璃料涂层(《5μm)在加热炉中的预烧结阶段。低厚度的玻璃料涂层仅仅需要在加热炉中完成去除有机溶剂、粘接剂两段保温阶段,不在加热炉中进行预烧结。将有机质去除后直接使用激光烧结进行处理,利用激光烧结工艺完成低厚度的玻璃料涂层的完全烧结过程,通过激光作用在玻璃料涂层,改善玻璃料涂层质量后,再施加玻璃盖板进行激光焊接连接。使用该方法进行烧结的玻璃料涂层在激光烧结及后续激光焊接连接过程中不易形成气孔,有效减少气孔,且激光烧结完成后的涂层的连接效果更好,可大幅提高其工艺窗口的范围,并且省去在加热炉中进行烧结处理的时间,大幅提高生产效率。
[0021]
第三、在进行更高厚度的玻璃料涂层(≥5μm)的烧结过程中,由于涂层厚度的提高,若在加热炉中加热烧结时,仅包括去除有机溶剂、粘接剂两段保温阶段,激光作用在玻璃料涂层后,能量无法及时传递到玻璃料涂层的底部,导致烧结后质量较差,难以用于后续对玻璃基板和玻璃盖板激光焊接处理。因此,更高厚度的玻璃料涂层(≥5μm)的加热炉加热过程,通过在加热炉中对涂敷玻璃料的玻璃基板烧结至预烧结阶段,可在加热炉中进行30min的初步烧结至得到烧结层,再取出涂覆玻璃料的玻璃基板并对其进行激光烧结,即使用激光进行二次烧结处理,最后盖上玻璃盖板进行激光焊接连接。使用该方法进行烧结的玻璃料涂层在激光烧结及后续激光焊接连接过程中同样不易形成气孔,能够有效减少气孔的效果,且扩大其工艺窗口。虽仍需在加热炉中进行初步烧结处理,但可大幅缩短加热炉中的烧结时间。
[0022]
第四、本发明制得的玻璃,具有焊缝气孔少、焊接质量好的优点。
[0023]
第五、本发明使用的装置,同一工位上完成激光烧结及激光连接的两个步骤,进一步的提高了生产效率。
附图说明
[0024]
本发明的上述和/或附加方面的优点在结合下面附图对实施例的描述中将变得明
显和容易理解,其中:
[0025]
图1是本发明所述的薄厚两种玻璃料涂层在加热炉中的加热温度曲线图;
[0026]
图2是本发明所述的激光烧结过程中焊缝中心点温度随时间的变化曲线图;
[0027]
图3是本发明所述的玻璃料的差示扫描量热法(dsc)及热重法(tg)图;
[0028]
图4是本发明所述加热炉中低厚度的玻璃料涂层预烧结后玻璃料涂层的表面形貌;
[0029]
图5是本发明所述激光完全烧结低厚度的玻璃料涂层后玻璃料涂层的表面形貌;
[0030]
图6是本发明所述直接激光完全烧结高厚度的玻璃料涂层后玻璃料涂层的表面形貌;
[0031]
图7是本发明所述激光二次完全烧结高厚度的玻璃料涂层后玻璃料涂层的表面形貌;
[0032]
图8是本发明所述激光完全烧结玻璃料涂层过程的同轴观察照片;
[0033]
图9是本发明所述激光完全烧结玻璃料涂层过程的截面示意图;
[0034]
图10是本发明所述激光焊接过程的同轴观察照片;
[0035]
图11是本发明所述激光焊接过程的截面示意图;
[0036]
图12是本发明所述仅使用加热炉进行烧结后的焊缝形貌;
[0037]
图13是本发明所述使用激光烧结后的焊缝形貌;
[0038]
图14是本发明所述加热炉进行烧结后大功率焊接焊缝形貌;
[0039]
图15是本发明所述激光烧结后的大功率焊接焊缝形貌;
[0040]
图16是本发明所述使用传统方式烧结后进行焊接出现的各种气孔缺陷图;
[0041]
图17是本发明所述装置的三维视图;
[0042]
图18是本发明所述装置的剖视图。
[0043]
其中:
[0044]
1-第四压板,2-第四气管,3-第四销,4-第四吸盘,5-第四气缸,6-第一压板;7-第一销,8-第一气缸,9-底座,10-支撑块,11-第二气缸;12-第二气管,13-第二压板,14-第二销,15-第三气缸,16-第三压板,17第三销,18-第三气管19-第二吸盘,20-第三吸盘,21-玻璃盖板-,22-玻璃基板,23-玻璃料涂层,24-销。
具体实施方式
[0045]
为了能够更清楚地理解本发明的上述目的、特征和优点,下面结合附图和具体实施方式对本发明进行进一步的详细描述。需要说明的是,在不冲突的情况下,本发明的实施例及实施例中的特征可以相互结合。
[0046]
