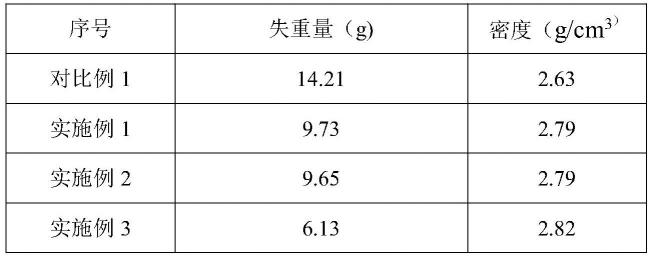
1.本发明属于功能陶瓷材料技术领域,更具体地,涉及一种耐磨的二氧化硅/碳化硅复合陶瓷及其制备方法和应用。
技术背景
2.目前,工业生产氧化物结合碳化硅制品使用的碳化硅都是用艾奇逊(acheson)法碳化硅冶炼炉冶炼得到的。冶炼得到的碳化硅为40~500mm的块状,其sic结晶体为α-sic,结晶体尺寸一般不超过5mm,大部分在3mm以下。在结晶体之间,存在大量气孔。将冶炼碳化硅块破碎和分级,可以得到不同粒度的sic颗粒。在破碎过程中,碳化硅易从结晶体之间的气孔处破裂,因此,当碳化硅颗粒小于1mm后,颗粒上的气孔会显著减少,且气孔一般较浅,颗粒难以沿这些浅气孔发生破裂。当碳化硅颗粒大于3mm时,颗粒上会存在大量片状气孔,这些气孔很多深度(片状气孔轮廓最大方向的尺寸)在数mm至数十mm,宽度(气孔轮廓最小方向的尺寸)在0.1μm至1000μm。这使得3mm以上的碳化硅颗粒的显气孔率可达2%甚至更高。在生产氧化物结合碳化硅制品时,碳化硅颗粒的最大粒度一般不大于3mm,并采用不同粒度的颗粒进行级配以得到较高的堆积密度;金属硅的配比一般为制品重量的5~15%,金属硅太多,不但制造成本较高,制品的耐磨性也会明显下降;金属硅太少,制品的机械强度会明显下降。如果是采用浇注成型,金属硅的粒度必须要严格控制,颗粒太粗,结合相分布不均匀,会导致制品的强度明显下降;颗粒太细,金属硅易和临时结合剂中的水发生水化反应,生成氢气和二氧化硅,导致毛坯疏松和制品强度及耐磨性下降。因此浇注成型工艺中金属硅的粒径一般选在数十μm至数百μm,这使得金属硅颗粒在成型时难以进入到颗粒中的片状或针状气孔中。采用干法成型可以采用较细的金属硅颗粒,粒度可以在数μm至数十μm,但由于干法成型的全部原料的物料中几乎没有液体,物料的流动性很差,这些细硅粉也很难进到0.1~10μm的气孔内,而且小于10μm的超细粉,非常容易形成团聚现象,特别是为了提高坯件的强度,在配料中加入一定的临时结合剂后,会进步增加颗粒的团聚现象。因此,即使选用颗粒更细的金属硅颗粒,在混料或压制过程中也只有极少量金属硅可以进入到碳化硅颗粒的气孔中,不可能将气孔填满。在氧化物结合碳化硅制品的烧结过程中,α-sic颗粒几乎不发生物理或化学变化,同时,在低于1420℃时在结合相中只有很少玻璃相生成,由于毛细作用,玻璃相一般只处于相邻的sic颗粒之间,不能进入到sic颗粒的气孔中。相当温度达到1420℃即金属硅的熔点以后,金属硅已几乎被完全氧化成为sio2,仅剩极少金属硅熔化可以成为液相,但这些极少的液态金属硅在毛细作用下不可能发生大的位移并对α-sic颗粒上的针状或片状气孔进行填充,并将气孔填满。因此,氧化物结合碳化硅制品中的3~5mm粗颗粒上,有大量的宽度在1~10μm的开放性气孔。氧化物结合碳化硅制品的显气孔率一般在12~22%,其显气孔大部分是位于结合相中,少部分位于主相中。这些气孔,特别是结合相中的气孔,可以明显降低氧化物结合碳化硅陶瓷烧结和冷却过程中产生的进残存内应力,从而有利于工件的大型化。氧化物结合碳化硅可被用于制造耐磨产品,如耐磨喷嘴、渣浆泵备件、旋流器等。特别是用于轻磨蚀、轻冲击的冲刷工况时,可以获得较好的使用效
