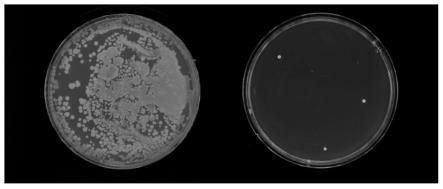
1.本发明属于薄膜材料技术领域,具体涉及一种抗菌阻燃的聚乙烯材料及其制备方法、一种抗菌阻燃聚乙烯薄膜及其制备方法。
背景技术:2.聚乙烯是目前世界上应用领域最广泛且产量最大的薄膜材料,其化学性质稳定,成型简单,无毒无味,价格低廉,且具有较好的加工性能和使用性能。聚乙烯薄膜广泛应用于运输包装、农膜、容器、医药、化工、电子、印刷等领域。然而聚乙烯材料本身不具备抗有害微生物及阻燃性能,阻碍了聚乙烯在有抗菌和阻燃需求的场合下的应用。
3.为了保障重大公共卫生安全,对包括病毒、细菌、真菌等有害微生物的消杀防护非常关键,阻止有害微生物以“物传人”的途径传播。另外,阻燃技术的研究和阻燃产品的开发已受到社会各个领域的重视,具有阻燃、抑烟性能的包装和容器材料是预防日常生活火灾的战略措施之一。
4.因此,随着科技发展和社会进步,长久的抗菌和阻燃性能已经成为包装和容器材料等领域亟需的性能。但是目前在国内市场具有抗菌抗病毒和阻燃抑烟功能的聚乙烯薄膜材料的性能仍然较差,不能满足日益增长的应用需求。
技术实现要素:5.有鉴于此,本发明提供了一种抗菌阻燃的聚乙烯材料及其制备方法、一种抗菌阻燃聚乙烯薄膜及其制备方法。本发明提供的抗菌阻燃的聚乙烯材料同时可具有优异的抗菌性能和阻燃性能。
6.为了解决上述技术问题,本发明提供了一种抗菌阻燃聚乙烯材料,包括以下质量份数的组分:聚乙烯75~90份、抗菌助剂0.1~10份、阻燃剂2~10份、纳米碳酸钙4~8份、抗氧剂0.2~1份和偶联剂1~4份;所述抗菌助剂为纳米铜氧化物-高分子复合材料,所述纳米铜氧化物-高分子复合材料中纳米铜氧化物吸附负载于高分子载体表面;所述阻燃剂为锡基阻燃剂。
7.优选的,所述纳米铜氧化物-高分子复合材料中的高分子载体包括聚四氟乙烯、尼龙66、聚氯乙烯、聚碳酸酯和聚苯硫醚中的一种或多种。
8.优选的,所述阻燃剂为无机锡基阻燃剂。
9.优选的,所述无机锡基阻燃剂为锡酸锌和/或羟基锡酸锌。
10.本发明提供了上述技术方案所述抗菌阻燃聚乙烯材料的制备方法,包括以下步骤:
11.将聚乙烯、抗菌助剂、阻燃剂、纳米碳酸钙、抗氧剂和偶联剂熔融共混挤出,得到所述抗菌阻燃聚乙烯材料。
12.优选的,所述熔融共混挤出在双螺杆挤出机中进行,所述双螺杆挤出机工作时由
加料口至挤出机头依次分布第1温度区域、第2温度区域、第3温度区域、第4温度区域、第5温度区域、第6温度区域、第7温度区域、第8温度区域、第9温度区域和第10温度区域,所述第1温度区域的温度为75~85℃,所述第2~6温度区域和第10温度区域的温度独立地为175~185℃,所述第7~9温度区域的温度独立地为165~175℃。
13.优选的,所述熔融共混挤出时,物料在所述双螺杆挤出机中的停留时间为3~5min,物料在所述双螺杆挤出机中的压力为10~15mpa。
14.本发明提供了一种抗菌阻燃聚乙烯薄膜,所述抗菌阻燃聚乙烯薄膜的成膜原料包括上述技术方案所述的抗菌阻燃聚乙烯材料或上述技术方案所述的制备方法制备获得的抗菌阻燃聚乙烯材料。
15.优选的,所述抗菌阻燃聚乙烯薄膜的成膜原料还包括聚乙烯母料,所述聚乙烯母料和抗菌阻燃聚乙烯材料的质量比为(0.1~10):1。
16.本发明提供了上述技术方案所述抗菌阻燃聚乙烯薄膜的制备方法,包括以下步骤:
17.将成膜原料熔融后制备成膜,获得所述抗菌阻燃聚乙烯薄膜,所述制备成膜包括吹塑成膜、注塑成膜、滚塑成膜或流延成膜。
