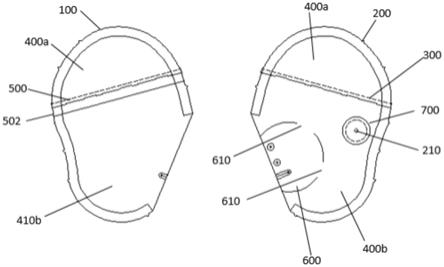
[0001]
本实用新型涉及汽车安全气囊技术领域,尤其涉及一种新型汽车侧面安全气囊气袋结构。
背景技术:[0002]
随着乘用车辆市场普及率的提高,人们对汽车的安全意识也在逐步提高。目前,大部分车辆都已配置安全气囊来提高车辆的安全约束保护能力。与此同时,中国汽车技术研究中心在深入研究和分析国外ncap的基础上,结合我国的汽车标准法规、道路交通实际情况和车型特征,并进行广泛的国内外技术交流和实际试验确定了c-ncap的试验和评分规则。而且在评分办法和试验项目上不断的有所改进。其中《c-ncap管理规则(2021年版)》就预计新增侧面柱碰撞试验及评分规则,侧面柱碰撞的假人指标共计16分。侧面柱碰撞的得分,直接影响整个车型的c-ncap总体得分情况。《c-ncap管理规则(2021年版)》即将引入侧面柱碰撞试验,这将对车身强度及结构设计要求更高,对于侧面气囊的安全性要求更高。
[0003]
由于在侧面柱碰撞试验中车身侵入量及侵入速度较快,首先要求车身强度足够,其次要求侧面气囊的厚度足够大且保护区域足够大,能够覆盖肩、胸、腹和骨盆。然而,在实际的侧面柱碰撞试验过程中,经常出现假人胳膊挤压胸部,导致胸部压缩量超标。为此,本申请人发明了一种新型汽车侧面安全气囊气袋结构,以便在发生侧面柱碰撞时侧面安全气囊能快速起到抬起假人胳膊的作用,从而避免假人胳膊挤压胸部而导致胸部压缩量超标的情况发生。
技术实现要素:[0004]
本实用新型所要解决的技术问题在于:针对现有技术的不足而提供一种新型汽车侧面安全气囊气袋结构,该气袋结构在发生侧面柱碰撞时能够快速抬起假人胳膊,避免假人胳膊挤压胸部而导致胸部压缩量超标的情况发生。
[0005]
本实用新型所要解决的技术问题可以采用如下技术方案来实现:
[0006]
一种新型汽车侧面安全气囊气袋结构,包括乘员侧料片以及车身侧料片,所述车身侧料片上开设有至少一排气孔,所述乘员侧料片的周缘与车身侧料片的周缘相互缝合后构成有一充气腔室;其特征在于,当所述气袋充气展开时,所述乘员侧料片上形成有用于将人体胳膊迅速抬起的台阶状凸包型结构。
[0007]
在本实用新型的一个优选实施例中,所述台阶状凸包型结构通过所述乘员侧料片进行局部折叠而形成。
[0008]
在本实用新型的一个优选实施例中,所述台阶状凸包型通过一片单独的料片折叠成型并缝纫至所述乘员侧料片上。
[0009]
在本实用新型的一个优选实施例中,在所述乘员侧料片与车身侧料片之间设置有分隔条,所述分隔条将所述充气腔室分隔成上充气腔室和下充气腔室,所述分隔条上开设有若干通气孔。
[0010]
在本实用新型的一个优选实施例中,所述若干通气孔沿所述分隔条的长度方向间隔开设在所述分隔条上。
[0011]
在本实用新型的一个优选实施例中,在所述乘员侧料片与车身侧料片之间位于所述下充气腔室内设置有一导气袋体,所述导气袋体上开设有至少一导气孔。
[0012]
在本实用新型的一个优选实施例中,在所述车身侧料片的内侧面上位于每一排气孔处设置有一排气孔加强圈片。
[0013]
由于采用了如上技术方案,本实用新型的有益效果在于:本实用新型通过在乘员侧料片上形成有用于将人体胳膊迅速抬起的台阶状凸包型结构,实现了假人胳膊迅速抬起的功能,这样在侧面柱碰撞试验工况下,该气袋结构可有效的保护假人,避免假人胳膊挤压胸部而导致胸部压缩量超标的失分。此外,本实用新型可以通过带有通气孔的分隔条将气袋的充气腔室分为上、下充气腔室,在发生器点爆产生气体时,气体先迅速的充满下充气腔室,并通过分隔条的通气孔充满上充气腔室,上、下充气腔室之间形成台阶形状,进一步提高假人胳膊迅速抬起的性能。
附图说明
[0014]
