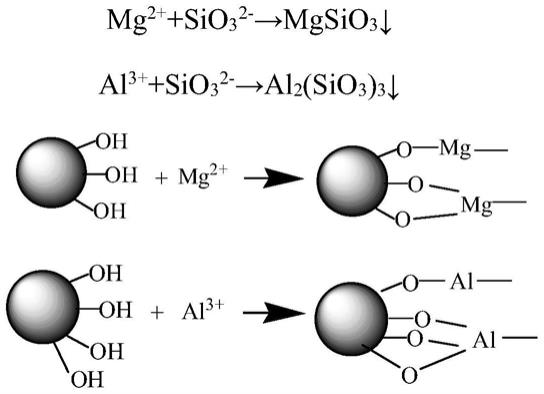
1.本发明属于纳米陶瓷涂料制备领域,具体涉及一种提高纳米陶瓷涂料耐水性的方法。
背景技术:2.纳米陶瓷涂料是以无机纳米氧化物溶胶(硅溶胶或铝溶胶)和硅烷单体为主要原料,通过溶胶-凝胶技术制备的一种新型绿色环保无毒涂料。纳米陶瓷涂料中的无机刚性纳米粒子与硅烷单体水解产物通过缩聚反应结合到一起,使涂层兼具有机涂层和无机涂层的优异特性,广泛应用于地铁内饰、厨房设备、建筑物外墙等领域。纳米陶瓷涂料作为装饰涂层使用寿命可达50年以上,这在很大程度上减少了资源浪费,作为新一代的绿色环保涂料,纳米陶瓷涂料具有广阔的应用前景。
3.其中碱性硅溶胶和硅烷单体在酸性催化剂(通常为乙酸,分子式为 ch3cooh)作用下发生水解反应是制备纳米陶瓷涂料的常规方法。碱性硅溶胶中含有大量的金属离子如na
+
或k
+
,含量约为1000-4000ppm,在涂料固化过程中,na
+
或k
+
会残留在涂层中与ch3coo-或sio
32-结合,生成可溶性盐,纳米陶瓷涂层在受到水的侵蚀时,这些可溶性盐将会发生溶解造成纳米陶瓷涂层出现发白、失去光泽等现象,影响涂层的装饰效果和保护效果。更重要的是,如果涂料中含有大量亲水性的硅羟基基团也会严重影响涂层耐水性,会造成纳米陶瓷涂层出现鼓包、开裂等现象,严重影响涂层的使用寿命。
4.目前,工业常采用传统高温烘烤工艺固化纳米陶瓷涂料,该工艺温度高达 200-300℃,之所以选择此温度,目的是为了促进涂料中的硅羟基发生缩聚反应,提高固化涂层的交联程度,使涂层表现出优异的耐水性。而纳米陶瓷涂料经低温烘烤也可以固化,但是低温烘烤会造成涂料中硅羟基缩聚的程度急剧降低,残留大量的硅羟基亲水基团,在受到水的侵蚀后会导致涂层结构受到破坏,产生鼓包、开裂等问题,严重影响涂层的使用寿命。虽然高温烘烤制备的纳米陶瓷涂层具有优异的耐水性,但是要满足这种高温生产条件需要消耗大量能源,不符合当今节能减排的政策,而低温烘烤工艺虽能满足节能减排的要求,但涂层的耐水性能不佳,因此如何实现低温烘烤固化纳米陶瓷涂料拥有良好的耐水性能成了众多纳米陶瓷涂料生产企业急需解决的技术难题,该难题的解决可实现纳米陶瓷涂料制备技术升级,响应国家倡导的节能减排号召。
技术实现要素:5.针对上述现有技术中存在的问题,本发明的目的是解决低温烘烤固化纳米陶瓷涂料耐水性差的问题,提供一种提高纳米陶瓷涂料耐水性的方法。
6.为实现上述目的,本发明通过以下技术方案来实现:
7.一种提高纳米陶瓷涂料耐水性的方法,包括以下步骤:
8.(1)氢型阳离子交换树脂的制备:将钠型阳离子交换树脂装填入离子交换柱,然后将2-3倍树脂体积的4-6%稀盐酸或稀硫酸流过树脂,控制流速 5-10cm/min,使树脂再生,
进酸完毕后用3-4倍树脂体积的纯水正向淋洗,洗至出水的ph为5-7,得到氢型阳离子交换树脂;
9.(2)酸性纳米硅溶胶的制备:将碱性硅溶胶流过上述步骤(1)中装有氢型阳离子树脂的离子交换柱中,控制流速5-10cm/min,去除碱性硅溶胶水相中游离的金属na
+
、k
+
等金属离子,得到ph为3-4的酸性纳米硅溶胶
10.(3)纳米陶瓷涂料的制备:取步骤(2)中得到的酸性纳米硅溶胶和硅烷单体加入到反应瓶中,在室温条件下,搅拌进行熟化反应4-8h,制得熟化液,然后向熟化液中加入颜填料和多价金属盐固体,经高速搅拌分散均匀得到纳米陶瓷涂料;
