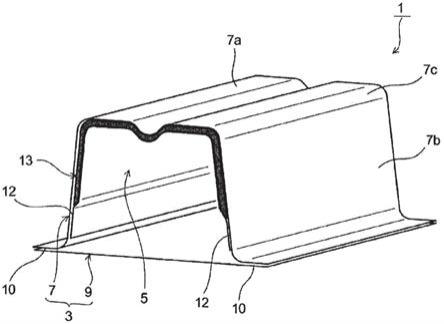
deformation)的刚性,由此能够抑制该汽车部件的变形。
11.但是,对于如前纵梁(front side member)或碰撞盒(crash box)那样,在从汽车的前方或后方输入碰撞载荷(crashworthiness load)而发生轴向压溃时呈波纹状(bellows-shaped)压曲变形来吸收碰撞能量的汽车部件,即使应用在该汽车部件的内部仅填充发泡填充材料或发泡体的技术,也存在难以提高碰撞能量的吸收性这样的课题。另外,会产生无间隙地填充发泡树脂这样的追加工序,存在汽车部件制造的生产成本上升这样的问题。
12.本发明是为了解决上述那样的课题而完成的,其目的在于提供一种汽车用碰撞能量吸收部件、该汽车用碰撞能量吸收部件的制造方法,在如前纵梁或碰撞盒那样从车身的前方或后方输入碰撞载荷而发生轴向压溃时,碰撞能量的吸收效果提高,并且能够减少追加的生产工序从而生产成本不会大幅上升。
13.用于解决课题的手段
14.本发明人对解决上述课题的方法进行了深入研究,得到如下见解:通过有效利用在汽车制造的涂装工序(coating process)中通常使用的电沉积涂料(electrodeposition paint),不需要无间隙地填充发泡树脂等填充材料这样的追加工序就能够提高碰撞能量的吸收效果。本发明是基于这样的见解而完成的,基本上由以下结构构成。
15.(1)本发明所涉及的汽车用碰撞能量吸收部件设置于车身的前部或后部,在从该车身的前方或后方输入了碰撞载荷时发生轴向压溃而吸收碰撞能量,其中,具有:筒状构件(tubular member),使用具有顶板部和纵壁部(side-wall portion)的帽形截面构件而形成;涂膜形成构件(coating parts),在所述顶板部和所述纵壁部的内表面中的包含将所述顶板部与所述纵壁部连结的角部(corner portion)的部分,形成与所述顶板部内表面、所述纵壁部内表面及所述角部内表面隔开0.2mm以上且3mm以下的间隙(gap)而配设的涂膜,并由强度比所述筒状构件低的材质构成;及涂膜(coating film),形成于所述间隙并由电沉积涂料形成。
16.(2)本发明涉及的汽车用碰撞能量吸收部件的制造方法是如下汽车用碰撞能量吸收部件的制造方法,该汽车用碰撞能量吸收部件设置于车身的前部或后部,在从该车身的前方或后方输入了碰撞载荷时发生轴向压溃而吸收碰撞能量,其中,包括:部件制造工序,制造涂装前部件,该涂装前部件具有:筒状构件,使用具有顶板部和纵壁部的帽形截面构件而形成;及涂膜形成构件,在该筒状构件的内表面中的包含将所述顶板部与所述纵壁部连结的角部的部分,形成与所述顶板部内表面、所述纵壁部内表面及所述角部内表面隔开0.2mm以上且3mm以下的间隙而配设的涂膜,并由强度比所述筒状构件低的材质(material)构成;及涂膜形成工序,在将所述涂装前部件安装到所述车身的状态下,在包含所述间隙的部件表面,通过基于电沉积涂装(electrodeposition coating)的电沉积工序(electrodeposition coating process)形成涂料层,并通过接下来的涂料烘烤处理(paint baking treatment)使所述涂料层(coating layer)热固化(thermosetting)而形成涂膜。
17.发明效果
18.根据本发明,在从车身的前方或后方输入了碰撞载荷时发生轴向压溃而吸收碰撞能量的筒状构件发生压缩变形(compressive deformation)的过程中,能够提高该筒状构
