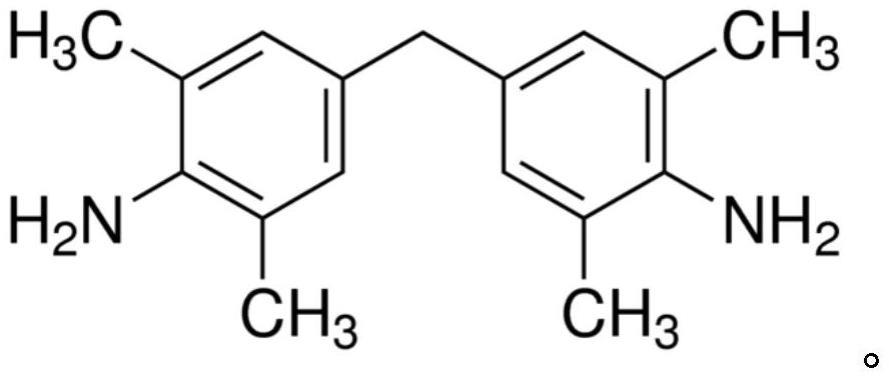
快速固化的树脂组合物和含有其的复合材料
具体实施方式
1.纤维增强聚合物复合材料已用于制造承重结构。高性能结构如航空器和汽车车身零件的主要和次要结构可以通过在模具表面上铺放多个可热固化预浸料层然后固结并固化来制造。每个可热固化预浸料由浸渍或嵌入基质树脂中的增强纤维层构成,该基质树脂包括热固性树脂,如环氧树脂。使用环氧树脂是因为它们以其耐热性和耐化学性为人所知。
2.用于航空航天结构中的复合材料的设计典型地考虑固化的材料的热/湿性能。热/湿性能是指材料在长时间暴露于相当高的温度和高湿度条件后测试时的机械特性。在航空器的制造中,必须考虑极端的环境因素,如高温和高水平的湿度,因为航天器可能经历数小时高温同时湿度水平是未知的。因此,通常评估用于航空航天应用的复合材料在热和湿条件下的使用。
3.就预浸料而言,要考虑的预浸料的一个特性是其“外置寿命(out-life)”或“贮存寿命”,其是指未固化的预浸料可在室温(20℃-25℃)下储存并且仍然可以保持足够的粘性和悬垂性(或柔性)以允许由此种预浸料制造具有可接受品质的复合零件的时间长度。未固化预浸料的“粘性”是未固化预浸料粘附到自身以及粘附到模具表面的能力的量度,并且是铺放和模制操作期间的重要因素,在这些操作中,铺放多个预浸料层片以形成层压体,随后将该层压体固化以形成复合零件。
4.典型地,由可热固化预浸料制造固化的复合结构是相当长的过程。预浸料叠层的固化通常占花费的总时间的绝大部分。大部分用于制造大型航空航天结构的预浸料典型地在高压釜中固化,高压釜是大型加压烘箱。在这种情况下,固化周期通常以从环境温度升至所需固化温度的温度斜坡开始。升温速率典型地为0.5℃/min至2℃/min,并且最终固化温度通常为约180℃或更高。在最终固化温度下的停留时间(或保持时间)通常为约2至3小时,然后接着是冷却步骤以将固化的材料以2℃/min至3℃/min的速率冷却至室温。因此,固化周期的总持续时间典型地在7至12小时的范围内。为了实现高度固化和希望的热机械特性,需要缓慢升温至最终固化温度并在高温下长时间停留。
5.当需要大型工具或当固化厚的复合结构时,由于可能出现不受控制的放热或整个复合零件厚度的固化度不均匀,不一定可以实现或希望更高的升温速率。进行了各种尝试来配制环氧基预浸料,这些环氧基预浸料可以在低于180℃温度下在高温釜中固化并且其中停留时间小于2小时。
6.为了降低固化温度或减少固化周期的持续时间,通常将预反应的环氧树脂、催化剂、共固化剂或其组合与主要的胺固化剂组合。预反应的环氧树脂或催化剂或共固化剂的存在可能对预浸料在环境条件下的处理和加工能力(如粘性、悬垂性、储存时间和外置寿命)产生不希望的影响。可替代地,过去已经使用了反应性很强的芳香族固化剂,如4,4
’‑
亚甲基二苯胺,但是现在它们被一些政府机构归类为致癌物和/或诱变剂,并且因此不希望用于未来应用。已经发现可以在低于180℃的温度下固化小于2小时的经催化的环氧树脂组合物产生以下固化的材料:其通常特征为低于150℃的热/湿tg,并且与通过标准的180℃/2小时固化周期固化的固化的环氧基材料相比,具有吸收更多水分的倾向,导致热/湿机械性能
显著降低。热/湿tg是指固化的复合材料的玻璃化转变温度,该固化的复合材料先前已经在高相对湿度(例如85%-95%)和高温(例如70℃-90℃)下经受长时间调节直至样品达到饱和。这样的热/湿tg可以通过en 6032确定。当高反应性的经催化的环氧树脂组合物用于制造厚的复合结构时,它们还具有产生局部不受控制的放热的倾向。不受控制的放热使得制造过程不安全或导致复合结构从固化的零件的顶部到中心部分具有不均匀的固化度。可以使用在100℃-140℃的温度下可变持续时间的中间停留(例如0.5至2小时)来减轻此类问题,但是这会进一步延长固化周期的持续时间并且违背了向树脂组合物中添加催化剂的目的。
