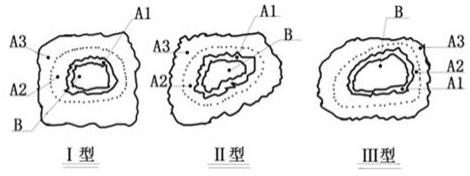
1.本发明属于混凝土骨料技术领域,具体涉及一种用煤矸石烧结型高强度轻质混凝土骨料的制备及生产方法。
背景技术:2.目前,大量结构用混凝土的骨料基本为天然石料,天然石料虽然其取料受限少、成本低,但因其自身密度需在2.6—3.0g/cm
³
之间才能有足够的抗压强度,这样直接导致混凝土的密度增大,从而导致建筑物整体质量的增大,导致在超高层建筑中,约150米以上就无法使用混凝土而改用钢结构,但即使用了钢结构主体,每层建筑物仍需大量的混凝土来配合钢结构完成。
3.同时,我国有约4700多个煤矿,每年产生约7亿吨煤矸石,这其中有约30%左右的矸石因其含固定碳低(《11%),成份复杂,含铁、钛高,并混有10—30%不等的页岩,这些低品位矸石基本都是以回填或填埋的方式处理,对环境带来重大的隐患。
4.因此,目前急需一种利用矸石制备质量轻,强度高的混凝土骨料的生产方法。
技术实现要素:5.针对现有技术存在的不足,本发明提供一种用煤矸石烧结型高强度轻质混凝土骨料的制备及生产方法,以解决现有技术中混凝土的骨料密度高,重量大,及矸石填埋造成环境负担的问题。
6.为了实现上述目的,本发明采用如下的技术方案:一种煤矸石烧结型高强度轻质混凝土骨料,所述混凝土骨料由内至外依次为空心层、无序层,部分瓷化层和完全瓷化层,所述无序层为冰凌状的半结晶半玻璃态;所述部分瓷化层为先还原气氛后氧化气氛烧结层,部分瓷化,且残留气孔。
7.进一步的,所述混凝土骨料由如下重量的组分组成:煤矸石:20-30份锂矿石尾渣:14-18份水磨长石水洗渣:8-12份花岗岩尾矿渣:8-12份污水压榨泥:7-11份钠长石:10-15份滑石泥:3-7份膨润土:4-8份炉膛渣:2-4份。
8.进一步的,所述煤矸石由如下重量的组分组成:
al2o3:32-40份sio2:40-18份固定碳:6-12份fe2o3:0.3-2.5份mgo:0.1-0.3份cao:0.01-2份k2o:0.05-1.5份na2o:0.05-1.5份tio2:0.5-1份loi:4-7份。
9.进一步的,所述混凝土骨料由如下重量的组分组成:煤矸石:28份锂矿石尾渣:16份水磨长石水洗渣:10份花岗岩尾矿渣:10份污水压榨泥:9份钠长石:13份滑石泥:5份膨润土:6份炉膛渣:3份。
10.进一步的,所述煤矸石由如下重量的组分组成:al2o3:37份sio2:41份固定碳:11份fe2o3:0.4份mgo:0.20份cao:1份k2o:0.2份na2o:0.3份tio2:0.7份loi:7份。
11.一种煤矸石烧结型高强度轻质混凝土骨料的制备方法,所述制备方法包括:一、原料的配制二、锅式造粒机滚动成型(1)将粉料与水按比例加入造粒机,5-8分钟至80%左右的粒子直径增大到13—14mm;(2)分离出小于8目的粒子,将大于8目的粒子倒入圆盘造粒机中,按料水比为8:1
的质量份同时喷雾加水,直至粒子长到15—16mm,取出粒子放入圆盘机中,加入白色炉膛渣粉末,喷雾加水约2—3分钟,至粒子表面覆盖一层薄的白色粉;(3)把成型好的粒子置入恒温干燥箱中干燥,至粒子含水率≤0.3%;三、烧成(1)将炉膛渣粗渣放入窑中,加入成型后的粒子,调节窑的温度只1200℃-1300℃进行烧结;(2)烧成粒子烧结后自动进入导环,冷却至600℃-700℃,即制得轻质骨料。
12.进一步的,所述一中的原料的配制包括:(1)把配制好的原料单独放入搅拌桶中,搅拌15分钟,把搅拌桶边、角的料铲起,混入主料中,再启动搅拌10分钟,保证混料均匀;(2)配制1.35%电解质水溶液,水溶液内的溶质为三聚磷酸钠。
13.进一步的,所述二中的锅式造粒机滚动成型包括:(1)先加入5kg备好的粉料,启动造粒机旋转,用喷壶加水的同时,逐渐加入粉料,最终要保证料与水的质量比为5:1至约有50%的粒子成型到11—12mm左右时停止喷水,改而用喷雾壶喷水,尽量保证料与水的质量比为7:1,继续滚动5-8分钟,至80%左右的粒子直径增大到13—14mm,停机,倒出全部粒子;(2)用8目筛过筛,分离出小于8目的粒子,小粒子倒回锅式造粒机中转动8分钟,取出8目以上的粒子倒入已启动圆盘造粒机中缓慢加入粉料,按料:水≈8:1的质量份同时喷雾加水,直至50%粒子长到15—16mm时,停止加料、加水,圆盘机继续旋转15—20分钟,取大粒子,表面无裂纹及不易掉渣为合格,加入适量白色炉膛渣粉末,喷雾加水约2—3分钟,粒子表面有一很薄的白色粉即可,继续转动3分钟停止;(3)把成型好的粒子分批次置入120℃恒温干燥箱中干燥,保证大粒子含水率≤0.3%为合格,并全部干燥好。
14.进一步的,所述三中的烧成步骤包括:(1)启动回转窑升温至1000℃时,取调节好含水约15—16%的炉膛渣粗渣,并以约6kg/分钟的量开始匀速加入窑中;炉膛渣加入完毕后即加入已制好的粒子,约3kg/分钟匀速加入粒子,回转窑调整参数至转速0.6转/分钟,温度保持在1250℃
±
3℃,粒子全部加入后继续以约4kg/min加入炉膛渣约5分钟;(2)回转窑开始出白色炉膛渣时,烧成粒子烧结后自动进入导环,用风扇吹冷风,并冷却到700℃为控制范围,使用转速为2.1转/分钟缓冷回转器冷却,出缓冷器粒子温度小于150℃,即制得轻质骨料。
