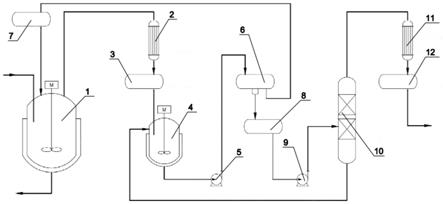
1.本发明涉及2-乙烯氧基乙氧基丙烯酸乙酯的制备方法,更具体地说,涉及一种制备2-乙烯氧基乙氧基丙烯酸乙酯的方法及装置。
背景技术:2.2-乙烯氧基乙氧基丙烯酸乙酯(veea),是一种双官能度的特种uv丙烯酸酯,结构中含有醚键和酯键,具有较低的粘度,对聚合物有较好的相容性,同时由于具有两个官能度,具有快速反应固化的特性。广泛应用于涂料、油墨和胶粘剂中。
3.文献报道veea的合成路线有酯交换法、酰氯法。目前,工业化生产veea主要以酯交换法为主,即丙烯酸甲酯与二乙二醇乙烯基醚在催化作用下反应生成veea和甲醇。由于酯交换反应过程是可逆的,反应产物的生成速度很大程度上由甲醇的移出速度决定。在veea工业生产中为获得较高的反应转化率,采用反应和精馏的组合或反应精馏耦合的反应装置进行酯交换反应,通过加入共沸剂,共沸剂与反应生成的甲醇形成共沸物,与部分丙烯酸甲酯一起被采出,然后在精馏装置中将共沸采出物移出。但在生产过程中,受到精馏回流液中低沸点甲醇含量较高、精馏回流比较大,返混严重的限制,甲醇不能及时、快速的移出反应装置,导致反应转化率不高,反应时间较长,原料和能量的消耗较大等问题。
技术实现要素:4.针对上述存在的问题,本发明的目的是提供一种制备2-乙烯氧基乙氧基丙烯酸乙酯的方法,将酯交换反应后的釜顶采出物进行水洗萃取,采出物中的甲醇萃取分离至水相中,分液后有机相回流组分中甲醇含量<0.5%,有效地解决了甲醇移出不及时,回流返混严重的问题,提高了甲醇的移出速度及酯交换反应的转化率。
5.本发明的上述技术目的是通过以下技术方案得以实现的,一种制备2-乙烯氧基乙氧基丙烯酸乙酯的方法,将丙烯酸甲酯、二乙二醇乙烯基醚、共沸剂、催化剂和阻聚剂加入反应釜中混合,在70~100℃下进行酯交换反应,将反应釜顶部物料采出后冷凝,冷凝后的采出物进行水洗萃取,静置分液,分液后上层有机相回流至所述反应釜中继续进行反应,下层水相进行精馏,冷凝后获得甲醇。
6.本发明中,丙烯酸甲酯和二乙二醇乙烯基醚进行酯交换反应,生成产物veea和甲醇,反应生成的甲醇与共沸剂形成共沸物,并与部分丙烯酸甲酯一起从反应釜顶部采出并冷凝,冷凝后的采出物加入水进行水洗萃取,采出物中的甲醇进入水相中,并与有机相分离。分液后的有机相中甲醇含量<0.5%,回流至所述反应釜中继续进行反应,从而有效避免了甲醇移出不及时,回流返混严重的问题,同时减低了原料用量。随后将水相中的甲醇水溶液进行精馏,冷凝后获得高纯度的甲醇,从而实现了高纯度甲醇的回收。
7.本发明中,所述水洗的水洗温度为10~30℃,水洗时间为10~60min。优选地,所述水洗的水洗温度20℃,水洗时间为30min。
8.本发明中,所述水洗过程中,水的用量与二乙二醇乙烯基醚的质量比0.5~2:1。优
选地,水的用量与二乙二醇乙烯基醚的质量比0.5~1.5:1。
9.本发明中,所述共沸剂为c5~c7的环状烷烃和/或c5~c7的直链烷烃。
10.优选地,本发明中,所述共沸剂包括环己烷和/或正己烷。
11.本发明中,所述催化剂为氢氧化锂、碳酸锂、氢氧化钾、碳酸钾、氧化锌、钛酸四丁酯和二丁基氧化锡中的一种或多种。
12.本发明中,所述阻聚剂为对苯二酚、对羟基苯甲醚、吩噻嗪、二丁基二硫代氨基甲酸铜、4-羟基-2,2,6,6-四甲基哌啶-1-氧自由基和四甲基哌啶氮氧自由基亚磷酸三酯中的一种或多种。
