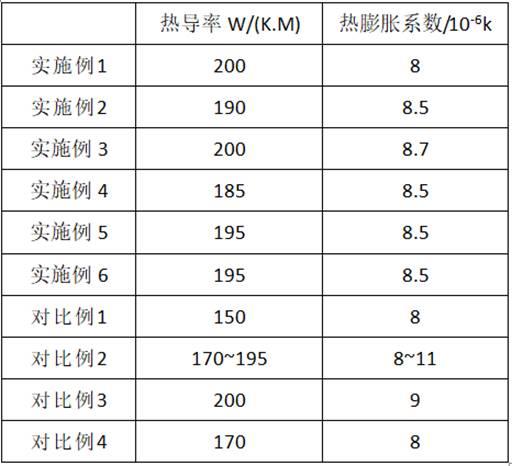
1.本发明涉及一种多孔碳化硅陶瓷及其制备方法和应用、铝碳化硅复合材料。
背景技术:2.随着电力电子以及半导体技术的发展,芯片正沿着大功率化、高频化的方向发展,大功率模块芯片集成度不断提高,例如绝缘栅双极型晶体管(igbt)功率模块集成度不断提高,功率不断增大,这也使得大功率模块芯片的工作温度不断上升,相应地对电子封装材料尤其是散热基板的要求越来越高,不仅要求散热基板具有与芯片相匹配的较低的热膨胀系数,而且还要求有较高的热导率。铝碳化硅(al-sic)复合材料作为一种高导热、低膨胀的新型电子封装材料,被广泛应用大功率模块芯片的封装。
3.铝碳化硅复合材料主要由金属铝和多孔碳化硅(sic)陶瓷制备而成,其中影响铝碳化硅复合材料性能的关键之一就是多孔碳化硅陶瓷的性能,碳化硅陶瓷的含量直接决定了复合材料的热导率和热膨胀,当碳化硅陶瓷含量越高,复合材料的热膨胀越低,但是复合材料的热导率也会降低。为了解决这一矛盾,就必须从多孔碳化硅陶瓷的配方和烧结工艺着手,保证复合材料的热膨胀和导热性能。
4.目前,多孔碳化硅陶瓷的制备主要有两种方法,一是通过添加低温粘接剂进行烧结,二是高温氧化法进行烧结。实际研究中发现,这两种方法,在烧结过程中都会在碳化硅陶瓷表面产生较多的低热导率的粘接相。例如,氧化法进行烧结时,由于采用高温(高于1000℃),会在碳化硅的表面形成氧化层-二氧化硅层,而在后期铝和碳化硅复合时,由于二氧化硅层的存在,铝与碳化硅之间的接触面积会减小,而二氧化硅的热膨胀系数又远低于碳化硅,因此,该二氧化硅层的存在严重影响后期复合材料的热导率。
技术实现要素:5.本发明所要解决的技术问题是提供一种多孔碳化硅陶瓷的制备方法,用该多孔碳化硅陶瓷制得的铝碳化硅复合材料具有低膨胀率和高热导率。
6.为达到上述目的,本发明采用的技术方案是:本发明提供一种多孔碳化硅陶瓷的制备方法,所述制备方法包括如下步骤:(1)按照如下骨料配方称取物料,其中,以所述骨料的质量为100%计,所述骨料的配方包括如下组分:碳化硅 95%~99.5%;二氧化硅 0.5%~5%;(2)使称量好的所述骨料混合、分散;(3)将分散后的所述骨料投入硫化造粒床进行造粒工序,获得陶瓷颗粒,其中,按照所述骨料总质量的40%~60%投加成型剂,所述成型剂为聚乙烯醇缩丁醛酯的醇溶液;(4)将所述陶瓷颗粒压成陶瓷预制体素坯;(5)使所述陶瓷预制体素坯烧结成所述多孔碳化硅陶瓷。
7.优选地,以所述骨料的质量为100%计,所述骨料的配方包括如下组分:碳化硅 98%~99.2%;二氧化硅 0.8%~2%。
8.进一步优选地,以所述碳化硅的质量为100%计,所述碳化硅包括:第一碳化硅 5%~
15%,所述第一碳化硅的中位径为1~10μm;第二碳化硅 20%~35%,所述第二碳化硅的中位径为25~35μm;第三碳化硅 55%~65%,所述第三碳化硅的中位径为70~90μm。
9.优选地,所述成型剂的投料量为所述骨料总质量的45%~55%。
10.优选地,所述醇包括乙醇、甲醇、乙二醇中的一种或多种。
11.进一步优选地,所述醇溶液中所述聚乙烯醇缩丁醛酯的质量浓度为10%~20%。
