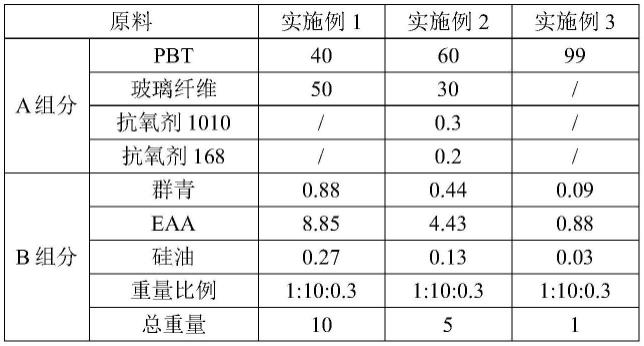
1.本发明属于塑料着色配色技术领域,具体涉及一种颜色均匀稳定可控的有色塑料复合材料及其制备方法和应用。
背景技术:2.工程塑料和特种工程塑料发展应用体现了多样化及高性能化,在航空航天,电动工具,通讯设施,电子元器件,运动工具和汽车部件等应用。作为结构件对力学性要求苛刻,而作为外观件,颜色设计呈现多样化,而且消费者对颜色外观的同一性要求越来越高。
3.目前工程塑料的着色方法主要有两种方式:1)一种为在注塑成型端(与色母粒混合着色,此种方式简单容易,也没有明显的环境污染,但其缺点是色母粒作为其他基材物质加入会影响工程复合材料的机械性能和尺寸稳定性,甚至影响外观,另外色母添加对颜色的均匀一致性比直接用着色料还是有一定差异,对颜色要求高的外观件难度大;2)另外一种为挤出造粒时进行配色着色,此种方式生产着色后在下游应用比较方便,而且颜色也比较稳定,下游加工材料的力学性能始终跟设计初期保持一致,所以目前作为工程塑料着色的主要方式。
4.但目前行业中挤出造粒着色方法绝大部分是直接用色粉与被着色材料进行预混合后直接投料挤出造粒,此种方法在生产过程中由于直接使用未被处理的色粉,在混合过程中不可避免地容易飘散到空气中,污染生产环境;而且色粉含量非常低,一般0.01~10wt%之间,直接与被着色料混合容易导致混合不均匀引起批次色差。
5.现有技术中虽然也对批次颜色稳定性的改进研究,例如中国专利 cn101759980a是先将色粉与碳酸钙混合制备得到色粉混合物,然后再与其他原料进行混合后加入到双螺杆挤出机中进行挤出造粒。虽然通过稀释方法能够避免在一些颜料色粉用量很少的场合提高颜色均匀性,但其操作方法还是稀释后的颜料包与被着色树脂共混混合,在实际混合过程中由于颗粒形态不一致,用量差别大等原因,在实际下料输送计量过程中物料产生分层离析作用,导致被着色材料在挤出生产过程中由于着色剂含量波动引起颜色波动的情况在所难免。另外加入的色粉混合物中加入了碳酸钙,在一定程度上会对材料的力学性能(如韧性)产生负面影响;且该方案仅改善了浅米色以及浅灰色等浅色产品的批次稳定性,并未公开对深色产品的稳定性的改善如何。
6.另外,有很多颜色在生产的过程中很难稳定生产,经常会发生同一挤出机中挤出前后色差的不一致,进而导致生产出的颜色与预定的颜色存在色差,无法准确生产出预定的颜色。
7.因此,需要开发一种颜色均匀稳定可控的有色塑料复合材料,且生产前后颜色一致,使生产出的有色塑料复合材料的颜色可控,同时力学性能保持较好。
技术实现要素:8.本发明的目的在于,克服现有技术中存在的色粉易飘散到空气中环境生产污染、混合不均匀引起批次色差以及色粉在生产过程中不稳定导致的无法准确生产出预定的颜色等问题,提供一种颜色均匀稳定可控的有色塑料复合材料。
9.本发明的另一目的在于,提供所述颜色均匀稳定可控的有色塑料复合材料的制备方法。
10.本发明的另一目的在于,提供所述颜色均匀稳定可控的有色塑料复合材料在制备航空航天材料、电子元器件或汽车零部件中的应用。
11.为实现上述目的,本发明采用如下技术方案:
12.一种颜色均匀稳定可控的有色塑料复合材料,包括按照如下重量份计算的组分:
13.a组分:
14.塑料树脂40~99份;
15.其它添加剂0~50份;
16.b组分:
17.颜料混合物1~10份;
18.其中,所述颜料混合物为颜料、粘结剂和协效剂按照重量比为1:(0.5~99):(0.1~5)复配得到的混合物;所述粘结剂的熔点为55~125℃;所述协效剂为矿物油或硅油中的一种或几种的组合;
