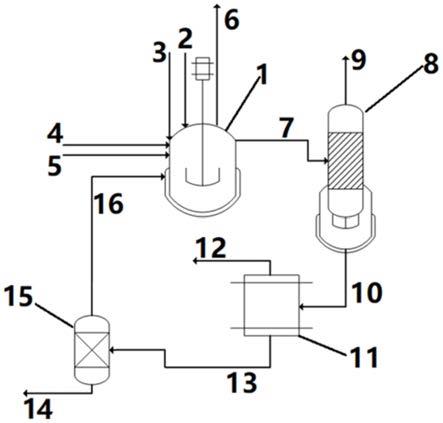
1.本发明涉及环己烷直接氧化制备己二酸的方法。
背景技术:2.环己烷直接空气氧化制备己二酸的反应通常采用环己烷、醋酸、催化剂和含氧气体在一定的温度和压力下催化反应,得到合成液中主要成分是未反应的环己烷、醋酸、催化剂、中间产物环己醇环己酮、产物己二酸,副产物丁二酸、戊二酸以及其它复杂的焦油类杂质。为了充分利用反应原料和中间产物,一般会将合成液分离回收大部分的环己烷、醋酸、己二酸和戊二酸以及丁二酸,由于得到的残液富含催化剂和中间产物,所以会把这部分残液当作循环液返回氧化反应釜提高经济性,随着连续反应的进行,循环液中的杂质不断富积,尤其是我们发现复杂的焦油类杂质会严重影响主反应,导致催化剂活性下降,降低环己烷的转化率和己二酸的转化率,同时也影响己二酸产品的纯度,因此需要及时的将循环液中的焦油类杂质分离除掉。而这些对反应有害的焦油却能够简单处理后用作缓冲剂、制革用油、干性油、煤的浮选剂等,有一定的经济价值。分析表明循环液主要成分是酮、醚、醇、酯、酸、醛、酚以及少量烃类有机物的混合物,简单举例来说主要含有醋酸、环己醇、环己酮、己二酸、戊二酸、丁二酸、二聚酮、三聚酮、6-羟基己酸、乙醛酸、环己二醇、环己醇酮环己烯醇、环己烯酮、环己基过氧化氢、己内酯、5-羟基戊酸、3-羟基丙酸、乙酰丙酸等。
3.专利cn102256927公开了环己烷氧化工艺副产物衍生物及其使用方法,利用酯组合物、溶剂、清洁制剂、固化剂、活性稀释溶剂、控制的酸性官能团释放剂、多元醇单体、钻井泥浆以及制造和使用上述各项方法。从环己烷氧化产物水洗出物、高沸点蒸馏底产物和浓缩水洗出物回收酯基溶剂的方法为在酯化温度和压力下利用酯化和酯交换催化剂处理原料与醇类形成新的酯。这种方法利用了氧化产物水洗出物或浓缩液中的酸和酯,需要补加大量的甲醇并在高温高压下反应,安全性和经济性并不高。
4.专利cn104276937公开了由环己烷氧化反应副产物制备己二酸和c
4-5
二元酸的方法,利用洗涤水与环己烷氧化液油相萃取,浓缩洗涤水后用硝酸氧化冷却结晶得到己二酸和c
4-5
二元酸溶液,该方法仅能处理不用醋酸作为溶剂的环己烷氧化液,利用水对油相中有机物的萃取再浓缩氧化作用回收反应副产物,需要消耗硝酸,对设备材质要求较高,对于体系中的焦油类杂质无法分离利用。
5.专利cn111378467公开了一种环己烷氧化副产物的处理方法,利用碱溶液处理环己烷氧化反应釜产物,将油相与重质残油混合后延迟焦化反应得到组分油和焦炭。这种处理方式采用了无机强碱,延迟焦化温度490-520℃,条件苛刻,反应得到焦化富气、汽油、柴油、蜡油和重蜡油等组分油气和焦炭,焦炭含量高达20-30%,碳原子经济性不高。
6.专利cn1300089公开了利用环己烷氧化液酸洗水过氧化氢催化氧化制备己二酸的方法,利用水洗涤环己烷氧化液浓缩后在催化剂的作用下用过氧化氢氧化,并利用氯仿萃取,萃余液冷却结晶得到己二酸,这种方法利用了钒酸钠、硼酸、铋酸或者锑酸作为氧化催化剂,采用氯仿、二氯甲烷、三氯乙烷或者二氯乙烷作为萃取剂进行萃取,反应复杂、分离成
本高,对环境不友好。
7.上述处理方法适用于无醋酸溶剂的环己烷氧化液,也就是环己烷氧化制ka油(环己酮/环己醇)的氧化液,对于含有醋酸的环己烷直接氧化制备己二酸氧化液并不适用,但现实问题是在环己烷直接氧化制己二酸工艺中催化剂和中间产物的循环利用时严重影响了催化剂活性和环己烷的转化率以及己二酸的选择性。
技术实现要素:8.本发明涉及一种环己烷直接氧化制备己二酸的方法,主要解决现有技术中环己烷直接氧化法制己二酸连续反应中循环液影响催化剂活性,环己烷转化率低、己二酸选择性不高的问题,提供一种新的环氧乙烷直接氧化制备已二酸的方法,该方法显著降低了循环液对催化剂活性的影响,提高了环己烷的转化率和己二酸的选择性。
9.为解决上述技术问题,本发明技术方案如下:
10.环己烷直接氧化制备己二酸的方法,包括以下几个步骤:
11.(1)环己烷、醋酸、催化剂和空气在氧化反应釜反应得到己二酸合成液;
12.(2)合成液蒸发结晶得到己二酸粗品和结晶母液a;
13.(3)结晶母液a经浓缩和结晶,得固体和结晶母液b;
14.(4)结晶母液b与双氧水溶液反应;
15.(5)静置分层分液得到上层水相和下层油相。
16.本发明的关键是步骤(4)采用双氧水与结晶母液反应和步骤(5)静置分层得到上层水相和下层油相,从而为母液a的后续处理奠定了基础。我们发现,不加双氧水单纯加入水无法分层,猜测是双氧水将母液b中某些亲水-亲油两亲性组分氧化,破坏了体系的均相稳定性造成分层的趋势。