件的压曲强度(buckling strength),并且能够不降低该筒状构件的变形阻力(deformation resistance)地呈波纹状发生压曲变形(buckling deformation),并且,能够防止所述筒状构件的所述压曲变形中的弯曲部(bending portion)的断裂,能够大幅提高碰撞能量的吸收性能。另外,能够吸收来自汽车发动机的振动或在汽车行驶(driving automobile)时从各方向输入到车身(automotive frame)的振动(vibration),提高减振性(vibration-damping properties)。而且,在本发明中,由于具有涂膜形成构件,因此能够在汽车制造的涂装工序中通常进行的电沉积涂装中形成作为目标的厚度的涂膜,由此能够直接利用以往的汽车制造生产线进行制造。
附图说明
19.图1是表示本发明的实施方式1所涉及的汽车用碰撞能量吸收部件的立体图。
20.图2是表示在本发明的实施方式1所涉及的汽车用碰撞能量吸收部件形成涂膜之前的状态的立体图。
21.图3是表示钢板(steel sheets)的拉伸强度(tensile strength)水平同钢板的断裂极限弯曲半径(fracture limit for bending radius)与板厚(thickness)之比之间的关系的图表。
22.图4是本发明的实施方式2所涉及的汽车用碰撞能量吸收部件的制造方法的说明图。
23.图5是表示本发明所涉及的汽车用碰撞能量吸收部件的其他方式的图(其1)。
24.图6是表示本发明所涉及的汽车用碰撞能量吸收部件的其他方式的图(其2)。
25.图7是表示本发明所涉及的汽车用碰撞能量吸收部件的其他方式的图(其3)。
26.图8是表示本发明所涉及的汽车用碰撞能量吸收部件的其他方式的图(其4)。
27.图9是表示本发明所涉及的汽车用碰撞能量吸收部件的其他方式的图(其5)。
28.图10是说明实施例中的轴向压溃试验(axial crush test)方法的图。
29.图11是说明实施例中的冲击振动试验(impact vibration test)方法的图。
30.图12是表示在基于实施例中的冲击振动试验方法的振动特性(vibration characteristics)评价中作为固有振动频率(character frequency)计算的对象的振动模式(vibration mode)的图。
31.图13是表示在实施例中作为发明例使用的试验体的构造的图。
32.图14是表示在实施例中作为比较例使用的试验体的构造的图。
具体实施方式
33.[实施方式1]
[0034]
以下,对本实施方式所涉及的汽车用碰撞能量吸收部件进行说明。另外,在本说明书和附图中,对于具有实质上相同的功能和构造的元件,通过标注相同的标号来省略重复说明。
[0035]
本实施方式所涉及的汽车用碰撞能量吸收部件1(图1)设置于车身的前部或后部,在从该车身的前方或后方输入了碰撞载荷时发生轴向压溃而吸收碰撞能量,在安装到所述车身的状态下,在表面形成由电沉积涂料形成的涂料层,并通过涂料烘烤处理使所述涂料
层固化,形成涂膜。如图1所示,在使用帽形截面构件(hat-shaped section part)而形成的筒状构件3的内表面侧设置涂膜形成构件5,在帽形截面构件与涂膜形成构件5之间的间隙形成有由电沉积涂料形成的涂膜13。图2表示汽车用碰撞能量吸收部件1的电沉积涂装前的状态(以下称为涂装前部件2)。以下,基于图1及图2对各构件进行说明。
[0036]
《筒状构件》
[0037]
筒状构件3由钢板等金属板(metal sheet)构成,通过帽形截面形状的外部件7(outer parts)(本发明中的帽形截面构件)与平板状的内部件9(inner parts)在接合部10接合而形成为筒状,该外部件7具有顶板部7a、纵壁部7b及将顶板部7a与纵壁部7b相连的角部7c。在具有这样的筒状构件3的汽车用碰撞能量吸收部件1中,在向汽车用碰撞能量吸收部件1的轴向前端输入碰撞载荷,筒状构件3超过压曲强度而发生轴向压溃的过程中,通过使筒状构件3呈波纹状反复发生压曲变形来吸收碰撞能量。
