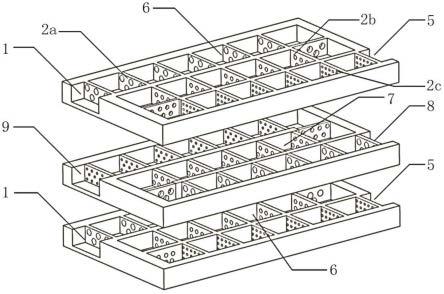
1.本实用新型属于燃料电池重整制氢技术领域,特别是涉及一种变催化剂粒径的填充床式重整制氢反应器。
背景技术:2.燃料电池具有能量转换效率高、噪音低等巨大优势。常见的燃料电池种类有碱性燃料电池、质子交换膜燃料电池、熔融碳酸盐燃料电池、固体氧化物燃料电池等。其中质子交换膜燃料电池工作温度低、可快速启动而且比功率、比能量密度大,是一种极具优势的燃料电池。
3.燃料电池需要用到可靠的供氢系统,传统的供氢方式为储氢罐供氢,但这种方式不仅能量密度低而且在质量、安全上也存在明显的不足。因此,目前,使用碳氢化合物重整制备氢有望成为解决这一问题的有效措施。典型的碳氢化合物重整反应制氢可分为三种:水蒸气重整、部分氧化重整和自热重整,其中水蒸气重整制氢可以得到较高纯度的氢气,而且可以在一定程度上抑制结焦现象的发生,是目前的一个研究热点,但该反应是吸热反应,需要外部热源。
4.对于催化剂的担载方式,目前应用较多的为微流道壁覆盖式、多孔纤维毡/泡沫金属式、填充床式等。但是微流道壁覆盖式,催化效果较差;多孔纤维毡/泡沫金属式,技术尚不成熟;填充床式是目前应用最为广泛,技术最为成熟的一种方式,具有很高的反应效率,但在流动过程中压降较大,且化学反应集中于反应器的入口,导致壁面温度分布不均,造成了催化剂的浪费。同时,传统的填充床式反应为多为固定式填充床重整器,对于移动式设备例如燃料电池车等,会因为设备的移动导致重整器内部的催化剂产生较大的位移,从而导致催化剂分布不均,重整效率较低。
5.除了供氢方面的问题外,燃料电池虽然清洁环保,但是燃料的利用率不是很高,因此会浪费掉部分高热值的氢气,其次,燃料电池尾气中可燃成分含量低,无法直接燃烧,采用催化燃烧进行尾气处理是一种正在蓬勃发展的技术。
6.因此,如何提供一种对燃料电池尾气进行充分利用,且重整反应和催化燃烧过程中壁面受热均匀、气体流动阻力小、催化剂性能稳定、转化率高、适用于移动设备的填充床式重整器是本领域技术人员亟需解决的问题。
技术实现要素:7.有鉴于此,本实用新型旨在提出一种变催化剂粒径的填充床式重整制氢反应器,以解决现有填充床式重整制氢反应器燃料电池尾气无法充分利用,重整反应和催化燃烧过程中壁面受热不均匀、气体流动阻力大、催化剂性能不稳定、转化率低、无法适用于移动设备的问题。
8.为实现上述目的,本实用新型采用以下技术方案:一种变催化剂粒径的填充床式重整制氢反应器,它包括两个催化燃烧腔和重整腔,所述两个催化燃烧腔对称布置在重整
腔的上下两侧,所述催化燃烧腔和重整腔内均设置有蛇形通道,所述蛇形通道内填充有催化剂,所述蛇形通道内催化剂沿反应流体的流动方向粒径逐渐减小,所述催化燃烧腔上开设有催化燃烧腔入口和催化燃烧腔出口,所述重整腔上开设有重整腔入口和重整腔出口,所述催化燃烧腔和重整腔为逆向流动布置。
9.更进一步的,所述蛇形通道内通过若干个多孔隔板均匀隔开,多孔隔板内放置不同大小的催化剂。
10.更进一步的,所述多孔隔板的孔径小于催化剂粒径。
11.更进一步的,所述多孔隔板包括大孔径隔板、中孔径隔板和小孔径隔板,所述大孔径隔板、中孔径隔板和小孔径隔板沿反应流体的流动方向依次均匀布置。
12.更进一步的,所述大孔径隔板、中孔径隔板和小孔径隔板均为铝制隔板。
