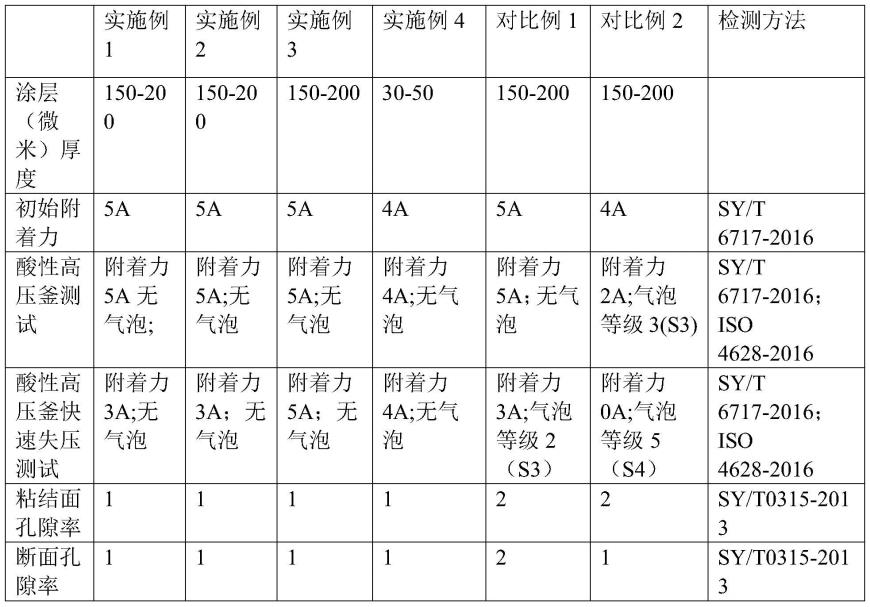
1.本发明涉及石油输送管道防腐技术领域,具体地说,是一种用于油井管酚醛环氧底漆及其制备方法和应用。
背景技术:2.油井管,又称石油专用管,是石油工业的基础,包括套管、油管、钻杆等,统称油井管(octg)。其需在高温高压条件下服役,输送介质常具有腐蚀性,具有较高的腐蚀失效风险。现阶段油井管通常是根据sy/t 6717(2016)以及sy/t0544(2016)标准在其内部涂覆涂料进行防护。按照标准涂层体系由面漆和底漆组成。施工过程中面漆和底漆都需要高温长时间固化,需要至少两个烘房,面漆和底漆整个生产时长超多3个小时,整套方案生产效率较低。
3.中国专利cn201910920990.3公开了一种油井管用高附着力内涂防腐涂料,按质量百分数计由如下组分组成:5-10%丙烯酸树脂、1-2%氨基树脂、25-40%碱式酚醛树脂、8-15%填料、10-15%环氧树脂、2-8%甲基异丁基酮、5-10%乙醇及8-15%丙二醇单甲醚醋酸酯。该发明的油井管用高附着力内涂防腐涂料,具有优异的附着力,满足油井管涂层测试标准sy/t 6717(2016)以及sy/t 0544(2016)中高温高压釜测试。使用该涂料,可延长油井管的使用寿命,但该涂料快速失压的情况下涂层的性能下降明显,涂层孔隙率较高,致密度较低。油井管涂料需要应对严苛的工况,石油采集过程中管道内压力和温度波动巨大,钻杆涂层需要克服以上困难。常规酚醛涂料由于涂层孔隙率较高,涂层致密度相对较低,在快速失压的测试情况下,涂层由于压力的快速降低,吸附在涂层孔隙中的气体急速膨胀,导致涂层结构受损,附着力降低,涂层表面会出现鼓泡开裂的现象,从而失去了对管道的防护作用。甚至会出现涂层大范围脱落的情况,会导致管道堵塞,危害采油设施的安全。
技术实现要素:4.本发明的目的就是为了克服上述现有技术存在的缺陷而提供一种油井管用酚醛环氧底漆及其制备方法和应用,该底漆可以用在严苛腐蚀环境中对金属物件的保护,涂层具有孔隙率低,附着力高,涂层致密,可薄涂等优异特点。
5.本发明的目的可以通过以下技术方案来实现:一种油井管用酚醛环氧底漆,包括质量比为1.75~2.5:1的a和b两组分:
6.其中a组分包括以下质量百分比的组分:
7.酚醛环氧树脂:20-40%;
8.增韧剂:2-5%;
9.受控絮凝型润湿分散剂:0.5-1%;
10.无有机硅聚合物消泡剂:0.2-0.5%;
11.有机膨润土触变剂:0.5-1%;
12.丁酮:5-20%;
13.氧化铁红:5-20%;
14.改性磷酸锌:10-30%;
15.硅烷低聚物:2.5-10%;
16.其中b组分包括以下质量百分比的组分:
17.丁酮:10-30%;
18.乙醇:10-20%;
19.热固性酚醛树脂:50-70%;
20.催化剂:0.01-0.1%;
21.胺络合物固化剂:2-5%。
22.进一步地,所述的酚醛环氧树脂的环氧当量为168-220g/eq。
23.进一步地,所述的增韧剂为反应性聚苯醚树脂,反应基团为酚羟基或乙烯基。
24.进一步地,所述的热固性酚醛树脂的环球法软化点100℃-120℃。
25.进一步地,所述的催化剂为二价无机汞盐,包括碘化汞或硫酸汞。
26.进一步地,所述的胺络合物固化剂为cvc生产的三氯化硼-胺的加成物omicure bc-120。