果。但由于sic大颗粒上存在有大量气孔和棱角,增大sic颗粒会导致陶瓷混合料的流动性变差,增加氧化物结合碳化硅制品成型的工艺难度和降低陶瓷毛坯的成型质量。因此,上述氧化物结合碳化硅制品极少采用5mm以上的sic颗粒。由于碳化硅颗粒上大量气孔的存在,现有氧化物结合碳化硅制品的密度一般只有2.5~2.65g/cm3,大量气孔的存在,使得现有氧化物结合碳化硅制品的耐磨性不能满足很多工况的要求。
3.反应烧结碳化硅陶瓷一般是采用艾奇逊(acheson)法生产的α-sic制成10~100μm的微粉,加入10~100μm的碳粉和结合剂,成型后和单质硅颗粒一起放入反应烧结炉中,在1500~1700℃的真空或保护气体中烧结,单质硅在其熔点(约1420℃)以上以液态或汽态渗入毛坯中,和碳粉反应生成β-sic,单质硅同时将毛坯中的气孔全部充填,得到含65~75%的α-sic,20~30%的β-sic,10~15%单质硅的几乎没有气孔的陶瓷件。反应烧结碳化硅相比氧化物结合碳化硅有更好的耐磨性,但由于几乎没有气孔(显气孔率一般为0~0.3%),且有较多量的脆性的单质硅,使得其在烧结后存在较大的残存内应内,并且其内应力随着工件的尺寸增大而明显增大,这使得反应烧结碳化硅陶瓷的大型工件抵抗冲击的能力极差,一些情况下甚至轻微的振动都会导致大型工件的破碎,同时,反应烧结碳化硅陶瓷一般需要在真空炉中进行,由于碳化反应烧结炉的结构特点,能够烧制造大型工件的真空炉成本很高。
4.为解决氧化硅结合碳化碳陶瓷耐磨性和耐大颗粒冲击性能不足的问题,cn113404723a提出了一种复相反应烧结碳化硅陶瓷的制造方法,其基本思路是将已烧结好的氧化物结合碳化硅陶瓷制品渗碳,再在渗碳后的氧化物结合碳化硅陶瓷制品的外表放置模具,在模具和氧化物结合碳化硅陶瓷制品之间注入含碳化硅微粉和碳微粉的浆料二次成型,再将二次成型的制品干燥后放入反应烧结炉进入二次烧结,得到表面覆盖有反应烧结碳化硅的复相陶瓷。这种技术方案的优点是可以根据需要在磨损严重的表面设置反应烧结陶瓷,同时,工件的整体气孔率也可以大幅下降,从而可以使制品可以具有更高的耐磨性能。但该技术方案存在以下问题:(1)产品需要经过二次成型、二次烧结,工艺复杂,成本较高;(2)二次烧结必须在反应烧结炉中进行,如果工件较大,较大的反应烧结炉价格是十分昂贵的,需要较大的固定资产投入;(3)由于工艺的特点,通过二次烧结得到的复相陶瓷的材料组成和气孔率在宏观或整体上是极不均匀的,分布在其在表面的主要是主要成份是自结合碳化硅(约为重量的85~90%)和金属硅(约为重量的10~15%),气孔率几乎为零;而在远离表面的部位,由于碳和硅难以渗入,其主要成分仍是氧化物结合碳化硅,其气孔率可达15~18%。对于大型工件而言,材质在宏观或整体上的巨大差异,会导致陶瓷件在二次烧结时或冷却后产生很大的残存内应内,不但使工件的成品率大幅下降,同时使制品的耐冲击性能和可靠性大大下降。
技术实现要素:5.为了解决上述现有技术存在的不足和缺点,本发明的目的在于提供一种耐磨的氧化物/碳化硅陶瓷的制造方法。
6.本发明的另一目的在于提供上述方法制备的耐磨的氧化物/碳化硅陶瓷。