17.上述技术方案中,步骤(2)优选采用蒸发结晶除掉合成液中的环己烷和大部分的醋酸,实际上闪蒸或者减压精馏也能除掉环己烷和醋酸,但是我们发现蒸发结晶在除掉环己烷和大部分醋酸的同时,得到的己二酸产品纯度较高,得益于蒸发和结晶过程的耦合效应,促进己二酸晶体的生长,随着蒸发量的增加,己二酸收率增加,但是己二酸产品纯度下降,因为蒸发量增大,体系中其它杂质结晶析出,但是如果蒸发量太小,己二酸收率低,经济性不高,我们通过实验发现采用蒸发结晶除掉全部的环己烷和总醋酸量30-60%的醋酸得到的己二酸晶体产品收率和纯度较好。
18.上述技术方案中,步骤(4)所述双氧水溶液优选所用的溶剂为水或主要为水。溶剂主要为水例如但不限于是指水在溶剂中所占的重量百分含量为50%以上~100%以下,作为更具体的非限制性举例,溶剂主要为水可以但不限于是指水在溶剂中所占的重量百分含量为55%、60%、65%、70%、75%、80%、85%、90%、95%。
19.上述技术方案中,优选还包括如下步骤:
20.所述上层水相经浓缩结晶得到混合二元酸。
21.上述技术方案中,优选还包括如下步骤:
22.所述下层油相经活性炭吸附除杂得净化焦油。该焦油可以进一步处理后用作缓冲剂、制革用油、干性油、煤的浮选剂等高附加值产品。
23.上述技术方案中,可选经历步骤(3)和步骤(4)处理的结晶母液a占步骤(2)全部母
液a的重量的10~100%,例如但不限于15%、20%、25%、30%、35%、40%、45%、50%、55%、60%、65%、70%、75%、80%、85%、90%、95%;进一步可选将步骤(2)剩余的母液a返回到步骤(1)的反应体系中。和/或步骤(4)用于与双氧水溶液反应的结晶母液b占步骤(3)全部母液b的重量的10~100%,例如但不限于15%、20%、25%、30%、35%、40%、45%、50%、55%、60%、65%、70%、75%、80%、85%、90%、95%;进一步可选将步骤(3)剩余的母液b返回到步骤(1)的反应体系中。
24.上述技术方案中,优选步骤(3)浓缩的方式为采用冷冻干燥机除掉采出液中挥发性组分。
25.上述技术方案中,优选冷冻干燥机操作压力为0.1-5pa,例如但不限于冷冻干燥机操作压力为0.15pa、0.20pa、0.25pa、0.30pa、0.35pa、0.40pa、0.45pa、0.50pa、0.55pa、0.60pa、0.70pa、0.80pa、0.90pa、1.0pa、1.5pa、2.0pa、2.5pa、3.0pa、3.5pa、4.0pa、4.5pa等等。
26.上述技术方案中,优选冷阱温度为-50~-80℃,例如但不限于冷阱温度为-55℃、-60℃、-65℃、-70℃、-75℃等等。
27.上述技术方案中,优选步骤(3)结晶的温度优选0~5℃,例如但不限于步骤(3)结晶的温度为0.5℃、1.0℃、1.5℃、2.0℃、2.5℃、3.0℃、3.5℃、4.0℃、4.5℃等等。
28.上述技术方案中,优选结晶母液a重量组成为:
29.醋酸10-40%,例如但不限于15%、20%、25%、30%、35%等等;
30.己二酸1-10%,例如但不限于1.5%、2.0%、2.5%、3.0%、3.5%、4.0%、4.5%、5.0%、5.5%、6.0%、6.5%、7.0%、7.5%、8.0%、8.5%、9.0%、9.5%等等;
31.戊二酸3-9%,例如但不限于3.5%、4.0%、4.5%、5.0%、5.5%、6.0%、6.5%、7.0%、7.5%、8.0%、8.5%等等;
32.丁二酸0.1-4%,例如但不限于0.2%、0.4%、0.6%、0.8%、1.0%、1.5%、2.0%、2.5%、3.0%、3.5%等等;
33.催化剂0.01-0.20%,例如但不限于0.02%、0.03%、0.04%、0.05%、0.06%、0.07%、0.08%、0.09%、0.1%、0.11%、0.12%、0.13%、0.14%、0.15%、0.16%、0.17%、0.18%、0.19%等等;
34.环己酮和环己醇总计1-5%,例如但不限于1.5%、2.0%、2.5%、3.0%、3.5%、4.0%、4.5%等等;
35.余量为焦油和其它未定量中间副产物。
36.上述技术方案中,所述双氧水溶液优选双氧水水溶液。
37.上述技术方案中,优选双氧水溶液中双氧水的重量浓度为20~40%,例如但不限于双氧水溶液中双氧水的重量浓度为21%、22%、23%、24%、25%、26%、27%、28%、29%、30%、31%、32%、33%、34%、35%、36%、37%、38%、39%等等。