[0038]
《涂膜形成构件》
[0039]
涂膜形成构件5由钢板等金属板构成,以在外部件7的内表面侧且包含角部7c的部分形成0.2mm以上且3mm以下的间隙11的方式而配置,并在接合部12通过点焊(spot welding)等而接合(joining)(参照图2)。涂膜形成构件5可以遍及外部件7的轴向的全长而设置,但也可以仅设置于汽车用碰撞能量吸收部件1的想要使其发生波纹变形的范围。例如在将汽车用碰撞能量吸收部件1设置于车身的前部,并想要使从前端到轴向中间的范围发生波纹变形的情况下,只要在外部件7的该范围设置涂膜形成构件5即可。并且,为了提高变形强度(deformation strength),外部件7的未设置涂膜形成构件5的部分、例如从轴向的中间到后端的范围只要形成例如沿轴向延伸的凸圆线脚形状(bead-shape)即可。
[0040]
在进行作为汽车制造的一般的涂装工序之一的电沉积涂装时,在该间隙11形成由电沉积涂料形成的涂膜13(参照图1)。作为电沉积涂料的种类,例如可举出聚氨酯类(polyurethane)阳离子电沉积涂料(cationic electrodeposition paint)、环氧类(epoxy)阳离子电沉积涂料、聚氨酯(urethane)阳离子电沉积涂料、丙烯酸类(acrylic)阴离子电沉积涂料、氟树脂(fluororesin)电沉积涂料等。通过后述的实施方式2对电沉积涂装进行具体说明。
[0041]
通常在进行电沉积涂装时,在钢板的表面形成0.05mm左右的涂膜,但在本实施方式中,通过在涂装前部件2的外部件7的内表面侧设置涂膜形成构件5,电沉积涂料进入间隙11而形成涂料层,通过对其进行热处理,能够形成如图1所示的具有0.2mm以上且3mm以下的厚度的涂膜13。以下对通过形成这样的涂膜13来提高汽车用碰撞能量吸收部件1的碰撞能量吸收效果的理由进行说明。
[0042]
在具有由钢板等金属板形成的筒状构件的汽车用碰撞能量吸收部件中,在向该汽车用碰撞能量吸收部件的轴向前端输入碰撞载荷,该筒状构件超过压曲强度而发生轴向压溃的过程中,通过使该筒状构件呈波纹状反复发生压曲变形来吸收碰撞能量。
[0043]
但是,由于波纹状的弯曲部分成为金属板固有的小的弯曲半径,所以应力(stress)集中于弯曲部分的外表面而容易产生裂纹(fracture),如果在轴向压溃的过程中在弯曲部分产生裂纹,则碰撞能量的吸收效果显著降低。因此,为了提高碰撞能量的吸收效果,需要防止在呈波纹状发生压曲变形的筒状构件产生的裂纹。
[0044]
特别是近年来,以兼顾碰撞特性和轻量化为目的而由汽车部件采用的高强度钢板
与以往的强度的钢板相比,延展性(elongation)较小。表1和图3所示的钢板拉伸强度水平与钢板的断裂极限弯曲半径r/板厚t之间的关系(参照下述的参考文献1)示出了在相同板厚的情况下,钢板的拉伸强度ts越大,即使为大的弯曲半径也容易发生断裂(fracture)。即,如果使用了高强度钢板的汽车用碰撞能量吸收部件呈波纹状发生压曲变形,则随着钢板强度的增加,在波纹形状的弯曲前端容易产生裂纹,这也成为阻碍为了汽车车身的轻量化而推进钢板的进一步高强度化的主要原因。(参考文献1)长谷川浩平、金子真次郎、濑户一洋、“有助于座舱周围的车身部件的轻量化的高强度冷轧/合金化熔融镀锌(ga)钢板(对应日文:
キヤビン
周
りの
車体部品
の
軽量化
に
貢献
する
高强度冷間压延
·
合金化溶融亜鉛
めっき
(ga)鋼板)”、jfe技术报告、no.30(2012年8月)、p.6-12.