19.且,a组分的原料和b组分的原料单独混合均匀后,再在熔融状态下进行共混、挤出。
20.本发明通过选用特定的粘结剂和协效剂,先与颜料在非熔融状态下进行共混,得到一种具有一定表面相互作用、同时还能够很好地进行分散的粉末状的颜料混合物(又可以称之为“色沙”);粘结剂会对颜料产生一定的吸附,减少颜料在空气中的飘散,而协效剂在混合颜料体系中具有一定的润湿作用,因此,在粘结剂和协效剂的协同作用下,包覆到颜料表面形成大小均一、分散稳定、且不团聚的混合料,可以提高颜料的耐热稳定性,使颜料在经过高温挤出后,色差基本保持不变,可以准确生产出预定的颜色;还可以与塑料树脂基体具有很好的相容性,能够帮助颜料稳定、均匀地分散到复合材料体系中,提升复合材料的力学性能。
21.现有市售的塑料树脂均可用于本发明中。所述塑料树脂包括但不限于聚乙烯(pe)、聚丙烯(pp)、聚碳酸酯(pc)、聚酰胺(pa)、聚对苯二甲酸丁二醇酯(pbt)、聚甲基丙烯酸甲酯(pmma)、聚苯硫醚(pps)、聚醚砜(pes)、聚醚醚酮(peek)、改性聚苯醚(ppo、mppo、mppe)或丙烯腈-丁二烯-苯乙烯共聚物(abs)中的一种或几种的组合。
22.现有市售的颜料也均可用于本发明中,所述颜料为有机颜料或无机颜料。
23.所述无机颜料包括但不限于硫化锌、炭黑、钒酸铋化合物、群青、硫化铈或云母珠光中的一种或几种的组合。
24.所述有机颜料包括但不限于喋啶类颜料、双偶氮类颜料、偶氮金属络合类颜料、酞青类颜料、杂环苝系颜料、喹吖啶酮类颜料、次甲基类染料、萘环酮类染料或蒽醌酮类染料中的一种或几种的组合。
25.优选地,颜料、粘结剂和协效剂的重量比为1:(1~20):(0.2~0.5);进一步优选为
1:10:6。
26.优选地,所述粘结剂在熔融状态下的粘度为60~8000cpa/s;进一步优选为 400~6000cps。
27.本发明中,粘度指的是动力粘度,动力粘度参照标准《din 53019-1-2008》所述的方法测试得到。
28.优选地,所述粘结剂为蒙旦蜡、聚乙烯蜡、氧化乙烯蜡、硬脂酸金属盐或乙烯-丙烯酸共聚物中的一种或几种的组合;进一步优选为乙烯-丙烯酸共聚物。
29.常规功能添加剂均可用于本发明中,所述功能添加剂包括但不限于增强填料、阻燃剂、抗氧剂、紫外光吸收剂、抗静电剂或抗菌剂、成核剂、抗静电剂、偶联剂、激光标识剂、消光剂、吸酸剂、抗水解剂、酯交换抑制剂、耐磨改性剂或金属效果颜料中的一种或几种的组合。
30.为了进一步提高颜料的分散均匀性,优选地,所述功能添加剂为颗粒状。
31.所述颜色均匀稳定可控的有色塑料复合材料的制备方法,包括如下步骤:
32.s1.将a组分的原料、b组分的原料分别单独混合均匀后得到混合物a和混合物b;
33.s2.将混合物a和混合物b分别从不同的加料口加入到挤出机中,经熔融共混挤出,即得所述颜色均匀稳定可控的有色塑料复合材料。
34.需要说明的是,所述功能添加剂的添加方式,可以添加在a组分中,也可以添加在b组分中,还可以以部分在b组中、部分在a组分中(a、b组分中的功能添加剂可以相同,也可以不同)的形式进行添加。
35.优选地,所述熔融共混挤出的温度高于塑料树脂的熔点或软化点20~80℃。
36.优选地,所述熔融共混挤出在双螺杆挤出机中进行,所述双螺杆挤出机的长径比为36~52:1,转速为300~900r/min。