在本发明中,术语“涂敷”、“连接”、“烧结”等术语均应做广义理解,对于本领域的普通技术人员而言,可以根据具体情况理解上述术语在本发明中的具体含义。
[0047]
如图1所示,低厚度的玻璃料涂层(《5μm)在加热炉中的温度曲线为方形标记点的曲线。低厚度的玻璃料涂层在加热炉中仅经过去除有机溶剂及去除粘接剂两步,这两步分别保温时长均为30min,其中温度上升速度为5℃/min。等经加热炉处理的低厚度的玻璃料涂层冷却后,使用激光束,对玻璃料涂层进行激光烧结处理。激光烧结过程中,焊缝中心点温度随时间的变化曲线如图2所示。玻璃料可以在1秒的时间内,实现温度迅速升高到700
℃,后温度迅速下降的过程。在金相显微镜下观察到的激光完全预烧结后玻璃料涂层的表面形貌如图5所示,涂层表面光滑,表明在激光烧结过程中玻璃料涂层发生了充分的熔融,其中易分解的成分及可高温去除的杂质均得到了充分的去除。本发明中使用到的玻璃料差示扫描量热法(dsc)及热重法(tg)图(5℃/s)如图3所示,对该图进行分析可得,使用加热炉烧结的最佳温度为340至480℃。经过大量工艺试验,确定使用加热炉进行烧结过程的加热曲线如图1中圆点标记的曲线所示。在金相显微镜下观察到的加热炉中预烧结后玻璃料涂层的表面形貌如图4所示,涂层表面粗糙,表明在激光烧结过程中玻璃料涂层未发生了充分的熔融,其中易分解的成分、部分杂质均及隐藏在其中的气体无法充分去除。但此时,玻璃料在加热炉中的烧结温度不宜提高,否则玻璃料涂层在预烧结过程中容易发生大量析晶,析出晶体将作为杂质存在玻璃料涂层中,影响最终焊接质量。
[0048]
对于高厚度的玻璃料涂层(≥5μm),不在加热炉中加热至预烧结(即不经历图1中圆点标记的曲线,而是经历方形标记点的曲线),直接采用激光进行烧结工艺。得到的焊缝表面形貌如图6所示,焊缝表面因为应力过大,产生了竖纹。较窄的竖纹在焊接过程中会伴随着玻璃料的再次熔融而消失,但较宽的竖纹将会继承在最终的焊缝中。为避免竖纹的产生,需要高厚度的玻璃料涂层在加热炉中经历一个完整的烧结曲线,加热直至预烧结得到烧结层。此时的玻璃料已经部分烧结,再次使用激光进行二次烧结后,如图7所示,玻璃料涂层表面光滑,无竖纹出现。
[0049]
以此方法进行激光烧结的玻璃料涂层能够实现玻璃料的充分烧结,且此方法经过改进后,不仅可以适用于低厚度的玻璃料涂层,也可适用于高厚度的玻璃料涂层。充分烧结后的玻璃料涂层在后续盖上玻璃盖板,进行激光焊接连接过程中,不易形成气孔,同时具备更大的窗口工艺范围。
[0050]
以下将结合附图17、18对本发明使用的装置进行详细说明。
[0051]
如图17所示,该实施例提供了一种在同一工位上进行激光烧结及激光焊接的装置,包括底座9、支撑块10及固定在底座四面的四套气压控制组件;使用螺钉连接的方式将支撑块10固定在底座9顶部。第一气缸8、第二气缸11、第三气缸15、第四气缸5通过螺纹连接分别固定在底座的四面;第一销7、第二销14、第三销17、第四销3分别通过支撑块10预留的孔洞,固定在支撑块10顶部的四面。
[0052]
如剖视图18所示,其中,第一压板6穿过第一销与支撑块10间的间隙,第一压板6前端与玻璃盖板21线接触,第一气缸8的顶部与第一压板6的后端凸出部线接触。第一气缸8升长时,前端通过线接触挤压第一压板6,第一压板6顶在第一销7上,实现第一压板6前端对玻璃盖板21的压力施加。第一气缸8收缩时,第一压板6卸力作用,可抽离装置,此处为玻璃板的上下料处,第一压板6抽离后,可在此位置进行上下料操作。
[0053]
第一气缸8、第一压板6、第一销7构成第一套气压控制组件。
[0054]
第三压板16放置在第三销17与支撑块10之间,前端与玻璃盖板21线接触,通过销24与第三气缸15铰链连接,第三压板16可绕销24转动。
[0055]
第三气缸15上升,第三压板16前端与玻璃盖板21线接触。第三气缸15伸长时,通过销24,使第三压板16后部抬升,第三压板16顶住第三销17,第三压板16完成对玻璃盖板21的压力施加。第三气缸15收缩时,通过销24,使第三压板16后部降低,第三压板16顶住支撑块10的凸出部位,实现第三压板16前端的抬升。
