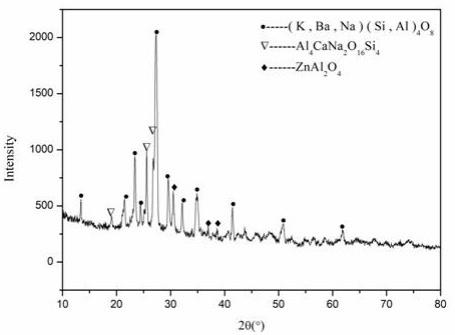
1.本发明属于陶瓷技术领域,具体地,涉及一种耐磨防污保护釉、亚光瓷砖及其制备方法瓷砖。
背景技术:2.建筑瓷砖为室内装修的主要材料,但随着消费者的审美发生的变化,不同时间段,消费者对瓷砖产品的喜好也在不断变化。目前市场上,低光泽度再结合石纹、布纹、木纹及砂岩类等素材,所生产的亚光类仿古瓷砖产品,深受消费者的喜爱。
3.近几年亚光类瓷砖产品成为了各大陶企争相开发的一个主推产品,但亚光砖目前普遍存在着一些难以克服的问题,从亚光机理以及实际生产要求上来分析,亚光砖的釉面往往不能同时兼顾手感细腻、防污性能好、耐磨度高、硬度高等这几种特性。比如:釉面手感细腻,但耐磨度不高;釉面耐磨度合格,但手感不够细腻;釉面硬度够高且耐磨度高,但釉面防污性能不佳。由于当前的亚光瓷砖产品存在着上述一系列问题,使得亚光瓷砖的应用受到了大大的限制。
技术实现要素:4.本发明的目的在于提供一种耐磨防污保护釉及应用其的亚光瓷砖,以使亚光瓷砖的釉面同时具备高耐磨、高防污、手感细腻的特性。
5.根据本发明的一个方面,提供一种耐磨防污保护釉,按照质量份数计算,耐磨防污保护釉的原料包括:保护釉矿物组分18~30份、第一氧化物熔块4~6份、第二氧化物熔块51~63份;第一氧化物熔块为高硼熔块,高硼熔块中的硼元素含量不低于8 wt%;第二氧化物熔块包括钡锌锶熔块和高钙熔块,其中,按照质量百分比计算:钡锌锶熔块的化学组成包括:al2o
3 11.22~14.38 wt%、sio
2 28.5~32.6 wt%、na2o 1.85~2.35 wt%、k2o 2.3~3.2 wt%、bao 25.6~29.4wt%、zno 15.6~18.9 wt%、sro 10.2~13.5 wt%;高钙熔块的化学组成包括:al2o
3 18.5~23.5 wt%、sio
2 36.5~41.6 wt%、cao 25.6~30.8 wt%、mgo 4.8~6.4 wt%、k2o 3.4~4.5 wt%、na2o 2.4~3.4 wt%。
6.本发明提供的耐磨防污保护釉中含有高硼熔块,高硼熔块的应用在于向釉料配方中引入b2o3,由此,通过在砖坯表面布施本发明提供的耐磨防污保护釉,在煅烧砖坯时,耐磨防污保护釉中的b2o3转化为[bo4]网络结构,从而显著地提高由此形成的保护釉的釉面硬度。另一方面,第二氧化物熔块所包括的钡锌锶熔块和/或高钙熔块在于向耐磨防污保护釉中引入大量的二价氧化物(如bao、zno、sro、cao、mgo)以及一价氧化物(例如:k2o、na2o等碱金属氧化物),由此可以使配方中的一价氧化物和二价氧化物复配组成复合熔剂,在煅烧砖坯时,上述复合熔剂能够提高釉料的始熔温度,从而减少釉面针孔缺陷,提高釉面防污能力。
[0007]
优选地,第二氧化物熔块包括钡锌锶熔块和高钙熔块,按照质量份数计算,耐磨防污保护釉包括钡锌锶熔块25~35份、高钙熔块20~32份。
[0008]
优选地,保护釉矿物组分包括球粘土、高岭土、刚玉中的至少一种。
[0009]
优选地,保护釉矿物组分由球粘土、高岭土和刚玉组成,按照质量份数计算,耐磨防污保护釉包括球粘土6~12份、高岭土8~12份、刚玉4~6份。
[0010]
