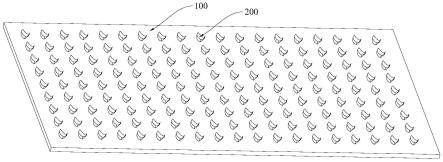
1.本发明属于仿生材料领域,涉及一种减阻减摩仿生材料,尤其涉及一种用于涉水的减阻减摩仿生织构。
背景技术:2.与陆地环境相比,海洋环境更为苛刻、复杂。海洋水下航行器的螺旋桨的等部件在安装、服役期间会承受多种载荷的影响,同样,也会受到海水或/和油气介质引起的腐蚀,以及可能遇到的低温或高温环境的作用。因此,提高水下航行器的螺旋桨等部件的减阻减摩性能具有重要意义,到目前为止,多种表面工程技术如强流脉冲离子束表面改性、激光熔覆、离子注入、物理气相沉积、激光表面织构化等方法已经被应用于提高金属表面的耐磨性。
3.在多种表面工程技术中,激光表面织构由于具有加工速度快、生产效率高、可控性好等优点受到了广泛的关注,而在水下螺旋桨方面,目前的减摩减阻方式的制备工艺比较复杂,成本较高,不易于工业化生产。实现水下螺旋桨的减阻减摩需要一种新型的制备工艺简单,经济易于操作的表面织构。
技术实现要素:4.本发明的目的正是基于上述问题,提出了一种用于涉水的减阻减摩仿生织构,可以应用于水下螺旋桨的表面减阻结构,由于仿生突起顶部的曲面形凹槽,涡流效应明显,可以在海水环境中将海水流动形成涡流从而形成“滚轴”效应,将滑动摩擦转化为滚动摩擦,并增强流体动压效应,于空白试样相比,摩擦系数降低率高达60%以上。
5.为了达到上述目的,本发明采用的技术方案如下:
6.一种用于涉水的减阻减摩仿生织构,其特征在于:包括基体材料和设于基体材料表面的若干仿生突起,所述仿生突起整体为扇形柱,在扇形柱顶部向下开设有一个曲面形凹槽,所述曲面形凹槽靠近扇形柱的轴心线一侧为下凹陡坡,相对靠近弧形面一侧为下凹平缓坡,整体形成涡流凹槽。
7.进一步地,定义穿过扇形柱的轴心线的平面与曲面形凹槽交线为纵向剖面,所述扇形柱的所有纵向剖面相同,所述纵向剖面的顶部曲线靠近扇形柱中心一段为下凹陡坡曲线,相对另一段为平缓坡曲线。
8.进一步地,所述下凹陡坡曲线和平缓坡曲线的坡度均为渐变式,越靠近圆心一侧坡度越陡。
9.进一步地,所述纵向剖面中,所述顶部曲线最低点距离扇形柱轴心线的距离为扇形柱半径的1/2-1/5。
10.进一步地,所述仿生突起的扇形尖端方向为基体材料表面迎流方向。
11.进一步地,所述仿生突起整体为扁平型的扇形柱,即扇形柱的高度半径比小于1。
12.进一步地,所述扇形柱的半径为0.1-100微米,扇形柱高度为0.1-20微米。
13.进一步地,顶部曲线最低点距离扇形柱顶部距离(曲面形凹槽最深深度)为扇形柱高度的1/2-4/5。
14.进一步地,所述仿生突起在基体材料表面阵列形分布,进一步,可以优选为行列型阵列分布。
15.进一步地,所述仿生突起占基体材料表面面积的5%-40%
16.进一步地,所述仿生突起的生成方式为:先定义纵向剖面形状,将纵向剖面绕着扇形柱的轴心线旋转β角度,即得到所述仿生突起,β取值范围为30-150度。
17.本发明减阻减摩原理如下:
18.本发明通过在基体材料表面设置微米级的仿生突起,仿生突起整体为扇形柱,扇形柱顶部向下开设有一个曲面形凹槽,所述曲面形凹槽靠近扇形柱的轴心线一侧为下凹陡坡,相对靠近弧形面一侧为下凹平缓坡,整体形成涡流凹槽;在流体在经过基体材料表面的仿生织构时,流体截面积变小,经过扇形柱棱边时,流体被分流从棱边尖两侧进入扇形柱顶部的曲面形凹槽内,由于曲面形凹槽先陡后缓,分流撞击织构曲面形凹槽先侧面从而形成涡流,从而形成“滚轴”效应,将滑动摩擦转化为滚动摩擦,并增强流体动压效应,达到减阻减摩的目的。
19.通过上述原理可知,扇形柱尺寸级别、密度、扇形柱顶部曲面形凹槽的深度、部曲面形凹槽深度、宽深比、液体粘度等都对减阻减摩效果造成比较大的影响。
20.与现有技术相比,本发明的优点在于:
21.(1)制备方法简单易行,实验过程仅需激光打标设备,没有涉及任何有机试剂,符合绿色环保路线
22.(2)加工材料广泛且经济,可广泛应用于各种材料螺旋桨。
23.(3)具有涡流增强效应能形成类似滚轴运动,将滑动摩擦转化为滚动摩擦。
24.(4)实现了优异的减阻减摩效果,摩擦系数降低率高达以上。
附图说明
25.图1为本发明实施例中减阻减摩仿生织构示意图。