15.本发明一种用煤矸石烧结型高强度轻质混凝土骨料的制备及生产方法的有益之处:本发明利用低品位煤矸石的特性,结合工厂周边锂矿尾渣,花岗岩采矿场废料,工厂产生的钾钠长石水洗渣,污水处理出的压榨泥为主要原料,生产出符合c40、c50标号混凝土用的轻质骨料,粗骨料(φ8.0—φ28.5mm)的平均密度为1200—1400kg/m
³
,堆积密度为780—820 kg/m
³
,其堆积密度仅为传统石子骨料的50—52%左右,同时产出的φ2.0—φ6.0的小粒子为瓷粒砂,堆积密度为840—880 kg/m
³
,经过高温烧结已完全瓷化,可以作为替代混凝土中使用的石英砂,粗骨料和瓷粒砂有机结合后可以大大降低混凝土密度,提高在高
层和超高层建筑物中的混凝土用量,同时可有效降低建筑物的自重。
16.附图说明
17.图1为本发明制备的骨料粒子的结构示意图;图2为本发明回转窑的结构示意图;图3为本发明粒子壁厚的测量示意图;
具体实施方式
18.下面结合附图对其具体实施方式作进一步阐述。
19.如下实施例中的设备为:
①
小型齿盘式磨粉机:可以把上表所列的各种原料磨细粉并达到过250目筛余≤0.2%;
②
锅式造粒机:φ600间隙式 转速10~25转/min;
③
圆盘式造粒机:φ1000转速15~30转/min;
④
干燥箱:最高温160℃;
⑤
回转窑,长15米、外径: φ1000.内径φ500,转速0.5~2.5转/min,红外线无线感应测温。最高烧成温度:1350℃,燃料:天燃气;
⑥
轴流风扇2台:1.1kw.φ400;
⑦
回转式缓冷器: φ273钢管. 长度:6米、转速0.8—2.8转/min;
⑧
干粉混料机:单次容量60kg;
⑨
300*300*300mm堆积密度测量箱。
20.实施例1:一种煤矸石烧结型高强度轻质混凝土骨料,通过固定碳分段反应产生高温气体膨胀后导致粒子膨胀的空心结构,且外层瓷化致密,低吸水,强度高,表面为无薄边及锋利棱角的大小连续的粒子,具体如图1所示:a3层:完全瓷化、致密、密度在2.70—3.00 g/cm
³
,吸水率≤1.2%,为氧化焰烧结层。
21.a2层:基本瓷化,但残留气孔较多,为先还原气氛后氧化气氛烧结层。
22.a1层:形成冰凌状的半结晶半玻璃态的无序层,结晶层的过渡层,对抗压指数无贡献。
23.b区:空心,是滚动成型成核时有较高的水份,较低的湿坯强度及低干燥强度,其固定碳分二级分解燃烧后产生从中心向外的膨胀力的同时粒子软化后相互滚动挤压,剪切力等导致粒子表面多层封闭,内部高温气体无法排出而产生空心结构。
24.骨料粒子的型状特征:整体外型类似圆型、椭圆形至苹果型、多边型,少部分为草莓型,因为粒子在烧制过程中是在回转窑内旋转滚动前进的,粒子之间还有相互挤压、剪切的作用,故骨料粒子基本无薄边和锋利的棱角,可有效控制骨料粒子的压碎比,且其表面为凹凸的草莓面状,可有效提高骨料与水泥的粘接力而提高混凝土的抗压值,经150x150x150标准试件试压,其抗压值完全达到c40、c50的标准。
25.制备原理为:利用滚动成型可以实现分段、分多层控制成型时的不同水份、湿度,不同的湿坯密度和干燥之后造成b区内有空隙,同时表面区即a3区的粉料,在滚动成型时,片状细粉是一层层错位叠加出来的,粉料的岩相结构以片状和针状为主,造成从b区和a1区排出的气体到1150℃后无法很快经过a2、a1区排出,而导致粒子内部为正压,同时因b区中缺少足够的氧
气,导致b区及a1区的部分固定碳要分二次反应,第一次c+o2→
co,第二次co+o2→
co2并释放大量热量,导致短时间内b区温度急升,最终内部的正压和熔融细粉在回转窑内自转和公转产生的离心力和表面张力的作用下,b区内的坯体液化后向外层渗透并与a1层产生各种物理化学反应,此时a3层已完全软化,加之不停的在回转窑内滚动、挤压及剪切力的作用,原毛细孔的通道基本封闭,最终形成内部正压,从粒子中心向外的推力和外部粒子之间的挤压和表面张力的作用下,实现粒子胀而不破、不裂的类似球体的空心结构,且其a3层相对致密,密度达2.7—3.0 g/cm
³
,只要a3层有足够的厚度比,即达到高强度骨料的要求(厚度比是指a3层厚度:粒子最大直径)。
26.在粒子成型最后阶段,单独加入电厂的炉膛渣,因其含al2o3高,单料无法烧结,在粒子表面附着一层少量的炉膛渣是为了在烧成温度到1200℃后,粒子坯体软化后在不停滚动过程中不让粒子之间出现大量的粘联,但此料应根据生产的实际情况及产量,炉内填料高度等而调整,过少则易出现粒子粘连严重而破坏了骨料的尺寸,过多则会造成水泥与粒子表面粘接强度的下降而降低混凝土的性能。
27.所述混凝土骨料由如下重量的组分组成:煤矸石:20-30份锂矿石尾渣:14-18份水磨长石水洗渣:8-12份花岗岩尾矿渣:8-12份污水压榨泥:7-11份钠长石:10-15份滑石泥:3-7份膨润土:4-8份炉膛渣:2-4份。
28.表1 各原料主要化学成份
