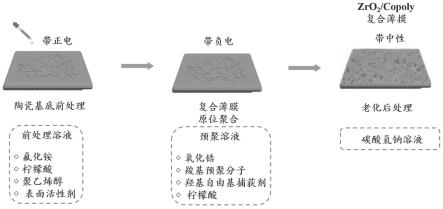
1.本发明涉及建筑技术领域,具体涉及一种氧化锆纳米颗粒羧基高分子复合涂层及其制备方法。
背景技术:2.陶瓷材料在诸多领域存在广泛应用,从电路板、电容器等精细电子元器件到日常生活中十分常见的杯具、卫浴、地砖等,大部分陶瓷材料都具有抗氧化、耐腐蚀、耐高温等性质。一方面,家庭都会采用玻化砖、釉面砖等作为主要的地面建材,不仅因为其稳定的性质,更是由于典雅大方的外观。但当选用瓷砖作为地板时,随之而来的便是陶瓷地面安全问题,如瓷砖需要静态摩擦系数大的陶瓷界面,以预防滑倒摔伤。因此,表面较为粗糙的陶瓷自然更为合适;与之相反,卫生洁具就需要静态摩擦系数小的表面,便于清洁处理,且相对于粗糙表面,光滑表面让人感觉更加舒适美观,许多杯具和装饰设计便是如此。
3.另一方面,卫生洁具等应用场景表面容易残留细菌微生物,尤其是公共卫生间,其问题更为严重。所以在装修时,这些场所多使用生物兼容性差的陶瓷以抑制细菌等的生长与繁殖。但需要注意的是,当考虑到食品安全问题时,餐具和厨具等使用的陶瓷显然需要良好的生物兼容性,以确保环保健康。
4.由此,生活用品领域对陶瓷材料两个物理化学特性要求却存在巨大矛盾性:静态摩擦系数和生物兼容性。在此情况下,各类技术手段被用于调控陶瓷表面的静态摩擦系数和生物兼容性这两个关键物化性质,以满足陶瓷材料在不同生活场景中的应用要求。首先,针对增强陶瓷界面静态摩擦系数(防滑效果),最为常见的技术方法为铺设防滑垫、表面图案粗糙化、物理刻蚀防滑凹槽等;然而,这些常规的陶瓷表面防滑产品和技术仅为名义上止滑效果,在水/油润湿下其摩擦系数就会大打折扣。其次,针对减小陶瓷界面静态摩擦系数(润滑效果),现有的方法主要是通过涂覆液体/固体润滑剂(润滑油、石墨、二硫化钼等);但是上述润滑防滑需要会形成肉眼可见的涂层,并且需要定期清理维护,在生活环境中使用并不现实。此外,对于优化陶瓷表面生物兼容性(生物安全性效果),陶瓷加工过程中通常采取表面抛光打磨、涂覆亲水高分子等手段;然而,上述工艺会在较大程度上影响陶瓷产品的生产成本和使用周期。对于降低陶瓷表面生物兼容性(杀菌效果),通过会采用涂覆季铵盐表面活性剂和金属ag涂层;显而易见,以上方法需要定期维护,且微生物杀灭效果并不稳定。
5.因此,实现陶瓷表面静态摩擦系数与生物兼容性这两个关键物理化学性质可控具有重要的工业价值和社会意义。在此背景下,杜邦、巴斯夫、3m等公司等分别开发了特氟龙、环氧树脂、氟碳表面活性涂层等技术产品,在一定程度上实现了陶瓷界面的静态摩擦系数或生物兼容性可控。但是,上述技术产品价格昂贵、且需要定期的专业维护,大规模普及应用存在较大挑战。更重要的是,以上技术尚未能实现陶瓷表面静态摩擦系数和生物兼容性的双重可控。
技术实现要素:6.(一)解决的技术问题针对现有技术的不足,本发明提供了一种氧化锆纳米颗粒羧基高分子复合涂层及其制备方法,解决背景技术中提出的至少一个技术问题。
7.(二)技术方案本发明采用的技术方案是:第一方面,本发明提供一种氧化锆纳米颗粒羧基高分子复合涂层,所述复合涂层包括如下组合物:羧基预聚高分子10-20份、柠檬酸10-30份、两性离子表面活性剂2-7份、羟基自由基捕获剂0.1-1份,氧化锆纳米颗粒2-10份,去离子水100~150份。
