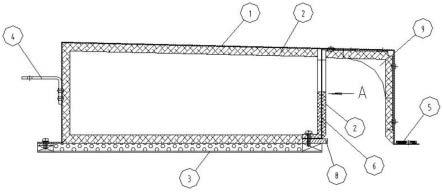
1.本实用新型属于单轨车辆空调系统技术领域,尤其涉及一种风道顶板一体化送风装置。
背景技术:2.在以往城轨车辆项目中,采用风道与顶板分别独立安装的结构,部分项目采用了二次骨架吊装顶板,占用空间较大,安装工艺复杂,重量较高,而单轨车项目需保证客室内顶板高度,受车顶空间限制较大,同时需满足整车减重需求,因此,需要开发一种新型的城轨车辆送风装置。
技术实现要素:3.本实用新型的目的是解决由于受车顶空间限制、风道断面较小而造成风道内风速较大、噪音高、送风不均匀等问题,简化了风道与顶板的安装工序,同时为整车减重做出一定贡献。
4.为达到上述目的,本实用新型提供一种风道顶板一体化送风装置,包括风道主体、隔热材、内顶板组成、风道吊、螺钉安装座、风道隔板、硬质聚氯乙烯板和导流板,所述的风道主体为一体成型且两侧下边缘呈折弯形状的铝板,风道主体内侧粘接隔热材,风道主体靠近客室两侧方向的下边缘折弯铝板上粘接螺钉安装座,风道主体靠近客室中部方向的一侧风道壁上连接风道吊,风道主体靠近客室两侧方向的内部上折弯处铆接圆弧状导流板,风道隔板两侧粘接隔热材组成静压隔板且通过铆钉与风道主体连接,风道隔板与风道主体铆钉连接处粘接硬质聚氯乙烯板,内顶板组成两侧分别与风道主体靠近客室中部方向的一侧下边缘的折弯形状的铝板和风道隔板粘接的硬质聚氯乙烯板通过螺钉连接,风道隔板与风道主体靠近客室两侧方向的风道臂形成一个朝着客室内开口的静压腔,风道隔板与两侧粘接的隔热材组成的静压隔板沿车体长度方向开有送风口,所述的风道吊与车体焊接安装吊连接,螺钉安装座与车体安装用铝型材连接。
5.进一步的,所述的风道吊为3mm厚的铝板,与风道主体通过铆钉连接。
6.进一步的,所述的风道吊与车体焊接安装吊通过螺栓螺母连接,螺钉安装座与车体安装用铝型材通过螺钉现车配钻攻丝安装连接。
7.进一步的,所述的内顶板组成包括上铝板、下铝板、聚氯乙烯泡沫板、钢板、硬质聚氯乙烯板,内顶板组成由上至下依次是上铝板、聚氯乙烯泡沫板和下铝板,内顶板组成与风道主体相连的一侧预埋钢板和硬质聚氯乙烯板,内顶板组成与风道隔板相连的一侧预埋硬质聚氯乙烯板。
8.进一步的,所述的上铝板厚度为0.5mm,下铝板的厚度为1.5mm,钢板厚度为3mm。
9.进一步的,所述的风道主体由厚度为1.2mm的铝板和粘接在铝板上厚度为10mm的隔热材组成,风道隔板两侧粘接的隔热材厚度为5mm。
10.进一步的,所述的风道隔板粘接的硬质聚氯乙烯板厚度为5mm。
11.进一步的,所述的预埋在内顶板组成与风道主体相连的一侧预埋的硬质聚氯乙烯板厚度为7mm,预埋在内顶板组成与风道隔板相连的一侧的硬质聚氯乙烯板厚度为10mm。
12.在现有城轨车辆空间及空调机组技术参数要求下,如采用风道与顶板独立的安装结构,主风道内风速约8.1m/s,且装配时风道与顶板独立安装,工序复杂,风道与顶板安装后重量约400
㎏
。采用风道顶板一体化设计结构,将内顶板做为风道底面,增加了车顶空间的利用率及主风道的通风面积,主风道内风速可降至约6.5m/s,有效改善了风速过高可能造成的送风均匀性差及噪音高等问题;将顶板做为风道底面,风道与顶板的整体重量可降至约320
㎏
,有效降低了整车重量;同时一体化送风装置可将风道与顶板整体同时安装,简化了安装工序,提高装配效率。
附图说明
13.图1为该装置集成示意图;
14.图2为该装置安装断面图;
15.图3为该装置内顶板组成示意图。
16.图中:1-风道主体;2-隔热材;3-内顶板组成;4-风道吊;5-螺钉安装座; 6-风道隔板;7-上铝板;8-硬质聚氯乙烯板;9-导流板;10-下铝板;11
‑ꢀ
聚氯乙烯泡沫板;12-钢板。
具体实施方式
17.设计一种风道顶板一体化送风装置,将车内顶板做为送风装置一部分,风道主体1采用1.2mm的铝板加10mm厚隔热材2,内顶板组成3由上铝板 7、下铝板10、聚氯乙烯泡沫板11、硬质聚氯乙烯板8、钢板12粘接而成,具有隔热性能,并保证安装强度,内顶板组成3各部位粘接后,外部粘接铝板,总厚度为12mm,保证内顶板组成3强度,内顶板组成3及风道主体 1分别制造合格后,将内顶板组成3与风道主体1集成并整体安装,最大化利用车顶空间,保证送风性能及客室顶板高度,简化装配工序,降低整车重量。