26.图2为减阻减摩仿生织构中单个仿生突起结构示意图。
27.图3为减阻减摩仿生织构中单个仿生突起结构俯视图。
28.图4为减阻减摩仿生织构中单个仿生突起结构的纵向剖面示意图。
29.图5为本发明实例1中的无织构和织构样件的摩擦系数对比。
30.图6为本发明实例2中的无织构和织构样件的摩擦系数对比。
31.图7为本发明实例3中的无织构和织构样件的摩擦系数对比。
32.图8为减阻减摩仿生织构流场矢量示意图。
33.图9为减阻减摩仿生织构流体压力示意图。
34.100-螺旋桨基体材料,200-仿生突起,210-扇形柱,211-轴心线,220-曲面形凹槽,230-纵向剖面,231-左侧竖线,232-右侧竖线,233-顶部曲线,234-底部水平线,240-最低点。
具体实施方式
35.为了能够更清楚地理解本发明的上述目的、特征和优点,下面结合附图和具体实施方式对本发明进行进一步的详细描述。需要说明的是,在不冲突的情况下,本发明的实施例及实施例中的特征可以相互组合。
36.在下面的描述中阐述了很多具体细节以便于充分理解本发明,但是,本发明还可以采用其他不同于在此描述的其他方式来实施,因此,本发明的保护范围并不受下面公开的具体实施例的限制。
37.实施例1
38.如图1至图4所示,一种应用于水下螺旋桨的减阻减摩仿生织构,包括螺旋桨基体材料100和加工于螺旋桨基体材料100表面阵列型的仿生突起200,仿生突起200的密度为25%(占螺旋桨基体材料表面比),
39.如图2所示,所述仿生突起200整体为扇形柱210,在扇形柱顶部向下开设有一个曲面形凹槽220,所述曲面形凹槽220靠近扇形柱的轴心线211一侧为下凹陡坡,相对靠近弧形面一侧为下凹平缓坡,整体形成涡流凹槽。
40.如图2所示,定义穿过扇形柱210的轴心线211的平面与曲面形凹槽220交线为纵向剖面230,所述扇形柱的所有纵向剖面230相同,如图4所示,所述纵向剖面230的顶部曲线233靠近扇形柱中心一段(图4中右侧段)为下凹陡坡曲线,相对另一段(图4中左侧段)为平缓坡曲线。
41.本实施例中,仿生突起200生成方式如下:
42.如图3和4所示,仿生突起200的纵向剖面由底部水平线234、左侧竖线231、右侧竖线232和顶部曲线233构成,底部水平线234长度为扇形柱210的半径r=10微米,左右两侧竖线高度为扇形柱210的高度h=3微米,顶部曲线233为下凹平滑曲线,下凹平滑曲线的最低点240距离右侧竖线232的距离l=0.25r=2.5微米,下凹平滑曲线的最低点240的深度h1=0.75h=2.25微米,将纵向剖面230绕着右侧竖线232旋转β=90度,即得到单个仿生突起;选择仿生突起在基体材料表面为阵列型分布,阵列方式为行列型阵列;阵列密度为25%。
43.作为一种优选实施例,所述仿生突起的扇形尖端方向(扇形柱棱边方向)为基体材料表面迎流方向。如图3所示,箭头方向为流体相对于基体材料表面的流动方向。
44.将上述定义结构采用cad定义在螺旋桨表面,导入激光加工设备中,在材料表面进行激光加工,加工次数2次。
45.需要说明的是,图1中螺旋桨基体材料为平面,实际上螺旋桨基体材料根据实际形状进行选择,图1仅为表达仿生突起在基体材料分布形态图,并不是意味着只能设置在平面型结构表面,对于曲面形的基体材料,满足扇形柱210的轴线与该处曲面法向重合或者平行即可,一般来说,相对于基体材料宏观结构,对于扇形柱210的尺寸来说,在扇形柱210附近的基体材料可以近似看做平面。
46.(1)减阻减摩仿生织构的制备
47.使用激光打标机进行加工,加工参数为:线速度500mm/s,加工功率2j,激光频率30khz,加工次数2次。
48.(2)减摩测定方法
49.销盘摩擦磨损试验机上进行销盘旋转摩擦试验:直径6.35mm,长度为19mm的upe
(超高分子量聚乙烯)销与直径25mm,厚度10mm的316l不锈钢盘进行旋转摩擦。
50.测试条件:载荷10n,速度300、500、700r/min(线速度0.785m/s、1.309m/s、1.833m/s)
51.(3)减摩结果对比分析
52.与无织构316l不锈钢样件对比,摩擦系数并无降低。
53.其摩擦系数对比如图5所示。
54.实施例2
