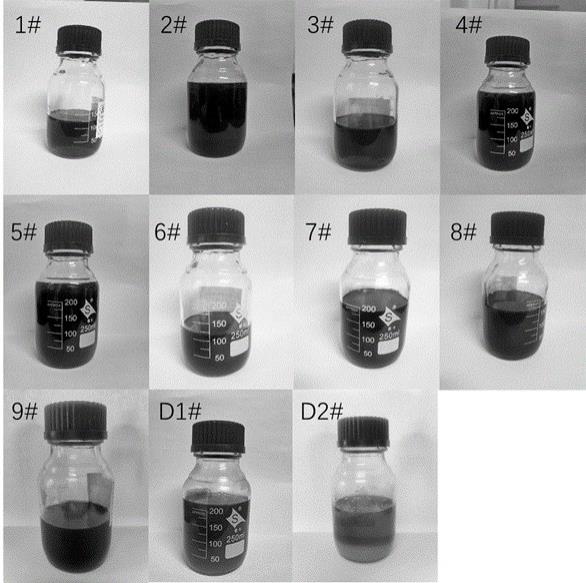
1.本技术涉及一种咪唑啉型缓蚀剂及其制备方法与应用,属于石油化工技术领域,具体属于缓蚀剂技术领域。
背景技术:2.我国油田大部分已进入注水开发阶段,注水主要来源于油田采出液分离出来的伴生水,而油田采出水成分复杂,矿化度高,细菌、微生物含量大,且溶解有co2、h2s、o2等腐蚀性气体,极易对水处理设备、注水井套管和注水泵及输水管线造成腐蚀,甚至造成输水管线的穿孔,导致油田污水的泄露,不但影响了油田的正常生产,而且还会给环境带来危害。
3.腐蚀所造成的危害不仅使金属材料本身在外形色泽及机械性能等方面受到破坏,更主要的是使其制品的质量等级下降以致报废,因腐蚀而造成的损失是惊人的,每年因腐蚀报废的钢材设备约相当于每年产品的30%,其中10%不可回炉再生。在油气田注水开发中,从油水井地下管柱到地面管道和储罐以及各种工艺设备都会遭到腐蚀,严重影响注水开发效果,造成巨大的经济损失。为了减缓油田采出水对水处理设备、注水设备及管线造成腐蚀,目前油田采取的通用做法是在采出水中添加污水缓蚀剂。
4.缓蚀剂是一种以适当的浓度和形式存在于环境(介质)中,可以防止或减缓腐蚀的化学物质或几种化学物质的混合物。它具有成本低、操作简单、见效快、能保护整体设备、适合长期保护等特点,因此,添加缓蚀剂是一种效果显著的防腐措施,是该领域国内外学者研究得最多的防腐措施。国内外的油田现场应用表明,加注缓蚀剂能大大提高油田设备的使用寿命。然而目前的缓蚀剂的缓蚀效率不高,不能高效的减缓污水对管道或设备等的腐蚀。
技术实现要素:5.为了解决上述问题,提供了一种缓蚀率高的污水缓蚀剂,该缓蚀剂由咪唑啉中间体和丙烯腈反应得到,能够广泛应用于油田采油、集输及工业存储、输水等领域,对上述领域所使用的管道及设备进行保护,可有效减缓污水对管道、管壁和设备等的腐蚀。
6.根据本技术的一个方面,提供了一种咪唑啉型缓蚀剂,所述缓蚀剂的结构式如下所示:式(1);或
式(2);其中r1独立选自包含2-10个碳原子的直链烷基、直链烷基衍生物、支链烷基或支链烷基衍生物中的任意一种,r2独立选自包含2-10个碳原子的直链或支链烷基;r3独立选自包含8-25个碳原子的直链或支链烷基。
7.上述直链烷基衍生物是指直链烷基中至少一个氢原子被其他原子取代,支链烷基衍生物是指支链烷基中至少一个氢原子被其他原子取代,上述其他原子可以是卤素原子、氧原子或氮原子中的至少一种。
8.可选地,所述r1独立选自
ꢀ‑
(ch2ch
2-nh)
n-ch2ch
2-中的任意一种,n为0-4之间的任意整数,所述r2独立选自
ꢀ‑ꢀ
(ch2ch2)
m-中的任意一种,m为1-5之间的任意整数;所述r3独立选自包含15-24个碳原子的直链或支链烷基。
9.可选地,所述缓蚀剂的结构式如式(1)所示,所述r1独立选自
ꢀ‑
(ch2ch
2-nh)
n-ch2ch
2-中的任意一种,n为0-2之间的任意整数;所述r3独立选自包含18-22个碳原子的直链或支链烷基。
10.可选地,所述缓蚀剂的结构式如式(1)所示,所述r1独立选自-ch2ch
2-。
