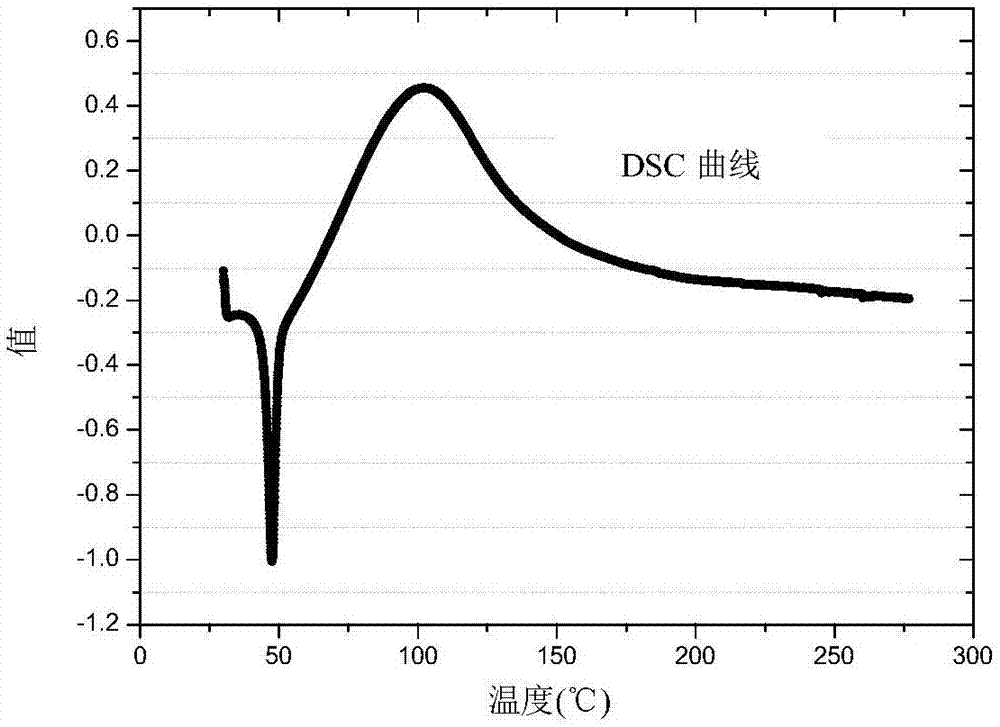
本发明涉及复合材料模具制造领域,尤其涉及用于制造复合材料模具的环氧树脂体系及其应用。
背景技术:
复合材料是将不同性质的材料组分优化组合而成的新材料。现代高科技的发展离不开复合材料,而复合材料对现代科学技术的发展也有着十分重要的作用。复合材料的研究深度和应用广度及其生产发展的速度和规模已成为衡量一个国家科学技术先进水平的重要标志之一。尤其是近年来随着航空航天、兵器、船舶、高铁等行业迅猛发展,复合材料替代传统金属材料已经成为军转民及军民融合的一个重要发展方向。复合材料模具是用于利用复合材料通过成型制备复合材料制件的模具。近年来,借助风电叶片的浪潮,复合材料模具技术得到了充分的继成和长足的发展。与传统的金属材质模具技术相比,复合材料模具技术在加工大尺寸复杂型面模具时具有压倒性的优势,在航空航天、船舶、轨道交通、电子系统等领域具备巨大的应用潜力。复合材料模具一般采用两步法制造:首先,需要对例如代木树脂进行成型与加工,其次,在代木树脂上进行预制体的铺层、复合材料模具用树脂的真空灌注及复合材料模具的加工。由于例如代木树脂的使用需求及真空灌注成型工艺自身的特点,因此对真空灌注过程中使用的复合材料模具用树脂的要求高。目前,复合材料模具用树脂还存在初始粘度大、力学性能不足、固化温度高、工艺适用期短等问题。而且,由于耐温性要求的提高,因此需要提高耐温等级(尤其是使用温度超过120℃时),而耐温等级的提高往往会增复合材料模具用树脂的初始粘度,提高灌注温度及固化温度,从而导致无法实现常温固化,延长固化时间,大大增加了复合材料模具的制造难度及成本,降低其使用性能,难以实现低温固化和高温使用的兼顾和平衡。因此,对复合材料模具的性能要求日益苛刻,尤其随着复合模具使用温度要求的提高,复合材料模具技术遇到了难以克服的技术瓶颈。因此,本领域迫切需要能够解决上述问题的复合材料模具用树脂。技术实现要素:本申请人针对代木树脂的使用需求及真空灌注成型工艺自身的特点,开发了一种能够解决现有技术中一个或者多个上述问题的作为复合材料模具用树脂的环氧树脂体系。本发明第一方面提供了一种环氧树脂体系,其特征在于,所述环氧树脂体系包括:组分a,所述组分a包含环氧树脂或者由环氧树脂组成;和组分b,所述组分b包含第一固化剂和第二固化剂或者由第一固化剂和第二固化剂组成,所述第一固化剂为脂肪胺,所述第二固化剂为芳香胺或酸酐固化剂。本发明第二方面还提供了本发明第一方面所述的环氧树脂体系在复合材料模具制造中的应用。本发明的环氧树脂体系具有如下优点:(1)常温初始粘度低,工艺适用期长,从而能够充分浸润到纤维间隙中,降低了复合材料模具的制造难度。(2)固化温度低,能够在常温下灌注和固化,降低了复合材料模具的制造成本。(3)玻璃化转变温度高,能够耐高温,收缩率低,力学性能好,提高了使用性能。因此,本发明的环氧树脂体系特别适用于复合材料模具制造,尤其是耐高温型复合材料模具的制造。由本发明的环氧树脂体系制得的复合材料模具具有优良的机械性能、耐化学腐蚀性、电绝缘性、加工性能、粘接性能,并且收缩率低,可以广泛应用于各种复合材料模具的制造。