27.进一步地,所述的硅烷低聚物通过以下方法制得:
28.(1)将质量比为5:1的硅烷偶联剂与去离子水高速搅拌30分钟,得到混合溶液;
29.(2)在混合溶液中加入丁炔二醇,其与去离子水的质量比为2:1,高速搅拌,室温水解24小时,然后70℃水解2小时;
30.(3)取出水解液70℃真空干燥2小时;
31.(4)干燥完成后,加入甲醇,甲醇与去离子水的质量比为1:1,反应2-5h,即得硅烷低聚物产品。
32.进一步地,所述的硅烷偶联剂为kh560。
33.本发明还提供一种油井管用酚醛环氧底漆的制备方法,包括以下步骤:
34.a组分的制备:
35.按照质量百分比将丁酮,酚醛环氧树脂,硅烷低聚物,增韧剂,受控絮凝型润湿分散剂,无有机硅聚合物消泡剂,有机膨润土触变剂混合搅拌至均匀;然后再按照质量比加入改性磷酸锌和氧化铁红,高速分散使温度保持在40-50℃,保温30分钟,冷却后加入砂磨机研磨,研磨至细度小于30微米,用60目滤网过滤包装;
36.b组分制备方法:
37.按照质量百分比加入丁酮,乙醇,热固性酚醛树脂,催化剂,胺络合物固化剂,混合均匀,用60目滤网过滤包装;
38.使用时,将a组分和b组分按质量比1.75~2.5:1混合。
39.本发明还提供一种油井管用酚醛环氧底漆的应用,将所述底漆在室温闪干后,在其表面涂覆液体面漆,与面漆同时固化;
40.或者,将底漆喷涂完成后直接放入烘房加热,达到设定温度后,直接涂覆粉末面漆,然后与粉末面漆同时固化。
41.与现有技术相比,本发明具有以下有益效果:
42.1.本发明配方中使用的高tg的增韧树脂,以及对酚醛树脂反应中缩合产生水分子
的控制,使涂层具有孔隙率低,附着力高,涂层致密,可薄涂等优异特点。
43.2.本发明自制的硅烷低聚物形成了kh560和丁炔二醇的低聚物,聚合物中的kh560作为硅烷偶联剂可以和基材性能较好的附着力,丁炔二醇可以作为缓释剂来使用提高产品的耐腐蚀性能,且其中的三键可以在催化剂的作用下进行水合反应,吸收反应中产生的水分降低了配方的孔隙率。该合成方法制备出含有丁炔二醇的低聚物,同时解决了丁炔二醇水溶性较大的问题,提升了其使用性能。
44.3.本发明选用市售受控絮凝型润湿分散剂,主要物质为低分子量不饱和多元羧酸聚合物,该分散剂可以使颜料受控絮凝,其单个分子可以和多个颜料粒子产生吸引作用,在单个颜料粒子之间形成架桥,从而发展成为三维结构,通过颜料间的可控絮凝,避免了颜料间的浮色,发花,沉降,流挂。
45.4.本发明选用市售的无有机硅聚合物消泡剂:其主要组成为破泡聚合物溶液或聚烯烃溶液,其有优异的抑泡,脱泡性能,由于其不含有机硅因此不会对涂层的层间附着力产生影响;有机膨润土为膨润土晶胞中的阳离子被有机季胺盐取代,形成的改性膨润土,其在高速分散作用下能形成凝胶体,具有良好的剪切触变性提升配方的抗沉淀、防流挂等性能。
