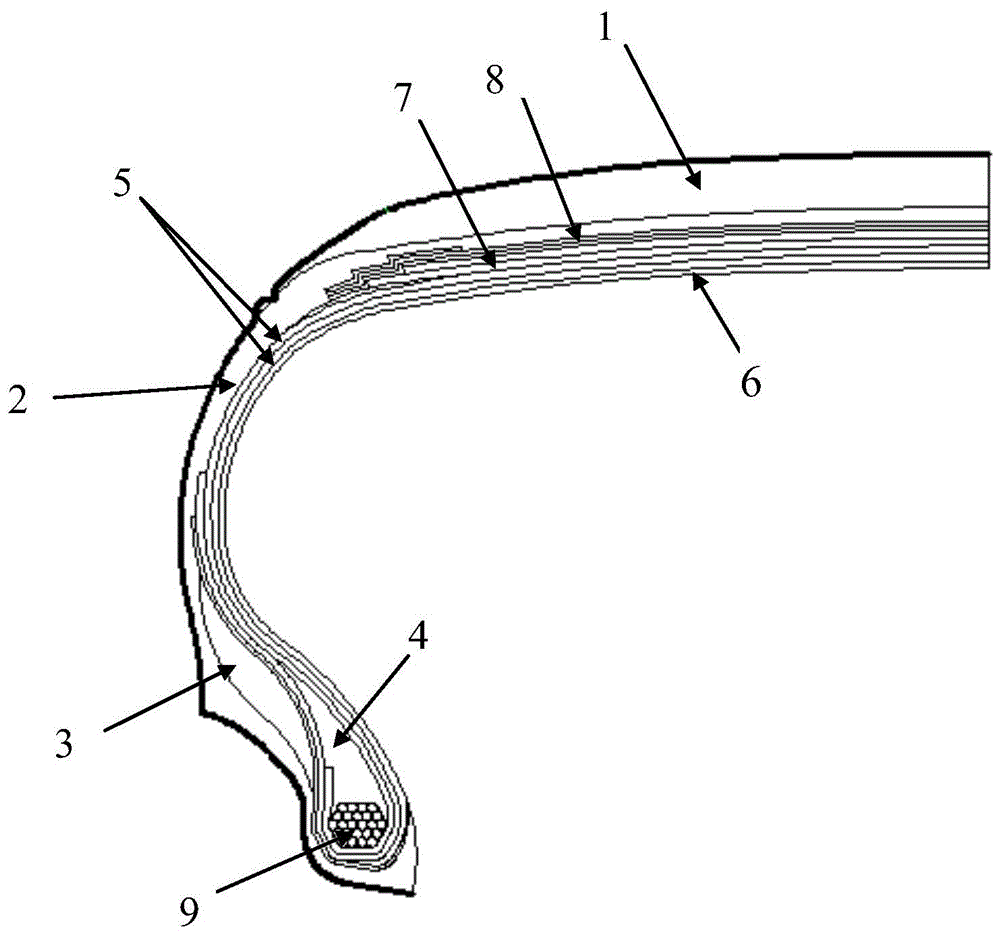
本发明属于轮胎制造领域,尤其涉及一种抗湿滑飞行汽车轮胎胎面配方及抗湿滑飞行汽车轮胎。
背景技术:
:近年来,随着人口数量和汽车数量的大幅度增多,道路交通越来越拥挤,人们迫切的需要解决这一窘境。目前,全球有二十多家公司正在研发飞行汽车,现代意义的飞行汽车有望从在科幻影片中的交通工具变为现实。而未来飞行汽车的大众化可以在一定程度上缓解这种日益严峻的地面交通压力。飞行汽车需要兼顾道路行驶和低空飞行技术,双重行驶功能可以实现从地上行驶变为天上飞行的自由切换,而这种双重行驶功能则对轮胎的性能提出了更高的要求。此外,随着飞行汽车研发技术的发展,要求飞行汽车可以适应各种恶劣路况,其中最为常见的为雨天。目前的道路车辆用轮胎发展较早,技术较成熟,可以满足车辆行驶时的舒适性和操控性,但却不具有飞机轮胎的高强度和高耐磨性,无法适应飞行汽车起飞和降落过程中强大的冲击力和瞬间的高速,而目前的飞机用轮胎在满足起飞降落要求的情况下又难以满足道路汽车行驶时的舒适性和操控性的要求,并且如遇雨天,更无法满足恶劣路况的行驶要求。因此,为满足飞行汽车进一步研发的需求,急需研发一种适用于飞行汽车并且可以提高雨天行驶性能的轮胎。技术实现要素:本发明针对上述的技术问题,提出一种抗湿滑飞行汽车轮胎胎面配方及抗湿滑飞行汽车轮胎。为了达到上述目的,本发明一方面提供一种抗湿滑飞行汽车轮胎胎面配方,包括生胶体系、填充体系、防老体系、硫化体系、增塑体系以及硅烷偶联剂,按重量份数计,所述生胶体系包括50~100份天然橡胶、0~40份丁苯橡胶和0~10份顺丁橡胶,所述天然橡胶、所述丁苯橡胶和所述顺丁橡胶共计100份;所述填充体系包括15~30份炭黑和30~50份白炭黑;所述增塑体系包括0~20份增塑材料;所述胎面配方还包括特殊功能助剂,所述特殊功能助剂包括1~3份粘合剂和1~6份功能树脂,所述功能树脂为含有共轭烯烃结构或闭合共轭体系结构的不饱和树脂。作为优选,按重量份数计,所述特殊功能助剂包括3份粘合剂ra-65和5份间甲树脂。作为优选,所述丁苯橡胶为溶聚丁苯橡胶,并且按质量分数计,所述溶聚丁苯橡胶包括含量为20%~50%的乙烯基和含量为20%~40%的苯乙烯。作为优选,所述炭黑的平均粒径在10~25nm之间,所述白炭黑的比表面积为160~200m2/g。作为优选,按质量分数计,所述天然橡胶中顺-1,4-聚异戊橡胶含量≥97%,所述顺丁橡胶为顺式含量≥98%的高顺式顺丁橡胶。作为优选,所述硫化体系包括2~6份氧化锌、1~4份硬脂酸、1~2.5份普通硫磺和/或1~2.5份充油硫磺ot20、1~3份n-叔丁基-2-苯并噻唑次磺酰胺和/或1~3份n-环己基-2-苯并噻唑次磺酰胺、0~1份抗硫化返原剂,以及1~3份二苯胍。作为优选,所述防老体系包括1~3份喹啉类防老剂、1~3份对苯二胺类防老剂和1~3份微晶石蜡。