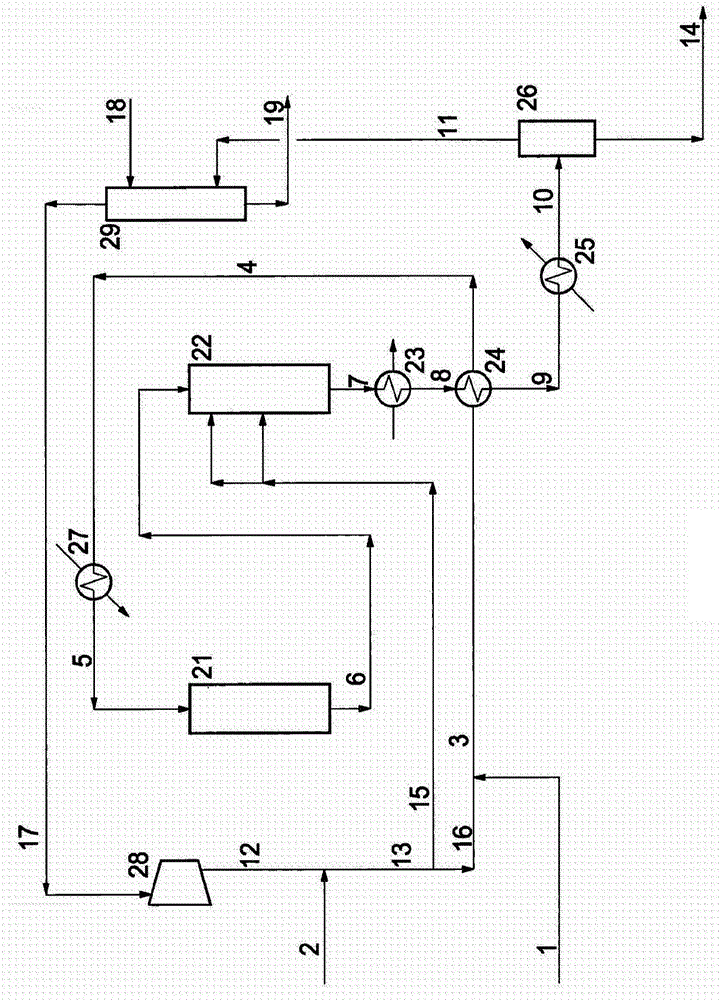
通过在混合的液相/气相中氢化马来酸二烷基酯生产1,4-丁二醇的方法发明概要描述了通过催化氢化马来酸二烷基酯生产1,4-丁二醇以及任选的γ-丁内酯和/或四氢呋喃的方法。所述方法基本上由以下步骤组成:a)在反应的第一阶段中,通过合适的催化剂使马来酸二烷基酯的料流氢化以产生琥珀酸二烷基酯;b)在反应的第二阶段中,通过使用不同的合适的催化剂使琥珀酸二烷基酯进一步氢化以产生主要的1,4-丁二醇以及作为副产物的γ-丁内酯和四氢呋喃。在反应的两个阶段中,条件如氢/有机原料之比、压力和温度使得反应器维持在混合的液相/气相中。技术领域本文所公开的实施方案一般涉及生产1,4-丁二醇以及作为副产物的γ-丁内酯和四氢呋喃的方法和设备,其通过使由马来酸烷基酯组成的原料与氢气在两个反应阶段中经过合适的催化剂反应来实现。发明背景1,4-丁二醇(BDO)由于其末端的伯羟基基团以及其耐化学品性而为多用途化学中间体。BDO是与聚合物(例如热塑性聚氨酯和聚酯,主要是聚对苯二甲酸丁二醇酯(PBT)、聚酯增塑剂、油漆、涂料和粘合剂)相关的合成技术中的重要原料。近年来,BDO的最大消耗者是四氢呋喃(THF),其用于生产氨纶纤维的关键原材料聚四亚甲基醚二醇(PTMEG)。大量的BDO被投入到γ-丁内酯(GBL)的制造中,进而用于制造N-甲基吡咯烷酮(NMP)和其他吡咯烷酮。有许多制造BDO的路线:第一条商业路线是由乙炔和甲醛的Reppe法。其他技术包括由丁二烯、由环氧丙烷、由丙烯醇的生产,以及最近的通过生物转化方法的生产。由于原料的可用性和低成本,所以在过去的二十年并且在未来,基于丁烷/马来酸酐的方法倾向于在市场中占据主要地位。基于丁烷/马来酸酐的方法包括两个主要组。第一组包括基于以下的所有方法:通过甲醇、乙醇或其他醇使马来酸酐酯化并且随后使二烷基酯(通常为马来酸二甲酯(DMM))氢化为丁二醇,和/或根据压力和温度条件以及根据催化剂氢化为四氢呋喃和γ-丁内酯。相反地,第二组包括基于使马来酸酐或马来酸直接氢化为BDO和/或THF和GBL的方法。虽然理论上这些方法似乎较为简单,具有较少的处理步骤(不需要马来酸酐的纯化和酯化),但是在工业应用中其很难成功,这可能是由于在高温下在马来酸存在下所需的催化剂和构造的复杂材料的高成本。此外,就基于马来酸酐酯化的第一组方法而言,在基于气相中氢化的方法与基于混合液相/气相中氢化的方法之间可有另外的区分。本发明引入的新方法属于混合相中马来酸酐二酯的氢化方法。无论是气相还是混合相,都认为马来酸二甲酯到1,4-丁二醇的反应经过至少两个中间体进行,如下:总之,1,4-丁二醇、四氢呋喃和γ-丁内酯是通过加成或消除氢和/或水彼此转化的反应产物。通过调节氢解反应的操作参数或催化剂的类型可改变产物分布。在现有技术中,一些发明已应用到马来酸酐酯的氢化以产生1,4-丁二醇。US专利2,110,488可被认为是涉及在250℃至300℃的温度范围内并且在150个大气压至300大气压的压力范围内使用由氧化铜和氧化铬组成的催化剂氢化脂肪族羧酸酯以产生脂肪族醇的首个应用。