8.优选的,所述复合涂层静态摩擦系数调控范围为0.25-0.68。
9.第二方面,本发明还提供一种氧化锆纳米颗粒羧基高分子复合涂层的制备方法,所述制备方法包括:陶瓷基底的预处理;在预处理后的陶瓷基底上涂覆预聚溶液,静置后得到复合涂层;将0.1-0.5 mol/l碳酸氢钠溶液喷涂至原位聚合后的复合涂层表面,静置后冲洗。
10.所述预聚溶液包括:羧基预聚高分子10-20份、柠檬酸10-30份、两性离子表面活性剂2-7份、羟基自由基捕获剂0.1-1份,氧化锆纳米颗粒2-10份,去离子水100~150份。
11.优选的,所述陶瓷基底的预处理包括:采用预处理溶液洗涤陶瓷基底,静置后冲洗;所述预处理溶液包括:氟化铵0.1~1份、柠檬酸10-30份、硬脂酸钠1~10份、表面活性剂1~5份、聚乙烯醇1~2份、去离子水100~150份。
12.优选的,通过调整预聚溶液中的羧基预聚高分子的浓度、涂覆预聚溶液后的静置时间,以及羧基预聚高分子和氧化锆纳米颗粒的质量比,调控复合涂层的静态摩擦系数。
13.优选的,所述预聚溶液中的羧基预聚高分子的浓度为10-30 g/l。
14.优选的,所述羧基预聚高分子和氧化锆纳米颗粒的质量比为2~10。
15.优选的,所述涂覆预聚溶液后的静置时间为5-10 min。
16.优选的,通过调整氧化锆纳米颗粒的尺寸和形貌,以及氧化锆纳米颗粒和羧基预聚高分子的质量比,调控复合涂层的生物兼容性。
17.优选的,所述氧化锆纳米颗粒的形貌包括球状或者片状。
18.优选的,球状所述氧化锆纳米颗粒的为直径40~80 nm,或者片状多孔氧化锆纳米颗粒的厚度为10~20 nm。
19.优选的,氧化锆纳米颗粒和羧基预聚高分子的质量比0.1~0.5。
20.优选的,所述预处理溶液ph值1.5-3。
21.(三)有益效果本发明提供了一种氧化锆纳米颗粒羧基高分子复合涂层及其制备方法,与现有技
术相比,具有以下有益效果:1、本发明实施例提供的氧化锆纳米颗粒羧基高分子复合涂层及其制备方法,通过含有氧化锆和羧基高分子前驱体的预聚溶液,在可在陶瓷界面上原位聚合形成氧化锆纳米颗粒/羧基高分子复合涂层(zro2/copoly),通过调节氧化锆(zro2)纳米颗粒尺寸和形貌,聚合时间,zro2/羧基高分子比例可在较大范围内调控陶瓷表面静态摩擦系数和生物兼容性。制备的zro2/copoly复合涂层具有较宽的静态摩擦系数可调范围为0.25-0.68,既可作为润滑涂层也可用作防滑涂层。制备的zro2/copoly复合涂层也具有较大的生物兼容性差异,改变制备参数和预聚液组分配比,可以使制备得到的zro2/copoly涂层成为生物安全性涂层也可以成为抗微生物涂层。
附图说明
22.下面结合附图和实施例对本发明作进一步说明:图1为本发明实施例氧化锆纳米颗粒羧基高分子复合涂层在陶瓷表面的制备工艺流程图;图2 为本发明实施例制备得到的具有不同静态摩擦系数与生物兼容性的氧化锆纳米颗粒羧基高分子复合涂层的扫描电镜图;图3为本发明实施例不同预聚溶液浓度,聚合时间,高分子组分比例对静态摩擦系数影响;图4为本发明实施例两种具有不同尺寸和形貌的氧化锆纳米颗粒对其表面小鼠胸腺细胞(4t1细胞)细胞凋影响;图5为本发明实施例不进行老化后处理的氧化锆纳米颗粒羧基高分子复合涂层在高压水流冲刷后的扫描电镜图;图6为本发明实施例的不同基材在不同浓度预聚液下氧化锆纳米颗粒羧基高分子复合涂层的静态摩擦系数影响。
