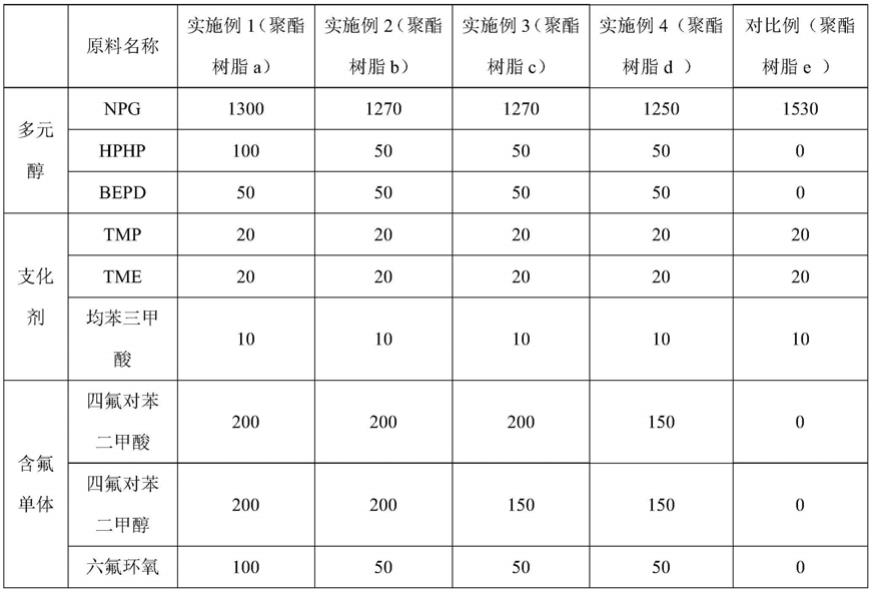
1.本发明属于粉末涂料技术领域,具体涉及一种低温固化耐候聚酯树脂、低温固化耐候粉末涂料及制备方法。
背景技术:2.在自然环境中,粉末涂料受到多种自然因素作用,例如紫外线、高温、雨淋和微生物等,从而导致粉末涂料光泽下降、颜色黯淡、涂膜出现裂纹或并造成涂层失效。因此,对户外用粉末涂料而言,耐候性能是一个非常重要的指标,通常在一些特殊领域如高层建筑,工程机械等领域,存在着超耐候的要求。
3.目前行业内大量超耐候粉末涂料主要采用的是200℃@10~15min和烘烤条件,由于烘烤温度较高,因此需要消耗大量的能源。同时超耐候粉末涂料用聚酯树脂多元酸主体成份为间苯二甲酸,由于其特殊的结构造成树脂的机械性能较差。低温固化由于降低了烘烤温度,可以进一步的拓展基材的应用领域以及降低能源消耗,符合未来的低碳发展方向。
技术实现要素:4.本发明的目的在于提供一种低温固化耐候聚酯树脂及其制备方法,采用含氟单体匹配多元酸及多元醇,制备低温固化耐候聚酯树脂,利用含氟单体中c-f键的键能高的优势显著提升粉末涂料的耐候性能,匹配超耐候结晶树脂机械性能和流平性能优异的特征,实现了制备机械和流平性能优的低温固化超耐候粉末涂料。
5.本发明的目的之二在于提供一种低温固化耐候粉末涂料及其制备方法,以本发明提供的低温固化耐候聚酯树脂和结晶聚酯树脂通过共挤的方式制备低温固化超耐候粉末涂料,利用结晶超耐候聚酯树脂的流平优和机械性能好的特点显著改善粉末涂料的流平和机械性能。
6.为实现上述目的,本发明采取的技术方案如下:
7.一种低温固化耐候聚酯树脂,所述低温固化耐候聚酯树脂包括以下重量百分比的原料:多元醇32~45%;多元酸44~55%;支化剂0.5~2%;含氟单体5~25%;酸解剂8~13%;催化剂0.03~0.15%;固化促进剂0.01~1%;所述含氟单体由含氟醇、含氟酸、含氟环氧按照任意配比组成。
8.所述低温固化耐候聚酯树脂的酸值为28~36mgkoh/g,数均分子量在2500~5000g/mol,玻璃化转变温度≥60℃。
9.所述含氟醇为四氟对苯二甲醇、4-甲基-2,3,5,6-四氟苯甲醇、2,3,5,6-四氟苄醇、4-甲氧基甲基-2,3,5,6-四氟苯甲醇、六氟异丙醇、六氟丁醇中的任意一种或多种。
10.所述含氟酸为四氟对苯二甲酸、四氟邻苯二甲酸、2,4-二氟-3-甲氧基苯甲酸中的任意一种或多种。
11.所述含氟酸可替换为4,4,-(六氟异丙烯)二酞酸酐。
12.所述含氟环氧为六氟环氧丙烷二聚体、六氟环氧丙烷三聚体、六氟环氧丙烷中的任意一中或多种。所述含氟单体优选为由四氟对苯二甲酸、四氟对苯二甲醇、六氟环氧丙烷按照质量比1-5:1-5:1组成。
13.所述多元醇为新戊二醇,或新戊二醇与羟基特戊酸新戊二醇单酯、乙基丁基丙二醇中的任意一种或多种的组合物,优选为新戊二醇、羟基特戊酸新戊二醇单酯、乙基丁基丙二醇按照质量比30-20:1-3:1-10组成的混合多元醇。
14.所述多元酸为间苯二甲酸、环己烷二甲酸中的任意一种或两种,优选为间苯二甲酸、环己烷二甲酸按照质量比15-25:1组成的混合多元酸。