18.本发明提供一种抗菌阻燃聚乙烯材料,包括以下质量份数的组分:聚乙烯75~90份、抗菌助剂0.1~10份、阻燃剂2~10份、纳米碳酸钙4~8份、抗氧剂0.2~1份和偶联剂1~4份;所述抗菌助剂为纳米铜氧化物-高分子复合材料,所述纳米铜氧化物-高分子复合材料中纳米铜氧化物吸附负载于高分子载体表面;所述阻燃剂为锡基阻燃剂。本发明提供的抗菌阻燃聚乙烯材料以纳米铜氧化物-高分子复合材料作为抗菌助剂,能够有效提高纳米铜氧化物在聚乙烯基材中的分散性,提高聚乙烯基材的抗菌、抗病毒性能;且无机锡基阻燃剂可与纳米铜氧化物-高分子复合材料抗菌剂起到协同增效抗菌的效果,配合纳米碳酸钙、抗氧剂和偶联剂,在上述质量份数的范围内实现了抗菌阻燃聚乙烯材料的制备,该材料具有优异的广谱高效的抗菌、抗病毒和阻燃、抑烟功能。
19.本发明提供上述技术方案所述抗菌阻燃聚乙烯材料的制备方法,包括以下步骤:将聚乙烯、抗菌助剂、阻燃剂、纳米碳酸钙、抗氧剂和偶联剂熔融共混挤出,获得所述抗菌阻燃聚乙烯材料。本发明提供的制备方法制备工艺简单,成本低、环境友好。
20.本发明提供一种抗菌阻燃聚乙烯薄膜,所述抗菌阻燃聚乙烯薄膜的成膜原料包括上述技术方案所述的抗菌阻燃聚乙烯材料或上述技术方案所述的制备方法制备得到的抗菌阻燃聚乙烯材料。本发明提供的抗菌阻燃聚乙烯薄膜具有优异的广谱高效的抗菌、抗病毒和阻燃、抑烟功能。由实施例1的结果表明,本发明提供的抗菌阻燃聚乙烯薄膜经过标准gb/t31402-2005《塑料表面抗菌性能试验方法》和标准gb/t4789.2-2016《食品安全国家标准食品微生物学检验菌落总数测定》测试,抗菌阻燃聚乙烯薄膜具有优异的抗菌效果:对大肠杆菌和金黄色葡萄球菌的杀菌率均达到了99.9%;参考《消毒技术规范》(2002年版)对抗菌阻燃聚乙烯薄膜进行了病毒灭活试验:对马动脉炎病毒(eva)的灭活效果达到了99.75%;且阻燃等级均达到了标准ul94的v0级别。
附图说明
21.图1为本发明实施例1制备的铜氧化物-高分子复合材料的x射线衍射(xrd)图谱;
22.图2为对实施例1制备获得的抗菌阻燃聚乙烯薄膜材料经标准gb/t4789.2-2016《食品安全国家标准食品微生物学检验菌落总数测定》的抗大肠杆菌效果照片,左图为空白对照组样品,右图为含抗菌剂的测试样品;
23.图3为实施例1制备获得的抗菌阻燃聚乙烯薄膜材料图片;
24.图4为实施例2制备得到的抗菌阻燃聚乙烯薄膜材料图片;
25.图5为实施例3制备得到的抗菌阻燃聚乙烯薄膜材料图片。
具体实施方式
26.本发明提供一种抗菌阻燃聚乙烯材料,包括以下质量份数的组分:聚乙烯75~90份、抗菌助剂0.1~10份、阻燃剂2~10份、纳米碳酸钙4~8份、抗氧剂0.2~1份和偶联剂1~4份;所述抗菌助剂为纳米铜氧化物-高分子复合材料,所述纳米铜氧化物-高分子复合材料中纳米铜氧化物吸附负载于高分子载体表面;所述阻燃剂为锡基阻燃剂。
27.在本发明中,如无特殊说明,所用原料均为本领域技术人员熟知的市售产品。
28.以质量份数计,本发明提供的抗菌阻燃聚乙烯材料包括聚乙烯75~90份,优选为75.5~87.5份,进一步优选为76~85份。
29.在本发明中,所述聚乙烯包括低密度聚乙烯和/或高密度聚乙烯。
30.在本发明中,所述低密度聚乙烯优选包括线型低密度聚乙烯。
