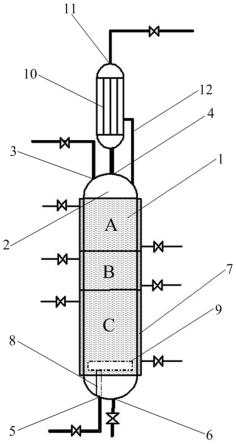
1.本发明是一种全氟聚醚油及其制备工艺和装置,具体涉及一种采用催化氟化制备的饱和稳定的全氟聚醚油及其制备工艺和装置,属于氟化工技术领域。
背景技术:2.全氟聚醚油是一类集合了优异的耐高低温、不燃、高耐热氧、高化学惰性、低挥发、优异介电、无毒及优异的粘温特性等众多性能于一体的一类氟代聚合物材料,在航空航天、国防装备、电子、核能等领域被广泛用作润滑油、润滑脂、高真空泵油、热传导液、绝缘液、冷却液等。现有技术中,不论是solvay的fomblin y型、z型分子链结构的全氟聚醚,还是chemours的krytox(k型),或者日本大金公司的demnum型(d型)全氟聚醚,它们都来自于分子链端基为高反应活性的聚醚酰氟或者聚醚羧酸。在生产过程中,必须将聚醚酰氟或者聚醚羧酸通过氟化处理工艺转化为稳定的分子链端基结构才能满足性能要求。
3.目前,成功应用于氟化处理的工艺技术主要有三种。一种是simons电解氟化技术,该技术是以无水氟化氢为溶剂和氟源,待氟化处理物溶解其中并于电解槽中通直流电进行电解氟化实现氟化处理。受限于无水氟化氢的溶解性能,电解氟化技术比较常见应用于对小分子化合物氟化处理。同时,大量无水氟化氢使用也带来较大的安全风险,而且还需要进行复杂的分离纯化处理,因此电解氟化技术在不稳定全氟聚醚端基稳定化处理上的应用存在问题。第二种是含氟盐催化氟化技术,使用氟盐为cof3、alf3、sbf5等氟化剂,过去报道技术一般在270~400℃高温条件下才展示出较好的氟化效果,高温氟化对过程控制以及配套设备投入带来挑战和困难。而且,这些氟化剂价格都较高,分离困难,产品品质难于得到保证。第三种是采用氟化试剂进行元素氟化,氟化试剂包括氟气、sf4、sf6、bf3等。该技术的优势是所得产品后处理简单、产品品质高。但由于氟化剂如氟气是气体形态,在不稳定全氟聚醚中溶解度低,是气液非均相反应过程,经常存在分散不均匀、气液接触不充分等原因造成氟化剂利用效率较低、常常需要氟气用量是理论用量10倍以上,常见氟化反应时间超长、反应成本高、尾气处理量大、环保压力大等等系列问题。
4.为解决上述工艺技术存在的问题,公开号为cn110092901a的发明专利公开了一种全氟聚醚不稳定端基的氟化工艺的发明专利,该氟化工艺通过配套使用的鼓泡塔式反应器,提高了气液两相反应物料的接触面积和传质能力,一定程度上提高了氟化反应的速率,解决了现有工艺技术中物料分散不均匀、气液接触不充分等缺陷,在一定程度提高了氟气的利用效率以及全氟聚醚的转化率。但是,对于规模化全氟聚醚油类产品生产,反应的时效仍然不高,反应效率较低。除此之外,公开号为cn112876669a的发明专利公开了一种全氟聚醚端基氟化的方法,采用紫外光照射氟气和惰性气体的混合气,使其活化后再通入装有全氟聚醚酰氟的反应釜中进行反应,得到端基氟化的全氟聚醚。但是,紫外光源的使用对反应设备提出了新的挑战,为保证充分的光效率和光通量,通常需采用玻璃设备,这对于高腐蚀性的聚醚酰氟或者羧酸耐受性常常无法满足要求,这要求对水分或者潮气要做严格管控。专利cn 111892705 a 、cn 113150262a分别介绍了以无机碱、有机胺作为处理剂或助剂结
合蒸汽高温脱羧实现饱和全氟聚醚油的制备方法,该技术通过脱羧反应实现了饱和分子结构全氟聚醚油的制备,但分子链端实际是一种-cf2h封端结构,并非高度稳定的-cf3分子结构,产品在应用于苛刻条件工况下时显然无法满足要求;并且,该工艺涉及到有机胺类原材料应用,从安全、环保等角度存在风险和隐患。
技术实现要素:5.本发明的目的是提供一种全氟聚醚油的制备工艺,是采用二氟化钴催化剂作为催化剂催化氟化不饱和的全氟聚醚酰氟和/或全氟聚醚羧酸进行氟化反应,实现饱和全氟聚醚油的规模化、高效生产的制备工艺,可提高现有技术存在的反应时间长、反应效率低、对反应装备投入高等缺陷。为此,本发明还提供了由该制备工艺得到的结构稳定的全氟聚醚油,以及可实现连续催化氟化制备全氟聚醚油的装置。