矿物组分中的高岭土和刚玉均含有丰富的al2o3,以高岭土和刚玉作为釉层的骨架,从而使由此所形成的釉层具有足够的硬度,从而具有良好的耐磨性。另一方面,使第二氧化物熔块与矿物组分以特定的组成与比例相搭配,从而能够使al2o3含量高的釉料具有较低的熔融温度,由此,拓宽釉层的烧成范围,使烧成后的釉层具有细腻的手感。此外,采用含有cao、bao、zno、sro等碱土金属氧化物和k2o、na2o等碱金属氧化物的熔块材料搭配石英、长石、高岭土,在烧成后形成的长石类晶体和锌铝尖晶石晶体,其柱状的结构不仅增加了釉面的硬度及耐磨度,另外各种晶体形成的漫反射,降低了光线的反射率,形成了具有亚光光泽的釉面。
[0011]
根据本发明的另一个方面,提供一种亚光瓷砖,包括砖体,砖体的表面覆盖有保护釉层,保护釉层为由如上所述耐磨防污保护釉经过煅烧成型所得。
[0012]
优选地,砖体的表面还覆盖有面釉层,在砖体的表面上,面釉层、保护釉层依次设置;按照质量份数计算,用于形成面釉层的面釉的配方包括面釉矿物组分50~90份、纳米硅酸锆8~12份、高硼熔块20~25份。
[0013]
上述面釉中的纳米硅酸锆具有较大的比表面积,在砖坯烧成的过程中,砖坯表面的纳米硅酸锆形成了大量的锆英石晶体,从而大大提升了釉料的耐磨度。另外,面釉配方中的高硼熔块向面釉中引入了b2o3,替代部分sio2,在烧成过程中,面釉中的b2o3、sio2分别转化为[bo4]硼氧四面体结构、[sio4]硅氧四面体结构,而具有相同几何构型的[bo4]和[sio4]能够共同形成网络结构,由此大大地增强了面釉的硬度,从而,在上述规定的b2o3用量范围内,随着面釉中的b2o3含量增加,经过烧成后所形成的面釉硬度增大。然而,面釉中的b2o3含量不宜过高,若b2o3在配制面釉中的用量超过了上述规定范围(b2o3在面釉中的含量大于15%),在高温烧成的过程中,面釉中的b2o3不仅会转化为[bo4],还会转化为[bo3],[bo3]并非呈四面体结构,从而无法与呈四面体结构的[sio4]共同形成网络结构,由此,[bo3]的产生不但无法增强面釉的强度,反而引起釉层结构松散、降低釉面的硬度,导致所形成的面釉层耐磨度降低。
[0014]
优选地,面釉矿物组分包括高岭土、球粘土、刚玉、石英、钾长石、钠长石中的至少一种。
[0015]
优选地,面釉矿物组分由高岭土、球粘土、刚玉、石英、钾长石、钠长石组成,按照质量份数计算,面釉包括高岭土15~25份、球粘土6~12份、刚玉3~5份、石英8~12份、钾长石15~25份、钠长石5~10份。
[0016]
优选地,纳米硅酸锆的粒径为40~100 nm;按照质量百分比计算,高硼熔块的化学组成包括:al2o
3 10.28~14.53wt%、sio
2 32.74~40.85wt%、cao 1.85~2.25wt%、k2o 2.57~3.68wt%、na2o 10.50~16.21wt%、b2o
3 26.40~32.48wt%。
[0017]
通过对组成釉料的物质及配比进行限定,控制面釉中铝离子的摩尔数小于碱金属离子和碱土金属离子摩尔数的总和,促使大部分铝离子在烧成得到的面釉层中以铝氧四面体存在于玻璃相中,与硼氧四面体、硅氧四面体形成统一的网络,从而进一步提高面釉强度以提高瓷砖的耐磨性能。
[0018]
根据本发明的另一个方面,提供一种制备上述瓷砖的制备方法,包括以下步骤:依次在砖坯的表面布施面釉、耐磨防污保护釉,然后使砖坯在1170~1190℃下煅烧40~60分钟,烧成后制得瓷砖。
[0019]
优选地,上述制备方法具体包括以下步骤:s1.对砖坯进行干燥处理;s2.在砖坯的表面布施面釉,施釉量为220~250 g/m2,使砖坯表面覆盖的面釉的厚度为0.05~0.08 mm;s3.在砖坯的表面布施耐磨防污保护釉,施釉量为110~130 g/m2,使砖坯表面覆盖的面釉的厚度为0.02~0.04 mm;s4.使砖坯在1180℃下煅烧40~60分钟,烧成后制得瓷砖。