另一方面,US专利4,032,458是生产1,4-丁二醇的首个应用,其中首先通过一元醇使包含马来酸的溶液酯化,然后使马来酸二烷基酯在两个反应步骤中氢化,第一个步骤使存在于马来酸中的双键饱和,并且第二个步骤产生1,4-丁二醇和一元醇。两个反应步骤使用亚铬酸铜催化剂。反应温度为100℃至300℃,反应压力为172巴(表压)至241巴(表压),催化剂溶解于浆料中。US专利4,172,961是在浆料中的亚铬酸铜催化剂的另一个应用,以将丁氧基琥珀酸二丁酯氢化为1,4-丁二醇。WO专利82/03854是用包含氧化铜和氧化锌的混合物的催化剂在气相中氢化羧酸酯的一般方法。几种可能应用之一涉及由马来酸、富马酸或琥珀酸的酯产生1,4-丁二醇。US专利4,584,419包括在亚铬酸铜催化剂存在下在气相中使马来酸酐的酯氢化为丁二醇的方法。US专利4,656,297是通过用亚铬酸铜催化剂在琥珀酸二甲酯的气相中氢化产生丁二醇的另一种方法,其通过向酯原料中添加甲醇来进行。US专利4,751,334也是用Cu-Cr或Cu-Zn氧化物催化剂在气相中的氢化方法,其由马来酸二乙酯在两个或三个串联的绝热氢解区中产生1,4-丁二醇。US专利5,872,276涉及在50巴至400巴的压力,30℃至160℃的温度以及20至40的氢/原料摩尔比下在液相中使马来酸二烷基酯氢化为琥珀酸二烷基酯的方法。催化剂由铁亚族元素以及过渡族IV或V的元素的压制粉末组成,其具有特殊的耐压强度和内表面积。WO专利99/52845示出了通过不同类型的原料(包括马来酸二甲酯)的气相氢化产生BDO的方法,其特征在于将一氧化碳添加到反应中。US专利6,100,410、6,239,292、6,274,743、6,350,924和6,433,192描述了马来酸酐设备与BDO生产设备之间不同的特定整合,其中首先将有机溶剂中吸收的马来酸酐酯化,通过氢气流带出所得马来酸酯,然后使其在气相中经历氢化。US专利6,350,924属于相同的组,但其是考虑在液相中氢化的唯一一个专利,其通过优选在非常高的压力下操作以在蒸馏后获得非常高纯度的丁二醇。US专利6,137,016和2007/0260073提供了用于纯化包含少量环状缩醛的BDO的方法,其通过在少量水存在下并且在液体/气体反应典型的温度和压力条件下氢化丁二醇来进行。US专利6,191,322是用于生产BDO的方法,其通过在75巴至90巴的压力和160℃至250℃的温度下,用在反应阶段之间注入冷氢气,在两个串联的催化步骤中γ-丁内酯或琥珀酸酐酯或其混合物的混合相催化氢化来进行。所述催化剂可在铜和锌氧化物或亚铬酸铜之间选择。US专利6,248,906是这样的方法,其中使马来酸酐酯经历两个连续的氢化步骤,其中初次氢化主要产生GBL和THF,二次氢化将一部分GBL转化为BDO。US专利6,288,245教导了通过包含二氧化硅-氧化铝催化剂的第二阶段反应器使经马来酸酯气相氢化产生的BDO转化为THF的方法。US专利6,433,193涉及马来酸酐与丁二醇生产之间的整合,其中通过吸收到γ-丁内酯中来回收马来酸酐并且使所得的马来酸酐和GBL的混合物在有利于THF和GBL形成的条件下经历氢化步骤。