37.上述颜色均匀稳定可控的有色塑料复合材料在制备航空航天材料、电子元器件或汽车零部件中的应用也在本发明的保护范围内。
38.与现有技术相比,本发明的有益效果是:
39.本发明通过选用特定的粘结剂、协效剂与颜料先在非熔融状态下进行共混 (a组分),然后再在熔融状态下与包含塑料树脂的b组分的原料共混、挤出,在本发明特定的原料搭配以及特定的制备工艺条件下,制备得到的有色塑料复合材料中的颜色分布均匀,且不同批次的产品以及挤出前后的产品的颜色的色差小,其中色差δe《0.5。
具体实施方式
40.以下结合具体实施例来进一步说明本发明,但实施例并不对本发明做任何形式的限定。除非特别说明,本发明采用的试剂、方法和设备为本技术领域常规试剂、方法和设备。除非特别说明,本发明所用试剂和材料均为市购。
41.本发明的实施例采用以下原料:
42.塑料树脂:
43.pc:11300 10np,购自韩国lg;
44.pa6:hy-2500a,购自沈阳化纤;
45.pbt:1200-211m,购自中国台湾长春;
46.pp:ep548r,购自中海壳牌;
47.abs:pa-757购自奇美;
48.颜料:
49.酞青蓝15:3:pv fast blue bg,购自科莱恩;
50.酞黄棕23:f2001,购自巴斯夫;
51.群青:ar,购自纽必莱;
52.钛白粉:2233,购自日本石原;
53.次甲基黄122:yellow g,购自拜耳;
54.溶剂红149:hfg,购自亚邦;
55.酞青绿7:pv fast green gnx,购自科莱恩;
56.粘结剂:
57.蒙旦蜡:glycolube-p,熔点为60-65℃,140℃下的动力粘度800cpa/s,购自lonza;
58.聚乙烯蜡:a-c6a,熔点为108℃,140℃下的动力粘度为400cpa/s,购自 honeywell;
59.硬脂酸镁:熔点为145℃,190℃下的动力粘度为90cpa/s,购自山东六佳药用辅料股份有限公司;
60.乙烯-丙烯酸共聚物(eaa):295a,熔点为99℃,190℃下的动力粘度为3600cpa/s,购自honeywell;
61.碳酸钙:熔点为1339℃,固体粉末,购自东莞梅立泰;
62.聚乙二醇peg-2000:熔点为52℃,140℃下的动力粘度为80cpa/s,购自江苏海安;
63.协效剂:
64.硅油:o-s04,购自广州汇硅;
65.矿物油:330760,购自西格玛奥德里奇(上海)贸易有限公司;
66.其它添加剂:
67.受阻酚类抗氧剂1010:市售;
68.亚磷酸酯类抗氧剂168:市售;
69.玻璃纤维:市售。
70.如未特别说明,本发明平行的实施例和对比例中的某一组分(例如受阻酚类抗氧剂1010、亚磷酸酯类抗氧剂168、玻璃纤维)均为相同的市售产品。
71.实施例1~24
72.本实施例提供一系列有色塑料复合材料,按照表1~4中的配方,按照包括如下步骤的制备方法制备得到:
73.s1.按表1~4中的比例,将a组分的原料、b组分的原料分别添加至高速混合机中混合5min,高速混合机的转速为800r/min,混合均匀后得到混合物a和混合物b;
74.s2.将s1.得到的混合物a和混合物b分别加入52d同向双螺杆挤出机的不同加料口中,在高于塑料树脂的熔点或软化点20~80℃的温度下、300~900rpm 转速下熔融共混挤出,然后在120℃下干燥4h得到,其中分别在挤出过程中的 15min、30min、45min和60min进行在线取样,便于后期性能测试。
