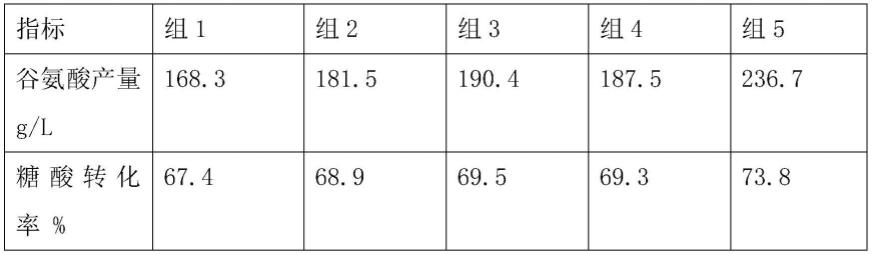
l-谷氨酸清洁发酵生产方法
技术领域
1.本发明属于氨基酸生产技术领域,具体涉及l-谷氨酸清洁发酵生产方法。
背景技术:2.谷氨酸作为氨基酸生产中产量最大的氨基酸,目前,制备谷氨酸最常用的方法是微生物发酵法。谷氨酸棒杆菌是谷氨酸发酵的常规菌株。影响谷氨酸棒杆菌发酵产酸效率的因素较多,主要包括以下几个方面:1、微生物在不同的环境条件下、利用不同底物代谢途径是不同的,有目的地对细胞代谢途径进行修饰和改造,改变细胞原有的代谢特征,可以提高目标产物的产量和得率;2、通过提高菌体的细胞膜通透性,增加谷氨酸分泌,进而解除菌体内高浓度谷氨酸的反馈调节作用,提高谷氨酸的产量;3、优化发酵培养基、发酵参数,使得菌体增殖速率提高,从而提高氨基酸的产量。据代谢网络定量分析原理,应用途径分析方法对l-谷氨酸生物合成途径进行分析,确定l-谷氨酸生物合成的理想载流途径,以提高谷氨酸的发酵效率。通过l-谷氨酸发酵中后期的代谢流分布与途径分析所得到的理想代谢流相比较,寻求代谢流中的扰动因子,以此指导l-谷氨酸高产菌的发酵条件优化,通过改变l-谷氨酸发酵过程中的关键节点处的代谢流分配,以提高产酸水平,并填补此领域中的研究空白。谷氨酸棒杆菌的代谢转向极为显著,不同的外部环境、控制条件都极大的影响代谢流的分布。l-谷氨酸发酵过程是典型的代谢控制发酵,发酵工艺研究至关重要。发酵环境条件,如培养基组成、ph、温度、溶氧水平等都明显地影响l-谷氨酸的产量。
3.申请人之前的专利技术“谷氨酸的绿色清洁发酵工艺”,有效解决了谷氨酸发酵过程中的多种问题,包括谷氨酸合成的反馈抑制、细胞通透性以及发酵培养基优化,提高了发酵效率,降低了谷氨酸分离纯化的难度;最高糖酸转化率为68.5%,最大产酸量为171g/l,仍有较大提升空间。
[0004]“cn113981019a,一种提高谷氨酸发酵速率的工艺”,通过优化培养基提高了发酵效率,但是发酵培养基中添加了玉米浆、豆粕水解液,会带来较多的色素等杂质,后续分离工艺中难以完全去除,无法达到清洁发酵的目的。
技术实现要素:[0005]
本发明所要解决的技术问题在于提供l-谷氨酸清洁发酵生产方法,优化了发酵工艺,提高了发酵效率,并且降低了谷氨酸分离纯化的难度。
[0006]
本发明是通过如下技术方案来实现的。
[0007]
谷氨酸清洁发酵生产方法,包括往发酵罐中流加调节剂的步骤,所述调节剂包括甘油、柠檬酸锌以及五水硫酸铜中的任其一或二者以上的组合。
[0008]
优选地,
[0009]
所述调节剂包括甘油、柠檬酸锌以及五水硫酸铜。
[0010]
更优选地,
[0011]
所述调节剂的组分为:甘油1-10g/l,柠檬酸锌1-4g/l,五水硫酸铜0.2-1.6g/l。
[0012]
最优选地,
[0013]
所述调节剂的组分为:甘油5g/l,柠檬酸锌2g/l,五水硫酸铜0.8g/l。
[0014]
进一步地,
[0015]
所述调节剂的流加速率为0.2ml/l.min。
[0016]
进一步地,
[0017]
所述调节剂在发酵8h时开始流加,直至发酵结束。
[0018]
具体地,
[0019]
所述方法包括如下步骤:将谷氨酸棒杆菌种子液接入装有清洁发酵培养基的发酵罐中进行发酵培养,发酵温度为32℃,待发酵液od