11.根据本技术的另一个方面,提供了上述任一项所述的咪唑啉型缓蚀剂的制备方法,该方法包括下述步骤:(1)有机酸和有机胺经过酰化和环化反应形成咪唑啉中间体;(2)所述咪唑啉中间体与丙烯腈反应得到所述缓蚀剂;其中所述有机酸选自葵酸、月桂酸、肉豆蔻酸、棕榈酸、油酸、芥酸或妥尔油酸中的至少一种,所述有机胺选自二乙烯三胺、三乙烯四胺、四乙烯五胺、五乙烯六胺、六乙烯七胺或羟乙基乙二胺中的至少一种。
12.优选的,所述有机酸选自油酸、芥酸或妥尔油酸中的至少一种,更优选为芥酸,芥酸中含有的碳碳双键能够产生共轭效应,进一步增加缓蚀剂对金属的吸附性,提高缓蚀剂的有效覆盖率,进而提高缓蚀效果。
13.优选的,所述有机胺选自二乙烯三胺。
14.可选地,步骤(1)中,有机酸和有机胺的摩尔比为1:(1-1.2)。
15.可选地,步骤(1)中,将有机酸加入至反应釜内,向所述反应釜内滴加有机胺,在90-105℃下反应1-2h,之后升温至140-230℃脱水4.5-7h,即得所述咪唑啉中间体;优选的,所述脱水分为三个阶段:一段脱水:在140-160℃下脱水2-3h;二段脱水:在200-220℃下脱水2-3h;三段脱水:在230℃和氮气氛围下,脱水至少0.5h。
16.优选的,所述步骤(1)中,将有机酸加入到反应釜内升温至40~50℃,通过滴加罐滴加有机胺,滴加过程会有放热,控制温度不超过105℃,滴加完成后控制温度在90~105℃内
保温反应1~2h,然后缓慢升温脱水,在140~160℃下脱水2~3h,然后升温在200~220℃下脱水2~3h,最后升温至230℃氮气吹扫0.5h,形成所述咪唑啉中间体。
17.可选地,步骤(2)中,所述咪唑啉中间体与丙烯腈的摩尔比为1:(1.1-2.2)。
18.可选地,步骤(2)中,将所述咪唑啉中间体加入至反应釜内,向所述反应釜滴加丙烯腈,在70-80℃下反应4-6h得到所述缓蚀剂。
19.优选的,步骤(2)中,将步骤(1)形成的咪唑啉中间体投加至反应釜内,升温至50~60℃,在此温度下缓慢滴加丙烯腈,滴加完毕后升温至70~80℃保温反应4-6h,制得所述缓蚀剂。
20.根据本技术的另一个方面,提供了一种上述任一项所述的咪唑啉型缓蚀剂,或者上述任一项所述的咪唑啉型缓蚀剂的制备方法制得的咪唑啉型缓蚀剂在油田开采中的应用。
21.本技术的有益效果包括但不限于:1.根据本技术的咪唑啉型缓蚀剂,n原子上的孤对电子及咪唑啉环的π电子,能与金属表面的fe原子的空d轨道形成电子给受体,使咪唑啉分子能紧密地吸附在金属表面,所用的有机酸具有较长的分子链,使得分子链形成π键,使其更紧密地吸附与金属表面,上述两种吸附作用提高缓蚀剂在金属表面排列的致密度,使得该缓蚀剂在相同浓度下缓蚀率更高。
22.2.根据本技术的咪唑啉型缓蚀剂,疏水基团远离并接近垂直于金属表面排列,形成吸附层保护膜,缓蚀剂中的咪唑啉结构中疏水基团链较长、基团大,对应覆盖面积也就大,从而能够抑制阴极反应的发生,使得缓蚀剂的缓蚀性能越好。
23.3.根据本技术的咪唑啉型缓蚀剂,丙烯腈与咪唑啉中间体发生加成反应,引入的丙烯腈基团能够提高缓蚀剂的水溶性,并且丙烯腈加入后引入了强极性的氰基,能够增加缓蚀剂在金属表面的吸附点位,使得疏水链段在金属表面均匀排布,阻止污水与金属的接触,进而促进缓蚀剂的缓蚀性能。
24.4.根据本技术的咪唑啉型缓蚀剂,长链侧基能够形成疏水缔合,不仅能够增加疏水集团的疏水性,还能够增加缓蚀剂的耐酸性、耐碱性和耐温性,从而提高该缓蚀剂的环境适应力,可将其用于各种场所下管道或设备等的防腐。
