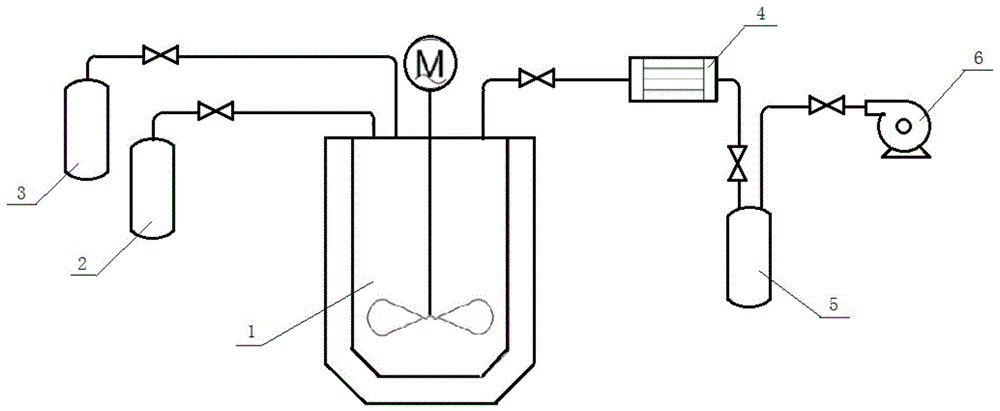
本发明涉及含硫硅烷偶联剂及其合成方法,属于硅烷偶联剂
技术领域:
。
背景技术:
:在轮胎制造工业中常使用含硫硅烷偶联剂来促进硫化来提高橡胶强度,常用的含硫硅烷偶联剂为si69、si75,它们的分子结构式如下:但是这类含硫硅烷偶联剂在硫化过程中释放出的小分子较多,造成橡胶中含有气孔,使轮胎强度降低。德固赛公司采用三乙醇胺与含硫硅烷反应,降低含硫硅烷中的乙氧基含量,得到一种名称为xpsi466的含硫硅烷,其分子式为n(ch2ch2o)3si(ch2)3sx(ch2)3si(och2ch2)3n,此偶联剂可以很大程度的降低含硫硅烷在硫化过程中放出的乙醇含量,但是此偶联剂存在诱导期短,加工安全性能差,合成过程中产品粘度大,导致乙醇需要在130~150℃的高温才能除去,增加了工艺难度,且收集率低。技术实现要素:本发明就是要解决现有的含硫硅烷偶联剂诱导期短、加工安全性能差,产品粘度大的技术问题,从而提供一种双基团改性的低挥发含硫硅烷偶联剂及合成方法。本发明的双基团改性的低挥发含硫硅烷偶联剂,其分子式为:x-si-r-sz-r-si-y;其中z为1~10的整数;r为ch2、ch2ch2、ch2ch2ch2、ch2ch2ch2ch2、ch(ch3)、ch2ch(ch3)、ch(ch3)ch2、c(ch3)2、ch(c2h5)、ch2ch2ch(ch3)、ch(ch3)ch2ch2、ch2ch(ch3)ch2或ch2-(phenyl);x为n(alk-o-)3;y为(alk-o-)3。上述的双基团改性的低挥发含硫硅烷偶联剂的制备方法,按以下步骤进行:一、将多硫化物硅烷偶联剂和催化剂加入到连接有冷凝器的反应装置中,带有机械搅拌、油浴加热和冷凝器的反应装置中,用油浴加热至温度为60~100℃,搅拌0.5~1小时;其中所述的多硫化物硅烷偶联剂为si69或si75;二、保持反应装置内的温度为60~100℃的条件下抽真空至真空度为-0.01~-0.02mpa,将三元醇胺化合物和三元醇化合物同时滴加到反应装置中,1~2小时滴完;滴完继续反应,反应过程中产生的气体经冷凝器冷凝进行收集,反应至冷凝器无馏分流出为止,反应装置内的物质即为双基团改性的低挥发含硫硅烷偶联剂。本发明的双基团改性的低挥发含硫硅烷偶联剂具有以下优点:1、分子中(alk-o-)3基团替代了50%的n(alk-o-)3基团,减弱了氨基在硫化过程中的活化作用,促使诱导时间增长,有利于提高操作安全性,延长胶料、胶浆的贮存期;2、乙氧基团的含量比xpsi466中乙氧基团含量更低,其实际挥发性有机物小于0.1%,混炼过程中几乎没有低挥发性有机物(voc)释放,环保效益明显;3、橡胶混炼过程中胶料与填料的交联效果与普通的含硫硅烷基本一致且硫化胶配方中活性剂(peg4000)的用量减少了约50%;4、产品粘度低,流动性好,乙醇在较低温度和微负压下被收集,乙醇收集率可达95%以上,适合工业化生产;5、无需后续处理就可以用作橡胶混炼使用;本发明的双基团改性的低挥发含硫硅烷偶联剂可用于橡胶领域。