其中,1#煤矸石:产地鄂尔多斯东胜区2#煤矸石:产地鄂尔多斯达拉特旗3#媒矸石:产地鄂尔多斯薛家湾以上所描述原料单个粉磨成细粉,要求细度达过250目筛余≤0.2%,1-8号料各磨200kg并在≤120℃烘箱中烘干,至含水≤0.3%。 9-11号料各磨60kg.相同的细度并烘干、其中10号料要封口,防止吸潮,待用。
29.本技术分级分段滚动成型再有机结合烧成制度和方法,制造出其本体密度平均为1.20—1.40 g/cm
³
,堆积密度为0.78—0.82 g/cm
³
的骨料,与传统石子骨料相比,相同体积时其重量仅为50%—52%左右。(石子骨料密度2.5 g/cm
³
)。
30.一种煤矸石烧结型高强度轻质混凝土骨料的制备方法:1.原料均化:因入厂原料均为固废级,其前后成份变化大,故原料入仓后必须做均化处理。每一次均化的量要大于45天的生产用量。
31.2.间隙式配料:为保证工艺配比和细粉在亚微观状态下混合均匀,每次自动控制的配料总量为1000kg—2000kg,水平搅拌机实现各种粉料宏观上的均匀,用锥式搅拌机实现微观上的均匀。注意,各原料干法混合均匀是保证骨料性质稳定的关键要求之一。
32.3.一级造粒:可选锅式或圆盘式造粒机,但设备的直径不能过大,宜控制在ф1300mm下,否则在第一级造粒时,其离心力过大后导致粒子的密度过大而导致最后粒子的空心比例不足,无法达到堆积密度的要求。
33.4.二级造粒:选用圆盘式造粒机,圆盘机的直径宜选择在ф1600mm内,同理,为控制粒子的离心力级,粒子b区和a2区的异性(不能同质化)结构,要控制b区的水分过多的被挤压到a2区。
34.5.三级造粒:选用连续式圆盘造粒机,其圆盘的直径宜选择为ф1600mm内,但设计转速可以提高。目的是快速成型的同时,保证a2层和a1层不同质化,并提高生产效率。
35.6.回转干燥窑粒子入干燥窑的平均水分约15%,且粒子在未干燥前其强度较低,故回转干燥窑设计时应遵循窑尾低温,窑内填料高度较小的原则,即干燥窑直径以小于φ2.4m为佳,长度根据产量要求可达60-90米。
36.7.烧成回转窑设计最高烧成温度为1350℃,实际烧成温度1250℃-1300℃,烧成周期40-90分钟。
37.并要求实现:
①
在窑尾的预热段(温度低于800℃段)助燃风及氧气的过氧量配置为0.98-1.02,目的是控制在800℃前,粒子表层(a3区)中的固定碳缓慢反应、燃烧。
38.②
在t2区的过氧量控制在1.02-1.05之间,(800℃-1150℃之间)。
39.③
在1200℃至最高温度区为弱氧化区,过氧量控制在1.04-1.08之间。
40.④
在高温保温区,过氧量控制在1.05-1.10之间。
41.8.在烧成骨料粒子进入缓冷回转窑中间设置急冷装置,并回收急冷放出的热风,可以用作助燃风和加热天然气至300℃-500℃的热源(设置热交换装置),可以有效降低能耗,减低高温烧成的能耗,同时极大地改善工作环境。
42.9.经过缓冷出窑后,分级过筛小于φ6.0mm为瓷粒砂,可作用混凝土中轻质细砂,也可用作其他行业。
43.10.对少部分粗骨料粒粘成团的处理设置φ800
×
1000的对辊机,最小间距为32mm,结团的粒子经过对辊后被剪切散开,注意对辊机设计为:不同步对辊(两个辊子的线速度不同)。
44.本发明经用标准试压件验证,完全可以达到c40、c50混凝土的要求,其密度只有普通混凝土的52%左右,可以预见在未来的建筑中有极大的发展空间。
45.虽然本发明需要高温烧制,需较高的能耗,产品的单一成本相对较高,但是经过从设计的改良,可节约大量的钢材,同时可降低建筑物的整体重量,其综合成本与普通混凝土的成本相差就不大了,特别是在高层及超高层建筑物中有不可替代的作用,故在以后的超高层建筑物中会被广泛接受。
46.同时,本发明所用原材料以固废为主,固废占比达80%以上,完全符合国家绿色建筑环保所鼓励的范畴,是绿色环保消减低品位煤矸石的新方向。
47.实施例2:一种煤矸石烧结型高强度轻质混凝土骨料的制备方法,第一步:骨料原料的配制1、按以下质量比例配料共60kg干料,表2 实施例2组分比例
原料1#矸石3#矸石锂矿渣水洗渣花岗石渣压榨泥钠长石滑石泥膨润土炉膛渣比例16%12%16%10%10%9%13%5%6%3%质量9.60kg7.20kg9.60kg6.0kg6.0kg5.40kg7.80kg3.00kg6.30kg1.80kg
2、将配制好的料同放入干粉搅拌筒中,搅拌15分钟后停机,再用人工的方式将搅拌桶底部和边、角的料铲起,混入主料中,再启动搅拌机10分钟,以保证搅拌料混合均匀。
48.3、配制含电解质的水溶液:配1.13%浓度水溶液称量9000g水,再称量103.5g三聚磷酸钠倒入水中,充分搅拌,要求三聚磷酸钠完全溶于水中,电解质水液总重量为9103.50g,再分出4600g水液放入第1个普通喷水壶中,剩余4503.5g水液倒入第2个喷雾壶中,待用。
49.第二步:用锅式造粒机滚动成型,具体如下:4、用锅式造粒机造粒,逐步加入上述准备好的粉料同时用喷壶加水,料:水≈5:1,至约有50%的粒子成型到约11—12mm左右停止喷壶加水,改而用喷雾方式加水,两者比例为料:水≈6:1(质量比),为适当提高粒子的强度,继续在锅式造粒机中滚动5—8分钟,此时成型的粒子增大成了约13—14mm,停机。