38.上述技术方案中,优选双氧水溶液与母液b的重量比为1~4,例如但不限于双氧水溶液与母液b的重量比为1.5、2.0、2.5、3.0、3.5等等。
39.上述技术方案中,优选步骤(4)反应的温度为25~50℃,例如但不限于步骤(4)反应的温度为26℃、27℃、28℃、29℃、30℃、31℃、32℃、33℃、34℃、35℃、36℃、37℃、38℃、39℃、40℃、41℃、42℃、43℃、44℃、45℃、46℃、47℃、48℃、49℃等等。
40.上述技术方案中,优选步骤(4)反应时间为0.1~2h,例如但不限于0.2h、0.3h、0.4h、0.5h、0.6h、0.7h、0.8h、0.9h、1h、1.1h、1.2h、1.3h、1.4h、1.5h、1.6h、1.7h、1.8h、1.9h等等。
41.上述技术方案中,优选所述水相的浓缩的程度是除掉上层水相中60-80%重量的水,例如但不限于所述水相的浓缩的程度是除掉上层水相中63%重量的水、66%重量的水、69%重量的水、72%重量的水、75%重量的水、78%重量的水等等。
42.上述技术方案中,优选活性炭与下层油相的重量比为0.1~0.5,例如但不限于活性炭与下层油相的重量比为0.15、0.2、0.25、0.30、0.35、0.40、0.45。
43.上述技术方案中,优选吸附时间为1~2h。
44.上述技术方案中,优选活性炭比表面积为800-1200m2/g,例如但不限于活性炭比表面积为850m2/g、900m2/g、950m2/g、1000m2/g、1050m2/g、1100m2/g、1150m2/g等等。
45.下面通过附图说明和具体实施方式对本发明进行详细说明。
附图说明
46.图1为本发明步骤(1)和步骤(2)采用装置的示意图。
47.其中:1为氧化反应釜;2为空气加入口;3为醋酸加入口;4为环己烷加入口;5为催化剂加入口;6为尾气出口;7为合成液出口;8为蒸发结晶器;9为蒸发结晶器顶部出口;10为蒸发结晶器底部出口;11为固液分离设备;12为己二酸粗晶;13为结晶母液a;14为结晶母液a采出液;15为系统循环液罐;16为循环液进口。
具体实施方式
48.【实施例1】
49.(1)催化剂从催化剂加入口5连续加入氧化反应釜1,催化剂体积空速50h-1
,其中含有钴离子0.1g/l,铜离子0.2g/l,锰离子0.1g/l;环己烷从环己烷加入口4连续加入氧化反应釜1,体积空速1h-1
;醋酸从醋酸加入口3连续加入氧化反应釜1,体积空速0.5h-1
;空气从空气加入口2连续加入氧化反应釜1,体积空速0.005h-1
(按标准状况下的气体体积计算),尾气从尾气出口6排出,合成液从合成液出口7排出到蒸发结晶器8;
50.(2)从蒸发结晶器顶部出口9回收环己烷和醋酸,从蒸发结晶器底部出口10排出己二酸晶浆到固液分离设备11得到己二酸粗品12和结晶母液a13进入系统循环液罐15;
51.取50%体积的结晶母液a13返回氧化反应釜1作为循环液,剩余50%作为结晶母液a采出液14从系统循环液罐15中移除,连续反应24h后分析循环液/采出液重量组成,醋酸36.2%、己二酸6.5%、戊二酸5.9%、丁二酸0.3%、催化剂(以钴离子、铜离子和锰离子总量计)0.11%、环己酮/环己醇1.3%、余下组分49.72%为杂质焦油和其它未定量中间副产物;
52.(3)上述100g结晶母液a采出液14采用冷冻干燥机处理,冷阱温度-75℃,绝对压力1pa,结束后残留物5℃冷冻结晶,固液分离得到二元酸固体混合物10.8g和45.9g结晶母液b;
53.(4)上述45.9g结晶母液b与35%重量浓度的双氧水水溶液混合,其中双氧水水溶液占混合物重量的50%,在搅拌下充分反应,反应温度40℃,反应时间1h;
54.(5)静置分层,得到58.2g上层水相和33.6g下层油相;
55.(6)58.2上层水相浓缩除掉60%重量的水后结晶得到二元酸混合物固体7.8g;
56.(7)33.6g下层油相与比表面积1023m2/g的活性炭混合处理1.5h,其中活性炭的重量为下层油相重量的20%,处理后得到净化焦油30.7g。
57.为便于比较,将主要工艺条件和实验结果列于表1。
58.【实施例2】
59.(1)催化剂从催化剂加入口5连续加入氧化反应釜1,催化剂体积空速50h-1
,其中含有钴离子0.1g/l,铜离子0.2g/l,锰离子0.1g/l;环己烷从环己烷加入口4连续加入氧化反应釜1,体积空速1h-1