7.本文披露了一种解决以上提及的问题的解决方案,这些问题涉及用于加工热固性预浸料的固化周期和由此类预浸料产生的固化的复合零件的热/湿性能。此种解决方案包括提供一种用于生产复合材料、特别是纤维增强的预浸料的热固性树脂组合物,该热固性树脂组合物包含不同环氧树脂的组合、作为主要的胺固化剂的邻甲基取代的芳香族二胺、一种或多种热塑性组分以及任选地一些填料。“主要的”胺固化剂意指这种胺构成热固性树脂组合物中所有胺固化剂的总摩尔量的≥50%的胺摩尔含量。在一些实施例中,邻甲基取代的芳香族二胺是组合物中唯一的胺固化剂。
8.热固性树脂组合物中的环氧树脂优选是每分子具有两个或更多个环氧基团的多官能环氧树脂。
9.热固性树脂组合物的热塑性组分包括一种或多种选自热塑性聚合物和热塑性颗粒的增韧剂。在一些实施例中,树脂组合物中存在热塑性聚合物和热塑性颗粒的组合。
10.邻甲基取代的芳香族二胺(主要的胺)每分子含有两个伯氨基和处于每个氨基邻位的两个甲基取代基。优选的芳香族二胺是4,4'-亚甲基双(2,6-二甲苯胺),4,4'-亚甲基双(2,6-二甲基苯胺)的同义词,通过以下化学结构表示:
11.优选的芳香族二胺是熔点为116℃的结晶固体,该芳香族二胺在环境温度和湿度下是稳定的并且在预浸料制造过程期间(典型地在80℃至130℃的范围内的温度下进行)不会引起热固性树脂、特别是环氧树脂的任何明显改进。因此此种芳香族二胺的存在不会影响未固化预浸料的粘性、处理能力、贮存寿命和可成形性。此上下文中的术语“可成形性”是指材料贴合或悬垂在三维工具表面的能力。
12.4,4'-亚甲基双(2,6-二甲基苯胺)与4,4
′‑
亚甲基双(2,6-二乙基苯胺)或4,4
′‑
亚甲基双(2,6-二异丙基苯胺)的区别在于,由于空间、诱导和超共轭效应,与乙基或异丙基相比,处于伯胺邻位的甲基是更强的给电子和更少的空间阻碍部分。虽然烷基全部可以被认为是弱电子活化基团,但当它们处于胺基的邻位时,由于与伯胺非常接近的脂肪族基团的空间阻碍,烷基对芳香族二胺的碱度贡献不大。这种效应在大的乙基或2-异丙基的情况下(如在m-dea、m-mipa和m-dipa芳香族胺的情况下)更加明显。
13.此外,由于乙基和异丙基分别只有两个或一个氢原子附接到与芳香族环直接连接的α碳原子上,与具有三个氢原子的甲基相反,乙基或异丙基中的超共轭效应将小于甲基的情况,导致甲基比乙基或异丙基具有更大的给电子能力。所述效应决定了在邻位包含甲基的芳香族伯胺对环氧树脂具有更高的反应性,并且因此可以实现复合水平的更高的反应动力学。
14.最后,亚甲基二苯胺分子中2,6邻位取代基的存在大大降低了与分子的挥发性及其被操作者潜在吸入相关的安全和职业健康风险。因此,亚甲基二苯胺分子作为人类肝毒素和动物致癌物的倾向大幅降低,从而使得此种固化剂成为更适合在用于航空航天应用的树脂配制品和复合材料中使用的化合物。
15.在一些实施例中,4,4'-亚甲基双(2,6-二甲苯胺)与另一种芳香族胺或多种其他芳香族胺组合使用,前提是4,4'-亚甲基双(2,6-二甲苯胺)的摩尔含量为所有芳香族胺的总摩尔量的≥50%。可以组合使用的其他芳香族胺包括:3,3'-二氨基二苯砜(3,3
’‑
dds);4,4'-二氨基二苯砜(4,4
’‑
dds);1,4-双(4-氨基苯氧基)-2-苯基苯;1,3-双(3-氨基苯氧基)苯;4,4