US专利6,620,949是另一种整合方法,其中用于生产BDO、GBL和THF的马来酸酐通过使来自马来酸酐催化氧化反应器的气体流出物部分冷凝来产生。US专利6,844,452是在气相中由马来酸二甲酯或马来酸二乙酯生产BDO和THF的氢化方法,其特征在于使用不同催化剂的三个串联氢化区,这样的布置允许接受原料中的少量酸性物质,以提高THF的产率以及减少环化缩醛的形成。US专利6,936,727涉及气相氢化的一个特定方案,其使用有利于四氢呋喃形成的催化剂和条件,特征在于将分为两部分的液体原料分别供给至两个连续的汽化器/反应器系统,以这种方式使得氢的总体较低循环能够使反应器原料维持在其露点温度以上。CN专利101307042涉及通过使用两个催化剂床层来生产BDO以及THF和GBL的方法,第一个床层包含氧化铜和亚铬酸铜或氧化锌以及Ba、Mg、Ti、Ce、Si、Zr和Mn氧化物添加剂之一,第二个床层包含氧化铜、氧化铝和上述添加剂之一。US专利7,598,404的目的与上面提及的US专利6,936,727相同:在目标在于主要生产四氢呋喃的方法中,首先使原料在包含有利于碳双键饱和的催化剂的预反应器区中氢化,即由马来酸二甲酯产生琥珀酸二甲酯。在该方式中,可利用反应的热使一些液体原料蒸发。根据该专利,在其中产生THF和任选的二醇和/或内酯的第二反应区中,反应严格地在完全蒸发的条件下发生。CN专利101747149公开了通过使用马来酸二烷基酯经过两个串联的阶段氢化来制备BDO的方法,其中使来自第一反应步骤的流出物冷却并在两相中分离,并且使所得液体产物在第二氢化段与氢气再次接触。大多数上面提及的和通过氢化马来酸二烷基酯来产生丁二醇的其他专利都涉及气相中的反应。高压下在气相中的操作需要大量的再循环富氢气体。此外,单一反应器(其中氢化(双键饱和)和氢解反应二者同时发生)中DMM的转化,由于氢化反应是较放热的步骤并且反应速率也更较快,导致催化床第一部分中的局部高温(热点)难以控制,产生了不受欢迎的副产物、丁醇和其他产物,并且导致了催化剂劣化的风险。参照已提及的US专利7,598,404的第3页:在使用氢气的常规气相反应中,资本和操作成本(特别是能量和其他功用需求)很大程度上由供给至汽化器的气体流速决定......压缩器、热交换器和相互连接的管道系统的尺寸由循环气体流速决定,就像压缩所需的动力和待添加至反应器进料中和从反应器移除产物所需的热量那样。因此存在很强的动力使特定过程中的循环气体流速最小化。显然,循环气体减少至某一限度以下,导致反应不再在气相中并且进入混合的液体/气体条件。减少气体循环的该操作,虽然当然在关于资金和操作成本均有利,但是由于氢化反应的高放热效应而导致反应温度更难控制。实际上,正如已经提及的,反应的过高温度涉及不期望副产物的形成更多以及催化剂寿命的减少。副产物是效率降低(原材料和有用物质的较高消耗)的确定原因,并且在某些情况下不利于产物的质量。上面提及的US专利6,191,322是在混合相中产生BDO的极少数专利之一。该专利解决了与温度控制有关的问题,其首先通过使用已经部分氢化的产物作为原料(即,γ-丁内酯或琥珀酸二甲酯或者两种化合物的混合物),其次通过使用多阶段反应器并且通过注入冷氢气使反应阶段之间的混合物冷却来实现。显然,该专利的主要限制涉及原料的类型,其需要另外分开的氢化设备将马来酸二甲酯转化为琥珀酸二甲酯或γ-丁内酯。本发明的目的是通过避免气相中的昂贵方法在单一氢化设备中由马来酸二烷基酯产生1,4-丁二醇的方法。