6.本发明通过下述技术方案实现:一种全氟聚醚油的制备工艺,采用聚四氟乙烯负载的具有多孔结构的二氟化钴催化剂催化全氟聚醚酰氟和/或全氟聚醚羧酸、氟化剂进行氟化反应,即得全氟聚醚油,所述全氟聚醚酰氟和/或全氟聚醚羧酸的结构满足下式(ⅰ)所示:
ꢀꢀꢀꢀꢀꢀꢀ
(ⅰ)式(ⅰ)中,m,n,q为≥0的自然数,rf1、rf2为-cf2cox1、-cf(cf3)co x1、-cf(cf3)cf2oco x1,x1为-oh或f,或者rf1、rf2中的一个为-cdf
2d
,d为1至3的自然数;所述全氟聚醚油的结构满足下式(ⅱ)所示:
ꢀꢀꢀꢀꢀꢀꢀ
(ⅱ)式(ⅱ)中,m,n,q为≥0的自然数,rf3、rf4为-c
pf2p
,p为1至3的自然数。
7.所述氟化反应温度控制在150-250℃。
8.所述氟化剂选自f2与n2的混合气、sf4、sf6、bf3中的至少一种。
9.所述氟化剂选自f2与n2的混合气,控制混合气中f2的体积浓度为20-30%。
10.一种采用上述工艺制备的全氟聚醚油。
11.一种制备上述全氟聚醚油的装置,包括反应器本体,于反应器本体内设二氟化钴催化剂床层,位于二氟化钴催化剂床层上方的反应器本体上设气体出口以及连接全氟聚醚酰氟和/或全氟聚醚羧酸管路的液体进料口,位于催化剂床层下方的反应器本体上设出料口以及连接氟化剂管路的气体进口,二氟化钴催化剂床层包括沿反应器本体轴向依次分布的至少三层填充段,对应每层填充段的反应器本体外均设有夹套。
12.所述每层填充段的反应温度通过夹套控制相同或不同。
13.所述气体进口上设气体分布器,氟化剂经气体分布器于二氟化钴催化剂床层内以鼓泡方式送入。
14.所述气体出口上设冷凝器,冷凝器上设尾气出口以及连接反应器本体的回流管。
15.所述反应器本体的长径比≥10︰1。
16.本发明与现有技术相比,具有以下优点及有益效果:(1)本发明采用高强度ptfe负载的具有多孔结构的二氟化钴作为催化剂进行氟化反应,相对于其它不饱和全氟聚醚酰氟、聚醚羧酸的端基处理技术显著提高了饱和基团-c
xf2x+1
(x=1~3)的转化率,封端反应具有更高的效率和能力。
17.(2)本发明在氟化反应过程中采用二氟化钴催化剂作为填充床层,反应温度控制在150-250℃,采用分段和多级控制,通过夹套控制每段反应温度,满足连续化的工艺控制过程,适合于规模化的全氟聚醚油的大规模生产。
18.综上所述,本发明采用连续生产的封端工艺,不仅节约了氟气封端的原料成本,避免溶剂助剂等大量使用回收,催化剂采用高强度ptfe负载,不会出现催化剂流失,同时减少三废的排放,是一种更加绿色环保高效的连续生产方法。
附图说明
19.图1为本发明中反应器本体的结构示意图。
20.图2为实施例1中液体进料口物料的ftir谱图。
21.图3为实施例1中出料口物料的ftir谱图。
22.图4为对比例1中出料口物料的ftir谱图。
23.其中,1—二氟化钴催化剂床层,2—反应器本体,3—液体进料口,4—气体出口,5—气体进口,6—出料口,7—夹套,8—气体分布器,9—冷凝器,10—尾气出口,11—回流管。
具体实施方式
24.下面将本发明的发明目的、技术方案和有益效果作进一步详细的说明。
25.应该指出,以下详细说明都是示例性的,旨在对所要求的本发明提供进一步的说明,除非另有说明,本文使用的所有技术和科学术语具有与本发明所属技术领域的普通技术人员通常理解的相同含义。
26.本发明是一种全氟聚醚油的连续化制备工艺,可制备得到饱和的结构稳定的全氟聚醚油。
27.具体采用图1所示装置,该装置在反应器本体内填充二氟化钴催化剂床层,分别将全氟聚醚酰氟和/或全氟聚醚羧酸、氟化剂送入反应器本体内进行催化氟化反应,即得全氟聚醚油。
28.全氟聚醚酰氟和/或全氟聚醚羧酸的结构满足下式(ⅰ)所示:
ꢀꢀꢀꢀꢀꢀꢀ
(ⅰ)式(ⅰ)中,m,n,q为≥0的自然数,rf1、rf2为-cf2cox1、-cf(cf3)co x1、-cf(cf3)cf2oco x1,x1为-oh或f,或者rf1、rf2中的一个为-cdf
2d
,d为1至3的自然数。