[0020]
优选地,在s1中,使砖坯在150~220 ℃下干燥,至砖坯的水份含量达到0.3%~0.8%。经过上述干燥操作,可以增强生坯的强度,为后续的加工工艺提供具有足够强度的砖坯主体。
[0021]
优选地,在进行面釉布施操作之前,对面釉所包括的原料进行如下的处理:将面釉所包括的物料充分混合得到面釉,然后向其中添加甲基纤维素钠(添加量为面釉总质量的0.15%~0.2%)、三聚磷酸钠(添加量为面釉总质量的0.3%~0.45%)、水(添加量为面釉总质量的38%~45%),对混合得到的浆料进行球磨处理,至浆料的细度达到325目筛余为0.4%~0.8%、流速为50~70 s/100ml。利用经过上述处理得到的浆料进行s2的面釉布施操作。
[0022]
优选地,在进行耐磨防污保护釉布施操作之前,对耐磨防污保护釉所包括的原料进行如下的处理:将耐磨防污保护釉所包括的物料充分混合得到耐磨防污保护釉,然后向其中添加甲基纤维素钠(添加量为耐磨防污保护釉总质量的0.15%~0.2%)、三聚磷酸钠(添加量为耐磨防污保护釉总质量的0.3%~0.45%)、水(添加量为耐磨防污保护釉总质量的38%~45%),对混合得到的浆料进行球磨处理,至浆料的细度达到325目筛余为0.4%~0.8%、流速为50~70 s/100ml。利用经过上述处理得到的浆料进行s3的耐磨防污保护釉布施操作。
[0023]
优选地,在上述制备方法的s2和s3之间还包括以下步骤:在砖坯的表面打印预设的花纹图案。可选地,使完成面釉布施的砖坯进入工业打印机进行产品花色图案打印,图案类型可选择石纹、大理石纹、木纹、玉石花纹等素材,图案素材效果不影响本方法所制得的亚光瓷砖的耐磨防污性能。
[0024]
本发明通过设计适用于亚光瓷砖的保护釉、面釉的配方组成以及瓷砖的烧成工艺,从而能够使釉层形成特定的晶相种类、数量及晶粒大小,使釉层中均匀分布细小的晶体,这些晶体的硬度一般高于玻璃相,另外,形成细小的晶粒可以减少晶体与玻璃相膨胀系数不匹配产生的微裂纹,同时减少釉面粗糙度,进而提高防污性能。发明人研究结果表明本发明所提供的釉料在烧成过程中受控析出亚微米和纳米级钙长石、钡长石、硅酸锆以及锌铝尖晶石晶粒,这些晶粒一方面提高釉面的耐磨性能,另一方面对光线具有漫反射的作用,由此在保证瓷砖釉面高耐污染性能的前提下实现瓷砖的亚光效果。
[0025]
本发明所提供的亚光瓷砖具有高耐磨、高防污、手感细腻、产品图案纹理清晰的特点,具体表现为:上述亚光瓷砖的耐污性能对轻油中的鉻绿、轻油中的红色污染物、碘酒液、橄榄油都达到了5级防污标准,远远大于国标的3级标准;上述亚光瓷砖的耐磨性能达到4级,高于国家标准3级。
附图说明
[0026]
图1为利用实施例6的保护釉所制得的瓷砖砖面物相分析图。
具体实施方式
[0027]
以下将结合附图及实施例对本发明做进一步说明。需要指出的是,以下所述实施例旨在便于对本发明的理解,而对其不起任何限定作用。
[0028]
按照质量份数计算,以下实施例中所采用的高硼熔块由以下物料制成:高岭土8份、石英12.5份、方解石5份、碳酸钾6.5份、碳酸钠17份、钠长石17份、硼酸钠41份。按照质量百分比计算,由此制得的高硼熔块具有以下化学组成:al2o
3 10.28~14.53wt%、sio
2 32.74~40.85wt%、cao 1.85~2.25wt%、k2o 2.57~3.68wt%、na2o 10.50~16.21wt%、b2o
3 26.40~32.48wt%。