’‑
(间亚苯基二异亚丙基)二苯胺;4,4
’‑
(对亚苯基二异亚丙基)二苯胺;2,2'-双(4-(4-氨基苯氧基)苯丙烷;4,4
’‑
双(3-氨基苯氧基)二苯砜;1,3-双(3-氨基苯氧基)苯;和4,4'-1,4-亚苯基双(1-甲基乙基茚)双苯胺。
16.添加相对少量的其他芳香族胺、特别是芳香族二胺可能影响某些增韧剂在未固化和固化状态下的环氧-胺树脂基质中的溶解度和与未固化和固化状态下的环氧-胺树脂基质的相容性。例如,如果使用热塑性聚合物(例如聚醚砜)来改善含有4,4'-亚甲基双(2,6-二甲苯胺)的环氧树脂基质的韧性,则添加相对少的更相容的芳香族胺(如4,4'或3,3'-二氨基二苯砜)可以有助于在固化后形成更均匀且相分离更少的共混物。在这种情况下,分散到环氧树脂中的分离的热塑性域的尺寸可能减小,并且可能可以实现更希望的形态(例如热塑性域小于5微米的微粒形态)。固化后,固化的聚合物基质或含有嵌入这种固化的聚合物基质中的增强纤维的复合零件通常可以表征为具有韧性/冲击特性、热-湿性能和耐侵蚀性溶剂的良好平衡。
17.在一些实施例中,本披露的热固性树脂组合物包含以下组分:(a)(i)双官能聚环氧化物和(ii)三官能聚环氧化物和/或四官能聚环氧化物的组合;(b)包含作为用于聚环氧化物的主要的胺固化剂的4,4'-亚甲基双(2,6-二甲苯胺)的固化剂组分;以及(c)增韧组分,其优选地包含热塑性聚合物和热塑性颗粒的组合,其中组分的相对量以重量百分比(wt%)计为:基于树脂组合物的总重量30-75wt%a,20-30wt%b,和5-40wt%c。对于组分b,4,4'-亚甲基双(2,6-二甲苯胺)可以是唯一的胺固化剂或者与一种或多种其他芳香族胺、优选芳香族二胺组合使用。当胺固化剂的组合用于组分b时,4,4'-亚甲基双(2,6-二甲苯胺)的摩尔含量为热固性树脂组合物中所有胺的总摩尔量的≥50%。
18.组分a和b的相对量使得环氧树脂与胺的摩尔比在0.9与1.1之间。此种热固性树脂组合物不含任何与多官能聚环氧化物反应的催化剂或促进剂。任选地,此种树脂组合物可以进一步包含无机填料,如基于树脂组合物的总重量0.1-10wt%的量的导电填料。
19.在优选实施例中,热固性树脂组合物不含任何与环氧树脂反应的催化剂或促进剂。此种催化剂或促进剂包括双脲,具有羧酸根配体的金属络合物,三氟化硼或其络合物,或任何共固化剂如叔胺、咪唑、卤化鏻以及与聚环氧化物的加合物。此类叔胺包括三(二甲基氨基-甲基)苯酚和苄基二甲胺。含有此类叔胺的环氧基树脂组合物缺乏储存稳定性,并且在大多数情况下,必须在添加这些共固化剂(作为促进剂)后24小时内使用,否则混合物在正常储存条件下开始固化。卤化鏻包括乙基三苯基碘化鏻。与聚环氧化物的加合物包括:(i)与4,4'-异亚丙基二苯酚(双酚a)的多缩水甘油醚的n-甲基-、n-(2-羟乙基)-、n-辛基-、n-苯基-和n-苄基哌嗪以及n-甲基高哌嗪加合物;以及(ii)与单环氧化物、聚环氧化物或酚醛/酚醛清漆树脂的咪唑加合物,例如与2,2-双-(4-羟基苯基)丙烷的缩水甘油聚醚的2-乙基-4-甲基咪唑加合物。这种催化剂/促进剂和共固化剂的存在可能对环境条件下未固化的预浸料的特性如粘性、悬垂性、储存时间和贮存寿命产生不希望的影响。
20.出于制造预浸料的目的,未固化的热固性树脂组合物的粘度在80℃下可以在50-1500泊范围内,或是在120℃-170℃范围内的温度下为1-500泊。
21.可热固化的预浸料可以通过用本文披露的热固性树脂组合物浸渍增强纤维层来制造,其中树脂组合物构成基于预浸料的总体积以体积分数(%)计30%至80%、或30%至65%,优选40%至50%。