13.本发明中,所述丙烯酸甲酯、共沸剂和二乙二醇乙烯基醚的质量比为0.68~1.4:1.1~4:1。优选地,所述丙烯酸甲酯、共沸剂和二乙二醇乙烯基醚的质量比为0.72~1.05:1.1~2:1。
14.本发明中,所述催化剂、阻聚剂和二乙二醇乙烯基醚的质量比为0.0025~0.02:0.0002~0.001:1。优选地,所述催化剂、阻聚剂和二乙二醇乙烯基醚的质量比为0.005~0.02:0.0005~0.001:1。
15.本发明的另一个目的在于提供一种制备2-乙烯氧基乙氧基丙烯酸乙酯的装置,包括:
16.反应釜,所述反应釜连接有第一冷凝器,所述第一冷凝器的出口与共沸液缓冲罐相连接;
17.水洗釜,所述水洗釜与所述共沸液缓冲罐的出口相连接;
18.分液罐,所述分液罐与所述水洗釜的出口相连接,所述分液罐包括有两个出口,其中一个出口与所述反应釜相连接;
19.精馏塔,所述精馏塔与所述分液罐的另一个出口相连接,所述精馏塔的塔釜与所述水洗釜相连接,所述精馏塔的塔顶连接有第二冷凝器。
20.本发明具有以下有益效果:
21.(1)本发明将酯交换反应后的釜顶采出物进行水洗萃取,采出物中的甲醇萃取分离至水相中,从而使分液后有机相回流组分中甲醇含量<0.5%,有效地解决了甲醇移出不及时,回流返混严重的问题,提高了甲醇的移出速度及酯交换反应的转化率。
22.(2)本发明优选合适的阻聚剂和催化剂,合适的阻聚剂、催化剂与反应原料的比例,制备产物veea,提高了反应速率,有效地抑制了反应物和产物的自聚或交叉聚合反应,大大降低安全隐患;此外,还减少副反应的发生,提高veea的选择性和收率。
23.(3)本发明精馏过程操作简单,可有效地从共沸物中分离出甲醇,且精馏获得的甲醇回收率高,纯度高。
附图说明
24.图1为本发明的结构示意图。
25.图中,1.反应釜;2.第一冷凝器;3.共沸液缓冲罐;4.水洗釜;5.水洗出料泵;6.分液罐;7.回流缓存罐;8.水相缓存罐;9.精馏塔进料泵;10.精馏塔;11.第二冷凝器;12.甲醇缓存罐。
具体实施方式
26.为了更好地理解本发明,下面结合实施例进一步阐明本发明的内容,但本发明的内容不仅仅局限于下面的实施例。
27.实施例1
28.如图1所示,一种制备2-乙烯氧基乙氧基丙烯酸乙酯的装置,包括:反应釜1、水洗釜4、分液罐6和精馏塔10,反应釜1的顶部连接有第一冷凝器2和回流缓存罐7,第一冷凝器2的出口与共沸液缓冲罐3相连接,共沸液缓冲罐3的出口与水洗釜4的进口相连接。
29.水洗釜4的出口通过水洗出料泵5与分液罐6相连接,分液罐6包括有两个出口,其中一个出口与回流缓存罐7相连接,另一个出口与水相缓存罐8相连接。
30.水相缓存罐8通过精馏塔进料泵9与精馏塔10相连接,精馏塔10的塔釜与水洗釜4相连接,精馏塔10的塔顶与第二冷凝器11相连接。第二冷凝器11的出口与甲醇缓存罐12相连接。
31.本实施例中,2-乙烯氧基乙氧基丙烯酸乙酯的制备方法为:
32.(1)将315kg丙烯酸甲酯、400kg二乙二醇乙烯基醚、800kg环己烷、4kg二丁基氧化锡和0.2kg四甲基哌啶氮氧自由基亚磷酸三酯通过原料管线加入反应釜1中进行酯交换反应,反应温度78~85℃。
33.(2)反应过程中生成甲醇,反应生成的甲醇与环己烷形成共沸物,并与部分丙烯酸甲酯一起被采出至第一冷凝器2中,采出物比例随反应程度变化,采出物经冷凝后进入共沸液缓冲罐3。采出物由共沸液缓冲罐3直接进入水洗釜4中进行水洗,水洗釜4中预先加入水,加入水的量和上一釜反应剩余水量一共400kg,水洗温度20℃,水洗时间30min。由水洗釜4的液位控制水洗釜4出液流量,并通过水洗出料泵5进入分液罐6中,分液罐6预先加入适量环己烷溶剂及丙烯酸甲酯(或上一釜反应剩余)。