11.(4)采用喷涂工艺,将步骤(3)中得到的纳米陶瓷涂料喷涂到经喷砂预处理的铝合金板表面,然后将铝合金板转移至烘箱中经低温烘烤一定时间使涂层固化,制得耐水纳米陶瓷涂层;
12.其中,步骤(3)中所述的多价金属盐固体为硝酸镁、硫酸镁、硝酸铝、硫酸铝、氯化镁、氯化铝中的一种,所述多价金属盐固体加入量根据下面公式(1) 计算:
[0013][0014]a‑‑
加入多价金属盐的质量,g;
[0015]b‑‑
多价金属盐的摩尔质量,g/mol;
[0016]
na‑‑
阿伏伽德罗常数,6.02
×
10
23
个/mol;
[0017]m‑‑
纳米硅溶胶质量,g;
[0018]w‑‑
纳米硅溶胶的固含量,wt%;
[0019]s‑‑
纳米硅溶胶的比表面积,m2/g;
[0020]
4.5
‑‑‑
纳米硅溶胶颗粒表面硅羟基个数,个/nm2。
[0021]
进一步地,步骤(1)所述钠型阳离子交换树脂为强酸性苯乙烯系阳离子树脂、弱酸性丙烯酸系阳离子树脂的混合树脂、强酸性苯乙烯系阳离子树脂和弱酸性丙烯酸系阳离子树脂的混合树脂中的一种。
[0022]
进一步地,步骤(2)所述碱性硅溶胶为钠或钾稳定型,粒径为50-120nm、固含量为30-40%、ph为9-10,含量为1000-4000ppm。
[0023]
进一步地,步骤(3)所述的硅烷单体与硅溶胶的反应质量比为1:(1~4)。
[0024]
进一步地,步骤(3)所述的硅烷单体为甲基三甲氧基硅烷、乙基三甲氧基硅烷、丙基三甲氧基硅烷、苯基三甲氧基硅烷中的至少一种。
[0025]
进一步地,步骤(3)中所述的颜填料为氧化铝粉、钛白粉、氧化铁粉中的一种;颜填料的加入量为熟化液质量的10%。
[0026]
进一步地,步骤(4)所述纳米陶瓷涂料的喷涂厚度为10-100μm,烘烤温度为60-80℃,烘烤时间为60-120min。
[0027]
本发明通过降低纳米陶瓷涂料中可溶性盐的含量,以及通过加入多价金属盐固体,利用多价金属离子与硅羟基发生反应达到“消灭”亲水性硅羟基数量的技术原理,来解决低温烘烤纳米陶瓷涂料耐水性差的问题。首先将碱性纳米硅溶胶经阳离子交换树脂处理,依靠树脂的吸附作用,去除水相中游离的na
+
、k
+
等金属离子,降低制备的纳米陶瓷涂料中可溶性盐的含量;然后再向纳米陶瓷涂料中加入多价金属盐如镁盐、铝盐等,mg
2+
、al
3+
多
价金属离子在低温烘烤过程中能与涂料中的硅羟基发生化学反应生成不溶性的mgsio3或al2(sio3)3,形成
ꢀ‑
si-o-mg或-si-o-al结构,反应如图1所示,涂料中大量亲水性基团硅羟基被多价金属离子结合而“消灭”,提高了涂层耐水性。依靠上述双重作用,使低温烘烤固化的纳米陶瓷涂料也能具有优异的耐水性。
[0028]
纳米陶瓷涂料中的硅羟基主要来源于纳米二氧化硅颗粒表面和硅烷单体水解产物。纳米二氧化硅颗粒小,比表面积大,颗粒表面存在的硅羟基数量约为4.5 个/nm2,二氧化硅颗粒表面结构如图2所示。根据纳米硅溶胶指标参数,纳米硅溶胶中含有的硅羟基数量可根据公式(2)计算:
[0029]
c=4.5mws(2)
[0030]c‑‑
纳米硅溶胶中的硅羟基数量,个;