;醋酸从醋酸加入口3连续加入氧化反应釜1,体积空速0.5h-1
;空气从空气加入口2连续加入氧化反应釜1,体积空速0.005h-1
(按标准状况下的气体体积计算),尾气从尾气出口6排出,合成液从合成液出口7排出到蒸发结晶器8;
60.(2)从蒸发结晶器顶部出口9回收环己烷和醋酸,从蒸发结晶器底部出口10排出己二酸晶浆到固液分离设备11得到己二酸粗品12和结晶母液a13进入系统循环液罐15;
61.取90%体积的结晶母液a13返回氧化反应釜1作为循环液,剩余10%作为结晶母液a采出液14从系统循环液罐15中移除,连续反应24h后分析循环液/采出液重量组成,醋酸35.1%、己二酸5.3%、戊二酸6.1%、丁二酸0.4%、催化剂(以钴离子、铜离子和锰离子总量计)0.15%、环己酮/环己醇0.3%、余下组分52.72%为杂质焦油和其它未定量中间副产物;
62.(3)上述100g结晶母液a采出液14采用冷冻干燥机处理,冷阱温度-75℃,绝对压力1pa,结束后残留物5℃冷冻结晶,固液分离得到二元酸固体混合物9.3g和55.2g结晶母液b;
63.(4)上述52.2g结晶母液b与35%重量浓度的双氧水水溶液混合,其中双氧水水溶液占混合物重量的50%,在搅拌下充分反应,反应温度40℃,反应时间1h;
64.(5)静置分层,得到60.1g上层水相和44.3g下层油相;
65.(6)60.1上层水相浓缩除掉60%重量的水后结晶得到二元酸混合物固体7.7g;
66.(7)44.3g下层油相与比表面积1023m2/g的活性炭混合处理1.5h,其中活性炭的重量为下层油相重量的20%,处理后得到净化焦油42.4g。
67.为便于比较,将主要工艺条件和实验结果列于表1。
68.【实施例3】
69.(1)催化剂从催化剂加入口5连续加入氧化反应釜1,催化剂体积空速50h-1
,其中含有钴离子0.1g/l,铜离子0.2g/l,锰离子0.1g/l;环己烷从环己烷加入口4连续加入氧化反应釜1,体积空速1h-1
;醋酸从醋酸加入口3连续加入氧化反应釜1,体积空速0.5h-1
;空气从空气加入口2连续加入氧化反应釜1,体积空速0.005h-1
(按标准状况下的气体体积计算),尾气从尾气出口6排出,合成液从合成液出口7排出到蒸发结晶器8;
70.(2)从蒸发结晶器顶部出口9回收环己烷和醋酸,从蒸发结晶器底部出口10排出己二酸晶浆到固液分离设备11得到己二酸粗品12和结晶母液a13进入系统循环液罐15;
71.取70%体积的结晶母液a13返回氧化反应釜1作为循环液,剩余30%作为结晶母液a采出液14从系统循环液罐15中移除,连续反应24h后分析循环液/采出液重量组成,醋酸35.6%、己二酸5.4%、戊二酸6.3%、丁二酸0.4%、催化剂(以钴离子、铜离子和锰离子总量计)0.11%、环己酮/环己醇0.7%、余下组分51.52%为杂质焦油和其它未定量中间副产物;
72.(3)上述100g结晶母液a采出液14采用冷冻干燥机处理,冷阱温度-75℃,绝对压力1pa,结束后残留物5℃冷冻结晶,固液分离得到二元酸固体混合物9.4g和53.4g结晶母液b;
73.(4)上述53.4g结晶母液b与35%重量浓度的双氧水水溶液混合,其中双氧水水溶液占混合物重量的50%,在搅拌下充分反应,反应温度40℃,反应时间1h;
74.(5)静置分层,得到63.9g上层水相和42.9g下层油相;
75.(6)63.9上层水相浓缩除掉60%重量的水后结晶得到二元酸混合物固体7.9g;
76.(7)42.9g下层油相与比表面积1023m2/g的活性炭混合处理1.5h,其中活性炭的重量为下层油相重量的20%,处理后得到净化焦油41.5g。
77.为便于比较,将主要工艺条件和实验结果列于表1。
78.【实施例4】
79.(1)催化剂从催化剂加入口5连续加入氧化反应釜1,催化剂体积空速50h-1
,其中含有钴离子0.1g/l,铜离子0.2g/l,锰离子0.1g/l;环己烷从环己烷加入口4连续加入氧化反应釜1,体积空速1h-1
;醋酸从醋酸加入口3连续加入氧化反应釜1,体积空速0.5h-1
;空气从空气加入口2连续加入氧化反应釜1,体积空速0.005h-1
(按标准状况下的气体体积计算),尾气从尾气出口6排出,合成液从合成液出口7排出到蒸发结晶器8;
80.(2)从蒸发结晶器顶部出口9回收环己烷和醋酸,从蒸发结晶器底部出口10排出己二酸晶浆到固液分离设备11得到己二酸粗品12和结晶母液a13进入系统循环液罐15;
