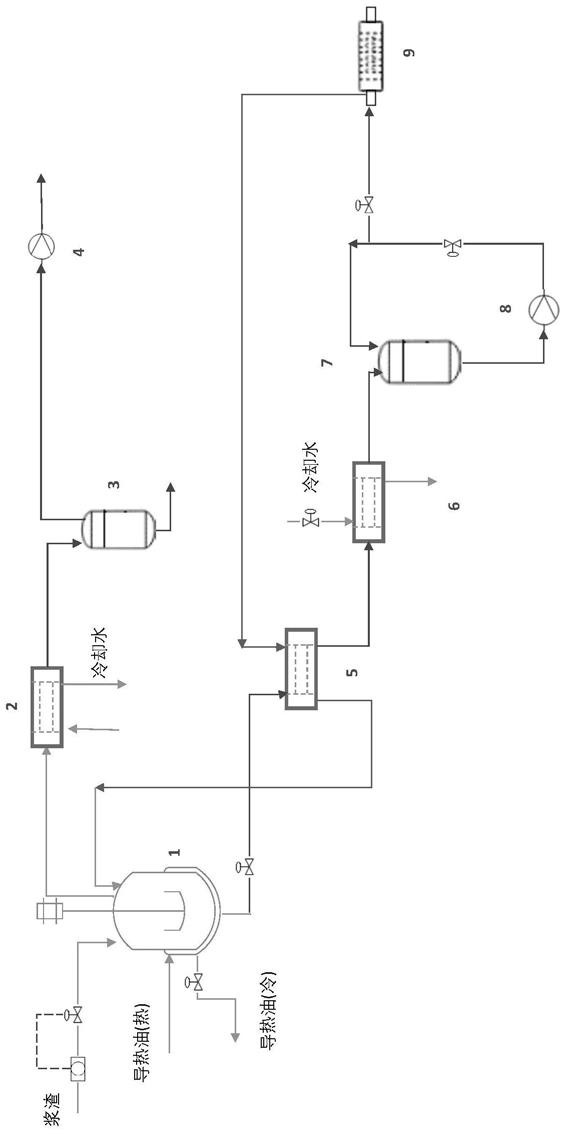
1.本发明涉及有机硅技术领域,特别涉及有机硅产业中浆渣中高沸物回收的方法。
背景技术:2.有机硅是性能优异,应用广阔的新型化工产品,有硅油、硅树脂、硅橡胶等产品,广泛应用于纺织、汽车、建筑、电子、化妆品等生活领域及国防等特殊领域。众多有机硅产品主要来自于直接法单体合成装置,其通常工艺流程为:液相氯硅烷经计量后,经汽化器气化,过热器加热后经分布板进入流化床,硅粉与催化剂混合后,由流化床补料口进入流化床,通过热导热油加热启动反应,反应正常后,通过冷导热油带走反应放热。为了维持流化床料位与反应,需要不断补充硅粉与催化剂。合成气(为反应产物硅烷、未反应的氯甲烷、细硅粉与催化剂)通过流化床顶部进入旋风系统,流化床反应器合成气夹带细粉,首先经过旋风分离系统捕捉大颗粒细粉,然后洗涤塔系统进一步分离出氯硅烷中的重组分,重组分包括未被旋风系统捕集的细粉与高沸点硅烷。重组分再经过闪蒸等蒸发处理蒸出轻组分,提取出部分硅烷,剩余的部分俗称为硅烷浆渣。硅烷浆渣是一种固液混合物,主要成分为高沸物、细硅粉、细催化剂(cu、zn、sn等),其中高沸物主要成分为高沸点氯硅烷。
3.通常情况下,这部分浆渣先进行蒸馏回收其中的高沸物(沸点>160℃),然后无法回收的浆渣通过水解等方式做进一步的无害化处理。由于浆渣是单体有机硅反应器直接排出的,因此含有活化的细硅粉、细催化剂(cu、zn、sn等),遇到空气存在着火风险,固体物质容易堵塞排放管线。
4.cn107501315a公开了一种处理有机硅浆渣的方法装置,其采用高温蒸发及氮气流化的方式回收高沸物;但是由于浆渣中含有细硅粉和催化剂存在,容易导致流化分布盘堵塞;高温情况下,对过滤器的选型及滤袋的选择提出了更高的要求,设备较昂贵,不利于推广实施。cn107501315a是目前工业中对有机硅浆渣回收处理的通常思路,即通过提高浆渣闪蒸或蒸馏的温度提高浆渣中高经济物质的回收,但是其缺点是闪蒸罐或蒸馏釜上固形物的结壁或固体物堵塞管路,结壁会严重威胁到设备及工艺安全。而如果要防止浆渣过度蒸馏威胁生产安全,则需要刻意保留适当液相组分,又会因此导致高经济物质的损失。
技术实现要素:5.为了有效的回收浆渣中高沸物(主要成分为高沸点氯硅烷,如甲基氯硅烷、乙烯基氯硅烷、甲基氯乙硅烷等,是高经济物质)、降低浆渣无害处理的污水排放量,同时又避免传统处理工艺中过度蒸馏导致的生产安全问题,本发明提出了一种有机硅浆渣高沸物回收的方法。
6.本发明的目的通过以下技术方案实现:
7.一种有机硅浆渣中的高沸物回收的方法,在有机硅浆渣中加入高沸点惰性油,进行蒸馏回收高沸物。
8.本发明中的“有机硅浆渣”或简称“浆渣”,是指单体有机硅合成中生成的合成气,
经最后的洗涤装置分离出的重组分,该重组分经过蒸发处理,蒸出轻组分后剩余的部分。其是一种固液混合物,主要成分为高沸物、细硅粉、细催化剂(cu、zn、sn等),其中高沸物主要成分为高沸点氯硅烷。