[0045]
(表1)
[0046]
钢板强度等级ts[mpa]r/t[-]780mpa级810小于1.0980mpa级10201.01180mpa级12101.51320mpa级13302.01470mpa级15102.5
[0047]
与此相对,本发明中,在碰撞时筒状构件3呈波纹形状发生压曲变形时,在变形为凸状的弯曲部中,通过使物体介于并夹持在金属板与金属板之间而进行压缩(compression),由此增大凸状的弯曲部的弯曲半径,防止弯曲前端的破裂。在此,作为介于金属板与金属板之间的物体,为了避免部件的重量增加而优选尽可能轻的物体,而且,优选不是如现有例的发泡树脂(foam resin)等那样在部件制造中需要追加材料或工序的物体,而是能够直接利用现有的汽车制造生产线进行制造的物体。因此,本发明有效利用在汽车制造中通常进行的电沉积涂装的涂料。
[0048]
另外,筒状构件3中吸收碰撞能量的能力高的部位是将顶板部7a与纵壁部7b相连的角部7c,但角部7c也是在冲压成形外部件7时最容易受到加工而发生加工硬化(work hardening)的部位,延展性因加工硬化而降低。因此,角部7c的波纹形状的弯曲部分是特别容易产生裂纹的部位。
[0049]
因此,在本发明中,通过在外部件7的包含角部7c的内表面侧设置涂膜形成构件5,使得在涂膜形成构件5与该内表面之间产生0.2mm到3mm的间隙11,从而能够在电沉积涂装时使电沉积涂料进入间隙11而形成具有规定厚度的涂料层。涂料层在电沉积涂装的烘烤工序中固化而固着于间隙11,由此成为涂膜13。本实施方式所涉及的汽车用碰撞能量吸收部件1中,在碰撞时筒状构件3发生了压曲变形时,通过涂膜13介于波纹形状的凸状弯曲部的内侧,能够增大弯曲半径而抑制裂纹的产生,因此碰撞能量吸收效果提高。另外,关于涂膜13的适当厚度为0.2mm到3mm的情况,将在后述的实施例中进行说明。
[0050]
本实施方式所涉及的汽车用碰撞能量吸收部件1中的涂膜13也作为吸收振动的减振材料(vibration-damping material)发挥作用。例如,在使用汽车用碰撞能量吸收部件1作为发生轴向压溃而吸收碰撞能量的部件即前纵梁的情况下,涂膜13吸收搭载于该前纵梁的汽车发动机(engine)的振动,减振性提高。该减振性提高的效果也在后述的实施例中进行说明。
[0051]
如上所述,涂膜形成构件5以在电沉积涂装时形成规定厚度的涂膜13为目的而不需要强度,因此可以是与外部件7和内部件9相比强度较低、板厚较薄的构件。进一步而言,如果强度过高,则会阻碍顺畅的波纹变形,因此例如优选为440mpa级(mpa-class)以下。
[0052]
[实施方式2]
[0053]
在本实施方式中,对在实施方式1中所说明的汽车用碰撞能量吸收部件1的制造方法进行说明。本实施方式所涉及的汽车用碰撞能量吸收部件1的制造方法包括:部件制造工序,制造在筒状构件3设置有涂膜形成构件5的涂装前部件2;及涂膜形成工序,在涂装前部件2形成涂料层,并通过烘烤处理使涂料层热固化而形成涂膜13。以下,使用图1及图2所示的汽车用碰撞能量吸收部件1的剖视图即图4对各工序进行具体说明。
[0054]
《部件制造工序》
[0055]
部件制造工序是制造在外部件7与内部件9接合而成的筒状构件3的内表面侧设置有涂膜形成构件5的涂装前部件2的工序。如图4(a)所示的例子那样,在外部件7的包含角部7c的范围的内侧,与外部件7的内表面之间隔开0.2mm~3mm的间隙11地设置涂膜形成构件5,并通过点焊等与纵壁部7b的内表面接合。外部件7与内部件9的接合及外部件7与涂膜形成构件5的接合可以先进行任一个。
[0056]
《涂膜形成工序》
[0057]
涂膜形成工序是使涂膜13形成于间隙11的工序。在上述部件制造工序中制造出的涂装前部件2安装到车身的状态下,通过实施在汽车的制造过程中通常进行的电沉积涂装,由此在间隙11形成涂膜13。以下,在对电沉积涂装及汽车制造中的其他涂装工序进行概述的同时对本工序进行说明。
[0058]
通常,对于汽车的车身,为了提高耐气候性(weatherability)、外观设计性(design)、防腐蚀性(anticorrosion property)等,对钢板依次实施电沉积涂装、中间涂层(intermediate coat)涂装、顶涂层(top coat)基底涂装、顶涂层透明涂装(clear coat)。其中,对钢板最先实施的电沉积涂装是为了提高车身的防锈性(rust prevention)的重要工序,被广泛使用。电沉积涂装实施通过电沉积而在钢板形成涂料层的处理和通过干燥炉(烘箱(oven))等使涂料层固化的处理。以下说明电沉积涂装的一例,并示出与本实施方式的涂膜形成工序的对应。