本发明另一方面提供一种抗湿滑飞行汽车轮胎,包括由上述任一项所述的抗湿滑飞行汽车轮胎胎面配方制备获得的胎面。作为优选,所述抗湿滑飞行汽车轮胎的胎体线选用尼龙与芳纶混纺,带束层选用芳纶。与现有技术相比,本发明的优点和积极效果在于:1、本发明针对飞行汽车的双重行驶要求以及雨天行驶所需的抗湿滑性能,有针对性地优化胎面配方,提出一种抗湿滑飞行汽车轮胎胎面配方。在该配方中通过加入特殊功能助剂,引入新的交联网络,提高所制备胎面胶料的模量与强度;通过调整生胶体系的配比,提高所制备胎面胶料的强度与磨耗性能;通过引入白炭黑、硅烷偶联剂以及丁苯橡胶配合使用,在保证飞行汽车轮胎所需性能的基础上,提高了抗湿滑性能。2、本发明的所提供的抗湿滑飞行汽车轮胎,通过胎面的特殊配方设计并配合轮胎的结构设计,使得制备获得的轮胎既可以满足道路车辆用轮胎的舒适性和操控性,又可以满足飞机用轮胎的高强度和高耐磨性,此外,还具有优异的抗湿滑性能,可以更好地满足飞行汽车轮胎的性能要求以及雨天行驶的要求。附图说明图1为本发明实施例所提供的抗湿滑飞行汽车轮胎的切面剖面图;图2为本发明实施例所提供的具有辅助模块的成型鼓的结构示意图;图中:1、胎面;2、胎侧;3、胎侧支撑胶;4、三角胶;5、胎体;6、内衬层;7、带束层;8、冠带条;9、钢丝圈;10、成型鼓;101、辅助模块。具体实施方式下面将对本发明实施例中的技术方案进行清楚、完整地描述,显然,所描述的实施例仅仅是本发明一部分实施例,而不是全部的实施例。基于本发明中的实施例,本领域普通技术人员在没有做出创造性劳动前提下所获得的所有其他实施例,都属于本发明保护的范围。本发明实施例一方面提供一种抗湿滑飞行汽车轮胎胎面配方,包括生胶体系、填充体系、防老体系、硫化体系、增塑体系以及硅烷偶联剂。其中,按重量份数计,所述生胶体系包括50~100份天然橡胶、0~40份丁苯橡胶和0~10份顺丁橡胶,所述天然橡胶、所述丁苯橡胶和所述顺丁橡胶共计100份;所述填充体系包括15~30份炭黑和30~50份白炭黑;所述增塑体系包括0~20份增塑材料;所述胎面配方还包括特殊功能助剂,所述特殊功能助剂包括1~3份粘合剂和1~6份功能树脂,所述功能树脂为含有共轭烯烃结构或闭合共轭体系结构的不饱和树脂。在上述实施例中,通过调整生胶体系的配比,提高所制备胎面胶料的强度与磨耗性能。所述生胶体系的重量份数为100份,具体地,在所选用的生胶体系中,为使所制备的胎面具有高强度,将天然橡胶的含量限定在上述范围内,但可以理解的是,所述天然橡胶的含量还可以为60份、70份、80份、90份等,本领域技术人员可以根据实际所要获得的性能在上述范围内进行选择。可在生胶体系中加入丁苯橡胶与天然橡胶并用,在充分发挥天然橡胶优异性能的同时,进一步提高胎面胶料的抗湿滑、耐磨、耐老化以及硫化性能等,但可以理解的是,所述丁苯橡胶的加入量还可以为10份、20份、30份等,本领域技术人员可根据实际需要在上述范围内进行选择。