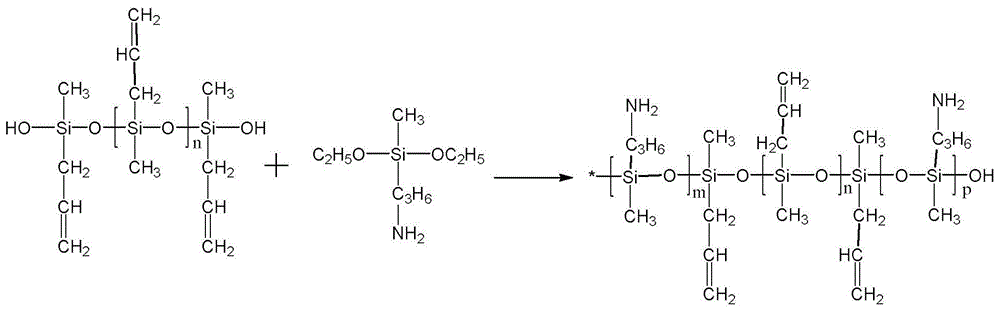
本发明属于密封圈制备领域,涉及一种改性硅胶密封圈的制备工艺。
背景技术:
:硅橡胶由于其具有较高的热稳定性和良好的电绝缘性、耐氧抗老化性、耐光抗老化性以及防霉性、化学稳定性而被广泛应用于密封圈的制备,但是硅橡胶的抗张强度低、不耐撕裂、耐磨性差、耐油性差,耐酸碱亦差,并且阻燃性能较低,因此在密封使用时对于密封的物体要求较高,对于酸碱盐以及有机物不能用于长期密封,同时对于易燃的物体也不能用于密封,为了克服这些缺点,现有技术中通常是直接在硅橡胶中通过混合熔炼的方法添加阻燃剂、抗腐蚀剂和耐磨助剂等实现阻燃耐老化耐磨的性能,但是由于硅橡胶的相容性较差,添加的助剂容易分散不均匀,进而造成其性能下降。技术实现要素:本发明的目的在于提供一种改性硅胶密封圈的制备工艺,通过制备的氨基化烯丙基聚硅氧烷,通过在氨基烯丙基聚硅氧烷链上通过自由基聚合引入1-烯丙基-3-羟基丙烷-2-基磷酸二氢阻燃剂,使得阻燃剂能够均布在氨基烯丙基聚硅氧烷链的不饱和单体上,进而使得引入的阻燃剂含量较高,并且分散均匀,提高了硅橡胶的阻燃性能,同时通过亲核加成作用在氨基烯丙基聚硅氧烷链上引入氟元素,不仅能够使得引入的氟元素分散均匀,同时提高了氟元素的引入量,进而提高了硅橡胶的抗腐蚀性能,解决了现有的硅橡胶材料通过混合熔炼的方法添加阻燃剂、抗腐蚀剂等实现阻燃耐老化的性能,但是由于硅橡胶的相容性较差,添加的助剂容易分散不均匀,进而造成其性能下降的问题。本发明在改性硅橡胶的制备过程引入的1-烯丙基-3-羟基丙烷-2-基磷酸二氢支链上含有羟基,同时氨基烯丙基聚硅氧烷的主链两端含有羟基,均能够与六亚甲基二异氰酸酯反应,通过六亚甲基二异氰酸酯与的交联作用使得相邻的硅胶链之间以及硅胶链内部之间交联成密实的网状结构,从硅橡胶本身的内部分子结构进行改进,从根本上提高了改性硅胶的韧性和耐磨性能,进而解决了现有的硅橡胶加入耐磨剂与硅橡胶相容性差,分散不均匀,长期使用时耐磨性能较差的问题。本发明的目的可以通过以下技术方案实现:一种改性硅胶密封圈的制备工艺,具体制备过程如下:第一步,向反应容器中通氮气20-30min,然后将氨基烯丙基聚硅氧烷和二氯甲烷加入反应釜中,同时向其中加入偶氮二异丁腈,混合均匀后升温至110-120℃,然后逐滴向反应釜中加入1-烯丙基-3-羟基丙烷-2-基磷酸二氢,边滴加边剧烈搅拌,滴加完全后恒温搅拌反应10-12h,得到棕色产物溶液;由于氨基烯丙基聚硅氧烷链上含有若干不饱和键,同时1-烯丙基-3-羟基丙烷-2-基磷酸二氢中含有不饱和键,在偶氮二异丁腈作用下能够发生自由基聚合反应,但是由于氨基烯丙基聚硅氧烷相邻不饱和键之间的空间位阻较大,进而使得每个不饱和键上只能接枝一个1-烯丙基-3-羟基丙烷-2-基磷酸二氢,通过自由基引发使得1-烯丙基-3-羟基丙烷-2-基磷酸二氢引入氨基烯丙基聚硅氧烷链上,进而使得氨基烯丙基聚硅氧烷链上的每个单体上均引入1-烯丙基-3-羟基丙烷-2-基磷酸二氢,同时在高温下作用下,环氧开环的羟基与相连的磷酸羟基之间通过氢键结合,进而使得氨基烯丙基聚硅氧烷上引入大量的磷氧键,大大的提高了氨基烯丙基聚硅氧烷的阻燃性能;第二步,向第一步中制备的棕色产物溶液中加入2-氨基-5-氟吡啶,升温至80-90℃搅拌回流20-30min,然后向反应容器中逐滴加入乙二醛溶液,滴加完全后恒温反应8-9h,由于氨基烯丙基聚硅氧烷链