7.本发明的再一目的在于提供上述耐磨的氧化物/碳化硅陶瓷的应用。
8.本发明的目的通过下述技术方案来实现:
9.一种耐磨的二氧化硅/碳化硅复合陶瓷的制备方法,包括以下具体步骤:
10.s1.将冶炼的α-sic破碎得到粒度为3~50mm的α-sic块和粒度为0.001~3mm的α-sic颗粒,将α-sic块浸入含有粒度在0.0001~0.01mm碳黑微粉或有机碳的液体中,使碳黑微粉或有机碳渗入到α-sic块的气孔中,炭黑微粉经干燥或有机碳在300~800℃碳化后,得到表面覆盖和气孔中填充碳粉的α-sic块-碳粉混合体;
11.s2.在真空或惰性气氛的烧结炉中,将α-sic块-碳粉混合体和硅颗粒,升温至1420~1700℃烧结,得到渗硅反应烧结sic块,冷却后将其进行破碎或/和分级筛选,得到渗硅反应烧结sic颗粒;
12.s3.按照质量百分比计,将15~50%的渗硅反应烧结sic颗粒、25~60%的步骤s1得到的α-sic颗粒、5~10%的金属硅和3~20%的结合剂混合成陶瓷料,加入模具中浇注成型或压力成型为陶瓷毛坯,将该陶瓷毛坯在1300~1420℃氧化气氛中烧结,冷却后得到耐磨的sio2/sic复合陶瓷。
13.优选地,步骤s1中所述的有机碳为25℃时粘度小于800mpa
·
s的环氧树脂。
14.优选地,步骤s2中所述硅颗粒的粒径为0.001~5mm。
15.优选地,步骤s3中所述渗硅反应烧结sic颗粒的粒径为2~20mm,金属硅的粒径为0.001~1mm。
16.优选地,步骤s2中所述α-sic块和碳粉的混合体与金属硅的重量比为10:(1-3)。
17.优选地,步骤s3中所述的结合剂包括铝酸盐水泥和/或氧化物。
18.优选地,所述氧化物为氧化钙、氧化铝或氧化硅。
19.优选地,步骤s3中所述的结合剂还包括临时结合剂,所述临时结合剂为水或有机粘接剂,所述临时结合剂为陶瓷料总重量的5~12%。
20.一种耐磨的二氧化硅/碳化硅复合陶瓷,所述复合陶瓷是由所述方法制备得到。
21.所述的耐磨的二氧化硅/碳化硅复合陶瓷在渣浆泵、旋流器或浮选机领域中的应用。
22.本发明在选择陶瓷颗粒的粒度时发现,当用含有1mm左右的固体颗粒的冲刷介质验证陶瓷的磨蚀性时,必须在氮化硅结合碳化硅陶瓷中加入大于5wt%的3~5mm粗sic颗粒,才能获得较好的耐磨效果,这是由于氮化硅结合碳化硅陶瓷中的小于1mm的sic颗粒易被冲刷介质中的1mm左右的固体颗粒冲击而发生脱落。当陶瓷中加入大于5wt%的3~5mm的sic颗粒后,冲刷介质中的1mm左右的固体颗粒的冲击能量不足以使氮化硅结合碳化硅陶瓷中3~5mm的sic颗粒脱落,同时也不足以使3~5mm的sic颗粒沿sic结晶体之间的气孔发生破碎。因此,这些3~5mm的sic颗粒可以显著提高这种工况下的耐磨性。而当冲刷介质中的固体颗粒进一步加大(大于1mm且小于5mm)时,冲刷介质中固体颗粒的冲击能随着其体积的增加而增加,虽不足以使氮化硅结合碳化硅陶瓷中的3~5mm颗粒发生脱落,但足以使其沿sic结晶体之间的片状气孔处发生破碎。由于这种破碎现象的出现,将陶瓷中的sic颗粒继续加大几乎不会提高氮化硅结合碳化硅陶瓷的耐磨性,有些工况下甚至会出现耐磨性下降的情况。而本发明选择粒度为2~20mm的渗硅反应烧结sic颗粒、粒度为0.001~3mm的α-sic颗粒和粒度为2~20mm反应烧结sic颗粒为原料,在真空或惰性气氛条件下1420~1700℃烧结,烧结完成后颗粒中大部分的气孔被β-sic、金属硅和sio2填满,且金属硅、β-sic、sio2与α-sic之间均有较好的结合力,使得渗硅反应烧结sic粗颗粒在受磨损和冲击时,颗粒从原