22.使用本披露的热固性树脂组合物制造的预浸料可以在160℃-180℃下固化15-120min以产生固化的复合材料,该固化的复合材料具有大于85%的固化度以及如通过en 6032确定的在干燥条件下等于或高于180℃(更具体地,180℃-200℃)的玻璃化转变温度(tg)和在热/湿条件下(在70℃/85%湿度下调节2周后)等于或高于150℃(更具体地,150℃-160℃)的玻璃化转变温度(tg)。在一些实施例中,固化在160℃-170℃下进行15-60min。
23.热固性树脂组合物或预浸料的固化度可以通过差示扫描量热法(dsc)来确定。热固性树脂组合物在固化期间经历不可逆的化学反应。当树脂体系中的组分固化时,树脂释放出热量,其由dsc仪器监测。可以使用固化热来确定树脂材料的固化百分比。例如,以下简单的计算可以提供固化百分比信息:固化%=[δh
未固化-δh
固化
]/[δh
未固化
]x 100%其中δh是由未固化或固化的样品产生的焓。
[0024]
包含用本披露的热固性树脂组合物浸渍的增强纤维的预浸料或预浸料叠层的合适的固化周期如下:以1℃/min从室温(20℃-25℃)升温至160℃,在160℃下停留60min,并且以3℃/min降温至60℃。树脂组合物的稳定性可以允许通过将支撑预浸料/预浸料叠层的模具预加热至最高达80℃-90℃的温度,之后以在0.5℃/min至2℃/min范围内的升温速率将温度升高至160℃-170℃来进一步减少固化周期持续时间。
[0025]
因此,固化周期的总持续时间可从7至12小时的工业标准减少至3-5小时,同时实现等效的热-机械性能。
[0026]
本披露的热固性树脂组合物的特征在于受控的反应性,并且当使用0.5℃/min至2℃/min的工业标准升温速率固化厚的复合零件(具有最高达56mm的厚度)时,不需要中间温度停留步骤(在100℃至140℃范围内的温度下保持30至60分钟)。
[0027]
由使用本披露的热固性树脂组合物得到的固化的复合材料的特征在于如通过en 2378确定的低吸水性(例如《1.5%)以及在热/湿条件下优异的热-机械特性。此类热-机械
特性是指如通过en 6035测量的填充孔拉伸强度、如通过en 6037测量的螺栓承载强度、以及如通过en 6038测量的冲击后压缩强度(cai)。
[0028]
如本文使用的术语“固化(cure)”和“固化(curing)”包括通过混合基础组分、在高温下加热、或暴露于紫外线和辐射而产生的聚合材料的聚合和/或交联。热固性树脂
[0029]
本披露的热固性树脂组合物是可硬化或可热固化的树脂组合物。在优选实施例中,可固化热固性树脂组合物含有多官能环氧树脂或聚环氧化物的组合。如本文使用的,术语“多官能的”环氧树脂或聚环氧化物是具有2或更大的官能度的树脂。在本披露中,术语“聚环氧化物”与“环氧树脂”可互换使用。优选的多官能树脂是双官能、三官能和四官能环氧树脂,尽管还可以使用具有更大官能度的环氧树脂,例如具有5或6个环氧基的那些。术语“多官能的”包括具有非整数官能度的树脂,例如环氧苯酚酚醛清漆(epn)树脂。
[0030]
合适的环氧树脂包括芳香族二胺、芳香族单伯胺、氨基苯酚、多元酚、多元醇、多元羧酸的多缩水甘油基衍生物。合适的环氧树脂的实例包括双酚如双酚a、双酚f、双酚c、双酚s和双酚k的多缩水甘油醚;和基于甲酚和苯酚的酚醛清漆的多缩水甘油醚。
[0031]