上的单体上含有大量的氨基,通过乙二醛的亲核加成反应使得2-氨基-5-氟吡啶引入硅胶链上,由于硅胶链上含有大量的氨基,加成后硅胶链上引入大量的氟元素,进而使得制备的改性硅胶具有较高的耐油耐酸碱性能;然后降温至40-50℃,逐滴向反应容器中滴加六亚甲基二异氰酸酯,边滴加边剧烈搅拌,滴加完全后恒温搅拌反应2-3h,然后进行过滤,再依次用丙酮和乙醇洗涤后烘干,得到阻燃耐磨改性硅胶;2-氨基-5-氟吡啶引入后的硅橡胶链两端仍含有活波羟基,同时引入的1-烯丙基-3-羟基丙烷-2-基磷酸二氢支链上也含有大量的羟基,通过六亚甲基二异氰酸酯的交联作用使得相邻的硅胶链之间以及硅胶链内部之间交联成密实的网状结构,进而提高了改性硅胶的韧性和耐磨性能;第三步,将第二步中制备的阻燃耐磨改性硅胶加入开炼机中,在170-180℃下硫化5-7min,然后进行加工成型,得到改性硅胶密封圈。其中每千克氨基烯丙基聚硅氧烷中加入二氯甲烷50-55l,加入1-烯丙基-3-羟基丙烷-2-基磷酸二氢268-274g,加入偶氮二异丁腈162-168g;同时每千克氨基烯丙基聚硅氧烷中加入2-氨基-5-氟吡啶123-128g,加入乙二醛68-72g,加入六亚甲基二异氰酸酯490-500g;其中氨基烯丙基聚硅氧烷的具体制备过程如下:步骤1:将烯丙基甲基二氯硅烷加入饱和浓盐酸中混合均匀,然后将混合后的物料加入填料塔中进行水解,同时用降膜分离器将生成的氯化氢收集直接用于氯甲烷的生产原料,水解得到的产物溶液直接在循环槽中进行层析,分离出烯丙基甲基二氯硅烷水解物待用;步骤2:将第一步中制备的烯丙基甲基二氯硅烷水解物中加入浓度为35%-38%的氢氧化钠溶液中,在100-110℃的氮气保护下反应3-4h,得到胶液,然后升温至170-180℃搅拌反应6-7h,然后向反应容器中加入浓度为80%的磷酸溶液,缓慢抽真空,然后升温至200-210℃,反应至无馏分蒸出时停止反应,得到二羟基聚甲基烯丙基硅氧烷;其中每升烯丙基甲基二氯硅烷水解物中加入35%-38%的氢氧化钠溶液85-90mg,加入浓度为80%的磷酸溶液110-120mg;步骤3:将第二步中制备的二羟基聚甲基烯丙基硅氧烷和二氯甲烷加入反应容器中,升温至90-100℃搅拌溶解,然后向反应容器中逐滴加入y-氨丙基甲基二乙氧基硅烷,滴加完全后升温回流反应48-52h,然后降低至室温,向其中加入冰醋酸调节溶液的ph=6-7,接着进行过滤洗涤,得到氨基烯丙基聚硅氧烷;其中每克二羟基聚甲基烯丙基硅氧烷中加入12.3-13.1gy-氨丙基甲基二乙氧基硅烷;二羟基聚甲基烯丙基硅氧烷端侧含有两个羟基,同时y-氨丙基甲基二乙氧基硅烷含量两个烷氧基,在高温下脱去烷氧键与二羟基聚甲基烯丙基硅氧进行聚合,进而使得氨基引入聚硅氧烷中,二羟基聚甲基烯丙基硅氧烷结构规则,具有较强的非极性,进而使得其溶解性能较低,通过向聚硅氧烷中引入氨基,由于氨基具有较强的极性,进而破坏了氨基聚硅氧烷的有序性,提高了聚合物的溶解能力,并且氨基的引入提高了聚合物的作用位点;1-烯丙基-3-羟基丙烷-2基磷酸二氢的具体制备过程如下:将烯丙基缩水甘油醚和水以质量比为1:0.85-0.87的比例混合,同时向其中加入硫酸钠,搅拌溶解后升温至降温50-55℃,然后向其中分四次加入五氧化二磷,每次加入五氧化二磷后保温回流反应30-40min,接着进行下一次五氧化二磷的加入,完全加入后恒温回流反应6-7h,然后将产物用饱和氯化钠洗涤后加入乙酸