81.取30%体积的结晶母液a13返回氧化反应釜1作为循环液,剩余70%作为结晶母液a采出液14从系统循环液罐15中移除,连续反应24h后分析循环液/采出液重量组成,醋酸36.8%、己二酸6.6%、戊二酸5.8%、丁二酸0.3%、催化剂(以钴离子、铜离子和锰离子总量计)0.11%、环己酮/环己醇1.4%、余下组分49.02%为杂质焦油和其它未定量中间副产物;
82.(3)上述100g结晶母液a采出液14采用冷冻干燥机处理,冷阱温度-75℃,绝对压力1pa,结束后残留物5℃冷冻结晶,固液分离得到二元酸固体混合物9.6g和55.2g结晶母液b;
83.(4)上述55.2g结晶母液b与35%重量浓度的双氧水水溶液混合,其中双氧水水溶液占混合物重量的50%,在搅拌下充分反应,反应温度40℃,反应时间1h;
84.(5)静置分层,得到60.1g上层水相和44.3g下层油相;
85.(6)60.1上层水相浓缩除掉60%重量的水后结晶得到二元酸混合物固体7.7g;
86.(7)44.3g下层油相与比表面积1023m2/g的活性炭混合处理1.5h,其中活性炭的重量为下层油相重量的20%,处理后得到净化焦油42.4g。
87.为便于比较,将主要工艺条件和实验结果列于表1。
88.【实施例5】
89.(1)催化剂从催化剂加入口5连续加入氧化反应釜1,催化剂体积空速50h-1
,其中含有钴离子0.1g/l,铜离子0.2g/l,锰离子0.1g/l;环己烷从环己烷加入口4连续加入氧化反应釜1,体积空速1h-1
;醋酸从醋酸加入口3连续加入氧化反应釜1,体积空速0.5h-1
;空气从空气加入口2连续加入氧化反应釜1,体积空速0.005h-1
(按标准状况下的气体体积计算),尾气从尾气出口6排出,合成液从合成液出口7排出到蒸发结晶器8;
90.(2)从蒸发结晶器顶部出口9回收环己烷和醋酸,从蒸发结晶器底部出口10排出己二酸晶浆到固液分离设备11得到己二酸粗品12和结晶母液a13进入系统循环液罐15;
91.取10%体积的结晶母液a13返回氧化反应釜1作为循环液,剩余90%作为结晶母液a采出液14从系统循环液罐15中移除,连续反应24h后分析循环液/采出液重量组成,醋酸37.5%、己二酸6.7%、戊二酸5.8%、丁二酸0.2%、催化剂(以钴离子、铜离子和锰离子总量
计)0.11%、环己酮/环己醇1.6%、余下组分48.12%为杂质焦油和其它未定量中间副产物;
92.(3)上述100g结晶母液a采出液14采用冷冻干燥机处理,冷阱温度-75℃,绝对压力1pa,结束后残留物5℃冷冻结晶,固液分离得到二元酸固体混合物9.3g和54.6g结晶母液b;
93.(4)上述54.6g结晶母液b与35%重量浓度的双氧水水溶液混合,其中双氧水水溶液占混合物重量的50%,在搅拌下充分反应,反应温度40℃,反应时间1h;
94.(5)静置分层,得到65.2g上层水相和44.0g下层油相;
95.(6)65.2上层水相浓缩除掉60%重量的水后结晶得到二元酸混合物固体8.1g;
96.(7)44.3g下层油相与比表面积1023m2/g的活性炭混合处理1.5h,其中活性炭的重量为下层油相重量的20%,处理后得到净化焦油42.4g。
97.为便于比较,将主要工艺条件和实验结果列于表1。
98.【实施例6】
99.(1)催化剂从催化剂加入口5连续加入氧化反应釜1,催化剂体积空速50h-1
,其中含有钴离子0.1g/l,铜离子0.2g/l,锰离子0.1g/l;环己烷从环己烷加入口4连续加入氧化反应釜1,体积空速1h-1
;醋酸从醋酸加入口3连续加入氧化反应釜1,体积空速0.5h-1
;空气从空气加入口2连续加入氧化反应釜1,体积空速0.005h-1
(按标准状况下的气体体积计算),尾气从尾气出口6排出,合成液从合成液出口7排出到蒸发结晶器8;
100.(2)从蒸发结晶器顶部出口9回收环己烷和醋酸,从蒸发结晶器底部出口10排出己二酸晶浆到固液分离设备11得到己二酸粗品12和结晶母液a13进入系统循环液罐15;
101.取50%体积的结晶母液a13返回氧化反应釜1作为循环液,剩余50%作为结晶母液a采出液14从系统循环液罐15中移除,连续反应24h后分析循环液/采出液重量组成,醋酸36.2%、己二酸6.5%、戊二酸5.9%、丁二酸0.3%、催化剂(以钴离子、铜离子和锰离子总量计)0.11%、环己酮/环己醇1.3%、余下组分49.72%为杂质焦油和其它未定量中间副产物;
102.(3)上述100g结晶母液a采出液14采用冷冻干燥机处理,冷阱温度-50℃,绝对压力0.1pa,结束后残留物5℃冷冻结晶,固液分离得到二元酸固体混合物10.8g和45.9g结晶母液b.