34.(3)物料在分液罐6中的静置分液时间为30min,上层有机相进入回流缓存罐7中,回流的有机溶剂中甲醇含量<0.1%,根据反应釜的液位连锁控制有机溶剂的回流流量;下层水相直接下放至水相缓存罐8,通过精馏塔进料泵9稳定进入精馏塔10中,精馏分离甲醇水溶液,汽化甲醇由精馏塔10塔顶进入第二冷凝器11中冷凝,冷凝后进入甲醇缓存罐12,水由精馏塔10塔釜回到水洗釜4中,重复使用。
35.(4)上述步骤(1)~(3)为连续过程,在此操作条件下,反应14h后,反应釜1顶部采出物中甲醇含量<0.1%,回流溶剂中无甲醇,取样分析,反应转化率98.80%,选择性99.10%,反应结束;反应液除溶剂后回收产品,产品收率97.6%,副产焦油收率1.9%。精馏回收高纯甲醇91.6%,含水量0.2%,次级甲醇含水量约20%,次级甲醇返回水相缓存罐8中。
36.实施例2
37.本实施例与实施例1的区别在于:投料420kg丙烯酸甲酯,反应时间12h,反应转化率98.61%,选择性98.82%;产品收率96.9%,副产焦油收率2.6%,精馏回收高纯甲醇90.9%,含水量0.2%,次级甲醇含水量约20%,次级甲醇返回水相缓存罐中。
38.实施例3
39.本实施例与实施例1的区别在于:投料270kg丙烯酸甲酯,反应时间18h,反应转化率96.73%,选择性98.54%;产品收率94.8%,副产焦油收率3.7%,精馏回收高纯甲醇
89.1%,含水量0.2%,次级甲醇含水量约20%,次级甲醇返回水相缓存罐中。
40.实施例4
41.本实施例与实施例1的区别在于:投料400kg环己烷,反应时间16h,反应转化率97.94%,选择性98.63%;产品收率96.1%,副产焦油收率3.3%。
42.实施例5
43.本实施例与实施例1的区别在于:投料800kg正己烷,反应时间14h,反应转化率98.51%,选择性98.05%;产品收率95.8%,副产焦油收率3.6%。
44.实施例6
45.本实施例与实施例1的区别在于:投料8kg氧化二丁基锡,反应时间12h,反应转化率99.06%,选择性98.12%;产品收率96.4%,副产焦油收率3.0%。
46.实施例7
47.本实施例与实施例1的区别在于:投料1kg氧化二丁基锡,反应时间22h,反应转化率95.90%,选择性98.41%;产品收率94.26%,副产焦油收率4.1%。
48.实施例8
49.本实施例与实施例1的区别在于:水洗釜洗涤水用量600kg,反应时间14h,反应转化率98.74%,选择性98.93%;产品收率97.4%,副产焦油收率2.0%。
50.实施例9
51.本实施例与实施例1的区别在于:水洗釜洗涤水用量200kg,反应时间16h,反应转化率98.03%,选择性98.80%;产品收率97.0%,副产焦油收率2.2%。
52.前述的实例仅是说明性的,用于解释本发明所述方法的一些特征。所附的权利要求旨在要求可以设想的尽可能广的范围,且本文所呈现的实施例为申请人真实试验结果加以论证。因此,申请人的用意是所附的权利要求不被说明本发明的特征的示例的选择限制。在权利要求中所用的一些数值范围也包括了在其之内的子范围,这些范围中的变化也应在可能的情况下解释为被所附的权利要求覆盖。