技术实现要素:本发明的目的是提出通过催化氢化马来酸二烷基酯产生1,4-丁二醇以及任选的γ-丁内酯和/或四氢呋喃的方法。所述方法基本由以下步骤组成:a)在反应的第一阶段中,通过合适的催化剂使马来酸二烷基酯的料流氢化以产生琥珀酸二烷基酯;b)在反应的第二阶段中,通过使用不同的合适的催化剂使琥珀酸二烷基酯进一步氢化以产生主要的1,4-丁二醇以及作为副产物的γ-丁内酯和四氢呋喃。在反应的两个阶段中,条件例如氢/有机原料之比、压力和温度使得反应器维持在混合的液相/气相中。在本发明的优选实施方案中,在氢化的第一个步骤中使用的催化剂应具有以下特征:i)对碳双键饱和的高选择性和对氢解作用的极低选择性;ii)甚至在中等温度下对碳双键饱和的高活性。通过使用具有上述特征的催化剂,除了由于反应在混合的液相/气相中而不是在气相中进行的已述的其他经济优势之外,还取得了以下的另一些优势:a)在反应的第一步骤期间释放的热仅限于碳双键的饱和;通过使用控制量的再循环氢气,也容易将固定床反应器中的温度增加维持在控制之下。b)通过适当地控制反应混合物(马来酸二烷基酯和再循环的富氢气体)的入口温度,来自第一反应步骤的出口温度可与其中发生大多数或所有氢解反应的反应第二阶段的入口温度相匹配。c)第一氢化步骤的所有反应热用于将进入第二阶段的反应混合物预热至适当的温度。d)在180℃至230℃的温度下,来自反应第二阶段的液体-气体混合物的热含量首先用于产生低压蒸气,所述低压蒸气可用于设备的其他段,例如用于蒸馏DMM或用于纯化产物(BDO、THF以及(如果需要的话)GBL)。然后流出的热被用于预热混合相原料(DMM和氢气)达到反应第一阶段的入口温度,所述入口温度如上面提及的可为中等的(80℃至130℃)。不需要外部热源。总之,如在本发明中所提出的两阶段反应体系不仅将外部能量消耗减少为零,这在常规的气相方法中通常是不能忽略的,而且通过使氢化反应的内在放热最佳化允许来自反应体系的蒸气的产生和输出。此外,所提出的解决方案允许更好地控制热点温度和更具选择性的方法,以及减少副产物的量。在本发明的另一个实施方案中,通过注入适量的冷氢气可改善反应第二阶段的温度曲线并使其变平,所述冷氢气从循环压缩器的排放物中离开并且被送入(没有任何热回收)反应第二阶段固定床的中间点。第一阶段中使用的合适催化剂的实例包括负载在碳或氧化铝上的低含量钯催化剂。第二阶段中用于氢解的合适催化剂的实例包括含铜催化剂,例如亚铬酸铜催化剂或铜-锌氧化物催化剂。在一定程度上,出乎意料地比期望更加有利的是,使用混合相和两个步骤的上述反应进行的测试示出,与气相中的其他类似方法相比,副产物环化缩醛2-(羟基丁氧基)-四氢呋喃的形成大大减少,2-(羟基丁氧基)-四氢呋喃因为其沸点与BDO的沸点非常接近而为特别不期望的杂质。