103.(4)上述45.9g结晶母液b与35%重量浓度的双氧水水溶液混合,其中双氧水水溶液占混合物重量的50%,在搅拌下充分反应,反应温度40℃,反应时间1h;
104.(5)静置分层,得到58.2g上层水相和33.6g下层油相;
105.(6)58.2上层水相浓缩除掉60%重量的水后结晶得到二元酸混合物固体7.8g;
106.(7)33.6g下层油相与比表面积1023m2/g的活性炭混合处理1.5h,其中活性炭的重量为下层油相重量的20%,处理后得到净化焦油30.7g。
107.为便于比较,将主要工艺条件和实验结果列于表1。
108.【实施例7】
109.(1)催化剂从催化剂加入口5连续加入氧化反应釜1,催化剂体积空速50h-1
,其中含有钴离子0.1g/l,铜离子0.2g/l,锰离子0.1g/l;环己烷从环己烷加入口4连续加入氧化反应釜1,体积空速1h-1
;醋酸从醋酸加入口3连续加入氧化反应釜1,体积空速0.5h-1
;空气从空气加入口2连续加入氧化反应釜1,体积空速0.005h-1
(按标准状况下的气体体积计算),尾气从尾气出口6排出,合成液从合成液出口7排出到蒸发结晶器8;
110.(2)从蒸发结晶器顶部出口9回收环己烷和醋酸,从蒸发结晶器底部出口10排出己
二酸晶浆到固液分离设备11得到己二酸粗品12和结晶母液a13进入系统循环液罐15;
111.取50%体积的结晶母液a13返回氧化反应釜1作为循环液,剩余50%作为结晶母液a采出液14从系统循环液罐15中移除,连续反应24h后分析循环液/采出液重量组成,醋酸36.2%、己二酸6.5%、戊二酸5.9%、丁二酸0.3%、催化剂(以钴离子、铜离子和锰离子总量计)0.11%、环己酮/环己醇1.3%、余下组分49.72%为杂质焦油和其它未定量中间副产物;
112.(3)上述100g结晶母液a采出液14采用冷冻干燥机处理,冷阱温度-80℃,绝对压力5pa,结束后残留物5℃冷冻结晶,固液分离得到二元酸固体混合物10.8g和45.9g结晶母液b;
113.(4)上述45.9g结晶母液b与35%重量浓度的双氧水水溶液混合,其中双氧水水溶液占混合物重量的50%,在搅拌下充分反应,反应温度40℃,反应时间1h;
114.(5)静置分层,得到58.2g上层水相和33.6g下层油相;
115.(6)58.2上层水相浓缩除掉60%重量的水后结晶得到二元酸混合物固体7.8g;
116.(7)33.6g下层油相与比表面积1023m2/g的活性炭混合处理1.5h,其中活性炭的重量为下层油相重量的20%,处理后得到净化焦油30.7g。
117.为便于比较,将主要工艺条件和实验结果列于表1。
118.【实施例8】
119.(1)催化剂从催化剂加入口5连续加入氧化反应釜1,催化剂体积空速50h-1
,其中含有钴离子0.1g/l,铜离子0.2g/l,锰离子0.1g/l;环己烷从环己烷加入口4连续加入氧化反应釜1,体积空速1h-1
;醋酸从醋酸加入口3连续加入氧化反应釜1,体积空速0.5h-1
;空气从空气加入口2连续加入氧化反应釜1,体积空速0.005h-1
(按标准状况下的气体体积计算),尾气从尾气出口6排出,合成液从合成液出口7排出到蒸发结晶器8;
120.(2)从蒸发结晶器顶部出口9回收环己烷和醋酸,从蒸发结晶器底部出口10排出己二酸晶浆到固液分离设备11得到己二酸粗品12和结晶母液a13进入系统循环液罐15;
121.取50%体积的结晶母液a13返回氧化反应釜1作为循环液,剩余50%作为结晶母液a采出液14从系统循环液罐15中移除,连续反应24h后分析循环液/采出液重量组成,醋酸36.2%、己二酸6.5%、戊二酸5.9%、丁二酸0.3%、催化剂(以钴离子、铜离子和锰离子总量计)0.11%、环己酮/环己醇1.3%、余下组分49.72%为杂质焦油和其它未定量中间副产物;
122.(3)上述100g结晶母液a采出液14采用冷冻干燥机处理,冷阱温度-75℃,绝对压力1pa,结束后残留物0℃冷冻结晶,固液分离得到二元酸固体混合物11.3g和45.4g结晶母液b;