12.优选地,所述混合、分散的步骤包括使用双垂直高速铰刀进行分散,其中,高速铰刀的搅拌速度为1500~2000转/分钟,低速铰刀的搅拌速度为400~500转/分钟;所述分散的时间为25~35分钟。
13.优选地,将所述陶瓷颗粒压成陶瓷预制体素坯的步骤包括使所述陶瓷颗粒逐层铺排,在40~50mpa压力下干压成厚度10~100mm陶瓷预制体素坯。
14.优选地,所述烧结的温度为850~900℃,在大气环境下进行所述烧结。
15.进一步优选地,按照如下升温曲线进行所述烧结,所述升温曲线包括:a、室温~300℃,升温速率为3~10℃/min,保温1~3h;b、300~900℃,升温速率为3~10℃/min,保温1~3h;c、自然冷却至室温。
16.本发明的第二个方面提供一种多孔碳化硅陶瓷,所述多孔碳化硅陶瓷按照如上所述的制备方法制得。
17.优选地,单位体积下,所述多孔碳化硅陶瓷中骨料的体积含量为55%~65%;所述多孔碳化硅陶瓷的平均孔径为15~20微米、弯曲强度不低于10mpa。
18.本发明的第三个方面提供一种多孔碳化硅陶瓷在制备金属碳化硅复合材料中的应用,所述多孔碳化硅陶瓷按照如上所述的制备方法制得。
19.优选地,所述复合材料包括金属碳化硅复合材料,所述金属碳化硅复合材料中的金属包括铝和/或铜。
20.本发明的第四个方面提供一种铝碳化硅复合材料,所述铝碳化硅复合材料由铝和上所述的制备方法制得的多孔碳化硅陶瓷制备得到。
21.优选地,所述铝碳化硅复合材料中的铝与多孔碳化硅陶瓷的投料质量比为1:(1~2)。
22.优选地,所述铝碳化硅复合材料的热导率为150~210w/(m
•
k),热膨胀系数(7.5~11)
×
10-6
k。
23.由于上述技术方案运用,本发明与现有技术相比具有下列优点:本发明通过添加二氧化硅,有效促进碳化硅颗粒之间的粘接;进一步地,通过工艺以及配方的控制,使得二氧化硅多集中于碳化硅颗粒之间的粘接处,碳化硅陶瓷的表面几乎没有低热导率的粘接相-二氧化硅层,从而在后续的铝和碳化硅陶瓷复合时,可增加两者之间的接触面积,大幅度消除两相界面处的二氧化硅层,进而有效提升铝碳化硅复合材料的热导率。
具体实施方式
24.传统的氧化法工艺制备多孔碳化硅陶瓷,需要使碳化硅粉料在高温下(一般大于1000℃)进行表面氧化,这样的方式会在碳化硅表面产生低导热率的粘结相-二氧化硅层,严重影响后续铝碳化硅复合材料的热导率。本发明人意外地发现,通过向碳化硅粉体中添
加一定量的二氧化硅,并通过工艺以及配方的控制,能够使二氧化硅多集中于碳化硅颗粒之间的粘接处,避免碳化硅表面二氧化硅层的形成,从而使得后期的铝碳化硅复合材料的热导率大大提升。
25.本发明提供一种多孔碳化硅陶瓷的制备方法,其包括如下步骤:(1)按照如下骨料配方称取物料,其中,以骨料的质量为100%计,骨料的配方包括如下组分:碳化硅 95%~99.5%;二氧化硅 0.5%~5%;(2)使称量好的骨料混合、分散;(3)将分散后的骨料投入硫化造粒床进行造粒工序,获得陶瓷颗粒,其中,按照骨料总质量的40%~60%投加成型剂,成型剂为聚乙烯醇缩丁醛酯的醇溶液;(4)将陶瓷颗粒压成陶瓷预制体素坯;(5)使陶瓷预制体素坯烧结成多孔碳化硅陶瓷。
26.根据本发明,二氧化硅在骨料中的质量含量优选为0.8%~5%,例如0.8%、1.0%、1.2%、1.4%、1.6%、1.8%、2.0%、3.0%、4.0%等。二氧化硅的粒径优选为0.3~5.0μm。