15.所述支化剂为三羟甲基丙烷、三羟甲基乙烷、均苯三甲酸中的任意一种或多种,优选为三羟甲基丙烷、三羟甲基乙烷、均苯三甲酸按照质量比1.5-2.5:1.5-2.5:1组成的混合物。
16.所述催化剂为锡类催化剂,优选为二丁基氧化锡,三丁基氧化锡,二羟基丁基氯化锡,草酸亚锡,单丁基氧化锡中的任意一种或多种,更优选为单丁基氧化锡、草酸亚锡按照质量比1:2.5-3.5组成的混合催化剂。
17.所述酸解剂为间苯二甲酸、富马酸、环己烷二甲酸中的任意一种或多种;如果是多种的混合物,则间苯二甲酸的摩尔含量》70%;优选为间苯二甲酸、富马酸、环己烷二甲酸按照质量比10-15:1-2:1-2组成的混合物。
18.所述固化促进剂为四乙基溴化铵、四甲基溴化铵、苄基三乙基氯化铵、三苯基乙基溴化膦、二月桂酸二丁基锡中的任意一种或多种。
19.本发明提供的所述低温固化耐候聚酯树脂的制备方法,包括以下步骤:
20.(1)将配方量多元醇、多元酸、支化剂、含氟单体中的含氟醇及含氟酸、催化剂同时投入反应釜中,在惰性气氛中升温至235~255℃并维持至体系澄清且酸值达到5~20mgkoh/g树脂;
21.(2)加入配方量的酸解剂于235~250℃酸解封端1.5~2h;
22.(3)待体系的酸值至40~55mgkoh/g树脂时,降温至230~240℃并真空缩聚至体系的酸值达到28~36mgkoh/g树脂;
23.(4)降温至180~230℃,加入配方量的固化促进剂并维持5~30min,即可得到所述低温固化耐候聚酯树脂。
24.步骤(1)中,所述惰性气氛为氮气气氛。
25.本发明提供的一种低温固化耐候粉末涂料,所述低温固化耐候粉末涂料包括以下重量百分比的原料:
26.低温固化耐候聚酯树脂:50~60%;
27.结晶聚酯树脂:5~15%
28.异氰尿酸三缩水甘油酯:4~6%;
29.流平剂0.8~1.2%;
30.颜料0.7~38;
31.无机填料0~35%;
32.助剂0~1%。
33.所述结晶聚酯树脂为结晶超耐候聚酯树脂pe 5900,晶体熔融温度
为105~120℃。
34.所述流平剂为glp588系二氧化硅吸附的聚丙烯酸酯流平剂。
35.所述无机填料为硫酸钡、云母中的任意一种或两种。
36.所述助剂为润湿剂、脱气剂、偶联剂或增电剂。
37.所述颜料为无机料,如钛白粉、铁黄、碳黑中的任意一种或多种。
38.本发明提供的低温固化耐候粉末涂料的制备方法包括以下步骤:原料按配方量混合
→
通过挤出机挤出
→
压片
→
粉碎
→
研磨
→
200目过筛
→
包装成品。挤出机进行熔融挤出时的参数为:螺杆转速45hz,i区温度95~105℃,ii区温度105~115℃。
39.本发明还提供了由所述低温固化耐候粉末涂料形成的漆膜。
40.本发明提供的低温固化耐候粉末涂料,以低温固化耐候聚酯树脂作为基体树脂,低温固化耐候聚酯树脂合成过程中所使用的多元酸和多元醇单体为超耐侯体系,叠加含氟单体的c-f的高键能的优势,实现了粉末涂料的超长耐候。并在配方中使用了结晶聚酯树脂与低温固化耐候聚酯树脂相互配合,结晶超耐候聚酯树脂pe 5900的结晶性能主要有下述两个优点:结晶树脂在130~200℃区间粘度相对于常规树脂而言显著的偏低,因此有利于流平等级的提升;结晶树脂的分子主链优异的柔韧性能显著的改善了涂层的冲击性能。因此本发明所述粉末涂料相对于常规耐候粉末涂料,其经过150~160℃低温15~20min烘烤之后得到的漆膜具备超耐候性能的同时流平和机械性能优异。