9.有机硅浆渣中含有铜和/或锌等催化剂用金属,在高温下具有一定裂解催化作用,因此根据本发明,所述高沸点惰性油是指常压下闪点大于210℃的能抵抗高温裂解的油品,例如:常压下闪点280℃的二甲基硅油;或烷基苯型导热油l
‑
qc,l
‑
qd等。在本发明的一个实施方式中,所述高沸点惰性油是常压下闪点280℃的二甲基硅油。
10.根据本发明,在蒸馏回收高沸物时,可以采用常压蒸馏或低压蒸馏,根据所用压力,将蒸馏回收高沸物的温度控制在150℃
‑
250℃之间。为防止高沸点惰性油在高温下裂解,优选采用负压下蒸馏,绝对压力0.01mpaa~0.08mpaa,蒸馏温度为150
‑
220℃。
11.根据本发明,蒸除高沸物后的浆渣(为方便描述,下文中也被称为“脱高后浆渣”)随着高沸点惰性油一起排出浆渣回收装置,经固液分离处理后,分别获得回收的高沸点惰性油和脱高后浆渣固体。
12.根据本发明,所述回收的高沸点惰性油可以循环回到浆渣回收装置,用于浆渣高沸物的蒸馏回收。
13.根据本发明,优选在进行固液分离处理前,通过热交换装置降低浆渣回收装置排出的脱高后浆渣和高沸点惰性油混合物的温度。为配合后续的固液分离方法和装置,优选,将所述混合物的温度降低到80℃以下,更优选为50℃以下。由于浆渣在空气中易被水解生成含有氯化氢气体的可燃物,降低温度不仅能方便选择过滤设备,还可有效降低固渣排放时的自燃风险。
14.根据本发明,通过热交换装置加热进入浆渣回收装置的高沸点惰性油的温度。
15.在本发明的一个实施方式中,采用两个热交换装置,即第一混合物用热交换装置和第二混合物用热交换装置,逐步降低所述混合物的温度。
16.根据本发明,优选降低前述混合物温度的第一混合物用热交换装置和加热高沸点惰性油温度的热交换装置是同一个装置,即,利用混合物的余热加热高沸点惰性油,用高沸点惰性油降低混合物的温度,实现提高综合能源效率的效果。
17.根据本发明,优选第二混合物用热交换装置采用冷却水作为冷却介质。
18.根据本发明,所述固液分离可以采用本领域已知的常规分离方法,包括但不限于压滤、离心、抽滤等。有机硅浆渣中的固体含量约20%~30%,因此固渣排放量及排放频次较高,在本发明的优选实施方式中,采用压滤进行固液分离。
19.根据本发明,蒸馏出的高沸物可以被冷凝后回收,进入其他工序进行利用,例如进行精馏作为终产品使用等。
20.根据本发明,所述方法中使用的高沸点惰性油体积要大于浆渣的体积。在本发明的一个实施方式中,在浆渣回收装置中加入高沸点惰性油和浆渣后,浆渣回收装置的液位控制在整个装置体积的35
‑
85%,低于该液位时则补充新的高沸点惰性油进系统。将液位控制在合理范围是为了防止结块和管道及设备被堵塞,有机硅浆渣中固含量约20%~30%,液位控制在前述范围内能有效防止结块及管道和设备堵塞,有利于系统稳定运行。
21.根据本发明,在浆渣回收装置中,浆渣搅拌转速控制在190
‑
500rpm。过低的转速易出现浆渣中固体物沉底结块,过高的转速会磨损设备,影响设备寿命。