这表明本发明另外的且不可忽视的优势。另一方面,已提及的DavyProcessTechnologyLtd.的US专利2007/0260073教导了缩醛的减少可通过在液相中与氢气流接触并且在催化剂存在下实现,所述催化剂是本发明中所描述的通常在气相中在另一个氢解反应器中生产丁二醇的相同类型。本发明在缩醛污染方面达到更好的结果,其简单地通过在混合的液相-气相中操作氢解反应来实现,而不需要在液相中进行任何另外的纯化步骤。本发明的另一个方面在实施实验室测试期间变得明显。在工业设备中,以大大过量于化学计量的量使用的总反应气体主要由再循环气体构成,所述再循环气体在位于第二阶段反应流出物冷却之后的低温(30℃至60℃)液体-气体分离器中产生。在反应的第二阶段中,一些四氢呋喃与化学计量的水一起产生。因为这样的水在沸点下比主产物(BDO)轻得多,所以大多数水保留在气相中,因此通过压缩器循环回反应第一阶段的再循环气体被水蒸气饱和。在设备布置比工业设备简单的实验室测试中,所有的反应气体由来自氢气瓶的高纯度气体形成。为了重现工业设备性能,通过向氢气流中添加计算量的蒸气来重复一些测试。出乎意料地,与使用无水氢气的测试相比,在使用添加蒸气的测试中,THF/BDO之比低得多,为大约一半。当来自设备的期望最终产物主要为或仅为THF而不是BDO时,可使用这个特征:通过从再循环气体中移除水,可在一定程度上增加THF的产率。可通过与多种类型的固体吸附剂相接触来完成再循环气体中的水移除。可能的吸附剂为用于气体脱水的标准沸石。或者,可通过使富氢气体在吸收柱中与具有高沸点和吸湿性倾向的有机溶剂(例如三甘醇)相接触来进行富氢气体的水移除。但是,液体吸收剂的优选类型是来自设备的产物之一,包括从设备的产物纯化系统中回收的丁二醇或γ-丁内酯。相反地,不认为四氢呋喃是正确的吸收剂,既因为其是挥发性产物(沸点仅为65℃),也因为由于两种组分形成共沸混合物其很难通过蒸馏与水分离。除了使THF的产率增加之外,由再循环气体中的水移除还可有助于减少催化剂的劣化和增加其寿命。本发明的方法允许改变丁二醇、四氢呋喃和γ-丁内酯的相对比率。除了通过上述的从循环气体移除水之外,甚至还可通过使粗制丁二醇或精制丁二醇在氢气存在或没有氢气下在120℃至250℃的中等温度下经历脱水过程来改变THF/BDO之比,所述脱水过程可通过与二氧化硅-氧化铝类型或者(如果应用于纯化的丁二醇)具有磺酸基的基于聚合物的树脂的酸性催化剂接触进行。此外,还可通过降低氢化反应的压力来增加THF+GBL/BDO之比。水移除、减少操作压力和酸催化剂床的正确组合可有助于达到期望的THF/BDO之比。此外,还可通过调整γ-丁内酯从纯化段到氢化段的再循环速率(在全再循环与零再循环之间)将其产生控制在零至一定量。与本发明相关的总氢化反应条件和性能归纳于所附表1中。表1-反应器条件和性能附图说明图1是如在公开点(a)、(b)、(c)、(d)的概述中所描述的氢化体系的简单工艺流程图,所述氢化系统通过催化氢化马来酸二烷基酯来生产1,4-丁二醇以及任选的γ-丁内酯和/或四氢呋喃。