46.热固性酚醛树脂本身具有较高的刚性,固化后具有较高的交联密度,可以抵御各种腐蚀介质的侵袭,可以在严苛环境下长期服役。热固性酚醛树脂与环氧树脂的反应过程包括自身的缩合作用和酚羟基与环氧基团的反应,上述的双重固化机理不但保证了产品的耐介质腐蚀性,也保证了底漆和面漆的附着力。酚醛树脂的缩合过程中需要放出水分子,且该反应要在160℃以上才会进行。160℃以上固化的底漆需要长时间冷却才能在表面涂覆面漆,如果为了方便喷涂液体面漆,只让底漆中低温固化,然后管体稍微降温后,在液体面漆不流淌的温度范围内涂覆面漆,此过程羟甲基不完全缩合,会在后续固化产生水分子,影响涂层性能。该种方法所需能耗高,时间长。本技术制备了含有炔基的硅烷水解低聚物,其具有多重积极效果。首先,硅烷偶联剂的主体具有较好的附着力促进剂的作用,其次缩聚形成较长的含硅链段具有增韧的效果,最后聚合物上的炔醇除了起到缓蚀剂的作用外,还可以在二价汞离子的催化下,发生水合反应生成酮,起到了水分子吸收剂的作用。该硅烷低聚物也可以单独用在含有酚醛树脂的涂料配方中,可以显著降低配方孔隙率,提高涂层性能。
47.5.本发明高适应性油井管用酚醛环氧底漆,在室温闪干后,就可以在其表面涂覆液体面漆,其可以和面漆同时固化,节约了生产成本提高了生产效率,也可以在喷涂完成后直接放入烘房加热,钢管达到设定温度后,直接涂覆粉末面漆,然后可以粉末面漆同时固化,该底漆可以同时配套液体和粉末涂料,具有较好的适用范围。
具体实施方式
48.下面对本发明的实施例作详细说明,本实施例在以本发明技术方案为前提下进行实施,给出了详细的实施方式和具体的操作过程,但本发明的保护范围不限于下述的实施例。
49.本发明采用的硅烷低聚物为自制产品,通过以下方法制得:
50.(1)将质量比为5:1的硅烷偶联剂kh560与去离子水高速搅拌30分钟,得到混合溶液;
51.(2)在混合溶液中加入丁炔二醇,其与去离子水的质量比为2:1,高速搅拌,室温水
解24小时,然后70℃水解2小时;
52.(3)取出水解液70℃真空干燥2小时;
53.(4)干燥完成后,加入甲醇,甲醇与去离子水的质量比为1:1,反应3h,即得硅烷低聚物产品。下面各实施例中采用的硅烷低聚物均为通过该方法自制而成。
54.其他原料均为市售产品。
55.实施例1
56.(一)一种油井管用酚醛环氧底漆,包含a组份和b组份,
57.其中,a组份中各原料的重量百分比为:
58.酚醛环氧树脂:20%(选用南亚环氧树脂有限公式生产的nppn-631,环氧当量168-178g/eq);
59.增韧剂:5%(采用沙特基础工业公司(sabic)生产的反应性聚苯醚sa90,反应基团酚羟基);
60.受控絮凝型润湿分散剂:1%(采用德国毕克助剂公司的毕克byk-p105);
61.无有机硅聚合物消泡剂:0.5%(采用德国毕克助剂公司的byk-051n);
62.有机膨润土触变剂:1%(采用海明斯
·
德谦助剂公司的sd-2);
63.丁酮:20%;
64.氧化铁红:20%;
65.改性磷酸锌:30%;
66.硅烷低聚物:2.5%。
67.b组分中各原料的重量百分比为:
68.热固性酚醛树脂50%,采用美国圣莱科特生产的r7522e酚醛树脂,环球法软化点100-120℃;
69.胺络合物固化剂5%,采用美国cvc热固性特种材料公司生产的omicure bc120;
70.催化剂0.01%,采用碘化汞;
71.丁酮30%;
72.乙醇14.99%。
73.(二)上述油井管用酚醛环氧底漆的制备过程如下:
74.a组分制备方法:
75.在容器中按照质量百分比加入丁酮,酚醛环氧树脂,硅烷低聚物,增韧剂,受控絮凝型润湿分散剂,无有机硅聚合物消泡剂,有机膨润土触变剂搅拌至均匀;然后再按照质量比加入改性磷酸锌和氧化铁红,高速分散使温度保持在40-50℃,保温30分钟,冷却后加入砂磨机研磨,研磨至细度小于30微米,用60目滤网过滤包装。