附图说明图1为实施例1和2中反应装置示意图;图2为混炼胶1、混炼胶2、混炼胶3和混炼胶4的硫化曲线图。具体实施方式具体实施方式一:本实施方式的双基团改性的低挥发含硫硅烷偶联剂,其分子式为:x-si-r-sz-r-si-y;其中z为1~10的整数;r为ch2、ch2ch2、ch2ch2ch2、ch2ch2ch2ch2、ch(ch3)、ch2ch(ch3)、ch(ch3)ch2、c(ch3)2、ch(c2h5)、ch2ch2ch(ch3)、ch(ch3)ch2ch2、ch2ch(ch3)ch2或ch2-(phenyl);x为n(alk-o-)3;alk表示烷基;y为(alk-o-)3。具体实施方式二:本实施方式与具体实施方式一不同的是其中alk为c3-c10的烷基。其它与具体实施方式一相同。具体实施方式三:具体实施方式一所述的双基团改性的低挥发含硫硅烷偶联剂的制备方法,按以下步骤进行:一、将多硫化物硅烷偶联剂和催化剂加入到连接有冷凝器的反应装置中,带有机械搅拌、油浴加热和冷凝器的反应装置中,用油浴加热至温度为60~100℃,搅拌0.5~1小时;其中所述的多硫化物硅烷偶联剂为si69或si75;二、保持反应装置内的温度为60~100℃的条件下抽真空至真空度为-0.01~-0.02mpa,将三元醇胺化合物和三元醇化合物同时滴加到反应装置中,1~2小时滴完;滴完继续反应,反应过程中产生的气体经冷凝器冷凝进行收集,反应至冷凝器无馏分流出为止,反应装置内的物质即为双基团改性的低挥发含硫硅烷偶联剂。具体实施方式四:本实施方式与具体实施方式三不同的是步骤一中机械搅拌的转速为每分钟80~300转;其它与具体实施方式三相同。具体实施方式五:本实施方式与具体实施方式三或四不同的是步骤一中所述的催化剂为钛酸四丁酯、钛酸四乙酯、钛酸四正丙酯或钛酸四异丙酯;其它与具体实施方式三或四相同。具体实施方式六:本实施方式与具体实施方式三至五之一不同的是步骤二中所述的三元醇胺化合物为三乙醇胺或三异丙醇胺;其它与具体实施方式三至五之一相同。具体实施方式七:本实施方式与具体实施方式三至六之一不同的是步骤二中所述的三元醇化合物为丙三醇、1,2,6己三醇或丁三醇;其它与具体实施方式三至六之一相同。具体实施方式八:本实施方式与具体实施方式三至七之一不同的是多硫化物硅烷偶联剂、三元醇胺化合物与三元醇化合物的摩尔比为1:(1.0~1.1):(1.0~1.1);其它与具体实施方式三至七之一相同。具体实施方式九:本实施方式与具体实施方式三至八之一不同的是催化剂的质量占多硫化物硅烷偶联剂、三元醇胺化合物、三元醇化合物与催化剂总质量之和的1%~2%;其它与具体实施方式三至八之一相同。