为了更清楚地说明本实用新型实施例或现有技术中的技术方案,下面将对实施例或现有技术描述中所需要使用的附图作简单地介绍,显而易见地,下面描述中的附图仅仅是本实用新型的一些实施例,对于本领域普通技术人员来讲,在不付出创造性劳动的前提下,还可以根据这些附图获得其他的附图。
[0015]
图1是本实用新型的实施例1的在展开状态下的结构示意图。
[0016]
图2是本实用新型的实施例1的在展开状态下且台阶状凸包型结构区域折叠后的结构示意图。
[0017]
图3是本实用新型的实施例1的缝制时的结构示意图。
[0018]
图4是本实用新型的实施例1的未采用分隔条在展开状态下的结构示意图。
[0019]
图5是本实用新型在充气展开时与车内乘员接触的侧面效果示意图。
[0020]
图6是本实用新型在充气展开时与车内乘员接触的正面效果示意图。
[0021]
图7是本实用新型的实施例2的带分隔条在开展状态下的结构示意图。
[0022]
图8是本实用新型的实施例2的不带分隔条在开展状态下的结构示意图。
[0023]
图9是本实用新型的实施例3的带分隔条在开展状态下的结构示意图。
[0024]
图10是本实用新型的实施例3的不带分隔条在开展状态下的结构示意图。
[0025]
图11是本实用新型的实施例4的带分隔条在开展状态下的结构示意图。
[0026]
图12是本实用新型的实施例4的不带分隔条在开展状态下的结构示意图。
[0027]
图13是本实用新型的实施例5的带分隔条在开展状态下的结构示意图。
[0028]
图14是本实用新型的实施例5的不带分隔条在开展状态下的结构示意图。
[0029]
图15是本实用新型的实施例6的台阶状凸包型结构的示意图。
[0030]
图16是本实用新型的实施例6的带分隔条在开展状态下的结构示意图。
[0031]
图17是本实用新型的实施例6的不带分隔条在开展状态下的结构示意图。
[0032]
图18是本实用新型的实施例7的带分隔条在开展状态下的结构示意图。
[0033]
图19是本实用新型的实施例7的带分隔条缝制完成台阶状凸包型结构在开展状态
下的结构示意图。
[0034]
图20是本实用新型的实施例7的不带分隔条在开展状态下的结构示意图。
[0035]
图21是本实用新型的实施例7的不带分隔条缝制完成台阶状凸包型结构在开展状态下的结构示意图。
[0036]
图22是本实用新型的实施例8的带分隔条在开展状态下的结构示意图。
具体实施方式
[0037]
为了使本实用新型实现的技术手段、创作特征、达成目的与功效易于明白了解,下面结合具体图示,进一步阐述本实用新型。
[0038]
实施例1:
[0039]
参见图1至图4,图中给出的是一种新型汽车侧面安全气囊气袋结构,包括乘员侧料片100以及车身侧料片200,车身侧料片200上开设一排气孔210。乘员侧料片100的周缘与车身侧料片200的周缘相互缝合后构成有一充气腔室。
[0040]
当气袋充气展开时,乘员侧料片100上形成有用于将人体胳膊迅速抬起的台阶状凸包型结构500。在本实施例中,由图1可看出,乘员侧料片100的外形与车身侧料片200的外形并非左右对称,乘员侧料片100比车身侧料片200多了一折叠区域510。该折叠区域510由折叠线501、502、503围合构成。乘员侧料片100沿折叠线502对折重叠缝制后形成台阶状凸包型结构500,如图2所示,这样使乘员侧料片100的外形与车身侧料片200外形轮廓对称。当气袋充气展开时,乘员侧料片100上形成有台阶状凸包型结构500,台阶状凸包型结构500可用于将人体胳膊迅速抬起的台阶状凸包型结构,实现了假人胳膊迅速抬起的功能,这样在侧面柱碰撞试验工况下,该气袋结构可有效的保护假人,避免假人胳膊挤压胸部而导致胸部压缩量超标的失分。
[0041]
在乘员侧料片100与车身侧料片200之间设置有一分隔条300,分隔条300将上述的充气腔室分隔成上充气腔室400a和下充气腔室400b。在本实施例中,上充气腔室400a的体积小于下充气腔室400b的体积。分隔条300上沿其长度方向间隔开设有若干通气孔(图中未示出),其用于将下充气腔室400b的气体导向至上充气腔室400a。