[0029]
按照质量份数计算,以下实施例中所采用的钡锌锶熔块由以下物料制成:高岭土14份、石英14份、钠长石12.5份、钾长石16.5份、碳酸钡36份、氧化锌17.5份、碳酸锶15份。按照质量百分比计算,由此制得的钡锌锶熔块具有以下化学组成:al2o
3 11.22~14.38 wt%、sio
2 28.5~32.6 wt%、na2o 1.85~2.35 wt%、k2o 2.3~3.2 wt%、bao 25.6~30.8 wt%、zno 15.6~18.9 wt%、sro 10.2~13.5 wt%。
[0030]
按照质量份数计算,以下实施例中所采用的高钙熔块由以下物料制成:高岭土14份、氧化铝13份、石英4.5份、方解石50份、滑石12.5份、碳酸钾6份、碳酸钠5份。按照质量百分比计算,由此制得的高钙熔块具有以下化学组成:al2o
3 18.5~23.5 wt%、sio
2 36.5~41.6 wt%、cao 25.6~30.8 wt%、mgo 4.8~6.4 wt%、k2o 3.4~4.5 wt%、na2o 2.4~3.4 wt%。
[0031]
实施例1按照质量份数计算,本实施例用于配置面釉配方的原料包括:煅烧高岭土19份、球粘土10份、刚玉5份、石英9份、钾长石20份、钠长石6份、高硼熔块21份、纳米硅酸锆(粒径为40~100 nm)10份。备料完成后,将配方所需原料混合均匀得到本实施例的面釉。
[0032]
实施例2按照质量份数计算,本实施例用于配置面釉配方的原料包括:煅烧高岭土15份、球粘土11份、刚玉5份、石英8份、钾长石18份、钠长石8份、高硼熔块25份、纳米硅酸锆(粒径为40~100 nm)10份。备料完成后,将配方所需原料混合均匀得到本实施例的面釉。
[0033]
实施例3按照质量份数计算,本实施例用于配置面釉配方的原料包括:煅烧高岭土15份、球粘土12份、刚玉5份、石英10份、钾长石20份、钠长石10份、高硼熔块20份、纳米硅酸锆(粒径为40~100 nm)8份。通过改变配方中不同物料的具体配比以形成不同的面釉配方。备料完成后,将配方所需原料混合均匀得到本实施例的面釉。
[0034]
实施例4按照质量份数计算,本实施例用于配置面釉配方的原料包括:煅烧高岭土15份、球粘土7份、刚玉4份、石英9份、钾长石22份、钠长石6份、高硼熔块25份、纳米硅酸锆(粒径为40~100 nm)12份。备料完成后,将配方所需原料混合均匀得到本实施例的面釉。
[0035]
对比例1本对比例作为实施例1的对比例,本对比例与实施例1的区别在于,在用于制备面釉的配方中,所采用的高硼熔块的用量偏高。
[0036]
按照质量份数计算,本对比例用于配置面釉配方的原料包括:煅烧高岭土19份、球
粘土10份、刚玉5份、石英9份、钾长石20份、钠长石6份、高硼熔块58份、纳米硅酸锆(粒径为40~100 nm)10份。备料完成后,将配方所需原料混合均匀得到本对比例的面釉。
[0037]
对比例2本对比例作为实施例1的对比例,本对比例与实施例1的区别在于,采用市售的熔块釉a,熔块釉a的化学组成包括:al2o
3 16.52~19.79 wt%、sio
2 52.51~56.84wt%、na2o 2.85~3.64 wt%、k2o 1.40~1.59 wt%、cao 8.75~9.05wt%、mgo 0.51~0.65wt%、bao 3.8~4.5wt%、zno 3.89~4.32 wt%。等质量地替代实施例1采用的面釉配方中的高硼熔块。
[0038]