27.根据本发明,以碳化硅的质量为100%计,其包括:第一碳化硅 5%~15%,第一碳化硅的中位径为1~10μm;第二碳化硅 20%~35%,第二碳化硅的中位径为25~35μm;第三碳化硅 55%~65%,第三碳化硅的中位径为70~90μm。
28.进一步地,以碳化硅的质量为100%计,其包括:第一碳化硅 8%~12%,第一碳化硅的中位径为3~8μm;第二碳化硅 25%~30%,第二碳化硅的中位径为28~32μm;第三碳化硅 58%~62%,第三碳化硅的中位径为75~85μm。
29.根据本发明,成型剂的投料量优选为骨料总质量的45%~55%,例如45%、47%、50%、52%、55%等。
30.本发明的方案至少具有如下优点:(1)本发明通过向碳化硅粉体中添加一定量的二氧化硅微粉,这些微粉作为粘接剂,无需进行高温烧结,在较低的温度下(小于1000℃),即可将碳化硅颗粒粘接在一起;而由于烧结温度的下降,在碳化硅表面并未生成二氧化硅层(一般在1350~1460℃时,随着温度的升高,碳化硅颗粒的表面逐步形成较明显的氧化层),从而在与金属复合的时候,两相之间没有了低热导率层,有助于大幅度提高复合材料的热导率。
31.(2)本发明采用硫化造粒工艺进行造粒,这种方式相对于手工造粒来讲,效率更高,均匀性更好;相较于喷雾造粒效率也更高,设备和人员投入低,而且均匀性也更加均匀,并且相较于喷雾造粒几乎没有固废和液废,对环境几乎没有影响。
32.(3)本发明使用聚乙烯醇缩丁醛酯的醇溶液作为成型剂,相较于水基的成型剂(例如聚乙烯醇的水溶液),其更容易进行造粒,可进一步提高造粒的效率。
33.(4)本发明中的铝碳化硅复合材料同时具有低膨胀率和高热导率。
34.下面结合实施例对本发明作进一步描述。但本发明并不限于以下实施例。实施例中采用的实施条件可以根据具体使用的不同要求做进一步调整,未注明的实施条件为本行
业中的常规条件。本发明各个实施方式中所涉及到的技术特征只要彼此之间未构成冲突就可以相互组合。
35.在没有特别说明的情况下,d50指中位径或中值粒径,具体指一个样品的累计粒度分布百分数达到50%时所对应的粒径。。
36.下述实施例以及对比例中的原料均可市购获得,其中:聚乙烯醇缩丁醛酯(pvb)购自伊士曼(eastman),牌号为b98;聚乙烯醇(pva)购自长春化工,牌号为2088。
37.实施例1一种多孔碳化硅陶瓷的制备方法,其包括如下步骤:(1)按照如下骨料配方称取物料,其中,以骨料的质量为100%计,骨料的配方为:sic(d50=5μm) 11%;sic(d50=30μm) 28%;sic(d50=80μm) 60%;sio2粉(0.3~5.0μm) 1%;(2)将上述骨料用双垂直高速铰刀进行分散,其中,高速铰刀的搅拌速度为1500转/分钟,低速铰刀的搅拌速度为500转/分钟;分散时间为30分钟;(3)将步骤(2)中混合好的物料导入硫化造粒床,按照骨料质量的50%加入成型剂,成型剂为聚乙烯醇缩丁醛酯和乙醇的混合溶液,混合溶液中聚乙烯醇缩丁醛酯的质量浓度为20%,硫化造粒床转盘的转速为1500-2000转/分钟,制得直径为150~200um的陶瓷颗粒;(4)将陶瓷颗粒采用逐层铺排,在40mpa压力下干压成厚度为10mm陶瓷预制体素坯;(5)将陶瓷预制体素坯在大气环境下进行烧结,烧结温度850-900℃,其中烧结曲线如下:a、室温~300℃,升温速率5℃/min,并保温2小时,这一阶段称之为脱胶阶段;b、300℃~900℃升温速率5℃/min,保温2小时之后自然冷却至室温,最终得到多孔碳化硅陶瓷。