23.具体实施方法为使本发明实施例的目的、技术方案和优点更加清楚,对本发明实施例中的技术方案进行清楚、完整地描述,显然,所描述的实施例是本发明一部分实施例,而不是全部的实施例。基于本发明中的实施例,本领域普通技术人员在没有作出创造性劳动前提下所获得的所有其他实施例,都属于本发明保护的范围。为了更好的理解上述技术方案,下面将结合说明书附图以及具体的实施方式对上述技术方案进行详细的说明:本发明实施例针对陶瓷表面静态摩擦系数和生物兼容性要求多样的重要问题,通过含有氧化锆和羧基高分子前驱体的预聚溶液,在可在陶瓷界面上原位聚合形成氧化锆纳米颗粒羧基高分子复合涂层(zro2/copoly)通过调节氧化锆(zro2)纳米颗粒尺寸和形貌,聚合时间,zro2/羧基高分子比例可在较大范围内调控陶瓷表面静态摩擦系数和生物兼容性。
24.本发明实施例提供了一种氧化锆纳米颗粒羧基高分子复合涂层(zro2/copoly)的制备方法,实质为氧化锆纳米颗粒羧基高分子复合涂层(zro2/copoly)在陶瓷表面的原位聚合制备方法,包括以下步骤:
s1、陶瓷基底的预处理:具体为通过预处理溶液洗涤陶瓷基底,静置等待一段时间,随后用纯净水冲洗;s2、原位聚合:在预处理后的陶瓷基底上涂覆预聚溶液,静置后得到复合涂层;即为氧化锆纳米颗粒羧基高分子复合涂层(zro2/copoly)在陶瓷基底上的原位聚合,将预聚溶液覆至陶瓷基底表面,自然流平,静置等待一段时间得到复合涂层,再用纯净水冲洗陶瓷表面;s3、氧化锆纳米颗粒羧基高分子复合涂层(zro2/copoly)老化后处理,将0.1-0.5 mol/l碳酸氢钠溶液喷涂至zro2copoly复合涂层表面,静置等待一段时间;随后,纯净水冲洗,并自然晾干;以上过程用于加强复合涂层力学性能并使之表面呈现电中性。
25.本发明实施例中,还提供了氧化锆纳米颗粒羧基高分子复合涂层的组合物,即上述预聚溶液,所述预聚溶液包括羧基预聚高分子10-20份、柠檬酸10-30份、两性离子表面活性剂2-7份、羟基自由基捕获剂0.1-1份,氧化锆纳米颗粒2-10份和去离子水100~150份。所述羧基预聚高分子为低聚酰胺类。
26.本发明实施例中,还提供了上述对陶瓷基底进行预处理的预处理液,所述预处理液包括氟化铵0.1份~1份、柠檬酸10-30份、硬脂酸钠1份~10份、表面活性剂1份~5份、聚乙烯醇1份~2份、去离子水100份~150。
27.本发明实施例中通过调节预聚溶液浓度,聚合时间,高分子组分比例这三个条件参数调控形成的zro2/copoly涂层静态摩擦系数,具体的聚合时间为涂覆预聚溶液后的静置时间,高分子组分比例为羧基预聚高分子和氧化锆纳米颗粒的质量比。
28.本发明实施例中通过调节氧化锆(zro2)纳米颗粒的尺寸和形貌,氧化锆组分比例这两个条件参数来实现zro2/copoly涂层生物兼容性调控,其中氧化锆组分比例即为氧化锆纳米颗粒和羧基预聚高分子的质量比。
29.进一步的,上述氧化锆纳米颗粒的形貌包括球状或者片状。