[0056]
第三吸盘20通过吸盘上的圆柱接头插入第三压板16前端中部的孔洞,使第三吸盘20与第三压板16固定在一起。第三吸盘20为橡胶材质,具有一定弹性,受力后会发生压缩,长度变短,不受力时吸盘略突出第三压板16。第三吸管18为橡胶软管,插入第三吸盘20上部的导气位置。当第三压板16压住玻璃盖板21时,第三吸盘20受力收缩与第三压板16前端凸出部平齐,同时与玻璃盖板21充分接触。此时气管18抽气,第三吸盘20中产生负压,可将玻璃盖板21与第三吸盘20吸附在一起,完成吸附后,玻璃盖板21可伴随第三压板前端上下运动。第三气缸15、第三压板16、第三气管18、第三吸盘20、第三销17构成第三套气压控制组件。
[0057]
第二气缸11、第二压板13、第二气管12、第二吸盘19、第二销14之间的连接方式以及第四气缸5、第四压板1、第四气管2、第四吸盘4、第四销3之间的连接方式,与第三套气压控制组件中第三气缸15、第三压板16、第三气管18、第三吸盘20、第三销17之间的连接方式相同,分别构成第二套气压控制组件与第四套气压控制组件。
[0058]
实施例1
[0059]
本例实施中激光烧结方法包括以下几个步骤:
[0060]
步骤1:以蒸馏水与清洁剂的混合液对玻璃基板进行超声波清洗。
[0061]
步骤2:玻璃浆料以丝印的方式涂敷在玻璃基板上。其中,采用的两种网版,膜厚10μm的丝印网版。丝印图案宽度0.8mm。最终涂层厚度为4~5μm,即获得低厚度的玻璃料涂层。
[0062]
步骤3:低厚度的玻璃料涂层在加热炉中加热阶段分为两段,加热炉在空气中将涂敷涂层的玻璃基板直接加热至150℃,保温30min,去除有机溶剂;再加热至300℃,保温30min,去除粘接剂。加热炉升温曲线如图1所示。
[0063]
步骤4:抽出第一压块6,收缩第一气缸8、第二气缸11、第三气缸15、第四气缸5,将玻璃盖板21盖在加热炉处理后的玻璃基板22上,并将试件由原第一压块6所在位置放入支撑块10上的凹槽内,装置安装在激光加工平台上,平台所用的连续激光为半导体激光,波长915nm。激光头的焦距为150mm,焦点处光斑直径为300μm。激光烧结所用的工艺参数设定为:离焦量-15mm,激光扫描速度为0.1m/min,激光功率为28w。将第一压板6放回原位置,伸长第二气缸11、第三气缸15、第四气缸5,使吸盘贴合在玻璃盖板21上,第二气管12、第三气管18、第四气管2抽气,吸盘吸附玻璃盖板21。收缩第二气缸11、第三气缸15、第四气缸5,使第二压板13、第三压板16、第四压板1上抬,被气缸吸附的玻璃盖板21同时上抬,使玻璃盖板21与玻璃基板22上的玻璃料涂层23留有充分的距离,此时激光透过玻璃盖板21对玻璃料涂层进行最终的激光烧结处理。处理后,同时伸长第一气缸8、第二气缸11、第三气缸15、第四气缸5,使第一压板6、第二压板13、第三压板16、第四压板1前端下压,玻璃盖板21与玻璃料涂层23充分接触后,在同一装置上进行激光焊接处理。焊接完成后,第二气管12、第三气管18、第四气管2吹气,收缩第一气缸8、第二气缸11、第三气缸15、第四气缸5,第二压板-413、第三压板16、第四压板1上抬,第一压板6卸力,抽出第一压板6,取出焊后成品。
[0064]
实施例2
[0065]
本例实施中激光烧结方法包括以下几个步骤:
[0066]
步骤1:以蒸馏水与清洁剂的混合液对玻璃基板进行超声波清洗。
[0067]
步骤2:玻璃浆料以丝印的方式涂敷在玻璃基板上。其中,采用的两种网版,膜厚25μm的丝印网版。丝印图案宽度0.8mm。最终涂层厚度为8~10μm,即获得高厚度的玻璃料涂
层。
[0068]
步骤3:高厚度的玻璃料涂层在加热炉中加热阶段分为三段:有机溶剂去除、粘接剂去除和预烧结。加热曲线如图1所示,去除有机溶剂及粘接剂后,加热至480℃保温30min,进行烧结处理。
[0069]
