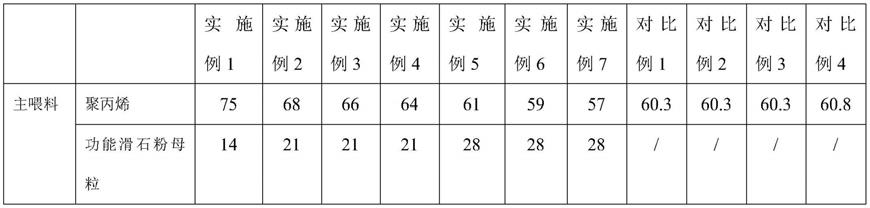
1.本发明属于高分子材料及其加工技术领域,涉及一种改善粘模、高性能、薄壁化聚丙烯复合材料及其制备方法。
背景技术:2.随着汽车工业的快速发展及环境问题的日益严峻,各大主流汽车厂商都致力于整车轻量化的相关研究。对于汽车用量最大的聚丙烯塑料件来说,对其进行薄壁化设计在整车轻量化技术手段中备受青睐。目前,各大主流汽车厂商用的汽车塑料件的传统壁厚在2.5-3.0mm,薄壁化设计之后其壁厚将达到1.8-2.2mm。零件壁厚减薄之后,为确保零件的外观、性能不受损失,薄壁化零件相比传统壁厚零件在材料性能的要求上表现典型的高刚性、高韧性、高流动性的一类材料,所以其在配方组成上是需要选择合适的聚丙烯基料、高性能的填料、弹性体增韧剂来协同实现。
3.目前,薄壁化聚丙烯材料广泛应用于汽车立柱、门板、仪表板、保险杠等内外饰件上,当遇到一些结构复杂、尺寸较大、流程较长的薄壁零件,如薄壁保险杠零件,材料在注塑生产过程中,零件局部位置的壁厚越薄、材料熔体在壁厚较薄的位置容易受到强流动剪切力影响,会导致材料出现一定的表层位移,在经历保压之后,零件表层与模具表面贴合比较紧,脱模时会出现一定的粘模现象,严重影响零件的外观,特别是随着零件注塑时间的加长,模具温度的升高,粘模现象会加剧,不利于零件的连续化生产。因此,如何解决薄壁化零件在注塑生产过程中出现的粘模问题具有重要的意义。
技术实现要素:4.为了解决上述问题,本发明的目的是提供一种改善粘模、高性能、薄壁化聚丙烯复合材料及其制备方法。以解决现有技术的上述技术问题。该方法是通过在薄壁化聚丙烯复合材料配方设计中,采用一种功能滑石粉母粒来取代传统配方中直接添加滑石粉+润滑剂等助剂来实现提升复合材料体系的润滑性能;该功能滑石粉母粒是由高流动聚丙烯、弹性体、高目数滑石粉、复合润滑剂、偶联剂等组成;复合润滑剂是采用乙撑双硬脂基酰胺与硬脂酸盐按1:1比例进行复配,它具有很好的内、外润滑的功效;偶联剂为钛酸酯类偶联剂,它可以在滑石粉表面形成一种覆盖膜,改善滑石粉原有亲水性质,能提升滑石粉与聚丙烯之间的界面结合力与相容性,从而可以提升聚丙烯复合材料体系的综合力学性能;同时功能滑石粉母粒以高流动性聚丙烯为载体,在随着聚合物体系从双螺杆挤出或注塑机中挤出时,能很好的将高目数滑石粉、弹性体均匀分散到复合材料体系,同时复合润滑剂也会首先向材料熔体外侧移动,富集于材料表层,达到提升复合材料体系润滑性,从而改善材料在注塑生产过程中出现的粘模问题;另外高目数滑石粉,优选具有规整层状结构的特点,可利用其层间的空隙来吸附固化材料在挤出生产过程中产生的气味小分子,可降低复合材料体系的气味散发性能,同时规整的层状结构有利于层间滑动,对复合材料注塑后润混有帮助,可与复合润滑剂一同发挥协同作用来改善粘模问题。
5.为实现上述目的,本发明具体采用以下技术方案:
6.一种改善粘模、高性能、薄壁化聚丙烯复合材料,其包括以下重量份计的原料:
7.聚丙烯:57-75;
8.功能滑石粉母粒:14-28;
9.弹性体:8-17;
10.抗氧剂:0-1;
11.其它助剂:0-3。
12.其中,
13.所述的聚丙烯基体树脂采用高流动性共聚聚丙烯的一种或两种混合物,熔融指数(230℃,2.16kg)在60g-100g/10min左右。