始气孔处碎裂的可能性大大下降,而且β-sic有很好的耐磨性,反应烧结sic颗粒的表面部分或全部覆盖有β-sic层后,可使复合陶瓷的耐磨和机械性能显著提高。
23.与现有技术相比,本发明具有以下有益效果:
24.1.本发明二氧化硅/碳化硅复合陶瓷中主相包括粒度为2~20mm的渗硅反应烧结sic颗粒、粒度为0.001~3mm的α-sic颗粒和粒度为2~20mm反应烧结sic颗粒,烧结完成后颗粒中大部分的气孔被β-sic、金属硅和sio2填满,且金属硅、β-sic、sio2与α-sic之间均有较好的结合力,使得渗硅反应烧结sic粗颗粒在受磨损和冲击时,颗粒从原始气孔处碎裂的可能性大大下降,同时,β-sic有很好的耐磨性,反应烧结sic颗粒的表面部分或全部覆盖有β-sic层后,可使陶瓷的耐磨和机械性能较现有技术的二氧化硅/碳化硅复合陶瓷显著提高,同时,也明显提高了复合陶瓷的耐大颗粒冲刷磨损的能力。
25.2.本发明采用浇注成型或压力成型法,制得耐磨的二氧化硅/碳化硅复合陶瓷,在整个制造过程中仅需一次成型,不但成型的难度小,而且成本较低。而且在成型后,仅需在氧化烧结炉中进行一次烧结,不但设备投资较少,易于大型化,烧结成本也低得多。
26.3.本发明的耐磨二氧化硅/碳化硅复合陶瓷相对均匀,不会产生大的烧结残余应力。同时由于结合相sio2中的显气孔率一般在6~12%,可以进一步减小烧结残余应力,这样在制造大或厚的陶瓷工件时,制品发生破碎的概率会大大降低。
27.4.在现有技术的二氧化硅/碳化硅复合陶瓷(二氧化硅结合碳化硅)中,将主相的颗粒设置到3~5mm以后,继续加大颗粒的粒度,几乎不会提高其耐磨性和耐冲击性,而本发明的反应烧结sic颗粒,由于大部分气孔被填满,磨损或冲击时不易从气孔位置发生破碎。因此,可以继续加大反应烧结sic颗粒的粒度,以提高陶瓷的耐冲击性,同时,本发明的反应烧结sic颗粒由于气孔基本被充填,可以提高陶瓷料的流动性,并提高陶瓷毛坯的成型质量和陶瓷烧结件质量。但粒度的加大会对陶瓷毛坯的成型工艺带来困难的趋势是不可改变的,所以一般的粒度为2~20mm,最佳为不超过15mm。
28.5.本发明通过破碎或分级,可以得到各种合适粒度的渗硅反应烧结sic颗粒。对α-sic块进行渗硅反应烧结时,浸入有碳黑微粉或有机碳的α-sic块的粒度一般在3~50mm,最佳为5~30mm。如果α-sic块的粒度太大,碳黑微粉或有机碳和金属硅难以充分填到α-sic块内部的气孔,会导致较多的气孔不能被有效填满。颗粒太小时,颗粒上几乎没有气孔,渗硅反应烧结也就没有了多大意义。
29.6.本发明对α-sic块进行渗硅反应烧结并破碎筛分后,2~20mm渗硅反应烧结sic颗粒中的气孔会大大减少,因此在浇注成型或压力成型时,加入的大粒度的渗硅反应烧结sic颗粒对浇注料的流动性影响较小,有利于成型并提高成型密度,从而提高陶瓷的耐磨性。