此外,为了提高胎面胶料的耐磨性能,可在生胶体系中加入顺丁橡胶,本领域技术人员可以根据实际所需要的耐磨性能,在上述范围内进行调整,例如顺丁橡胶的加入量还可以为5份、8份等。在上述实施例中,通过加入特殊功能助剂,引入新的化学交联网络,提高了胶料的交联密度,使交联键类型多样化,提高所制备胎面胶料的模量与强度。其中,所述粘合剂可以根据需要选择,例如ra-65、hmt-80、hmt等以及其它可实现该功能的粘合剂,所述粘合剂的加入量在上述范围内还可以为1.5份、2份、2.5份等,所述功能树脂的加入量在上述范围内还可以为2份、3份、4份、5份等,本领域技术人员可以进行合理选择。在上述实施例所选用的填充体系中,通过添加炭黑和白炭黑作为补强材料,在提高胎面胶料的耐磨性能的同时,可以提高胎面胶料的抗湿滑性能;其中,所述炭黑的加入量还可以为20份、22份、25份、28份等,所述白炭黑的加入量还可以为35份、40份、45份等,本领域技术人员可根据实际所需要的性能在上述范围内进行调整。此外,加入增塑材料与补强材料相配合,改善橡胶的加工性能,增塑材料可以根据需要选择,本实施例优选采用橡胶加工油,所述增塑材料的加入量还可以为5份、10份、15份等,本领域技术人员可根据实际其概况在上述范围内进行选择。在上述实施例中,为配合白炭黑,加入硅烷偶联剂作为白炭黑与橡胶大分子之间的“桥梁”,有利于白炭黑在橡胶基体中的稳定均匀分散,以提供最佳的湿地抓地性能和低生热性能。本发明上述实施例所提供的抗湿滑飞行汽车轮胎胎面配方,通过调整各体系的配比,并且引入白炭黑和硅烷偶联剂,使得各体系内及体系间的组分可以更好地协同作用,在保证所需性能的基础上,进一步提高胎面胶料的抗湿滑性能。此外,通过添加特殊功能助剂,引入新的化学交联网络,进一步提高胎面胶料的模量与强度。通过以上,使得该胎面配方所制备获得的胶料具有高强度、高抗湿滑性以及舒适性,为成功研发适用于具有双重行驶功能及满足雨天行驶要求的抗湿滑飞行汽车的轮胎奠定了基础。在一优选实施例中,按重量份数计,所述特殊功能助剂包括3份粘合剂ra-65和5份间甲树脂。为进一步提高模量与强度,选用间甲树脂作为功能树脂添加,并且将粘合剂ra-65和间甲树脂的含量分别限定为3份和5份,使得所形成的交联网络可以更好地发挥作用。在一优选实施例中,所述丁苯橡胶为溶聚丁苯橡胶,并且按质量分数计,所述溶聚丁苯橡胶包括含量为20%~50%的乙烯基和含量为20%~40%的苯乙烯。优选较高的乙烯基含量,提高所制备的胎面胶料的耐磨性能;苯乙烯具有较高的刚度,能够破开湿地路面的水膜,从而提高湿地抓地性能,进一步提高抗湿滑性能。可以理解的是,所述乙烯基的含量还可以为24%、30%、35%、40%、45%等,所述苯乙烯的含量还可以为25%、30%、35%、38%等,本领域技术人员可以在上述范围内进行合理选择。