步骤4:抽出第一压板6,收缩第一气缸8、第二气缸11、第三气缸15、第四气缸5,将玻璃盖板21经过盖在加热炉处理后的试件玻璃基板22上,并将试件由原第一压板6所在位置放入支撑块10上的凹槽内,装置安装在激光加工平台上,平台所用的连续激光为半导体激光,波长915nm。激光头的焦距为150mm,焦点处光斑直径为300μm。激光烧结所用的工艺参数设定为:离焦量-15mm,激光扫描速度为0.1m/min,激光功率为23w。将第一压板6放回原位置,伸长第二气缸11、第三气缸15、第四气缸5,使吸盘贴合在玻璃盖板21上,第二气管12、第三气管18、第四气管2抽气,吸盘吸附玻璃盖板21。收缩第二气缸11、第三气缸15、第四气缸5,使第二压板13、第三压板16、第四压板1前端上抬,被气缸吸附的玻璃盖板21同时上抬,使玻璃盖板21与玻璃基板22上的玻璃料涂层23留有充分的距离,利用适当的工艺参数,此时激光透过玻璃盖板21对玻璃料涂层进行最终的激光烧结处理。激光烧结处理后,同时伸长第一气缸8、第二气缸11、第三气缸15、第四气缸5,第一压板6、第二压板13、第三压板16、第四压板1下压,使玻璃盖板21与玻璃料涂层23充分接触后,在同一激光加工平台装置上进行激光焊接处理。焊接完成后,第二气管12、第三气管18、第四气管2吹气,不再吸附玻璃盖板21,收缩第一气缸8、第二气缸11、第三气缸15、第四气缸5,第二压板13、第三压板16、第四压板1前端上抬,第一压板6卸力,抽出第一压板6,取出焊后成品。
[0070]
在上述实施例中,由于玻璃料本身并非均质材料,故丝印涂敷后的玻璃料涂层有可能出现某处杂质或玻璃料颗粒较大的情况,这种情况将导激光致烧结过程中形成较大的气泡。较大的气泡溢出后,会在玻璃料涂层表面形成小的凹坑,如同轴观测的图8中的白色小点。其中:图8(a)t=10.07s,图8(b)t=10.10s,图8(c)t=10.20s;而更大一些的气孔将会在玻璃料涂层表面形成一个环形的凸台,如同轴观测的图(8c)中圈中白点所示。整气泡的溢出过程的截面示意图,如图9所示,其中,图9(a)析出气孔,图9(b)形成凹坑,图9(c)形成环状凸台。
[0071]
激光烧结后会形成凹坑或环状凸台,看似会阻碍连接过程。图10为激光烧结后试件的连接过程,其中,图10(a)t=11.01s,图10(b)t=11.09s,图10(c)t=11.13s;图(10a)中的玻璃料涂层白点为小凹坑,圈中的为环形凸台,深黑色区域为熔融玻璃料与上玻璃基板的连接部分。如示意图10(a)所示,玻璃上基板向下弯曲变形。图10(b)所示,小凹坑直接被熔融玻璃料覆盖,环形凸台在熔融玻璃料前沿到达前,便出现熔融。如示意图11(b)所示,环形凸台形成色中心,具有较周边玻璃料更强的激光吸收率,受激光束边沿作用熔融并润湿玻璃上基板,同时出现了间隙。图10(c)所示,熔融的环形凸台被熔融前沿覆盖。即示意图11(c)所示,间隙部分被熔融玻璃料完全填充,其中:图11(a)析出气孔,图11(b)微小气孔去除凸台重熔,图11(c)间隙填充;因此,使用激光烧结工艺后,玻璃料涂层中较大的杂质或玻璃料颗粒并不会影响最终的激光玻璃焊接成型。
[0072]
如图12所示,采用传统加工工艺,仅在加热炉中完成烧结工艺的玻璃料涂层,进过激光焊接后,焊缝中部出现较多细小气孔。如图13所示,在使用激光烧结工艺处理后的玻璃料涂层,经过激光焊接连接玻璃基板和盖板后,气孔几乎不可见,焊缝成型良好。提高激光
焊接功率2w后,仅在加热炉中完成烧结工艺的玻璃料涂层经焊接后焊缝表面如图14所示,焊缝宽度相较图12中,焊缝宽度大幅扩展,与之相伴的是气孔增大且数量增多。而使用激光烧结的玻璃料涂层在提高激光焊接功率2w后的焊缝表面如图15所示,焊缝宽度同样更宽,仅少量的微细气孔出现焊缝两端。可见,使用激光烧结方法处理的玻璃料涂层,在后续的激光焊接过程中能够适应更大的工艺窗口范围。
[0073]
虽然上面结合本发明的优选实施例对本发明的原理进行了详细的描述,本领域技术人员应该理解,上述实施例仅仅是对本发明的示意性实现方式的解释,并非对本发明包含范围的限定。实施例中的细节并不构成对本发明范围的限制,在不背离本发明的精神和范围的情况下,任何基于本发明技术方案的等效变换、简单替换等显而易见的改变,均落在本发明保护范围之内。