图2是所述氢化体系的更完整布置,其中除了反应的两个阶段之外,还包括以下额外的特征:(i)通过注入富含氢的冷的再循环气体使反应第二阶段的温度曲线变平。(ii)在吸收柱中洗涤再循环气体以降低其含水量,从而增加四氢呋喃的形成。将参照这些附图描述本发明。具体实施方式图1说明了通过马来酸二烷基酯(通常为马来酸二甲酯)与氢在混合的液相-气相中的催化反应来产生BDO以及任选的GBL和THF的设备。将通过催化酯化马来酸酐产生的马来酸二甲酯作为流1供给至液相中。除DMM之外,流1还可包含从设备的纯化段再循环回来的少量未转化DMS,通常与一些量的GBL混合。流1与流13混合,流13代表新鲜氢气流2和反应再循环气体流12的混合物。因此,所得流3是混合的液体/气体流体。所述流3首先通过从第二阶段氢化反应器22的流出物流8中回收热而在热交换器24中预热,然后使用冷凝低压蒸气作为加热介质在热交换器27中预热。该热交换器27特别地在设备启动期间出于温度控制的原因而使用;在设备的正常稳定操作期间,可不连接或绕过它。通过使用特殊的启动程序,甚至可省略热交换器27。来自交换器的出口流5进入反应的第一阶段21中。其是下流式固定床绝热反应器,包含用于饱和马来酸二烷基酯中所含的碳双键的高选择性特定催化剂。在反应器21的催化剂床中,马来酸二甲酯以非常高的转化率和选择性转化为琥珀酸二甲酯。该反应是高度放热的,因此流出物流6的出口温度比入口流5的温度稍微高一些。在本发明的一个优选实施方案中,以第一反应器阶段的出口温度与第二反应阶段的入口温度相匹配的方式设计反应体系,因此在系统的设计中不包括热交换器。来自反应器第一阶段的流出物6在控制温度下进入第二阶段反应器22。所述反应器22也是下流式固定床绝热反应器,其包含与第一阶段不同的催化剂,更具体地为适于将琥珀酸二甲酯氢解为1,4-丁二醇的催化剂;根据压力和温度条件,可与BDO一起产生不同量的γ-丁内酯和/或四氢呋喃。来自反应器的产物流7首先在热交换器23中被冷却。热交换器23是蒸气发生器,优选为在交换器的壳内部产生蒸气的釜(kettle)型。作为替代情方案,其也可以是自然循环交换器,其中将用于产生蒸气的热水器给水供给到外部容器并且在容器与热水器之间产生自然热对流循环。来自热交换器23的出口流8经过已经描述的内交换器24。出口流9在热交换器25中被进一步冷却,所述热交换器无差别地是水冷却器或空气冷却器。经冷却的流10进入分离器容器26,在其中使粗制液体产物14与气相流11分离,所述粗制液体产物14包含大部分BDO以及较低百分比的γ-丁内酯、四氢呋喃、甲醇、水、未反应的琥珀酸二甲酯和杂质,所述气相流11基本上由氢气以及较少量的甲醇、四氢呋喃和水组成。然后气态流11通过压缩器28被再循环回来,其压差相当于包括设备的反应器、热交换器、分离器、管道和控制阀在内的总压降。来自压缩器的排出流12与新鲜氢气流2一起构成用于氢化反应器的总反应气体13。