31.以所述聚乙烯的质量份数为基准,本发明提供的抗菌阻燃聚乙烯材料包括抗菌助剂0.1~10份,优选为0.2~8份,进一步优选为0.25~6份。
32.在本发明中,所述抗菌助剂为纳米铜氧化物-高分子复合材料,所述纳米铜氧化物-高分子复合材料中纳米铜氧化物吸附负载于高分子载体表面。
33.在本发明中,所述纳米铜氧化物-高分子复合材料中的高分子载体优选包括聚四氟乙烯、尼龙66、聚氯乙烯、聚碳酸酯和聚苯硫醚中的一种或多种。
34.在本发明中,所述抗菌助剂为纳米铜氧化物-高分子复合材料中纳米铜氧化物和高分子载体的质量比优选为1:(5~10),更优选为1:(5.5~8),进一步优选为1:(6~7.8)。
35.在本发明中,所述纳米铜氧化物-高分子复合材料的制备方法优选包括以下步骤:
36.将有机铜盐、高分子材料载体和有机溶剂混合,得到混合物前驱体;
37.将所述混合物前驱体去除有机溶剂,得到干燥的混合物前驱体;
38.将所述干燥的混合物前驱体煅烧,得到所述纳米铜氧化物-高分子复合材料。
39.本发明将有机铜盐、高分子材料载体和有机溶剂混合,得到混合物前驱体。
40.在本发明中,所述有机铜盐具体优选为甲酸铜。
41.在本发明中,所述有机溶剂具体优选为乙醇。
42.在本发明中,所述高分子材料载体具体优选为聚四氟乙烯、尼龙66、聚氯乙烯、聚碳酸酯和聚苯硫醚中的一种或多种。
43.本发明对所述有机溶剂的用量没有特殊要求,能够将所述有机铜盐完全溶解即可。
44.在本发明中,所述有机铜盐和所述高分子材料载体的质量比优选为(2~4):1。
45.在本发明中,所述混合优选在搅拌的条件下进行。
46.在本发明中,所述搅拌具体优选为磁力搅拌。
47.本发明对所述搅拌的具体时间没有特殊要求,能够将上述原料混合均匀即可。
48.得到混合物前驱体后,本发明将所述混合物前驱体去除有机溶剂,得到干燥的混合物前驱体。
49.在本发明中,所述去除有机溶剂具体优选为鼓风干燥。
50.在本发明中,所述鼓风干燥的温度优选为80℃。
51.本发明对所述鼓风干燥的具体时间没有特殊要求,将所述有机溶剂完全去除即可。
52.得到干燥的混合物前驱体后,本发明将所述干燥的混合物前驱体煅烧,得到所述纳米铜氧化物-高分子复合材料。
53.在本发明中,所述煅烧的温度优选为200~280℃,更优选为220~250℃。
54.本发明通过使用纳米铜氧化物-高分子复合材料作为抗菌助剂,能够实现抗菌助剂铜氧化物在聚乙烯基材中的均匀分散,提高聚乙烯材料的抗菌性能。
55.以所述聚乙烯的质量份数为基准,本发明提供的抗菌阻燃聚乙烯材料包括阻燃剂2~10份,优选为2.2~9份,进一步优选为2.5~8.5份。
56.在本发明中,所述阻燃剂优选为无机锡基阻燃剂。
57.在本发明中,所述阻燃剂更优选包括锡酸锌和/或羟基锡酸锌。
58.以所述聚乙烯的质量份数为基准,本发明提供的抗菌阻燃聚乙烯材料包括纳米碳酸钙4~8份,优选为4.5~7.5份,进一步优选为5~7份。
59.在本发明中,所述纳米碳酸钙的粒径优选为30~200nm。
60.以所述聚乙烯的质量份数为基准,本发明提供的抗菌阻燃聚乙烯材料包括抗氧剂0.2~1份,优选为0.3~0.8份,进一步优选为0.35~0.7份。
61.在本发明中,所述抗氧剂优选包括抗氧剂1076、抗氧剂168和抗氧剂dltdp中的一种或多种。
62.以所述聚乙烯的质量份数为基准,本发明提供的抗菌阻燃聚乙烯材料包括偶联剂1~4份,优选为1.5~3.5份,进一步优选为1.8~3.2份。
