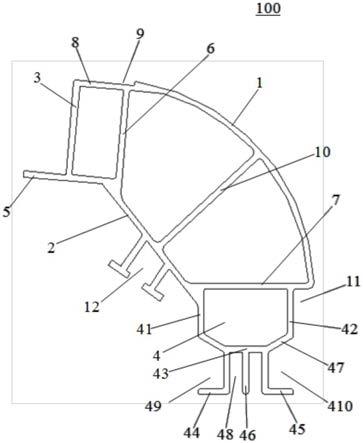
一种高强度的全铝车身顶边梁
【技术领域】
[0001]
本实用新型涉及汽车行业车身用铝型材技术领域,特别是涉及一种高强度的全铝车身顶边梁。
背景技术:[0002]
客车铝合金车身结构具有轻量、环保及可再生等优势,目前已作为一种车身新材料、制造新工艺成为客车领域研究的热点。目前铝车身整车结构已不局限于单一的连接方式,在车身满足强度、刚度及模态设计要求的前提下,更多的通过焊接、螺接及铆接等多种连接方式并用来降低车身质量、提高生产工艺、降低生产成本。顶骨架与侧围骨架在设计过程中往往出现两者连接方式不同,针对于单一连接结构而开发的顶转角无法实现合拢过程中两者的自然过渡。
[0003]
因此,有必要提供一种新的高强度的全铝车身顶边梁来解决上述问题。
技术实现要素:[0004]
本实用新型的主要目的在于提供一种高强度的全铝车身顶边梁,能实现顶骨架与侧围骨架不同连接结构的自然过渡,且能将连接件藏在型材内部,大大提高了美观度。
[0005]
本实用新型通过如下技术方案实现上述目的:一种高强度的全铝车身顶边梁,其包括位于外围的圆弧转角部、位于内围且与所述圆弧转角部相对设置的内支撑部、位于所述圆弧转角部两端连接部位的铆接连接板面和螺栓连接单元、自所述内支撑部垂直于所述铆接连接板面向外伸出的顶横梁支撑板;其通过一板材连接件与一侧围立柱连接、通过一型材连接件与顶横梁铆接,所述板材连接件与所述顶边梁铆接、与所述侧围立柱螺栓连接。
[0006]
进一步的,所述圆弧转角部与所述内支撑部的两端分别设置有连接两者的第一连接板、第二连接板;所述第二连接板水平设置。
[0007]
进一步的,所述螺栓连接单元包括垂直于所述第二连接板向下设置的且相互平行的第三连接板与第四连接板、连接所述第三连接板与所述第四连接板且水平设置的第五连接板、垂直于所述第五连接板向下伸出的且相互平行的第一l型连接部与第二l型连接部、垂直于所述第五连接板向下伸出的限位隔挡板,所述限位隔挡板位于所述第一l型连接部与所述第二l型连接部之间。
[0008]
进一步的,所述顶横梁支撑板表面与所述顶横梁下表面粘接在一起。
[0009]
进一步的,所述第五连接板与所述第三连接板、所述第四连接板在连接处设置有倒角部。
[0010]
进一步的,所述第一l型连接部与所述限位隔挡板之间、所述第二l型连接部与所述限位隔挡板之间围挡形成有限位凹槽。
[0011]
进一步的,所述第一l型连接部与所述倒角部围绕形成第一收纳槽;所述第二l型连接部与所述倒角部围绕形成第二收纳槽。
[0012]
进一步的,所述板材连接件的连接部插入到所述限位凹槽中再通过螺栓锁紧实现
所述板材连接件与所述顶边梁的螺栓连接,且螺栓两端表面以及螺母的外端表面均内陷藏在所述第一收纳槽或所述第二收纳槽中,未伸出所述第三连接板或所述第四连接板的外端表面。
[0013]
进一步的,所述第四连接板的外表面与所述圆弧转角部的端部外表面设置有高度落差,使得所述第四连接板与所述第二连接板之间围挡形成有收纳外围蒙皮的第三收纳槽。
[0014]
进一步的,所述圆弧转角部与所述内支撑部之间还设置有加强支撑筋。
[0015]
与现有技术相比,本实用新型一种高强度的全铝车身顶边梁的有益效果在于:通过顶边梁针对顶盖与侧围不同的型材连接方式,设计与之匹配的连接结构,实现其同时顶盖铆接、与侧围螺接的装配工艺;在满足铝车身侧、顶分片不同型材连接结构的情况下,实现便捷地自然过渡。
【附图说明】
[0016]
图1为本实用新型实施例与侧围立柱、顶横梁连接处的立体结构示意图;
[0017]
图2为本实用新型实施例与顶横梁连接的结构示意图;
[0018]
图3为本实用新型实施例与侧围立柱、顶横梁连接的剖面结构示意图;
[0019]
图4为本实用新型实施例的断面结构示意图;
[0020]
图中数字表示:
[0021]
100顶边梁;200板材连接件;300侧围立柱;400型材连接件;500顶横梁;
[0022]
1圆弧转角部;2内支撑部;3铆接连接板面;