[0059]
在一般的电沉积涂装中,首先,对通过钢板的冲压成形(press-forming)等而形成的车身部件,进行作为预处理的脱脂(degreasing)、水洗(washing)和化学转化处理(chemical conversion treatment)等表面处理(surface treatment),之后,将进行了表面处理的车身部件浸渍于装有电沉积涂料的电沉积槽(electrodeposition tank),并以被涂物(object to be coated)(车身部件)为阴极(cathode)、以电沉积涂料为阳极(anode)来进行通电(conducting),由此在钢板表面形成由电沉积涂料形成的涂料层(阳离子电沉积涂装)。通过电沉积槽内的通电而在表面形成有电沉积涂料的涂料层的车身部件经过之后的水洗等处理而被输送到高温的干燥炉(烘箱),通过烘烤处理(baking finish)而使涂料层固化。
[0060]
在本实施方式的部件制造工序中制造出的涂装前部件2(参照图4(a))也是在安装到车身骨架的状态下浸渍于上述电沉积槽时,电沉积涂料进入间隙11,并通过之后的通电而形成涂料层。在间隙11以外的其他部位也在钢板表面形成由电沉积涂料形成的涂料层,
但其厚度为0.05mm左右,因此省略图示。
[0061]
形成有涂料层的汽车用碰撞能量吸收部件1之后经过如上所述的烘烤处理而使涂料层固化,规定厚度的涂膜13固着于间隙11(图4(b))。另外,涂膜13优选遍及间隙11内的整个区域以实心状态(solid state)形成,但也考虑以在间隙11的一部分存在空隙(void)的状态形成涂膜13的情况,即使在这样的情况下,与没有涂膜13的情况相比,也能够发挥本发明的效果,因此不排除在间隙11的一部分存在空隙的情况。
[0062]
电沉积涂装的相对于被涂物的追随性(deposition property of electrodeposition coating)高,因此相对于凹凸多的内板构件(车身骨架部分和发动机室等)特别有效。电沉积涂料有各种种类,根据涂装对象和要求功能(追随性、节能性(energy saving)、防腐蚀性等)而分开使用。对于本发明的汽车用碰撞能量吸收部件1,设想利用主要用于内板(内装)的软质涂料(flexible coating film)进行的电沉积涂装,作为其种类,例如可举出聚氨酯类阳离子电沉积涂料、环氧类阳离子电沉积涂料、聚氨酯阳离子电沉积涂料、丙烯酸类阴离子电沉积涂料、氟树脂电沉积涂料等。
[0063]
对实施了电沉积涂装的车身部件实施中间涂层涂装、顶涂层基底涂装、顶涂层透明涂装。它们主要通过被称为静电涂装(electrostatic painting)的将带电的涂料用喷雾器等喷射到被涂物的方法来进行,中间涂层涂装具有电沉积涂装面的粗糙度掩蔽(roughness masking)和光线透过抑制(light transmittance restraining)的功能,顶涂层基底涂装和顶涂层透明涂装具有着色(coloring)等外观设计性和耐久性(durability)等功能。作为用于中间涂层涂装、顶涂层基底涂装和顶涂层透明涂装的涂料的例子,可举出聚酯-三聚氰胺类涂料(polyester-melamine paint)、丙烯酸-三聚氰胺类涂料(acrylic-melamine paint)、丙烯酸-聚酯-三聚氰胺类涂料(acrylic-polyester-melamine paint)、醇酸-聚酯-三聚氰胺类涂料(alkyd-polyester-melamine paint)等。
[0064]
如在电沉积涂装的说明中也提到的那样,在门板(door panel)等与汽车的外观相关的外板(outer panel)(外装)部位、及发动机室和作为本发明的对象的碰撞能量吸收部件等内板(inner panel)(内装)部位中,对涂装要求的功能不同,因此可以在最终的车身组装之前,按照部位结束上述的任一种涂装。
[0065]