76.b组分制备方法:
77.在容器中按照质量百分比加入丁酮,乙醇,热固性酚醛树脂,催化剂,胺络合物固化剂,混合均匀,用60目滤网过滤包装。
78.(三)使用所述一种油井管用酚醛环氧底漆的使用过程如下
79.1.油井管内部进行喷砂处理;
80.2.a与b按质量比2.5:1进行混合;
81.3.施工中将步骤2得到的混合物进行一次涂覆在步骤1处理后的油井管内部,干膜
厚度30-50微米;
82.4.底漆闪干后,上面涂覆面漆(在本实施例中配套面漆采用采用海隆石油产品技术服务(上海)有限公司生产的tc-3000f);
83.5.涂覆完成的油井管在210℃固化1小时,所得为成品。
84.使用该底漆整个涂覆生产过程仅需加热烘干1小时,节省了生产时间,底面漆可以同时固化,只需要一个烘房,减少了设备投入,整体的生产成本和效率大幅度提高。
85.实施例2
86.(一)一种油井管用酚醛环氧底漆,包含a组份和b组份,
87.所述a组份中各原料的重量百分比为:
88.酚醛环氧树脂:20%,采用南亚环氧树脂有限公司生产的nppn-704,环氧当量200-220g/eq;
89.增韧剂:5%,采用沙特基础工业公司(sabic)生产的反应性聚苯醚sa9000,反应基团乙烯基;
90.受控絮凝型润湿分散剂:1%,采用德国毕克助剂公司的毕克byk-p104;
91.无有机硅聚合物消泡剂:0.5%,采用德国毕克助剂公司的byk-057;
92.有机膨润土触变剂:1%,采用海明斯
·
德谦助剂公司的sd-828;
93.丁酮:20%;
94.氧化铁红:20%;
95.改性磷酸锌:30%;
96.硅烷低聚物:2.5%。
97.所述b组分中各原料的重量百分比为:
98.热固性酚醛树脂50%;采用日本住友化学生产的pr-50731酚醛树脂,环球法软化点120℃;
99.胺络合物固化剂5%
100.催化剂0.01%,采用硫酸汞;
101.丁酮30%;
102.乙醇14.99%。
103.(二)所述油井管用酚醛环氧底漆的制备过程同实施例1;
104.(三)使用所述油井管用酚醛环氧底漆的过程同实施例1。
105.实施例3
106.(一)一种油井管用酚醛环氧底漆,包含a组份和b组份,所述a组份中各原料的重量百分比为:
107.酚醛环氧树脂:40%同实施例1
108.增韧剂:2%同实施例1
109.受控絮凝型润湿分散剂:0.5%同实施例1
110.无有机硅聚合物消泡剂:0.2%同实施例1
111.有机膨润土触变剂:0.5%同实施例1
112.丁酮:10%;
113.氧化铁红:20%;
114.改性磷酸锌:20%;
115.硅烷低聚物:6.8%。
116.所述b组分中各原料的重量百分比为:
117.热固性酚醛树脂70%同实施例1
118.胺络合物固化剂2%同实施例1
119.催化剂0.1%同实施例1
120.丁酮17%;
121.乙醇10.9%。
122.(二)所述油井管用酚醛环氧底漆的制备过程同实施例1。
123.(三)使用所述油井管用酚醛环氧底漆的过程如下:
124.1.油井管内部进行喷砂处理;
125.2.a与b的配比为1.75:1;