合适的双官能环氧树脂包括基于以下的那些:双酚f、双酚a(任选地溴化的)的二缩水甘油醚,苯酚和甲酚环氧酚醛清漆的缩水甘油醚,酚醛加合物的缩水甘油醚,脂肪族二醇的缩水甘油醚,二缩水甘油醚,二乙二醇二缩水甘油醚,芳香族环氧树脂,脂肪族多缩水甘油醚,环氧化烯烃,溴化树脂,芳香族缩水甘油胺,杂环缩水甘油酰亚胺(glycidyl imidine)和酰胺,缩水甘油醚,氟化环氧树脂或其任何组合。双官能的环氧树脂优选地选自双酚f的二缩水甘油醚(dgebf)、双酚a的二缩水甘油醚(dgeba)、二羟基萘的二缩水甘油醚或其任何组合。
[0032]
合适的三官能环氧树脂,通过举例,可以包括基于苯酚和甲酚环氧酚醛清漆的那些、酚醛加合物的缩水甘油醚、芳香族环氧树脂、脂肪族三缩水甘油醚、二脂肪族三缩水甘油醚、脂肪族多缩水甘油醚、环氧化烯烃、溴化树脂、三缩水甘油基氨基苯酚(包括三缩水甘油基对氨基苯酚(tgpam)和三缩水甘油基间氨基苯酚)、芳香族缩水甘油胺、杂环缩水甘油酰亚胺和酰胺、缩水甘油醚、氟化环氧树脂、羟基苯基甲烷的三缩水甘油基衍生物、或其任何组合。
[0033]
合适的四官能环氧树脂包括:四缩水甘油基二氨基二苯基甲烷(tgddm);四缩水甘油基-双(4-氨基苯基)-1,4-二异丙基苯;四缩水甘油基-双(4-氨基-3,5-二甲基苯基)-1,4-二异丙基苯、羟基苯基乙烷的四缩水甘油基衍生物和四缩水甘油基间二甲苯二胺。
[0034]
在优选实施例中,双官能环氧树脂与三官能环氧树脂和/或四官能环氧树脂组合使用。增韧剂
[0035]
用于热固性树脂组合物的合适的增韧剂(toughening agent或toughener)包括热塑性聚合物,其可以以颗粒的形式存在。如本文使用的,术语“颗粒”包含各种形状的微粒材料,包括但不限于球形和非球形颗粒。在一些实施例中,热塑性增韧颗粒包括在其固化期间基本上不溶于热固性树脂组合物的颗粒,并且在固化后在固化的材料中保持为离散颗粒。适合于本文目的不可溶的热塑性颗粒包括:脂肪族聚酰胺(pa)、环脂肪族聚酰胺,芳香族聚酰胺、聚邻苯二甲酰胺(ppa)、聚芳醚酮(paek)(如聚醚醚酮(peek)和聚醚酮酮(pekk))、聚
苯硫醚(pps)、聚酰胺酰亚胺、液晶聚合物(lcp)、聚酰亚胺、其共聚物及其衍生物。这些增韧颗粒不具有导电涂层如金属。
[0036]
已经发现不可溶的热塑性颗粒作为层间增韧剂对于避免热/湿性能的损失是有效的。因为这些热塑性颗粒在固化后仍保持不溶于聚合物基质,所以它们赋予固化的聚合物基质改善的韧性、损伤耐受性、热/湿性能、加工性、抗微开裂性和降低的溶剂敏感性。
[0037]
不可溶的热塑性颗粒可以与可溶的热塑性聚合物组合作为附加的增韧剂使用。这种可溶的热塑性聚合物可以选自:聚芳砜(例如聚醚砜(pes)、聚醚醚砜(pees)、pes-pees共聚物)、聚苯醚(ppo)、热塑性苯氧基树脂、聚砜、聚醚酰亚胺(pei)和聚酰亚胺(pi)。这些可溶的热塑性聚合物可以作为固体(例如粉末)添加到树脂组合物中,当在制备组合物期间或在浸渍增强纤维以形成预浸料期间加热组合物时,这些可溶的热塑性聚合物溶解到树脂组合物中。如本文使用的,“溶解”到树脂中意指与树脂形成均匀或连续的相。
[0038]
增韧剂还可以选自具有能够在固化期间与多官能环氧树脂反应的官能团的弹性体聚合物。合适的官能团包括但不限于-cooh、-nh、-nh2、oh、-sh、-conh