38.该实施例中,多孔碳化硅陶瓷的收粉率为95%,其中,收粉率=[(制得的多孔碳化硅陶瓷的总质量
×
多孔碳化硅陶瓷中碳化硅的含量)/碳化硅的总投料质量]
×
100%;体分为65%,其中体分是指单位体积下,多孔碳化硅陶瓷中骨料的体积占比;平均孔径为16
µ
m;弯曲强度为16mpa。
[0039]
该实施例制得的多孔碳化硅陶瓷均一性好,体分、孔径、弯曲强度的波动较小。
[0040]
实施例2该实施例与实施例1的区别如下:(1)按照如下骨料配方称取改料,其中,以骨料的质量为100%计,骨料的配方为:sic(d50=12μm) 11%;sic(d50=30μm) 28%;sic(d50=80μm) 60%;sio2粉(0.3~5.0μm) 1%;该实施例中,多孔碳化硅陶瓷的收粉率为95%,体分为60%,平均孔径为18
µ
m;弯曲
强度为10mpa。
[0041]
该实施例制得的多孔碳化硅陶瓷均一性好,体分、孔径、弯曲强度的波动较小。
[0042]
实施例3该实施例与实施例1的区别如下:(1)按照如下骨料配方称取改料,其中,以骨料的质量为100%计,骨料的配方为:sic(d50=5μm) 11.2%;sic(d50=30μm) 28%;sic(d50=80μm) 60%;sio2粉(0.3~5.0μm) 0.8%。
[0043]
该实施例中,多孔碳化硅陶瓷的收粉率为95%,体分为65%,平均孔径为16
µ
m;弯曲强度为8mpa。
[0044]
该实施例制得的多孔碳化硅陶瓷均一性好,体分、孔径、弯曲强度的波动较小。
[0045]
实施例4该实施例与实施例1的区别如下:(1)按照如下骨料配方称取改料,其中,以骨料的质量为100%计,骨料的配方为:sic(d50=5μm) 10%;sic(d50=30μm) 28%;sic(d50=80μm) 60%;sio2粉(0.3~5.0μm) 2%。
[0046]
该实施例中,多孔碳化硅陶瓷的收粉率为95%,体分为65%,平均孔径为16
µ
m;弯曲强度为17mpa。
[0047]
该实施例制得的多孔碳化硅陶瓷均一性好,体分、孔径、弯曲强度的波动较小。
[0048]
实施例5该实施例与实施例1的区别如下:(3)按照骨料质量的40%加入成型剂。
[0049]
该实施例中,步骤(3)制得的陶瓷颗粒中含有较多的粉状物,物料未全部形成陶瓷颗粒,多孔碳化硅陶瓷的收粉率为80%,体分为65%,平均孔径为16
µ
m;弯曲强度为16mpa。
[0050]
该实施例制得的多孔碳化硅陶瓷均一性好,体分、孔径、弯曲强度的波动较小。
[0051]
实施例6该实施例与实施例1的区别如下:(3)按照骨料质量的60%加入成型剂。
[0052]
该实施例中,步骤(3)中出现明显的颗粒长大和结块现象,多孔碳化硅陶瓷的收粉率为75%,体分为62%,平均孔径为16
µ
m;弯曲强度为16mpa。
[0053]
该实施例制得的多孔碳化硅陶瓷均一性好,体分、孔径、弯曲强度的波动较小。
[0054]