18.如图1所示,风道主体1一体成型且两侧下边缘呈折弯形状的铝板,风道主体1靠近客室两侧方向的下边缘铝板上粘接螺钉安装座5,风道主体 1与内顶板组成3集成时,先将风道主体1与隔热材2和螺钉安装座5分别粘接牢固,在风道隔板6两侧粘接隔热材2组成静压隔板后,与风道主体1 通过铆钉连接,并粘接硬质聚氯乙烯板8用于与内顶板组成3集成固定,风道吊4和导流板9与风道主体1通过铆钉连接。
19.如图2所示,工作时,风道隔板6两侧粘接隔热材2组成静压隔板后沿车体长度方向开送风口,风道隔板6与风道主体1靠近客室两侧方向的风道形成一个朝着车内开口的静压腔,通过静压将主风道内空气通过风道隔板6和隔热材2组成的静压隔板开口送至静压腔,再通过导流板9将空气导流经过车顶格栅均匀送至车内。
20.整个送风装置与车体安装时,风道吊4与车体焊接安装吊通过螺栓螺母等紧固件安装连接,螺钉安装座5与车体安装用铝型材通过螺钉现车配钻攻丝安装连接,完成送风装置及顶板一体化的整体安装。
21.如图3所示,在内顶板组成3预埋钢板12及硬质聚氯乙烯板8、硬质聚氯乙烯板8用于内顶板组成3生产完成后与风道主体1和风道隔板6通过螺钉安装集成,保证强度。
技术特征:1.一种风道顶板一体化送风装置,其特征在于:包括风道主体、隔热材、内顶板组成、风道吊、螺钉安装座、风道隔板、硬质聚氯乙烯板和导流板,所述的风道主体为一体成型且两侧下边缘呈折弯形状的铝板,风道主体内侧粘接隔热材,风道主体靠近客室两侧方向的下边缘折弯铝板上粘接螺钉安装座,风道主体靠近客室中部方向的一侧风道壁上连接风道吊,风道主体靠近客室两侧方向的内部上折弯处铆接圆弧状导流板,风道隔板两侧粘接隔热材组成静压隔板且通过铆钉与风道主体连接,风道隔板与风道主体铆钉连接处粘接硬质聚氯乙烯板,内顶板组成两侧分别与风道主体靠近客室中部方向的一侧下边缘的折弯形状的铝板和风道隔板粘接的硬质聚氯乙烯板通过螺钉连接,风道隔板与风道主体靠近客室两侧方向的风道臂形成一个朝着客室内开口的静压腔,风道隔板与两侧粘接的隔热材组成的静压隔板沿车体长度方向开有送风口,所述的风道吊与车体焊接安装吊连接,螺钉安装座与车体安装用铝型材连接。2.根据权利要求1所述的一种风道顶板一体化送风装置,其特征在于:所述的风道吊为3mm厚的铝板,与风道主体通过铆钉连接。3.根据权利要求1所述的一种风道顶板一体化送风装置,其特征在于:所述的风道吊与车体焊接安装吊通过螺栓螺母连接,螺钉安装座与车体安装用铝型材通过螺钉现车配钻攻丝安装连接。4.根据权利要求1所述的一种风道顶板一体化送风装置,其特征在于:所述的内顶板组成包括上铝板、下铝板、聚氯乙烯泡沫板、钢板、硬质聚氯乙烯板,内顶板组成由上至下依次是上铝板、聚氯乙烯泡沫板和下铝板,内顶板组成与风道主体相连的一侧预埋钢板和硬质聚氯乙烯板,内顶板组成与风道隔板相连的一侧预埋硬质聚氯乙烯板。5.根据权利要求4所述的一种风道顶板一体化送风装置,其特征在于:所述的上铝板厚度为0.5mm,下铝板的厚度为1.5mm,钢板厚度为3mm。6.根据权利要求4所述的一种风道顶板一体化送风装置,其特征在于:所述的预埋在内顶板组成与风道主体相连的一侧预埋的硬质聚氯乙烯板厚度为7mm,预埋在内顶板组成与风道隔板相连的一侧的硬质聚氯乙烯板厚度为10mm。7.根据权利要求1所述的一种风道顶板一体化送风装置,其特征在于:所述的风道主体由厚度为1.2mm的铝板和粘接在铝板上厚度为10mm的隔热材组成,风道隔板两侧粘接的隔热材厚度为5mm。8.根据权利要求1所述的一种风道顶板一体化送风装置,其特征在于:所述的风道隔板粘接的硬质聚氯乙烯板厚度为5mm。
技术总结本实用新型提供一种风道顶板一体化送风装置,在现有城轨车辆空间及空调机组技术参数要求下,如采用风道与顶板独立的安装结构,主风道内风速约8.1m/s,且装配时风道与顶板独立安装,工序复杂,风道与顶板安装后重量约400
技术研发人员:许鹏 于文晶 曹先伟
受保护的技术使用者:中车长春轨道客车股份有限公司
技术研发日:2021.04.23
技术公布日:2022/8/16