在一优选实施例中,所述炭黑的平均粒径在10~25nm之间,所述白炭黑的比表面积为160~200m2/g。通过优选较小粒径的炭黑,进一步提高胎面胶料的耐磨性能,此外,优选上述比表面积范围的白炭黑,通过白炭黑在橡胶基体中的均匀分散,进一步提高胎面胶料的抗湿滑性能,同时进一步降低胶料的生热。在一优选实施例中,所述天然橡胶中含有质量分数≥97%的顺-1,4-聚异戊橡胶。本实施例中,天然橡胶主要由顺-1,4-聚异戊橡胶组成,具有优异的拉伸和耐撕裂性能。在一优选实施例中,按质量分数计,所述顺丁橡胶为顺式含量≥98%的高顺式顺丁橡胶。选用高顺式顺丁橡胶,可以改善低温性能,提高磨耗性能。在一优选实施例中,所述硫化体系包括2~6份氧化锌、1~4份硬脂酸、1~2.5份普通硫磺和/或1~2.5份充油硫磺ot20、1~3份n-叔丁基-2-苯并噻唑次磺酰胺(简称:促进剂ns)和/或1~3份n-环己基-2-苯并噻唑次磺酰胺(简称:促进剂cz)、0~1份抗硫化返原剂,以及1~3份二苯胍(简称:促进剂dpg)。上述实施例所选用的硫化体系为更有利于上述胎面配方的硫化体系,可以使得硫化后的胎面胶料具备优异的力学性能。其中,可以理解的是,所述氧化锌的含量还可以为3份、4份、5份等,所述硬脂酸的含量还可以为1.5份、2份、2.5份、3份等,所述普通硫磺的含量还可以为1.5份、2份等,所述充油硫磺ot20的含量还可以为1.5份、2份等,所述促进剂ns的含量还可以为1.5份、2份、2.5份等,所述促进剂cz的含量还可以为1.5份、2份、2.5份等,所述抗硫化返原剂的含量还可以为0.3份、0.5份、0.8份等,所述促进剂dpg的含量还可以为1.5份、2份、2.5份等,本领域技术人员可以根据实际的硫化需要将上述各硫化剂在上述相应范围内分别进行调整。在一优选实施例中,所述防老体系包括1~3份喹啉类防老剂、1~3份对苯二胺类防老剂中和1~3份微晶石蜡。上述防老剂为配合其它体系所优选的,但可以理解的是,本领域技术人员还可以合理选择其它可替代的防老剂。本申请实施例的另一方面提供一种抗湿滑飞行汽车轮胎用胎面,所述胎面根据上述任一实施例所述的抗湿滑飞行汽车轮胎胎面配方制备获得。本实施例制备获得的胎面由于其胎面配方的优化设计,使其具有高强度,并且同时兼备优异的抗湿滑性能、舒适性能和操控性能,适用于飞行汽车轮胎并且可以满足雨天行驶的要求。本申请实施例的再一方面提供一种抗湿滑飞行汽车轮胎,所述抗湿滑飞行汽车轮胎包括由上述任一实施例所述的飞行汽车轮胎胎面配方制备获得的胎面。在一优选实施例中,所述抗湿滑飞行汽车轮胎的胎体线选用尼龙、芳纶或尼龙与芳纶混纺中的一种。尼龙耐热性好,耐冲击强度高;芳纶强力高,抗刺扎,耐曲挠性能好。进一步地,胎体线优选为尼龙与芳纶混纺,所选用的尼龙与芳纶混纺则结合了两者的优点,强度高,高温时强度不衰减,尺寸稳定性高。