50.5、倒出第一次成型好的粒子,用5目筛筛出小于5目的粒子。
51.6、大于5目的粒子放入圆盘式造粒机中继续滚动,缓慢加入粉料,按约料:水≈9:1的质量份缓慢加入,直至粒子成长到14—16mm左右时停止加料和水,圆盘机继续转动约10—20分钟,取粒子观察表面无小裂纹,不易掉皮时再用喷雾壶喷很薄的水在粒子表面,并加入200—400g上述准备好的炉膛渣,继续滚动约2—3分钟,看到粒子表面有一层很薄的白色粉即可(粒子为深灰色),此时所备9103.5g的水基本也用完。
52.7、放出全部粒子,称重。
53.粒子的重量:58.50kg小于5目的粒子:9.87kg剩于未加水:10g8、把成型好的粒子放入15个不锈钢盘中置于两个烘箱烘干,烘箱恒温120℃,烘10小时,测粒子含水量。小于0.3%为合格,并继续置于烘箱内恒温120℃。
54.第三步:烧成
烧成曲线的合理设定是产出预定粒子的关键环节,故各环节必须严格控制。
55.a.启动回转窑并升温,如图2,开中火。
56.设定转数0.6转/分钟,倾角:1
°
b.至t3温度升到1000℃时,开始快速加入约30kg粒子,由于粒子的快速吸热,需通过调节各参数使t1温度降到≤300℃,否则大量粒子因受热太快而产生裂纹,影响粒子的质量及抗压指数。
57.c.温度达到300℃左右时,开始以约2kg/分钟的速度加入全部作好的粒子。
58.d.同时加大烧咀的燃气量,让t3快速升至1250℃,并控制助燃风量,过氧量控制在1.05—1.08之间,(通过观察窑内清晰度和火焰颜色可以判段过氧量的大小),即在t2以前是弱还原气氛,接近t3温度时才能转为氧化气氛烧成,这是控制的一个关键点。
59.e.最高烧成温度1250℃,保温12—15分钟(设定燃烧气的火焰长度及窑体转速实现)。
60.f.从烧成回转窑头流出的粒子通过网状导流环自动滚入缓冷器中(回转冷却器一部分)在导环两侧用轴流风扇错位对吹粒子。尽量控制在过导流环上把粒子表面温度从1250℃降到700℃左右(手持红外仪侧)然后进入缓冷回转器,慢速冷却。降温速度控制在5~8℃/分钟,到低于350℃后吹冷风直冷。
61.烧成时间:入窑至出窑.周期为60分钟。
62.g.待全部料出完,分段收集第一时间出来约10分钟的粒子单独放入1#不锈钢大盆,中间出来较完整的粒子放入2#大盆中,最后10分钟出来的粒子放入3#大盆中。
63.h.三个盆中的粒子分别称重后过5目筛1#盆﹤5目占比14.9﹪(质量比)2#盆﹤5目占比7.8﹪(质量比)3#盆﹤5目占比21.3﹪(质量比)i:用5倍放大镜肉眼观测粒子的情况。
64.1#盆:表面裂纹较多,不合格比例高,不再测试其性能。
65.2#盆:粒子完整,基本无爆裂,裂纹少。
66.发胀程度基本符合预期.10mm至28mm粒子。
67.形状为椭圆形、苹果型、草莓型状。
68.直经约15mm左右的多边型,符合预期。
69.3#盆:粒子约占50%.片状约占30%.小于8mm占的20%,用5目筛选并分离出片状.j:测试粒子的吸水率:
①
用5倍放大镜逐一观察从8m~25mm每个粒子.表面不见裂纹的粒子为合格,共10kg.
②
取1000g上述挑选的8~25m的粒子,用常用的红墨水,按红墨水:水=1:2质量份数调300g红水,搅拌均匀后置入不锈钢盆中并把1000g粒子倒入红水中,翻搅粒子,让红水充分浸蚀到粒子表面,时间1分钟。
70.③
把浸红水的粒子全部倒进φ300不锈钢筛(16目)中,用自来水反复冲洗粒子.逐
粒观测有无连续红线和长度大于5mm的红线(红线说明是有裂纹)。
71.结果:经冲洗后,粒子表面红色基本已冲洗掉,凹陷边缘有红色属正常。仅有6个粒子有连续红线,再把此6个粒子按红线的垂直方向切开。切断面内部无红墨水印,说明水溶液没有渗入粒子空心部位,可以判定合格。
72.④
另取1000g粒子.在清水中浸泡24小时,用棉布擦拭测粒子的吸水率:1.83%,用风筒冷风吹表面再测:1.15%,另取1000g粒子,在清水中浸泡48小时,用棉布擦拭测粒子的吸水率:2.13%。用风筒冷风快吹表面再测:1.56%。
73.说明:测吸水率的方法只能用浸泡法,而不能用国标的真空法,因为粒子为空心结构,真空法会导致一部分水进入粒子空心内而失去意义。
74.结论:虽然浸泡48小时的吸水率稍偏高,但粒子表面为菠萝面或草莓面,表面有的凹凸在凹线位,会有很多残留水,故粒子实际吸水率达到设计要求。
75.⑤
用骨料干粒子自然堆积方式,分别测3次堆积密度,平均值为:793.1 kg/cm
³
。
76.k:制成混凝土标准试件测抗压值
①
c40混凝土标准试件150x150x150立方体,制作2个标准试压体。
77.水泥::4000g水:1600g天然石英砂:4900g骨料粒子:6530g减水剂:40g
②
对标准件作好全程养护。
78.③
28天后取出标准件,软毛刷扫去边角毛刺,测重:1#件:重量为:6032g、密度为:1.78 g/cm
³
2#件重量为:6073g、密度为:1.80 g/cm
³
平均值为1.79 g/cm
³
而常规c40混凝土的密度按2.43 g/cm