13.更进一步的,所述催化剂包括大粒径催化剂、中粒径催化剂和小粒径催化剂,所述大粒径催化剂设置在大孔径隔板分隔区域内,所述中粒径催化剂设置在中孔径隔板分隔区域内,所述小粒径催化剂设置在小孔径隔板分隔区域内。
14.更进一步的,所述催化燃烧腔入口和催化燃烧腔出口分别与催化燃烧腔内蛇形通道的两端连通。
15.更进一步的,所述重整腔入口和重整腔出口分别与重整腔内蛇形通道的两端连通。
16.更进一步的,所述催化燃烧腔入口与燃料电池尾气通道相连。
17.更进一步的,所述重整腔入口与蒸发段通道相连。
18.本实用新型还提供了一种变催化剂粒径的填充床式重整制氢反应器的反应方法,它包括以下步骤:
19.步骤1:燃料电池尾气通过催化燃烧腔入口进入催化燃烧腔,液体燃料蒸发后通过重整腔入口进入重整腔,催化燃烧腔和重整腔内进行催化反应;
20.步骤2:随着反应气的流动,依次通过大粒径催化剂、中粒径催化剂和小粒径催化剂,燃料在重整腔内发生水蒸气重整反应,尾气在催化燃烧腔内发生燃烧反应,提供反应所需热量;
21.步骤3:最终重整气通过重整腔出口流出,反应后的尾气通过催化燃烧腔出口流出。
22.与现有技术相比,本实用新型的有益效果是:
23.本实用新型从上至下依次层叠布置的催化燃烧腔、重整腔和催化燃烧腔;所述重整腔和所述催化燃烧腔内部均为蛇形通道,内部填充有助于反应进行的催化剂,同时沿着反应流体的流动方向,催化剂的粒径逐渐变小,流道由多孔隔板均匀隔开,分段放置不同粒径大小的催化剂;所述重整腔入口通过气态燃料通道连接至蒸发段。本实用新型的重整反应器集尾气催化燃烧、重整制氢于一体,壁面受热均匀,催化反应充分,气体流动阻力小,反应器的催化性能稳定,可以使得转化效率进一步提高。
24.本实用新型提供的一种变催化剂粒径的填充床式重整制氢反应器,将尾气进行催化燃烧,为重整反应提供热量,同时在蛇形反应通道内设置有多孔隔板,减少催化剂在设备运动过程中的位移,使催化性能稳定,转化率进一步提高。
25.本实用新型采用催化燃烧腔-重整腔-催化燃烧腔的方式上中下层叠布置,回收燃
料电池的尾气进行催化燃烧,为重整反应提供热量,避免了氢气的浪费,同时解决了重整反应吸热的问题,重整腔的反应通道壁面受热更加均匀,减少了温度分布差异对反应带来的影响,反应更加稳定。
26.本实用新型采用变催化剂粒径的分段式填充,利用蛇形通道增加反应流程,通过填充床式的重整器进一步提高反应时间,同时将不同粒径尺寸的催化剂固定在蛇形通道内的多孔隔板之间,且多孔隔板的孔径小于两侧催化剂的粒径尺寸,有效减少了催化剂的位移,使填充床式重整器可有效用于多种场合,例如燃料电池飞机等。减小气体流动阻力,使催化性能更加稳定,同时多孔隔板采用铝材,具有很强的导热性,增强了蛇形通道内的传热,使反应腔内的温度更加均匀,提高反应效率。同时,采用隔板的分段式填充,更易实现,更易实现工程应用。
27.本实用新型采用变催化剂粒径布置的方式,随着反应气体的流动,反应气浓度越来越低,而反应气与催化剂的接触面积越来越大,可以有效降低压力损失,减小压降,同时提高反应效率,减少催化剂用量,提高反应器的经济性。
附图说明
28.构成本实用新型的一部分的附图用来提供对本实用新型的进一步理解,本实用新型的示意性实施例及其说明用于解释本实用新型,并不构成对本实用新型的不当限定。在附图中:
29.图1为本实用新型所述的一种变催化剂粒径的填充床式重整制氢反应器分体结构示意图;
30.图2为本实用新型所述的催化燃烧腔结构示意图;
31.图3为本实用新型所述的催化燃烧腔内部流体流动平面示意图;
32.图4为本实用新型所述的大粒径催化剂排布结构示意图;
33.图5为本实用新型所述的中粒径催化剂排布结构示意图;
34.图6为本实用新型所述的小粒径催化剂排布结构示意图。
35.1-催化燃烧腔入口,2a-大孔径隔板,2b-中孔径隔板,2c-小孔径隔板,3a-大粒径催化剂,3b-中粒径催化剂,3c-小粒径催化剂,4-蛇形通道,5-催化燃烧腔出口,6-催化燃烧腔,7-重整腔,8-重整腔入口,9-重整腔出口。
具体实施方式
36.下面将结合本实用新型实施例中的附图,对本实用新型实施例中的技术方案进行清楚、完整地阐述。需要说明的是,在不冲突的情况下,本实用新型中的实施例及实施例中的特征可以相互组合,所描述的实施例仅仅是本实用新型一部分实施例,而不是全部的实施例。
37.参见图1-6说明本实施方式,一种变催化剂粒径的填充床式重整制氢反应器,它包括两个催化燃烧腔6和重整腔7,所述两个催化燃烧腔6对称布置在重整腔7的上下两侧,所述催化燃烧腔6和重整腔7内均设置有蛇形通道4,所述蛇形通道4内填充有催化剂,所述蛇形通道4内催化剂沿反应流体的流动方向粒径逐渐减小,所述催化燃烧腔6上开设有催化燃烧腔入口1和催化燃烧腔出口5,所述重整腔7上开设有重整腔入口8和重整腔出口9,所述催
化燃烧腔6和重整腔7为逆向流动布置。
38.本实施例所述蛇形通道4内通过若干个多孔隔板均匀隔开,多孔隔板内放置不同大小的催化剂,所述多孔隔板的孔径小于催化剂粒径,所述多孔隔板包括大孔径隔板2a、中孔径隔板2b和小孔径隔板2c,所述大孔径隔板2a、中孔径隔板2b和小孔径隔板2c沿反应流体的流动方向依次均匀布置,所述大孔径隔板2a、中孔径隔板2b和小孔径隔板2c均为铝制隔板,所述催化剂包括大粒径催化剂3a、中粒径催化剂3b和小粒径催化剂3c,所述大粒径催化剂3a设置在大孔径隔板2a分隔区域内,所述中粒径催化剂3b设置在中孔径隔板2b分隔区域内,所述小粒径催化剂3c设置在小孔径隔板2c分隔区域内,所述催化燃烧腔入口1和催化燃烧腔出口5分别与催化燃烧腔6内蛇形通道4的两端连通,所述重整腔入口8和重整腔出口9分别与重整腔7内蛇形通道4的两端连通,所述催化燃烧腔入口1与燃料电池尾气通道相连,所述重整腔入口8通过气态燃料通道与蒸发段通道相连,使预热蒸发后的气体进入重整腔7发生化学反应。
39.本实施例变催化剂粒径的填充床式重整制氢反应器整体为板型结构,从上至下依次层叠布置的催化燃烧腔6、重整腔7和催化燃烧腔6,两个催化燃烧腔6对称布置在重整腔7的上下两侧,通过催化燃烧为整个装置提供热量。所述催化燃烧腔6和重整腔7内部均为蛇形通道4,内部填充有助于反应进行的催化剂,同时沿着反应流体的流动方向,催化剂的粒径逐渐变小,蛇形通道4由铝制多孔隔板均匀隔开,以分段放置不同粒径大小的催化剂,且隔板固定。所述重整腔入口8通过气态燃料通道连接至蒸发段,重整反应器集尾气催化燃烧、重整制氢于一体,壁面受热均匀,催化反应充分,气体流动阻力小,反应器的催化性能稳定,可以使得转化效率进一步提高。