附图说明图1是本申请制备例1制得的环氧树脂体系的dsc(differentialscanningcalorimeter)曲线图。图2是本申请制备例1制得的环氧树脂体系的模量曲线图(e')和损耗曲线图(tanδ)。图3显示采用本发明的环氧树脂体系制造高铁大型复合材料模具时的灌注现场照片。图4显示采用本发明的环氧树脂体系制造得到的大型复合材料模具产品照片。具体实施方式为使本发明的目的、技术方案和优点更加清楚,下面将结合本发明实施例对本发明的技术方案进行更加清楚、完整地描述。但是,所提供的实施例仅仅是本发明的一部分实施例,而不是全部的实施例。基于本申请所公开的内容,本领域普通技术人员在未付出创造性劳动的前提下就可以想到的技术方案,都属于本发明保护的范围。如上所述,本发明第一方面提供了一种环氧树脂体系,所述环氧树脂体系包括:组分a,所述组分a包含环氧树脂或者由环氧树脂组成;组分b,所述组分b包含第一固化剂和第二固化剂或者由第一固化剂和第二固化剂组成,所述第一固化剂为脂肪胺,所述第二固化剂为芳香胺或酸酐固化剂。环氧树脂具有优良的机械性能、耐化学腐蚀性、电绝缘性、加工性能、粘接性能,并且收缩率低,广泛应用于社会各行各业。为了获得耐高温(tg>150℃)复合材料模具,需要复合材料模具用树脂具备良好的力学性能及较低的固化收缩率。本发明人经过长期深入的研究,发现选用环氧树脂作为体系主体成分,并与适当的固化剂配合,可以在常温下具备较低的初始粘度和较长的工艺适用期,从而能够充分浸润纤维,并且能够耐受高温,具有良好的力学性能和较低的固化收缩率,而且能降低树脂成本,从而克服了过去无法实现低温固化和高温使用兼顾的问题。环氧树脂固化剂是与环氧树脂发生化学反应,形成网状立体聚合物,把复合材料骨材包络在网状体之中,因此环氧树脂固化剂是环氧树脂体系中不可缺少的一部分,环氧树脂必须与固化剂反应以生成三向立体结构才具有实用价值。目前市场上环氧树脂固化剂品种繁多,性能各异。国外对固化剂的研究与开发远比环氧树脂活跃,与环氧树脂品种相比,固化剂品种更多,且保密性很强。每开发一种新的固化剂就可以解决一个方面的问题,就相当于开发一种新的环氧树脂或开辟了环氧树脂一个新的用途。开发新型固化剂远比开发新型环氧树脂更为重要已成共识。本发明人发现,单一选用脂肪胺固化剂会降低固化后树脂的耐热性,而芳香胺固化剂、酸酐固化剂较难在常温下实现固化;但是如果选用脂肪胺固化剂来与选自芳香胺固化剂和酸酐固化剂中任一种固化剂配合使用,可以同时满足兼顾低温固化和高温使用的要求。环氧树脂通常具有高的粘接性,但在室温下,初始粘度比较大,不利于浸润到例如纤维及其织物中。为了克服这一缺点,通常需要使用过程中加入稀释剂以增加环氧树脂对纤维及其织物的浸润能力,改善成型工艺性能,同时可以增加填料的用量。但是,发明人发现,选择适当的环氧树脂和固化剂组成环氧树脂体系,可以不需要使用稀释剂,而且如此可以提高环氧树脂体系的力学性能和耐热性能,并降低其固化收缩率。于是,在一些实施方式中,本发明的所述环氧树脂体系不包括稀释剂。