³
计算得密度是常规混凝土的 =74.4%
④
1#件:抗压值48.7 mpa2#件:抗压值49.3mpa两件试压平均值为:49.0mpa,完合符合c40混凝土标准的要求。
79.结论:利用本发明的粒子做粗骨料,混凝土的密度是常规的74.4%,虽然明显的降低,但仍比目标值偏高,主要原因是混凝土配比中用了天然石英砂,故提高了试件的密度。将在以下的实施案例中,将天然砂改为用本发明的生产工艺制成的瓷粒砂替代。
80.分析实施案例:一、全过程出现的不足及试压标准件密度与预设的密度偏高的问题作出分析,以便在以后的实施案例中校正,得出最优选的方案。
81.a:在制备配方的料总质量偏少,导致做成的粒子骨料偏少,在进行烧结时回转窑有效调节时间偏短、有效烧成的时间偏少成品率偏低。
82.b:用天然砂后,试件的密度仍偏高,高于预设的1.60g/cm
³
。
83.实施例3:
一种煤矸石烧结型高强度轻质混凝土骨料的制备方法,第一步1.按以下质量比例配料60公斤,分三次配料,共180kg.表3 实施例3组分比例
原料ꢀ1#矸石3#矸石锂矿渣水洗渣花岗石渣压榨泥钠长石滑石泥膨润土炉膛渣比例16%12%16%10%10%9%13%5%6%3%质量28.8kg21.6kg28.8kg18.0kg18.0kg16.2kg23.4kg9.0kg18.9kg5.4kg
2.把每次配制好的料单独放入搅拌桶中。搅拌15分钟暂停,用人工把搅拌桶边、角的料铲起,混入主料中,再启动搅拌10分钟,保证混料均匀。
84.3.配制电解质水溶液.1.35%浓度水溶液称自来水:30kg.称三聚磷酸钠:410g.倒入30kg水中,充分搅拌,保证三聚磷酸钠完全溶解后,加满喷水壶和喷雾壶.待用。
85.第二步:成型1.用锅式造粒机滚动成型造粒.具体如下:2.每次先加入6kg备好的粉料,启动造粒机旋转,用喷壶加水的同时,逐渐加入粉料,最终要保证料:水≈5:1至约有50%的粒子成型到11—12mm左右时停止喷水改而用喷雾壶喷水,尽量保证比例:料:水≈6:1(质量比).继续滚动5-8分钟,便80%左右的粒子直径增大到13—14mm,停机,到处全部粒子。
86.3.用5目筛过筛,分离出小于5目的粒子,小粒子倒回锅式造粒机中。
87.4.大于5目的粒子全部倒入已启动圆盘造粒机中(发现有半圆和扁形的少量粒子)缓慢加入粉料,按料:水≈9:1的质量份同时喷雾加水,直至粒子长到14—16mm时,停止加料、加水,圆盘机继续旋转15—20分钟,取大粒子.用手指试压,不易压裂为基准,合格后停机,取出圆盘机全部半成品,并过5目筛后再把大粒子放入圆盘机中,启动.加入适量白色炉膛中,喷雾加水约2—3分钟,粒子表面有一很薄的白色粉即可。(粒子为深灰色)如此反复制料,直至制完配好的180kg干料。
88.5.因制得粒子较多,把制得合格的粒子倒在干净铺有瓷砖的室内地面上自然干燥,注意堆积高度不要大于60mm。
89.6.把成型好的粒子分批次置入120℃恒温干燥箱中干燥,保证大粒子含水率≤0.3%为合格,并全部干燥好。
90.第三步:烧成a.启动回转窑升温,升温至1000℃时,b.取调节好含水约15—16%的炉膛渣粗渣200kg,并以约10kg/分钟的量开始匀速加入窑中。(目的量调整t1.t2温度)c.炉膛渣加入完毕后即加入已制好的粒子,约5kg/分钟匀速加入粒子,全部加完制好约175kg粒子。
91.d.回转窑调整参数:转速0.6转/分钟t3:温度保持在1250℃
±
3℃
e.烧成粒子烧结后自动进入导环,用2台风扇吹冷风,并冷却到680℃
±
10℃为控制范围(红外线测温仪测量)。
92.f.缓冷回转器转速:2.1转/分钟出缓冷器粒子温度以小于150℃为原则,即制得轻质骨料。
93.g.待粒子自然冷却至常温后,在成品堆里任意取约20kg。
94.第四步:测试
①
用5倍放大镜观测粒子表面有无破裂情况,25mm左右粒子表面有无裂纹、空洞,并逐粒挑选,把不合格的归一盆内。
95.②
用卡尺测粒子的最大尺寸:从9mm—28mm粒子大小基本为连续,符合预期。
96.③
测试粒子的表面吸水性,同时判断表面层烧结程度即瓷化程度。
97.用红墨水:水=1:1(质量比)共200g,取约50粒完好的骨料,充分浸湿表面,后用清水冲洗,平整及凸出部分看有无明显红印渍。
98.④
测骨料粒子的平均吸水率:a.取2000g10—28mm骨料粒子,在清水中浸泡24小时后用棉布擦拭,再用风筒,开冷风吹去凹陷处的吸附水,等附着在粒子表面的水份。
99.测得吸水率为:1.18%b.另取2000g10—28mm骨料粒子,清水中浸泡48小时用同样的方法去附着水。
100.测得吸水率为:1.54%h.骨料粒子结构分析从上述
③
、
④
测试的骨料粒子中各挑出12mm、15mm、20mm、25mm、28mm直径的粒子各3个,从中心位切开观察粒子的空心结构(切割时不能用水)其中b区:空心区a1层:冰棱状晶体,深灰色,对粒子抗压强度基本没有贡献,用锥形磨头磨去a1层的冰棱状,可见属过烧状态的部分为结晶体,部分为玻璃体的混合体。
101.a2层:浅灰色,约50%的断面(靠中心)多针孔,靠外侧的约50%断面颜色逐渐变白,针孔相对较少。