55.一种应用于水下螺旋桨的减阻减摩仿生织构,包括螺旋桨基体材料和加工于螺旋桨基体材料表面的阵列型仿生突起,仿生突起的密度为30%(占螺旋桨基体材料表面比),仿生突起生成方式如下:
56.参见图4所示,仿生突起由纵向剖面由底部水平线、左右两侧竖线和顶部曲线构成,底部水平线长度为r=10微米,左右两侧竖线高度h=3微米,下凹平滑曲线的最低点240的深度h1=0.75h=2.25微米,顶部曲线为下凹平滑曲线,下凹平滑曲线最低点距离右侧竖线距离l=0.25r=2.5微米,将纵向剖面绕着右侧竖线旋转β=60度,即得到单个仿生突起;选择仿生突起在基体材料表面为阵列型分布,阵列方式为行列型阵列;阵列密度为30%。
57.将上述定义结构采用cad定义在螺旋桨表面,导入激光加工设备中,在材料表面进行激光加工,加工次数2次。
58.(1)减阻减摩仿生织构的制备
59.使用激光打标机进行加工,加工参数为:线速度500mm/s,加工功率2j,激光频率30khz,加工次数2次。
60.(2)减摩测定方法
61.销盘摩擦磨损试验机上进行销盘旋转摩擦试验:直径6.35mm,长度为19mm的upe(超高分子量聚乙烯)销与直径25mm,厚度10mm的316l不锈钢盘进行旋转摩擦。
62.测试条件:载荷10n,速度300、500、700r/min(线速度0.785m/s、1.309m/s、1.833m/s)(3)减摩结果对比分析
63.与无织构316l不锈钢样件对比,摩擦系数降低率60%。
64.其摩擦系数对比如图6所示。
65.实施例3
66.一种应用于水下螺旋桨的减阻减摩仿生织构,包括螺旋桨基体材料和加工于螺旋桨基体材料表面的阵列型仿生突起,仿生突起的密度为35%(占螺旋桨基体材料表面比),仿生突起生成方式如下:
67.参见图4所示,仿生突起由纵向剖面由底部水平线、左右两侧竖线和顶部曲线构成,底部水平线长度为r=10微米,左右两侧竖线高度h=3微米,顶部曲线为下凹平滑曲线,下凹平滑曲线最低点距离右侧竖线距离l=0.25r=2.5微米,下凹平滑曲线的最低点240的深度h1=0.75h=2.25微米,将纵向剖面绕着右侧竖线旋转β=120度,即得到单个仿生突起;选择仿生突起在基体材料表面为阵列型分布,阵列方式为行列型阵列;阵列密度为35%。
68.将上述定义结构采用cad定义在螺旋桨表面,导入激光加工设备中,在材料表面进行激光加工,加工次数2次。
69.(1)减阻减摩仿生织构的制备
70.使用激光打标机进行加工,加工参数为:线速度500mm/s,加工功率2j,激光频率30khz,加工次数2次。
71.(2)减摩测定方法
72.销盘摩擦磨损试验机上进行销盘旋转摩擦试验:直径6.35mm,长度为19mm的upe(超高分子量聚乙烯)销与直径25mm,厚度10mm的316l不锈钢盘进行旋转摩擦。
73.测试条件:载荷10n,速度300、500、700r/min(线速度0.785m/s、1.309m/s、1.833m/s)
74.(3)减摩结果对比分析
75.与无织构316l不锈钢样件对比,摩擦系数降低率14.8%。
76.其摩擦系数对比如图7所示。
77.综上所述,本发明提出了一种应用于水下螺旋桨的减阻减摩仿生织构,在材料表面进行激光加工类似穿山甲鳞片的减阻减摩仿生织构,所述仿生突起面积占比为5%-40%,穿山甲鳞片的形状为均匀分布的盾鳞形状,本发明采用顶部凹陷曲面的扇形柱模仿盾鳞形状,以达到类似的仿生效果。减阻减摩仿生织构的制备方法为在cad中根据所需进行密度及单个尺寸设定,并采用分层叠加的加工方式,将单个织构拆分,多次加工以达到织构底部具有深度梯度结构。由于织构底部的梯度深度结构,涡流效应明显,新型的仿生织构可以在海水环境中将海水流动形成涡流从而形成“滚轴”效应,将滑动摩擦转化为滚动摩擦,并增强流体动压效应,于空白试样相比,摩擦系数降低率高达60%以上。该仿生织构制备方法简单易行,实验过程仅需激光加工设备,没有涉及任何有机试剂,符合绿色环保路线,可以广泛用于水下螺旋桨表面织构。
78.以上所述仅为本发明的优选实施例而已,并不用于限制本发明,对于本领域的技术人员来说,本发明可以有各种更改和变化。凡在本发明的精神和原则之内,所作的任何修改、等同替换、改进等,均应包含在本发明的保护范围之内。