[0023]
4螺栓连接单元,41第三连接板,42第四连接板,43第五连接板,44第一l型连接部,45第二l型连接部,46限位隔挡板,47倒角部,48限位凹槽,49第一收纳槽,410第二收纳槽;
[0024]
5顶横梁支撑板;6第一连接板;7第二连接板;8延伸部;9第四收纳槽; 10加强支撑筋;11第三收纳槽;12风道线束固定螺栓装配槽单元。
【具体实施方式】
[0025]
实施例:
[0026]
请参照图1-图4,本实施例为高强度的全铝车身顶边梁100,其通过一板材连接件200与侧围立柱300连接、通过一型材连接件400与顶横梁500铆接,板材连接件200与顶边梁100铆接、与侧围立柱300螺栓连接,顶边梁100为一体结构且包括位于外围的圆弧转角部1、位于内围且与圆弧转角部1相对设置的内支撑部2、位于圆弧转角部1两端连接部位的铆接连接板面3和螺栓连接单元4、自内支撑部2垂直于铆接连接板面3向外伸出的顶横梁支撑板5。
[0027]
圆弧转角部1与内支撑部2的两端分别设置有连接两者的第一连接板6、第二连接板7。第二连接板7水平设置。
[0028]
铆接连接板面3与顶横梁支撑板5、第一连接板6以及一延伸部8形成一矩形结构。延伸部8上表面与圆弧转角部1端部上表面设置有高度差形成第四收纳槽9,该第四收纳槽9中可以设置顶盖蒙皮,使得顶盖蒙皮表面与圆弧转角部1的外围表面无缝对接完美弧度过渡。顶横梁支撑板5表面与顶横梁下表面采用粘接工艺实现位置固定,提高连接强度和整车
的刚度。
[0029]
螺栓连接单元4包括垂直于第二连接板7向下设置的且相互平行的第三连接板41与第四连接板42、连接第三连接板41与第四连接板42且水平设置的第五连接板43、垂直于第五连接板43向下伸出的且相互平行的第一l型连接部44与第二l型连接部45、垂直于第五连接板43向下伸出的限位隔挡板46,限位隔挡板46位于第一l型连接部44与第二l型连接部45之间。
[0030]
第五连接板43与第三连接板41、第四连接板42在连接处设置有倒角部 47。
[0031]
第一l型连接部44与限位隔挡板46之间、第二l型连接部45与限位隔挡板46之间围挡形成有限位凹槽48。第一l型连接部44与倒角部47围绕形成第一收纳槽49;第二l型连接部45与倒角部47围绕形成第二收纳槽410。
[0032]
板材连接件200的连接部插入到限位凹槽48中再通过螺栓锁紧实现板材连接件200与顶边梁100的螺栓连接,且螺栓两端表面以及螺母的外端表面均内陷藏在第一收纳槽49或第二收纳槽410中,未伸出第三连接板41或第四连接板42的外端表面,提高整体美观性和连接的整体性,提高了整体强度。
[0033]
第四连接板42的外表面与圆弧转角部1的端部外表面设置有高度落差,使得第四连接板42与第二连接板7之间围挡形成有收纳外围蒙皮的第三收纳槽11,通过第三收纳槽11的设置,可以使得侧围蒙皮外表面与顶边梁100 的圆弧转角部1表面无缝对接形成完美的圆弧过渡,提高其美观性;且侧围蒙皮无需开设避让孔,提高了蒙皮整体性,从而提高了强度和密封防水性能。
[0034]
圆弧转角部1与内支撑部2之间还设置有加强支撑筋10,提高顶边梁100 刚度。
[0035]
内支撑部2上向外延伸设置有风道线束固定螺栓装配槽单元12。
[0036]
本实施例高强度的全铝车身顶边梁100在开发设计过程中根据顶盖和侧围不同的连接方式,设计与之匹配的连接结构,与顶盖连接的设计为铆接结构,与侧围连接的设计为螺栓连接结构;在装配过程中,顶边梁的铆接连接板面通过型材连接件和顶横梁铆接在一起;顶横梁和顶横梁支撑板贴合,采用粘接工艺提高连接强度和整车的刚度;顶边梁螺栓连接单元通过板材连接件用螺栓与侧围窗立柱连接;圆弧转角部与整车外龙门线贴合;实现顶骨架与侧围骨架不同连接结构的自然过渡,将连接件藏在型材内部,大大提高了美观度。
[0037]
以上所述的仅是本实用新型的一些实施方式。对于本领域的普通技术人员来说,在不脱离本实用新型创造构思的前提下,还可以做出若干变形和改进,这些都属于本实用新型的保护范围。