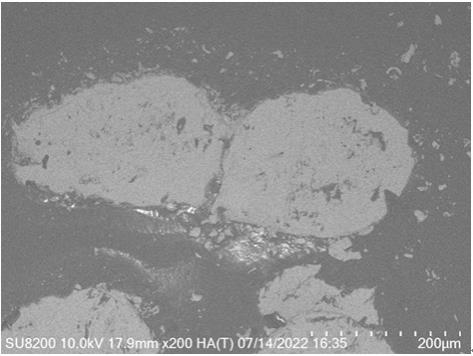
1.本发明属于多孔金属材料领域,具体涉及一种高阻尼高刚度的金属橡胶-高分子复合材料。
背景技术:2.金属橡胶是一种新型的弹性多孔材料,具有超轻结构,优异的吸声、电磁屏蔽以及一定的耗能特性,在航空航天、交通运输以及军事装备等领域得到了大量的运用。金属橡胶仅由金属丝经过绕制而成,由于金属橡胶的多孔特性,使得金属橡胶既具备了高强度又具备了一定的阻尼特性。但金属橡胶阻尼性能偏低,在阻尼性能要求较高的环境下,无法提供持续的高性能。此外一般的金属橡胶刚度较低,需通过增加金属橡胶的密度来提高金属橡胶的刚度,但密度的提升会进一步降低金属橡胶的阻尼性能。因此,现有材料越来越无法同时满足高阻尼高刚度的需求,提高金属橡胶的刚度以及阻尼能力已显得尤为重要。
技术实现要素:3.本发明采用分步真空渗流的方式制备了一种高阻尼高刚度的金属橡胶-高分子复合材料,其可有效拓宽金属橡胶的应用领域。
4.为实现上述目的,本发明采用如下技术方案:一种高阻尼高刚度的金属橡胶-高分子复合材料,其是采用分步真空渗流法,以双组分高分子为填充材料,将其与金属橡胶进行硫化,以制得一种同时具备高阻尼及高刚度特性的金属橡胶-高分子复合材料;其包括如下步骤:1)将金属橡胶进行超声波清洗,以去除金属丝表面的油污以及灰尘;2)将清洗后的金属橡胶进行热处理;3)将双组分高分子搅拌均匀后,将热处理后的金属橡胶浸入双组分高分子中并进行抽真空,待将空气抽除完毕后,对其进行固化处理,得到所述高阻尼高刚度的金属橡胶-高分子复合材料。
5.进一步地,所述双组分高分子为环氧树脂、天然橡胶、硅橡胶等。
6.进一步地,所述金属橡胶的密度在1.6 g/cm3~2.6 g/cm3范围内。
7.进一步地,所述热处理的温度为400℃,时间为3h。
8.进一步地,所述固化处理的温度为50℃,时间为8h。
9.本产品的优点及用途:本发明采用真空渗流的方式将金属橡胶与双组分高分子硫化在一起,进而提出了一种高阻尼以及抗冲击的金属橡胶-高分子复合材料,其具有如下几个优点:1)本发明所采用的真空渗流工艺简单,易于操作,且采用分步真空渗流的方式更容易将高分子材料渗入到金属橡胶内部的空隙中,从而可提高所制备复合材料的一致性及效率。
10.2)本发明所采用的双组分高分子具有可在常温下操作的优点,且双组分高分子的
填充增加了复合材料的刚度,从而极大的提高了复合材料的抗冲击能力。
11.3)本发明利用金属橡胶内部金属丝之间的接触挤压摩擦及金属橡胶与硅橡胶之间的界面摩擦,在不改变金属橡胶内部金属丝之间接触状态的前提下,实现了金属橡胶与高分子的有效结合,进而极大地提高了复合材料的阻尼性能及稳定性。
12.4)为了提高金属橡胶-高分子复合材料的强度,在硫化前需对金属橡胶进行热处理;为了提高金属橡胶的阻尼能力,可采用多股金属丝制备金属橡胶,以增加金属丝之间的摩擦。
13.5)本发明所制备的复合材料相较于泡沫铝等复合材料具有可重复使用的优点,可减小更换的成本。
附图说明
14.图1为实施例所制备金属橡胶-硅橡胶复合材料的显微图。
15.图2为实施例所制备金属橡胶-硅橡胶复合材料的显微局部放大图。
16.图3为实施例所制备金属橡胶-硅橡胶复合材料的面扫频图。
17.图4为实施例所制备金属橡胶-硅橡胶复合材料的低速抗冲击性能测试结果图。
18.图5为不同密度金属橡胶所制备复合材料在低速冲击下的时间-能量图(a)和吸收能量图(b)。
具体实施方式
19.一种高阻尼高刚度的金属橡胶-高分子复合材料,其制备包括如下步骤:1)将金属橡胶进行超声波清洗,以去除金属丝表面的油污以及灰尘;2)将清洗后的金属橡胶于400℃热处理3h;3)将双组分高分子搅拌均匀后,将热处理后的金属橡胶浸入双组分高分子中并进行抽真空,待将空气抽除完毕后,于50℃对其进行固化处理8h,得到所述高阻尼高刚度的金属橡胶-高分子复合材料。
