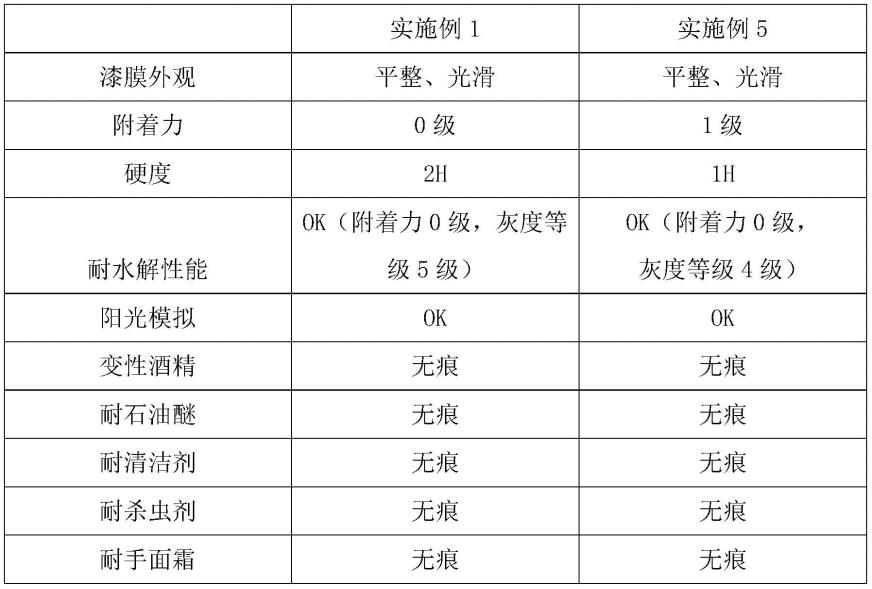
一种汽车内饰用uv色漆涂料及其制备方法
技术领域
1.本发明涉及一种汽车内饰用uv色漆涂料,涉及c09d,具体涉及涂料组合物领域。
背景技术:2.采用紫外光固化涂料可以使涂料瞬间固化,相比于高温固化涂料具有固化时间段,能耗低的优势,运用于汽车内饰的色漆涂料多以深色系为主,但是深色系的紫外固化涂料固化效果不佳,容易出现表干内湿的情况,目前市面上的深色系紫外固化涂料虽然可以实现加色和固化效率并存,但是固化后的色漆涂层耐水解性和耐候性较差,不能满足用于汽车内饰的要求,因此开发一种深色系的紫外固化涂料用于汽车内饰,同时满足挥发性气体voc挥发量少,耐水解耐候性能好的要求至关重要。
3.中国发明专利cn201511025483.1公开了一种紫外光固化涂料及其制备方法,通过对聚氨酯丙烯酸酯进行环己基二甲醇改性,提高了光固化涂料的热稳定性和耐磨性,但是形成的涂料为透明涂料,加入深色色浆后可能导致固化效果下降。中国发明专利cn201410214908.2公开了一种车用uv光固化迷彩伪装涂料及其制备方法,采用4官能度的聚氨酯丙烯酸酯与环氧丙烯酸酯共混形成固化速度快,附着力好的迷彩涂料,但是形成的漆膜硬度过高,手感欠佳不适合汽车内饰使用。
技术实现要素:4.为了提高深色色漆在紫外光下的固化效果,并满足汽车内饰的要求,本发明的第一个方面提供了一种汽车内饰用uv色漆涂料,制备原料以重量份计包括:丙烯酸树脂聚合物55-80份,丙烯酸酯单体5-20份,色浆10-20份,引发剂1-10份,助剂0.1-1份,哑粉1-10份,醋酸酯3-15份。
5.作为一种优选的实施方式,所述制备原料以重量份计包括:丙烯酸树脂聚合物60-75份,丙烯酸酯单体10-18份,色浆10-20份,引发剂2-6份,助剂0.3-1份,哑粉3-6份,醋酸酯5-10份。
6.作为一种优选的实施方式,所述制备原料以重量份计包括:丙烯酸树脂聚合物62份,丙烯酸酯单体11份,色浆13份,引发剂3.8份,助剂0.7份,哑粉4份,醋酸酯5份。
7.作为一种优选的实施方式,所述丙烯酸树脂聚合物选自聚酯丙烯酸脂、聚醚丙烯酸酯、环氧丙烯酸酯、聚氨酯丙烯酸酯中的一种或几种的组合。
8.作为一种优选的实施方式,所述聚氨酯丙烯酸酯为脂肪族聚氨酯丙烯酸酯,优选的,所述脂肪族聚氨酯丙烯酸酯的官能度为3-6。
9.作为一种优选的实施方式,所述脂肪族聚氨酯丙烯酸酯为官能度为5和6的脂肪族聚氨酯丙烯酸酯的组合。
10.作为一种优选的实施方式,所述官能度为5的脂肪族聚氨酯丙烯酸酯在25℃下的粘度为700-2600cps,优选的,所述官能度为5的脂肪族聚氨酯丙烯酸酯固含量为50-60wt%。