按照质量份数计算,本对比例用于配置面釉配方的原料包括:煅烧高岭土19份、球粘土10份、刚玉5份、石英9份、钾长石20份、钠长石6份、市售熔块釉21份、纳米硅酸锆(粒径为40~100 nm)10份。备料完成后,将配方所需原料混合均匀得到本对比例的面釉。
[0039]
对比例3本对比例作为实施例1的对比例,本对比例与实施例1的区别在于,在用于制备面釉的配方中,并不含有纳米硅酸锆。
[0040]
按照质量份数计算,本对比例用于配置面釉配方的原料包括:煅烧高岭土19份、球粘土10份、刚玉5份、石英9份、钾长石20份、钠长石6份、高硼熔块21份。备料完成后,将配方所需原料混合均匀得到本对比例的面釉。
[0041]
对比例4本对比例作为实施例1的对比例,本对比例与实施例1的区别在于,采用市售面釉e5283等质量地替代实施例1采用的面釉配方中的纳米硅酸锆。
[0042]
按照质量份数计算,本对比例用于配置面釉配方的原料包括:煅烧高岭土19份、球粘土10份、刚玉5份、石英9份、钾长石20份、钠长石6份、高硼熔块21份、面釉e528310份。备料完成后,将配方所需原料混合均匀得到本对比例的面釉。
[0043]
测试例1参试对象:以实施例1~4、对比例1~4制得的面釉作为本测试例的参试对象。
[0044]
试验构建方式:(1)预处理:向参试面釉中添加甲基纤维素钠(添加量为面釉总质量的0.15%~0.2%)、三聚磷酸钠(添加量为面釉总质量的0.3%~0.45%)、水(添加量为面釉总质量的38%~45%),对混合得到的浆料进行球磨处理,至浆料的细度达到325目筛余为0.4%~0.8%、流速为50~70 s/100ml。
[0045]
(2)生坯施釉:将预处理得到的釉料布施在生坯的表面:施釉量为220~250 g/m2,使砖坯表面覆盖的面釉的厚度为0.05~0.08 mm。然后将生坯放入辊道窑进行烧成,煅烧温度为1180℃,煅烧时间为50分钟。由此得到表面形成不同面釉层的砖坯,该面釉层为由参试面釉经上述高温烧成而得到。性能测试:对表面形成不同面釉层的砖坯进行釉面性能测试,所检验项目的检验结果符合gb/t4100—2015标准中的规定。
[0046]
本测试例的8种参试面釉的性能测试结果如表1所示。
[0047]
依据表1展示的数据,实施例1~4提供的参试面釉所形成的釉层都具有良好的耐磨性能,其中,实施例1和实施例3提供的参试面釉所形成的釉层在经受6000转摩擦后,依然没有出现明显的磨损,表现出优异的耐磨性能。
[0048]
与实施例1所提供的参试面釉相比,对比例3和对比例4提供的参试面釉的配方中均不含有硅酸锆,由此形成的釉层的耐磨性能较差,由上述两种面釉成型的面釉层在经受1500转的摩擦后,釉面出现明显磨损。此外,对比例2提供的参试面釉的配方中不含高硼熔块,由其所制得的面釉层的耐磨性能也不理想,由此能够说明,在本发明所提供的面釉配方中,硅酸锆和高硼熔块在联合使用时,才能够使所形成的面釉层获得高耐磨的性能。其原因在于,当来自于高硼熔块的b2o3在面釉中的含量控制在一定范围内(b2o3质量不超过面釉总质量的15%),在烧成过程中,面釉中的b2o3全部转化为[bo4]硼氧四面体结构,而釉料中sio2转化为 [sio4]硅氧四面体结构,具有相同几何构型的[bo4]和[sio4]能够共同形成网络结构,由此大大地增强了面釉层的硬度,进而使得所形成的面釉层的耐磨性能得到提高。
[0049]