30.上述实施例中,步骤s1中预处理溶液ph值1.5-3之间,处理时间与用量根据陶瓷基底性质不同而变化,预处理溶液的用量40-160 ml/m2,静置等待1-10 min,处理完成后陶瓷基底表面带正电(zeta电位~25-45 mv)。
[0031] zro2/copoly涂层的静态摩擦系数调控:通过改变预聚溶液中的预聚羧基高分子浓度(10-30 g/l),涂覆预聚溶液后的静置时间(5-10 min),羧基预聚高分子和氧化锆纳米颗粒的质量比(预聚羧基高分子/zro2质量比2-10之间),来调控复合涂层的静态摩擦系数。预聚羧基高分子浓度提高,涂覆预聚溶液后的静置时间延长,羧基预聚高分子和氧化锆纳米颗粒的质量比上升均可提升zro2/copoly涂层的静态摩擦系数,静态摩擦系数可调控范围主要集中于0.25-0.68之间; zro2/copoly涂层的生物兼容性调控:通过使用不同尺寸和形貌的zro2纳米颗粒,改变zro2组分比例(zro2/预聚羧基高分子质量比0.1-0.5之间),来调控复合涂层的生物兼容性。分别使用直径40-80 nm球状zro2颗粒与厚度10-20 nm连续片状多孔zro2结构来优化复合涂层生物兼容性,结果表明40-80 nm球状结构的zro2(其组分比例0.1-0.3之间)具有较高的生物安全性;上述实施例步骤s2中,涂层预聚溶液的中氧化锆组分浓度0.01-0.06g/ml,羧基聚合物组分浓度0.05-0.12g/ml,处理时间与用量根据陶瓷基底性质不同而变化,预聚液用量
20-80ml/m2,涂覆预聚溶液后的静置时间为5-15min)。处理完成以后陶瓷基底静态摩擦系数范围为0.25-0.68;生物兼容性由其表面培养小鼠胸腺细胞(4t1细胞)凋亡率表示,培养72小时,细胞凋亡率范围为1%-63%。
[0032]
上述实施例步骤s3中喷涂的碳酸氢钠溶液0.1-0.5 mol/l,处理时间与用量根据陶瓷基底性质不同而变化,碳酸氢钠溶液用量20-80 ml/m2,静置等待1-10 min,处理完成后陶瓷基底表面带少量电荷或电中性(zeta电位-5-5 mv之间)。
[0033]
上述实施例中,不同的陶瓷基材吸水率有差异,按照吸水率不一样,陶瓷可划分为高(>10%)、中(>3%,≤10%)、低吸水率砖(≤3%,),吸水率的差异导致预聚液在基材表面及毛细孔所形成涂层的时间有差异,进而也就决定了预处理的时间和预处理溶液的量不同。不同基材带电能力不同,达到强吸附作用的时间不等,表面带正电是为了静电吸附要求,根据静电吸附原理,只要有带点差异即可吸附,带多容易浪费材料。根据不同吸水率选择的不同基材,不同的基材在不同浓度预聚液下氧化锆纳米颗粒羧基高分子复合涂层的静态摩擦系数影响,具体如图6所示。
[0034]
进一步的,下面结合具体的实施例进行详细说明:实施例1采用预处理清洗、原位聚合、后处理老化三段法在陶瓷基底表面构建氧化锆纳米颗粒/羧基高分子复合涂层(zro2/copoly),如图1所示:第一步,将配置好的预处理清洗通过加压喷淋的方式分散至陶瓷基底表面,用量约为40-160 ml/m2;随后,涂覆有预处理清洗的陶瓷表面静置1-10 min;以zeta作为标准参数,陶瓷表面zeta电位大于等于35 mv时,其表面即可用纯净水冲洗。较高的zeta电位表明其表面带正电,说明前处理洗涤祛除了陶瓷表面沉积碳与其他杂质,使其表面对带负电的羧基高分子可形成较强的相互作用。