123.(4)上述45.4g结晶母液b与35%重量浓度的双氧水水溶液混合,其中双氧水水溶液占混合物重量的50%,在搅拌下充分反应,反应温度40℃,反应时间1h;
124.(5)静置分层,得到57.3g上层水相和33.5g下层油相;
125.(6)57.3上层水相浓缩除掉60%重量的水后结晶得到二元酸混合物固体7.5g;
126.(7)33.5g下层油相与比表面积1023m2/g的活性炭混合处理1.5h,其中活性炭的重量为下层油相重量的20%,处理后得到净化焦油30.6g。
127.为便于比较,将主要工艺条件和实验结果列于表1。
128.【实施例9】
129.(1)催化剂从催化剂加入口5连续加入氧化反应釜1,催化剂体积空速50h-1
,其中含
有钴离子0.1g/l,铜离子0.2g/l,锰离子0.1g/l;环己烷从环己烷加入口4连续加入氧化反应釜1,体积空速1h-1
;醋酸从醋酸加入口3连续加入氧化反应釜1,体积空速0.5h-1
;空气从空气加入口2连续加入氧化反应釜1,体积空速0.005h-1
(按标准状况下的气体体积计算),尾气从尾气出口6排出,合成液从合成液出口7排出到蒸发结晶器8;
130.(2)从蒸发结晶器顶部出口9回收环己烷和醋酸,从蒸发结晶器底部出口10排出己二酸晶浆到固液分离设备11得到己二酸粗品12和结晶母液a13进入系统循环液罐15;
131.取50%体积的结晶母液a13返回氧化反应釜1作为循环液,剩余50%作为结晶母液a采出液14从系统循环液罐15中移除,连续反应24h后分析循环液/采出液重量组成,醋酸36.2%、己二酸6.5%、戊二酸5.9%、丁二酸0.3%、催化剂(以钴离子、铜离子和锰离子总量计)0.11%、环己酮/环己醇1.3%、余下组分49.72%为杂质焦油和其它未定量中间副产物;
132.(3)上述100g结晶母液a采出液14采用冷冻干燥机处理,冷阱温度-75℃,绝对压力1pa,结束后残留物2℃冷冻结晶,固液分离得到二元酸固体混合物11.1g和45.6g结晶母液b;
133.(4)上述45.6g结晶母液b与20%重量浓度的双氧水水溶液混合,其中双氧水水溶液占混合物重量的80%,在搅拌下充分反应,反应温度25℃,反应时间2h;
134.(5)静置分层,得到194.9g上层水相和33.1g下层油相;
135.(6)194.9上层水相浓缩除掉80%重量的水后结晶得到二元酸混合物固体5.3g;
136.(7)33.6g下层油相与比表面积1211m2/g的活性炭混合处理1.5h,其中活性炭的重量为下层油相重量的20%,处理后得到净化焦油30.5g。
137.【实施例10】
138.(1)催化剂从催化剂加入口5连续加入氧化反应釜1,催化剂体积空速50h-1
,其中含有钴离子0.1g/l,铜离子0.2g/l,锰离子0.1g/l;环己烷从环己烷加入口4连续加入氧化反应釜1,体积空速1h-1
;醋酸从醋酸加入口3连续加入氧化反应釜1,体积空速0.5h-1
;空气从空气加入口2连续加入氧化反应釜1,体积空速0.005h-1
(按标准状况下的气体体积计算),尾气从尾气出口6排出,合成液从合成液出口7排出到蒸发结晶器8;
139.(2)从蒸发结晶器顶部出口9回收环己烷和醋酸,从蒸发结晶器底部出口10排出己二酸晶浆到固液分离设备11得到己二酸粗品12和结晶母液a13进入系统循环液罐15;
140.取50%体积的结晶母液a13返回氧化反应釜1作为循环液,剩余50%作为结晶母液a采出液14从系统循环液罐15中移除,连续反应24h后分析循环液/采出液重量组成,醋酸36.2%、己二酸6.5%、戊二酸5.9%、丁二酸0.3%、催化剂(以钴离子、铜离子和锰离子总量计)0.11%、环己酮/环己醇1.3%、余下组分49.72%为杂质焦油和其它未定量中间副产物;
141.(3)上述100g结晶母液a采出液14采用冷冻干燥机处理,冷阱温度-75℃,绝对压力1pa,结束后残留物4℃冷冻结晶,固液分离得到二元酸固体混合物10.8g和45.9g结晶母液b;
142.(4)上述45.9g结晶母液b与40%重量浓度的双氧水水溶液混合,其中双氧水水溶液占混合物重量的50%,在搅拌下充分反应,反应温度40℃,反应时间1h;