2-、-conh-、-nhconh-、-nco、-ncs、以及环氧乙烷基或缩水甘油基。示例性的弹性体包括但不限于天然橡胶、苯乙烯-丁二烯橡胶、聚异戊二烯、聚异丁烯、聚丁二烯、异戊二烯丁二烯共聚物、氯丁橡胶、腈橡胶、丁二烯-丙烯腈共聚物、丁基橡胶、丁腈橡胶、聚硫化物弹性体、丙烯酸弹性体、丙烯腈弹性体、硅酮橡胶、聚硅氧烷、聚酯橡胶、二异氰酸酯连接的缩合弹性体、epdm(乙烯-丙烯二烯橡胶)、氯磺化聚乙烯、氟化烃、聚丙烯酸丁酯-甲基丙烯酸甲酯(mam)共聚物、热塑性弹性体如苯乙烯和丁二烯或异戊二烯的(ab)和(aba)型嵌段共聚物、以及聚氨酯或聚酯的(ab)n型多链段嵌段共聚物等。
[0039]
在优选实施例中,聚芳砜、例如聚醚砜(pes)用作增韧剂。在另一个优选实施例中,不可溶的聚酰胺颗粒和可溶的聚芳砜(例如pes)的组合用作热固性树脂组合物中的增韧剂。
[0040]
增韧组分可以以基于热固性树脂组合物的总重量5-40wt%、包括5-23wt%的范围内的量存在。其他添加剂
[0041]
任选地,本披露的热固性树脂组合物还含有一种或多种选自以下的添加剂:流变控制剂、增粘剂、无机或有机填料、稳定剂、抑制剂、颜料、染料、阻燃剂、反应性稀释剂、导电填料以及其他本领域技术人员所熟知的用于在固化之前或之后改性树脂特性的添加剂。
[0042]
当存在时,无机或有机填料构成基于树脂组合物的总重量的约0.1-10wt%。在一些实施例中,将导电填料添加到热固性树脂组合物中。通常,导电填料可以具有任何合适的三维形状,包括例如球形、椭圆形、球状、盘状、树枝状、棒状、圆盘、长方体或多面体。
[0043]
适合于热固性树脂组合物的导电填料包括但不限于碳纳米材料,如碳纳米管(cnt)、碳纳米纤维、碳纳米针、碳纳米片、碳纳米棒,炭黑,石墨纳米板或纳米点,石墨烯,具有或不具有部分或全部金属涂层的石墨或其组合,或其他富勒烯材料,及其组合。如本文使用的,术语“碳纳米材料”是指具有至少一个尺寸小于约0.1微米(《100纳米)并且全部或大部分由在分子尺度上以五边形或六边形或两者排列的碳原子构成的材料。增强纤维
[0044]
为了制造高性能复合材料和预浸料,合适的增强纤维具有如根据astm c1557-14
测量的优选大于500ksi(或3447mpa)的高拉伸强度。可用于此目的的纤维包括碳纤维或石墨纤维,玻璃纤维,以及由碳化硅、氧化铝、硼、石英等形成的纤维,以及由有机聚合物(例如像聚烯烃、聚(苯并噻唑)、聚(苯并咪唑)、聚芳酯、聚(苯并噁唑)、芳香族聚酰胺、聚芳醚等)形成的纤维,并且可以包括具有两种或更多种此类纤维的混合物。优选地,纤维选自玻璃纤维、碳纤维、和芳香族聚酰胺纤维,如由杜邦公司(dupont company)以商品名kevlar销售的纤维。增强纤维可以以不连续纤维的形式、作为连续的单向或多向纤维、或作为织造织物、非卷曲织物、或非织造织物使用。织造形式可以选自平纹、缎纹或斜纹编织类型。非卷曲织物可以具有多个层片和纤维取向。
[0045]
增强纤维可以呈连续束(每个束由多根长丝构成)、单向或多向纤维、单向纤维的带、或非织造或织造织物的形式。在优选实施例中,用于预浸料的增强纤维是单向碳纤维。术语“单向”是指平行的、间隔的纤维的单向位置,即以相同的方向取向。预浸料和复合结构的制造
[0046]
如本文使用的,术语“预浸料”是指已经用可固化树脂组合物浸渍的增强纤维片或层。预浸料可以是完全浸渍的预浸料或部分浸渍的预浸料。如本文使用的,术语“浸渍的”是指已经经受浸渍过程的纤维,由此这些纤维部分地被树脂包围或完全嵌入树脂主体(也称为“基质树脂”)中。
[0047]
一般而言,可以通过将可固化树脂加热至其熔融状态并将所述熔融的可固化树脂引到干纤维层上并引入干纤维层中来用可固化树脂浸渍干纤维层。典型的浸渍方法包括:(1)将这些增强纤维连续地移动通过溶剂化树脂组合物的浴以完全或基本上浸湿这些纤维;接着是施加热以蒸发该溶剂;或者(2)在高温(热熔融技术)下将顶部树脂膜和/或底部树脂膜压靠在增强纤维层上。