在一些实施方式中,所述环氧树脂包含双酚a型环氧树脂和/或双酚f型环氧树脂,或者由双酚a型环氧树脂和/或双酚f型环氧树脂组成。在另外优选的一些实施方式中,所述环氧树脂选自由830环氧树脂、e51环氧树脂、f51环氧树脂和f44环氧树脂组成的组。在一些实施方式中,所述脂肪胺选自由氢化二亚乙基三胺、三亚乙基四胺、乙二胺、己二胺、二乙烯三胺、三乙烯四胺、四乙烯五胺和二乙氨基丙胺组成的组。在一些实施方式中,所述芳香胺选自由二乙基甲苯二胺、氢化间苯二胺、氢化间苯二甲胺、氢化邻甲基间苯二胺、苄甲基胺、苄基二甲胺、间苯二胺、间苯二甲胺组成的组。在一些实施方式中,所述酸酐固化剂选自由顺丁烯二酸酐、邻苯二甲酸酐、甲基四氢化邻苯二甲酸酐(mthpa)、偏苯三甲酸酐(tma)、四溴邻苯二甲酸酐、四氯邻苯二甲酸酐、一氯苯二甲酸酐和二氯顺丁烯二酸酐组成的组。在一些更加优选的实施方式中,所述环氧树脂包含双酚a型环氧树脂和双酚f型环氧树脂或者由双酚a型环氧树脂和双酚f型环氧树脂组成,并且其中的双酚a型环氧树脂和双酚f型环氧树脂的质量比为1:(1~5),例如为1:1、1:2、1:3、1:4或1:5。本发明人发现,采用双酚a型环氧树脂和双酚f型环氧树脂的组合并且选用适当的固化剂组合可以配制得到能够保证机械强度和耐温性的同时初始粘度甚至小于300mpas,从而特别有利于树脂灌注。在一些实施方式中,所述第一固化剂和所述第二固化剂的质量比为1:(1~3),例如为1:1、1:2或1:3。在一些实施方式中,所述组分a和所述组分b的质量比为20:(1~4),例如为20:1、20:2、20:3或20:4。在一些实施方式中,所述环氧树脂体系在25℃的初始粘度为小于400mpa.s,例如为50至400mpa.s;工艺适用期(即从调配好后开始至25℃的粘度不超过1000mpa.s的时间)为2至4小时,例如3小时。在一些实施方式中,所述环氧树脂体系的固化温度为小于或者等于40℃,优选为15℃至30℃,例如为25℃;在25℃的固化时间为12至24小时,例如为12、16、20或24小时。低温固化可以降低制造复合材料模具所需的材料和用具对耐温性的要求,可以减少能量消耗,可以减少温度大幅度变化造成内应力在制件中的产生和累积,从而显著降低复合材料模具的制造成本,提高复合材料模具的力学性能。在灌注之后,需要在较高的温度下进行后处理,以使环氧树脂体系反应更加充分,提高复合材料模具的性能尤其是耐温性。在本发明中,后处理温度为100℃至140℃,例如为100、110、120、130或140℃。在一些实施方式中,所述环氧树脂体系的玻璃化转变温度为155℃至165℃,例如160℃。玻璃化转变温度是复合材料模具耐温性的指标,本发明的环氧树脂体系能够同时满足常温固化和高温使用的要求,解决了目前耐高温型复合材料模具的技术瓶颈。本发明第二方面还提供了本发明第一方面所述的环氧树脂体系在制备复合材料模具中的应用。实施例下文将通过以实施例的形式对本发明进行进一步的说明。但是本发明的保护范围不限于这些实施例。实施例中使用的纤维复合材料为sw220(一种玻璃布增强材料,购自南京玻璃钢研究院,厚度为3mm,尺寸为440mmx240mm)。