143.(5)静置分层,得到104.4g上层水相和33.3g下层油相;
144.(6)104.4上层水相浓缩除掉70%重量的水后结晶得到二元酸混合物固体6.8g;
145.(7)33.3g下层油相与比表面积806m2/g的活性炭混合处理1.5h,其中活性炭的重
量为下层油相重量的20%,处理后得到净化焦油30.9g。
146.为便于比较,将主要工艺条件和实验结果列于表1。
147.【对比例1】
148.(1)催化剂从催化剂加入口5连续加入氧化反应釜1,催化剂体积空速50h-1
,其中含有钴离子0.1g/l,铜离子0.2g/l,锰离子0.1g/l;环己烷从环己烷加入口4连续加入氧化反应釜1,体积空速1h-1
;醋酸从醋酸加入口3连续加入氧化反应釜1,体积空速0.5h-1
;空气从空气加入口2连续加入氧化反应釜1,体积空速0.005h-1
(按标准状况下的气体体积计算),尾气从尾气出口6排出,合成液从合成液出口7排出到蒸发结晶器8;
149.(2)从蒸发结晶器顶部出口9回收环己烷和醋酸,从蒸发结晶器底部出口10排出己二酸晶浆到固液分离设备11得到己二酸粗品12和结晶母液a13进入系统循环液罐15;
150.取100%体积的结晶母液a13返回氧化反应釜1作为循环液,连续反应24h后分析循环液/采出液重量组成,醋酸36.7%、己二酸3.7%、戊二酸6.2%、丁二酸0.4%、催化剂(以钴离子、铜离子和锰离子总量计)0.11%、环己酮/环己醇0.1%、余下组分52.82%为杂质焦油和其它未定量中间副产物。
151.为便于比较,将主要工艺条件和实验结果列于表1。
152.说明随着反应的全循环进行,由于没有采出液,体系中杂质富集,己二酸选择性下降催化剂活性降低直到反应无法继续进行,没有新的己二酸生成。
153.【对比例2】
154.(1)催化剂从催化剂加入口5连续加入氧化反应釜1,催化剂体积空速50h-1
,其中含有钴离子0.1g/l,铜离子0.2g/l,锰离子0.1g/l;环己烷从环己烷加入口4连续加入氧化反应釜1,体积空速1h-1
;醋酸从醋酸加入口3连续加入氧化反应釜1,体积空速0.5h-1
;空气从空气加入口2连续加入氧化反应釜1,体积空速0.005h-1
(按标准状况下的气体体积计算),尾气从尾气出口6排出,合成液从合成液出口7排出到蒸发结晶器8;
155.(2)从蒸发结晶器顶部出口9回收环己烷和醋酸,从蒸发结晶器底部出口10排出己二酸晶浆到固液分离设备11得到己二酸粗品12和结晶母液a13进入系统循环液罐15;
156.取50%体积的结晶母液a13返回氧化反应釜1作为循环液,剩余50%作为结晶母液a采出液14从系统循环液罐15中移除,连续反应24h后分析循环液/采出液重量组成,醋酸36.2%、己二酸6.5%、戊二酸5.9%、丁二酸0.3%、催化剂(以钴离子、铜离子和锰离子总量计)0.11%、环己酮/环己醇1.3%、余下组分49.72%为杂质焦油和其它未定量中间副产物;
157.(3)上述100g结晶母液a采出液14采用冷冻干燥机处理,冷阱温度-75℃,绝对压力1pa,结束后残留物5℃冷冻结晶,固液分离得到二元酸固体混合物10.8g和45.9g结晶母液b;
158.(4)上述45.9g结晶母液b与45.9g水混合,在搅拌下充分混合,混合温度40℃,混合时间1h;
159.(5)静置,未出现分层现象。
160.为便于比较,将主要工艺条件和实验结果列于表1。
161.说明如果不加入双氧水与结晶母液b充分反应,单纯加入水无法分层,猜测是双氧水将焦油中某些亲水-亲油两亲性组分氧化,造成均相状态被打破,从而得到油水两相。
162.本发明提出的具体的一种环己烷直接氧化制备己二酸循环液处理方法,已通过较
佳实施例子进行了描述,相关技术人员明显能在不脱离本发明内容、精神和范围内对本文所述的结构和制备方法进行改动或适当变更与组合,来实现本发明技术。特别需要指出的是,所有相类似的替换和改动对本领域技术人员来说是显而易见的,他们都被视为包括在本发明精神、范围和内容中。
163.表1(待续)
[0164][0165]
表1(续1)
[0166][0167]
表1(续2)
[0168]