102.a3区断面:白色,很少针孔,瓷化程度好。
103.i.测粒子的堆积密度,用300mm的立方体箱。
104.瓷粒砂:φ3.0~φ8.0,分别测 3次,平均值为:860kg/cm3骨料:φ8.0~φ28.5,分别测 3次,平均值为:800.2kg/cm3g.另取50g粒子φ25~φ28mm骨料粒子,测量其最小壁厚并分析极端粒子的比例及危害性。测量部位如图3所示。
105.以上三种对抗压值影响最大其最小壁厚dmin的大小直接影响抗压破坏值,因此要控制其比例(粒子数量比),50粒中有4粒,其dmin值分别是2.2mm、2.4mm、2.5mm、3.1mm(大于φ25的粒子要求壁厚在4.0mm以上)占比为8%。
106.g:测堆积密度:第五步:制c40标准试压件15cm
×
15cm
×
15cm
①
42.5r水泥:4000g水:1600g天然砂:4900g骨料粒:6530g减水剂:45g按国标方法进行养护,28天后,测平均密度:1.80g/cm3,抗压密度:49.2mpa。
107.②
42.5r水泥:4100g水:1650g瓷粒砂:3630g(在上述烧制出来的3.0—8.0mm之间的小粒子)骨料粒:6530g减水剂:45g按国标法全程养护:28天后测平均密度:1.42g/cm3平均抗压值:47.3mpa标准件完全达到国家标准要求,说明骨料的抗压指数完全可以满足c40混凝土的要求,其在试件
②
中加入的瓷粒砂,有效降低了混凝土的密度,且其强度基本与天然砂的值接近,说明瓷粒砂和骨料粒子同时取代天然砂和石子骨料是完全可行的。
108.本实施例中,在第一道锅式造粒时,吸水多的粒子含水太高,导致倒出后挤压变形成扁形,也有因含水少,倒出后有破裂成两个或多个粒子.这些破碎的粒子其外形不规格,导致粒子最后定型后,其b区为不规则的多面体或有尖角,导致烧结后出现dmin有2.2mm的不合格品。
109.实施例4:一种煤矸石烧结型高强度轻质混凝土骨料的制备方法,第一步:1、按以下质量比例配料60kg干料表4实施例4组分比例 原料ꢀ1#矸石3#矸石锂矿渣水洗渣花岗石渣压榨泥钠长石滑石泥膨润土炉膛渣比例16%12%16%10%10%9%13%5%6%3%质量9.60kg7.20kg9.60kg6.0kg6.0kg5.40kg7.80kg3.00kg6.30kg1.80kg
2、将配制好的料放入干粉搅拌机中搅拌15分钟,停机后手工铲出边、角上难搅到的部位,再搅拌10分钟,混料一定要均匀。
110.3、配制电解质水溶液,浓度1.35%称9000g水,再称123g三聚磷酸钠放入水中,充分搅拌,三聚磷酸钠完全溶于水中。
111.4、把喷水壶的喷水口改为单排并加入约4600g水溶液,把剩余4523g水倒入喷雾壶中。
112.第二步:滚动成型(分三个阶段)1、在锅式造粒机先加入约5kg粉料,启动造粒机转动。
113.2、按料:比≈5:1的质量比例缓慢加入料和水,至有50%粒子成型到约11—12mm左右停止喷壶加水,而改用喷雾加水方式,两者比例料:比≈7:1(质量比)至粒子滚动长大到
一、配制2件c40标准块(150*150*150mm)42.5r水泥:4100g.水:1700g瓷粒砂:3600g. (φ3.0~φ8.0粒子)骨料粒子:6500g. (φ10~φ28.5)减水剂:45g.按同样方法养护28天后测得:平均密度:1.44g/cm3平均抗压强度:47.6mpa二、配制2件c50标准件r52.5r水泥:4200g.水:1720g瓷粒砂:4600g.骨料粒子:5200g.减水剂:45g.按国标方法养护28天,测抗压值平均值为:54.6mpa.完全符合c50混凝土的标准要求。
126.从试压标准件的裂开的断面分析,瓷粒砂没有从中间断开,骨料有一粒从中间断开。其最小壁厚为3.72mm。
127.实施例5:一种煤矸石烧结型高强度轻质混凝土骨料的制备方法,第一步:骨料原料的配置1.按以下质量比例配料共60kg干料表5 实施例5组分比例
原料2#矸石3#矸石锂铲渣水洗渣花岗石渣压榨泥钠长石滑石泥膨润土炉膛渣比例17%12.5%17%10%9%8%13.5%5%6%2%质量10.20kg7.50kg10.20kg6.00kg7.20kg4.80kg8.10kg3.0kg3.6kg1.20kg
2.将配置好的粉料放入干粉搅拌机中,搅拌15分钟,用人工的方式将搅拌桶的底部和边、角的料铲起并混入料中,再开动搅拌机10分钟,保证粉料的混合均匀。
128.3.配置电解质水溶液:浓度:1.35%称9000g水,123g三聚磷酸钠内放入水中。
129.充分搅拌,保证三聚磷酸钠完全溶于水中。
130.第二步:滚动成型(分三个阶段)1、在锅式造粒机先加入约5kg粉料,启动造粒机转动。
131.2、按料:比≈5:1的质量比例缓慢加入料和水,至有50%粒子成型到约11—12mm左右停止喷壶加水,而改用喷雾加水方式,两者比例料:比≈7:1(质量比)至粒子滚动长大到13—14mm时停机。
132.3、把锅式造粒机中的全部料倒出,过8目筛之后放回锅式造粒机中转动8分钟。