图2说明了通过马来酸二烷基酯的催化反应产生BDO以及任选的GBL和THF的设备,其中(i)通过注入富含氢的冷的再循环气体使反应第二阶段的温度曲线变平,以及(ii)在吸收柱中洗涤再循环气体以减少其含水量,从而增加四氢呋喃的形成。将通过催化酯化马来酸酐产生的马来酸二甲酯作为流1供给至液相中。除DMM之外,流1还可包含从设备的纯化段再循环回来的少量未转化DMS,通常与一些量的GBL混合。流1与流16混合,流16表示新鲜氢气流2与反应再循环气体流12的混合物13的一部分。再循环气体的另一小部分作为流15在冷的温度下直接再循环到反应的第二阶段以控制其温度增加。图2示出两个不同的注入点:根据反应器条件,注入点可多于两个或者甚至为单一注入。因此,由新鲜原料和再循环气体之混合物产生的流3是混合的液体/气体流。其首先通过从第二阶段氢化反应器22的流出物流8中回收热而在热交换器24中预热,然后使用冷凝低压蒸气作为加热介质在热交换器27中预热。该热交换器27特别地在设备启动期间出于温度控制的原因而使用;在设备的正常稳定操作期间,可不连接或绕过它。通过使用特殊的启动程序,甚至可省略热交换器27。来自交换器的出口流5进入反应的第一阶段21。所述第一阶段21是下流式固定床绝热反应器,包含用于饱和在马来酸二烷基酯中所含的碳双键的高选择性特定催化剂。在反应器21的催化剂床中,马来酸二甲酯以非常高的转化率和选择性转化为琥珀酸二甲酯。该反应是高度放热的,因此流出物流6的出口温度比入口流5的温度稍微高一些。在本发明的一个优选实施方案中,以第一反应器阶段的出口温度与第二反应阶段的入口温度相匹配的方式设计反应系统,因此在系统的设计中不包括热交换器。来自反应器第一阶段的流出物6在控制温度下进入第二阶段反应器22。反应器22也是下流式固定床绝热反应器,包含与第一阶段不同的催化剂,更具体地为适于将琥珀酸二甲酯氢解为1,4-丁二醇的催化剂;根据压力和温度条件,可与BDO一起产生不同量的γ-丁内酯和/或四氢呋喃。来自反应器的产物流7首先在热交换器23中被冷却。热交换器23是蒸气发生器,优选为在交换器的壳内部产生蒸气的釜型。作为替代方案,其也可以是自然循环交换器,其中将用于产生蒸气的热水器给水供给到外部容器并且在容器与热水器之间产生自然热对流循环。来自热交换器23的出口流8经过已经描述的内交换器24。出口流9在热交换器25中被进一步冷却,所述热交换器25无差别地是水冷却器或空气冷却器。经冷却的流10进入分离器容器26,在其中使粗制液体产物14与气相流11分开,所述粗制液体产物14包含大部分BDO以及较低百分比的γ-丁内酯、四氢呋喃、甲醇、水、未反应的琥珀酸二甲酯和杂质,所述气相流11基本上由氢气以及较少量的甲醇、四氢呋喃和水组成。包含在反应第二阶段中产生的一定百分比水分的气态流11进入包括不同类型塔板(tray)和填料(packing)的吸收柱29,其中通过与供给至柱顶部的冷液体流18接触来移除水分,所述冷液体流18优选地由纯化的GBL或BDO组成。来自柱底部的所得液体流19由湿的GBL或BDO,组成,并入流14被一起送入设备的蒸馏段中。然后通过压缩器28使来自柱顶的干燥气态流17再循环,其压差相当于包括设备的反应器、热交换器、分离器、管道和控制阀在内的总压降。