实施例1与对比例1所采用的面釉配方所包含的原料种类相同,然而,值得注意的是,与实施例1的面釉所形成的面釉层相比,对比例1的面釉所形成的面釉层的的耐磨性能并不理想。其原因在于对比例1用于配制面釉的配方中高硼熔块的用量偏多,当面釉中的b2o3含量过高(b2o3质量超过面釉总质量的15%),在烧成过程中,面釉中的b2o3不仅会转化为[bo4],还会转化为[bo3],[bo3]并非呈四面体结构,从而无法与呈四面体结构的[sio4]共同形成网络结构,由此,[bo3]的产生不但无法增强面釉的强度,反而引起釉层结构松散、降低釉面的硬度,导致所形成的面釉层耐磨度、耐污度降低。综合对比实施例1、对比例1和对比例2的参试面釉所形成面釉层的性能检测结果,可以证明,向面釉中添加高硼熔块,需要将高硼熔块的用量控制在一定范围内,才能够有效地起到改善面釉层耐磨性能的效果。
[0050]
此外,在耐污性能方面,实施例1~4的面釉形成的面釉层所能够达到的耐污性能也会优于对比例1~4的面釉形成的面釉层,其中,由实施例1的面釉所形成的面釉层表现出最佳的耐污性能。
[0051]
实施例5按照质量份数计算,本实施例用于配置保护釉配方的原料包括:煅烧高岭土12份、球粘土12份、刚玉6份、高硼熔块4份、钡锌锶熔块30份、高钙熔块25份。备料完成后,将配方所需原料混合均匀,即得到本实施例的保护釉。
[0052]
实施例6按照质量份数计算,本实施例用于配置保护釉配方的原料包括:煅烧高岭土8份、球粘土7份、刚玉5份、高硼熔块5份、钡锌锶熔块30份、高钙熔块25份。备料完成后,将配方所
需原料混合均匀,即得到本实施例的保护釉。
[0053]
实施例7按照质量份数计算,本实施例用于配置保护釉配方的原料包括:煅烧高岭土11份、球粘土8份、刚玉6份、高硼熔块5份、钡锌锶熔块25份、高钙熔块30份。备料完成后,将配方所需原料混合均匀,即得到本实施例的保护釉。
[0054]
实施例8按照质量份数计算,本实施例用于配置保护釉配方的原料包括:煅烧高岭土12份、球粘土7份、刚玉6份、高硼熔块5份、钡锌锶熔块35份、高钙熔块20份。备料完成后,将配方所需原料混合均匀,即得到本实施例的保护釉。
[0055]
实施例9按照质量份数计算,本实施例用于配置保护釉配方的原料包括:煅烧高岭土12份、球粘土12份、刚玉6份、高硼熔块4份、钡锌锶熔块26份、高钙熔块25份。备料完成后,将配方所需原料混合均匀,即得到本实施例的保护釉。
[0056]
实施例10按照质量份数计算,本实施例用于配置保护釉配方的原料包括:煅烧高岭土12份、球粘土9份、刚玉4份、高硼熔块5份、钡锌锶熔块31份、高钙熔块32份。备料完成后,将配方所需原料混合均匀,即得到本实施例的保护釉。
[0057]
对比例5本对比例作为实施例6的对比例,本对比例与实施例6的区别在于,在用于制备保护釉的配方中,所采用的高硼熔块的用量偏高。
[0058]
按照质量份数计算,本实施例用于配置保护釉配方的原料包括:煅烧高岭土8份、球粘土7份、刚玉5份、高硼熔块15份、钡锌锶熔块30份、高钙熔块25份。备料完成后,将配方所需原料混合均匀,即得到对比例的保护釉。
[0059]
对比例6本对比例作为实施例6的对比例,本对比例与实施例6的区别在于,在用于制备保护釉的配方中,并不含有高硼熔块。
[0060]
按照质量份数计算,本实施例用于配置保护釉配方的原料包括:煅烧高岭土8份、球粘土7份、刚玉5份、钡锌锶熔块30份、高钙熔块25份。备料完成后,将配方所需原料混合均匀,即得到本对比例的保护釉。
[0061]
对比例7本对比例作为实施例6的对比例,本对比例与实施例6的区别在于,在用于制备保护釉的配方中,所采用的钡锌锶熔块的用量偏高。
[0062]
