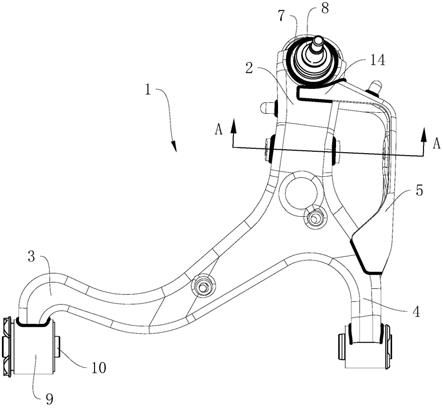
1.本实用新型涉及汽车悬挂技术领域,尤其是涉及一种控制臂。
背景技术:2.目前,三角控制臂是汽车悬架的主要结构,车子行驶在不平路面,轮胎会上下摆动,即靠三角臂的摆动来完成的,轮胎安装在轴头上,轴头通过球头和三角臂连接。具体的,所述三角臂通过其上设置的副车架前连接点铰接套筒与副车架连接,车轮所受到的力量和冲击都是通过副车架前连接点铰接套筒传递到车身上,副车架前连接点铰接套筒是可能发生开裂的部位,也就是如果发生“断轴”事故,很大几率就在副车架前连接点铰接套筒的位置。
3.现有专利授权公告号:cn106041815b《三角控制臂装配组件》公开了一种三角控制臂装配组件,包括臂体、衬套和锥套,所述臂体和所述锥套都设置为预设固定尺寸,所述锥套套接于所述臂体的侧面上,所述衬套套接于所述锥套的外侧面上。
4.上述中的现有技术方案存在以下缺陷:该三角控制臂在使用时,臂体本身将会承受较大的力,可能会使得臂体因无法承受而断裂,从而发生安全事故。
技术实现要素:5.针对现有技术存在的不足,本实用新型的目的是提供一种结构强度更高的控制臂。
6.本实用新型的上述目的是通过以下技术方案得以实现的:
7.一种控制臂,包括控制臂本体,所述控制臂本体包括第一臂体、第二臂体和第三臂体,所述第二臂体和所述第三臂体外端设置有相对齐的橡胶衬套,所述第一臂体外端设置有垂直于所述橡胶衬套的球头,所述第一臂体和所述第三臂体在远离所述第二臂体的一侧设置有辅助臂。
8.通过采用上述技术方案,该控制臂在使用时,控制臂上的第一臂体、第二臂体和第三臂体分别通过球头和橡胶衬套与其他汽车悬挂的零件进行连接,该方案中在第一臂体和第三臂体的侧端设置辅助臂,通过辅助臂提升了第一臂体和第三臂体、第一臂体和第二臂体、第二臂体和第三臂体之间的抗弯折能力,使得该控制臂如被折断将会需要更大的力,通过简单的设置有效的提升了控制臂的结构强度,从而减少控制臂在使用时损坏的风险,进而延长控制臂的使用寿命。
9.本实用新型进一步设置为:所述第一臂体平行于所述橡胶衬套开设有转动孔,所述转动孔内设置有转动管,所述辅助臂中部开设有连接孔,所述转动孔和所述连接孔的轴线重合。
10.通过采用上述技术方案,控制臂在使用时,其本身将会与汽车悬挂系统中的其他零件进行连接,在第一臂体上开设转动孔并在转动孔内设置转动管,使得其他线路或管路可穿过转动管,同时在辅助臂中部开设连接孔,使得线路或管路穿过转动管后可穿过连接
孔,从而方便汽车悬挂系统处零件、线路和管路的排布。
11.本实用新型进一步设置为:所述辅助臂中部截面为波浪状。
12.通过采用上述技术方案,将辅助臂的中部设置为波浪状,使得辅助臂自身中部抗弯折的能力较平直状将会有较大的增强,进而使得安装有辅助臂的控制臂的抗弯折的能力得到进一步的提升,同时是在不增大辅助臂本身体积的情况下,更加实用。
13.本实用新型进一步设置为:所述第一臂体、第二臂体和第三臂体内部中空。
14.通过采用上述技术方案,控制臂本身体积较大,如采用全实心的钢材或铸铁进行制造,将会使得控制臂本体的质量提高,从而提高安装有多个控制臂的汽车的轮上重量,进而将会影响车辆的行驶性能,该方案中将第一臂体、第二臂体和第三臂体内设置成中空状,从而减少控制臂本身的重量,一方面可提高汽车的行驶性能,另一方面方便控制臂的安装。
15.本实用新型进一步设置为:所述控制臂本体为两扇半臂焊接而成。
16.通过采用上述技术方案,在第一臂体、第二臂体和第三臂体内部为中空的状态下,在制造控制臂的过程中将不能采用数控加工,而直接一体铸造而成的话生产成本又比较高,为满足控制臂内部中空又不提高生产成本的情况下,该方案将整个控制臂本体分成两份半臂,将两份一端是中空的半臂单独生产后再焊接,从而形成控制臂,使得控制臂的生产更加方便,成本更低。
17.本实用新型进一步设置为:所述辅助臂在靠近所述第一臂体以及所述第三臂体的两端分叉并分别抵接于所述第一臂体和所述第三臂体的两端面。
18.通过采用上述技术方案,辅助臂的两端进行分叉,使得第一臂体的侧端插接于辅助臂一端的分叉内,而第三臂体的侧端插接于辅助臂的另一分叉内,使得辅助臂不仅可以加强控制臂本身的抗弯折能力,还可以使得焊接在一起的两份半臂更加牢固,从而提升控制臂本身的结构强度。