乙酯中提取,并将得到的油相进行减压蒸馏,得到1-烯丙基-3-羟基丙烷-2基磷酸二氢;其中每摩尔烯丙基缩水甘油醚中加入五氧化二磷0.51-0.52mol,加入硫酸钠1-1.5gg,同时每次加入五氧化二磷的量相同;由于五氧化二磷加入热水中生成磷酸释放大量的热,进而控制磷酸加入量防止反应过快发生爆炸,同时生成的磷酸在较低温度下能够与烯丙基缩水甘油醚中的环氧基团进行开环反应,进而使得磷酸基团引入产物中,同时烯丙基缩水甘油醚开环后生成醇羟基,其中的醇羟基与磷酸基团在较高温度下才能进行酯化反应,进而实现聚合,通过控制反应容器的温度和五氧化二磷的分次加入进而控制热量的放出,控制反应体系的温度变化,同时通过加入阻聚剂硫酸钠,可以有效防止开环后的羟基与磷酸进行反应发生聚合,进而使得每个烯丙基缩水甘油醚上接枝一个磷酸分子。本发明的有益效果:通过制备的氨基化烯丙基聚硅氧烷,通过在氨基烯丙基聚硅氧烷链上通过自由基聚合引入1-烯丙基-3-羟基丙烷-2-基磷酸二氢阻燃剂,使得阻燃剂能够均布在氨基烯丙基聚硅氧烷链的不饱和单体上,进而使得引入的阻燃剂含量较高,并且分散均匀,提高了硅橡胶的阻燃性能,同时通过亲核加成作用在氨基烯丙基聚硅氧烷链上引入氟元素,不仅能够使得引入的氟元素分散均匀,同时提高了氟元素的引入量,进而提高了硅橡胶的抗腐蚀性能,解决了现有的硅橡胶材料通过混合熔炼的方法添加阻燃剂、抗腐蚀剂等实现阻燃耐老化的性能,但是由于硅橡胶的相容性较差,添加的助剂容易分散不均匀,进而造成其性能下降的问题。本发明在改性硅橡胶的制备过程引入的1-烯丙基-3-羟基丙烷-2-基磷酸二氢支链上含有羟基,同时氨基烯丙基聚硅氧烷的主链两端含有羟基,均能够与六亚甲基二异氰酸酯反应,通过六亚甲基二异氰酸酯与的交联作用使得相邻的硅胶链之间以及硅胶链内部之间交联成密实的网状结构,从硅橡胶本身的内部分子结构进行改进,从根本上提高了改性硅胶的韧性和耐磨性能,进而解决了现有的硅橡胶加入耐磨剂与硅橡胶相容性差,分散不均匀,长期使用时耐磨性能较差的问题。附图说明为了便于本领域技术人员理解,下面结合附图对本发明作进一步的说明。图1为本发明氨基烯丙基聚硅氧烷反应结构式;图2为本发明1-烯丙基-3-羟基丙烷-2基磷酸二氢反应结构式;图3为阻燃耐磨改性硅胶反应过程中的局部反应结构式;图4为阻燃耐磨改性硅胶反应过程中的局部反应结构式。具体实施方式请参阅图1-4,结合如下实施例进行详细说明:实施例1:氨基烯丙基聚硅氧烷的具体制备过程如下:步骤1:将烯丙基甲基二氯硅烷加入饱和浓盐酸中混合均匀,然后将混合后的物料加入填料塔中进行水解,同时用降膜分离器将生成的氯化氢收集直接用于氯甲烷的生产原料,水解得到的产物溶液直接在循环槽中进行层析,分离出烯丙基甲基二氯硅烷水解物待用;步骤2:将1l第一步中制备的烯丙基甲基二氯硅烷水解物中加入85mg浓度为35%-38%的氢氧化钠溶液中,在100-110℃的氮气保护下反应3-4h,得到胶液,然后升温至170-180℃搅拌反应6-7h,然后向反应容器中加入110mg浓度为80%的磷酸溶液,缓慢抽真空,然后升温至200-210℃,反应至无馏分蒸出时停止反应,得到二羟基聚甲基烯丙基硅氧烷;步骤3:将1kg第二步中制备的二羟基聚甲基烯丙基硅氧烷和30l二氯甲烷加入反应容器中,升温至90-100℃搅拌溶解,然后向反应容器中逐滴加入12.3kgy-氨丙基甲基二乙氧基硅烷,滴加完全后升温回流反应48-52h,然后降低至室温,向其中加入冰醋酸调节溶液的ph=6-7,接着进行过滤洗涤,得到氨基烯丙基聚硅氧烷。