29.进一步的,本发明采用不饱和的全氟聚醚酰氟和/或全氟聚醚羧酸,平均分子量不小于200,优选平均分子量在500以上,由于不饱和基团酰氟与水、潮气等的高反应活性,因此实际生产过程中,通常为不饱和的全氟聚醚酰氟和全氟聚醚羧酸的混合物。
30.全氟聚醚油的结构满足下式(ⅱ)所示:
ꢀꢀꢀꢀꢀꢀꢀ
(ⅱ)式(ⅱ)中,m,n,q为≥0的自然数,rf3、rf4为-c
xf2x
,x为1至3的自然数。
31.进一步的,本发明可制备得到结构稳定的饱和全氟聚醚油,特别是全氟聚醚油结构中饱和基团-c
xf2x+1
(x=1~3)的转化率得到提高,使得饱和产物的酸值至少可控制在1mgkoh/g以下,更低可达到0.3mgkoh/g以下。
32.本发明采用的二氟化钴催化剂床层的填充物料为采用聚四氟乙烯负载的具有多孔结构的二氟化钴催化剂,是采用氧化钴、高强度的聚四氟乙烯以及致孔剂混配并压制进入定型模具,再经烧结定型、无水氢氟酸反应而制得。在用于催化氟化反应时,二氟化钴与元素氟进行原位反应转化为三氟化钴催化活性中心实现对式(i)不饱和全氟聚醚酰氟和/或全氟聚醚羧酸的快速、高效的氟化封端反应,实现饱和全氟聚醚油的规模化、高效生产。
33.发生的原位反应历程如下:cof2+f2→
cof3r-h+2cof3→
r-f+2cof2+ hf本发明的氟化剂选自f2与n2的混合气、sf4、sf6、bf3中的至少一种,优选f2与n2的混合气,混合气中f2的体积浓度控制在20-30%。
34.在具体制备过程中,将不饱和的全氟聚醚酰氟和/或全氟聚醚羧酸从反应器本体的液态进料口连续进料,将氟化剂由反应器本体的气体进口进料,如通过气体进口的气体分布器于二氟化钴催化剂床层内以鼓泡方式连续或间歇进料。反应时,利用二氟化钴在150-250℃以上的高温条件下通过与元素氟进行原位反应转化为三氟化钴催化活性中心实现对不饱和聚醚酰氟和/或全氟聚醚羧酸的催化氟化,同时对二氟化钴催化剂床层采用分级温度控制及反应控制,即将二氟化钴催化剂床层沿反应器本体轴向依次划分为至少三层填充段,对应每层填充段的反应器本体外均设有夹套,通过不同填充段外夹套的温度控制,可实现分段控温和反应控制。例如,在一个具体的温度控制过程中,设计温度控制范围在150-250℃,图1所示的a层填充段温度控制为150℃,b层填充段温度控制在170℃,c层填充段温度控制在200℃,并对各层填充段的长度无比例要求。
35.下面以几个典型实施例来列举说明本发明的具体实施方式,当然,本发明的保护范围并不局限于以下实施例。
36.实施例1:以长径比为10:1的一个三段式分段反应器本体作为反应装置,各段均以ptfe负载的二氟化钴催化剂做填充,对结构式为cf3o[cf2cf(cf3)o]mcf(cf3)cof的具有不饱和结构的酰氟及其羧酸进行稳定化处理,平均分子量为650的酰氟及其羧酸从上部液体进料口以10g/min进料速度连续进料,f2和n2的混合气(f2的体积浓度占20%)从下部气相进口以
0.1kg/h气速进行鼓泡进料,三段分级的反应器本体从下部向上各级控制温度为200℃、170℃和150℃,不凝气经过上部冷凝器联接尾气处理系统进行尾气处理,冷凝液回流至反应器本体,反应器本体内经过稳定化处理的全氟聚醚油从下部出料口进行收集。
[0037]
分别对液体进料口及出料口的物料进行取样检测,参见图2和图3所示,经红外测试显示,全氟聚醚油的吸收峰为1774.5cm-1、1726cm-1处的不饱和羰基吸收峰、3000cm-1~3500cm-1处钝头羧酸振动吸收完全消失,说明经过氟化处理已不含不饱和基团,滴定酸值测试为1mgkoh/g(酸碱滴定法,下同)。
[0038]
实施例2:本实施例在实施例1的基础上,采用平均分子量为1050的酰氟及其羧酸,其余催化氟化反应的控制条件和反应装置均与实施例1相同,经过稳定化处理得到的全氟聚醚油,经取样进行红外测试结果与实施例1一致,不含不饱和基团吸收峰,滴定酸值测试为0.8mgkoh/g。
[0039]