126.3.施工中进行一次涂覆,干膜厚度30-50微米;
127.4.底漆闪干后,上面涂覆面漆(在本实施例中配套面漆采用海隆石油产品技术服务(上海)有限公司生产的tc-3000f)。
128.5.涂覆完成的油井管在210℃固化1小时,所得为成品。
129.实施例4
130.一种油井管用酚醛环氧底漆,配方同实施例3
131.油井管用酚醛环氧底漆的制备过程同实施例3
132.使用所述油井管用酚醛环氧底漆的过程如下:
133.1.油井管内部进行喷砂处理;
134.2.a组分与b组分按质量比1.75:1混合;
135.3.施工中将步骤2得到的混合物进行一次涂覆在步骤1处理后的油井管内部,干膜厚度30-50微米;
136.4.底漆210℃干燥1小时(不涂面漆)。
137.对比例1
138.以专利cn110607110b公开涂料涂覆的油井管为对比。
139.对比例2
140.以实施例1中配套面漆直接喷涂。
141.将上述各实施例和对比例制得的油井管材切片进行测试,按照《sy/t6717-2016油管和套管内涂层技术条件》标准进行测试,试片可以通过碱性高压釜测试(液相:naoh溶液,ph值12.5;温度:148℃;压力:70mpa;时间:16h。试件完全浸入液体中,用气体n2加压。实验后涂层无气泡,附着力不降级);无法通过酸性高压釜测试(液相:水、甲苯和煤油(等体积比混合)温度:107℃;压力:35mpa;时间:16h。试件2/3浸入液体中,用气体co2加压。实验后涂层无气泡,附着力不降级),涂层测试完成后,以标准《iso4628色漆和清漆涂层性能试验后的评级方法》,判断表面气泡密度和大小,根据标准,涂层表面有气泡等级为3(s3),数字越大气泡数量越多,气泡体积越大,附着力2a级。由此对比可知,该底漆可以显著提高涂层体系的抗腐蚀性的能力。
142.具体如下:
[0143][0144]
从上表可以看出,本发明的底漆测试结果满足《sy/t 6717-2016油管和套管内涂层技术条件》标准要求,完成测试后涂层附着力不降低,为最高级5a级。本发明的底漆可以用在严苛腐蚀环境中对金属物件的保护,涂层具有孔隙率低,附着力高,涂层致密,可薄涂等优异特点。
[0145]
对比例1所得产品也具有很好的测试性能,可以通过sy/t 6717-2016标准的测试。但是其中的酚醛树脂固化过程中的水分子的释放并没有进行很好的处理,导致产品孔隙率有所升高,在常规测试条件下这一情况并不会影响性能。在快速失压的情况下涂层的性能下降明显。根据sy/t 6717-2016标准,高压釜测试结束后,待温度降低到50℃,再进行泄压,降温过程为4-5h,泄压时釜内压力在5-7mpa之间,该种测试条件与实际工况差别较大。为了检验涂层性能,我们在高压釜测试时间到后,在107℃,35mpa的情况下进行泄压,5分钟内完成,观察涂层表面状态和附着力,评估涂层性能。
[0146]
根据对比,本发明制备的底漆涂料,具有提升涂层配套体系防护能力的作用,底漆和面漆可以同时固化,不必单独配备烘房,提升了生产效率,降低了设备投资。其也可作为单层防护系统使用,具有很好的防护性能。
[0147]
以上所述仅是本发明的优选实施方式,应当指出,对于本技术领域的普通技术人员,在不脱离本发明组份重量百分比的前提下,还可以做出若干改进和润饰,这些改进和润饰也应视为本发明的保护范围。