30.7.本发明结合剂中加入氧化铝等氧化物,可以提高陶瓷毛坯的强度并改善陶瓷结构,提高其强度。
具体实施方式
31.下面结合具体实施例进一步说明本发明的内容,但不应理解为对本发明的限制。若未特别指明,实施例中所用的技术手段为本领域技术人员所熟知的常规手段。除非特别说明,本发明采用的试剂、方法和设备为本技术领域常规试剂、方法和设备。
32.实施例1
33.1.将冶炼制得的α-sic破碎筛分,得到α-sic块(粒度在3~30mm,sic含量≥98%)和α-sic颗粒(粒度为0.001~2mm);
34.2.将α-sic块(粒度3~30mm)浸入含有碳黑微粉(粒径在0.00001~0.01mm)的水悬浊液中,其中碳黑微粉的重量浓度为25~35%,可在水中加入分散剂防止炭黑颗粒团聚,分散剂可选用六偏磷酸钠(含量为水质量的0.5~1%)或司马产pc67(含量为水质量的0.15%)。使碳黑微粉渗入到α-sic块的气孔中,干燥后得到表面覆盖和气孔中填充有碳粉的α-sic块-碳粉混合体。
35.3.将重量比为10:1的α-sic块-碳粉混合体与金属硅(粒度2~10mm,si含量≥98%)混合,在真空炉中在1700℃烧结120~240min,冷却后得到渗硅反应烧结sic块;将其进行破碎和分级,得到渗硅反应烧结sic颗粒(粒度在2~20mm);
36.4.按质量百分比,将15%的渗硅反应烧结sic颗粒(粒度为2~20mm)、5%的金属硅(粒度为0.01~0.5mm)、60%的步骤1所得α-sic颗粒(粒度0.001~2mm)、20%的结合剂(15%的铝酸盐水泥和5%的氧化铝)混合成为陶瓷料,为便于成型,还加入了上述固体物重量的8~12%的水作为临时结合剂,混合均匀后在模具中采用浇注成型为陶瓷毛坯;
37.5.将陶瓷毛坯放入氧化炉中,加温至1350~1420℃,将陶瓷毛坯中的金属硅氧化生成sio2,冷却后得到耐磨的sio2/sic复合陶瓷,其密度为2.79g/cm3。
38.在陶瓷烧结过程中,在渗硅反应烧结碳化硅块的气孔内的残余的金属硅部分会和氧气反应生成氧化硅,体积略有膨胀,有利于气孔的填满,但有微量金属硅由于气孔的结构或位置,难以和氧气接触,不能被完全氧化,在陶瓷烧结结束后仍为单质硅。
39.实施例2
40.与实施例1不同的在于:步骤4中临时结合剂为固体总重量5%的酚酫树脂,作为临时结合剂,也可采用其它有机粘接剂替代(如淀粉糊、聚乙烯醇、呋喃树脂等)。采用压力成型,成型压力为10~100mpa。本实施例的sio2/sic复合陶瓷的密度为2.79g/cm3。
41.实施例3
42.1.将冶炼制得的α-sic破碎得到α-sic块(粒度在5-50mm,sic含量≥98%)和α-sic颗粒(粒度为0.001~3mm);
43.2.将α-sic块(粒度为5~50mm)浸入含固化剂的cy-183环氧树脂(25℃时粘度约为500~600mpa
·
s)中,真空下使树脂渗入α-sic块的气孔中,室温或加热至120℃固化后得到表面覆盖和气孔中填充有树脂的α-sic块的混合体;