11.作为一种优选的实施方式,所述官能度为6的脂肪族聚氨酯丙烯酸酯在60℃下的粘度为55000-75000cps,优选的,所述官能度为6的脂肪族聚氨酯丙烯酸酯固含量为90-100wt%。
12.作为一种优选的实施方式,所述官能度为5和6的脂肪族聚氨酯丙烯酸酯的重量比为(50-60):(10-15)。
13.作为一种优选的实施方式,官能度为5和6的脂肪族聚氨酯丙烯酸酯的重量比为52:10。
14.作为一种优选的实施方式,所述丙烯酸酯单体的官能度为3-6,优选的,所述丙烯酸酯单体选自三羟甲基丙烷三丙烯酸酯、二季戊四醇六丙烯酸树脂、三(2-羟乙基)异氰酸酯三丙烯酸酯、季戊四醇四丙烯酸树脂、二缩季戊四醇五丙烯酸树脂、季戊四醇三丙烯酸树脂、二缩三羟甲基丙烷四丙烯酸酯中的一种或几种的组合。
15.申请人在实验过程中发现,采用官能度为3-6的聚氨酯丙烯酸酯聚合物与丙烯酸单体反应可以使紫外固化丙烯酸涂料在深色体系下仍能保持良好的固化率,使固化后漆膜的上下层呈现均匀的固化状态,猜测可能的原因是:深色体系在紫外固话涂料中深色色浆可以吸收绝大多数的能量,当深色色浆的加入量过多时,大多数的光被深色色浆吸收,导致光引发剂不能吸收能量产生足够的自由基引发反应物的聚合,产生的部分自由基引发上层漆膜固化,底层漆膜未经引发不能发生反应,上层漆膜已经固化成型,底层漆膜中仍然含有大量的低聚物未发生反应,造成漆膜的耐候性和耐磨性下降,申请人发现通过引入官能度为3-6的聚氨酯丙烯酸酯聚合物与丙烯酸单体反应,可以使底层漆膜快速固化,达到良好的固化效果,猜测可能的原因是:官能度为3-6时,丙烯酸单体与丙烯酸预聚物具有多个反应活性位点,使用较少的自由基即可实现快速反应固化,使底层涂料与上层涂料实现同时固化,避免出现外干内湿的情况。
16.作为一种优选的实施方式,所述丙烯酸酯单体为三羟甲基丙烷三丙烯酸酯,二季戊四醇六丙烯酸树脂的组合。
17.作为一种优选的实施方式,所述三羟甲基丙烷三丙烯酸酯和二季戊四醇六丙烯酸树脂的重量比为(5-10):(5-8)。
18.作为一种优选的实施方式,所述三羟甲基丙烷三丙烯酸酯和二季戊四醇六丙烯酸树脂的重量比为6:5。
19.作为一种优选的实施方式,所述引发剂为光引发剂,优选的,所述光引发剂选自苯偶酰类引发剂、烷基苯酮类引发剂、酰基磷氧化物引发剂、二苯甲酮类引发剂中的一种或几种的组合。
20.作为一种优选的实施方式,所述引发剂为烷基苯酮类引发剂,酰基磷氧化物引发剂的组合。
21.作为一种优选的实施方式,所述烷基苯酮类引发剂为1-羟环己基苯酮,所述酰基磷氧化物引发剂为2,4,6-三甲基苯甲酰基-二苯基氧化膦和苯基双(2,4,6-三甲基苯甲酰基)氧化膦的组合。
22.作为一种优选的实施方式,所述1-羟环己基苯酮,2,4,6-三甲基苯甲酰基-二苯基氧化膦和苯基双(2,4,6-三甲基苯甲酰基)氧化膦的重量比为(1-3):(0.5-1):(0.1-0.5)。