[0048]
为了制造预浸料层片,首先通过将本披露的热固性树脂组合物涂覆到离型纸上制造树脂膜。接着,在热和压力的帮助下,将一个或两个这样的树脂膜层压到增强纤维层的一侧或两侧上以浸渍纤维,从而形成具有特定纤维面积重量(faw)和树脂含量的纤维增强的树脂层(或预浸料层片)。如果存在粒径大于纤维长丝之间的间距的增韧颗粒,则这些增韧颗粒在层压过程期间被过滤出并且保持在纤维层的外部。
[0049]
为了形成复合结构,可以将多个预浸料层片以堆叠顺序铺放在工具上以形成“预浸料叠层”。叠层内的预浸料层片可以相对于彼此在选定的取向,例如0
°
、
±
45
°
、90
°
等上定位。预浸料叠层可以通过以下技术制造,这些技术可以包括但不限于手工铺放、自动带铺放(atl)、先进纤维放置(afp)、和长丝卷绕。然后根据本文披露的固化周期固化预浸料叠层。实例实例1
[0050]
根据下表1的环氧树脂配制品(1a-1i)通过以下方式制备:在70℃下预共混环氧组分,然后添加聚醚砜(pes)以形成混合物,然后在115℃下加热该混合物直至实现pes的完全溶解。然后将混合物冷却至80℃,添加聚酰胺颗粒并且然后添加胺固化剂并混合,直至获得均质组合物。表1
[0051]
dgebpf是基于双酚f的环氧树脂。tgddm是四缩水甘油基二氨基-二苯基甲烷环氧树脂。tgpap是三缩水甘油基对氨基苯酚环氧树脂。dgebpa是基于双酚a的环氧树脂。4,4
’‑
dds是4,4
’‑
二氨基二苯砜。聚酰胺颗粒具有约250℃的熔点(如通过dsc确定的)。
[0052]
然后将每种所得配制品浇铸到钢模具中并在烘箱中根据表2中所述的固化周期之一固化以形成树脂块。表2固化周期123从25℃至停留温度的升温速率[℃/min]112停留温度[℃]160170180停留时间[min]6030120从停留温度至25℃的降温速率[℃/min]333
[0053]
然后从每个固化的树脂块中取出大约2mm厚的测试样,并且根据en 6032在1hz频率下在玻璃化转变事件开始之前和之后从储存模量曲线上的点绘制的外推切线的交点处测量固化的树脂块的起始tg。根据en 2823,将湿试样在70℃和85%湿度的气候静态室中预调节至饱和并且然后通过动态力学分析(dma)进行测试。固化的树脂的固化程度(eoc)通过示扫描量热法(dsc)测量并且计算为分别以j/g计的固化树脂与未固化树脂的反应热之间的比率并且以百分数表示。dsc在-50℃至350℃的温度范围内以10℃/min进行。固化的树脂的tg和eoc数据报告在表3中。表3
[0054]
如表2和表3所示,在树脂1a至1h中使用4,4'-亚甲基双(2,6-二甲苯胺)作为单一组分固化剂,这些树脂在160℃-170℃下固化30-60分钟,在干燥或h/w两种条件下的tg值等于或优于树脂1i的tg,后者含有更常规的4,4
’‑
dds并且在180℃(更高的温度)下固化2小时(更长的停留时间)。
[0055]
当树脂1i在160℃-170℃下固化30-60分钟时,测得的tg比用4,4'-亚甲基双(2,6-二甲苯胺)固化的树脂1a至1h低大约25℃-35℃。此外,只有使用4,4
’‑
dds才能实现71%-76%范围内的固化度,而所有被评估的衍生自含4,4'-亚甲基双(2,6-二甲苯胺)作为固化剂的组合物的固化的树脂均实现了85%-91%范围内的转化度。实例2
[0056]
将表1的树脂配制品1a浇铸到离型纸上以形成树脂膜。将两张这样的树脂膜用于浸渍单向碳纤维层(来自帝人公司(teijin)的ims65e23-24k-830tex),以产生具有268gsm纤维面积重量(faw)和34%树脂含量的单向(ud)预浸料。