1-烯丙基-3-羟基丙烷-2基磷酸二氢的具体制备过程如下:将1.14kg烯丙基缩水甘油醚和0.97kg水混合,同时向其中加入10g硫酸钠,搅拌溶解后升温至降温50-55℃,然后向其中分四次加入724g五氧化二磷,每次加入五氧化二磷的量相同,每次加入五氧化二磷后保温回流反应30-40min,接着进行下一次五氧化二磷的加入,完全加入后恒温回流反应6-7h,然后将产物用饱和氯化钠洗涤后加入乙酸乙酯中提取,并将得到的油相进行减压蒸馏,得到1-烯丙基-3-羟基丙烷-2基磷酸二氢,产率达到92.3%。实施例2:氨基烯丙基聚硅氧烷的具体制备过程与实施例1相同,将实施例1中添加的12.3kgy-氨丙基甲基二乙氧基硅烷替换为14kgy-氨丙基甲基二乙氧基硅烷。烯丙基-3-羟基丙烷-2基磷酸二氢的具体制备过程与实施例1相同,将实施例1中添加的724g五氧化二磷替换为1.448kg,产率达到92.5%。实施例3:氨基烯丙基聚硅氧烷的具体制备过程与实施例1相同,将实施例1中添加的12.3kgy-氨丙基甲基二乙氧基硅烷替换为10kgy-氨丙基甲基二乙氧基硅烷。烯丙基-3-羟基丙烷-2基磷酸二氢的具体制备过程与实施例1相同,将实施例1中添加的724g五氧化二磷替换为692g,产率达到85.2%。由此可知当烯丙基缩水甘油醚与五氧化二磷的摩尔比为1:0.51-0.52mol时产率达到最高值,当继续添加五氧化二磷时产率不变。实施例4:一种改性硅胶密封圈的制备工艺,具体制备过程如下:第一步,向反应容器中通氮气20-30min,然后将1kg实施例1制备的氨基烯丙基聚硅氧烷和50l二氯甲烷加入反应釜中,同时向其中加入162g偶氮二异丁腈,混合均匀后升温至110-120℃,然后逐滴向反应釜中加入268g实施例1制备的1-烯丙基-3-羟基丙烷-2-基磷酸二氢,边滴加边剧烈搅拌,滴加完全后恒温搅拌反应10-12h,得到棕色产物溶液;第二步,向第一步中制备的棕色产物溶液中加入123g2-氨基-5-氟吡啶,升温至80-90℃搅拌回流20-30min,然后向反应容器中逐滴加入68g乙二醛溶液,滴加完全后恒温反应8-9h,然后降温至40-50℃,逐滴向反应容器中滴加490g六亚甲基二异氰酸酯,边滴加边剧烈搅拌,滴加完全后恒温搅拌反应2-3h,然后进行过滤,再依次用丙酮和乙醇洗涤后烘干,得到阻燃耐磨改性硅胶;第三步,将第二步中制备的阻燃耐磨改性硅胶加入开炼机中,在170-180℃下硫化5-7min,然后进行加工成型,得到改性硅胶密封圈。实施例5:一种改性硅胶密封圈的制备工艺与实施例1相同,将实施例1第一步中使用的实施例1制备的氨基烯丙基聚硅氧烷替换为实施例2制备的氨基烯丙基聚硅氧烷。实施例6:一种改性硅胶密封圈的制备工艺与实施例1相同,将实施例1第一步中使用的实施例1制备的氨基烯丙基聚硅氧烷替换为实施例3制备的氨基烯丙基聚硅氧烷。实施例7:一种改性硅胶密封圈的制备工艺,具体制备过程如下:将1kg实施例1制备的氨基烯丙基聚硅氧烷和268g实施例1制备的1-烯丙基-3-羟基丙烷-2-基磷酸二氢加入开炼机中,在120-130℃下混合炼制3-5min,然后向其中加入123g2-氨基-5-氟吡啶的在120-130℃下混合炼制3-5min后升温至170-180℃下硫化5-7min,然后进行加工成型,得到改性硅胶密封圈。