133.4、从锅式造粒机中取出全部成型好的料子放入圆盘造粒机中,启动圆盘机,按料:比≈8:1的质量比继续加入,直至粒子有50%左右直径达15—16mm,此时停止加料和水,并继续转动约15分钟,取粒子观测,表面无裂纹及不易掉渣为合格。
134.5、再加入已制好的炉膛渣粉约200—400g并喷入少量水,主要白色的炉膛渣能较紧地贴附在粒子表面即可,白色的粉不能加太多,否则会影响以后的性能,继续转动3分钟停止。
135.如此,三个周期,直至把配置好的60kg干粉全部成型好(第一次8目筛过出半的细粉及小颗粒回到锅式造粒机中当成核剂使用)第三步:烧制骨料粒子1、把制好的全部料(包括小于5mm的粒子和少量细粉)全部在120℃恒温干燥箱中干燥10小时。
136.2、准备好含水约15%的大于8目的炉膛渣约200kg,作调节回转窑参数的预烧料。
137.3、当回转窑t3达1000℃时,开始以6kg/min的速度加入炉膛渣直至t1温度为350
±
10℃时,开始以3kg/min的速度加入已制好的粒子,此时加大燃烧强度,开始控制好助燃风量,使t1全段、t2前半段为弱还原气氛。直至制好的57kg粒子全部进入回转窑内(在粒子转动到t2时,t3升到1250℃)并继续以约4kg/min加入炉膛渣约5分钟。
138.4、回转窑开始出白色炉膛渣时,启动轴流风扇直吹,把骨料粒子的表面温度降至700℃左右。
139.检测骨料粒子和瓷粒砂的性能:1、烧制好的骨料粒子冷却至常温后,对其进行分选、检测
①
用10倍放大镜观测表面破损、破壳、裂纹情况。
140.共测20kg(从8.0~28mm连续颗粒)测得不良率:2.67%
②
用红墨水试骨料粒子表面吸水性。用之前相同的方法,冲洗后无明显的红斑。
141.③
浸泡法测骨料和瓷粒砂的吸水性骨料:浸泡24小时,吸水率为1.17%浸泡48小时,吸水率为1.43%瓷粒砂:浸泡24小时,吸水率为0.73%浸泡48小时,吸水率为0.92%2、取φ15~φ28.5mm骨料共100粒,以每粒最大尺寸为切割线,对切开,观测其最小壁厚,并找出其空心结构为极端异型的粒子,有3个粒子不合格,不合格率为3.0%3、测骨料和瓷粒砂的体积密度和堆积密度。
142.a.用2000ml量筒和加水分体积的方法。共测5次,取平均值,测得骨料体积密度为1.33g/cm3瓷粒砂体积密度为1.52g/cm3b.用300
×
300
×
300mm立方体测堆积密度,每种料共测3次。
143.测得骨料堆积密度为:810kg/cm3
瓷粒砂堆积密度为:930kg/cm34、标准混凝土试压件的配制:
①
c40标准混凝土试压件制作,制2件42.5r水泥4100g水:1700g瓷粒砂:3400g(φ3.0~φ8.0小粒子)骨料粒:6300g(φ10~φ28.5粗粒子)减水剂:45g养护28天:测得平均密度:1.46g/cm3平均抗压强度:47.7mpa
②
c50标准混凝土试压件,配制2件52.5r水泥:4200g水:1720g瓷粒砂:4700g(φ3.0~φ8.0)骨料粒:5200g(φ10.0~φ28.5)减水剂:45g养护28天:测得平均密度:1.48g/cm3平均抗压强度:55.1mpa结论:试制出的骨料和瓷粒砂完全满足c50混凝土的要求。
144.实施例6:一种煤矸石烧结型高强度轻质混凝土骨料的制备方法,第一步:原料的配制1、按以下质量比例配料工60kg干料表6 实施例6组分比例
原料1#矸石2#矸石锂铲渣水洗渣花岗石渣压榨泥钠长石滑石泥膨润土炉膛渣比例14%13%15%12%9%9%10%7%7%4%质量10.20kg7.50kg10.20kg6.00kg7.20kg4.80kg8.10kg3.0kg3.6kg1.20kg
2.将配制好的料同干粉混料搅拌均匀,方法同上述实施例的过程。
145.3、配置三聚磷酸钠溶液:浓度1.35%质量分数:水:三聚磷酸钠=9000g:123g混匀,完全溶解于水,待用第二步:锅式造粒机滚动成型1、在锅式造粒机先加入约5kg粉料,启动造粒机转动。
146.2、按料:比≈5:1的质量比例缓慢加入料和水,至有50%粒子成型到约11—12mm左右停止喷壶加水,而改用喷雾加水方式,两者比例料:比≈7:1(质量比)至粒子滚动长大到13—14mm时停机。
147.3、把锅式造粒机中的全部料倒出,过8目筛之后放回锅式造粒机中转动8分钟。
148.4、从锅式造粒机中取出全部成型好的料子放入圆盘造粒机中,启动圆盘机,按料:
比≈9:1的质量比继续加入,直至粒子有50%左右直径达15—16mm,此时停止加料和水,并继续转动约15分钟,取粒子观测,表面无裂纹及不易掉渣为合格。
149.5、再加入已制好的炉膛渣粉约200—400g并喷入少量水,主要白色的炉膛渣能较紧地贴附在粒子表面即可,白色的粉不能加太多,否则会影响以后的性能,继续转动3分钟停止。
150.第三步:烧制骨料粒子1、把制好的全部料(包括小于5mm的粒子和少量细粉)全部在120℃恒温干燥箱中干燥10小时。
151.2、准备含水约15%的较粗的炉膛渣200kg作烧制时调节回转窑参数的预烧料。
152.3、当回转窑t3温度达到1000℃时,开始以6kg/分钟的速度加入炉膛渣直到t2温度为350土10℃时开始以3kg/分钟的速度加入已制好的粒子,此时适量加大燃烧强度,并控制好助燃用量。加完所有粒子,在粒子转动前进到t2(120℃土10℃)时一t3升到1270℃直至所有粒子烧成出回转窑。