对比例1该对比例与实施例1的区别如下:(1)按照如下骨料配方称取改料,其中,以骨料的质量为100%计,骨料的配方为:sic(d50=5μm) 10.20%;sic(d50=30μm) 28.58%;
sic(d50=80μm) 61.22%;(5)将陶瓷预制体素坯在大气环境下进行烧结,烧结温度1350℃,其中烧结曲线如下:a、室温~300℃,升温速率5℃/min,并保温2小时,这一阶段称之为脱胶阶段;b、300~1350℃升温速率3℃/min,保温3小时之后自然冷却至室温,最终得到多孔碳化硅陶瓷。
[0055]
该对比例中,多孔碳化硅陶瓷的体分为62%,平均孔径为16~20
µ
m;弯曲强度为15~17mpa。
[0056]
对比例2该对比例与实施例1的区别如下:(2)按照骨料质量的50%加入成型剂,并加入增稠剂(羧甲基纤维素)、分散剂(南通市晗泰化工 ht a30)以及水,在立式搅拌机搅拌2h,其中,成型剂为聚乙烯醇和水的混合溶液,混合溶液中聚乙烯醇的质量浓度为30%;控制增稠剂、分散剂以及水的投料量以使体系中聚乙烯醇的质量浓度为1%、增稠剂的质量浓度0.3%、分散剂的质量浓度0.4%;(3)将步骤(2)中混合好的物料导入喷雾干燥设备,进行喷雾干燥造粒。
[0057]
该对比例中,多孔碳化硅陶瓷的收粉率为75%,体分为62%,平均孔径为16
µ
m;弯曲强度为16mpa。
[0058]
该对比例中制得的多孔碳化硅陶瓷的均一性不好,体分、孔径以及弯曲强度的波动较大。
[0059]
对比例3(1)按照如下骨料配方称取改料,其中,以骨料的质量为100%计,骨料的配方为:sic(d50=5μm) 11.5%;sic(d50=30μm) 28%;sic(d50=80μm) 60%;sio2粉(0.3~5.0μm) 0.5%。
[0060]
该实施例中,多孔碳化硅陶瓷的收粉率为95%,体分为65%,平均孔径为16mpa;弯曲强度低于3mpa。
[0061]
对比例4该实施例与实施例1的区别如下:(1)按照如下骨料配方称取改料,其中,以骨料的质量为100%计,骨料的配方为:sic(d50=5μm) 6%;sic(d50=30μm) 28%;sic(d50=80μm) 60%;sio2粉(0.3~5.0μm) 6%。
[0062]
该实施例中,多孔碳化硅陶瓷的收粉率为95%,体分为16%,平均孔径为16
µ
m;弯曲强度为20mpa。
[0063]
应用验证将上述对比例和实施例中的多孔碳化硅陶瓷与金属铝按照2:1的体积比进行复合,制成铝碳化硅复合材料,复合工艺为反向真空压力浸渗工艺,具体可参照文献:真空变
压力浸渗法制备高体积分数sic
p
/al复合材料,中国有色金属学报,第16卷第9期1551-1557,本技术不作具体限制,铝碳化硅复合材料的性能参照表1所示。
[0064]
表1上述热导率的测试方法所依据的标准是astm e1461用闪光法测定热扩散率的标准试验方法;上述热膨胀率的测试方法所依据的国标是gb/t 16535-1996 工程陶瓷线热膨胀系数试验方法。
[0065]
以上对本发明做了详尽的描述,其目的在于让熟悉此领域技术的人士能够了解本发明的内容并加以实施,并不能以此限制本发明的保护范围,凡根据本发明的精神实质所作的等效变化或修饰,都应涵盖在本发明的保护范围内。