40.所述催化燃烧腔6、重整腔7内的催化剂粒径尺寸沿气体流动方向依次减小,即所述大粒径催化剂3a靠近催化燃烧腔6和重整腔7的催化燃烧腔入口1和重整腔入口8一侧,小粒径催化剂3c靠近催化燃烧腔6和重整腔7的催化燃烧腔出口5和重整腔出口9一侧。所述催化燃烧腔6、重整腔7内的多孔隔板的孔径要小于隔板两侧催化剂的粒径。所述催化燃烧腔6和重整腔7采用逆向流动布置。
41.采用催化燃烧腔6-重整腔7-催化燃烧腔6的方式上中下层叠布置,受热均匀,反应稳定充分,回收燃料电池的尾气进行催化燃烧,为重整反应提供热量,避免了氢气的浪费,同时解决了重整反应吸热的问题,重整腔7的反应通道壁面受热更加均匀,减少了温度分布差异对反应带来的影响,反应更加稳定。
42.采用变催化剂粒径的分段式填充,利用蛇形通道4增加反应流程,通过填充床式的重整器进一步提高反应时间,同时将不同粒径尺寸的催化剂固定在蛇形通道4内的多孔隔板之间,且多孔隔板的孔径小于两侧催化剂的粒径尺寸,有效减少了催化剂的位移,使填充床式重整器可有效用于多种场合,例如燃料电池飞机等。减小气体流动阻力,使催化性能更加稳定,同时多孔隔板采用铝材,具有很强的导热性,增强了蛇形通道4内的传热,使催化燃烧腔6和-重整腔7内的温度更加均匀,提高反应效率。同时,采用多孔隔板的分段式填充,更易实现,更易实现工程应用。
43.采用变催化剂粒径布置的方式,随着反应气体的流动,反应气浓度越来越低,而反应气与催化剂的接触面积越来越大,可以有效降低压力损失,减小压降,同时提高反应效率,减少催化剂用量,提高反应器的经济性。
44.本实施例为一种变催化剂粒径的填充床式重整制氢反应器的反应方法,它包括以下步骤:
45.步骤1:燃料电池尾气通过催化燃烧腔入口1进入催化燃烧腔6,液体燃料蒸发后通过重整腔入口8进入重整腔7,催化燃烧腔6和重整腔7内进行催化反应;
46.步骤2:随着反应气的流动,依次通过大粒径催化剂3a、中粒径催化剂3b和小粒径催化剂3c,燃料在重整腔7内发生水蒸气重整反应,尾气在催化燃烧腔6内发生燃烧反应,提供反应所需热量;
47.步骤3:最终重整气通过重整腔出口9流出,反应后的尾气通过催化燃烧腔出口5流出。
48.燃料电池尾气通过催化燃烧腔入口1进入催化燃烧腔6,在催化燃烧腔6内发生燃烧反应,放出大量的热,燃烧后的尾气通过催化燃烧腔出口5排出;汽化后的燃料通过蒸发段进入气态燃料通道,然后通过重整腔入口8进入重整腔7,燃料在重整腔7内发生水蒸气重整反应,由催化燃烧提供反应所需热量,最终重整气通过重整腔出口9流出。其中,催化燃烧腔6与重整腔1内均采用填充床式反应器,反应气进入到催化反应段,依次通过大粒径催化剂3a、中粒径催化剂3b和小粒径催化剂3c,完全反应后的气体再流出重整腔7。当反应气浓度较高时,接触到的是大粒径催化剂3a,当反应气浓度较低时,接触到的是小粒径催化剂3c。
49.以上公开的本实用新型实施例只是用于帮助阐述本实用新型。实施例并没有详尽叙述所有的细节,也不限制该实用新型仅为所述的具体实施方式。根据本说明书的内容,可作很多的修改和变化。本说明书选取并具体描述这些实施例,是为了更好地解释本实用新型的原理和实际应用,从而使所属技术领域技术人员能很好地理解和利用本实用新型。