14.所述的功能滑石粉母粒由下列组分按重量份数制备而成:高流动聚丙烯10份、弹性体15份、高目数滑石粉71.5份、复合润滑剂1.5份、偶联剂2份。其中所述的高流动性聚丙烯为熔融指数(230℃,2.16kg)在60-100g/10min左右;所述的弹性体为一种乙烯和辛烯共聚物;所述的高目数滑石粉为10000目作用滑石粉,具有规整层状结构的特定;所述的复合润滑剂是采用乙撑双硬脂基酰胺与硬脂酸盐按1:1比例进行复配,其中乙撑双硬脂基酰胺为n,n_亚乙基双硬脂酰胺,硬脂酸盐为硬脂酸钙和硬脂酸镁的一种;所述的偶联剂为钛酸酯类偶联剂。
15.所述的弹性体为一种乙烯和辛烯共聚物,其密度在0.86-0.90g/cm3,熔融指数在0.5-6g/10min。
16.所述的抗氧剂为本领域技术人员认为所需的抗氧剂,主要为四[β-(3,5-二叔丁基-4-羟基苯基)丙酸]季戊四醇酯(抗氧剂1010)、三[2,4-二叔丁基苯基]亚磷酸酯(抗氧剂168)、硫代二丙酸十八酯(抗氧剂dstp)、β-(3,5-二叔丁基-4-羟基苯基)丙酸正十八碳醇酯(抗氧剂1076)、中的一种或者两种以上混合组成。
[0017]
所述的其它助剂为主要为本领域技术人员认为所需的各种颜色成分、光稳定剂、加工助剂等的一种或几种的组合物。
[0018]
上述改善粘模、高性能、薄壁化聚丙烯复合材料的制备方法,其步骤如下:
[0019]
a.功能滑石粉母粒的制备:
[0020]
按重量组分将高流动聚丙烯、弹性体、高目数滑石粉、复合润滑剂、偶联剂一同加入高速混料机进行混合均匀后,接着转入到密炼机的混炼室内进行高速密炼混合,接着将密炼混合好的块状物料转移到双腕式喂料口进行喂料,由单螺杆挤出机对其进行挤出、风冷、造粒制备出功能滑石粉母粒。其中密炼机中的密炼室的温度设置在170-190℃,单螺杆直径为70mm,长径比为12,单螺杆挤出机分为三段控制温度,从喂料口到机头各段的温度依次为180℃、200℃、210℃。
[0021]
b.改善脱模、高性能、薄壁化聚丙烯复合材料及其制备:
[0022]
(1)按照质量比例称配好上述各组分;
[0023]
(2)将聚丙烯、功能滑石粉母粒、弹性体、抗氧剂、其它助剂等组分放于高速混合机中高速混合5-10min;
[0024]
(3)将上述混合均匀后的原料从主喂料口加入到双螺杆挤出机中,进行熔融挤出、拉条、冷却、造粒后,再经过烘料处理制备出改善脱模、高性能、薄壁化聚丙烯复合材料,其
中双螺杆挤出机各区的加工工艺温度分别为:一区:180-205℃,二区190-205℃,三区210-215℃,四区205-210℃,机头190-200℃。整个挤出过程的时间约为2分钟,压力12-18mpa,主螺杆转速500-800r/min,水槽温度为30~60℃,在双螺杆挤出机两侧添加抽双真空设置,双真空的真空度为-0.07mpa~-0.08mpa,烘料处理采用烘料工艺:a罐储料,b罐烘料,c罐冷却,其中b罐烘料工艺:130℃*4h。
[0025]
本发明的优点在于:
[0026]
(1)本发明在薄壁化聚丙烯复合材料的配方设计中上采用一种高效的功能滑石粉母粒来代替传统的改性聚丙烯配方直接用滑石粉+助剂方式来做料,功能滑石粉母粒以高流动性聚丙烯为载体,在随着聚合物体系从双螺杆挤出或注塑机中挤出时,能很好的将高目数滑石粉、弹性体均匀分散到复合材料体系,同时复合润滑剂也会首先向材料熔体外侧移动,富集于材料表层,可达到提升整个材料体系润滑性能;