23.作为一种优选的实施方式,所述1-羟环己基苯酮,2,4,6-三甲基苯甲酰基-二苯基
氧化膦和苯基双(2,4,6-三甲基苯甲酰基)氧化膦的重量比为3:0.5:0.3。
24.申请人在实验过程中发现,在深色色漆体系中由于深色涂料可以吸收绝大多数的光使引发剂不能有足够的能量产生自由基引发反应,通过1-羟环己基苯酮,2,4,6-三甲基苯甲酰基-二苯基氧化膦和苯基双(2,4,6-三甲基苯甲酰基)氧化膦三种引发剂协同作用,可以使引发剂吸收少部分的光线即可达到良好的固化效果。
25.作为一种优选的实施方式,所述助剂为流平剂,优选的,所述流平剂选自聚醚改性硅氧烷、烷基改性硅氧烷、聚二甲基硅氧烷、聚酯改性硅氧烷、丙烯酸酯性流平剂中的一种或几种的组合。
26.作为一种优选的实施方式,所述流平剂为聚醚改性硅氧烷和烷基改性硅氧烷的组合。
27.作为一种优选的实施方式,所述聚醚改性硅氧烷为流平剂byk333和流平剂tego450,所述烷基改性硅氧烷为流平剂byk306。
28.作为一种优选的实施方式,所述流平剂byk333,流平剂tego450和流平剂byk306的重量比为(0.2-0.5):(0.1-0.3):(0.2-0.5)。
29.作为一种优选的实施方式,所述流平剂byk333,流平剂tego450和流平剂byk306的重量比为0.3:0.1:0.3。
30.申请人在实验过程中发现,采用单一的流平助剂,涂料的流平效果不好,影响漆膜的外观表现,申请人同时采用三种流平剂复配使用,可以大大降低漆膜缩孔的概率,增加漆膜的光泽度,改善流平性能。
31.作为一种优选的实施方式,所述色浆为黑色色浆,所述醋酸酯为醋酸丁酯。
32.本发明的第二个方面提供了一种汽车内饰用uv色漆涂料的制备方法,包括以下步骤:
33.(1)在避光条件下,将丙烯酸树脂聚合物和丙烯酸酯单体依次加入搅拌混合,搅拌10-15min,得混合物a;
34.(2)将醋酸酯在搅拌条件下加入引发剂,溶解后得混合物b;
35.(3)将混合物b过300目筛,在搅拌条件下将混合物b加入混合物a中,得到混合物c;
36.(4)将混合物c在搅拌状态下加入色浆,混匀后再加入助剂,混匀后再加入哑粉,搅拌20-40min,测试黏度和细度,过滤出料即得。
37.作为一种优选的实施方式,所述步骤4得到的产物粘度为在t-2杯测得粘度为20-30秒,依据标准astmd1200-2010;细度为小于20μm。
38.与现有技术相比,本发明具有以下有益效果:
39.(1)本发明所述汽车内饰用uv色漆涂料,通过采用官能度为3-6的脂肪族聚氨酯丙烯酸酯协同作用,增加聚合物体系中的反应活性位点,使其在深色色漆中仍能达到较好的固化效率。