高强度以及高温强度不衰减给抗湿滑飞行汽车轮胎带来了高耐久性;高的尺寸稳定性则给驾乘带来更舒适的体验。在一优选实施例中,所述抗湿滑飞行汽车轮胎的带束层选用钢丝或芳纶,更优选为芳纶。芳纶强力高,抗刺扎,热力学和化学稳定性好,并且甚至可以满足超过极端性能的要求;芳纶在承受张力、外应力以及在曲挠作用的条件下生热低。基于以上优点,带束层选用芳纶材料,可以使抗湿滑飞行汽车轮胎适应飞行汽车起飞和降落过程中强大的冲击力和瞬间高速,此外,芳纶的超高尺寸稳定性,可以保证轮胎均匀受压,进一步提高驾乘的舒适性。本申请实施例所提供的抗湿滑飞行汽车轮胎,在结构设计方面,充分考虑到轮胎的舒适性与操控性,采用半钢轮胎结构设计的工艺,结合飞行汽车轮胎的飞行起落方面的特殊性能要求,进行了相应的调整,配合上述实施例所制备的适用于抗湿滑飞行汽车轮胎的特殊胎面,获得能同时满足陆地行驶和飞行降落的双重驾驶要求以及雨天行驶要求的轮胎。所述抗湿滑飞行汽车轮胎的规格通常为14-17寸,最高使用速度可达320km/h,正常行驶时负荷为2500n,起飞时为3500n。在一优选实施例中,所述抗湿滑飞行汽车轮胎由以下工艺制备获得,具体包括部件工艺、成型工艺和硫化工艺。制备获得的抗湿滑飞行汽车轮胎的切面剖面图如图1所示。(1)部件工艺a)胎面1:由上述实施例的胎面配方制备获得;b)胎侧2:上胎侧胶料厚度6mm;c)胎侧支撑胶3:轮胎子口部位增加胎侧支撑胶3,支撑胶形状根据轮胎轮廓曲线进行设计;具体形状设计方法为本领域公知常识,此处不作解释。d)三角胶4:压出三角胶4时三角胶口型板一侧开槽,提高三角胶4的弯曲性能,减少轮胎硫化过程中内部胶料的流动;e)胎体5:胎体5为两层结构;f)内衬层6:采用双层胶料设计,过渡层比气密层宽20mm;g)带束层7:边部使用包胶封边设计;h)冠带条8:采用3层冠带条设计,冠带条宽度10mm,缠绕形式为环形正周缠绕;i)钢丝圈9:单根钢丝缠绕的钢丝圈,缠绕截面近似圆形。(2)成型工艺采用一步法侧包冠成型工艺,使用定制开发的具有辅助模块的成型鼓,即如图2所示,在成型鼓10两侧分别增加辅助模块101,该辅助模块101用于在成型过程中支撑两侧的半部件。(3)硫化工艺采用140℃~160℃低温硫化,一次定型压力为0.05~0.08mpa,二次定型压力为0.06~0.10mpa。为了更清楚详细地介绍本发明实施例所提供的抗湿滑飞行汽车轮胎胎面配方、胎面及轮胎,下面将结合具体实施例进行描述。实施例1本实施例所提供的抗湿滑飞行汽车轮胎,包括轮胎的配方设计、结构设计和工艺设计。(1)配方设计:参见表1实施例1。(2)结构设计:胎体线选用尼龙与芳纶混纺;带束层选用芳纶。(3)工艺设计:(i)部件工艺a)胎面:通过表1实施例1的胎面配方制备获得胎面a;b)胎侧:上胎侧胶料厚度6mm;c)胎侧支撑胶:轮胎子口部位增加胎侧支撑胶,支撑胶形状根据轮胎轮廓曲线进行设计。