[0031]m‑‑
纳米硅溶胶质量,g;
[0032]w‑‑
纳米硅溶胶的固含量,wt%;
[0033]s‑‑
纳米硅溶胶的比表面积,m2/g;
[0034]
4.5
‑‑
纳米硅溶胶颗粒表面硅羟基个数,个/nm2;
[0035]
假设要将纳米二氧化硅颗粒表面的硅羟基全部用多价金属离子结合而将其“消灭”,这意味着每个硅羟基都需要和单个金属离子结合,结合公式(1)、 (2)可理论计算出需要加入多价金属盐的质量。
[0036]
然而在实际涂料固化过程中,加入的多价金属盐离子和二氧化硅表面硅羟基不可能完全按1:1结合,也可能存在2-3个硅羟基和单个金属离子结合的情况;硅烷单体水解也会生成硅羟基,这部分硅羟基除自身发生缩聚反应生成链状结构外,还会和硅溶胶颗粒表面硅羟基发生缩聚反应,同时还存在少量硅羟基和多价金属离子结合情况,反应如图3-6所示。由于硅烷水解产物中硅羟基与多价金属离子结合量较少,基本可忽略不计,为了最大程度“消灭”涂料中亲水性硅羟基数量,按照公式(1)计算出的多价金属盐固体量加入到纳米陶瓷涂料中。
[0037]
由于采用以上技术方案,本发明的有益效果包括:
[0038]
(1)获得的酸性纳米二氧化硅溶胶可显著降低涂料体系中的可溶性盐含量,可直接与硅烷单体发生水解反应,不需要额外加入酸性催化剂,降低了voc含量,制备过程更加绿色环保;
[0039]
(2)操作过程简单,纳米陶瓷涂料直接经低温烘烤就能拥有优异的耐水性;
[0040]
(3)节能降耗优势明显,生产成本低,适合工业大规模生产。
附图说明
[0041][0042]
图1为纳米硅溶胶颗粒表面硅羟基与多价金属离子反应示意图;
[0043]
图2为纳米二氧化硅颗粒表面结构示意图;
[0044]
图3为硅烷单体水解反应示意图;
[0045]
图4为硅烷水解产物自身发生缩聚反应示意图;
[0046]
图5为硅烷水解产物自身缩聚以及和纳米硅溶胶颗粒表面硅羟基缩聚反应示意图;
[0047]
图6为硅烷水解产物与多价金属离子反应示意图;
[0048]
图7为实施例1中纳米陶瓷涂层(a为60℃固化、厚度25μm;b为80℃固化、厚度45μm)表面显微镜照片;
[0049]
图8为实施例2中纳米陶瓷涂层(a为60℃固化、厚度25μm;b为80℃固化、厚度45μm)表面显微镜照片;
[0050]
图9为实施例3中纳米陶瓷涂层(a为60℃固化、厚度25μm;b为80℃固化、厚度45μm)表面显微镜照片;
[0051]
图10为实施例4中纳米陶瓷涂层(a为60℃固化、厚度25μm;b为80℃固化、厚度45μm)表面显微镜照片。
[0052]
图11为对比例2中纳米陶瓷涂层(a为60℃固化、厚度25μm;b为80℃固化、厚度45μm)表面显微镜照片;
[0053]
图12为对比例3中纳米陶瓷涂层(a为60℃固化、厚度25μm;b为80℃固化、厚度45μm)表面显微镜照片。
具体实施方式
[0054]
为使本领域技术人员更好地理解本发明的技术方案,下面对本发明作进一步详细描述。但本发明的内容不仅仅局限于下面的实施例。
[0055]
实施例选用钠型阳离子交换树脂为强酸性苯乙烯系阳离子交换树脂,主要交换基团为磺酸基(-so3h),型号为001
×
7型;选用市售85nm碱性纳米硅溶胶,具体指标参数如表1所示:
[0056]
表1碱性纳米硅溶胶产品指标参数
[0057]
粒径85nm固含量40%比表面积48m2/gph9-10稳定剂类型na型钠含量2630ppm
[0058]
实施例1
[0059]
(1)将001
×
7型树脂装填入离子交换柱,然后将2-3倍树脂体积的5%稀盐酸流过树脂,控制酸液流速5-10cm/min,使树脂再生,进酸完毕后用3-4倍树脂体积的纯水正向淋洗,洗至出水的ph为5-7,得到氢型阳离子交换树脂。
[0060]
(2)将85nm碱性纳米硅溶胶流过上述步骤(1)中装有氢型阳离子交换树脂的离子交换柱中,控制流速5-10cm/min,去除水相中游离的na
+
等金属离子,得到ph为3-4的酸性纳米硅溶胶。
[0061]
(3)按照硅烷单体与硅溶胶反应质量比1:1.5,取40g甲基三甲氧基硅烷和步骤(2)中得到的60g酸性纳米硅溶胶直接在三口烧瓶中混合,在室温条件下,搅拌熟化反应6h,制得熟化液,然后向熟化液中加入10g钛白粉,按照公式(1) 计算加入硫酸铝(摩尔质量342g/mol)固体2.95g,经高速分散制得耐水纳米陶瓷涂料。
[0062]
(4)将步骤(3)制得的耐水纳米陶瓷涂料喷涂到经喷砂预处理的铝合金表面,控制
喷涂厚度为20-50μm,然后将喷涂好的铝合金板转移至烘箱中分别在 60℃、80℃条件下烘烤固化60min,制得耐水纳米陶瓷涂层。
[0063]
实施例2
[0064]
(1)将001
×
7型树脂装填入离子交换柱,然后将2-3倍树脂体积的5%稀盐酸流过树脂,控制酸液流速5-10cm/min,使树脂再生,进酸完毕后用3-4倍树脂体积的纯水正向淋洗,洗至出水的ph为5-7,得到氢型阳离子交换树脂。
[0065]
(2)将85nm碱性纳米硅溶胶流过上述步骤(1)中装有氢型阳离子树脂的离子交换柱中,控制流速5-10cm/min,去除纳米硅溶胶水相中游离的na
+
等金属离子,得到ph为3-4的酸性纳米硅溶胶。
[0066]
(3)按照硅烷单体与硅溶胶反应质量比1:1.5,取40g甲基三甲氧基硅烷和步骤(2)中得到的60g酸性纳米硅溶胶直接在三口烧瓶中混合,在室温条件下,搅拌熟化反应6h,制得熟化液,然后向熟化液中加入10g钛白粉,按照公式(1) 计算加入硝酸铝(摩尔质量213g/mol)固体1.83g,经高速分散制得耐水纳米陶瓷涂料。
[0067]
(4)将步骤(3)制得的耐水纳米陶瓷涂料喷涂到经喷砂预处理的铝合金表面,控制喷涂厚度为20-50μm,然后将喷涂好的铝合金板转移至烘箱中分别在 60℃、80℃条件下烘烤固化60min,制得耐水纳米陶瓷涂层。
[0068]
实施例3
[0069]
(1)将001
×
7型树脂装填入离子交换柱,然后将2-3倍树脂体积的5%稀盐酸流过树脂,控制酸液流速5-10cm/min,使树脂再生,进酸完毕后用3-4倍树脂体积的纯水正向淋洗,洗至出水的ph为5-7,得到氢型阳离子交换树脂。
[0070]
(2)将85nm碱性纳米硅溶胶流过上述步骤(1)中装有氢型阳离子交换树脂的离子交换柱中,控制流速5-10cm/min,去除水相中游离的na
+
等金属离子,得到ph为3-4的酸性纳米硅溶胶。
[0071]