[0027]
(2)本发明功能滑石粉母粒中的钛酸酯类偶联剂的加入可以加大滑石粉与聚丙烯之间的界面结合力与相容性,从而可进步提升聚丙烯复合材料体系的综合力学性能;
[0028]
(3)本发明利用功能滑石粉母粒中高目数滑石粉的规整层状结构的层间空隙特点,可吸附固化材料在挤出生产过程中产生的气味小分子,可降低复合材料体系的气味散发性能,还利用其层间滑动的特点可与复合润滑剂一起发挥协同作用来改善材料在注塑生产过程中的出现的粘模问题;
[0029]
(4)本发明提出的改善粘模、高性能、薄壁化聚丙烯复合材料的制备工艺比较简单,生产成本较低,可制备出的综合性能更优异的薄壁化聚丙烯复合材料。
具体实施方式
[0030]
下面结合具体实例对本发明进行详细说明。除特殊说明外,实施例中各组分都为重量份。
[0031]
本发明实施例和对比例所含各组分含量见表1。
[0032]
表1 实施例和对比例中的各主要组分含量(质量百分含量)
[0033][0034][0035]
上述表1中的实施例和对比例中的述的聚丙烯为共聚聚丙烯,采用ep5075x、
bx3920按2:1复配而成,牌号ep5075x为中沙石化生产,熔体流动速率分别为60g/10min,牌号bx3920为韩国sk公司生产,熔体流动速率为100g/10min。所述的滑石粉为10000目左右的滑石粉,来自上海缘江化工有限公司,所述的弹性体为lg公司生产的热塑性poe弹性体,牌号为168。所述的功能滑石粉母粒中的高流动聚丙烯、高目数滑石粉、弹性体与上述一样;所述的功能滑石粉母粒中复合润滑剂是采用乙撑双硬脂基酰胺与硬脂酸盐按1:1比例进行复配,其中乙撑双硬脂基酰胺为n,n_亚乙基双硬脂酰胺,西格玛奥德里奇(上海)贸易有限公司,硬脂酸盐为硬脂酸镁,来自上海源叶生物科技有限公司;所述的功能滑石粉母粒中的偶联剂为钛酸酯类偶联剂,牌号是tc-70,来自宏盛精细化工公司;润滑剂1为n,n_亚乙基双硬脂酰胺,润滑剂2为硬脂酸镁;所述的抗氧剂为1010(四[β-(3,5-二叔丁基-4-羟基苯基)丙酸]季戊四醇酯)/三[2,4-二叔丁基苯基]亚磷酸酯(抗氧剂168)/dstp(硫代二丙酸十八酯)按质量比1:2:1复配型抗氧剂。所述的其它助剂主要是指颜色成分、光稳定剂等。
[0036]
上述实施例具体实施方式展开如下:
[0037]
a.功能滑石粉母粒的制备:
[0038]
按重量组分将高流动聚丙烯、弹性体、高目数滑石粉、复合润滑剂、偶联剂一同加入高速混料机进行混合均匀后,接着转入到密炼机的混炼室内进行高速密炼混合,接着将密炼混合好的块状物料转移到双腕式喂料口进行喂料,由单螺杆挤出机对其进行挤出、风冷、造粒制备出功能滑石粉母粒。其中密炼机中的密炼室的温度设置在170-190℃,单螺杆直径为70mm,长径比为12,单螺杆挤出机分为三段控制温度,从喂料口到机头各段的温度依次为180℃、200℃、210℃。
[0039]
b.改善脱模、高性能、薄壁化聚丙烯复合材料及其制备:
[0040]
(1)按照质量比例称配好上述各组分;
[0041]
(2)将聚丙烯、功能滑石粉母粒、弹性体、抗氧剂、其它助剂等组分放于高速混合机中高速混合5-10min;
[0042]