实施例3:本实施例采用实施例1的基础上,采用平均分子量为850、结构式为cf3o(cf2o)n[cf2cf(cf3)o]mcf(cf3)cof的不饱和的酰氟及其羧酸进行稳定化处理,其余催化氟化反应的控制条件和反应装置均与实施例1相同,经过稳定化处理得到的全氟聚醚油,经取样进行红外测试结果与实施例1一致,不含不饱和基团吸收峰,滴定酸值测试为0.7mgkoh/g。
[0040]
实施例4:本实施例采用实施例1的基础上,采用平均分子量为1520、结构式为foc(cf3)cf(cf2)n[cf2cf(cf3)o]mcf(cf3)cof的不饱和的酰氟及其羧酸进行稳定化处理,其余催化氟化反应的控制条件和反应装置均与实施例1相同,经过稳定化处理得到的全氟聚醚油,经取样进行红外测试结果与实施例1一致,不含不饱和基团吸收峰,滴定酸值测试为0.5mgkoh/g。
[0041]
实施例5:本实施例采用实施例1的基础上,采用长径比为15:1的反应器本体,采用平均分子量为1520、结构式为foc(cf3)cf(cf2)n[cf2cf(cf3)o]mcf(cf3)cof的不饱和的酰氟及其羧酸进行稳定化处理,控制 f2和n2的混合气的气速为0.12kg/h,三段分级的反应器本体从下部向上各级控制温度为250℃、180℃和150℃,其余催化氟化反应的控制条件和反应装置均与实施例1相同,经过稳定化处理得到的全氟聚醚油,经取样进行红外测试结果与实施例1一致,不含不饱和基团吸收峰,滴定酸值测试为0.4mgkoh/g。
[0042]
实施例6:本实施例采用实施例1的基础上,采用平均分子量为2250、结构式为cf3o(cf2o)n[cf2cf(cf3)o]mcf(cf3)cof的不饱和的酰氟及其羧酸进行稳定化处理,控制 f2和n2的混合气的气速为0.15kg/h,三段分级的反应器本体从下部向上各级控制温度为200℃、180℃和150℃,其余催化氟化反应的控制条件和反应装置均与实施例1相同,经过稳定化处理得到的全氟聚醚油,经取样进行红外测试结果与实施例1一致,不含不饱和基团吸收峰,滴定酸值测试为0.3mgkoh/g。
[0043]
对比例1:本对比例采用长径比为3:1的反应器本体作为反应装置,反应器本体内填充cof3作为催化剂床层,对平均分子量为650、结构式为cf3o[cf2cf(cf3)o]mcf(cf3)cof的不饱和的
酰氟及其羧酸进行稳定化处理,反应器本体上部的液体进料速度控制在10g/min,氟化剂由反应器本体的下部鼓泡进料,采用f2和n2的混合气(f2的体积浓度占20%),气速控制在0.1kg/h,反应器本体外设加热套对催化剂床层进行加热,温度控制在200℃进行催化氟化反应,反应器本体内的不凝气经过上部冷凝器联接尾气处理系统进行尾气处理,冷凝液回流至反应器本体,反应器本体内经过稳定化处理的全氟聚醚油从下部出料口进行收集。
[0044]
对出料口的物料进行取样检测,参见图4所示,经红外测试显示,全氟聚醚油在1602cm-1
和3232cm-1
~3417cm-1
出现羰基吸收峰和羧基吸收,说明其端基稳定化不完全,滴定酸值测试为5.2mgkoh/g。
[0045]
按上述实施例1-6、对比文件1的方法进行全氟聚醚油的连续制备,制备过程中,不饱和全氟聚醚酰氟及其羧酸连续进料,氟化剂按工艺条件连续或间歇进料,在连续化生产过程中,分别对全氟聚醚油进行取样检测,测定其酸值如下表1所示。
[0046]
表1 全氟聚醚油的酸值测试数据表由上表1可知,本发明在不饱和全氟聚醚酰氟和/或全氟聚醚羧酸的稳定化处理过程中,采用高强度ptfe负载的具有多孔结构的二氟化钴催化剂,利用分级温度控制过程,可以在连续化氟化处理工艺中获得结构更加稳定的全氟聚醚油,且在连续化生产过程中,本发明采用的二氟化钴催化剂较对比例1使用的cof3催化剂而言,不仅能提高封端反应效率,还能减少流失,更有利于全氟聚醚油的大规模工业生产。
[0047]
以上所述,仅是本发明的较佳实施例,并非对本发明做任何形式上的限制,凡是依据本发明的技术实质对以上实施例所作的任何简单修改、等同变化,均落入本发明的保护范围之内。