来自压缩器的排出流12与新鲜氢气流2一起构成用于氢化反应器的总反应气体13。实施例实验装置实验室规模的实验突出本发明的性质,但不旨在限制其范围。在这些实验室实验中,通过使用两个串联的反应器进行了马来酸二甲酯(DMM)到丁二醇(BDO)的氢化:第一个反应器将DMM转化为琥珀酸二甲酯(DMS),第二个反应器将DMS转化为BDO。第一个反应器由通过加热带(heatingband)进行外部热控制的不锈钢管(长度为1000mm,内径为20mm)组成。已将反应器设计成包含用于将马来酸二甲酯(DMM)氢化为琥珀酸二甲酯(DMS)的单一催化床,其高度为60mm并且由碳负载的Pd组成。第二个反应器由通过加热带进行外部热控制的不锈钢管(长度为1800mm,内径为20mm)组成。对于本专利中所描述的测试,其使用用于将DMS氢化为丁二醇(BDO)的单一催化床,高度为600mm。用于测试中的催化剂是基于铜的,例如亚铬酸铜催化剂或铜-锌氧化物催化剂。两个催化床前面均有高度为约500mm的玻璃柱床(5mm×10mm),用于将原料预热到反应起始温度。通过使原料毛细管穿过第一个反应器的加热带来进行液体原料的预热。通过分别位于每个催化床的入口和出口处的四个热电偶来进行温度的连续监控。在两个分开的容器中回收反应产物,第一个用于回收重质产物,直接位于第二个反应器的底部,第二个主要用于回收轻质产物,位于用于冷却出口混合物的双管热交换器的下游。使用配备有质谱仪检测器的气相色谱仪(Agilent5893N)分析样品。实施例1在该实施例1中仅使用第一个反应器。在以下条件下,将液态DMM的流供给至具有钯碳催化剂的第一个反应器中:不同温度下的测试的主要结果示于表2中。表2-DMM至DMS的氢化温度℃转化率%对DMS的选择率%10010099.012010098.916510099.0该实施例1示出,用于反应第一个步骤的催化剂具有两个必要特征:i)对碳双键饱和的高选择性和对氢解的非常低选择性,ii)甚至在中等温度下对碳双键饱和的高活性。虽然由于实验室设备尺寸较小而不能重现完全绝热的条件,但是在测试期间使用的条件的计算机模拟示出,从绝热的固定床反应器的入口到出口的温度增加量为约60℃。实施例2在该实施例2中,使用如在实验装置中描述的两个反应器阶段。在以下条件下,将液态DMM的流供给至具有钯碳催化剂的第一个反应器中:液时空速第一阶段2.0小时-1第二阶段0.2小时-1分析测试的主要结果示于表3中。表3-DMM氢化和氢解-干燥条件实施例3在该实施例3中,重复实施例2的条件,唯一的不同是添加少量水到原料中以模拟工业设备的条件,从而使再循环气体被水饱和。分析测试的主要结果示于表4中。表4-DMM氢化和氢解-湿的条件该实施例3示出,在湿的条件下,总结果与干燥条件下的结果非常相似,主要差异在于THF的产率由13%下降到约6%,该差异由BDO产率的等量增加所补偿。三种有价值的产物(BDO、GBL和THF)的总产率为95.6%。考虑到未反应DMS可通过蒸馏单独或与GBL混合来分离,并且再循环回到反应体系中,实际的总产率为约97.8%。