[0042]
参见图3,乘员侧料片100与车身侧料片200对称缝制在一起形成包型。其中,带有通气孔的分隔条300的两侧分别与乘员侧料片100和车身侧料片200缝合,把该侧面安全气囊包型分成了上充气腔室400a和下充气腔室400b。因分隔条带有一定数量的通气孔,在点爆时气体通过分隔条300的通气孔冲向上腔气室400a。
[0043]
在乘员侧料片100与车身侧料片200之间位于下充气腔室400b内设置有一导气袋体600,导气袋体600将气体发生器(图中未示出)包裹住,导气袋体600上开设有两个导气孔610。导气袋体600在气囊点爆时起到良好的导气作用,能使气体快速充满下充气腔室400b,同时也将折叠区域510迅速充满形成台阶状凸包型结构500。随着台阶状凸包型结构500充满成型,使得乘员胳膊迅速抬起一定高度,这样就可以有效避免假人胳膊挤压胸部导致的胸部压缩量超标的情况发生,具体保护效果示意图如图5和图6所示。
[0044]
本领域的技术人员可以理解的是,上文所述说明的分隔条300的通气孔、导气袋体600的形状及其导气孔610大小、数量均不限定,可依据调整导气袋体600、导气孔尺寸及导气孔数量进行气流大小控制来匹配不同车型设计。另外,本领域技术人员还可以理解的是,
折叠线501、502、503的斜线角度及位置均不限定,在不同碰撞工况和不同车型中,气囊展开位置与乘员胳膊之间的关系可以通过调整折叠线501、502、503的斜线角度及高度,从而适应所侧面柱碰撞时抬起乘员胳膊的工况,折叠线501、502、503围合构成的折叠区域510的宽度也不限定,根据整车空间大小可以适配调整折叠区域510的宽度,从而增厚台阶状凸包型结构500。
[0045]
此外,在车身侧料片200的内侧面上位于排气孔210处设置有一排气孔加强圈片700,提高排气孔210处的结构强度,避免因排气压力过大而导致排气孔处的料片破裂。
[0046]
需说明的是是否要设计分隔条结构,可依据实际整车布置及周边环境灵活调整适配。有分隔条300的气袋整体容积相对略小,分隔条300将气袋分为上充气腔室400a和下充气腔室400b,两个腔室的厚度差异更大,抬手臂效果更好。但另一方面因为分隔条的作用,也导致假人肩部位置充气速度及展开速度会慢一些。不带分隔条300的气袋整体容积略大,单腔保护效果通过下方凸起部分起到迅速抬举胳膊,其它部位如肩部位置的气袋展开时间比较快速。
[0047]
本实施例中不带分隔条在展开状态下的结构示意图见图4所示。与图1相比,图4少了分隔条300部分,其它结构与图1一样。
[0048]
以上显示和描述了本实用新型的基本原理和主要特征和本实用新型的优点。本实用新型主要展现了一种新型侧面安全气囊气袋结构,该结构通过在乘员侧的假人胳膊位置增加一台阶状凸包型结构500来使假人胳膊迅速抬起一定高度,进而避免假人胳膊挤压胸部导致的胸部压缩量超标的情况发生。通过技术人员不断的研究和试验,凸出的台阶形状除上述实现方式以外,还有多种实现方式,另外是否使用分隔条结构也可依据车辆实际环境灵活匹配设计。下面将逐一展现和描述台阶状凸包型结构500和分隔条300的主要组合实现方式。
[0049]
实施例2:
[0050]
本实施例中的气袋结构与实施例1中的气袋结构基本相同,其区别在于:本实施例的台阶状凸包型结构是实施例1中的台阶状凸包型结构的扩展。参见图7,折叠区域510由折叠线504、505、506、507、508围合而成,将折叠线504沿着折叠线505向折叠线506方向折叠,折叠完成后折叠线504、506重合。将折叠线508沿着折叠线507向折叠线506方向折叠,折叠完成后折叠线504、506、508三线重合。这样折叠线504、505、506、507、508围合折叠形成折叠区域510,用来增厚台阶状凸包型结构500。本实施例也可不带分隔条300,如图8所示。