600
=30时,提高发酵温度为37.5℃,直至发酵结束;整个发酵过程中,控制通风比1∶0.8,搅拌转速300rpm,溶氧维持在20%,流加800g/l的葡萄糖溶液维持残糖为1%,流加消泡剂消泡,同时流加氨水调节发酵液的ph值至7.2,直至发酵结束;发酵总时间36h。优选地,
[0020]
所述清洁发酵培养基为:葡萄糖80g/l,mnso4·
h2o 3mg/l,feso4·
7h2o 3mg/l,mgso4·
7h2o 2g/l,na2hpo4·
12h2o 4g/l,kcl 2g/l,vb110mg/l,生物素7μg/l,生物氮素2g/l,甲硫氨酸0.6g/l。
[0021]
与现有技术相比,本发明取得的有益效果主要包括但是并不限于以下几个方面:
[0022]
实现各营养元素的合理配比,最大发挥菌体的产酸能力,以提高发酵转化率和产酸;谷氨酸产生菌增殖到较大值,谷氨酸生成酶系形成完全时,加入适量的cu2+离子能够抑制乙醛酸循环中的关键酶,削弱乙醛酸循环,进而增加tca循环中的碳流,提高谷氨酸的发酵效率;甘油提供碳骨架,促进谷氨酸的合成,并且能够提高细胞膜通透性,促进谷氨酸分泌到发酵液中;通过添加柠檬酸锌能够加强菌体细胞代谢能力,提高菌体细胞内关键酶的活力,有利于维持菌体细胞活力,进而提高谷氨酸产率。三种营养物质配伍合理,实现了1+1+1>3的协同效果,增加谷氨酸分泌,提高了谷氨酸的产量,实现了谷氨酸发酵效益的提升。
附图说明
[0023]
图1:柠檬酸钠对谷氨酸产量的影响;
[0024]
图2:五水硫酸铜对谷氨酸产量的影响。
具体实施方式
[0025]
为了使本技术领域的人员更好地理解本技术中的技术方案,下面将结合本技术具体实施例,对本技术的技术方案进行清楚、完整地描述,显然,所描述的实施例仅仅是本技术一部分实施例,而不是全部的实施例。基于本技术中的实施例,本领域普通技术人员在没有作出创造性劳动前提下所获得的所有其他实施例,都应当属于本发明保护的范围。
[0026]
实施例1
[0027]
谷氨酸清洁发酵生产方法,包括如下步骤:将谷氨酸棒杆菌gdk-9种子液(od
600
=20)按10%接种量接入装有500l清洁发酵培养基的1000l发酵罐中进行发酵培养,发酵温度为32℃,待发酵液od
600
=30时,提高发酵温度为37.5℃,直至发酵结束;整个发酵过程中,控制通风比1∶0.8,搅拌转速300rpm,溶氧维持在20%,流加800g/l的葡萄糖溶液维持残糖为1%,流加消泡剂消泡,同时流加氨水调节发酵液的ph值至7.2,直至发酵结束;发酵总时间
36h;发酵至8h时,往发酵罐中流加调节剂,流加速率为0.2ml/l.min(即按照每升发酵液每分钟流加0.2ml)。
[0028]
所述清洁发酵培养基为:葡萄糖80g/l,mnso4·
h2o 3mg/l,feso4·
7h2o 3mg/l,mgso4·
7h2o 2g/l,na2hpo4·
12h2o 4g/l,kcl 2g/l,vb110mg/l,生物素7μg/l,生物氮素2g/l,甲硫氨酸0.6g/l。
[0029]
所述调节剂为:甘油5g/l,柠檬酸锌2g/l,五水硫酸铜0.8g/l。
[0030]
上述培养基和调节剂的溶剂均为水。
[0031]
对比例1
[0032]