如上所述,根据在本实施方式中所说明的汽车用碰撞能量吸收部件1的制造方法,通过在筒状构件3设置涂膜形成构件5,从而在汽车制造的涂装工序中通常进行的电沉积涂装时,在筒状构件3与涂膜形成构件5之间的间隙11形成由电沉积涂料形成的涂膜13,因此能够在不使生产成本大幅上升的情况下制造碰撞能量的吸收效果高的汽车用碰撞能量吸收部件1。
[0066]
在实施方式1和2中,对如图4的剖视图所示的在外部件7的纵壁部7b设置涂膜形成构件5的接合部12,在顶板部7a、角部7c及纵壁部7b的一部分内表面形成涂膜13的例子进行了说明,但本发明并不限于此。例如,如图5所示,也可以在纵壁部7b少且以顶板部7a和角部7c为主体的内表面形成涂膜。另外,如上所述,如果在碰撞时特别容易产生裂纹的角部7c的内表面形成涂膜,则能够期待碰撞能量吸收效果的提高,因此如图6所示,也可以在以角部7c为主体的内表面形成涂膜13。此时,可以使用两个涂膜形成构件5在顶板部7a和纵壁部7b分别设置接合部12(图6(a)),也可以使用一个涂膜形成构件5在纵壁部7b设置接合部12(图6(b))。
[0067]
另外,如图7所示,也可以在纵壁部7b及角部7c的内表面形成涂膜13。与图6同样地,可以使用两个涂膜形成构件5在顶板部7a和纵壁部7b分别设置接合部(joining portion)12(图7(a)),也可以使用一个涂膜形成构件5在纵壁部7b设置接合部12(图7(b))。而且,也可以将如图8所示的帽形截面型的涂膜形成构件5与外部件7和内部件9合并而在接合部10接合。
[0068]
在本实施方式中,举出了由帽形截面形状的外部件7和平板形状的内部件9构成的筒状构件3为例,但本发明并不限于此,也能够应用于图9所例示的使帽形截面构件对置并使凸缘部(flange portion)合并而成的筒状构件。图9(a)是在对置的帽形截面构件分别设置有图5所示的方式的涂膜形成构件5的例子。同样地,图9(b)是设置有图6(a)所示的方式的涂膜形成构件5的例子,图9(c)是设置有图7(a)所示的方式的涂膜形成构件5的例子,图9(d)是设置有图8所示的方式的涂膜形成构件5的例子。另外,在图9中,对外部件7标注与图5~图8相同的标号,对内部件9标注与外部件7对应的标号。另外,在图9中示出了外部件7和内部件9是相同形状的帽形截面构件的例子,但内部件9也可以是与外部件7不同形状的帽形截面构件。
[0069]
实施例
[0070]
由于进行了用于确认本发明所涉及的汽车用碰撞能量吸收部件1的效果的实验,因此以下对其结果进行说明。
[0071]
在本实施例中,将本发明所涉及的汽车用碰撞能量吸收部件作为试验体,进行基于轴向压溃试验的碰撞能量的吸收特性的评价、和基于冲击振动试验中的频率响应函数(frequency response function)的测定和固有振动频率(character frequency)的计算的减振特性的评价。
[0072]
在轴向压溃试验中,如图10所示,测定载荷-行程曲线(load-stroke curve),并且利用高速照相机进行拍摄,观察变形状态和筒状构件3中有无发生断裂,该载荷-行程曲线(load-stroke curve)表示在具有筒状构件3的试验体21的轴向上以试验速度17.8m/s输入载荷而使试验体长度(试验体21的轴方向长度l0)从200mm到120mm轴向压溃变形80mm时的载荷与行程(轴向压溃变形量(amount of axial crush deformation))之间的关系。而且,根据测定出的载荷-行程曲线求出行程为0~80mm的吸收能量。
[0073]
另一方面,在冲击振动试验中,如图11所示,对于悬挂的试验体21将加速传感器(acceleration sensor)(小野测器制:np-3211)安装于外部件7的顶板部7a的边缘附近,用冲击锤(impact hammer)(小野测器制:gk-3100)对试验体21的外部件7的纵壁部7b进行冲击励振(impact vibration),并将励振力和在试验体21产生的加速(acceleration)取入到fft分析仪(小野测器制:cf-7200a),计算频率响应函数。在此,频率响应函数通过基于5次冲击的平均化处理和曲线拟合(curve fitting)来计算。然后,利用计算出的频率响应函数进行振动模式解析(vibration mode analysis),求出同一模式下的固有振动频率。图12示出作为对象的振动模式。
[0074]