63.在本发明中,所述偶联剂优选为硅烷偶联剂。
64.在本发明中,所述偶联剂更优选包括硅烷偶联剂kh-550、硅烷偶联剂kh-560和硅烷偶联剂kh-570中的一种或多种。
65.本发明提供了上述技术方案所述抗菌阻燃聚乙烯材料的制备方法,包括以下步骤:
66.将聚乙烯、抗菌助剂、阻燃剂、纳米碳酸钙、抗氧剂和偶联剂熔融共混挤出,得到所述抗菌阻燃聚乙烯材料。
67.在本发明中,所述熔融共混挤出优选在双螺杆挤出机中进行。
68.在本发明中,进行所述熔融共混挤出之前,本发明优选将聚乙烯、抗菌助剂、阻燃剂、纳米碳酸钙、抗氧剂和偶联剂混合。
69.在本发明中,所述聚乙烯、抗菌助剂、阻燃剂、纳米碳酸钙、抗氧剂和偶联剂混合时优选在高速混料机中进行。
70.在本发明中,所述双螺杆挤出机工作时由加料口至挤出机头依次分布第1温度区域、第2温度区域、第3温度区域、第4温度区域、第5温度区域、第6温度区域、第7温度区域、第
8温度区域、第9温度区域和第10温度区域。
71.在本发明中,所述第1温度区域的温度优选为75~85℃。
72.在本发明中,所述第2温度区域的温度优选为175~185℃。
73.在本发明中,所述第3温度区域的温度优选为175~185℃。
74.在本发明中,所述第4温度区域的温度优选为175~185℃。
75.在本发明中,所述第5温度区域的温度优选为175~185℃。
76.在本发明中,所述第6温度区域的温度优选为175~185℃。
77.在本发明中,所述第7温度区域的温度优选为165~175℃。
78.在本发明中,所述第8温度区域的温度优选为165~175℃。
79.在本发明中,所述第9温度区域的温度优选为165~175℃。
80.在本发明中,所述第10温度区域的温度优选为175~185℃。
81.在本发明中,所述熔融共混挤出时,物料在所述双螺杆挤出机中的停留时间优选为3~5min,更优选为3.5~4min。
82.在本发明中,物料在所述双螺杆挤出机中的压力优选为10~15mpa,更优选为11.5~14mpa。
83.在本发明中,所述聚乙烯、抗菌助剂、阻燃剂、纳米碳酸钙、抗氧剂和偶联剂经过双螺杆配混挤出机搅拌、熔融、冷却、切粒、干燥后得到所述抗菌阻燃聚乙烯材料。
84.本发明对所述冷却、切粒和干燥的具体实施过程没有特殊要求。
85.本发明提供一种抗菌阻燃聚乙烯薄膜,所述抗菌阻燃聚乙烯薄膜的成膜原料包括权上述技术方案所述的抗菌阻燃聚乙烯材料或上述技术方案所述的制备方法制备得到的抗菌阻燃聚乙烯材料。
86.在本发明中,所述抗菌阻燃聚乙烯薄膜的成膜原料优选还包括聚乙烯母料。
87.在本发明中,所述聚乙烯母料和抗菌阻燃聚乙烯材料的质量比优选为(0.1~10):1,更优选为(0.15~8):1,进一步优选为(0.2~7):1。
88.本发明提供了上述技术方案所述的抗菌阻燃聚乙烯薄膜的制备方法,包括以下步骤:
89.将成膜原料熔融后制备成膜,获得所述抗菌阻燃聚乙烯薄膜,所述制备成膜包括吹塑成膜、注塑成膜、滚塑成膜或流延成膜。
90.在本发明中,进行所述制备成膜之前,本发明优选将聚乙烯母料和抗菌阻燃聚乙烯材料混合。
91.在本发明中,所述聚乙烯母料和抗菌阻燃聚乙烯材料混合时优选在高速混料机中进行。
92.在本发明中,所述吹塑成膜优选在挤出吹膜机进行。
93.在本发明中,所述挤挤出吹膜机工作时由加料口至挤出机头依次分布第1温度区域、第2温度区域、第3温度区域、第4温度区域。