19.本实用新型进一步设置为:所述辅助臂的两端焊接于所述第一臂体和第三臂体的侧端。
20.通过采用上述技术方案,将辅助臂的两端直接焊接在第一臂体和第三臂体的侧端,一方面使得辅助臂的安装更加牢固,另一方面并不会在第一臂体或第三臂体上进行多余的设置,从而影响控制臂的结构强度或生产效率。
21.本实用新型进一步设置为:所述第一臂体、第二臂体和第三臂体侧端设置有圆弧状倒角,所述控制臂两侧端向所述辅助臂本体一侧弯曲。
22.通过采用上述技术方案,将第一臂体、第二臂体和第三臂体侧端设置圆弧状的倒角,同时将辅助臂的两侧端弯曲,使得控制臂外侧的棱角不存在,避免割伤搬运或安装人员,使得更加安全。
23.综上所述,本实用新型的有益技术效果为:
24.1.通过在第一臂体和第三臂体侧端设置辅助臂,提升了第一臂体和第三臂体、第一臂体和第二臂体、第二臂体和第三臂体之间的抗弯折能力,从而提升了控制臂的结构强度,从而减少控制臂在使用时损坏的风险;
25.2.通过将第一臂体、第二臂体和第三臂体内部设置为中空状,并将辅助臂的截面设置为波浪状,使得在不降低控制臂结构强度的同时,减轻控制臂的重量,从而方便控制臂的运输和安装;
26.3.将控制臂通过两扇半臂焊接而成,从而方便控制臂的制造。
附图说明
27.图1为控制臂的结构示意图;
28.图2为图1的a-a处剖视图,展示转动孔、转动管和连接孔的位置;
29.图3为控制臂的结构示意图,展示辅助臂的结构。
30.图中:1、控制臂本体;2、第一臂体;3、第二臂体;4、第三臂体;5、辅助臂;6、半臂;7、转动座;8、球头;9、安装座;10、橡胶衬套;11、转动孔;12、转动管;13、连接孔;14、连接片。
具体实施方式
31.以下结合附图对本实用新型作进一步详细说明。
32.参见图1,一种控制臂,包括控制臂本体1,控制臂本体1包括第一臂体2、第二臂体3和第三臂体4,第一臂体2和第三臂体4在远离第三臂体4的一侧设置有辅助臂5。
33.参见图1和图2,控制臂是由两份半臂6焊接而成,控制臂本体1的内端为中空状,其壁厚为3.5mm-4.5mm,控制臂的两端面为近乎为平面,控制臂本体的周侧为弧状倒角,使得在拿取控制臂时,控制臂侧端不会存在棱角从而割伤安装人员。
34.第一臂体2在外端焊接有转动座7,该转动座7内转动嵌入球头8。
35.第二臂体3和第三臂体4外端各焊接有一安装座9,两安装座9为圆柱状,两个安装座9的轴线重合,安装座9内过盈插接有橡胶衬套10。
36.第一臂体2的中部开设有转动孔11,转动孔11内过盈插接有转动管12,转动管12的两端穿出转动孔11的两侧,将转动管12直接焊接于转动孔11内,转动管12的轴线与安装座9的轴线相互平行,使得转动管12和安装座9的朝向相同。
37.辅助臂5中部开设有连接孔13,该连接孔13的中心位于转动管12轴线的延长线上,使得汽车悬挂系统中的零件杆、线路和管路可依次穿过连接管和连接孔13。
38.辅助臂5的中部的截面为波浪状,且宽度宽于控制臂的厚度,辅助臂5的厚度大约为4mm,使得辅助臂5的抗弯折能力更强。辅助臂5的侧端向控制臂本体1一侧弯曲。
39.参见图1和图3,辅助臂5的两端分叉形成弧状的连接片14,辅助臂5一端的连接片14抵接至第一臂体2中靠近转动座7的两端面,并进行焊接,辅助臂5另一端的连接片14抵接至第二臂体3靠近安装座9的两端面并进行焊接,使得辅助臂5完全固定于控制臂本体1一侧。
40.本实施例的实施原理为:
41.当生产该控制臂时,先通过铸造的方式将两份半臂6单独生产,然后将两份半臂6对齐至一起后焊接,然后将转动管12插接于转动孔11内,使其两端突出于转动孔11外侧,然后焊接于转动孔11的外侧,此时将辅助臂5置于控制臂一侧,使得辅助臂5两端分叉的连接片14抵接在第一臂体2和第二臂体3的两端面,此时将一根笔直的金属杆穿过转动管12中部然后穿过辅助臂5中部的连接孔13,从而确定辅助臂5的位置准确后,将连接片14与控制臂本体1进行焊接,从而将一完整的控制臂生产完成。
42.本具体实施方式的实施例均为本实用新型的较佳实施例,并非依此限制本实用新型的保护范围,故:凡依本实用新型的结构、形状、原理所做的等效变化,均应涵盖于本实用
新型的保护范围之内。