153.4、回转窑开始出白色炉膛渣时,启动轴流风扇直吹,把骨料粒子的表面温度降至700℃左右。
154.检测粒子的性能:1、用5倍放大镜观测表面破损、破壳、裂纹情况共测20kg最大粒子为31.7%测得不率为3.47%2、用红墨水试骨料粒子表面吸水性冲洗后基本无明显红印3、浸泡法测粒子的吸水率a. φ3.0—φ8.0mm小粒子浸泡24小时.测吸水率为:0.87%浸泡48小时.测吸水率为:1.08%b.10—31.7mm粗粒子浸泡24小时.测吸水率为:0.98%浸泡48小时.测吸水率为:1.15%4、测瓷粒砂的压碎值取3.0—8.0mm粒子,用同标法测量三次:用150压碎值测试仪,加压至400kg平均压碎值≈14.3%(国标为≤20%)说明:制出的瓷粒砂完全可以取代天然石英砂。
155.5、抽查骨料粒子的极端情况以最大的尺寸为切割线,对切开,测量其最小壁厚,而危害最大的属c型粒子,测其长边长度:lmax:l≤0.25lmax:最薄壁长度l:最大截面周长
不合格骨料粒子:6.3%6、测试堆积密度和配制标准块骨料堆积密度,3次平均值:890kg/cm3瓷粒砂堆积密度,3次平均值:970kg/cm3(1)配制两件c40标准块(150
×
150
×
150mm)42.5r水ф/r:4100g水:1680g瓷粒砂(ф3.0~ф8.0mm):3500g骨料粒(ф10.0~ф31.70mm):6100g减水剂:45g测得c40标准块:平均密度:1.47g/cm3平均抗压强度:44.6mpa(2)配制两件c50标准块52.5r水泥:4200g水:1690g瓷粒砂:4900g骨料粒:5000g减水剂:45g养护28天测得平均密度:1.44g/cm3平均抗压强度:52.3mpa本技术中:1.骨料配方的要点a.坯体配方中固定碳的比例要满足既要膨胀又不能过多后燃烧排气大而导致粒子爆裂、破裂。
156.b.有较高的al2o3含量,坯体烧结反应后形成以莫来石晶型为主的胎体。
157.c.控制原料成份中cao的含量,否则易形成钙长石,最后在粒子部分表面形成很薄的类似鸡蛋壳的壳,严重影响粒子的抗压性能。
158.2、粒子成型的节点机理:a.b区要有较大的水份,16%~21%,滚动成核即可,否则b区的坯体太致密后导致空心比例不足,而提高了粒子的体积密度。同时a2区为过渡区,其成型的水份和密度要控制在a1和b区之间。过松疏则粒子易破损,过致密则在高温软化前后,氧气难以供给到a2区内层及b区,也会出现膨胀不够和b区固定碳燃烧不完全而影响骨料粒子的综合性能。
159.b.另一方面,在烧成温度达1150℃左右,坯体a3层由外向中心逐步软化。要控制b区内的固定碳的反应只能50%左右,必须是在a3层全部软化完成后才能完全反应燃烧,形成b区内短时间过烧产生液相并渗入a2区产生物理化学反应。
160.c.控制a1层的厚度:因为a1层占用了粒子的空间和体积,但对粒子的抗压强度基本没有贡献。所以a1层愈小,骨料粒子的综合性能就愈容易提高。
161.3.烧成温度的要求:设定并实现合理的烧成制度及冷却制度是控制骨料粒子的第三部分,坯体的软化温度及区域控制、助燃风量的控制来调控粒子的a2和a1区域的固定碳的反应和燃烧速率,是控制a3层的厚度及b区空心区域的直径均相互关联。
162.4.急冷制度:为提高生产效率及骨料粒子的性能,粒子经1250—1270℃烧成后快速降低粒子温度到680℃左右是一个重要的节点。
163.5.最高烧成温度:本发明在坯体的成份设计时,充分利用煤矸石含al2o3较高的特点,让坯的烧结温度在1250—1270℃左右,是为了减少骨料粒子中玻璃相,而多以莫来石为主的晶相,提高粒子的综合力学性能,及抗压和抗冲击强度。
164.6.骨料粒子的型状骨料粒子的接近球形、苹果型、多边型、草莓型为主,占比≥95%,是在成型的混凝土中,充分利用球型和圆锥型、半圆型的力学特点,骨料粒子四周填充有水泥砂浆并固化后,其受力沿骨料圆弧向四周传递,故本发明没有单独测试粗骨料粒子的抗压碎值,只测试了瓷粒砂的压碎值的原因。
165.7.粒子的表面特征:粗骨料粒子和小粒子的瓷粒砂,其表面都类似草莓颗粒表面,是让粒子和水泥浆有较大的粘接表面和粘接力,从而提高混凝土的抗压强度,当然地需适当提高c40、c50中水泥的用量比例。
166.8.瓷粒砂:在连续大生产过程中,三级造粒成型的连续过程中,必然都会产生ф2.0—ф5.0mm的粒子。小粒子没有形成较明显的三层结构,而是形成了基本同质化的结构。加之其直径小,中心受热快,故在烧成过程中,难以形成明显的空心结构而只能形成中心区较疏松、外层较致密的瓷化层,故其堆积密度相对较大,但仍比天然石英砂小,故配合粗骨料仍是制作高强度、低密度混凝土的关键材料。
167.上述实施例只是为了说明本发明的技术构思及特点,其目的是在于让本领域内的普通技术人员能够了解本发明的内容并据以实施,并不能以此限制本发明的保护范围。凡是根据本发明内容的实质所做出的等效的变化或修饰,都应涵盖在本发明的保护范围内。