用下面的实施例验证本发明的有益效果:实施例1:本实施例的改性低挥发含硫硅烷偶联剂的制备方法,按以下步骤进行:一、反应装置由反应釜1、第一加料罐2、第二加料罐3、冷凝器4、接收罐5和真空泵6组成,反应釜1设置有加热夹套和搅拌浆;第一加料罐2、第二加料罐3与反应釜1上部的加料口连接;反应釜1上部的排气口与凝冷器4的进气口相连接,凝冷器4的出口与接收罐5连接;真空泵6与接收罐5连接,可给整个反应装置抽真空;将538g双-[3-(三乙氧基硅)丙基]-四硫化物(si-69)和7.78g钛酸四丁酯加入到反应釜1中,用油浴加热,在油浴温度为90℃的条件下以每分钟150转的搅拌速度搅拌1小时;二、保持反应釜1内的温度为90℃抽真空至的反应釜1内真空度为-0.019mpa,将第一加料罐2中的149g三乙醇胺与第二加料罐3中的91g丙三醇同时滴加到反应釜1中,1小时滴完;滴完继续反应6小时后冷凝器4无馏分流出为止,反应完毕,反应过程中产生的气体经冷凝器4冷凝进行收集得到乙醇,反应釜1的物质即为双基团改性的低挥发含硫硅烷偶联剂。本实施例1得到的改性低挥发含硫硅烷偶联剂为棕黄色液体,质量为515g,计算出转化率97.8%,挥发度0.3%,收集乙醇质量为259.2g,收集率为95.7%。本实施例制备的双基团改性的低挥发含硫硅烷偶联剂的分子式为用硅核磁共振sinmr法测试本实施例制备的双基团改性的低挥发含硫硅烷偶联剂,表明大于97%的si-oet被替代,说明所合成的产物为上述分子结构式的目标产物。实施例2:本实施例的改性低挥发含硫硅烷偶联剂的制备方法,按以下步骤进行:一、反应装置由反应釜1、第一加料罐2、第二加料罐3、冷凝器4、接收罐5和真空泵6组成,反应釜1设置有加热夹套和搅拌浆;第一加料罐2、第二加料罐3与反应釜1上部的加料口连接;反应釜1上部的排气口与凝冷器4的进气口相连接,凝冷器4的出口与接收罐5连接;真空泵6与接收罐5连接,可给整个反应装置抽真空;将538g双-[3-(三乙氧基硅)丙基]-四硫化物(si-69)和7.78g钛酸四丁酯加入到反应釜1中,用油浴加热,在油浴温度为90℃的条件下以每分钟150转的搅拌速度搅拌1小时;二、保持反应釜1内的温度为90℃抽真空至反应釜1的真空度为-0.019mpa,将第一加料罐2中的149g三乙醇胺与第二加料罐3中的138g已三醇同时滴加到反应釜1中,1小时滴完;滴完继续反应6小时后冷凝器4无馏分流出为止,反应完毕,反应过程中产生的气体经冷凝器4冷凝进行收集到接收罐5中得到乙醇,反应釜1的物质即为双基团改性的低挥发含硫硅烷偶联剂。本实施例2得到的改性低挥发含硫硅烷偶联剂为棕黄色液体,质量为564.23g,计算出转化率97.3%,挥发度0.28%,收集乙醇质量为261.57g,收集率为97.4%。本实施例制备的双基团改性的低挥发含硫硅烷偶联剂的分子式为用硅核磁共振sinmr法测试本实施例制备的双基团改性的低挥发含硫硅烷偶联剂,表明大于97%的si-oet被替代,说明所合成的产物为上述分子结构式的目标产物。对实施例1、2制备的改性低挥发含硫硅烷偶联剂与si-69、xpsi466按照gb/t20020标准进行挥发度(voc)测试,测试温度为105℃,时间为30分钟。得到的挥发度(voc)结果如表1所示。