谷氨酸的绿色清洁发酵工艺,包括如下步骤:将谷氨酸棒杆菌gdk-9种子液(od
600
=20)按10%接种量接入装有清洁发酵培养基的发酵罐中进行发酵培养,发酵温度为32℃,待发酵液od
600
=30时,提高发酵温度为37.5℃,直至发酵结束;整个发酵过程中,控制通风比1∶0.8,搅拌转速300rpm,溶氧维持在20%,流加800g/l的葡萄糖溶液维持残糖为1%,流加消泡剂消泡,同时流加氨水调节发酵液的ph值至7.2,直至发酵结束;发酵总时间36h。
[0033]
所述清洁发酵培养基为:葡萄糖80g/l,mnso4·
h2o 3mg/l,feso4·
7h2o 3mg/l,mgso4·
7h2o 2g/l,na2hpo4·
12h2o 4g/l,kcl 2g/l,vb110mg/l,生物素7μg/l,生物氮素2g/l,甲硫氨酸0.6g/l。
[0034]
实施例2
[0035]
1.在对比例1的基础上,验证不同组分和配比的调节剂对谷氨酸发酵的影响。根据之前的研究成果首先确定调节剂中甘油的最适添加浓度为5g/l;设置柠檬酸锌的浓度为0,1,2,3,4,5,6,7,单位为g/l,如图1所示,谷氨酸的产量随着柠檬酸锌浓度的增大而增加,柠檬酸锌浓度达到2g/l后谷氨酸产量增速明显放缓,糖酸转化率的趋势和谷氨酸产量基本保持一致。
[0036]
2.在调节剂(甘油5g/l+柠檬酸锌2g/l)的基础上进行进一步的试验,设置五水硫酸铜的浓度为0,0.1,0.2,0.4,0.8,1.6,3,2,6.4单位为g/l,如图2所示,过低浓度的五水硫酸铜对谷氨酸的产量没有明显影响,当五水硫酸铜浓度增加到0.4g/l时,谷氨酸产量有一定的提升,继续增大到0.8g/l,谷氨酸产量达到峰值,继续增加五水硫酸铜浓度,谷氨酸产量并没有明显提高,糖酸转化率的趋势和谷氨酸产量基本保持一致。
[0037]
五水硫酸铜对谷氨酸棒杆菌发酵产谷氨酸的影响,可能源于其对乙醛酸循环中关键酶的弱化和抑制作用;但是也有研究表明,缺失乙醛酸循环活性的突变株的谷氨酸产量非但没有降低,反而有所下降,这说明乙醛酸循环的存在是必需的,鉴于细胞信号通路的复杂性,难以通过推理来判断某一物质对乙醛酸循环和谷氨酸合成途径之间的影响。
[0038]
3.调节剂中各组分对谷氨酸产量和糖酸转化率的影响。
[0039]
相同发酵条件下,具备可比性。
[0040]
组1:不添加调节剂;
[0041]
组2:甘油5g/l;
[0042]
组3:柠檬酸锌2g/l;
[0043]
组4:五水硫酸铜0.8g/l;
[0044]
组5:甘油5g/l,柠檬酸锌2g/l,五水硫酸铜0.8g/l。
[0045]
各组的谷氨酸发酵产量和糖酸转化率见表1:
[0046]
表1
[0047][0048]
如上表1所示,调节剂中的三种组分配伍合理,实现了1+1+1>3的协同效果,增加谷氨酸分泌,提高了谷氨酸的产量,实现了谷氨酸发酵效益的提升。谷氨酸糖酸转化率从67.4%提升至73.8%,计算按照在年产20万吨生产线上实施应用来计算,实现综合生产成本下降15%以上,年新增效益8000万元以上。
[0049]
以上列举的仅是本发明的最佳具体实施例。显然,本发明不限于以上实施例,还可以有许多变形。本领域的普通技术人员能从本发明公开的内容直接导出或联想到的所有变形,均应认为是本发明的保护范围。