d)三角胶:压出三角胶时三角胶口型板一侧开槽,提高三角胶的弯曲性能,减少轮胎硫化过程中内部胶料的流动;e)胎体:胎体为两层结构;f)内衬层:采用双层胶料设计,过渡层比气密层宽20mm;g)带束层:边部使用包胶封边设计;h)冠带条:采用3层冠带条设计,冠带条宽度10mm,缠绕形式为环形正周缠绕;i)钢丝圈:单根钢丝缠绕的钢丝圈,缠绕截面近似圆形。(ii)成型工艺采用一步法侧包冠成型工艺,使用定制开发的具有辅助模块的子午线轮胎成型机,即在成型鼓两侧增加支撑。(iii)硫化工艺采用140℃低温硫化,一次定型压力为0.05mpa,二次定型压力为0.07mpa。通过上述方法制备获得规格为16寸的抗湿滑飞行汽车轮胎a。实施例2(1)配方设计:参见表1实施例2。(2)结构设计:同实施例1。(3)工艺设计:(i)部件工艺:通过表1实施例2的胎面配方制备获得胎面b,其它同实施例1;(ii)成型工艺设计:同实施例1;(iii)硫化工艺:采用150℃低温硫化,一次定型压力为0.06mpa,二次定型压力为0.08mpa。通过上述方法制备获得规格为16寸的抗湿滑飞行汽车轮胎b。实施例3(1)配方设计:参见表1实施例3。(2)结构设计:同实施例1。(3)工艺设计:(i)部件工艺:通过表1实施例3的胎面配方制备获得胎面c,其它同实施例1;(ii)成型工艺设计:同实施例1;(iii)硫化工艺:采用160℃低温硫化,一次定型压力为0.07mpa,二次定型压力为0.10mpa。通过上述方法制备获得规格为16寸的抗湿滑飞行汽车轮胎c。实施例4(1)配方设计:参见表1实施例4。(2)结构设计:同实施例1。(3)工艺设计:(i)部件工艺:通过表1实施例4的胎面配方制备获得胎面d,其它同实施例1;(ii)成型工艺设计:同实施例1;(iii)硫化工艺:采用150℃低温硫化,一次定型压力为0.07mpa,二次定型压力为0.10mpa。通过上述方法制备获得规格为16寸的抗湿滑飞行汽车轮胎d。实施例5(1)配方设计:参见表1实施例5。(2)结构设计:同实施例1。(3)工艺设计:(i)部件工艺:通过表1实施例5的胎面配方制备获得胎面e,其它同实施例1;(ii)成型工艺设计:同实施例1;(iii)硫化工艺:采用150℃低温硫化,一次定型压力为0.07mpa,二次定型压力为0.10mpa。通过上述方法制备获得规格为16寸的抗湿滑飞行汽车轮胎e。对比例1选用本公司生产的普通抗湿滑汽车轮胎,规格为205/55zr1694w,其中,胎面配方包括80phrsbr、20phrbr、60phr白炭黑、8phrsi69、2phr氧化锌、2phr硬脂酸、1phr微晶石蜡、25phrtdae油、3phr防老剂4020、2phr防老剂rd、2phrs、2.5phr促进剂cz、2phrdpg;制备工艺采用普通半钢子午线轮胎的制备工艺。