94.在本发明中,所述第1温度区域的温度优选为155~165℃。
95.在本发明中,所述第2温度区域的温度优选为160~170℃。
96.在本发明中,所述第3温度区域的温度优选为160~170℃。
97.在本发明中,所述第4温度区域的温度优选为155~165℃。
98.在本发明中,所述制备成膜包括注塑成膜、滚塑成膜或流延成膜时,本发明对所述注塑成膜、滚塑成膜或流延成膜的具体实施方法没有特殊要求。
99.为了进一步说明本发明,下面结合实施例对本发明提供的技术方案进行详细地描述,但不能将它们理解为对本发明保护范围的限定。
100.实施例1
101.步骤1:将甲酸铜(ii)、高分子材料载体(聚氯乙烯)和无水乙醇通过磁力搅拌进行充分混合,得到混合物前驱体;通过鼓风干燥箱去除所述混合物前驱体中的乙醇溶剂,得到干燥的混合物前驱体;将所述干燥的混合物前驱体在275℃条件下进行煅烧,得到所述铜氧化物-高分子复合材料,纳米铜氧化物和高分子载体的质量比为1:6。
102.将低密度聚乙烯、铜氧化物-高分子复合材料、锡酸锌、纳米碳酸钙、抗氧剂、偶联剂按照一定剂量配料后通过高速混料机进行受力均匀混合,然后经过双螺杆配混挤出机搅拌、熔融、冷却、切粒、干燥后,获得抗菌阻燃聚乙烯母粒。
103.其中,低密度聚乙烯、铜氧化物-高分子复合材料、锡酸锌、纳米碳酸钙、抗氧剂、偶联剂的质量百分比分别为:80.5wt%,2.0wt%,10.0wt%,5.0wt%,0.5wt%、2.0wt%。所用抗氧剂为抗菌剂1076和抗菌剂168的组合抗氧剂,质量百分比为1:2;偶联剂为硅烷偶联剂kh-560。
104.双螺杆配混挤出机从加料口到机头按顺次分布共10个温区,温度分步分别为80℃
±
5℃,180℃
±
5℃,180℃
±
5℃,180℃
±
5℃,180℃
±
5℃,180℃
±
5℃,170℃
±
5℃,170℃
±
5℃,170℃
±
5℃,185℃
±
5℃,停留时间为3~5min,熔体压力为10~15mpa。
105.步骤2:将上述抗菌阻燃聚乙烯材料与低密度聚乙烯按1:1的质量比进行配料,经高速混料机进行受力混合后通过挤出吹膜机熔融、挤出吹膜成型,得到抗菌阻燃聚乙烯薄膜材料。所得抗菌阻燃聚乙烯薄膜材料中,抗菌剂铜氧化物-高分子复合材料的质量比为1.0wt%,阻燃剂锡酸锌的质量比为5.0wt%。
106.其中,吹膜机温度分布设定为:160℃
±
5℃,165℃
±
5℃,165℃
±
5℃,160℃
±
5℃。
107.实施例2
108.实施例2与实施例1基本一致,仅在步骤2中,将步骤1所制备的抗菌阻燃聚乙烯材料直接经过挤出吹膜机熔融、挤出吹膜成型,不再经过与低密度聚乙烯配料混合的过程,获得抗菌阻燃聚乙烯薄膜。所得抗菌阻燃聚乙烯薄膜材料中,抗菌剂铜氧化物-高分子复合材料的质量比为2.0wt%,阻燃剂锡酸锌的质量比为10.0wt%。
109.实施例3
110.实施例3与实施例1基本一致,仅在步骤2中,抗菌阻燃聚乙烯材料与低密度聚乙烯按1:4的质量比进行配料。所得抗菌阻燃聚乙烯薄膜材料中,抗菌剂铜氧化物-高分子复合材料的质量比为0.4wt%,抗菌聚乙烯薄膜材料中阻燃剂锡酸锌的质量比为2.0wt%。
111.对比例1
112.对比例1与实施例1基本一致,仅在步骤1配料时,不添加阻燃剂锡酸锌,经过步骤1、步骤2的注塑、吹膜工艺处理后得到抗菌聚乙烯薄膜材料。所得抗菌聚乙烯薄膜材料中抗菌剂铜氧化物-高分子复合材料的质量比为1.0wt%。