固化剂来自市购济南汇丰达化工有限责任公司。环氧树脂购自上海市合成树脂研究所。制备例1按照下表1所示的比例分别称取作为组分a的830环氧树脂、作为第一固化剂的四乙烯五胺和作为第二固化剂的二乙基甲苯二胺,然后将第一固化剂和第二固化剂混合在一起,得到组分b。再将组分a和组分b调配在一起,得到环氧树脂体系e1。对比制备例1按照制备例1的方式进行,不同之处在于仅使用四乙烯五胺作为固化剂,其重量为制备例1中的第一固化剂和第二固化剂的总和。制得对比环氧树脂体系ce1。树脂工艺性测试然后测量环氧树脂体系的树脂工艺性,发现室温(25℃)初始粘度为356.4mpa·s,工艺适用期为3小时左右;该环氧树脂体系在常温(25℃)即可固化,在25℃固化的固化时间为12小时;最佳后处理温度为110℃(参见图1),后处理时间为约4小时。耐热性测试经过对玻璃化转变温度(tg)进行测量发现,环氧树脂体系e1的平均tg为155.3℃(参见图2),环氧树脂体系ce1的平均tg为84.8℃。浇注体力学性能测试利用环氧树脂体系进行浇注,然后在25℃固化12小时,并在120℃后处理4小时,制得18个浇注体(每个浇注体包含15g环氧树脂体系)。将这些浇注体分为3组,一组用于测量拉伸强度和拉伸模量,一组用于测量弯曲强度和弯曲模量,另一组用于测量固化收缩率。每组6个,其中5个用于测量相应性能,1个备用。结果参见下表2。复合材料模具试验件的力学性能测试利用制备例1所制得的环氧树脂体系e1和对比制备例1所制得环氧树脂体系ce1通过真空灌注方式对sw220玻璃布(厚度为3mm,尺寸为440mmx240mm)进行灌注,然后在25℃固化24小时,并在100℃后处理5小时,获得30个复合材料模具试验件平板。将这些试验件平板分为如下5组:(1)用于测量拉伸强度和拉伸模量的组,(2)用于测量压缩强度和压缩模量的组;(3)用于测量弯曲强度和弯曲模量;(4)用于测量层间剪切强度的组;(5)用于测量tg值。每组6个,其中5个用于测量相应性能,1个备用,并求算5个测量值的平均值。结果列于表3中。由表3中可以看出,测得的力学性能与(830环氧树脂+四乙烯五胺)体系相当,在拉伸强度、压缩强度和层间剪切强度甚至还略优于(830环氧树脂+四乙烯五胺)体系,但是由e1灌注制得的平板试验件的tg(161.2℃)显著高于由ce1灌注制得的平板试验件的tg(89.8℃)。另外,利用制备例1制得的环氧树脂体系制造大型复合材料模具(如图3和4所示),该复合材料模具具有优异的性能,其表面粗糙度为约0.8,型面及尺寸精度为0.2mm,孔隙率小于0.1%,成本为金属材质模具的45%,净周期为21天。制备例2至7除了表1的内容之外,按照制备例1基本相同的方式进行,并采用相同的方法测量环氧树脂体系在25℃的初始粘度、工艺适用期、在25℃固化18小时是否能够固化以及由相应的环氧树脂体系制得的复合材料模具平板试验件的层间剪切强度(结果参见表4)。对比制备例2和3除了表1的内容之外,按照制备例1基本相同的方式进行。