20.所述双组分高分子为环氧树脂、天然橡胶、硅橡胶等。
21.所述金属橡胶的密度在1.6 g/cm
3 ~2.6g/cm3范围内。
22.为了使本发明所述的内容更加便于理解,下面结合具体实施方式对本发明所述的技术方案做进一步的说明,但是本发明不仅限于此。
23.实施例1本实施案例中以双组分硅橡胶为例进行说明。
24.1)使用转用设备将不锈钢丝绕制成螺旋卷,并定螺距拉伸,制备长金属橡胶,将制备好的金属橡胶进行超声波清洗,以去除金属丝表面的油污以及灰尘等杂质;为了提高金属橡胶的阻尼能力,金属橡胶可采用多股金属丝进行制备,以提高金属丝之间的摩擦;2)为了提高金属橡胶-高分子复合材料的强度,在硫化前对金属橡胶进行热处理,热处理温度为400℃左右,时间为3h;3)将双组分硅橡胶以质量比1:1混合并搅拌约1min,使硅橡胶混合均匀,然后将混合后的硅橡胶进行抽真空处理,以去除硅橡胶中的气泡;将抽完气泡的一半硅橡胶倒入内壁均匀涂有脱模剂(如凡士林等)的聚四氟乙烯模具中,然后将热处理后的金属橡胶缓缓的
压入硅橡胶中,并将剩余的硅橡胶倒入到金属橡胶上方,然后在对其进行抽真空,利用真空的压力将硅橡胶填充到金属橡胶的内部孔隙中,直到将金属橡胶中的空气抽除完毕(一般抽30min),再将聚四氟乙烯模具放入到温度箱中,50℃固化8小时,最后将完全固化的金属橡胶-硅橡胶复合材料脱模取出,并用砂轮机打磨掉多余的硅橡胶。
25.在实际的使用过程中,应根据实际的需要的制备不同形状的金属橡胶并选择相对应的聚四氟乙烯模具。但所用聚四氟乙烯模具的高度以金属橡胶长度的2倍为最佳,其内径应比金属橡胶的直径或者边长大0.5mm为最佳。聚四氟乙烯底座与外壳体用螺栓连接。
26.所采用的金属橡胶密度不易过大,应在2.6g/cm3以下为最佳,密度过大的金属橡胶将导致硅橡胶无法充分的渗入到金属丝的空隙中,无法达到较为理想的填充效果;金属橡胶的密度也不宜过小,一般≥1.6g/cm3,密度过小会导致无法成型或承载能力急剧降低。
27.图1、2分别为所制备金属橡胶-硅橡胶复合材料的显微图及局部放大图。从图中可以看出,金属橡胶与硅橡胶的界面结合较好。
28.图3为所制备金属橡胶-硅橡胶复合材料的面扫频图。由图中可以看出其主要含fe和si。
29.图4为所制备金属橡胶-硅橡胶复合材料的低速抗冲击性能测试结果图(按标准astm d7136m进行试验,所用金属橡胶的密度为1.6 g/cm3)。其中,a为金属橡胶和复合材料的位移-力曲线对比图,b、c分别为金属橡胶和复合材料冲击后的凹痕图,c为硅橡胶的时间-位移和能量图,d为硅橡胶冲击后的凹痕图。从图中可以看出所制备的复合材料最大峰值力和最大位移得到了很大的降低,抗冲击性能得到了提高,表明所制备的复合材料具备更高的刚度。
30.实施例2使用密度为1.6 g/cm3、1.8 g/cm3、2.0 g/cm3、2.2 g/cm3、2.4 g/cm3、2.6 g/cm3的金属橡胶,分别按实施例1所述步骤进行制备,获得不同密度的金属橡胶-硅橡胶复合材料。
31.将所得金属橡胶-硅橡胶复合材料在相同冲击能量下进行机械冲击试验,结果见图5。如图5所示,金属橡胶密度较大时,会产生较大的冲击力,且随着金属橡胶密度的增加,其最大位移逐渐减小,最大峰值力逐渐增加,冲击所吸收的能量也越大,综合考虑冲击力和冲击位移,以2.2 g/cm3的金属橡胶密度的冲击力、冲击位移以及吸收的能量均达到较为理想的效果。
32.以上所述仅为本发明的较佳实施例,凡依本发明申请专利范围所做的均等变化与修饰,皆应属本发明的涵盖范围。