[0057]
使用该ud预浸料制造测试面板。每个测试面板是预浸料层片的层压体。根据en 2565制造测试面板并根据实例1表2中所述的固化周期1在高压釜中固化。在固化的面板上进行热-机械测试,并将结果报告在表4中。表4
[0058]
在表4中,ar代表“按原样”,而rt代表室温(约25℃)。70℃/湿代表在相对高的温度(70℃)和高湿度水平(85%)下以使测试样实现饱和的调节工艺。
[0059]gic
是i型层间断裂韧性的测量值,其是根据en 6033确定的。ilss是根据en 2563测量的表观层间剪切强度。csai是在30焦耳冲击后并根据en 6038测量的冲击后压缩强度。fht是如通过en 6035测量的缺口拉伸强度。bbs是通过en 6037测量的螺栓承载强度。tg是固化的测试面板的玻璃化转变温度并且是通过dma并根据en 6032确定的。测试面板的固化程度(eoc)通过dsc测量并且计算为分别以j/g计的固化的测试面板与未固化的预浸料的反应热之间的比率并且以百分数表示。使用以10℃/min的升温速率从-50℃至350℃的温度斜坡实验来测量反应热。
[0060]
如表4所示,当在160℃下固化1小时时,固化的面板达到大于90%的固化度和155℃的热/湿(h/w)tg。固化的面板还展现出546j/m2的高抗分层性和215mpa的损伤容限。此外,在暴露于70℃和85%湿度的条件下两周之后未观察到csai或fht的降低。暴露于这样的h/w条件后还观察到bbs和ilss的相对较低的减少。实例3
[0061]
将表1的树脂配制品1h沉积在硅酮离型纸上以形成膜。将所得树脂膜用于在预浸料生产线上浸渍单向碳纤维层(sglc t50 4.4/255e100),产生在35%树脂含量下具有190g/m2的标称纤维面积重量的预浸料。
[0062]
使用该预浸料制造测试面板。每个测试面板是预浸料层片的层压体。根据en 2565制造测试面板并根据实例1表2中所述的固化周期1在高压釜中固化。在固化的面板上进行热-机械测试,并将结果报告在表4中。
表4表4
实例4-放热
[0063]
实例3中所述的预浸料的放热通过由该预浸料制造两个标称厚度分别为30mm(面板4.1)和56mm(面板4.2)的层压体并在高压釜中固化它们来评估。将热电偶放置在每个层压体的中心(tc2),而第二个放置在相同的位置,但在两个顶层之间(tc1)。根据实例1表2中披露的固化周期1来固化每个预浸料层压体。评估结果报告于表5中。表5
[0064]
在30mm厚的面板(面板4.1)的情况下,在层压体的中间层片的中心处(tc2)登记的最高温度为166℃,而通过在顶部两个片层之间(tc1)的热电偶测量的最高温度为162.4℃。因此,在固化周期期间测量的最大差值小于4℃。获得了从固化的层压体的外部至中心部分的标准偏差小于1%的88%的平均固化度。
[0065]
同样,在56mm厚的面板(面板4.2)的情况下,通过tc2登记的最高温度为168.4℃,与通过tc1读到的最高温度相比最大差值仅为7.7℃。获得了从固化的层压体的外部至中心部分的标准偏差小于1%的89%的平均固化度。
[0066]
本文所述的实验证明,当在基质树脂中使用胺固化剂4,4'-亚甲基双(2,6-二甲苯胺)时,可以制造厚度最高达56mm的厚复合结构,而不需要在固化周期期间漫长的中间停留时间,并且可以防止出现不受控的放热。受控的固化导致在层压体的整个厚度上非常均匀的固化度,并且因此导致均匀的热-机械性能。