44.3.将重量比为10:3的填充有树脂的α-sic块的混合体和金属硅(粒度在2-10mm,si含量≥98%)在氩气保护炉中以200℃/h升温至300~800℃,树脂分解碳化,继续升温至1500~1700℃保温2h,金属硅液和蒸汽和碳反应,得到的渗硅反应烧结sic块(粒度在5~50mm),冷却后将其进行破碎和筛分,得到渗硅反应烧结sic颗粒(粒度在2~20mm);
45.4.按质量百分比,将50%的渗硅反应烧结sic颗粒(包括25%的粒度为2-5.9mm和25%的粒度为6~20mm)、25%的步骤1制得的α-sic颗粒(粒度为0.001~3mm)、15%的金属硅(粒度为0.01~0.5mm)和10%结合剂(5%的铝酸盐水泥和5%氧化铝)的混合成为陶瓷料,还加入固体重量的8~12%的水作为临时结合剂,在模具中浇注成型为陶瓷毛坯;
46.5.将陶瓷毛坯放入氧化炉中,加温至1300~1420℃,将陶瓷毛坯中的金属硅氧化
生成sio2,冷却后得到耐磨的sio2/sic复合陶瓷,其密度为2.82g/cm3。
47.实施例4
48.与实施例1不同的在于:步骤4中所述金属硅的粒度为0.001~0.1mm,采用压力成型,成型压力为100~200mpa,结合剂为铝酸盐水泥15%,未加入临时结合剂。本实施例的sio2/sic复合陶瓷的密度为2.80g/cm3。
49.对比例1
50.陶瓷料按原料的重量配比如下:15%的α-sic颗粒(粒度3~5mm),15%的α-sic颗粒(粒度1~2.5mm),20%的α-sic颗粒(粒度0.1~0.75mm),30%的α-sic颗粒(粒度0.001~0.074mm),5%的金属硅颗粒(粒度0.001~0.5mm),20%结合剂(铝酸盐水泥15%和氧化铝5%),加入固体物重量5%的酚酫树脂为临时结合剂,将陶瓷料和临时结合剂混合均匀后放入模具中,用压力机以10~100mpa压力成型为陶瓷毛坯,烧结工艺和实施例1完全相同,上述碳化硅和金属硅的含量大于98%。本对比例的sio2/sic复合陶瓷的密度为2.63g/cm3。
51.表1实施例1-4和对比例1制得的sio2/sic复合陶瓷的密度和冲刷磨损试验
[0052][0053][0054]
表1为本发明实施例1-4和对比例1制得的sio2/sic复合陶瓷的密度和冲刷磨损试验的对比数据表。从表1可以看出,本发明实施例的sio2/sic复合陶瓷的密度为2.79g/cm3以上,较对比例1有明显提高。冲刷磨损试验方法参照gb/t18301-2012。从表1中可知,实施例1的sio2/sic复合陶瓷的冲刷损失仅为对比例1的68.5%,实施例2的sio2/sic复合陶瓷的冲刷损失仅为对比例1的67.9%,实施例3的sio2/sic复合陶瓷的冲刷损失仅为对比例1的43.1%,实施例4的sio2/sic复合陶瓷的冲刷损失仅为对比例的71.2%,均有明显下降,说明实施例1-4制得的sio2/sic复合陶瓷的耐磨性均较对比例1的sio2/碳化硅复合陶瓷有明显提高。
[0055]
上述实施例为本发明较佳的实施方式,但本发明的实施方式并不受上述实施例的限制,其他的任何未背离本发明的精神实质与原理下所作的改变、修饰、替代、组合和简化,均应为等效的置换方式,都包含在本发明的保护范围之内。