第二步,将配置好的涂层预聚溶液通过旋转涂膜的方式滴加至瓷砖基体表面,用量约为40-60 ml/m2,光照空气条件下静置5-15min;当陶瓷基体表面固化后,用纯净水冲洗,即得到zro2/copoly复合涂层,如图2所示;第三步,将配置好的将碳酸氢钠溶液加压喷淋至zro2/copoly复合涂层表面,静置1-10 min;以zeta作为标准参数,陶瓷表面zeta电位介于-5-5mv时,其表面纯净水冲洗,并自然晾干;接近电中性的表面可强化zro2/copoly复合涂层力学性能。
[0035]
实施例2制备过程同实施例1,不同仅在于:通过调节预聚溶液浓度(羧基预聚分子浓度为0.05-0.12g/m),聚合时间为5-15分钟,高分子组分比例(zro2/预聚高分子质量比2-10)这三个条件参数可制备得到具有不同形貌结构的多孔结构zro2/copoly复合涂层,实现zro2/copoly涂层在干燥与潮湿条件下的静态摩擦系数0.25-0.68之间,如图3所示。
[0036]
实施例3制备过程同实施例1,不同仅在于:分别使用直径40-80 nm球状zro2颗粒与厚度10-20 nm连续片状多孔zro2结构来优化复合涂层生物兼容性;结果表明实用40-80 nm球状结构的zro2组分,复合涂层具有较高的生物安全性,其表面培养小鼠胸腺细胞(4t1细胞)72小时,细胞凋亡率≤5%;反之,实用10-20 nm连续片状多孔结构zro2,复合涂层生物兼容性能显著先讲,其表面培养小鼠胸腺细胞(4t1细胞)72小时,细胞凋亡率≥52% ,如图4所示。
[0037]
实施例4制备过程同实施例1,不同仅在于:略去s1陶瓷表面清洗程序,所得zro2/copoly复
合涂层不均匀,且易于从陶瓷表面大面积脱落。
[0038]
实施例5制备过程同实施例1,不同仅在于:略去s3的zro2/copoly复合薄膜老化后处理程序, zro2/copoly涂层易于磨损,使用周期大幅下降,如图5所示。
[0039]
本发明实施例由于采用以上技术方案,其具有以下优点:(1)本发明实施例所述的氧化锆纳米颗粒羧基高分子复合涂层(zro2/copoly)制备方法简单,条件温和,易于操作。
[0040]
(2)制备的zro2/copoly复合涂层具有较宽的静态摩擦系数可调范围(0.25-0.68),既可作为润滑涂层也可用作防滑涂层。
[0041]
(3) 制备的zro2/copoly复合涂层也具有较大的生物兼容性差异,改变制备参数和预聚液组分配比,可以使制备得到的zro2/copoly涂层成为生物安全性涂层也可以成为抗微生物涂层。
[0042]
需要说明的是,在本文中,术语“包括”、“包含”或者其任何其他变体意在涵盖非排他性的包含,从而使得包括一系列要素的过程、方法、物品或者设备不仅包括那些要素,而且还包括没有明确列出的其他要素,或者是还包括为这种过程、方法、物品或者设备所固有的要素。
[0043]
以上实施例仅用以说明本发明的技术方案,而非对其限制;尽管参照前述实施例对本发明进行了详细的说明,本领域的普通技术人员应当理解:其依然可以对前述各实施例所记载的技术方案进行修改,或者对其中部分技术特征进行等同替换;而这些修改或者替换,并不使相应技术方案的本质脱离本发明各实施例技术方案的精神和范围。