表1实施例1、2制备的双基团改性的低挥发含硫硅烷偶联剂与双-[3-(三乙氧基硅)丙基]-四硫化物、xpsi466的挥发度从表1可以看出,实施例1、2制备的双基团改性的低挥发含硫硅烷偶联剂的挥发度与si-69相比,几乎不排放低挥发的物质,也可以说是无voc排放的硅烷产品。按表2所示的配方,将实施例1、2制备的改性低挥发含硫硅烷偶联剂与si-69、xpsi466分别与橡胶混炼,得到混炼胶,再对混炼胶进行性能测试。其中混炼胶的制备过程如下:一、将天然橡胶(nr)加入到密炼机中,在起始温度为75~85℃、转速为70~80转/分钟的条件下塑炼0.5~2分钟;二、将白炭黑、a级氧化锌、含硫硅烷偶联剂、硬脂酸(st)加入密炼机中,与橡胶原料一同混炼2~4分钟;三、将芳香油加入密炼机中,继续混炼1~3分钟,然后将混炼后的母胶排出;四、将母胶加入到开炼机中,然后加入硫化剂s、促进剂m、促进剂dm和促进剂ts进行混炼,薄通六次后下片,获得混炼胶。表2为混炼胶的配方对得到的混炼胶1、混炼胶2、混炼胶3和混炼胶4进行物理和力学性能测试,得到的结果如表3所示。表3混炼胶的性能实验项目混炼胶1混炼胶2混炼胶3混炼胶4比重1.1361.1341.1351.132硬度(shorta)67676867弹性@rt(%)54535355抗拉强度(kg/cm)119114114126撕裂强度(kg/cm)61656465延伸率(%)425401387419300%定伸强度(mpa)79788483磨耗78727472从表3可以看出,混炼胶1、混炼胶2、混炼胶3和混炼胶4的比重、硬度、弹性、抗拉强度、撕裂强度、延伸率和磨耗无明显区别,但300%定伸强度指标,混炼胶3和混炼胶4相对稍高。混炼胶1、混炼胶2、混炼胶3和混炼胶4的硫化曲线如图2所示,从图2中读出ts1、ts2、tc10、tc90、ml和mh的值如表4所示。其中ts1:最低扭矩值(ml)再加一个单位扭矩值后所对应的焦烧时间。亦即ml+1所对应焦烧时间。ts2:是ml+2所对应的焦烧时间。tc10:是达到10%硫化时所需要的时间。tc90:亦称正硫化时间,是达到90%硫化时所需要的时间。ml:一条硫化曲线上最低点的扭矩值。mh:一条硫化曲线上最高点的扭矩值。表4混炼胶的硫化性能从表4可以很明显看出,混炼胶1与混炼胶2相比,其硫化曲线焦烧安全时间(ts1、ts2)明显缩短,这是氨基作用的结果,这对橡胶硫化是很不利的。而使用实施例1和2的含硫硅烷偶联剂的混炼胶3和混炼胶4的硫化曲线ts1和ts2与混炼胶1相近,表现出良好的焦烧安全性,这对橡胶硫化的操作安全性是非常有利的,同时配方中活性剂peg4000的用量减少了一半,得到的硫化胶性能与硫化曲线都是比较理想的。从表4还能看出混炼胶3和4的ml值要相比混炼胶2的值要低,从这一点证明了混炼胶3和4胶料流动性要优于混炼胶2的胶料流动性。在橡胶混炼过程中,用实施例1和2的含硫硅烷偶联剂的橡胶的挥发性有机气体的排放量非常少,几乎不排放挥发性有机气体,这对环境保护也是非常有利的。当前第1页12