具体实施方式
41.下面结合实施例,对本发明进行详细说明。
42.各实施例及对比例中的低温固化耐候聚酯树脂的原料组成及用量、及制备过程中的酸值控制如表1所示。
43.表1聚酯树脂a原料配方、生产过程中的控制酸值和性能(原料单位:g)
44.[0045][0046]
上述各实施例及对比例中的低温固化耐候聚酯树脂均采用以下方法进行制备,具体步骤如下:
[0047]
(1)将配方量多元醇、多元酸、支化剂、含氟单体中的含氟醇及含氟酸、催化剂同时投入反应釜中,在氮气气氛中升温至235~255℃并维持至体系澄清且酸值达到5~15mgkoh/g树脂;
[0048]
(2)加入配方量的酸解剂于235~250℃酸解封端1.5~2h;
[0049]
(3)待体系的酸值至43~48mgkoh/g树脂时,降温至230~240℃并真空(~0.1mpa)缩聚至体系的酸值达到28~36mgkoh/g树脂;
[0050]
(4)降温至180~230℃,加入配方量的固化促进剂并维持5~30min,即可得到所述低温固化耐候聚酯树脂;
[0051]
其中不同阶段的酸值控制指标标注于表1中。
[0052]
以上述各实施例及对比例制备得到的聚酯树脂为聚酯树脂a,结晶超耐候聚酯树脂pe 5900为聚酯树脂b,制备低温固化耐候粉末涂料,低温固化耐候粉末涂料的配方如表2所示。
[0053]
表2为采用聚酯树脂a和聚酯树脂b制备得到的低温固化粉末涂料的配方(单位:g)
[0054][0055]
参照表2中的配方将不同原材料称好
→
在混料罐中充分预混合
→
通过螺杆挤出机熔融挤出
→
压片
→
粉碎
→
研磨
→
200目过筛
→
包装成品即得到低温固化耐候粉末涂料(配方9为对比样品),挤出机进行熔融挤出时的参数为:螺杆转速45hz,i区温度95~105℃,ii区温度105~115℃,配方1-9对应的粉末涂料均是在相同的工艺流程及工艺参数下进行生产的。
[0056]
随后将粉末涂料喷涂在经表面磷化处理之后的铁板上,固化,固化条件155℃下烘烤20min,再测试涂层的不同性能,结果见表3。
[0057]
表3.不同配方下粉末涂料的性能汇总。
[0058][0059]
备注*:流平等级pci从1到10代表着流平性能的提升,其中pci~10代表着流平性能和镜子一样,目前有商用的标准板用于评估pci等级。
[0060]
从表3中可以看出,对比对比例中的低温固化聚酯树脂e和粉末配方9,本发明提供的低温固化超耐侯粉末涂料以及对应的聚酯树脂具备着流平性能和机械性能优异的同时耐候性能显著提高。
[0061]
上述参照实施例对一种低温固化耐候聚酯树脂、低温固化耐候粉末涂料及制备方法进行的详细描述,是说明性的而不是限定性的,可按照所限定范围列举出若干个实施例,因此在不脱离本发明总体构思下的变化和修改,应属本发明的保护范围之内。