22.本发明进一步提供用于前述方法的装置,包括:浆渣回收装置,第一混合物用热交换装置、固液分离装置以及各装置间的连接管线。
23.根据本发明,所述浆渣回收装置中进行有机硅浆渣中高沸物的蒸馏,浆渣回收装置顶部分别设有浆渣入口、高沸点惰性油入口和高沸物排出口,浆渣回收装置底部通过管线连接第一混合物用热交换装置。所述浆渣回收装置具有搅拌结构,所述搅拌结构对加入浆渣回收装置中的浆渣和高沸点惰性油进行搅拌,使其混合均匀并防止浆渣中的固体物沉底。在本发明的一个实施方式中,所述浆渣回收装置是夹套式浆渣闪蒸罐,外壁设置有导热油套、导热油入口和导热油出口,通过导热油加热浆渣回收装置以蒸馏高沸物。
24.根据本发明,所述第一混合物用热交换装置用于降低从浆渣回收装置底部排出的脱高后浆渣与高沸点惰性油混合物的温度。
25.根据本发明,所述第一混合物用热交换装置连接固液分离装置,所述固液分离装置将冷却降温后的脱高后浆渣与高沸点惰性油混合物进行分离,获得分离的高沸点惰性油和脱高后浆渣固体。在本发明的一个实施方式中,所述固液分离装置是压滤机。
26.所述装置进一步包含高沸点惰性油用热交换装置,该热交换装置在固液分离装置和浆渣回收装置的连接管线上。所述经过固液分离装置分离出的高沸点惰性油,经过高沸点惰性油用热交换装置预热,送入浆渣回收装置循环利用。
27.所述装置进一步包含高沸点惰性油存储装置,其在固液分离装置和高沸点惰性油用热交换装置的连接线路上。分离出的高沸点惰性油和外加高沸点惰性油都可以进入高沸点惰性油存储装置中存储,由其输出的高沸点惰性油经过高沸点惰性油用热交换装置预热,再加入浆渣回收装置。
28.在本发明的一个实施方式中,为提高综合能源效率,所述第一混合物用热交换装置和高沸点惰性油用热交换装置是同一个热交换装置,以浆渣回收装置排出的高沸点惰性油和脱高后浆渣的混合物为加热介质,以要输入浆渣回收装置的高沸点惰性油为冷却介质,利用混合物的余热加热高沸点惰性油,用高沸点惰性油降低混合物的温度。
29.在本发明的一个实施方式中,所述装置进一步包含第二混合物用热交换装置,所述第二混合物用热交换装置位于第一混合物用热交换装置和固液分离装置的连接管线上,和第一混合物用热交换装置配合,逐步降低混合物的温度。在本发明的一个实施方式中,第二混合物用热交换装置的冷却介质是冷却水。
30.所述装置进一步包含缓冲装置,所述缓冲装置在混合物用热交换装置和固液分离装置的连接管线上,用于接收冷却后的高沸点惰性油和脱高后浆渣混合物。其个数可以是一个或多个。其可以全部位于热交换装置之后、固液分离装置之前。在存在第一和第二混合物用热交换装置时,其也可以分别位于第一和第二混合物用热交换装置之间以及第二混合物用热交换装置和固液分离装置之间,或者全部位于第一和第二混合物用热交换装置之间,或者全部位于第二混合物用热交换装置和固液分离装置之间。在本发明的一个实施方式中,所述缓冲装置数量为1个,位于热交换装置之后、固液分离装置之前。在本发明的另一个实施方式中,所述缓冲装置数量为2个,一个位于第一和第二混合物用热交换装置之间,一个位于第二混合物用热交换装置和固液分离装置之间。在本发明的再一个实施方式中,所述缓冲装置数量为2个,全部位于第一和第二混合物用热交换装置之间。在本发明的再一个实施方式中,所述缓冲装置数量为2个,全部位于第二混合物用热交换装置和固液分离装