而且,采用相同的方法测量环氧树脂体系在25℃的初始粘度、工艺适用期、在25℃固化18小时是否能够固化以及由相应的环氧树脂体系制得的复合材料模具试验件平板的层间剪切强度(结果参见表4)。对比制备例4除了表1的内容之外,按照制备例1基本相同的方式进行,还有不同之处在于向环氧树脂体系中添加以环氧树脂体系的总质量计为5%的二缩水甘油醚作为稀释剂。而且,采用相同的方法测量环氧树脂体系在25℃的初始粘度、工艺适用期、在25℃固化18小时是否能够固化以及由相应的环氧树脂体系制得的复合材料模具试验件平板的层间剪切强度(结果参见表4)。表1.各制备例中的环氧树脂体系的配方。表2.制备例1中所制得的环氧树脂体系浇注得到的浇注体的力学性能。性能12345平均值拉伸强度/mpa74.273.975.475.174.474.6拉伸模量/gpa2.82.93.13.02.92.9弯曲强度/mpa115.2112.5114.7114.5116.7114.7弯曲模量/gpa2.82.72.82.82.82.8固化收缩率%0.70.70.50.50.50.6表3.利用制备例1中所制得的环氧树脂体系和830环氧树脂体系灌注sw220复合材料得到的复合材料模具试验件平板的力学性能。性能sw220/(830环氧树脂+四乙烯五胺)sw220/e1拉伸强度/mpa508550拉伸模量/gpa23.521.9压缩强度/mpa378385压缩模量/gpa25.022.4弯曲强度/mpa608585弯曲模量/gpa18.217.1层间剪切强度/mpa56.862.1tg/℃89.8161.2表4.各制备例和对比制备例制得的环氧树脂体系的性能。从上表可以看出,制备例1至7中的初始粘度都在400mpa·s,其中制备例5的初始粘度甚至小于300mpa·s;工艺适用期为3至6小时;都能够常温固化,并且tg为155℃以上,表现出良好的耐温性。相反,使用单一固化剂的对比制备例2和3在常温下无法固化,对比制备例1虽然能够固化,但是tg过低,不到90℃,耐温性差。对比制备例4由于加了稀释剂以后,尽管能够降低初始粘度,但是tg和层间剪切强度尤其是后者都明显的降低。从以上各个制备例和对比制备例的结果可以看出,本发明的环氧树脂体系适用于耐高温复合材料模具,其工艺性能和使用性能优异,是一种常温灌注、固化,高温使用的低收缩率环氧树脂体系。所述环氧树脂体系已经成功应用于高铁的复合材料材质模具,该环氧树脂体系的成功研制使得高温复合材料材质模具取得突破性的进展,克服了高温下金属材料与复合材料线膨胀差导致的产品尺寸变化等问题。不仅如此,还大幅度降低复合材料用模具的制造成本,显著缩短生产周期,提高了性价比,工艺操作简单,力学性能优异,在复合材料材质模具及构件尤其是航空航天、轨道交通、船舶等大尺寸构件上具有广泛的应用前景。最后应说明的是:以上实施例仅用以说明本发明的技术方案,而非对其限制;尽管参照前述实施例对本发明进行了详细的说明,本领域的普通技术人员应当理解:其依然可以对前述各实施例所记载的技术方案进行修改,或者对其中部分技术特征进行等同替换;而这些修改或者替换,并不使相应技术方案的本质脱离本发明各实施例技术方案的精神和范围。当前第1页12