实施例8:将实施例1-3中制备的氨基烯丙基聚硅氧烷通过x射线光电子能谱进行分析,结果如表1所示:表1氨基烯丙基聚硅氧烷元素分析结果实施例1实施例2实施例3氮元素含量5.11%5.36%4.85%由表1可知,实施例2中添加的y-氨丙基甲基二乙氧基硅烷的含量较多时,氨基烯丙基聚硅氧烷中引入的氨基含量较多,而实施例3中y-氨丙基甲基二乙氧基硅烷的含量较少时,氨基烯丙基聚硅氧烷中引入的氨基含量较少。实施例9:按照gb/t10707-2008测定实施例4-7中制备的改性硅橡胶的极性氧指数,同时按照gb/t529-19981测定改性硅橡胶的拉伸性能,测定结果如表2所示:表2实施例4-7中制备的改性硅橡胶的性能测定结果实施例4实施例5实施例6实施例7极性氧指数%36.235.136.828.3拉伸强度mpa12.611.512.88.7由表2可知,实施例4中在氨基烯丙基硅氧烷的链上直接通过聚合反应引入阻燃剂烯丙基-3-羟基丙烷-2基磷酸二氢,使得制备的改性硅橡胶链上引入大量的阻燃剂,并且阻燃剂分布均匀,进而使得制备的改性硅橡胶阻燃性能较高,极限氧指数为36.2%,同时经过六亚甲基二异氰酸酯交联作用使得相邻的硅胶链之间以及硅胶链内部之间交联成密实的网状结构,进而提高了改性硅胶的拉伸强度和耐磨性能;而实施例5中由于氨基烯丙基硅氧烷制备时引入的氨基含量较多,造成硅橡胶链中引入的阻燃剂平均含量降低,进而使得其阻燃性能降低,阻燃剂的降低导致六亚甲基二异氰酸酯交联时内部提供的作用位点减少,进而使得制备的硅橡胶拉伸强度降低;实施例6中由于氨基烯丙基硅氧烷制备时引入的氨基含量较少,造成硅橡胶链中引入的阻燃剂平均含量升高,进而使得其阻燃性能升高,阻燃剂的含量升高导致六亚甲基二异氰酸酯交联时内部提供的作用位点增多,进而使得制备的硅橡胶拉伸强度提高;而实施例7中直接通过混合炼制制备的硅橡胶由于阻燃剂分散不均匀造成其阻燃性能降低,同时没有经过交联固化作用,进而使得其强度降低。实施例10:将实施例4-7中制备的改性硅橡胶分别在苯、氯仿、15%的稀盐酸溶液、10%的氢氧化钠溶液、12%的氯化钠溶液中分别浸泡10天、20天和30天后取出,然后测定浸泡前后改性硅橡胶的拉伸强度,结果如表3所示:表3改性硅橡胶在有机溶剂和酸碱盐中浸泡不同时间后拉升强度测定结果由表3可知,实施例4制备的改性硅橡胶具有较高的耐受性能,实施例5制备的改性硅橡胶中由于氨基烯丙基硅氧烷制备时引入的氨基含量较多,进而造成其中引入的2-氨基-5-氟吡啶含量增多,使得改性硅橡胶中氟元素的含量提高,进而使得改性硅橡胶的耐溶剂性能和耐酸碱盐性能提高,而实施例6中制备的改性硅橡胶中由于氨基烯丙基硅氧烷制备时引入的氨基含量较少,进而造成其中引入的2-氨基-5-氟吡啶含量减少,使得改性硅橡胶中氟元素的含量降低,进而使得改性硅橡胶的耐溶剂性能和耐酸碱盐性能降低,同时实施例7中直接通过混合添加2-氨基-5-氟吡啶,造成其不能均匀分散,进而使得局部耐受性降低,老化加快,局部抗拉伸强度降低就会造成改性硅橡胶的拉伸强度降低。以上公开的本发明优选实施例只是用于帮助阐述本发明。优选实施例并没有详尽叙述所有的细节,也不限制该发明仅为所述的具体实施方式。显然,根据本说明书的内容,可作很多的修改和变化。本说明书选取并具体描述这些实施例,是为了更好地解释本发明的原理和实际应用,从而使所属
技术领域:
技术人员能很好地理解和利用本发明。本发明仅受权利要求书及其全部范围和等效物的限制。当前第1页12