75.表1实施例1~3的颜色均匀稳定可控的有色塑料复合材料中各组分含量(重量份)
[0076][0077]
表2实施例4~11的颜色均匀稳定可控的有色塑料复合材料中各组分含量(重量份)
[0078][0079][0080]
表3实施例12~18的颜色均匀稳定可控的有色塑料复合材料中各组分含量(重量份)
2000。
[0089]
对比例3
[0090]
本对比例与实施例2的不同之处在于,未添加粘结剂乙烯-丙烯酸共聚物。
[0091]
对比例4
[0092]
本对比例与实施例2的不同之处在于,未添加协效剂。
[0093]
对比例5
[0094]
本对比例与实施例2的不同之处在于,在制备过程中,将所有原料组分(包括a组分和b组分中所有原料)先在高速混合机中混合均匀,然后从同一个加料口中加入到双螺杆挤出机中在相同的条件下进行熔融共混挤出、烘干。
[0095]
性能测试
[0096]
对上述实施例和对比例制备得到的有色塑料复合材料注塑成色板,并对其性能进行测试,具体测试方法如下:
[0097]
1.同批次产品色差δe:取同批次60min的挤出产品注塑成10块色板,在标准光源灯箱条件(d65光源)下观察10块色板的色差,用分光光度计测试颜色色差,记录色差最大的两块色板的色差;
[0098]
2.挤出前后色差稳定性:分别取15min、30min、45min和60min四组的挤出样注塑成色板,每组样品注塑成5块样板,取5块样板的色值的平均值作为该组样品的色值,并与其它组的色值对比得到色差值,记录最大色差;
[0099]
3.颜色均匀性:取60min的挤出产品注塑成色板,在一块样板上按照五点取样法进行标记,测量5个样点之间每两个样点之间的色差,并记录最大色差;
[0100]
测试结果详见表5。
[0101]
表5性能测试结果
[0102][0103][0104]
从上述结果中可以看出:
[0105]
本发明特定的原料搭配以及特定的制备工艺条件下,制备得到的有色塑料复合材料中的颜色分布均匀,且不同批次的产品以及挤出前后的产品的颜色的色差小,其中色差
δe《0.5。
[0106]
实施例2、实施例4~7(表2)、对比例3的结果表明:合适占比的粘结剂添加量,能够得到颜色均匀稳定的复合材料。
[0107]
实施例2、实施例8~11(表2)、对比例4的结果表明:合适占比的协效剂添加量,能够得到颜色均匀稳定的复合材料。
[0108]
且,对比例3和4的结果表明,仅添加粘结剂或协效剂的材料的颜色稳定性显著变差,表明两种组分之间存在协同作用。
[0109]
实施例2、实施例12~14、对比例1和2的结果表明:粘结剂的种类对颜色稳定性的影响较大,其中对比例1选用了熔点较高的碳酸钙作为粘结剂,在熔融挤出过程中,碳酸钙对色粉在树脂基体中的分散效果较差,得到的复合材料的颜色稳定性较差;对比例2选用了熔点较低的聚乙二醇peg-2000作为分散剂,在还未进入到熔融挤出阶段,粘结剂就已经融化成液态或膏状,使色粉出现团聚结块现象,得到的复合材料的颜色稳定性同样很差。
[0110]
对比例5是选择常规的将所有原料混合后在熔融挤出,制备得到的材料的性能显著差于各实施例,表明本发明的在非熔融状态下进行混合对材料的颜色的稳定性有重要的作用。
[0111]
以上所述的具体实施方式,对本发明的目的、技术方案和有益效果进行了进一步详细说明,所应理解的是,以上所述仅为本发明的具体实施方式而已,并不用于限定本发明的保护范围,凡在本发明的精神和原则之内,所做的任何修改、等同替换、改进等,均应包含在本发明的保护范围之内。