25.5.根据本技术的咪唑啉型缓蚀剂的制备方法,操作步骤简单,原料易得,所使用的原料毒性小,易于工业化生产,并且制备的缓蚀剂分子链具有较多侧链,具有较高的缓蚀率。
26.6.根据本技术的咪唑啉型缓蚀剂的制备方法,制备得到的缓蚀剂广泛用于油田采油、集输及工业存储、输水等领域,在保护金属资源、减少生产事故和产品损失、减少因腐蚀造成的资源浪费和环境污染等方面将体现出重要作用。
附图说明
27.此处所说明的附图用来提供对本技术的进一步理解,构成本技术的一部分,本技术的示意性实施例及其说明用于解释本技术,并不构成对本技术的不当限定。在附图中:图1为本技术涉及的实施例和对比例合成的各个缓蚀剂的产品示意图;图2为本技术涉及的缓蚀实验测试后各个实验钢片的直观图。
具体实施方式
28.下面结合实施例详述本技术,但本技术并不局限于这些实施例。
29.如无特别说明,本技术的实施例中的原料均通过商业途径购买。
30.本技术的实施例中分析方法如下:利用傅里叶变换红外光谱仪对缓蚀剂进行红外光谱分析,将所得的缓蚀剂在室温下,采用衰减全反射模式进行测试分析。
31.缓蚀率评价实验:针对东辛采油厂污水共进行缓蚀实验,测试所制得的缓蚀剂在同一温度、同一加药量、同一时间周期条件下的缓蚀性能。实验钢片为a3,钢片规格50mm
×
13mm
×
1.5mm,实验温度50℃,缓蚀剂加药量为30ppm,实验周期7d。测试各个实施例或对比例中缓蚀剂的缓蚀率。
32.实施例1(1)咪唑啉中间体的合成:将500kg的芥酸加入到反应釜内升温至40~50℃,通过滴加罐滴加155kg的二乙烯三胺,滴加过程会有放热,控制温度不超过105℃,滴加完成后控制温度在90~105℃内保温反应1.5h,然后缓慢升温脱水,在140~160℃下脱水2.5h,然后升温在200~220℃下脱水2.5h,最后升温至230℃氮气吹扫0.5h,形成咪唑啉中间体,反应方程式如下:;(2)缓蚀剂的合成:将650kg的咪唑啉中间体投加至反应釜内,升温至50~60℃,在此温度下缓慢滴加170kg的丙烯腈,滴加完毕后升温至70~80℃保温反应4.5h,即得咪唑啉型缓蚀剂,命名为缓蚀剂1#,产品形态参考图1中1#,反应方程式如下:
。
33.实施例2(1)咪唑啉中间体的合成:将500kg的芥酸加入到反应釜内升温至40~50℃,通过滴加罐滴加280kg的四乙烯五胺,滴加过程会有放热,控制温度不超过105℃,滴加完成后控制温度在90~105℃内保温反应1.5h,然后缓慢升温脱水,在140~160℃下脱水2.5h,然后升温在200~220℃下脱水2.5h,最后升温至230℃氮气吹扫0.5h,形成咪唑啉中间体,反应方程式如下:;(2)缓蚀剂的合成:将750kg的咪唑啉中间体投加至反应釜内,升温至50~60℃,在此温度下缓慢滴加160kg的丙烯腈,滴加完毕后升温至70~80℃保温反应5.5h,即得咪唑啉型缓蚀剂,命名为缓蚀剂2#,产品形态参考图1中2#,反应方程式如下:
。