对比例2选用本公司生产的飞机轮胎,规格为380×150-160,其中,胎面配方采用传统的飞机轮胎配方;成型工艺采用套筒法实现胎胚成型,硫化工艺采用过热水工艺。表1实施例1-5胎面配方性能测试1、轮胎胎面力学性能测试:本发明实施例1-5所生产的胎面与对比例1-2的胎面的进行性能测试的结果如表2所示。表2胎面力学性能测试结果由以上力学性能测试结果可以看出,上述实施例1-5所制备获得的胎面的力学性能介于现有的普通汽车轮胎和飞机轮胎之间,包含该类胎面的抗湿滑飞行汽车轮胎不仅可以满足地面行驶和飞行的双重要求,而且其湿滑性能与传统的飞机轮胎相比有大幅提升,能够满足雨天行驶的要求,并且部分实施例的湿滑性能非常接近普通抗湿滑汽车轮胎的湿滑性能,特别是实施例5,其具有较好的湿地性能,同时拉伸强度、300%定伸应力能够达到较高的水平,性能最优。2、飞行汽车轮胎性能测试:对本发明实施例制备获得的抗湿滑飞行汽车轮胎a-e分别进行两种试验,一种按照轿车子午线轮胎实验程序方法ece-r30法规;一种按照中国民用航空技术标准规定ctso-c62e法规。根据两种试验方法检验该抗湿滑飞行汽车轮胎是否既符合轿车胎的标准,又符合航空胎标准。(1)ece-r30法规的高速性能试验首先将抗湿滑飞行汽车轮胎按照轿车轮胎的测试方式进行试验,步骤如以下表3、表4所示。表3负荷、高速实验步骤待抗湿滑飞行汽车轮胎通过第一步试验,开始进入表4所示的下一步试验。表4最高速度超过300km/h的轿车轮胎高速性能第二次试验程序试验结果:本发明实施例1-5所制备获得的抗湿滑飞行汽车轮胎a-e在试验完成后,没有出现胎面分离、脱层、帘线分离、崩花或帘线断裂等问题,试验结束6小时后,测试轮胎外直径与试验前相比不超过±3.5%,顺利通过试验,说明该抗湿滑飞行汽车轮胎在地面行驶时完全达到了半钢轮胎在地面行驶时的标准。(2)ctso-c62e法规航空轮胎测试试验按照表5中的测试程序对实施例1-5制备获得的抗湿滑飞行汽车轮胎进行测试。表5航空轮胎测试程序试验项目试验速度/(km/h)试验负荷/(n)试验时间/(s)循环次数起飞0~320350069.750次超载起飞0~320525069.71次试验结果:本发明实施例1-5所制备获得的抗湿滑飞行汽车轮胎a-e经过上述测试后,轮胎未出现除胎面正常磨损以外的其它可见损坏现象,成功通过测试,说明该抗湿滑飞行汽车轮胎在起飞以及飞行过程中完全达到了飞机在起飞及飞行过程中的标准。此外,由专业的测试人员对上述飞行汽车轮胎a-e进行操控性与舒适性打分,根据评分结果,飞行汽车轮胎a-e在操控性和舒适性方面均达到汽车胎水平,完全可以满足飞行汽车在路面行驶过程中的要求。通过以上成品轮胎测试,充分说明通过本发明所提供的胎面配方并结合结构设计和工艺设计所制备获得的轮胎,既可以满足道路车辆行驶的要求,又可以满足飞机轮胎的高强度和高耐磨性能,可以成功应用于新研发的飞行汽车中。当前第1页12