按照质量份数计算,本实施例用于配置保护釉配方的原料包括:煅烧高岭土8份、球粘土7份、刚玉5份、高硼熔块5份、钡锌锶熔块45份、高钙熔块25份。备料完成后,将配方所需原料混合均匀,即得到本对比例的保护釉。
[0063]
对比例8本对比例作为实施例6的对比例,本对比例与实施例6的区别在于,在用于制备保护釉的配方中,所采用的高钙熔块的用量偏高。
[0064]
按照质量份数计算,本实施例用于配置保护釉配方的原料包括:煅烧高岭土8份、
球粘土7份、刚玉5份、高硼熔块5份、钡锌锶熔块30份、高钙熔块40份。备料完成后,将配方所需原料混合均匀,即得到本对比例的保护釉。
[0065]
对比例9本对比例作为实施例6的对比例,本对比例与实施例6的区别在于,在用于制备保护釉的配方中,所采用的钡锌锶熔块的用量偏低。
[0066]
按照质量份数计算,本实施例用于配置保护釉配方的原料包括:煅烧高岭土8份、球粘土7份、刚玉5份、高硼熔块5份、钡锌锶熔块15份、高钙熔块25份。备料完成后,将配方所需原料混合均匀,即得到本对比例的保护釉。
[0067]
对比例10本对比例作为实施例6的对比例,本对比例与实施例6的区别在于,在用于制备保护釉的配方中,所采用的高钙熔块的用量偏低。
[0068]
按照质量份数计算,本实施例用于配置保护釉配方的原料包括:煅烧高岭土8份、球粘土7份、刚玉5份、高硼熔块5份、钡锌锶熔块30份、高钙熔块3份。备料完成后,将配方所需原料混合均匀,即得到本对比例的保护釉。
[0069]
测试例2参试对象:以实施例5~10、对比例5~10制得的保护釉作为本测试例的参试对象。
[0070]
试验构建方式:(1)预处理:向参试面釉中添加甲基纤维素钠(添加量为面釉总质量的0.15%~0.2%)、三聚磷酸钠(添加量为面釉总质量的0.3%~0.45%)、水(添加量为面釉总质量的38%~45%),对混合得到的浆料进行球磨处理,至浆料的细度达到325目筛余为0.4%~0.8%、流速为50~70 s/100ml。
[0071]
基于实施例1所得到的测试结果,选用实施例1中的最佳面釉配方与本实施例设置的不同保护釉进行搭配使用,按照下述步骤制备亚光瓷砖:(1)砖坯准备步骤,压制生坯坯体,本实施例用于压制生坯坯体的物料配方为目前的仿古瓷砖所适用的坯料(在其他实施方式中,坯体的规格和厚度、选用坯体种类可以按照实际生产需要调整,这些因素均不对产品釉面的耐磨防污性能构成影响),对压制得到的砖坯进行干燥处理,使砖坯在150~220 ℃下干燥,使生坯中的水份含量从6.5%~7%降至0.3%~0.8%。
[0072]
(2)采用实施例1中的面釉,依照配方按量称取所需物料,将各配方所需原料混合均匀得到面釉,然后向其中添加甲基纤维素钠(添加量为面釉总质量的0.15%~0.2%)、三聚磷酸钠(添加量为面釉总质量的0.3%~0.45%)、水(添加量为面釉总质量的38%~45%),对混合得到的浆料进行球磨处理,至浆料的细度达到325目筛余为0.4%~0.8%、流速为50~70 s/100ml;利用由此得到的浆料布施在经过干燥的生坯的表面,施釉量为220~250 g/m2,使砖坯表面覆盖的面釉的厚度为0.05~0.08 mm。
[0073]
(3)将布施完面釉的砖坯放入工业打印机进行产品花色图案打印。
[0074]
(4)分别向本实施例的参试保护釉中添加甲基纤维素钠(添加量为面釉总质量的0.15%~0.2%)、三聚磷酸钠(添加量为面釉总质量的0.3%~0.45%)、水(添加量为面釉总质量的38%~45%),对混合得到的浆料进行球磨处理,至浆料的细度达到325目筛余为0.4%~