34.实施例3(1)咪唑啉中间体的合成:将500kg的芥酸加入到反应釜内升温至40~50℃,通过滴加罐滴加165kg的羟乙基乙二胺,滴加过程会有放热,控制温度不超过105℃,滴加完成后控制温度在90~105℃内保温反应1.5h,然后缓慢升温脱水,在140~160℃下脱水2.5h,然后升温在200~220℃下脱水2.5h,最后升温至230℃氮气吹扫0.5h,形成咪唑啉中间体,反应方程式如下:;(2)缓蚀剂的合成:将650kg的咪唑啉中间体投加至反应釜内,升温至50~60℃,在此温度下缓慢滴加150kg的丙烯腈,滴加完毕后升温至70~80℃保温反应4h,即得咪唑啉型缓蚀剂,命名为缓蚀剂3#,产品形态参考图1中3#,反应方程式如下:
。
35.实施例4(1)咪唑啉中间体的合成:将500kg的芥酸加入到反应釜内升温至40~50℃,通过滴加罐滴加220kg的三乙烯四胺,滴加过程会有放热,控制温度不超过105℃,滴加完成后控制温度在90~105℃内保温反应1.5h,然后缓慢升温脱水,在140~160℃下脱水2.5h,然后升温在200~220℃下脱水2.5h,最后升温至230℃氮气吹扫0.5h,形成咪唑啉中间体,反应方程式如下:;(2)缓蚀剂的合成:将650kg的咪唑啉中间体投加至反应釜内,升温至50~60℃,在此温度下缓慢滴加155kg的丙烯腈,滴加完毕后升温至70~80℃保温反应5.5h,即得咪唑啉型缓蚀剂,命名为缓蚀剂4#,产品形态参考图1中4#,反应方程式如下:
。
36.实施例5(1)咪唑啉中间体的合成:将500kg的芥酸加入到反应釜内升温至40~50℃,通过滴加罐滴加360kg的五乙烯六胺,滴加过程会有放热,控制温度不超过105℃,滴加完成后控制温度在90~105℃内保温反应1.5h,然后缓慢升温脱水,在140~160℃下脱水2.5h,然后升温在200~220℃下脱水2.5h,最后升温至230℃氮气吹扫0.5h,形成咪唑啉中间体,反应方程式如下:;(2)缓蚀剂的合成:将750kg的咪唑啉中间体投加至反应釜内,升温至50~60℃,在此温度下缓慢滴加130kg的丙烯腈,滴加完毕后升温至70~80℃保温反应5.5h,即得咪唑啉型缓蚀剂,命名为缓蚀剂5#,产品形态参考图1中5#,反应方程式如下:
。
37.实施例6(1)咪唑啉中间体的合成:将500kg的芥酸加入到反应釜内升温至40~50℃,通过滴加罐滴加410kg的六乙烯七胺,滴加过程会有放热,控制温度不超过105℃,滴加完成后控制温度在90~105℃内保温反应1.5h,然后缓慢升温脱水,在140~160℃下脱水2.5h,然后升温在200~220℃下脱水2.5h,最后升温至230℃氮气吹扫0.5h,形成咪唑啉中间体,反应方程式如下:(2)缓蚀剂的合成:将750kg的咪唑啉中间体投加至反应釜内,升温至50~60℃,在此温度下缓慢滴加140kg的丙烯腈,滴加完毕后升温至70~80℃保温反应5.5h,即得咪唑啉型缓蚀剂,命名为缓蚀剂6#,产品形态参考图1中6#,反应方程式如下:
实施例7实施例7与实施例1的区别在于:芥酸和二乙烯三胺的重量比发生变化,步骤(1)中,将500kg的芥酸加入到反应釜内升温至40~50℃,通过滴加罐滴加90kg的二乙烯三胺,剩余步骤与实施例1相同,制得缓蚀剂7#,产品形态参考图1中7#。
38.实施例8实施例8与实施例1的区别在于:咪唑啉中间体与丙烯腈的重量比发生变化,步骤(1)与实施例1相同,步骤(2)中,将650kg的咪唑啉中间体投加至反应釜内,升温至50~60℃,在此温度下缓慢滴加70kg的丙烯腈,剩余步骤与实施例1相同,制得缓蚀剂8#,产品形态参考图1中8#。