置之间。
31.所述装置进一步包含高沸物冷凝装置,所述高沸物冷凝装置位于浆渣回收装置的高沸物排出口后,将蒸馏出的高沸物进行冷凝。在本发明的一个实施方式中,所述冷凝装置采用冷却水为冷却介质。
32.所述装置进一步包含高沸物回收装置,所述高沸物回收装置位于高沸物冷凝装置后,用于收集存储冷凝后的高沸物。
33.相对于现有技术,本发明取得了以下有益效果:
34.一、通过加入高沸点惰性油的方式,改善加热的均匀性,有利于高沸物通过蒸发的方式分离,保证了高经济价值的物质(如甲基氯硅烷、乙烯基氯硅烷、甲基氯乙硅烷等)的回收率,提高了经济效益。
35.二、由于高经济价值的物质有效回收,降低了最终需要处理的浆渣量,进而减少了浆渣无害化处理的污水量,对环境友好。
36.三、由于使用高沸点惰性油例如硅油作为中间介质,改善了浆渣的流动性,避免了过度回收高经济物质,导致剩余浆渣中固体物结壁、堵塞管路等危害,达到了既提高了高经济物质的回收利用率,又有效避免了固体物质结壁或堵塞管路对蒸馏设备或闪蒸设备的危害的目标。
附图说明:
37.图1:本发明具体实施方式中所用装置的连接以及工艺流程示意图。图中:1、浆渣回收装置
‑
夹套式浆渣闪蒸罐;2、高沸物冷凝器;3、高沸物回收罐;4、真空泵;5、第一混合物用热交换器;6、第二混合物用热交换器;7、缓冲罐;8、循环泵;9、压滤机。
具体实施方式:
38.按照图1所示的设备装置和流程示意图,进行有机硅浆渣中高沸物回收处理。
39.有机硅浆渣通过浆渣入口、硅油通过硅油入口加入到夹套式浆渣闪蒸罐1中,闪蒸罐中的搅拌桨对浆渣和硅油进行搅拌混合,闪蒸罐采用导热油进行加热以蒸馏高沸物。蒸馏出的高沸物从闪蒸罐1顶部的出口排出,经过高沸物冷凝器2的冷凝处理,进入高沸物回收罐3。回收的高沸物可以与粗硅氧烷产品混合进入精馏单元进行分步提纯,最终生成合格产品,达到实现浆渣有效的分离及产品回收的目的,降低生产运营成本。
40.蒸除高沸物后的浆渣为“脱高后浆渣”和硅油形成混合物从闪蒸罐1的底部一同排出闪蒸罐1,所述混合物经管线送入第一混合物用热交换器5,再进入第二混合物用热交换器6,被降温冷却后进入缓冲罐7,通过循环泵8的作用送入压滤机9。压滤机9将脱高后浆渣固体和硅油分离,分离出的硅油送入第一混合物用热交换器5,被预热后从闪蒸罐1的顶部硅油入口进入闪蒸罐循环利用。
41.高沸物冷凝器2和第二混合物用热交换器6都采用冷却水作为冷却介质。第一混合物用热交换器5以闪蒸罐1排出的硅油和脱高后浆渣的混合物为加热介质,以要输入闪蒸罐1的硅油为冷却介质,利用混合物的余热加热硅油,用硅油降低混合物的温度。