0.8%、流速为50~70 s/100ml;然后利用由此得到的对应不同参试保护釉配方的浆料布施在完成图案打印的不同生坯的表面,施釉量为220~250 g/m2,使砖坯表面覆盖的面釉的厚度为0.05~0.08 mm。
[0075]
(5)最后,将完成上述步骤后的砖坯放入辊道窑进行烧成,煅烧温度为1180℃,煅烧时间为50分钟。
[0076]
性能测试:对烧成得到的砖坯进行釉面性能测试,所检验项目的检验结果符合gb/t4100—2015标准中的规定,检测结果如表2所示。
[0077]
依据表2展示的数据,实施例5~10提供的保护釉制得的瓷砖成品都具有良好的耐磨性能以及耐污性能,其中,实施例5~7的保护釉所形成的釉层在经受6000转摩擦后,依然没有出现明显的磨损,表现出优异的耐磨性能,而分别利用实施例5、实施例6的保护釉制得的瓷砖成品的耐污性能都能够达到较高的等级。与此形成对比,利用对比例5~10的保护釉制得的瓷砖成品的耐磨性性能以及耐污性能都明显较差。
[0078]
如上所述,以实施例6的保护釉作为参照,对比例5的保护釉中的高硼熔块含量偏高,而对比例6的保护釉中不含有高硼熔块,将上述3种保护釉所形成的釉面进行对比,实施例6的保护釉在耐磨性能、耐污性能上表现出了显著的优越性,由此能够说明,在保护釉中添加一定量的高硼熔块能够使保护釉的耐磨、耐污性能都得到优化,然而如果添加的量过大,反而会使耐磨、耐污性能变差。这样的原因在于,往保护釉中添加一定量的高硼熔块,在烧成过程中,来自于高硼熔块的b2o3全部转化为[bo4]硼氧四面体结构,硼氧四面体结构通过进一步形成网络结构而增大了保护釉形成的釉层的硬度,但是,若保护釉中的高硼熔块过量,在烧成过程中,来自于高硼熔块的b2o3不仅会转化为[bo4],还会转化为[bo3],[bo3]并非呈四面体结构,从而无法与呈四面体结构的[bo4]共同形成网络结构,由此,[bo3]的产生不但无法增强釉层的强度,反而引起釉层结构松散、降低釉面的硬度,导致所形成的保护釉层耐磨度、耐污度降低。
[0079]
与实施例6提供的保护釉相比,对比例7的保护釉中的钡锌锶熔块含量偏高,对比例8的保护釉中的高钙熔块含量偏高,钡锌锶熔块和高钙熔块的使用,都在于向釉料中引入熔剂,然而,若向保护釉中的熔剂含量过高,会导致瓷砖烧成后釉层硬度偏低、质地偏软,无
法达到良好的耐磨性能。另外,参照表2,通过将实施例6与对比例7~10的参试保护釉所形成的釉面进行亚光效果对比,采用实施例6的保护釉制成的瓷砖的釉面光泽度为9,表现出良好的亚光效果,然而,对比例7~10的保护釉制成的瓷砖的釉面光泽度远远超过了10,釉面光泽度偏高,其釉面所展现的亚光效果不佳。在实施例6中,采用含有cao、bao、zno、sro等碱土金属氧化物和k2o、na2o等碱金属氧化物的钡锌锶熔块和高钙熔块,并使上述两种熔块按照一定的配比搭配石英、长石、高岭土,进行高温烧成,由此能够形成的长石类晶体和锌铝尖晶石晶体,利用实施例6的保护釉制得的瓷砖的砖面物相分析如图1所示,这些晶体具有优异的漫反射效果,能够降低了光线的反射率,从而使含有上述晶体的釉面展现亚光光泽。然而,对比例7~10所采用的钡锌锶熔块、高钙熔块超出了合适的用量范围,进而会对因高温烧成而在釉面形成的晶体种类、数量构成影响,进而影响了釉层的亚光效果。
[0080]
以上实施例仅用以说明本发明的技术方案而非对本发明保护范围的限制,尽管参照较佳实施例对本发明作了详细说明,本领域的普通技术人员应当理解,可以对本发明的技术方案进行修改或者等同替换,而不脱离本发明技术方案的实质和范围。