39.实施例9实施例9与实施例1的区别在于:原料中的芥酸替换为油酸,步骤(1)中,将500kg的油酸加入到反应釜内升温至40~50℃,通过滴加罐滴加155kg的二乙烯三胺,剩余步骤与实施例1相同,制得缓蚀剂9#。
40.对比例1对比例1与实施例2的区别在于,步骤(2)中的丙烯腈替换为氯化苄,步骤(2)中,将750kg的咪唑啉中间体投加至反应釜内,升温至50~60℃,在此温度下缓慢滴加160kg的氯化苄,滴加完毕后升温至70~80℃保温反应5.5h,即得咪唑啉型缓蚀剂,命名为对比缓蚀剂d1#。
41.对比例2对比例2与实施例3的区别在于,对比例3仅合成了咪唑啉中间体,未进行步骤(2)的反应,其余步骤与实施例3相同,制得对比缓蚀剂d2#。
42.试验例1将上述实施例制得的缓蚀剂1#-9#及对比例制得的对比缓蚀剂d1#-d2#,进行缓蚀实验,实验用污水取自东辛采油厂,实验钢片为a3,钢片规格50mm
×
13mm
×
1.5mm,将实验钢片浸泡于污水中,设置实验温度为50℃,缓蚀剂的加药浓度为30ppm,实验周期7d,分别称重实验钢片在实验前和实验后的重量。每组实验设置三个平行实验,并且设置一空白实验,即
仅将实验钢片放置于污水中,不加任何缓蚀剂,计算空白实验中实验钢片在实验前和实验后的重量为
△
m0。
43.按照各个实验钢片在实验前和实验后的重量差
△
m与空白实验中的
△
m0进行计算得到缓蚀率,缓蚀率=[(
△
m0‑△
m)/
△
m0]
×
100%,例如缓蚀剂1#中
△
m为0.0033g,空白实验中
△
m0为0.0359,则缓蚀剂1#的缓蚀率为[(0.0359-0.0033)]/0.0359
×
100%=90.8%,其余缓蚀剂的测试结果见下表1,对于缓蚀剂1#-9#、对比缓蚀剂d1#-d2#和空白实验测试中,实验钢片在测试后的直观图参考图2。
[0044]
表1根据表1可知,实施例1-9提供的咪唑啉型缓蚀剂1#-9#,缓蚀率高,效果均显著好于对比例1-2制得的缓蚀剂d1#-d2#,表现出了显著的缓蚀性能。其中,缓蚀剂1#的缓蚀效果
最好,缓蚀率能够达到90.8%。
[0045]
试验例2将上述缓蚀剂1#进行耐酸和耐温性试验,实验用配置酸液,实验钢片为n-80,钢片规格50mm
×
10mm
×
3mm,将已称量的试片放入恒温的不同浓度的酸溶液中,设置实验温度为分别为90℃、140℃和180℃,90℃采用常压静态腐蚀试验装置测定,120 ℃以上腐蚀速率采用高温高压动态腐蚀试验装置测定,浸泡4h 后,取出试片,清洗、干燥处理后称量,计算失量,每组实验设置三个平行实验,计算平均腐蚀速率。计算不同温度下的缓蚀剂的平均腐蚀速率,计算结果见下表2。
[0046]
表2由表2可知,本技术合成的缓蚀剂在酸性和高温环境下,具有较好的缓蚀效果,对于酸性或高温环境,仍能持续发挥缓蚀作用,在油气开采中使用本技术的缓蚀剂能够对管道或设备长期起到保护作用,延长设备的使用时间,节约成本。
[0047]
以上所述,仅为本技术的实施例而已,本技术的保护范围并不受这些具体实施例的限制,而是由本技术的权利要求书来确定。对于本领域技术人员来说,本技术可以有各种更改和变化。凡在本技术的技术思想和原理之内所作的任何修改、等同替换、改进等,均应包含在本技术的保护范围之内。