42.下文将结合具体实施例对本发明的有机硅浆渣中高沸物回收方法的效果做更进一步的详细说明。应当理解,下列实施例仅为示例性地说明和解释本发明,而不应被解释为
对本发明保护范围的限制。凡基于本发明上述内容所实现的技术均涵盖在本发明旨在保护的范围内。
43.除非另有说明,以下实施例中使用的原料和试剂均为市售商品,或者可以通过已知方法制备,或者来源于上游工艺路线的副产物。
44.实施例:采用高沸点惰性油进行浆渣中高沸物蒸馏回收的效果验证
45.按照硅油与浆渣的体积比为2:1,首先在2l四口烧瓶中添加500ml惰性硅油(蓝星星火有机硅二甲基硅油v100),再缓慢加入约240ml浆渣(约360g),采用控温电加热套进行加热,在190rpm的搅拌速度下,真空泵进行加热真空负压蒸馏,尾部采用冷凝管回收馏分,共计收集馏分190ml。
46.实验条件如下:
47.条件测试1测试2测试3测试4测试5测试6加热温度/℃150170190210220220停留时间/min202060606030绝对压力/mpaa0.040.030.030.030.030.07馏分收集速度(滴/秒)1.52211.51
48.所述各测试后得到的硅油和脱高后浆渣的混合物,其中硅油与脱高后浆渣中的固体分离的效果如下显示:
[0049] 600目400目300目300目+过滤助剂过滤速度几乎不能过滤40ml/h50ml/h100ml/h
[0050]
以测试3所得馏分为例,馏分的分析数据如下:
[0051]
物流名称质量百分比(%)ch3sicl30.004838c2h6sicl20.008634c3h9sicl0.003031c4h
12
si0.043425ch2=chsicl2ch30.024605ch3ch2‑
sicl30.022784ch3ch2‑
sicl2ch2ch30.051541c6h5sicl30.037029(ch3)2clsi
‑
si
‑
cl2ch30.178747ch3cl2si
‑
si
‑
cl2ch30.207195(ch3)2clsi
‑
si
‑
cl(ch3)20.060566(ch3)2clsi
‑
ch2‑
si
‑
cl(ch3)20.033622ch3cl2si
‑
ch2‑
si
‑
cl(ch3)20.083987(ch3)2clsi
‑
o
‑
si
‑
cl(ch3)20.073861(ch3)2clsi
‑
o
‑
si
‑
cl2ch30.035086cl3si
‑
si
‑
cl30.061003其他0.069812
硅油(v100)0
[0052]
从上述实验及结果可见,馏分中未含有硅油,且硅油可以和脱高后浆渣中的固体顺利过滤分离,能够经过分离而被循环利用。通过对分离后的硅油进行检测,确认在所述蒸馏温度下,硅油未发生裂解,其虽然含有少量的浆渣中组分,但不影响硅油在本发明工艺方法中的循环使用。
[0053]
以上,对本发明的实施方式进行了说明。但是,本发明不限定于上述实施方式。凡在本发明的精神和原则之内,所做的任何修改、等同替换、改进等,均应包含在本发明的保护范围之内。