40.(2)本发明所述汽车内饰用uv色漆涂料,通过采用二季戊四醇六丙烯酸树脂和三羟甲基丙烷三丙烯酸酯协同作用与聚氨酯丙烯酸酯发生聚合反应,使漆膜达到较好的硬度,附着力,耐刮性能,并且形成致密的漆膜具有良好的耐水解,耐酒精,耐有机溶剂、耐表面活性剂、耐杀虫剂,耐油脂的效果。
41.(3)本发明所述汽车内饰用uv色漆涂料,通过采用1-羟环己基苯酮,2,4,6-三甲基
2010;细度为19μm。
60.实施例2
61.一种汽车内饰用uv色漆涂料及其制备方法,具体步骤同实施例1,不同点在于所述丙烯酸树脂聚合物为官能度为5和6的脂肪族聚氨酯丙烯酸酯的组合,重量比为52:5。
62.实施例3
63.一种汽车内饰用uv色漆涂料及其制备方法,具体步骤同实施例1,不同点在于所述丙烯酸树脂聚合物为官能度为5和6的脂肪族聚氨酯丙烯酸酯的组合,重量比为52:8。
64.实施例4
65.一种汽车内饰用uv色漆涂料及其制备方法,具体步骤同实施例1,不同点在于所述哑粉的加入量为8重量份。
66.实施例5
67.市售哑光黑漆色漆涂料,购自惠州市百时达化工有限公司。
68.性能测试
69.将实施例1-4制备得到的色漆涂料与uv稀释剂按照重量比调配后,搅拌均匀,用300目过滤网过滤后,喷涂于abs板材上,紫外固化,uv能量为600-800mj/cm2,即可成膜。
70.将实施例5在60℃的环境中烘烤6min,成膜。
71.1.漆膜外观:使用肉眼观察漆膜外观是否平整光滑。
72.2.附着力:依据gb/t 9286-98标准测试涂装后色漆涂料与abs板材的百格附着力。
73.3.硬度:依据gb/t 6739-2006标准测试涂装后色漆涂料的硬度。
74.4.耐水解性能:依据gb/t 1733-1993标准,在90℃,湿度90%rh的环境下放置72h,测试涂装后色漆涂料与abs板材的耐水解性能,灰度等级≥4级,附着力≤2级,即为合格。
75.5.阳光模拟:按照din 75220-d-in1-t标准照射240h,然后进行划格性能测试(依据gb/t 9286-98标准),灰卡等级≥4级且划格性能测试后附着力≤2级,记为ok。
76.6.耐变性酒精性能:质量分数为99%的无水乙醇与质量分数为1%丁酮混合,使用棉球蘸取摩擦10次,观察耐酒精性能。
77.7.耐石油醚性能:用棉球蘸取石油醚摩擦10次,观察耐石油醚性能。
78.8.耐清洁剂性能:用棉球蘸取市售车用清洁剂摩擦10次,观察耐清洁剂性能。
79.9.耐杀虫剂性能:用棉球蘸取市售杀虫剂摩擦10次,观察耐杀虫剂性能。
80.10.耐手面霜:将护手霜涂抹漆膜,静止5-10min后,观察耐手面霜性能。
81.依据上述标准对实施例1和实施例5进行测试,测试结果见表1。由测试结果可得经紫外固化可达到与热固化相同的效果,但是缩短了施工时间,减少了能源消耗。
[0082][0083]
依据上述标准2,3,4,6,10对实施例1-4进行测试,测试结果见表2。
[0084]
表2
[0085]