图13示出作为上述实施方式1和2所涉及的形成有涂膜13的汽车用碰撞能量吸收部件1(图2和图4(b))的试验体21的构造和形状。试验体21具有通过点焊将外部件7与内部件9接合而成的筒状构件3,涂膜形成构件5与外部件7的纵壁部7b的内表面接合。在外部件7与涂膜形成构件5之间形成有涂膜13。
[0075]
图13示出了将顶板部7a与涂膜形成构件5之间的间隙11设为3mm的例子,但在本实施例中也准备了将间隙11设为2mm、1mm、0.2mm的试验体21,一边改变形成在间隙11内的涂膜13的厚度一边进行试验。
[0076]
而且,作为比较例,准备如图14所示的具有筒状构件3和涂膜形成构件5且未形成涂膜13的试验体31,并与发明例同样地进行轴向压溃试验及冲击振动试验。表2示出作为发明例的试验体21及作为比较例的试验体31的构造和涂膜的各条件和试验体重量、以及进行了轴向压溃试验时的吸收能量的计算结果和通过冲击振动试验求出的固有振动频率的结果。
[0077][0078]
发明例1~发明例5均使用具备涂膜形成构件5和涂膜13的试验体21(图13),并使外部件7及涂膜形成构件5的强度(材质)和涂膜13的厚度发生变化。另一方面,比较例1~比
较例4使用具备涂膜形成构件5但未形成涂膜13的试验体31(图14),并使外部件7的强度(材质)及板厚、外部件7与涂膜形成构件5之间的间隙11发生变化。比较例5不具备涂膜形成构件5而形成有涂膜13。比较例6与试验体21同样地具备涂膜形成构件5和涂膜13,但涂膜形成构件5的材质超过外部件7及内部件9的材质的强度。
[0079]
表2所示的试验体重量中,对于形成有涂膜13的试验体,是外部件7、内部件9、涂膜形成构件5和涂膜13的各重量的总和,对于没有涂膜13的试验体(比较例1~比较例4),是外部件7、内部件9和涂膜形成构件5的各重量的总和。
[0080]
在比较例1中,试验体重量为1.06kg,吸收能量为6.5kj。而且,固有振动频率为155hz。
[0081]
比较例2相对于比较例1变更了外部件7的板厚和外部件7与涂膜形成构件5之间的间隙,试验体重量为1.17kg,吸收能量为7.0kj,与比较例1相比增加。固有振动频率为175hz。
[0082]
在比较例3中,使外部件7为980mpa级的高强度钢板(high-strength steel sheet),试验体重量为1.06kg。吸收能量为8.1kj,与比较例2相比进一步增加,但筒状构件3发生了断裂。固有振动频率为155hz。
[0083]
在比较例4中,使外部件7为1180mpa级的高强度钢板,试验体重量为1.07kg。吸收能量为8.5kj,与比较例3相比进一步增加,但筒状构件3发生了断裂。固有振动频率为155hz。
[0084]
在比较例5中,使外部件7为1180mpa级的高强度钢板,不设置涂膜形成构件5而使涂膜13成膜,涂膜13的厚度为0.05mm。试验体重量为0.96kg,吸收能量为8.7kj,与比较例4相比增加,但筒状构件3发生了断裂。固有振动频率为155hz。
[0085]
在比较例6中,涂膜形成构件5的材质超过外部件7及内部件9(筒状构件3)的材质的强度,而且形成有3mm厚度的涂膜13。试验体重量为1.06kg,吸收能量为8.1kj,与比较例2相比增加,但筒状构件3发生了断裂。固有振动频率为155hz。
[0086]
在发明例1中,使用使外部件7为钢板强度590mpa级的钢板、涂膜13的厚度为3mm的试验体21。发明例1中的吸收能量为11.1kj。与未形成涂膜13的相同材质的比较例1中的吸收能量(=6.5kj)相比大幅提高,筒状构件3未发生断裂。而且,与使外部件7为980mpa级的高强度钢板的比较例3(=8.1kj)、使外部件7为1180mpa级的高强度钢板的比较例4(=8.5kj)相比,大幅提高。发明例1的试验体重量(=1.25kg)与比较例1(=1.06kg)、比较例3(=1.06kg)及比较例4(=1.07kg)相比增加,但吸收能量除以试验体重量所得的每单位重量的吸收能量为8.9kj/kg,与比较例1(=6.1kj/kg)、比较例3(=7.6kj/kg)及比较例4(=7.9kj/kg)相比提高。另外,发明例1中的固有振动频率为430hz,与比较例1、比较例3及比较例4(=155hz)相比大幅上升。
[0087]