(3)将上述混合均匀后的原料从主喂料口加入到双螺杆挤出机中,进行熔融挤出、拉条、冷却、造粒后,再经过烘料处理制备出改善脱模、高性能、薄壁化聚丙烯复合材料,其中双螺杆挤出机各区的加工工艺温度分别为:一区:180-205℃,二区190-205℃,三区210-215℃,四区205-210℃,机头190-200℃。整个挤出过程的时间约为2分钟,压力12-18mpa,主螺杆转速500-800r/min,水槽温度为30~60℃,在双螺杆挤出机两侧添加抽双真空设置,双真空的真空度为-0.07mpa~-0.08mpa,烘料处理采用烘料工艺:a罐储料,b罐烘料,c罐冷却,其中b罐烘料工艺:130℃*4h。
[0043]
c.将按上述制备的复合材料粒子在80-100℃的鼓风烘箱中干燥2小时,然后将干燥好的粒子在注射成型机上进行注塑成型,然后进行性能测试。
[0044]
d.基本力学性能测试:密度按照iso1183-1标准进行测试,熔融指数按照iso1133-1标准进行测试,测试温度为230℃,负荷2.16kg,拉伸强度按照iso527-2标准进行检验,样条尺寸为170*10*4mm,拉伸速度50mm/min,弯曲模量按照iso178标准进行检验,样条尺寸为80*10*4mm,跨距64mm,弯曲速度为2mm/min,简支梁缺口冲击强度按照iso179-1标准进行检验,样条尺寸为80*10*4mm,缺口深度为试样宽度的五分之一。零件气味测试按照pv3900测方方法进行评判,取30模之后的零件,裁样放在1l气味瓶中80℃*2h后到60℃进行评价。零件的粘模现象改善效果评估如下:将材料在特定的注塑工艺下,注塑成300*100*1.5mm样
板,样板注塑30模之后开始评估,通过肉眼观察样板在脱模时其表面的粘模效果,可分为无粘模现象、有轻微粘模现象、有较多粘模现象,有严重粘模现象。
[0045]
表2 实施例和对比例中材料性能测试数据
[0046][0047][0048]
从上述表中的实施例和对比例的数据结果可以发现,通过选择合适的聚丙烯基料、高性能的填料、弹性体增韧剂可制备出高熔指、高模量、高韧性的满足薄壁化材料的性能要求的高性能材料。特别是由实施例1-7数据可发现,通过配方的合理设计,可制备出不同规格的薄壁化材料,其中实施例7的刚韧平衡性能最优,其材料的流动性接近40,完全可用来制备超薄壁零件;实施例1-7中与对比例1-4可以发现,添加高效的功能滑石粉母粒的薄壁化的聚丙烯复合材料体系几乎没有粘模现象,而采用滑石粉+助剂方案制备复合材料体系不同成度出现了粘模现象。由实施例7与对比例1-4进一步对比发现,添加润滑剂会对材料体系的粘模有明显改善效果;发现相同添加量下,润滑剂采用复配方式对材料体系的粘模改善要明显好于单一润滑体系,同时进步对比实施例7与对比例3发现,本方案实施例7在选用复配润滑剂预先做到功能滑石粉母粒中,可起到总添加量少,但是其对改善粘模效果要好于对比例3;同时发现无粘模现象有改善的同时其零件的气味也比较好,首先是本方
案中选用了规整层状结构的滑石粉层间空隙的吸附固化功能起到作用,其次说明了材料熔体在流动过程中因润滑性能提升之后,减少材料熔体在流动过程剪切热的产生,两者发挥协同作用,从而降低了材料体系的气味小分子散发;综上,本发明在薄壁化聚丙烯复合材料的配方设计中上采用一种高效的功能滑石粉母粒来代替传统的改性聚丙烯配方直接用滑石粉+助剂方式来做料,能制备出一种改善粘模、高性能、薄壁化聚丙烯复合材料。