[0051]
实施例3:
[0052]
本实施例中的气袋结构与实施例1中的气袋结构基本相同,其区别在于:参见图9,本实施例的台阶状凸包型结构是通过乘员侧料片100位于下充气腔室400b的部分料片折叠缝制出台阶状凸包型结构。折叠区域510由折叠线509、511、512、513、514围合构成,将折叠线514沿着折叠线513向上方折叠,并与折叠线512重合。折叠线514和折叠线512同时沿着折叠线511向上再次折叠,与折叠线509重叠,这样通过折叠两次形成双层台阶。同理,也可多次折叠形成多层台阶,折叠次数不受限制。本实施例也可不采用分隔条300,如图10所示。
[0053]
实施例4:
[0054]
本实施例中的气袋结构与实施例1中的气袋结构基本相同,其区别在于:本实施例的台阶状凸包型结构是采用纵向折叠方式成型,参见图11,将折叠线515、516、517围合成的
区域沿折叠线517折叠,然后沿着折叠线516折叠使折叠线515、517折叠线重合形成纵向台阶。同理,将折叠线518、519、520围合成的区域沿着折叠线520折叠,然后沿着折叠线519折叠使折叠线518、520重合形成另外一个纵向台阶。本实施例也可不采用分隔条300,如图12所示。
[0055]
实施例5:
[0056]
本实施例中的气袋结构与实施例4中的气袋结构基本相同,其区别在于:本实施例中的台阶状凸包型结构相对于实施例4中的台阶状凸包型结构而言,少了位于右侧的折叠线518、519、520围成的折叠区域,其余实施例4的一样,如图13所示。本实施例也可不采用分隔条300,如图14所示。
[0057]
实施例6:
[0058]
本实施例中的气袋结构与实施例1中的气袋结构基本相同,其区别在于:参见图16,乘员侧料片100和车身侧料片200形状大小左右对称,通过额外一片布料524来缝制成台阶状凸包型结构后再缝制到乘员侧料片100上来实现台阶包型效果。参见图15,布料524具有折叠线521、522、523、524、525,折叠线522沿折叠线521向上折叠,折叠线523沿折叠线524向下折叠形成台阶结构525。然后把台阶结构525缝制在乘员侧料片100上,这样形成台阶状凸包型结构。本实施例也可不采用分隔条,如图17所示。
[0059]
实施例7:
[0060]
本实施例中的气袋结构与实施例1中的气袋结构基本相同,其区别在于:乘员侧料片100分割为100a、100b两部分如图18所示。折叠线527a沿折叠线526向垂直布料方向折叠,折叠线527b沿折叠线528向垂直布料方向折叠,然后折叠线527a、527b缝制在一起形成527,如图19所示气袋缝制完成后的效果。本实施例也可不采用分隔条300,如图20所示,对应的缝制后的效果,如图21所示。
[0061]
实施例8:
[0062]
在实际开发和应用中,台阶状凸包型结构的方案不限于上述实施例的实现方法,可依据实际开发情况灵活变化和改进,比如参见图22,台阶状凸包型结构也可以把乘员侧气袋布料分成两部分100a、100b。将该部分100b沿折叠线528向里侧折叠使折叠线529、530重合缝制成台阶状凸包型结构,气袋缝制完毕后气袋结构示意图同图2。上述实施例2-6中的台阶状凸包型结构也可灵活的将乘员侧料片100分成两片甚至多片布料来实现台阶状凸包型的效果。
[0063]
以上显示和描述了本实用新型的基本原理和主要特征和本实用新型的优点。本行业的技术人员应该了解,本实用新型不受上述实施例的限制,上述实施例和说明书中描述的只是说明本实用新型的原理,在不脱离本实用新型精神和范围的前提下,本实用新型还会有各种变化和改进,这些变化和改进都落入要求保护的本实用新型范围内。本实用新型要求保护范围由所附的权利要求书及其等效物界定。