发明例2使用与发明例1相同的材质,并使涂膜13的厚度为2mm。试验体重量为1.18kg,与发明例1(=1.25kg)相比较轻。发明例2中的吸收能量为9.0kj,与相同形状且外部件的板厚较厚的比较例2中的吸收能量(=7.0kj)相比提高。筒状构件3未发生断裂。而且,发明例2中的每单位重量的吸收能量为7.6kj/kg,与比较例2(=6.0kj/kg)相比提高。另外,发明例2中的固有振动频率为340hz,与比较例2(=175hz)相比大幅上升。
[0088]
发明例3与发明例2同样地将涂膜13的厚度设为2mm,并将涂膜形成构件5的钢板强
度设为440mpa级。在涂膜形成构件5的钢板强度为超过外部件的钢板强度的780mpa的比较例6中,筒状构件3发生了断裂,但在发明例3中未发生断裂。另外,发明例3的吸收能量为9.5kj,与比较例6(=8.1kj)相比提高。而且,发明例3中的固有振动频率为340hz,与比较例6(=155hz)相比大幅上升。
[0089]
在发明例4中,使外部件7为钢板强度1180mpa级的高强度钢板,并将涂膜13的厚度设为1mm。发明例4中的吸收能量为11.2kj,筒状构件3未发生断裂。与外部件7使用相同材料的钢板并产生了断裂的比较例4(=8.5kj)相比大幅提高。另外,发明例4中的试验体重量为与发明例1相比较轻的1.14kg,而且,每单位重量的吸收能量(=9.8kj/kg)与发明例1(=8.9kj/kg)及比较例4(=7.9kj/kg)相比提高。而且,发明例4中的固有振动频率为310hz,与比较例4(=155hz)相比大幅上升。
[0090]
发明例5在与发明例4为相同的原材料的试验体中,将涂膜13的厚度设为与通常的层压钢板(laminated steel sheet)中的层压层相同程度的0.2mm,试验体重量为1.08kg。发明例5中的吸收能量为10.7kj,每单位重量的吸收能量为9.9kj/kg,与不具备涂膜形成构件5而形成0.05mm的涂膜的比较例5(=9.1kj/kg)相比提高。另外,比较例5在筒状构件产生了断裂,但发明例5未产生断裂。而且,发明例5中的固有振动频率为280hz,与比较例5(=155hz)相比上升。
[0091]
另外,虽然表中没有记载,但在使外部件7与涂膜形成构件5之间的间隙为4mm以上的情况下,即,在形成了4mm以上的厚度的涂膜13的情况下,在电沉积涂装的烘烤处理中无法进行充分的干燥。因此,将本发明中的涂膜13的适当厚度设为0.2mm~3mm。
[0092]
由以上示出,本发明所涉及的汽车用碰撞能量吸收部件1在沿轴向输入碰撞载荷而发生轴向压溃的情况下,能够抑制重量的增加且高效地提高碰撞能量的吸收效果,并且,施加有冲击时的固有振动频率上升而能够提高减振性。
[0093]
另外,通过固有振动频率上升来提高减振性的理由如下所述。如上述前纵梁那样的作为碰撞部件的筒状构件3的固有振动频率若落入搭载于该部件的发动机的振动的频率范围,则发生共振(sympathetic vibration)而振动变大。例如,当发动机以通常行驶的高转速区域即4000rpm旋转时,曲轴(crankshaft)以相同的转速旋转,在四冲程发动机中每两转爆发一次而进行振动,因此振动的频率在四气缸(cylinder)发动机中为133hz,在六气缸发动机中为200hz,在八气缸发动机中为267hz。因此,只要是本发明的约280hz以上的固有振动频率,就能够可靠地防止上述共振,从而减振性提高。
[0094]
产业上的可利用性
[0095]
根据本发明,能够提供一种汽车用碰撞能量吸收部件、该汽车用碰撞能量吸收部件的制造方法,在如前纵梁或碰撞盒那样从车身的前方或后方输入碰撞载荷而发生轴向压溃时,碰撞能量的吸收效果提高,并且能够减少追加的生产工序从而生产成本不会大幅上升。
[0096]
标号说明
[0097]
1 汽车用碰撞能量吸收部件
[0098]
2 涂装前部件
[0099]
3 筒状构件
[0100]
5 涂膜形成构件
[0101]
7 外部件
[0102]
7a 顶板部
[0103]
7b 纵壁部
[0104]
7c 角部
[0105]
9 内部件
[0106]
9a 顶板部
[0107]
9b 纵壁部
[0108]
9c 角部
[0109]
10 接合部(筒状构件)
[0110]
11 间隙
[0111]
12 接合部(涂膜形成构件)
[0112]
13 涂膜
[0113]
21 试验体(发明例)
[0114]
31 试验体(比较例)。