113.对比例2
114.对比例2与实施例1基本一致,仅在步骤1配料时,不添加抗菌剂铜氧化物-高分子复合材料,经过步骤1、步骤2的注塑、吹膜工艺处理后得到阻燃聚乙烯薄膜材料。所得阻燃聚乙烯薄膜材料中阻燃剂锡酸锌的质量比为5.0wt%。
115.实施例4
116.实施例4与实施例1基本一致,仅在步骤1中,低密度聚乙烯与锡酸锌、铜氧化物-高分子复合材料、纳米碳酸钙、抗氧剂、偶联剂的剂量比调整为:75.5wt%,10.0wt%,2.0wt%,8.0wt%,0.5wt%、4.0wt%。
117.实施例5
118.实施例5与实施例1基本一致,仅在步骤1中,抗氧剂调整为抗氧剂1076和抗氧剂dltdp的组合抗氧剂。
119.实施例6
120.实施例6与实施例1基本一致,仅在步骤1中,偶联剂调整为硅烷偶联剂kh-550。
121.实施例7
122.实施例7与实施例1基本一致,仅在步骤1和步骤2中,所使用的聚乙烯类型均调整为高密度聚乙烯,其他条件不变。
123.实施例8
124.实施例8与实施例1基本一致,仅在步骤1和步骤2中,所使用的聚乙烯类型调整均为低密度聚乙烯,其他条件不变。
125.实施例9
126.实施例9与实施例1基本一致,仅在步骤1,所使用的阻燃剂由锡酸锌调整均为羟基锡酸锌,其他条件不变。
127.性能测试
128.对实施例1进行了抗菌性能测试,测试结果见表1和图2;对实施例1进行了病毒灭活性能测试测试结果见表2;对实施例1、实施例2、实施例3进行阻燃性能测试,测试结果见表3。
129.其中,性能测试的对照样品为常规的聚乙烯薄膜,无添加阻燃剂及抗菌剂。
130.其中,抗菌测试参考标准gb/t 31402-2005塑料表面抗菌性能试验方法和标准gb/t4789.2-2016《食品安全国家标准食品微生物学检验菌落总数测定》;病毒灭活测试参考《消毒技术规范》(2002年版);阻燃测试参考标准ul 94。
131.表1实施例1经过标准gb/t31402-2005《塑料表面抗菌性能试验方法》测试对大肠杆菌和金黄色葡萄球菌的杀菌性能测试结果
[0132][0133]
表2实施例1对马动脉炎病毒的灭活性能测试结果
[0134][0135]
表3实施例1、实施例2、实施例3的阻燃性能测试结果
[0136]
测试样品阻燃等级ul94实施例1v0实施例2v0实施例3v1对照样不阻燃
[0137]
由表1和图2的数据可知,经过标准gb/t31402-2005《塑料表面抗菌性能试验方法》和标准gb/t4789.2-2016《食品安全国家标准食品微生物学检验菌落总数测定》测试,本发明制备的抗菌阻燃聚乙烯薄膜材料具有优异的抗菌效果:实施例1测试样品对大肠杆菌和金黄色葡萄球菌的杀菌率均达到了99.9%。由表2的数据可知,本发明制备的抗菌阻燃聚乙
烯薄膜材料具有优异的抗病毒效果:实施例1测试样品对马动脉炎病毒的灭活效果达到了99.75%。本发明制备的抗菌阻燃聚乙烯薄膜材料具有显著的阻燃效果:实施例1、实施例2的阻燃等级均达到了标准ul 94的v0级别,实施例3在制备工艺过程中相对于实施例2,阻燃剂添加量稀释了5倍,但相对于未添加阻燃剂的对照样,仍然表现出了较好的阻燃性能,达到了v1级别。
[0138]
尽管上述实施例对本发明做出了详尽的描述,但它仅仅是本发明一部分实施例,而不是全部实施例,人们还可以根据本实施例在不经创造性前提下获得其他实施例,这些实施例都属于本发明保护范围。