(3)按照硅烷单体与硅溶胶质量比1:1,取50g甲基三甲氧基硅烷和步骤(2) 中得到的50g酸性纳米硅溶胶直接在三口烧瓶中混合,在室温条件下,搅拌熟化反应6h,制得熟化液,然后向熟化液中加入10g钛白粉颜,再按照上述公式(1) 计算加入硫酸铝(摩尔质量342g/mol)固体2.46g,经高速分散制得耐水纳米陶瓷涂料。
[0072]
(4)将步骤(3)制得的纳米陶瓷涂料喷涂到经喷砂预处理的铝合金表面,控制喷涂厚度为20-50μm,然后将喷涂好的铝合金板转移至烘箱中分别在60℃、80℃条件下烘烤固化90min,制得耐水纳米陶瓷涂层。
[0073]
实施例4
[0074]
(1)将001
×
7型树脂装填入离子交换柱,然后将2-3倍树脂体积的5%稀盐酸流过树脂,控制酸液流速5-10cm/min,使树脂再生,进酸完毕后用3-4倍树脂体积的纯水正向淋洗,洗至出水的ph为5-7,得到氢型阳离子交换树脂。
[0075]
(2)将85nm碱性纳米硅溶胶流过上述步骤(1)中装有氢型阳离子交换树脂的离子交换柱中,控制流速5-10cm/min,去除水相中游离的na
+
等金属离子,得到ph为3-4的酸性纳米硅溶胶。
[0076]
(3)按照硅烷单体与硅溶胶反应质量比1:4,取20g甲基三甲氧基硅烷和步骤(2)中得到的80g酸性纳米硅溶胶直接在三口烧瓶中混合,在室温条件下,搅拌熟化反应6h,制得
熟化液,然后向熟化液中加入10g钛白粉,再按照上述公式(1)计算加入硝酸镁(摩尔质量148g/mol)固体1.70g,经高速分散制得耐水纳米陶瓷涂料。
[0077]
(4)将步骤(3)制得的纳米陶瓷涂料喷涂到经喷砂预处理的铝合金表面,控制喷涂厚度为20-50μm,然后将喷涂好的铝合金板转移至烘箱中分别在60℃、 80℃条件下烘烤固化120min,制得耐水纳米陶瓷涂层。
[0078]
对比例1
[0079]
制备方法与实施例1相同,其不同之处在于,步骤(2)中碱性硅溶胶未经氢型阳离子交换树脂处理。实验发现,碱性硅溶胶与硅烷单体直接混合后,两者会快速反应形成凝胶状,无法进行喷涂。
[0080]
对比例2
[0081]
制备方法与实施例1相同,其不同之处在于,步骤(2)中碱性硅溶胶用乙酸调节碱性硅溶胶ph为3-4。
[0082]
对比例3
[0083]
制备方法与实施例1相同,其不同之处在于,步骤(3)中不加入硫酸铝固体。
[0084]
对比例4
[0085]
制备方法与实施例1相同,其不同之处在于,步骤(3)中加入硫酸铝固体质量为理论计算值的一倍,实验发现:当加入过量金属盐固体时,会加速纳米陶瓷涂料的缩聚反应速度,导致纳米陶瓷涂料快速凝胶,无法进行喷涂。
[0086]
利用电感耦合等离子发射光谱仪(icp)对实施例中经氢型阳离子交换树脂处理后的酸性纳米硅溶胶中na
+
含量进行测定,检测结果为1382ppm。由结果可以看出,碱性纳米硅溶胶经阳离子交换树脂处理后,体系中na
+
离子含量大约会减少一半,此步骤可显著降低纳米陶瓷涂料中的可溶性盐含量,同时硅溶胶ph 由碱性变为酸性,不需要额外加入酸性催化剂,可直接与硅氧烷单体混合发生水解反应。
[0087]
参照gb/t1733-93《漆膜耐水性测定法》对实施例和对比例中制得纳米陶瓷涂层进行耐水性测定,将纳米陶瓷涂层在恒温23℃去离子水中浸渍24h,并用显微镜观察纳米陶瓷涂层表面变化情况,表面观察结果如图7-12所示。